Advanced Techniques in Heat Pipe Bending
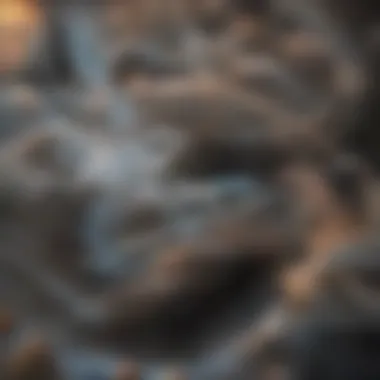
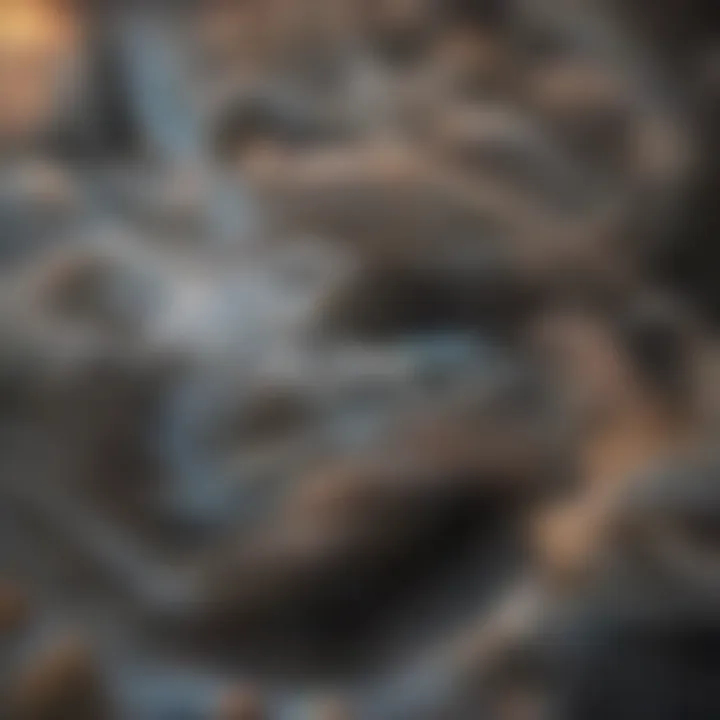
Intro
The technology of heat pipes has garnered significant attention in various industries, particularly for its efficiency in heat management. Consequently, understanding heat pipe bending remains crucial. This article aims to elucidate key concepts, methods, and implications related to this specialized area of heat transfer technology.
The bending process directly influences how effectively a heat pipe can function. By examining the physics behind heat transfer and the materials used in heat pipe design, we can appreciate how bending techniques optimize performance. Those in research and industry alike will benefit from the insights offered here, which can pave the way for advanced applications and improved designs.
Key Concepts and Terminology
Definition of Key Terms
Understanding heat pipe bending requires familiarity with some essential terms:
- Heat Pipe: A device that efficiently transfers heat via phase changes of a working fluid within a sealed container.
- Bending Technique: Methods used to alter the shape of a heat pipe without compromising its heat transfer efficiency.
- Thermal Conductivity: A measure of a material's ability to conduct heat, critical in heat pipe applications.
Concepts Explored in the Article
This article will delve into several fundamental concepts:
- The principles governing heat transfer mechanics in bent heat pipes.
- The significance of material properties in relation to bending techniques.
- Challenges presented during bending and solutions to overcome them.
Findings and Discussion
Main Findings
The investigation into heat pipe bending has uncovered several noteworthy findings:
- Precision in the bending process can significantly enhance heat transfer efficiency.
- Incorrect bending may lead to stress fractures or diminished performance, underscoring the need for careful design.
- The choice of materials directly impacts the flexibility and durability of heat pipes when bent.
Potential Areas for Future Research
Future research could focus on:
- Developing new materials that offer better thermal properties and bendability.
- Exploring innovative bending techniques to improve efficiency.
- Investigating the environmental impacts of different materials and methods in heat pipe production and operation.
In summary, heat pipe bending combines intricate scientific principles with practical applications. The insights provided in this article aim to inform and inspire further advancements in this vital area of technology.
Prelude to Heat Pipe Technology
Heat pipe technology plays a crucial role in modern thermal management systems. This section introduces fundamental aspects that underpin the efficiency and effectiveness of heat pipes in various applications. Understanding these principles is vital not only for effective design but also for ensuring optimal performance across different industries, such as electronics cooling, aerospace engineering, and renewable energy systems.
Heat pipes are designed to transfer heat from one point to another with minimal temperature difference. They utilize the phase change of a working fluid, which allows for high thermal conductivity. The advantages of heat pipes include a lightweight structure, high thermal performance, and the capability to operate in diverse environmental conditions. Moreover, they require minimal maintenance once properly installed.
The exploration of heat pipe technology reveals its complex nature, combining principles from thermodynamics and fluid mechanics. Key considerations when employing heat pipes include orientation, effective heat transfer surface area, and the selection of a suitable working fluid. These factors collectively influence the overall performance and extract maximum efficiency.
Heat pipes represent a sophisticated solution for thermal management, enabling effective regulation of heat flow in energy-efficient and compact designs.
