Mastering Boiler Capacity Calculation Techniques
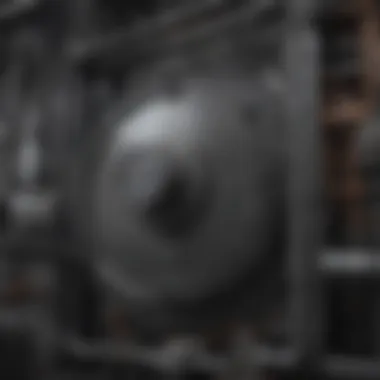

Intro
In the realm of industrial processes, understanding boiler capacity is pivotal. Not only does it play a key role in designing efficient systems, but it also influences operational costs and environmental impact. A boiler, often considered the heart of steam generation, must meet the demands of various applications, from heating to powering turbines. Therefore, knowing how to accurately calculate boiler capacity is essential for engineers and operators alike.
When discussing boiler capacity, several factors come into play, such as thermal efficiency, steam demand, and system design parameters. These elements weave together a broader picture of how boilers function and how their output can be tailored to specific needs. This article embarks on a meticulous exploration of the principles and methodologies behind boiler capacity calculations, ensuring that readers can grasp these concepts comprehensively.
Key Concepts and Terminology
Definition of Key Terms
To establish a solid foundation, it’s crucial to clarify some fundamental terms associated with boiler capacity:
- Boiler Capacity: This term generally refers to the maximum amount of steam a boiler can produce in a given timeframe, often expressed in pounds per hour (lb/h) or tons per hour (t/h).
- Thermal Efficiency: It reflects how well a boiler converts fuel energy into steam energy, which is an essential factor in calculating the required fuel input.
- Steam Demand: This indicates the quantity of steam needed for specific applications at a given time, often influenced by operational requirements.
- Heat Input: This is the amount of heat energy supplied to the boiler, crucial for understanding the relationship between fuel consumption and steam production.
Concepts Explored in the Article
This guide encompasses a variety of interrelated concepts:
- The significance of precise boiler capacity calculations in preventing overloading or underutilization.
- How system design factors interplay with capacity to optimize performance.
- The impact of external conditions like ambient temperature and water quality on boiler efficiency.
Through dissecting these concepts, the aim is to furnish readers—whether they be students, researchers, or professionals—with insights that they can apply in real-world scenarios.
Findings and Discussion
Main Findings
The exploration of boiler capacity calculation reveals several noteworthy findings:
- An accurate assessment of steam demand not only conserves energy but also mitigates costs associated with fuel wastage.
- Recognizing the significance of thermal efficiency can lead to better selection of boiler types and designs.
- Implementing advanced calculation methods enhances system reliability and extends the lifespan of equipment.
"An accurate understanding of boiler capacity can prevent costly downtime and improve overall operational efficiency."
Potential Areas for Future Research
While the current findings serve as a solid base, they also open avenues for further investigation:
- Exploring the impact of renewable energy sources on boiler capacity calculations.
- Investigating innovative materials that could improve the thermal efficiency of boilers.
- Analyzing operational data to develop predictive models for steam demand based on real-world usage patterns.
By identifying these areas, the guide aims to motivate ongoing research and adaptation in the field of boiler technology, further enhancing understanding and application.
In closing, mastering the principle of boiler capacity calculation isn’t just an academic exercise; it holds real implications for industry effectiveness and environmental stewardship.
Prologue to Boiler Capacity
Understanding boiler capacity is pivotal in both industrial and residential applications. This topic lays the foundation for effectively managing steam systems, which play a crucial role in various operations from heating to powering equipment. The capacity of a boiler directly influences efficiency, performance, and cost-effectiveness in thermal systems.
Definition of Boiler Capacity
Boiler capacity refers to the maximum amount of steam that a boiler can generate in a specified time. This measurement is typically expressed in units such as pounds of steam per hour (lb/hr) or megawatts (MW). In essence, the capacity determines how well the boiler can meet the heating demands of a system. The greater the capacity, the more heat it can produce, which is essential in ensuring that industrial processes or heating systems operate smoothly.
To dive deeper, boiler capacity encompasses several factors, including:
- Type of Boiler: Different boilers have varying efficiencies. For instance, a water-tube boiler generally has a higher capacity than a fire-tube boiler due to its design, which allows for quicker steam generation.
- Heat Input: The heat input determines how much fuel is being used, thus affecting the steam output.
- Temperature and Pressure: Higher steam temperatures and pressures can lead to increased capacity.
A clear grasp of these points allows professionals to make informed decisions when selecting or designing boiler systems.
