The Assembly Line of Production: In-Depth Analysis
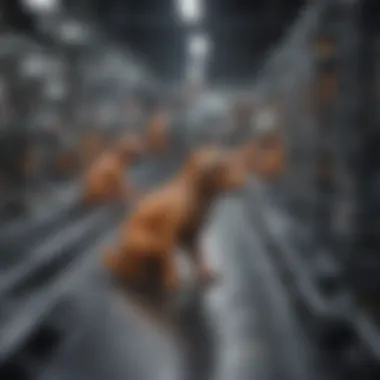
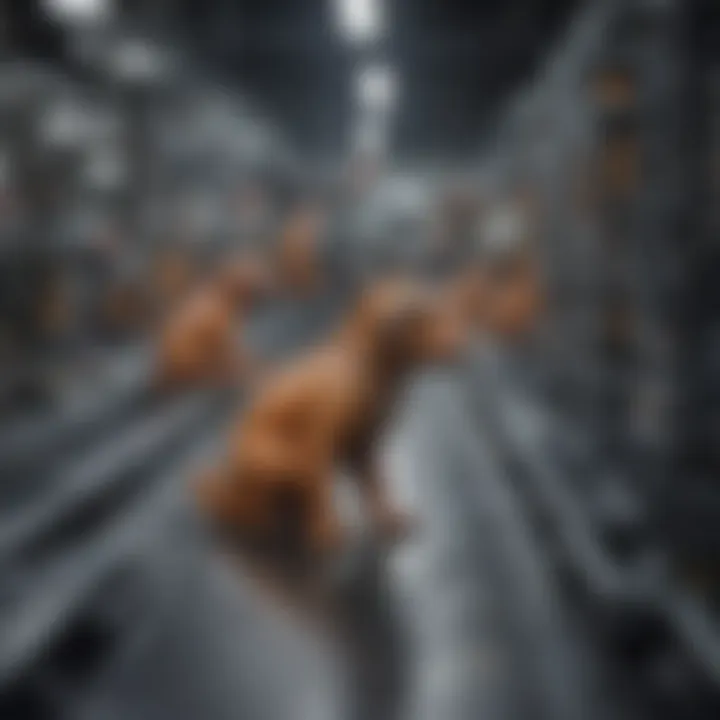
Intro
In a world where speed and efficiency reign supreme, the assembly line of production stands as a beacon of industrial advancement. This method has transformed how products are created, forever altering the landscape of manufacturing. From tinkerers in the early days to modern tech giants, the journey of the assembly line is fascinating and layered with lessons that resonate even today. In this article, we aim to unravel its intricacies—taking a look at its historical roots, the mechanics behind its functionality, and the socio-economic ripple effects that stem from its implementation.
Understanding the assembly line is not just about grasping its operational framework; it's about recognizing its significance in shaping economies, industries, and workforces across the globe. The assembly line does more than just churn out items; it encapsulates the evolution of production methods and tackles contemporary challenges faced by various sectors.
Through a blend of historical analysis, detailed case studies, and insights into technological advancements, we will dissect the assembly line’s dynamics. We’ll also look at how modern methodologies like automation and lean manufacturing influence production efficiency today. This also includes an exploration of future paths that might lead to even greater advancements in the field.
As we embark on this exploration, we invite students, researchers, and industry professionals alike to dive deeper into the complexities that underpin assembly line production. Let's peel back the layers and discover the mechanics that keep the wheels of industry turning.
Prelude to the Assembly Line Concept
The assembly line represents a significant evolution in production methods, embodying speed and efficiency in manufacturing. This section aims to cut through the clutter and lay bare the crucial role of assembly lines in modern industry. From producing automobiles to electronic devices, assembly lines have created a framework that not only bolsters output but also revolutionizes how we think about contributing skills in labor. Understanding this concept is essential not just for comprehending production mechanics, but also for scrutinizing the societal shifts and economic logic that anchor them.
Definition and Context
To describe an assembly line is to speak of a systematized approach to manufacturing, where various tasks happen in sequential steps to produce a consistent product. Think of it like a well-oiled machine – parts and workers all working in concert to achieve a shared goal. The roots of this approach spring from the desire for efficiency. A solid grasp of this concept necessitates recognizing its backbone: division of labor and standardized tasks. In essence, this model empowers workers to specialize in specific operations, which hones skills and leads to faster production times.
Historical Background
The history of assembly lines is rich and layered, reflecting changes in society and technology. Examining this backdrop helps unravel the motivations and innovations that shaped the production landscape we see today.