As industries increasingly demand solutions that conserve space while achieving high efficiency, understanding heat pipe technology becomes essential. Armed with knowledge of how these systems work and their evolution, professionals can make informed decisions about their applications and integration into existing systems.
Fundamental Principles of Heat Transfer
Understanding the fundamental principles of heat transfer is crucial in the context of heat pipe bending. These principles lay the groundwork for how heat is managed in various applications, making them pivotal for effective design and operations. In heat pipe technology, the efficiency of heat transfer directly impacts the performance and reliability of the system.
Bending processes involve intricate interactions between heat transfer phenomena. Efficiently managing these interactions ensures that the heat pipe operates optimally. As we delve into different modes of heat transfer and their implications, we recognize that clear knowledge leads to better design choices and ultimately superior technical outcomes.
Conduction, Convection, and Radiation
Conduction, convection, and radiation represent the three core mechanisms of heat transfer. Each mechanism plays its role in how heat is moved and utilized within a heat pipe.
- Conduction happens when heat flows through solid materials. It is a direct transfer of energy through molecular interactions. For heat pipes, selecting materials with high thermal conductivity is vital to enhance conduction. Common materials include copper and aluminum, known for their excellent conductive properties.
- Convection involves heat transfer through fluids (liquids and gases). In heat pipes, this may occur as the working fluid evaporates and condenses. The efficiency of convection is influenced by the flow velocity and the temperature difference. Proper design must ensure efficient vapor movement throughout the pipe.
- Radiation is the transfer of energy through electromagnetic waves. Although its contribution is less significant compared to conduction and convection in heat pipes, it cannot be ignored, especially in high-temperature applications where radiant heat exchange can occur.
"The interplay of conduction, convection, and radiation determines the overall thermal performance of heat transfer systems."
Understanding these mechanisms aids engineers and researchers in optimizing heat pipe designs, as well as improving strategies for bending processes.
Thermal Resistance and Load Analysis
Thermal resistance is another essential aspect of heat transfer in heat pipes. It quantifies how effectively heat flows through the system, influencing overall efficiency. The total thermal resistance comprises components such as conduction resistance, convective resistance, and any additional resistances due to the geometry of the heat pipe.
Load analysis refers to understanding the thermal loads that a heat pipe must handle under various operational conditions. Evaluating the thermal load helps determine specifications for the pipe's dimensions, angles, and materials. This analysis ensures that the heat pipe can accommodate the expected temperature changes without compromising performance.
Standards and methodologies for assessing thermal resistance and load are available and essential tools for engineers working on heat pipe bending. This knowledge helps in troubleshooting issues, as well as in designing more robust and durable heat transfer solutions in various applications.
Materials Used in Heat Pipe Bending
The selection of materials used in heat pipe bending is crucial for optimizing performance and ensuring the longevity of these systems. Heat pipes rely on the efficient transfer of thermal energy, making material choice a significant factor in their functionality. The right materials can enhance heat transfer rates, resistance to corrosion, and structural integrity under various operational conditions.
Commonly Used Materials
In the construction of heat pipes, several materials are frequently utilized due to their superior thermal properties and mechanical strength. Some of these materials include:
- Copper: This is one of the most common materials used in manufacturing heat pipes. Its excellent thermal conductivity ensures efficient heat transfer, making it ideal for various applications, particularly in electronics cooling.
- Aluminum: Aluminum is lighter than copper and also offers good thermal conductivity. It is often used in applications where weight reduction is essential, such as in aerospace engineering.
- Stainless Steel: While not as thermally conductive as copper or aluminum, stainless steel provides superior corrosion resistance. This makes it a suitable choice for heat pipes exposed to harsh environments.
- Graphite: Known for its thermal management capabilities, graphite is also explored as an alternative material in certain specialized applications. Its lightweight nature and ability to conduct heat efficiently make it an attractive option for advanced designs.
The choice of material directly impacts the heat pipe's operational efficiency and cost, driving further research into innovative materials.
Selection Criteria for Materials
When selecting materials for heat pipe bending, various criteria must be evaluated to ensure optimal performance. Key considerations include:
- Thermal Conductivity: Higher thermal conductivity materials reduce resistances to heat flow, thus enhancing the overall efficiency of the heat pipe. This is a primary factor in material selection.
- Mechanical Strength: The material must withstand mechanical stresses without deforming, especially during bending processes. It should retain its structural integrity under varying thermal loads.
- Corrosion Resistance: Given that heat pipes often operate in environments where they are exposed to corrosive substances, materials with high corrosion resistance are preferred. This is critical for maintaining longevity.
- Weight: In applications such as aerospace, minimizing weight is as important as optimizing thermal efficiency. The selection process must consider both the weight and the performance capabilities of the material.
- Cost and Availability: The economic aspect is also fundamental. High-cost materials might provide superior performance but could limit the feasibility of using heat pipes in broader applications. Therefore, a balance between performance and cost is necessary.
Choosing the right materials for heat pipe bending is not just about performance; it also determines the practicality and sustainability of the application itself.
