Exploring Active Brazing Techniques for Industrial Applications
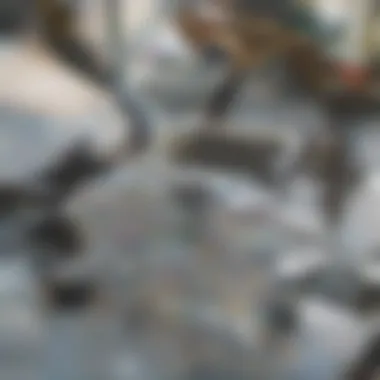
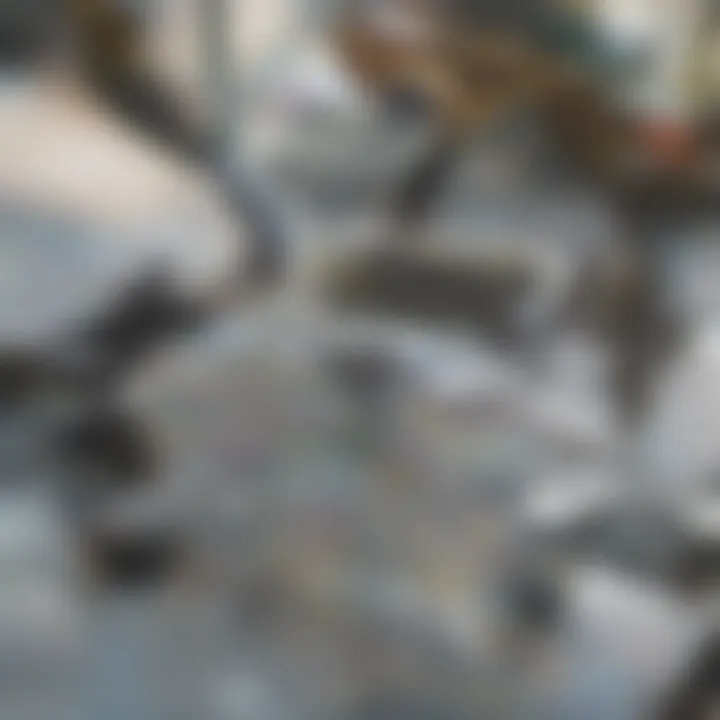
Intro
Active brazing is a significant technique in the world of materials joining. It is essential in various high-tech industries for creating strong bonds between dissimilar materials. Understanding this process requires familiarity with its terminology and concepts, which lay the groundwork for deeper exploration.
In this examination, we will address not just the mechanisms at play in active brazing, but also its advantages, challenges, and the diverse applications that make it indispensable in contemporary engineering. This knowledge is crucial for students, researchers, educators, and professionals in the field who seek to expand their comprehension of advanced joining technologies.
Key Concepts and Terminology
Definition of Key Terms
Active Brazing: This is a joining process that utilizes a filler metal with an active element that enhances the wetting of the base materials.
Wetting: Refers to the ability of the filler metal to spread over the surfaces being joined, which is crucial for strong bonds.
Filler Metal: The material added during the brazing process. It melts and flows to join the workpieces without melting them.
Concepts Explored in the Article
- Mechanisms of Active Brazing: This involves how the active element in the filler interacts with the surfaces.
- Material Compatibility: Understanding how different metals can be bonded successfully.
- Temperature Control: The significance of operating at lower temperatures and the benefits it offers.
- Applications: Critical industries that rely on active brazing, such as aerospace, automotive, and electronics.
Findings and Discussion
Main Findings
The analysis reveals several key advantages to active brazing. First, it allows the joining of materials that are traditionally difficult to bond, such as ceramic to metal. This expands the range of potential applications significantly.
Another notable finding is that lower operating temperatures reduce thermal stress on components. This is crucial in industries where distortions could compromise the integrity of assemblies.