Early Manufacturing Techniques
From the get-go, early manufacturing was a far cry from the sleek, efficient systems we see today. Artisans and craftsmen would often single-handedly create items, leading to intricate but painstakingly slow production methods. This traditional approach placed emphasis on individual artistry, but it came with limitations – high costs and long lead times drove home the need for change. A noteworthy characteristic of these early techniques was their reliance on hand tools and manual labor, making them a popular but burdensome choice in sparse conditions during that period. Key strengths included the ability to customize products but with clear downsides like lack of consistency and scalability. So, it was clear that a pivot was necessary as industry grew.
Henry Ford and Mass Production
Fast forward to the 20th century, where Henry Ford redefined the game with his mass production techniques. By integrating the assembly line into automobile manufacturing, he slashed production times drastically. Ford’s breakthrough was the moving assembly line, enabling workers to focus on specific tasks as vehicles moved along a conveyor belt. One of the defining features of this system is its reliance on timed motion, which is a key reason this method became so widely adopted. The value was evident: cheaper prices for cars meant more people could afford them, boosting the economy. However, the mechanical nature of the system led to a level of monotony for workers which raised concerns about job satisfaction and morale.
Evolution Through the Industrial Revolution
The Industrial Revolution served as the catalyst for an explosive transformation of manufacturing techniques. This era, marked by innovations in machinery and technology, saw the transition from hand production to machine-based labor. Assembly lines emerged not just in factories, but also came to life in various industries—from textiles to food processing. What made this evolution pivotal was its acceleration in production capabilities while lowering costs—it was an attractive proposition for manufacturers. Yet, the increased reliance on machinery frequently highlighted challenges related to worker displacement and the often dangerous working conditions. Though it got results, trade-offs in human costs were just as palpable.
As we move into further sections, the detailed exploration of assembly lines will guide us through their operational intricacies, technological advancements, and the expansive influence on industries worldwide.
"Efficiency is doing things right; effectiveness is doing the right things." - Peter Drucker
Understanding the past is imperative for grasping the nuances of assembly line structures today. It's not just about assembling products; it's about assembling ideas, practices, and ultimately, the future of how we produce.
The Mechanics of Assembly Line Operations
Understanding the mechanics of assembly line operations is like opening a door to the heart of production efficiency. It’s vital in today’s fast-paced world where speed, precision, and flexibility matter immensely. An assembly line's mechanics dictate how products move through various stages of production, ultimately influencing cost, quality, and delivery timelines. Operating an effective assembly line means grasping not just the flow of materials but also the interplay between human labor and machinery, ensuring every cog in the wheel turns smoothly.
Core Principles of Line Production
At the core of line production are several principles that guide its framework:
- Division of Labor: Each worker or machine performs a specific task, minimizing the time spent switching tasks.
- Continuous Flow: Products move smoothly from one stage to the next, reducing bottlenecks.
- Standardization: Every part and process is uniform, promoting consistency and quality control.
Grasping these principles is essential for anyone intending to implement or understand assembly line dynamics, as they collectively enhance productivity while reducing waste.
Types of Assembly Lines
Different assembly lines cater to the varied needs of production processes. Each type serves a unique purpose, addressing specific operational goals. Here’s a closer look:
Straight Line Assembly
A straight line assembly is the textbook version of assembly line production. In this setup, products follow a linear path through a series of stations. What makes this model stand out is its simplicity. It’s an accessible choice because it requires less space and management.
One unique feature is its efficiency in high-volume production scenarios. When demand is consistent, this approach ensures that each station can perform its task independently but in unison with the others.
The disadvantage, however, lies in its inflexibility. If a design change is needed or there’s a shift in product variation, adjustments can be tedious and time-consuming.