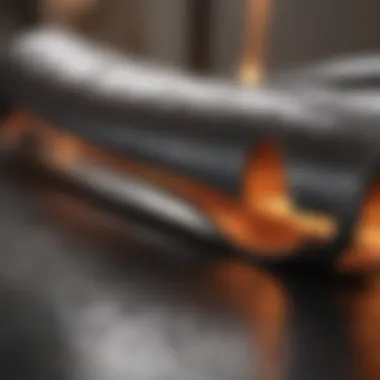
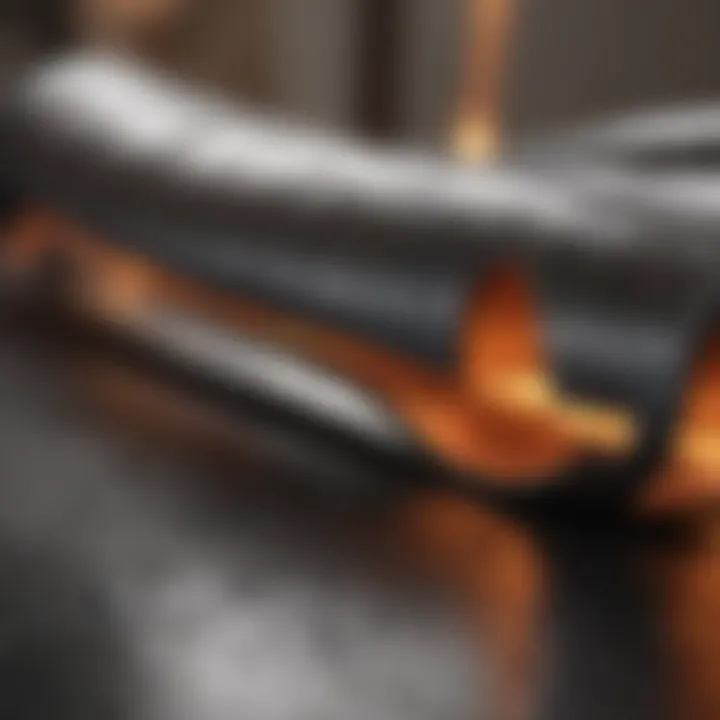
By understanding the properties and implications of various materials, engineers and designers can better optimize heat pipe bending techniques and ensure the reliability of heat transfer systems.
Heat Pipe Bending Techniques
Heat pipe bending is a critical aspect of heat pipe technology. It affects performance, reliability, and integration in various applications. Understanding the techniques associated with bending is essential for optimizing performance. Different bending methods influence the efficiency of heat transfer, which is the core function of heat pipes. Additionally, the choice between manual and automated processes can dictate the overall productivity and precision of the bending operation, making it a subject of significant interest.
Manual vs. Automated Bending
Manual bending of heat pipes involves skilled technicians applying their knowledge and experience to shape the pipes. This process allows for a high degree of customization. It is particularly useful for unique or complex designs. However, it can introduce variability and is time-consuming. Technicians must be well-trained to maintain consistency and quality.
On the other hand, automated bending techniques employ machinery for shaping heat pipes. This method can ensure more uniform results and higher efficiency. Automation significantly reduces labor costs and speeds up production. It is suited for high-volume manufacturing, where precision is non-negotiable. However, the initial setup costs for automated systems can be high. Thus, businesses must consider the scale and nature of their projects when choosing between manual and automated processes.
Key Considerations:
- Skill Level: Manual requires high proficiency.
- Consistency: Automated approaches yield uniform results.
- Cost: Upfront investments differ greatly.
- Flexibility: Manual allows for quicker adjustments.
Heat and Cold Bending Methods
The methods of bending heat pipes can be broadly classified into heat bending and cold bending. Heat bending involves applying heat to soften the material before it is shaped. This technique reduces the risk of cracking or damaging the pipe during the bending process. It is advantageous for particular materials and designs, allowing for smooth curves without compromising structural integrity.
In contrast, cold bending occurs at ambient temperatures without any heating. This process is typically quicker and cheaper than heat bending. However, it may lead to increased risk of material failure if not executed properly. Cold bending can be applied when the pipe material has sufficient ductility to withstand the stress of bending. Understanding the properties of the material is crucial for selecting the appropriate method.
"Selecting the right bending technique based on the application and materials is vital to maintaining the performance and reliability of heat pipes."
Each method has its benefits:
- Heat Bending:
- Cold Bending:
- Reduces risk of cracking.
- Useful for complex shapes.
- Faster and more cost-effective.
- Suitable for ductile materials.
In summary, mastering heat pipe bending techniques is essential for ensuring efficiency and reliability in applications. Proper understanding leads to better design choices and ultimately contributes to the success of projects involving heat pipes.
Design Considerations in Heat Pipe Bending
Design considerations in heat pipe bending are crucial for optimizing system performance and ensuring long-term reliability. Effective bending techniques greatly influence heat transfer efficiency. Several specific elements must be addressed in the design process. Attention to these aspects can yield significant benefits.
Geometric Layout and Constraints
Understanding geometric layout is vital in heat pipe systems. The design must accommodate the space within which the heat pipes will operate. Their placement can impact the heat transfer characteristics substantially. Crucial metrics include radius of curvature and bend angle, which dictate the heat pipe’s flow dynamics.
