Benefits of Digital Twin Technology in Manufacturing
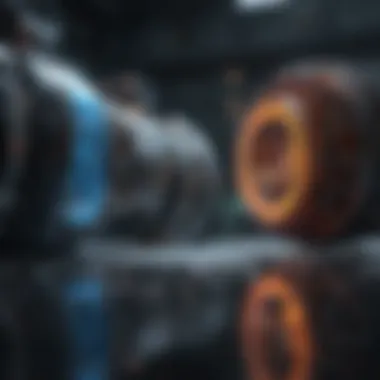
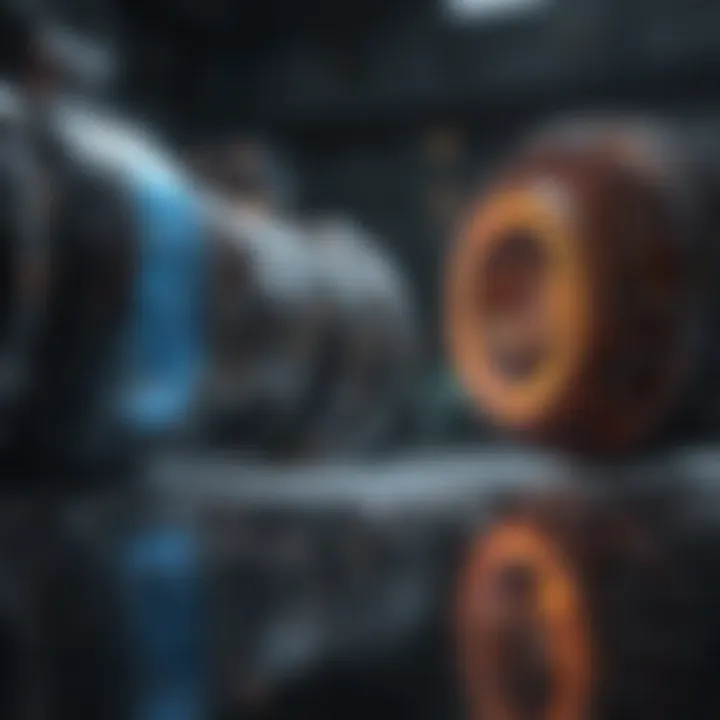
Intro
In the rapidly evolving landscape of manufacturing, the adoption of cutting-edge technologies is not just a trend but a necessity. Among these advancements, digital twin technology has emerged as a transformative force, offering a plethora of benefits that significantly enhance operational effectiveness. Digital twins serve as virtual replicas of physical assets, processes, or systems, enabling organizations to analyze and optimize performance in real-time. This article will dissect how the integration of digital twin technology can reshape manufacturing practices, driving efficiency and quality while minimizing costs.
Key Concepts and Terminology
Definition of Key Terms
To fully grasp the significance of digital twin technology, itโs crucial to familiarize ourselves with some key terms:
- Digital Twin: A digital representation of a physical entity that mirrors its current state and behavior.
- IoT (Internet of Things): A network of interconnected devices that collect and exchange data.
- Predictive Maintenance: An approach to maintenance that uses data analysis to predict equipment failures before they occur.
Concepts Explored in the Article
This article will explore several core concepts surrounding digital twin technology, focusing on:
- The mechanics of how digital twins operate within manufacturing environments
- The role of real-time data analysis in enhancing operational agility
- Collaborative innovation facilitated by digital twins
- Future trends that may shape the evolution of this technology in the industry
Findings and Discussion
Main Findings
The application of digital twin technology in manufacturing has revealed numerous advantages:
- Improved Efficiency: By providing real-time insights into processes, companies can adjust operations dynamically, optimizing overall efficiency.
- Cost Reduction: Through predictive maintenance and process optimization, organizations can lower operational costs significantly.
- Enhanced Quality: Constant monitoring allows for quicker response times to any product quality issues, reducing defects.
- Increased Collaboration: Digital twins facilitate a shared understanding among different teams, helping streamline innovations that a lone department may miss.
With digital twin technology, organizations are not merely reacting to changes but instead anticipating them. This proactive approach fundamentally changes how manufacturers operate.