U-Shape Assembly
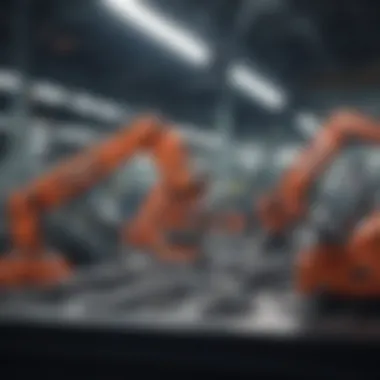
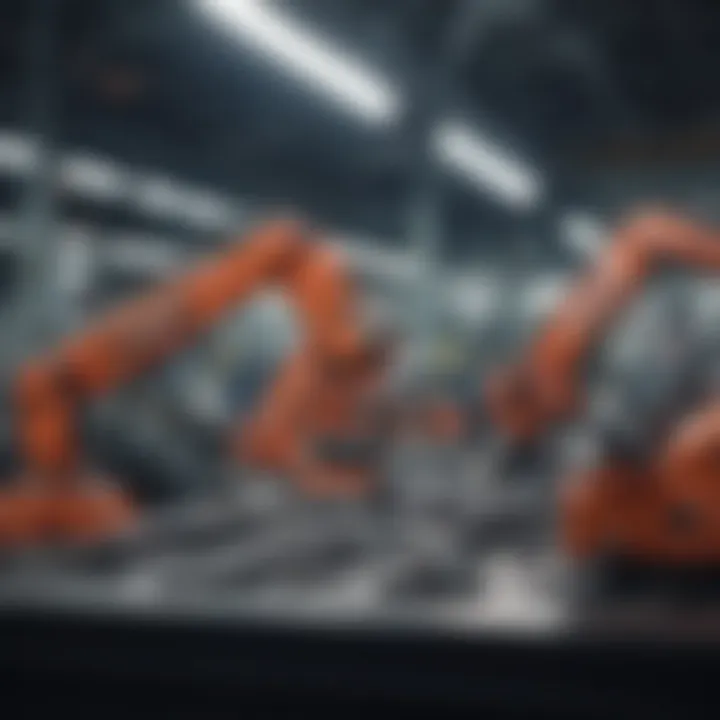
A U-shape assembly line brings a twist to the conventional straight line approach. The configuration allows for workers to operate on both sides of the assembly line, creating a more compact setup. This space-efficient design supports easier communication among workers, which can lead to improved teamwork and quicker problem-solving.
Another key characteristic is its flexibility. Workers can easily adapt to different tasks as needed, which is a boon for companies facing fluctuating demand or varying product lines. However, a challenge with this model can be balancing the workload among workers; if one side is busier than the other, it can lead to discrepancies in production output.
Modular Assembly Systems
Modular assembly systems represent a step up in customization for production needs. These systems utilize interchangeable modules that can be reconfigured based on specific product requirements. This adaptability is what makes them a popular choice in industries needing to pivot quickly to new products or specifications.
One unique feature is that these systems can grow with the business. Adding additional modules allows a manufacturer to scale operations without a complete overhaul of their existing setup. Yet, in terms of drawbacks, modular systems can require more initial investment and more complex planning, potentially posing challenges for smaller outfits.
By delving into these various types of assembly lines, a clearer picture emerges of how different setups cater to diverse manufacturing processes. Each system has its unique advantages and considerations, which can make or break its success in a competitive environment.
Technological Innovations in Assembly Lines
Technological innovations are reshaping the panorama of assembly line production, driving efficiency and precision to new heights. In an age where flexibility and cost-effectiveness are imperative, exploring these advancements is critical for any industry looking to stay ahead of the curve. The integration of technology within the production framework not only enhances operational capabilities but also paves the way for greater adaptability to market demands and consumer preferences.
Automation and Robotics
Automation and robotics stand as cornerstone elements in the modern assembly line. They allow for the seamless execution of repetitive tasks with remarkable accuracy and speed. By reducing human error, these technologies significantly contribute to the overall efficiency of production processes. Moreover, robots can operate in hazardous environments without the risk of injury, presenting a safer solution for manufacturers.
Companies like KUKA and ABB are leading the charge in this field, developing robots that can work collaboratively with human operators. This synergy results in a notable augmentation of productivity. By automating tedious and mundane tasks, workers can focus on more complex issues that require human ingenuity.
But these innovations come with their own set of challenges. For instance, the initial investment in automation equipment can be steep. Smaller manufacturers may find it difficult to allocate enough capital upfront, raising important questions about the return on investment. Yet, many argue that the long-term gains, in terms of productivity and reduced operational costs, often justify the expense.
Advanced Manufacturing Technologies
Computer Numerical Control (CNC)
Computer Numerical Control, or CNC, represents another leap forward in assembly line technology. At its core, CNC allows for precise control of machinery through computer software, thus enhancing the production of complex parts with extreme accuracy. This high level of precision is key for industries like aerospace or automotive, where even a minor deviation can have significant consequences.
A fundamental characteristic of CNC technology is its ability to consistently replicate parts without deviation. The machines can run 24/7, ensuring uninterrupted production. This leads to lower labor costs and less waste, as the need for manual adjustments is drastically reduced.
However, CNC machining comes with its share of challenges. As these machines become more advanced, the need for skilled operators who can manage this technology also rises. Training can be time-consuming and expensive, which may deter some manufacturers from adopting CNC systems. Yet, those who embrace it typically find their productivity significantly boosted.