Potential Areas for Future Research
There is substantial scope for advancements in active brazing techniques. Future research could explore new filler compositions to enhance properties like corrosion resistance and mechanical strength. Additionally, there is a need to investigate the long-term reliability of joints made through active brazing in various environmental conditions.
"Active brazing stands at the intersection of innovation and necessity in modern manufacturing, promising enhanced performance in joining technologies."
Through understanding these various aspects of active brazing, industry professionals can make informed decisions to leverage its advantages in practical applications.
Intro to Active Brazing
Active brazing represents a crucial advancement in the field of joining technologies. It transcends traditional brazing by enabling the attachment of various dissimilar materials. The significance of this technique lies in its ability to achieve strong and durable joints at lower temperatures, making it essential in modern manufacturing processes.
Definition and Historical Context
Active brazing is defined as a joining method that utilizes active fluxes to promote the wetting of the filler material on the base materials. Historically, this technique arose as an improvement over conventional brazing. Conventional methods often struggled with bonding areas that have different thermal, electrical, or physical properties. In the mid-20th century, the integration of active fluxes led to better adhesion and enhanced metallurgical bonds. This evolution allowed industries to explore new applications and optimize production efficiency.
Importance in Modern Manufacturing
The relevance of active brazing in today’s manufacturing landscape cannot be overstated. Its ability to bond different metals, ceramics, and composites effectively broadens design possibilities in engineering and production. Key considerations include:
- Reduced Thermal Stress: Working at lower temperatures minimizes the risk of damaging sensitive components.
- Versatility: It caters to several industries, including electronics, automotive, and aerospace, where the bonding of diverse materials is often required.
- Precision Engineering: Active brazing supports the creation of complex assemblies that demand exacting standards, which is crucial for fields like medical equipment.
Active brazing also contributes to sustainability efforts by reducing energy consumption during the manufacturing process. Manufacturers are increasingly adopting these techniques, acknowledging both their operational and environmental benefits.
"Active brazing is pivotal for innovative solutions in complex manufacturing environments, supporting advancements in technology while maintaining quality and efficiency."
In summary, understanding active brazing is essential for stakeholders engaged in the production and application of modern materials. Its unique capabilities promote not only mechanical strength but also innovation across various sectors.
Fundamental Principles of Active Brazing
Active brazing is not just a technique; it represents a systematic approach that combines the fundamentals of metallurgy with practical applications in various industries. The principles of active brazing pave the way for advanced joining solutions. Understanding these principles is essential for effective application in fields such as electronics, automotive, and medical device manufacturing. This section compiles the necessary mechanisms and the critical role of active fluxes in the brazing process.
Basic Mechanisms of Brazing
Brazing operates on a principle where two or more materials are joined together using a filler metal that has a melting point above 450°C but below that of the base metals. The mechanisms that govern this process include surface cleaning, filler metal flow, and solidification. When heat is applied, the filler metal melts and is drawn into the joint by capillary action. This is essential for forming strong metallurgical bonds between substrates.
A notable aspect of brazing is the necessity for clean surfaces. Oxidation or contamination can undermine the bond strength. In an active brazing context, cleaning occurs at lower temp compared to other methods.