Potential Areas for Future Research
As this technology continues to develop, several research avenues merit further exploration:
- Integration with AI and Machine Learning: Understanding how these technologies can work together to enhance digital twin functionality remains a prime concern.
- Scalability: Research into how smaller manufacturers can effectively implement digital twins could democratize access to this powerful technology.
- Impact on Workforce Dynamics: Evaluating how digital twins affect job roles and perspectives among manufacturing staff.
In summary, digital twin technology is paving the way for a revolution in manufacturing. Its capacity for real-time data processing, predictive capabilities, and fostering collaboration opens new horizons for efficiency and innovation. As organizations continue to harness these tools, the potential for improved processes and products is vast.
Understanding Digital Twin Technology
The landscape of manufacturing is rapidly shifting, and at the heart of this transformation lies digital twin technology. This innovative concept enhances the way manufacturers operate by creating virtual replicas of physical systems. By utilizing data and AI, these digital twins offer insights that can optimize processes, predict maintenance needs, and improve product quality. Understanding the dynamics of digital twin technology is crucial, as it paves the way for better decision-making and operational resilience in an increasingly competitive market.
Definition and Origins
Digital twin technology refers to the digital representation of physical objects, processes, or systems. This technique originates from the aerospace industry in the 1960s, when NASA utilized it to monitor spacecraft systems. Today, it has evolved significantly, integrating advanced sensors, IoT connectivity, and data analytics that allow real-time tracking and simulation of physical entities. To illustrate, think of a digital twin as a sort of cloning magic where a factory or a machine lives both in the tangible world and in a computer simulation, continuously exchanging information.
Core Components of Digital Twins
Digital twins are not a single, simple technology; they consist of several interlinked components that work in harmony:
- Physical Assets: The actual machinery or process that is monitored.
- Digital Representation: A comprehensive digital model that mirrors the physical asset, complete with real-time data feeds.
- Data Analytics: Tools and systems that interpret the data, enabling insights into performance and operational effectiveness.
- User Interface: Dashboards or applications that visualize the data, making it accessible for decision-makers.
These components combined allow manufacturers to gain a holistic view of operations.
The Role of IoT in Digital Twins
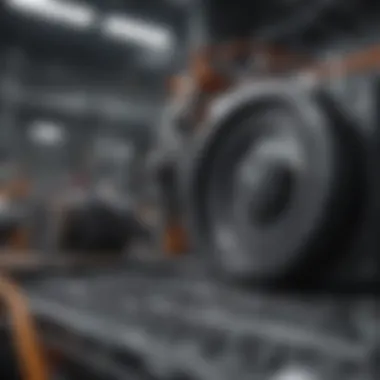
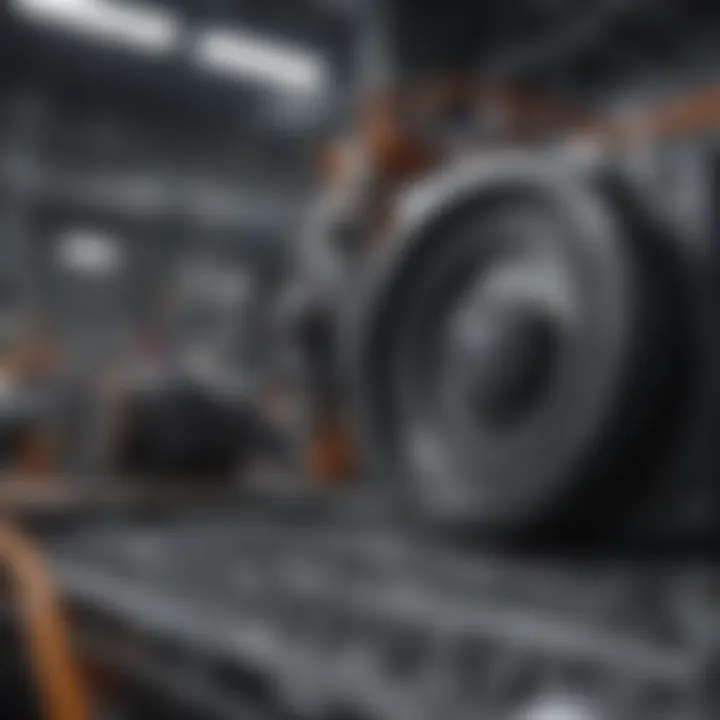
The Internet of Things (IoT) is like the oil in the engine of digital twin technology. It acts as the conduit for data flow between the physical and digital realms. Hereโs how it works:
- Connectivity: IoT devices collect data from sensors embedded in machinery. This data can include temperature, vibrations, and usage rates.