Internet of Things (IoT) Integration
The Internet of Things (IoT) integration in assembly lines introduces a new layer of connectivity. Devices linked through IoT can communicate and share information instantaneously, allowing for real-time monitoring and analysis. This is especially beneficial in predicting maintenance needs and minimizing downtime, crucial factors in maintaining a smooth production flow.
A key feature of IoT is its ability to gather vast amounts of data from numerous points along the production line. This data can be analyzed to identify inefficiencies, optimize workflows, and enhance overall productivity. The interconnectedness fosters a more agile production environment that can adapt to sudden market changes.
Yet, with great power comes great responsibility. The reliance on networked devices raises concerns about cybersecurity threats, as vulnerabilities could potentially disrupt operations. Therefore, while IoT presents immense benefits, manufacturers must also consider risk management strategies to mitigate these threats.
Supply Chain Management Systems
Effective supply chain management systems are vital for any assembly line, serving as the backbone for production efficiency. These systems help orchestrate the flow of materials, ensuring that every part arrives on time and in the right conditions. Advanced software solutions can track inventory levels, forecast demand, and manage orders seamlessly.
A notable characteristic of modern supply chain systems is their capability to provide end-to-end visibility. This means that manufacturers can monitor every aspect of the supply chain, from raw materials to customer delivery. Such insight enables businesses to make informed decisions quickly, reducing the risk of shortages and excess inventory.
However, these systems can be complex and require significant training for staff to use effectively. Additionally, integration with existing systems isn't always straightforward and may require dedicated resources to ensure seamless operation. Nonetheless, when implemented effectively, these systems can dramatically improve coordination and responsiveness within manufacturing processes.
"In an ever-evolving industrial landscape, technology remains a key driver of efficiency and adaptability across assembly lines."
Case Studies in Assembly Line Implementation
The investigation of assembly line implementation through case studies reveals the practical applications of concepts discussed previously. These real-world examples provide insight into the effectiveness and adaptability of assembly line methods. Each industry has unique needs, yet the analytical frameworks remain relevant across distinct sectors. Examining successful implementations allows us to draw lessons and understand common challenges faced by industries.
Automotive Industry Success
The automotive sector stands as a lighthouse for the success of assembly line production. Companies like Toyota have pioneered lean manufacturing, perfecting the art of just-in-time production, which minimizes waste and maximizes efficiency. Toyota's approach integrates employee feedback into their processes, creating a culture of continuous improvement.
An illustrative example is the production of the Toyota Camry. The assembly line process involves various stages: stamping, welding, painting, and assembly. Each segment has its own team, and communication flows smoothly to ensure seamless transitions. The emphasis on quality at every stage leads to fewer defects and higher customer satisfaction. Moreover, the use of automation, combined with skilled labor, strikes a balance that enhances both productivity and product integrity.
"In the automotive industry, mastering the assembly line isn't just a strategy—it's a competitive edge that can dictate market share and brand loyalty."
Consumer Electronics Manufacturing
In the realm of consumer electronics, companies like Apple and Samsung leverage assembly line production to meet the demands of rapidly changing markets. The production of smartphones illustrates the complexities faced in this industry. Each device carries a multitude of components, from chips to screens, assembled at a breakneck pace to keep up with consumer demand.