Several constraints can emerge. For example:
- Space Limitations: Tight configurations may require more intricate bending techniques.
- Component Interference: Adjacent components might impede the optimal layout of heat pipes.
- Thermal Expansion: Different materials expand at different rates. Designers must account for this to avoid stress and potential failure.
Additionally, the effectiveness of thermal coupling between components can be significantly influenced by the geometry of the heat pipe. Optimizing this layout can enhance thermal performance.
Mechanical Strength and Durability
Mechanical strength and durability should never be underestimated. The integrity of heat pipes is paramount since they often serve critical applications. Bending introduces stress points that can lead to fatigue and failure over time. Understanding the mechanics at play is vital for long-lasting performance.
Key factors include:
- Material Selection: High-quality materials can withstand the demands of bending without losing structural integrity.
- Bend Radius: A tighter bend increases the chance of creasing, which can compromise the heat pipe’s lifespan.
- Fatigue Resistance: Continuous operation under varying temperatures can lead to material fatigue. Resistance to such conditions enhances durability.
Proper design mitigates risks related to mechanical failure, enhancing overall system reliability and efficiency.
In summary, when considering design aspects in heat pipe bending, one must explore both geometric layouts and mechanical attributes. These factors are interconnected and play an integral role in determining the effectiveness and longevity of heat pipe systems. By focusing on these considerations, practitioners can ensure optimized performance in diverse applications.
Challenges in Heat Pipe Bending
The process of bending heat pipes presents unique challenges that must be addressed to ensure both the efficiency and reliability of the final product. Understanding these challenges is crucial for those involved in the design and manufacturing of heat pipes. Proper handling of these issues can lead to improved performance, extended lifecycle, and optimized efficiency in heat transfer applications.
Heat Transfer Efficiency Issues
One of the foremost challenges in heat pipe bending is maintaining heat transfer efficiency. The efficiency of heat pipes largely depends on how effectively they can transfer heat from one end to another without significant losses. Bending can introduce structural alterations that may affect this efficiency.
Key factors that impact heat transfer during the bending process include:
- Changes in Geometry: When a heat pipe is bent, its internal structure changes. These changes can create points of thermal resistance, leading to reduced efficiency.
- Fluid Distribution: The working fluid must adequately fill the evaporator section to ensure effective heat transfer. Bending may cause uneven fluid distribution, which can hinder the vapor flow and consequently affect efficiency.
- Temperature Gradients: Bending can also lead to unintended temperature gradients along the length of the heat pipe. These gradients can result in localized overheating or cooling, impacting overall thermal performance.
To mitigate these issues, careful design considerations should be taken into account. This may include selecting appropriate bending techniques that minimize structural changes and preserving optimal flow characteristics.
Material Fatigue and Failure
Material fatigue is another significant challenge associated with heat pipe bending. The mechanical strength of the materials used can influence the durability and reliability of the bent heat pipe. This is particularly important in applications that endure high temperature and pressure changes.
There are several critical aspects to consider regarding material fatigue:
- Stress Concentration: The bending process can lead to localized stress areas. If the stresses exceed the material's yield strength, it may lead to deformation or failure.
- Cyclic Loading: Many heat pipe applications involve fluctuating operational conditions. This cyclic loading can exacerbate material fatigue, potentially leading to premature failure if not adequately accounted for.
- Material Selection: Choosing the right material is essential in preventing fatigue-related failures. Materials must be evaluated for their resistance to bending stresses and environmental conditions.
Research and innovative methods may provide solutions to address these challenges. Techniques such as advanced metallurgical treatments can enhance material performance, improving the likelihood of withstanding bending stresses over time. In summary, recognizing these challenges in heat pipe bending is foundational to developing effective strategies for their mitigation.
Applications of Heat Pipe Bending
Heat pipe bending technology plays a critical role in advancing various industries. This section discusses how bending techniques apply to specific scenarios, emphasizing their benefits, considerations, and relevance to today's engineering challenges.
Electronics Cooling Solutions
In the realm of electronics, efficient heat dissipation is paramount. Heat pipes are often used in devices such as computers and high-performance graphic cards. Bending techniques allow heat pipes to be shaped into efficient, space-saving forms that fit within compact hardware designs.