- Real-time Monitoring: Continuous data transmission enables instant monitoring of conditions that might affect production efficiency.
- Predictive Insights: The analytics performed on IoT data can lead to predictions about potential malfunctions or maintenance needs before they emerge as costly failures.
In summary, without IoT, the vision of a seamless digital twin would remain an unrealized dream, showcasing how integral connectivity is to this sophisticated technology.
Benefits of Implementing Digital Twins
The implementation of digital twin technology holds immense importance in the realm of manufacturing. As companies strive for greater efficiency and optimization, the ability to create a digital replica of physical assets opens up a myriad of potential benefits. From refining production processes to enhancing maintenance protocols, digital twins serve as a beacon of innovation.
In a fast-evolving industry landscape, this technology is no longer optional; itโs becoming a necessity for businesses looking to maintain a competitive edge. By integrating digital twins, manufacturers can expect not only to streamline operations but also to foster a culture of continuous improvement dependent on real-time data and analytics.
Enhanced Visualization and Simulation
When manufacturers adopt digital twin technology, they gain access to superior visualization and simulation capabilities. Imagine being able to see a virtual representation of a factory floor, complete with moving parts and operational metrics. This allows for a more analytical approach to design and process management. Companies can simulate various scenarios without the costs and risks associated with real-world testing.
For instance, a manufacturer can visualize how changes in assembly line configurations might impact output. These simulations help identify bottlenecks, ensuring they are addressed before they become problematic. This technology not only enhances understanding but also fosters creativity among teams by providing a platform to brainstorm and visualize solutions.
Real-Time Data Processing and Analysis
The heart of digital twin technology beats with real-time data. By continuously receiving information from sensors and systems, manufacturers can process data on the fly. This instantaneous feedback loop enables quick adjustments, reducing downtime and maximizing productivity.
For example, if a machine starts to underperform, alerts can trigger immediate investigation and remediation. This is a stark contrast to traditional methods that may involve days or weeks of data collection before any conclusions can be drawn. The ability to act promptly can save time and reduce operational costs significantly, adding another layer to the value of digital twins.
Predictive Maintenance Capabilities
One of the standout features of digital twins is their predictive maintenance capabilities. Instead of relying on fixed schedules for servicing equipment, manufacturers can use data analytics to predict when machinery will likely fail or need maintenance. In this way, problems can be tackled before they escalate, extending the lifespan of crucial assets.
Take, for instance, an automotive parts manufacturer using a digital twin. By analyzing data patterns from their equipment, they can foresee potential breakdowns and schedule maintenance during non-peak hours, thereby minimizing disruption to production. This preventive approach fosters a smoother operation and enhances overall reliability in manufacturing processes.
Operational Efficiency Improvements
Operational efficiency is the ultimate goal of implementing digital twins in manufacturing. By leveraging the vast insights generated through real-time monitoring and analysis, companies can refine their workflows considerably. Digital twins help in identifying inefficiencies that may go unnoticed in conventional operations.
For example, consider a textile manufacturer who switches to a digital twin approach. They could uncover that a particular dyeing machine consumes more energy than needed during certain processes. Through targeted adjustments, they can not only cut costs but also reduce their environmental footprint, aligning with industry trends favoring sustainability.
By fostering a deep-seated culture of efficiency through these digital methodologies, manufacturers position themselves not just as competitors but as leaders in their field.
Ultimately, the benefits of implementing digital twins extend beyond immediate operational gains. They lay the groundwork for a future-oriented, data-driven manufacturing environment that responds nimbly to market demands, ensuring long-term sustainability and growth.