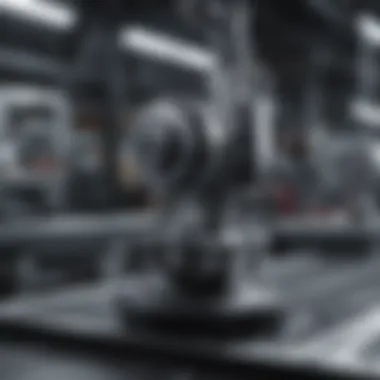
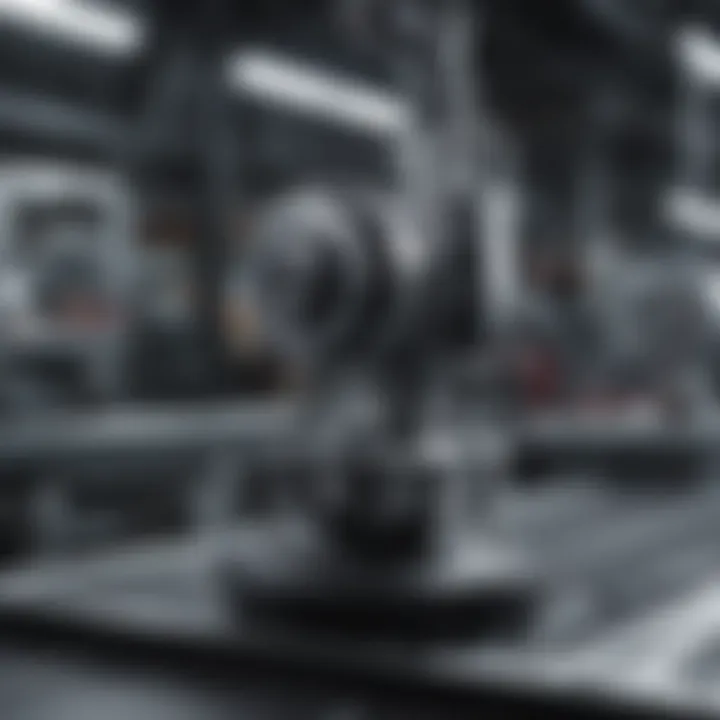
Apple, for instance, utilizes a highly synchronized assembly line approach. With factories optimized for efficiency, workers perform specific tasks on a rotating basis. This setup not only minimizes the physical strain on employees but also ensures that multiple perspectives contribute to quality control. A misaligned screen, for example, can be caught and corrected in real-time, preventing larger issues later on in the production cycle.
Pharmaceutical Production Efficiency
The pharmaceutical industry presents a compelling case for understanding the needs and nuances of assembly line production. Here, the stakes are exceptionally high, as inaccuracies can lead to health risks. Companies like Pfizer have implemented stringent protocols within their assembly lines to ensure the highest standards of quality and regulatory compliance.
For instance, during vaccine production, the assembly line includes rigorous testing stages that integrate both technology and human oversight. Automation assists in repetitive tasks, but the ultimate assurance of quality comes from skilled professionals who monitor every phase. The result is an assembly line that doesn’t just prioritize efficiency but also patient safety. The recent COVID-19 vaccine rollout was a testament to how adaptive assembly line methods can respond to urgent public health needs, achieving unprecedented results in record time.
In summation, the lessons from these industries are clear. Assembly line production has evolved into a sophisticated practice, suggesting both its advantages and limitations. Whether through advanced technologies or human insight, the challenges endured by these sectors offer critical reflections applicable to future implementations.
Challenges and Limitations of Assembly Line Production
In the realm of manufacturing, assembly line production stands out as a key technique for producing goods efficiently and systematically. However, like any approach, it comes with its own set of challenges and limitations that deserve a thorough examination. Understanding these factors not only sheds light on the operational intricacies of assembly lines but also highlights areas where improvements can be made to enhance productivity and workforce satisfaction.
Labor Issues and Workforce Dynamics
At the heart of assembly line production lies the workforce. The reliance on a large number of workers to carry out repetitive tasks can lead to several issues. Employees in such environments might experience job dissatisfaction, as the monotony of their tasks can diminish morale. When jobs become overly repetitive, it can create a disengaged workforce where employees feel they are just cogs in a machine, leading to higher turnover rates. Moreover, the physical demands of assembly line work can sometimes lead to workplace injuries, especially if ergonomic considerations are ignored.
Another element to consider is labor cost. As automation and advanced technologies gain a foothold in industries, the need for manual labor decreases. This shift raises concerns about what happens to workers displaced by machines. Retraining and reskilling initiatives become essential, but they also require significant investment on the part of companies. This presents a balancing act: companies want to streamline operations and reduce costs, but they must also address the human element.
Quality Control Concerns
The speed and efficiency of assembly lines often come at the cost of quality control. The nature of mass production can lead to oversight errors that might go unnoticed until they become costly issues. When a single flaw occurs in one step of the line, it can have a snowball effect, impacting the final product's reliability and customer satisfaction.
Furthermore, strict adherence to production quotas can pressure employees to rush their work, which inherently increases the likelihood of mistakes. Striking the right balance between efficiency and quality is crucial for businesses aiming to maintain their reputation in a competitive marketplace.
It’s important to implement robust quality assurance practices, and continuously refine them to ensure that defects are caught before products reach the consumer. This addresses both customer expectations and compliance with industry standards.
Flexibility and Adaptability in Production
One of the inherent limitations in traditional assembly lines is their lack of flexibility. As market demands shift swiftly—think changing consumer preferences or sudden supply chain issues—assembly lines can struggle to adjust. Modifying a production line setup can be a daunting task that takes time and resources, potentially leading to operational downtimes.