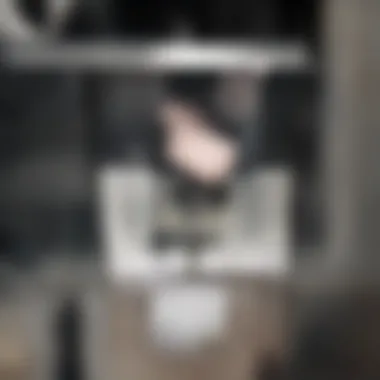
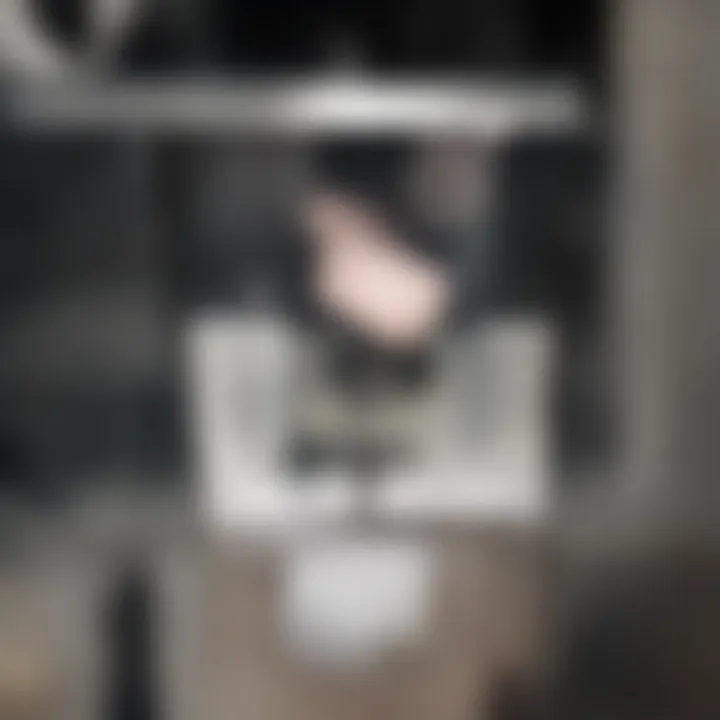
- Key Benefits:
- Enhanced thermal performance through optimized design.
- Ability to direct heat away from critical components effectively.
- Flexible configurations enable integration into diverse electronic systems.
The design must ensure that the heat pipes maintain their functional integrity even when bent. Precision in bending and selection of materials are vital to avoid any compromise on the thermal performance of the pipe.
Renewable Energy Systems
As countries shift towards renewable energy sources, heat pipes are becoming increasingly important. Their applications in solar thermal systems exemplify this technology's benefits. In such systems, bent heat pipes facilitate effective heat transfer from solar collectors to storage units.
- Considerations for Application:
- Thermal efficiency must be maximized to ensure proper energy collection.
- Materials must withstand environmental exposure without degrading.
- Installation techniques need to account for the pipe's orientation and angle to ensure optimal performance.
Bending enables heat pipes to be adapted to various configurations, ensuring they can function efficiently in a range of circumstances. This adaptability is essential for maximizing the effectiveness of renewable energy systems.
Aerospace Engineering
In aerospace engineering, weight and space restrictions drive innovative designs. Heat pipe bending technology meets these challenges by allowing for compact heat management solutions in spacecraft and aircraft.
- Advantages in Aerospace Applications:
- Reduction in weight as opposed to traditional cooling systems, therefore improving fuel efficiency.
- Capability to fit into complex geometries found in modern aerospace designs.
- Enhanced reliability due to reduced components and connections.
The bending of heat pipes in aerospace applications requires rigorous testing to ensure they can withstand extreme conditions.
"The integration of advanced bending techniques in heat pipes is revolutionizing cooling solutions in the aerospace sector."
By leveraging these techniques, engineers can devise solutions that are not only functional but also highly efficient, advancing aerospace technology.
Performance Evaluation of Bending Techniques
Performance evaluation of bending techniques is essential in understanding how well the heat pipes function in various applications. Assessing these techniques ensures that they meet the required standards and deliver efficient thermal performance. Several factors contribute to a successful evaluation, including the assessment of thermal performance, mechanical integrity, and manufacturing consistency. Improved performance can lead to better heat dissipation outcomes, which is particularly important in electronics and renewable energy systems.
Testing Methods and Standards
To accurately evaluate bending techniques, testing methods and standards are crucial. These methods can be categorized into both laboratory tests and in-field assessments. In laboratory settings, thermal conductivity tests and pressure drop measurements provide insights into how bending affects the functionality of heat pipes. Common standards such as ASTM E1952 or ISO 8302 guide the testing processes, ensuring uniformity and reliability of results.
Some widely used testing techniques include:
- Thermal Performance Testing: In this method, a heat source is applied, and the temperature response is measured. This helps determine the efficiency of heat transfer within the bent sections of a heat pipe.
- Mechanical Testing: These tests assess the mechanical strength and deformation of the heat pipes post-bending. They help identify any weaknesses caused by the bending process.
- Load Testing: Assessing how well the pipe handles thermal and mechanical loads during operation provides valuable insights into its durability.
Standardized metrics enable engineers to compare the performance of different bending techniques directly, enhancing decision-making in design and manufacturing processes.
Data Analysis and Interpretation
Once the testing methods are applied, analyzing the resulting data becomes a significant task. Effective data analysis requires a clear framework for interpretation, focusing on key performance indicators such as heat transfer efficiency and structural integrity.
Graphs and charts often present data visually, making trends easier to spot. Statistical methods can help validate the results. Some analytical tools and software facilitate the interpretation of large datasets, leading to deeper insights into performance factors. By identifying patterns in the data, professionals can make informed improvements to bending techniques.
In summary, the evaluation of heat pipe bending techniques incorporates rigorous testing methods and robust data analysis. The ultimate goal is to achieve optimal heat transfer capabilities while maintaining mechanical integrity. These evaluations lead to innovations in application designs and methodologies that benefit various industries.
"Understanding the performance of heat pipe bending techniques is paramount for optimizing their functionality and reliability in crucial applications."