Impact on Production Processes
The impact of digital twin technology on production processes cannot be overstated. This is where practical applications unfold, transforming traditional methods into modern narratives of efficiency and precision. The benefits extend beyond simple cost savings; they fundamentally alter how manufacturers approach their entire production chain. Let's delve into some specific aspects that make this digital evolution a game-changer in manufacturing.
Streamlining Manufacturing Workflows
Streamlining manufacturing workflows is crucial in today's highly competitive environment. By leveraging digital twins, factories can create virtual replicas of their physical assets, which allow for an intricate understanding of each component and process.
These replicas enable real-time monitoring of production activities. Problems can be identified instantly, and adjustments can be made on-the-fly. This reduces downtime significantly, which can often equate to significant losses in productivity and revenue.
For instance, a factory that produces automobile parts might use digital twins to ensure that each machine operates at optimal levels. Data from the machines feeds into their digital counterparts, revealing inefficiencies that might otherwise go unnoticed. This proactive approach can lead to streamlined operations and the improved allocation of resources, aligning with the company's financial goals.
Quality Control and Assurance Enhancements
Quality control has always been a foundational element of manufacturing. Digital twin technology takes this to a new level. Strengthened quality assurance processes come from the ever-present ability to monitor conditions and performance.
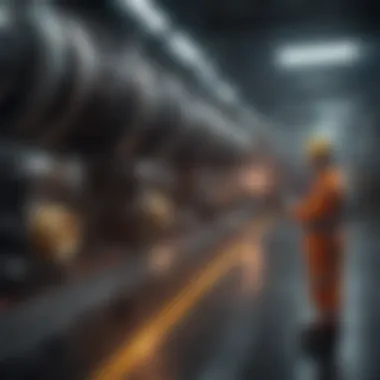
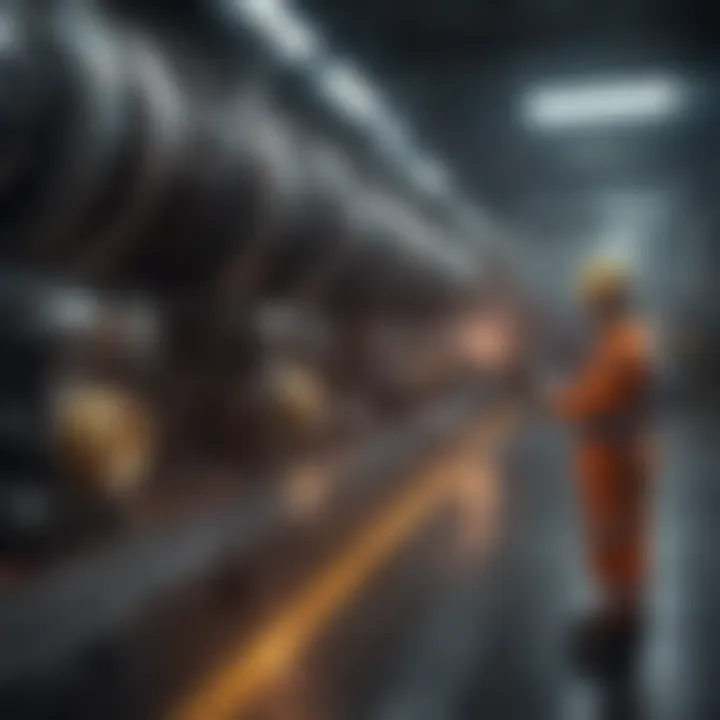
With digital twins, manufacturers can gather data from every stage of production, creating a continuous feedback loop. This means that any deviations from quality standards can be identified early in the production process, not just at the end when problems are more costly to fix.
For example, a food processor could use a digital twin of a processing line to ensure that temperature and hygiene standards are consistently maintained. Through this constant vigilance, products that do not meet quality specifications can be flagged in real time for corrective action, reducing waste and enhancing consumer trust.
Supply Chain Optimization
Supply chains often resemble a complex puzzle, with various parts dependent on one another for success. Digital twin technology shines here, illuminating pathways for optimization. By simulating the entire supply chain, manufacturers can identify potential bottlenecks or issues before they arise.