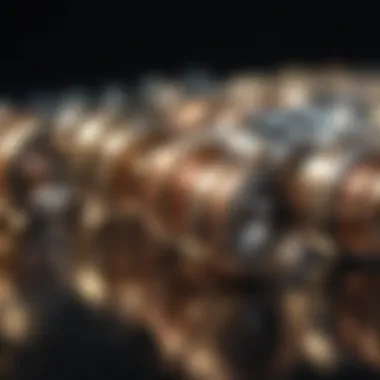
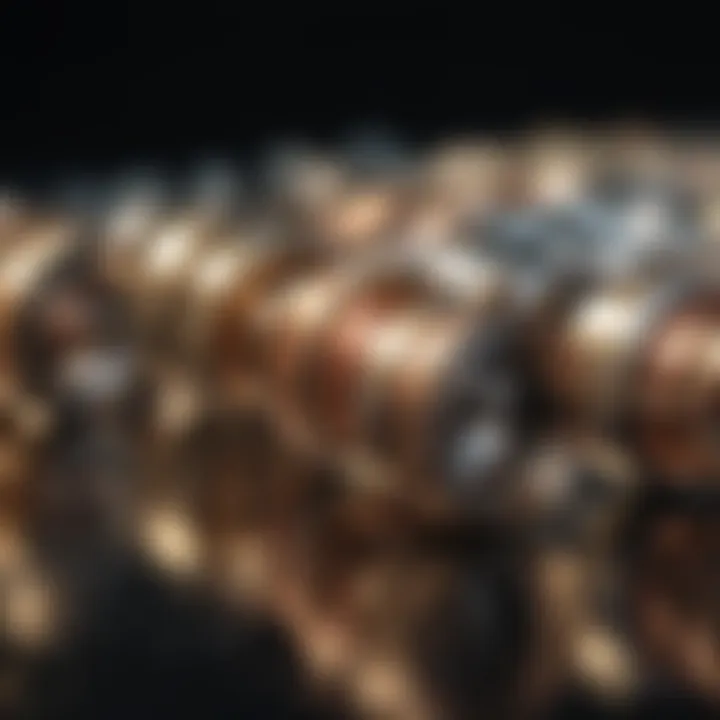
The concepts of heat transfer and thermal management also play significant roles in the effectiveness of this technique. It is essential to maintain an optimal heating rate to avoid undesirable phase changes in the material structure. A precise control over temperature ensures that the base materials do not melt.
Role of Active Fluxes
Active fluxes are critical in promoting successful brazing operations. Their main purpose is to prevent oxidation of the base metals during the heating process. Unlike passive fluxes, active fluxes chemically react and remove surface contaminants. This characteristic of active fluxes enables them to aid the filler metal in wetting and penetrating the joint more effectively.
These fluxes often contain elements like boron or phosphorus. Their presence enhances the fluidity of the molten filler metal. As a result, they lead to improved joint characteristics such as strength and durability.
Moreover, the selection of the appropriate flux is vital. The type of alloys being joined and the environmental conditions can dictate the choice of flux. Using an incompatible flux can lead to joint failures or weak points in the assembly. Hence, understanding the role of active fluxes becomes indispensable in the brazing process.
Test results have shown that using the right active flux can increase the joint strength by significant percentages, reemphasizing the importance of their selection and application in active brazing.
In deliberating the fundamentals of active brazing, both the basic mechanisms and the role of active fluxes hold significance. By mastering these principles, practitioners can advance their capabilities in manufacturing and engineering applications.
Materials Used in Active Brazing
Active brazing requires careful consideration regarding the materials involved. This process typically employs specialized materials that not only facilitate strong bonds but also enhance the overall performance of the joint. Understanding the types of materials used is crucial, as it impacts both the efficiency and efficacy of the brazing operation. This section explores the two main categories of materials used in active brazing, highlighting their roles, properties, and considerations.
Brazing Filler Materials
The choice of brazing filler material is fundamental in active brazing, as it directly influences the joint’s strength and durability. These filler materials often contain a mix of metals with lower melting points. Common examples are silver, copper, and aluminium-based alloys. The properties of these fillers also determine how well they can wet base materials, which is critical for achieving a reliable bond.
When selecting a filler material, several factors must be taken into account:
- Melting Point: Choose a filler with a melting point significantly lower than that of the base materials to prevent damage during the brazing process.
- Compatibility: Ensure that the filler is compatible with the materials being joined. For instance, silver excels when joining copper and brass.
- Mechanical Properties: The final joint’s properties depend on the filler’s inherent characteristics. Higher strength fillers enhance the overall strength of the joint.