Advancements in Heat Pipe Design
The field of heat pipe technology is continuously evolving, driven by advancements in materials and design practices. Heat pipes have become indispensable in various industries, from electronics to aerospace. The importance of advancements in heat pipe design lies in their potential to optimize performance, enhance thermal efficiency, and reduce costs. Improved heat pipe systems can lead to significant energy savings, crucial in today’s sustainability-focused marketplace.
One key element of advancements is the innovation in material science. The selection of materials used in heat pipe construction has a direct impact on their thermal conductivity, structural integrity, and overall functionality. Moreover, designing heat pipes that can operate effectively under various environmental conditions broadens their applicability and enhances reliability.
Benefits of Effective Heat Pipe Designs:
- Improved thermal performance reduces heat transfer limitations.
- Customized designs enhance adaptability for specific applications.
- Altogether, energy efficiency is increased, benefitting operational costs.
Innovations in Material Science
Innovations in material science are reshaping the landscape of heat pipe design. Researchers are exploring advanced materials, including composites and novel alloys, to create heat pipes capable of withstanding higher temperatures and pressures. The emergence of nanomaterials demonstrates promising results, notably enhancing the thermal conductivity substantially. Such innovations allow for lighter and more compact designs without compromising performance.
For example, materials like carbon nanotubes and graphene are being studied for their unique thermal properties. These materials may enable the creation of heat pipes that are both high-performing and energy-efficient. This is particularly relevant in applications like electronics cooling, where space and weight savings are paramount. The benefits of such advancements include:
- Increased heat transfer efficiency
- Enhanced durability and lifespan
- Adaptability to diverse environments
Computational Modeling Techniques
The integration of computational modeling techniques into heat pipe design has significantly advanced the field. By using simulation tools, designers can predict thermal performance and optimize geometric parameters before physical prototypes are built. This not only saves time but also allows for iterative improvement in design.
Numerical methods, such as Computational Fluid Dynamics (CFD) and Finite Element Analysis (FEA), have become critical in understanding the fluid dynamics and thermal behaviors within heat pipes. They help engineers identify potential issues early in the design process, ensuring that the final product meets performance standards.
"The use of computational modeling techniques enables engineers to push the boundaries of what is possible in heat pipe design, optimizing designs effectively before manufacturing."
Furthermore, these techniques permit the assessment of various operating conditions and their impact on efficiency. As a result, manufacturers can adapt designs to meet specific demands in different applications. The implementation of computational modeling provides:
- Faster and more accurate design iterations
- Reduced prototype costs and time
- Enhanced ability to tailor heat pipes for unique applications
Future Directions in Research
The future of heat pipe bending technology presents a landscape rich with potential advancements. Research in this field is pivotal, as it enables the enhancement of existing applications and the exploration of new ones. By focusing on innovations, stakeholders can optimize heat transfer efficiency, reduce costs, and improve material capabilities. Among the essential areas to explore are the integration of smart materials, the role of computational modeling in design processes, and the impact of interdisciplinary strategies.
Emerging Trends in Applications
Recent studies highlight significant trends regarding the applications of heat pipe bending technology. Industries such as electronics, aerospace, and renewable energy systems are continually seeking more effective cooling solutions. For instance:
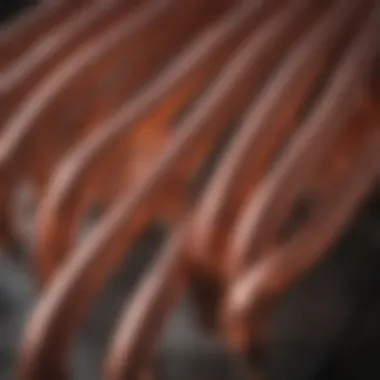
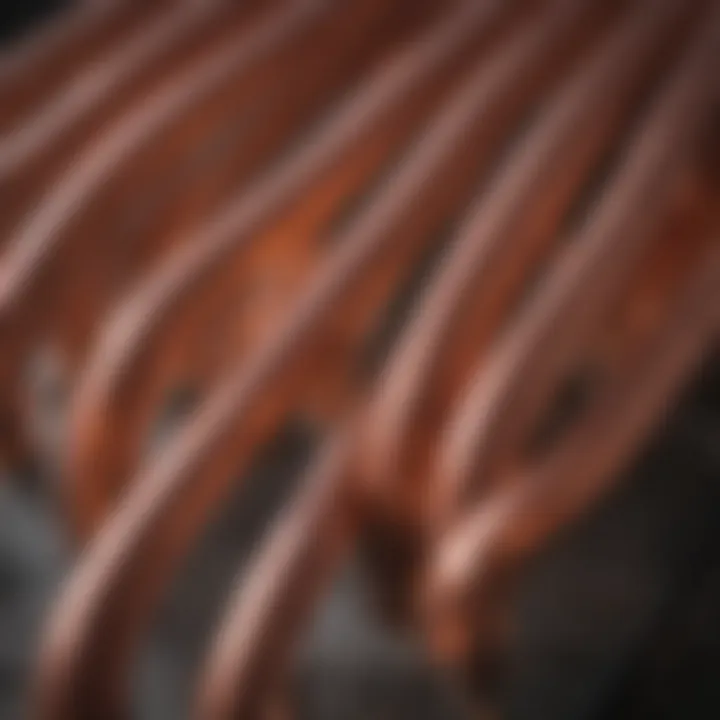
- Miniaturization of components in electronics requires advanced cooling methods to dissipate heat effectively. Developers are now looking into compact heat pipes that integrate seamlessly within small devices.