Utilizing real-time data feeds, companies can accurately predict delays, adjust schedules, and even renegotiate supplier contracts based on demand forecasting. For instance, a textile manufacturer might discover that sourcing particular fabrics leads to consistent delays due to transportation, prompting a shift to a nearer supplier. This agility boosts overall responsiveness and significantly enhances customer satisfaction.
Analytics and Decision Making
In today's fast-paced manufacturing environment, the need for effective analytics and decision-making processes cannot be overstated. Digital twins leverage sophisticated data analytics techniques, enabling companies to make informed decisions based on real-time insights. By using digital twin technology, firms can gather extensive data from their operations, allowing them to transform raw information into actionable intelligence.
One of the key advantages provided by digital twins is their ability to create a comprehensive digital representation of physical assets and processes. This approach serves as a solid foundation for data-driven decision-making. Specifically, the analytics derived from a digital twin can help identify inefficiencies, optimize workflows, and enhance product development by enabling manufacturers to simulate various scenarios before committing to any process changes.
Data-Driven Insights for Better Strategy
Accessing data-driven insights is essential for shaping a robust business strategy. With digital twin technology, organizations can obtain vital information about their systems' performance and customer behavior. As a result, they can refine their strategies based on solid evidence rather than relying on guesswork or gut feelings.
- Performance Analysis: The continuous monitoring of machine performance helps identify patterns and trends that indicate potential issues. For instance, if a piece of equipment consistently shows signs of wear and tear, the analytics can detail its performance against operational standards.
- Customer Behavior: Understanding customer preferences and needs becomes simpler. By analyzing this data, companies can tailor their products and services to better meet market demands.
- Resource Optimization: When data insights reveal areas where resources are being underutilized, the company can reallocate or invest in those sectors, ensuring better output and reduced waste.
"What gets measured gets managed. By utilizing analytics, companies can make informed choices that lead to resilience and sustainabilty."
Scenario Modeling and Forecasting
Scenario modeling and forecasting are among the most valuable applications of digital twin analytics. This technology enables manufacturers to simulate different future scenarios based on current data inputs, helping them anticipate and prepare for various outcomes.
- Risk Assessment: By testing hypothetical situations, organizations can identify potential risks and develop contingency plans to mitigate them. For example, if a supplier faces disruptions, predictive models can help ascertain how that will impact the supply chain and what actions may be needed to minimize losses.
- Production Planning: With forecasting tools, firms can more accurately estimate production levels based on demand signals. This means fewer bottlenecks and overproduction, leading to streamlined operations and cost savings.
- Investment Decisions: Understanding how different decisions affect outcomes helps executives make better investments in technology, processes, or personnel.
Challenges of Digital Twin Integration
The introduction of digital twin technology in manufacturing isn't all smooth sailing. While the benefits are both numerous and impactful, various challenges pop up that can complicate the integration process. Understanding these hurdles is crucial for manufacturing stakeholders aiming to leverage digital twins effectively. These challenges, be it concerns over data security, the costs associated with implementation, or the need for a skilled workforce, can significantly affect the overall success of digital twin initiatives.
The integration of this technology requires not just the right tools and software but also a well-planned approach that considers these roadblocks. Without a clear understanding of these challenges and strategies to mitigate them, manufacturers may find themselves in rocky waters.
Data Security and Privacy Concerns
In this digital age, safeguarding data is paramount. When dealing with digital twin technology, sensitive operational information and intellectual property are often at risk. The collection and storage of massive data sets raise eyebrows when it comes to security and privacy. Data breaches could lead to financial losses and damaged reputations; thus, itโs essential for manufacturers to engage in robust cybersecurity practices.
Key strategies to mitigate risks include:
- Implementing encryption protocols: This keeps data safe from unauthorized access.
- Regular security audits: Continual assessment helps spot vulnerabilities early.
- Compliance with regulations: Adhering to industry standards like GDPR is crucial for privacy protection.
"In an era where information is as valuable as the products manufactured, protecting that information is not just smartโit's necessary."
High Implementation Costs
Adopting digital twin technology is not a low-cost endeavor. The initial investment can be substantial, as it requires specialized software, hardware, and often, significant customization. These expenses can be a roadblock for smaller manufacturers, especially when budgets are tight.