Additionally, the choice of active flux is essential when using these materials. Active fluxes help to remove oxides from the base materials, improving the wetting and bonding capabilities of the filler. This results in a seam that is both structurally sound and resistant to corrosion.
Base Materials and Their Selection
The selection of base materials is as important as the choice of filler materials. Base materials can be metals, ceramics, or composites, but metals are the most prevalent in active brazing applications. Each type of base material presents unique challenges and requires specific considerations to achieve optimal bonding.
When selecting base materials, one should consider:
- Thermal Conductivity: Materials with high thermal conductivity, such as copper, can lead to quick heat dissipation, affecting the brazing process. Conversely, low conductivity materials such as ceramics may require specific heating methods to ensure effective bonding.
- Surface Preparation: The surface condition influences the ability of the filler to bond. Clean, oxide-free surfaces are critical. This might involve chemical cleaning or mechanical polishing before brazing.
- Property Matching: It is beneficial to match the thermal expansion coefficients of the base and filler materials. Mismatch can lead to stresses, impacting the joint integrity under service conditions.
Other factors, such as cost and availability, may also affect material selection. Understanding the application’s specific requirements—such as temperature resistance, mechanical stress, and environmental conditions—is paramount.
Selecting the correct materials is crucial for successful active brazing and has a direct impact on both performance and longevity of the joint.
Advantages of Active Brazing
Active brazing offers a range of benefits that contribute significantly to its growing adoption in different industries. Understanding these advantages is essential for professionals and students in engineering and manufacturing fields. Active brazing not only enhances performance but also expands the possibilities for material combinations in modern applications.
Enhanced Joint Strength
One of the most compelling advantages of active brazing is its ability to achieve enhanced joint strength. By utilizing specially formulated active fluxes alongside suitable filler metals, active brazing allows for the formation of robust joints that can endure mechanical stress. The bonding process effectively reduces potential voids and imperfections often seen in other joining methods.
Moreover, the high strength of the joints formed is crucial in applications where reliability is paramount. For instance, in the aerospace sector, components are subjected to varying loads and pressures. Active brazing can create connections that maintain their integrity under such conditions. The metallurgical bond created during the active brazing process often yields joint strengths that meet or exceed the base materials.
"Joint strength is not merely a function of the materials used but how they are joined together. Active brazing takes this to a new level."
Ability to Bond Dissimilar Materials
Another notable advantage of active brazing is its capability to bond dissimilar materials efficiently. Traditional welding techniques frequently struggle when merging materials with different thermal expansion rates or compositions. However, active brazing mitigates these challenges by utilizing specialized filler materials designed for compatibility. This feature is particularly advantageous for industries that require hybrid structures, such as the electronics and automotive sectors.
For example, in electronic assemblies, components made of copper and aluminum can be joined using active brazing. This opens up possibilities for lighter designs and improved performance. Benefits include both reduced overall weight and enhanced thermal management, crucial elements in modern high-performance devices. Thus, the ability to unite unlike materials broadens the scope of design innovation.
Lower Joining Temperatures
Active brazing typically occurs at lower temperatures compared to fusion welding. The reduction in heat contributes to various advantages. First, lower joining temperatures minimize the risk of thermal distortion of the base materials. Heat-affected zones are smaller, preserving the material properties near the joint.
This is particularly vital when dealing with sensitive electronic components, where excessive heat can lead to failure. Additionally, the lower temperatures help in preserving the microstructure of the materials, ensuring that their mechanical and physical properties remain intact.
Therefore, reduced energy consumption during the brazing process is another compelling factor. Utilizing lower temperatures not only decreases operational costs but also makes the process more environmentally friendly.