For instance, imagine a company that specializes in producing a specific model of a gadget. If consumer interest suddenly shifts to a different model, the existing assembly line setup may need substantial changes. This can involve everything from retraining workers to reconfiguring machinery, all of which can be both costly and time-consuming.
To combat this rigidity, companies are increasingly looking into modular assembly systems that can be reconfigured more swiftly to adapt to different products. Incorporating this level of adaptability seems to be a movement towards the future in production methodologies.
"In a world where change is the only constant, an adaptable assembly line could be the difference between thriving and merely surviving."
As we analyze these challenges, it becomes evident that addressing them is crucial not only for the efficiency of production systems but also for the well-being of the workforce involved. It underlines the need for a thoughtful approach that integrates technology and human factors into assembly line design and operation.
Comparative Analysis of Production Systems
Understanding the landscape of production systems offers a clear lens through which businesses can assess their operational efficiency and adaptability. Comparative analysis plays a critical role here, allowing organizations to scrutinize different production methods and draw insights that can foster better decision-making. It doesn't just highlight the strengths and weaknesses of each system but also identifies unique opportunities for enhancement. This analysis is especially crucial in a world where technological advancements and market dynamics necessitate continuous evolution.
Continuous vs. Batch Production
In the realm of manufacturing, the fundamental distinction lies between continuous production and batch production.
Continuous production operates like a well-oiled machine, aiming for perpetual output. It’s akin to a river that flows unceasingly, generating products without interruption. Industries such as oil refining or chemical production typically employ this method. This approach enhances efficiency as large-scale operations can maintain consistent output levels, reduce idle time, and streamline resource usage. However, it does come with its baggage—think of high initial costs and the risk of potential overproduction.
In contrast, batch production resembles cooking a meal in a series of steps. Here, products are created in groups or "batches". A company may produce a specific quantity of a product before switching to another. This method finds its footing in the textile or food industries, where variety and customization are prime. The flexibility of batch production allows for adaptations based on consumer demand, but on the flip side, it can lead to inefficient resource usage and higher per-unit costs due to setup changes.
"Each production method has its unique rhythm; choosing the wrong one can spell disaster for scalability and responsiveness."
Lean Manufacturing Principles
When discussing production systems, lean manufacturing emerges as a vital concept. It seeks to maximize value while minimizing waste. Adopting lean principles is like getting rid of unnecessary baggage before a long journey; it allows companies to focus on what truly matters.
Lean manufacturing emphasizes:
- Value Stream Mapping: Understanding the flow of materials and information helps identify waste.
- 5S Methodology: Sort, Set in order, Shine, Standardize, Sustain ensures a clean and organized workplace.
- Kaizen: A philosophy of continuous improvement that encourages contributions from all levels of the workforce.
By honing in on these principles, companies not only elevate productivity but also invest in culture, enhancing employee engagement and satisfaction.
Just-in-Time Production Strategies
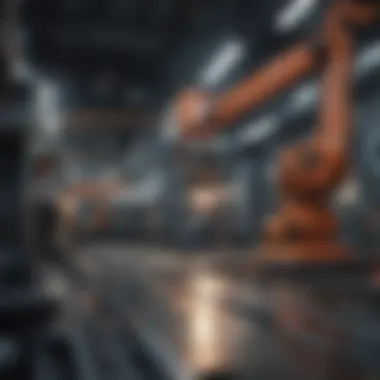
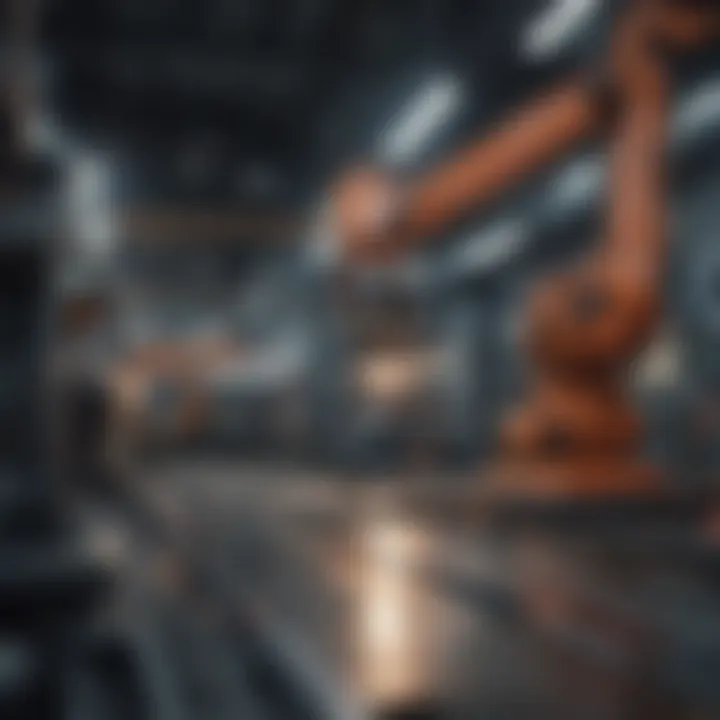
Just-in-Time (JIT) production takes lean manufacturing a step further. Here, the aim is to produce only what is needed when it is needed. Rather than having materials or products on hand, JIT fosters a pull-based system where inventory is minimized, promoting efficiency and cost savings.