- In aerospace, the demand for lightweight and efficient heat management systems is increasing. Innovations in bending techniques can lead to designs that reduce weight without sacrificing performance.
- The push for sustainability in energy systems has directed research towards heat pipes that operate at higher efficiencies utilizing eco-friendly materials.
These trends indicate a strong direction toward adaptability and efficiency that can redefine operational standards across various sectors.
Interdisciplinary Approaches
Adopting interdisciplinary approaches can greatly enhance the field of heat pipe bending research. Collaboration between material scientists, engineers, and thermodynamics experts may yield significant breakthroughs. Key considerations for this holistic approach include:
- Material Innovation: By combining insights from different fields, researchers can develop new alloys or composites that withstand higher pressures and temperatures, improving the reliability and lifespan of heat pipes.
- Computational Techniques: Utilizing software tools for modeling and simulations can help predict thermal behavior and validate designs before physical production. This reduces testing time and costs.
- Integration of Smart Technology: As electronics become smarter, integrating sensors within heat pipes for real-time monitoring can optimize performance dynamically, showcasing a move towards more intelligent systems.
Research in these areas not only opens new avenues for heat pipe bending applications but also addresses the growing demand for reliable, efficient, and eco-friendly heat management solutions.
"The convergence of disciplines in research can lead to leaps in innovation that single-field studies may not achieve."
Understanding these emerging trends and interdisciplinary methods can provide the foundation for evolving the discourse surrounding heat pipe bending, ensuring that this technology continues to meet the demands of future developments.
Case Studies in Heat Pipe Bending
Case studies serve as invaluable resources in understanding the effectiveness and applicability of heat pipe bending technology. Specific examples illustrate the innovative use of heat pipes across various fields. They provide context and highlight real-world impacts, offering lessons that can inform future projects. The discussion of success stories and lessons learned paints a clearer picture of best practices and potential pitfalls.
Through detailed case analyses, stakeholders can grasp critical trends and techniques that shape the industry. This section digs into notable case studies that both exemplify the success of heat pipe bending and identify challenges encountered along the way. By examining these instances, readers will appreciate the broader implications of this technology.
Success Stories
Several notable projects demonstrate how heat pipe bending has achieved efficiency and performance enhancements. For example, a recent project in aerospace engineering involved the integration of heat pipes into aircraft wing designs. The innovative bending techniques used in this case allowed for significant weight reduction without compromising thermal performance. This optimization leads to lower fuel consumption and, ultimately, reduced operational costs.
Another significant success story involves the use of heat pipes in electronics cooling systems. A tech company implemented heat pipes in their server farms. The precision bending allowed for tailored designs that improved airflow and dissipated heat effectively. Thus, energy efficiency improved, which is crucial in today's competitive tech environment.
These real-world examples are compelling. They show that strategic application of heat pipe bending can yield tangible benefits.
Lessons Learned
While success stories provide inspiration, they also serve as a reminder of the lessons learned in implementing heat pipe bending. One crucial takeaway centers on the importance of accurate thermal modeling prior to bending. In one case study, engineers overlooked precise load analysis, leading to unforeseen material fatigue. This mistake necessitated costly redesigns and delays.
Another lesson emphasizes the need for material selection that aligns with design constraints. In a renewable energy project, poor material choice resulted in limited thermal efficiency. Adapting materials to the specific application context is vital.
In summary, case studies reveal that the implementation of heat pipe bending requires careful planning and execution. They illustrate potential challenges while celebrating successful outcomes. The insights garnered from these studies build a knowledge base for future endeavors in heat pipe technology.
Comparative Analysis with Traditional Cooling Systems
In the realm of thermal management solutions, heat pipe technology stands out against traditional cooling systems such as air cooling, liquid cooling, and even more complex setups like thermoelectric coolers. Understanding the distinctions between these systems is pivotal for researchers and industry professionals. This section presents essential elements, benefits, and considerations in drawing a comparative analysis, emphasizing the relevance of heat pipe bending as an advanced solution.
Efficiency Metrics
The efficiency of cooling systems is a vital metric that affects performance and cost-effectiveness. Heat pipes are often rated on their thermal conductivity and heat transfer coefficient. When compared with air cooling systems, heat pipes generally achieve significantly higher thermal conductance. This is because their operation relies on the phase change of the working fluid, allowing for effective heat transport despite minimal temperature gradients.
In contrast, traditional air coolers are limited by the ambient conditions and often require larger surface areas to dissipate heat effectively. The thermal resistance in these systems can be substantial, especially at higher power densities. To illustrate:
- Heat Pipes: High efficiency, compact size, suitable for high heat flux.
- Air Coolers: Lower efficiency at high loads, bulky designs, influenced by environmental conditions.