To ease this burden, manufacturers can consider phased implementation. Taking a step-by-step approach allows them to spread out costs while gradually reaping the advantages of digital twins.
Cost-effective strategies include:
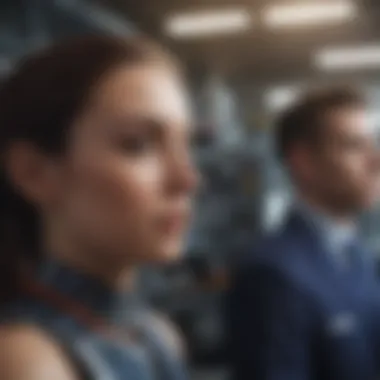
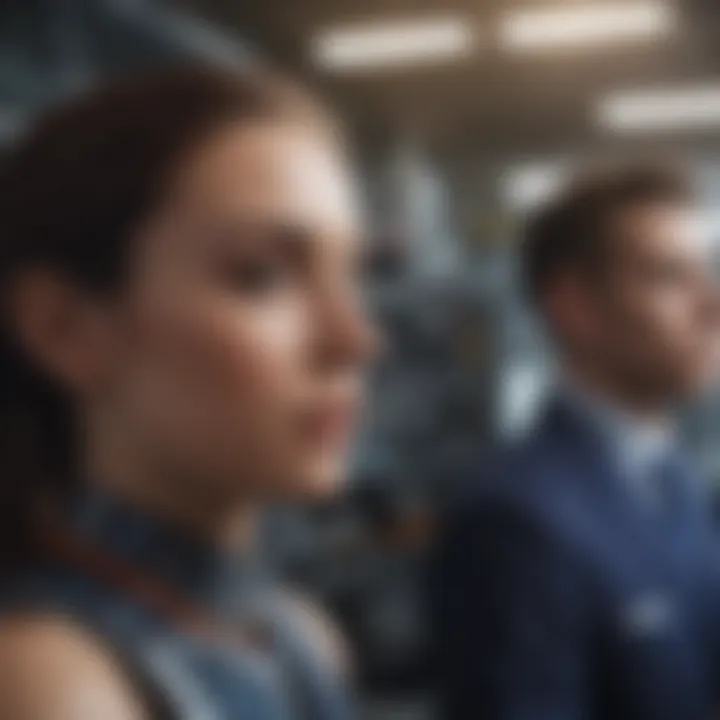
- Lease options: Instead of purchasing, consider renting software solutions.
- Leveraging cloud technologies: These can reduce infrastructure costs and improve scalability.
- Partnerships with tech providers: Collaborating can lessen the financial load on single entities.
Requirement for Skilled Workforce
Finding and retaining talent capable of managing digital twin integrations presents another challenge. Specialized skills in data analytics, machine learning, and information technology are factors that can make or break a successful digital twin application.
Training existing employees is one route, but it involves timeโa resource manufacturing cannot afford to waste. Manufacturers must devise effective training programs that bridge skills gaps and prepare the workforce for this advanced technology.
Strategies for developing talent include:
- Investing in continuous learning: Encourage staff to pursue courses in relevant areas.
- Building partnerships with educational institutions: Collaborate with universities to foster training programs tailored to industry needs.
- Cultivating a culture of innovation: Encourage an environment where experimentation and learning from failures are seen as steps toward success.
Integrating digital twin technology in manufacturing certainly has its share of challenges. But with a clear strategy in addressing data security, implementation costs, and workforce skills, companies can harness the true potential of this transformative technology.
Future Trends in Digital Twin Technologies
The evolution of digital twin technology is pivotal for the manufacturing sector, as it continues to redefine standards. Understanding current and emerging trends is crucial for stakeholders to stay ahead of the curve and leverage the full potential of this innovative approach. By exploring how digital twins are set to evolve, one gains invaluable insight into shaping future strategies that align with industry demands.
Artificial Intelligence Integration
Artificial Intelligence, or AI for short, is carving an essential place in digital twin technology. As manufacturing processes become increasingly complex, integrating AI enhances the predictive power of digital twins. By utilizing machine learning algorithms, companies can discover patterns and anomalies in real-time data with remarkable accuracy. For instance, a machine on the production line may exhibit certain vibrations, alerting operators before a potential malfunction. This proactive approach not only prevents downtime but also contributes to overall operational efficiency.