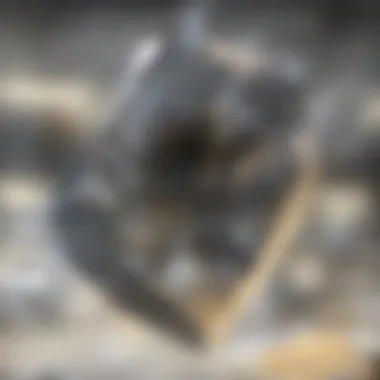
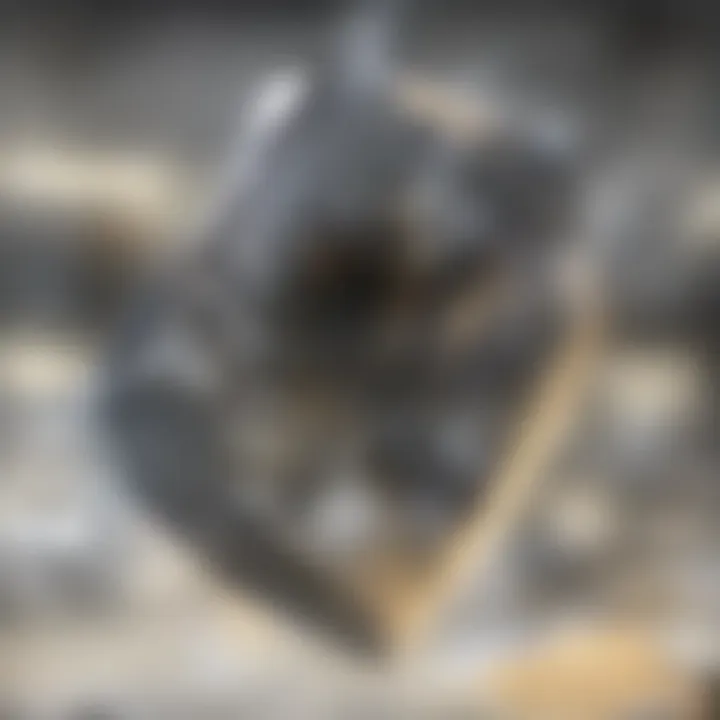
Challenges in Active Brazing
Active brazing, while offering distinct advantages, is not without its challenges. These difficulties must be understood and managed effectively to ensure the success of the overall brazing process. In this section, we will examine several key challenges: thermal management, control of microstructure and properties, and quality assurance and testing. Understanding these challenges is crucial for students, educators, researchers, and professionals who are keen on mastering active brazing techniques.
Thermal Management Issues
Thermal management is one of the primary challenges in active brazing. The process involves precise temperature control to achieve optimal bonding without damaging the base materials. If the temperature exceeds the material's tolerance, it can lead to warping, loss of mechanical properties, or even complete failure of the joint.
Cost-effective methods must be implemented to maintain the required temperatures. Precise heating techniques, such as induction or resistance heating, are commonly employed. However, inadequate control can lead to undesirable thermal gradients which can affect the joint integrity.
Key points regarding thermal management:
- Optimization of heating methods: Select efficient methods based on the specific materials being joined.
- Use of thermal sensors: Implement sensors to monitor temperatures in real-time during the brazing process.
- Proper fixture design: Assist in distributing heat uniformly across the joint, reducing hotspots and ensuring a stable bond.
Control of Microstructure and Properties
The microstructure of the brazed joint plays a vital role in determining its mechanical properties. Variations in cooling rates and temperatures can lead to changes in the microstructure, potentially resulting in weak points within the joint. It is essential to control these parameters to enhance the properties of the joint, such as strength, ductility, and corrosion resistance.
Accurate control can involve selecting specific filler materials that facilitate desired microstructural outcomes. For instance, certain alloys promote the formation of fine grains in the joint area, which improves overall strength.
Strategies to control microstructure:
- Material selection: Choose filler materials compatible with the base metals that provide a beneficial microstructure.
- Controlled cooling rates: Implement cooling strategies that maintain desirable microstructural characteristics.
- Post-braze treatments: Utilize techniques such as annealing to refine the microstructure further and improve mechanical characteristics.