Importance of Capacity Calculation
Calculating boiler capacity accurately is not merely a formality; it significantly impacts operational efficiency and safety. Here are some reasons why capacity calculation holds such importance:
- Meeting Demand: A precise calculation ensures that a boiler can meet the maximum steam demand of a process. Undercapacity can lead to interruptions and operational failures, while excessive capacity may waste fuel and increase costs.
- Regulatory Compliance: Many jurisdictions mandate that thermal systems must adhere to certain capacity standards for safety and environmental protection. Accurate calculations assist in compliance with these regulations.
- Cost Control: Optimally sized boilers help in controlling operational costs. Oversized boilers can lead to inefficient operation, resulting in unnecessary fuel consumption.
One critical point to remember is that improper capacity calculation can have rippling effects down the line, causing inefficiencies that might not be immediately apparent. Therefore, a thorough understanding of boiler capacity is essential for any engineer or technician working within thermal systems.
"A well-sized boiler is akin to a well-fitted suit; it ensures efficiency and performance tailored to specific needs."
Capacity calculations, therefore, aren't just numbers; they symbolize the intricate balance between demand, efficiency, and cost. Armed with this knowledge, professionals can better navigate the complex landscape of boiler systems.
Fundamental Principles of Boiler Operations
Understanding the fundamental principles of boiler operations is crucial for anyone involved in energy management and engineering. These principles lay the groundwork for how a boiler functions and influences its overall capacity. The basic concepts help in diagnosing issues, optimizing performance, and implementing effective maintenance strategies. Knowledge in this area not only aids in operational efficiency but also in designing systems that meet specific requirements.
Basic Boiler Functionality
At its core, a boiler's primary function is to convert water into steam, which is then used for various applications ranging from heating to driving turbines in power plants. This process involves the transfer of heat from a fuel source to water within the boiler. When the water reaches a specified temperature, it transitions into steam. This steam can be used directly for heating or further directed into a steam turbine to generate electricity.
Different types of heat exchange mechanisms exist, like sensible heat and latent heat, which influence how effectively a boiler operates. Understanding these methods is essential because it affects the energy conversion efficiency - key for maximizing output while minimizing fuel consumption.
Types of Boilers
Boilers come in various types, each designed for specific applications and operational requirements. Here, we will look at three common types: water-tube boilers, fire-tube boilers, and electric boilers.
Water-tube Boilers
Water-tube boilers, as the name suggests, contain water tubes through which water circulates, while combustion gases pass around outside the tubes. This structural design allows for a higher steam generation rate, making water-tube boilers ideal for large industrial applications.
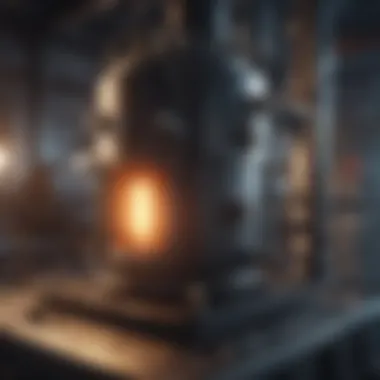

One key characteristic of water-tube boilers is their ability to handle high pressures and temperatures. They are, therefore, efficient at producing a significant volume of steam quickly. This feature makes water-tube boilers an attractive option for industries with fluctuating steam demands. However, a downside is that they can be more complex in design and construction, often requiring more maintenance than their counterparts.
"Water-tube boilers are often considered the backbone of high-efficiency industrial steam generation."
Fire-tube Boilers
In contrast, fire-tube boilers are structured such that flames pass through tubes submerged in water. The heat generated from the flames warms the water, creating steam. One notable advantage of fire-tube boilers is their simpler design and lower construction costs. This makes them favorable for smaller operations or facilities that require less steam output.
However, their capacity limitation in terms of high pressure and temperature can be a disadvantage compared to water-tube boilers. Nonetheless, they offer ease in maintenance and operation, especially in residential heating applications.
Electric Boilers
Electric boilers utilize electricity as their heat source, converting electrical energy directly into thermal energy. They are gaining popularity due to their compact size and the ability to produce steam without combustion, thus eliminating fuel-related emissions.
A significant upside of electric boilers is their flexibility. They can be implemented seamlessly into various settings, like residential or commercial spaces, where conventional fuel sources may be impractical. However, operational costs may be higher, especially if electricity prices fluctuate. Furthermore, they typically have lower capacity limits making them less suitable for large-scale industrial use, although they excel in niche applications.
By exploring these different types of boilers, one gains a better appreciation of how each functions and the role they play in effective boiler capacity calculations.
Key Factors Affecting Boiler Capacity
Understanding the nature of boiler capacity is akin to grasping the pulse of a heating system. The boiler, serving as the core of steam generation, plays a pivotal role in various applications from powering industrial machinery to heating residential spaces. The factors that influence this capacity are crucial for ensuring optimal performance, efficiency, and safety.