One practical application could be seen in quality control. AI can analyze vast datasets generated by digital twins to predict when a product is likely to deviate from quality standards. This means that manufacturers can correct issues before they escalate, paving the way for a more reliable product. So, in essence, merging digital twins with AI ensures a smarter, more responsive manufacturing environment, where decisions are data-driven and less prone to human error.
Advancements in Augmented Reality
Augmented Reality (AR) is set to play a transformative role in the future of digital twin technology. Imagine factory workers equipped with smart glasses that overlay digital twin data directly onto real-world equipment. With AR, technicians can visualize complex assembly processes or maintenance requirements without the need for cumbersome instruction manuals. This real-time assistance can drastically reduce training time and improve operational proficiency.
Furthermore, AR can strengthen remote collaboration. Experts from various locations can interact with a digital replica of the machine, thereby resolving issues without being physically present on the floor. Such advancements not only help in getting immediate support but also facilitate knowledge sharing across teams worldwide.
"The blend of AR and digital twins redefines how we interact with manufacturing processes, making complex information digestible and immediate for those on the shop floor."
Expansion in Cross-Industry Applications
The beauty of digital twin technology lies in its versatility. It is no longer confined to a single industry; instead, it is finding applications across various sectors. In manufacturing, the insights gained from digital twins can be utilized in sectors such as aerospace, automotive, and even healthcare. For example, an automotive company can employ digital twin tech for prototyping, while an airplane manufacturer can predict maintenance needs for fleet optimization.
This cross-industry expansion means that manufacturers are not just innovating within their domain but are also collaborating with other sectors to push boundaries further. Companies that recognize this potential can adapt best practices from different areas to enhance their processes. Think about how a healthcare facility might adopt supply chain strategies observed in the manufacturing sector, creating synergies that yield significant benefits.
End
Digital twin technology stands at the helm of a manufacturing revolution, offering pathways to improved efficiencies and innovation. Understanding its multifaceted benefits is crucial not just for businesses but also for students and researchers who seek to be at the cutting edge of technology. As industries aim to reduce costs while increasing output quality, digital twins offer a beacon of hope.
In our exploration, several key advantages emerged, such as enhanced visualization and real-time data analysis. These features allow businesses not just to react but to proactively manage their processes. Predictive maintenance, a game changer in operational economics, can save manufacturers significant money and resources. Through data-driven insights, organizations can fine-tune their strategies in ways that were previously unimaginable.
"Digital twins provide a framework for real-time insights that reshape traditional manufacturing processes."
Summarizing Key Benefits
To encapsulate the potential of digital twin technology, one must consider these salient points:
- Real-time Monitoring: Keeping an eye on equipment and processes helps in immediate identification of anomalies.
- Predictive Maintenance: Anticipating issues before they arise can mitigate unforeseen downtimes, translating to tangible cost savings.
- Enhanced Collaboration: Teams can leverage the digital twin to work together seamlessly, breaking silos that often hinder efficiency.
- Improved Product Quality: With continuous data feedback, quality assurance can be integrated throughout the production lifecycle.
These benefits paint a clear picture of why digital twin technology is a necessity rather than a luxury in today's manufacturing landscape.
Considerations for Future Development
As we gaze into the horizon of digital twin technology, certain considerations warrant attention:
- Evolution of Technology: The pace of change is steep; keeping abreast of advancements in AI and other computational technologies is pivotal for maximizing the utility of digital twins.
- Training Workforce: Employees must be well-equipped to handle the shifts in workflow, ensuring they can utilize these technologies to their fullest potential.
- Cost Dynamics: The balance between implementation costs versus long-term savings must be carefully analyzed by all stakeholders.
- Cross-Industry Applications: While manufacturing benefits greatly, looking towards how digital twin technology can cross into other fields (like healthcare or urban planning) may broaden its applications.
Recognizing these aspects will help businesses strategize effectively for a future that increasingly leans on digital twins for smarter manufacturing insights.