Consider this analogy: a restaurant that prepares dishes based on orders rather than preparing a fixed amount. This concept significantly reduces waste due to unsold meals or expired ingredients.
Two key elements of JIT include:
- Supplier Integration: Close relationships with suppliers ensure that materials arrive just as production demands them.
- Efficient Workflow: Continuous monitoring and adjustments to production processes facilitate smooth operations and reduce delays.
However, adopting JIT isn't without risks, such as vulnerability to supply chain disruptions. Balancing responsiveness with reliability is key to mastering JIT strategies.
In summary, a comparative analysis of production systems is not just a theoretical exercise; it highlights core components and methods that define manufacturing efficiency. Embracing the right system could significantly influence success in today's fast-paced industrial environment.
Future Trends in Assembly Line Production
As we move deeper into the 21st century, the landscape of assembly line production is undergoing transformative changes. The importance of this topic cannot be overstated. Understanding future trends allows companies to adapt to new realities, optimize processes, and sustain competitive advantages. These trends are not mere whims of technological advancement; they are essential elements shaping the industry.
Sustainability in Manufacturing
Sustainability is becoming a critical consideration in manufacturing strategies. Companies are increasingly recognizing the need to reduce their environmental footprint. Here are some aspects driving this trend:
- Resource Efficiency: Modern assembly lines are focusing on minimizing waste. This involves using materials more effectively and finding innovative ways to recycle by-products.
- Energy Consumption: Companies are adopting energy-efficient machines and processes. This not only reduces costs but also supports broader environmental goals.
- Regulatory Compliance: Governments around the world are implementing stricter environmental regulations. Being proactive about sustainability ensures compliance and can enhance a company's public image.
- Customer Preferences: Today's consumers are more aware of environmental issues. They are choosing brands that demonstrate social responsibility.
Moving forward, sustainability in manufacturing isn't just a trend; it's becoming a standard all players must consider to remain relevant. Companies that get ahead in this area can set themselves apart in a crowded market.
"The key to achieving sustainability isn’t just about making changes, but about making changes that matter."
The Role of Artificial Intelligence
Artificial Intelligence (AI) is revolutionizing the assembly line. Its integration into production systems is no longer a futuristic concept but a hallmark of modern industry. Here’s how AI is impacting assembly line production:
- Predictive Maintenance: AI can analyze data from machines to predict when maintenance will be needed. This prevents unexpected downtimes and reduces operational costs.
- Quality Control: Through machine vision systems, AI can perform real-time inspections. This ability not only enhances product quality but also reduces waste and the cost of reworks.
- Supply Chain Optimization: AI systems can forecast demand with greater accuracy. This ensures that supplies are aligned with production schedules, avoiding bottlenecks and delays.
- Flexibility in Production: AI allows for dynamic adjustments to production lines. This means that lines can be easily configured to meet varying customer demands without significant downtime.
Staying informed about these trends will be essential for those in the industry—students, researchers, and professionals alike—as they navigate the complexities of modern manufacturing.
Socio-Economic Implications of Assembly Line Production
The evolution of assembly line production has not just transformed manufacturing but has deeply influenced socio-economic dynamics globally. Understanding these implications offers insights into how industries adapt to technological change, and how society as a whole responds to these shifts. This segment emphasizes the importance of recognizing both the positive and negative ramifications of assembly line systems.
Impact on Employment
The assembly line has historically altered employment landscapes, often sparking vigorous debates. On one end, it brought about mass job creation in factories, during the heyday of industrialization. Numerous positions emerged, allowing unskilled workers a chance to earn wages that would support their families, often for the first time. However, this growth was met with the dark underbelly of automation, where increasingly sophisticated machinery began to replace human labor.