Quality Assurance and Testing
Ensuring quality in active brazing is vital for maintaining the reliability and durability of the final product. Rigorous quality assurance processes must be established to monitor every stage of the brazing operation, from preparation through to final inspection.
Different testing methods are employed to verify joint integrity. Non-destructive testing methods, including ultrasonic testing and X-ray diffraction, are commonly used to assess joints without compromising the product. Alternatively, destructive testing may be necessary in some applications to guarantee performance under extreme conditions.
Considerations for quality assurance:
- Standardized processes: Develop and adhere to standardized procedures for each brazing operation.
- Testing protocols: Implement thorough testing protocols to evaluate joint strength and integrity based on industry standards.
- Documentation of results: Ensure there is a reliable record of all tests conducted, which aids in quality control and informs future practices.
The intricate nature of active brazing calls for an understanding of these challenges. By addressing them diligently, professionals can achieve superior results and maintain high standards in their projects.
Applications of Active Brazing
Active brazing has wide applications across various industries due to its ability to bond different materials effectively at lower temperatures. This property makes it particularly valuable in fields where thermal sensitivity is an important consideration. In this section, we will explore specific applications of active brazing, its benefits, and key considerations for its use.
Electronics and Electrical Components
Active brazing plays a crucial role in the electronics industry. It allows manufacturers to join dissimilar metals, such as copper and aluminum, which is often necessary in electronic devices. These materials have different thermal expansion rates, making traditional soldering techniques less feasible.
One of the main advantages of active brazing in electronics is the integrity of the joints. Higher joint strength leads to more durable connections, crucial in devices that undergo constant stress and thermal cycling. Moreover, the process occurs at lower temperatures, reducing the risk of damaging sensitive components.
Key benefits of active brazing in electronics include:
- Enhanced thermal and electrical conductivity.
- Reduced thermal stress on components.
- Versatility in joining materials like die-cast aluminum to copper.
Automotive and Aerospace Industries
In the automotive and aerospace industries, the demand for lightweight and high-strength materials is increasing. Active brazing meets this need by enabling the bonding of lightweight alloys, such as magnesium and aluminum. This method helps manufacturers reduce weight while maintaining structural integrity.
Active brazing also provides remarkable resistance to corrosion and fatigue, important for parts subjected to harsh environments. Various components such as heat exchangers, radiators, and wing structures can benefit from active brazing. Through this technique, the automotive sector can enhance fuel efficiency while ensuring safety.
The advantages here are substantial:
- Ability to join complex geometries without altering mechanical properties.
- Improved fatigue life of the joint under dynamic loading.
Medical Equipment and Devices
In the medical field, the precise and reliable joining of components is essential. Active brazing allows for the fabrication of medical devices that require clean and strong joints. Applications range from surgical instruments to diagnostic equipment. The process is particularly beneficial in creating assemblies that need to be sterilized, as the joint integrity helps maintain the cleanliness and functionality of the equipment.
Furthermore, active brazing provides biocompatibility when specific filler materials are used. This is critical for implants and devices that come into contact with biological tissues. The attributes of active brazing serve to advance the performance of medical equipment significantly, where reliability can be a matter of life or death.