Recent studies indicate that systems employing heat pipe technology can improve energy efficiency by up to 30% compared to conventional methods in electronics cooling. This substantial performance enhancement underlines the necessity to include heat pipe analysis in thermal management discussions.
Cost-Benefit Considerations
When assessing the cost-effectiveness of cooling systems, multiple factors must be considered. Initial installation costs, operational efficiency, maintenance, and lifespan of the system all play critical roles. Heat pipes typically involve a higher upfront investment due to the complexity involved in their design and manufacturing. However, their long-term benefits often outweigh these initial costs.
- Reduced Operating Costs: Heat pipes consume no power during operation, leading to savings in energy costs. This is particularly important in continuous operation scenarios, such as in server farms or large electronic systems.
- Longevity: Heat pipes often have longer lifespans than traditional cooling technologies. With fewer moving parts and no need for pumps, they demonstrate enhanced reliability.
- Space Efficiency: The compact nature of heat pipes allows for reduced footprints in designs, potentially lowering material costs in the overall system architecture.
The balance between initial cost and operational savings necessitates a thorough cost-benefit analysis for stakeholders. Implementing heat pipe technology may present a higher initial economic barrier, but the lifecycle benefits frequently justify the investment, demonstrating a larger return on investment for technology-driven applications.
"Heat pipes offer a unique fusion of efficiency and longevity that traditional systems often fail to achieve, making them a worthy consideration in modern thermal management."
The evolution of available cooling technologies continues to influence best practices in thermal management. Heat pipe bending techniques have emerged as a strategic solution, enhancing the operational efficiency and flexibility of thermal systems across various industries, thus warranting deeper investigation in comparative studies.
Regulatory and Safety Standards
Regulatory and safety standards play a pivotal role in the domain of heat pipe bending technology. They establish a framework that ensures the safe and efficient operation of heat pipes across various industries. Adherence to these standards promotes not only the physical safety of personnel but also protects the equipment and environment, thereby fostering a culture of excellence in engineering practices.
Industry Guidelines
The industry guidelines regarding heat pipe bending are designed to ensure consistency, reliability, and safety. These guidelines are often established by organizations such as the American Society of Mechanical Engineers (ASME) or international standards bodies like the International Organization for Standardization (ISO). They cover a myriad of aspects, including:
- Material Specifications: Recommendations on the materials that should be used in the fabrication of heat pipes to ensure optimal heat transfer efficiency and mechanical strength.
- Bending Techniques: Instructions on the best practices for bending heat pipes, including manual and automated methods. This ensures that the structural integrity of the pipe is not compromised during the bending process.
- Quality Assurance: Standards concerning the testing and quality assessment of bent heat pipes, ensuring they meet performance and safety criteria before deployment.
Proper implementation of these guidelines can greatly enhance the reliability of heat pipes, making them suitable for demanding applications like electronics cooling or aerospace engineering.
Environmental Impacts
The environmental impacts of heat pipe bending cannot be overlooked. Regulatory standards dictate that processes involved in heat pipe manufacture and bending must minimize waste and reduce emissions.
- Energy Efficiency: It is essential to use methods that lower energy consumption during heat pipe production. Energy-efficient practices not only reduce operational costs but also lessens the carbon footprint.
- Waste Management: Guidelines promote the responsible disposal of materials and the use of recyclable materials in the manufacturing process.
- Sustainability Practices: Encouraging the use of sustainable resources and materials can contribute positively to the environment. This includes focusing on life-cycle assessments during the design phase, ensuring that every step, from material selection to end-of-life recycling, is optimized for minimal environmental impact.
In summary, regulatory and safety standards in heat pipe bending are integral to engineering practices. They influence the design, manufacture, and application of heat pipes, shaping a future where heat transfer technologies function safely and sustainably.
Culmination
The examination of heat pipe bending offers a crucial perspective on optimizing thermal management in various applications. This article has laid out several important elements associated with heat pipe technology and specifically its bending techniques. Understanding these aspects can lead to improved performance and reliability in systems that rely on effective heat transfer.
Summary of Key Insights
Throughout this article, we explored the fundamental principles of heat pipe technology, emphasizing their functionality and the various materials utilized. We also examined the intricate techniques of bending and the various design considerations that engineers must keep in mind. Key insights include:
- Precision in Bending Techniques: Achieving optimal bend angles is essential for maintaining heat transfer efficiency. The design and execution of bends must be done carefully to avoid compromising the integrity of the heat pipe.
- Material Selection: The choice of materials, such as copper or aluminum, affects performance factors like thermal conductivity and durability. This selection process must align with application-specific demands.
- Performance Evaluation: Regular testing and adherence to industry standards are necessary to ensure that the bent heat pipes operate within expected parameters.
These elements significantly contribute to enhancing the efficacy of heat pipes in their respective applications.
Final Thoughts on the Future of Heat Pipe Bending
As technology continues to advance, the future of heat pipe bending holds promise. Emerging methods and materials are likely to refine the capabilities of heat pipes. Innovations such as the use of nanomaterials or advanced composite materials could lead to increased efficiency and broader applications. Further interdisciplinary research can facilitate deeper insights into thermal behavior and structural integrity of heat pipes, promoting better designs and practices.