- Job Displacement: Many traditional roles, especially in low-skilled positions have vanished, creating anxiety among workers. For instance, in automotive manufacturing, robots perform tasks previously undertaken by humans. This not only raises the stakes for workers but also encourages upskilling to meet the demands of a diversified job market.
- Job Transformation: On the flip side, many roles have morphed into higher-skill positions, demanding a broader range of abilities. Those willing to adapt can find themselves reaping the benefits of new technologies.
"In a rapidly changing environment, adaptability isn’t just beneficial—it’s survival."
- Regional Impact: Additionally, employment shifts are not evenly distributed; regions that once thrived on assembly line jobs may face economic decline when factories close or automate. This can lead to wider inequality across geographical areas, creating pockets of wealth and poverty.
Cultural Shifts in Work Ethos
As assembly line production became entrenched in corporate culture, it also precipitated significant changes in work ethos. The mechanization of tasks instigated a transition from craftsmanship to a more rigid, task-oriented approach. Here are several aspects of how this cultural transformation manifested:
- Efficiency Over Individuality: The emphasis on efficiency means that every worker is seen as part of a machine, rather than as an individual craftsman. This has led to a sense of alienation among workers, with fewer opportunities for creativity in their roles. Traditionally, artisans took pride in their handiwork—today, many assemble parts without a connection to the whole.
- Reinforcement of Hierarchies: The division of labor has reinforced hierarchical structures. Workers, managers, and engineers often have clearly defined roles, separating them in terms of responsibilities and authority. This can create a culture of communication barriers and less collaboration across levels.
- The Rise of Job Satisfaction Issues: With monotonous tasks often characteristic of assembly work, job satisfaction can plummet, resulting in higher turnover rates. Employers are faced with the challenge of creating an environment that maintains morale while maximizing productivity.
In light of these socio-economic implications, it becomes essential for all stakeholders—businesses, governments, and communities—to actively engage in dialogues about the future of work in an assembly line economy. The very fabric of societal interactions, job fulfillment, and economic stability hinges upon how effectively we adapt to these transformational forces.
Ending and Future Directions
The significance of the assembly line concept cannot be overstated. This intricate system of production has shaped the modern manufacturing landscape dramatically. Through its historical evolution, operational mechanisms, and technological advancements, the assembly line has proven to be both resilient and adaptable. The findings and insights presented in this article underscore the critical need for ongoing evaluation and adaptation of assembly line processes to keep pace with the rapid changes in the industry. In the future, it will become increasingly important for manufacturers to mesh sustainability and innovation into their operational frameworks while addressing socio-economic challenges.
One of the central lessons from our exploration is the innovative use of technology within assembly lines. From automation to advances in artificial intelligence, these elements not only enhance efficiency but also reshape labor dynamics. As firms work to streamline production and cut costs, the dialogue surrounding job displacement and workforce transformation will evolve.
Summarizing Key Insights
Reflecting on the main themes discussed throughout this article, several key insights emerge:
- Historical Context: The origins and evolution of the assembly line provide a foundation for understanding its usefulness today. Starting from rudimentary manufacturing methods, it has transformed into a sophisticated arrangement that pushes the boundaries of productivity.
- Operational Efficiency: The mechanics of assembly line operations highlight how minimizing downtime while maximizing output can significantly affect productivity ratios. In today's competitive market, these principles remain essential for any production operation.
- Technological Integration: Automation, robotics, and the Internet of Things not only elevate productivity levels but also usher in new paradigms for manufacturing that prioritize precision and responsiveness.
- Challenges Ahead: Despite the advantages, challenges such as labor issues, quality control, and the need for flexibility demand attention. Future assembly line designs must consider these factors carefully.
- Socio-Economic Effects: The tension between technology and labor raises concerns; understanding its implications is vital for communities as they adapt to a changing workforce landscape.
Recommendations for Further Research
To stay ahead of the curve in assembly line production, several areas warrant deeper investigation:
- Sustainable Practices: Future research should delve into how eco-friendly methods and materials can be integrated into assembly line operations without sacrificing efficiency.
- Impact of AI: With artificial intelligence increasingly influencing production processes, examine how AI can optimize not just output but also decision-making and machine learning outcomes.
- Workforce Adaptation: Investigate training programs and education strategies necessary for adapting the workforce to technological advancements. Understanding how institutions can evolve educational frameworks could lead to smoother transitions.
- International Case Studies: Comparing assembly line adaptations across different cultural and economic landscapes might reveal novel solutions to common production challenges.
- Long-term Viability: Assess the long-term sustainability of current assembly line practices. As the global economy changes, it will be interesting to see how these lines adapt or redefine themselves.