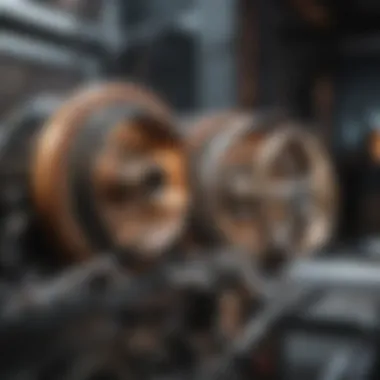
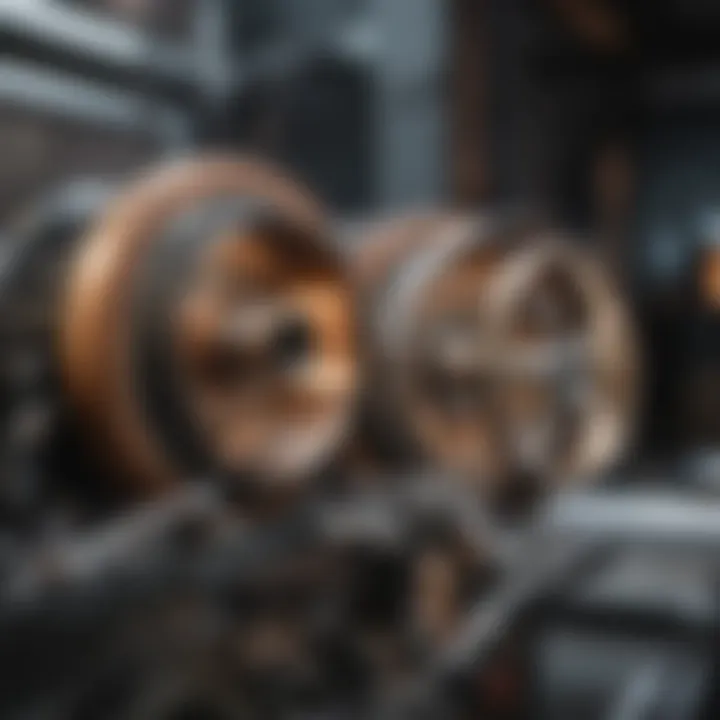
Overall, the specific advantages in this field include:
- High reliability of the joints necessary for critical applications.
- Compatibility with sterilization processes.
Active brazing emerges as a pivotal technology across sectors like electronics, automotive, aerospace, and medical, showcasing its versatility and reliability.
In summary, the applications of active brazing are vast and varied, supporting industries in achieving improved product quality, enhanced performance, and reduced manufacturing costs.
Recent Advancements in Active Brazing
Recent advancements in active brazing have significant implications for various industries. As technology evolves, new materials and techniques surface, offering improved efficiency and effectiveness in the joining process. Staying updated on these advancements is crucial, as they may enhance joint strength, reduce costs, and streamline production.
Innovative Materials and Techniques
The development of innovative materials plays a pivotal role in active brazing. Researchers are increasingly focusing on creating filler materials that possess superior properties. For example, improved alloys with higher melting points are designed to withstand harsher environments. Additionally, unique fluxes are under exploration to enhance the wetting and flow characteristics of the filler metals.
Another key area of innovation lies in surface treatments. Techniques aimed at optimizing the microstructure of base materials can significantly impact the effectiveness of the brazing process. Coatings that increase surface energy help in achieving better adhesion, which ultimately leads to stronger joints.
The usage of advanced additive manufacturing methods also contributes to the field. These methods allow for intricate geometries that traditional manufacturing cannot produce. As a result, the ability to join complex parts while maintaining integrity is considerably increased. The exploration of these materials not only improves joint performance but can also lead to novel applications across different sectors.
Automation and Robotics in Brazing Processes
Automation and robotics are revolutionizing the active brazing landscape. Automation reduces the potential for human error, ensuring more consistent results across production batches. Robots equipped with precision tools can execute processes with high repeatability, leading to better quality control.
Moreover, automation in active brazing allows for faster production rates. As industries become more competitive, companies increasingly turn to automation to maintain efficiency and reduce labor costs.
One of the notable developments in this area is the integration of sensors and intelligent systems that monitor the brazing process in real time. These systems provide feedback that enables immediate adjustments, ensuring optimal conditions throughout the operation. The combination of automation and innovative materials leads to significant advancements in the reliability and performance of brazed joints.
In summary, both innovative materials and advancements in robotics and automation shape the future of active brazing. These developments not only address current challenges but also open new pathways for exploration and application. Keeping abreast of these changes will be critical for professionals, researchers, and educators involved in the industry.
Future Perspectives on Active Brazing
The field of active brazing is experiencing significant growth, and its future holds many exciting possibilities. This process, which allows for the effective joining of dissimilar materials at lower temperatures, is becoming increasingly relevant in various industries. As modern manufacturing demands evolve, the importance of looking ahead becomes apparent. Targeting specific advancements can lead to improvements in joint strength, material compatibility, and process efficiency.
Key areas of focus include new materials and innovative joining techniques. Ongoing research in this area is paramount, and institutions worldwide are investing resources into understanding how to enhance active brazing processes.
Potential Developments and Research Directions
Research initiatives are likely to concentrate on several critical aspects of active brazing. Notably, the exploration of novel filler materials is essential. Materials such as new alloys or composite fillers can improve performance and expand the range of applications. Moreover, optimizing active flux formulations could lead to enhanced wetting characteristics. This improvement may make it easier to achieve high-quality joints across various material types.
Here are some potential new research pathways:
- Development of High-Performance Alloys: Future work could focus on tailoring alloys that provide superior mechanical properties and corrosion resistance.
- Advanced Flux Alternatives: Researchers might explore eco-friendly fluxes and their potential in minimizing environmental impact.
- Process Automation: The potential for integrating automation and robotics into active brazing workflows is another exciting avenue for research. Automation can enhance precision and repeatability, ultimately boosting product quality.
"The direction of future research in active brazing will influence the efficiency of joining technologies across multiple sectors."
Sustainability and Environmental Impact
In today's industrial landscape, sustainability plays a crucial role. Active brazing, as a process, is already seen as an energy-efficient method, but opportunities for further improvement exist. Research into more sustainable practices is critical, especially as environmental regulations tighten and industries strive to reduce their carbon footprint.
Considering the environmental impact of brazing materials is essential. Future developments may include:
- Use of Eco-Friendly Materials: Shifting towards non-toxic materials for active fluxes and fillers could significantly reduce hazardous waste generation.
- Waste Reduction Techniques: Implementing strategies to minimize waste, such as recycling scrap materials, can make a substantial difference in sustainability efforts.
- Energy Consumption: Investigating energy-efficient heating methods is also vital, as reducing energy input can lower operational costs while benefitting the environment.
Emphasizing sustainability not only addresses regulatory pressures but also enhances the marketability of products. A commitment to environmentally responsible practices can resonate well with consumers, and therefore increase competitiveness in the marketplace.
Overall, the future of active brazing appears promising, with significant emphasis on innovative material developments and sustainable practices that not only enhance current capabilities but also align with global sustainability goals.
End
The conclusion serves a vital role in this article, consolidating the extensive exploration of active brazing techniques. This section not only encapsulates the critical information shared but also emphasizes the significance of understanding active brazing in various industrial contexts.
Summary of Key Points
Throughout this article, several key aspects of active brazing were examined:
- Definition and Mechanisms: Active brazing enables effective bonding at lower temperatures, utilizing active fluxes to promote adhesion.
- Materials: A variety of fillers and base materials have been identified, broadening the scope of applications.
- Advantages: Enhanced joint strength, compatibility with dissimilar materials, and lower temperature requirements stand out as major benefits.
- Challenges: The difficulties in managing thermal effects, controlling microstructural properties, and achieving quality assurance were also noted.
- Applications: Industries such as electronics, aerospace, and medical equipment are increasingly relying on this technique to meet demanding requirements.
- Future Perspectives: Ongoing innovations hint at a transformative path ahead for the technology, particularly concerning sustainability and automation.
Final Thoughts on Active Brazing Practices
"Understanding the principles of active brazing will empower industry professionals to make informed decisions that enhance product integrity and performance."
As active brazing continues to be a focal point in modern manufacturing, the insights gained from this comprehensive examination will serve as a foundational resource for all stakeholders involved.