In this segment, we will delve into the specific elements that govern boiler capacity, highlighting the significance of each aspect in effective boiler operations. By comprehending these factors, professionals can effectively tailor systems to meet precise demands, thereby minimizing operational hiccups and maximizing productivity.
Feedwater Temperature
The temperature of feedwater is a fundamental aspect in boiler operations. This essentially refers to the water entering the boiler for steam generation. If the feedwater is too cold, it can lead to inefficiencies, significantly affecting the heating process.
A higher feedwater temperature can enhance boiler efficiency, reducing overall fuel consumption while also ensuring quicker steam generation. However, there are thermal limits; too high a temperature might compromise system integrity or safety, therefore maintaining balance is key. It's important to get the feedwater at the right temperature, ideally between 150 and 180 degrees Fahrenheit, to allow for optimal performance without risking thermal shock to boiler materials.
Steam Pressure Requirements
Steam pressure establishes how much steam can be generated and delivered to various systems. Higher steam pressure generally translates to a greater capacity. This makes it vital to identify the required steam pressure for your application's specific needs.
For instance, industrial applications typically operate at higher pressure, often exceeding 150 psi, whereas residential heating systems tend to work efficiently at lower pressures around 30 psi or less. It's essential to recognize that exceeding design pressure can lead to catastrophic failures or inefficiencies; thus maintaining the pressure within specified limits is a non-negotiable factor in capacity calculations.
Thermal Efficiency
Thermal efficiency determines how well a boiler converts fuel into usable energy. A boiler operating at higher thermal efficiency not only conserves energy but also results in lower operational costs, which is a win-win in any setting.
Considering factors like the fuel type, combustion process, and design can significantly impact thermal efficiency. For example, condensing boilers can achieve thermal efficiencies of over 90%, while traditional models may only reach between 70% and 80%. Regular maintenance and updates to newer technology can help attain maximum efficiency and prolong boiler life, thus ensuring capacity that meets evolving demands.
Heat Loss Considerations
Heat losses in a boiler system can arise from various sources, including insulation deficiencies, leaks, or improper configurations. These losses directly reduce the effective capacity of the boiler, resulting in wasted energy and increased costs.
Understanding heat loss is critical in the design and implementation phases. By assessing and minimizing these losses, a more accurate capacity calculation can be achieved. For instance, using adequate insulation, sealing joints properly, and ensuring venting systems are efficiently designed will significantly mitigate these losses. Poorly maintained systems can lead to losses of up to 15-20%, highlighting the importance of continual assessment and upgrades.
Key Takeaway: Successfully managing these factors not only aids in accurate boiler capacity calculations but also enhances the overall efficiency and lifespan of the equipment, making a substantial difference in any operation.
In sum, by diving deep into these key factors, one can appreciate the dynamics involved in boiler operations, allowing for a more tailored and effective approach to system design and maintenance.
Calculating Boiler Capacity
Calculating boiler capacity stands as a pivotal segment in ensuring that steam-producing systems function optimally. The essence of determining the right capacity lies not only in operational efficiency but also in aspects like safety and cost management. A precise calculation can prevent over-sizing, which leads to energy wastage, or under-sizing, which jeopardizes system performance. Grasping how to achieve accurate capacity calculations is essential for engineers, operators, and anyone involved with boiler systems.
Understanding Boiler Horsepower
Boiler horsepower serves as a key metric in evaluating boiler capacity. Defined as the amount of energy needed to produce a certain amount of steam in a given time, it allows for straightforward assessment against demand. One boiler horsepower typically equals 34.5 pounds of steam produced per hour at a pressure of 0 psig and a feedwater temperature of 212°F. This measurement simplifies calculations across various applications, providing clarity on how much energy a boiler can actually deliver.
Furthermore, knowing the boiler horsepower allows individuals to compare different boilers more effectively. It's just like trying to pick the right vehicle for the job; knowing the horsepower gives insights into how much load it can carry.
Relevant Formulas for Calculation
A grasp of relevant formulas is crucial for accurate boiler capacity calculations. Let’s break down these formulas further:
Basic Formula for Capacity
The basic formula for calculating boiler capacity hinges on the steam output desired. This can be summarized as:
[ Capacity (lb/hr) = (Water Flow Rate (GPM) \times 500) \div (Hg Total Heat Value) ]
This formula addresses a fundamental aspect: the relationship between water flow, temperature, and system pressure. This straightforward calculation method prioritizes accessibility, making it suitable for a range of professionals. Its key characteristic is its ability to translate complex heat transfer into a simple equation, thereby making it a favorable tool in many real-world scenarios.
Advantages of this formula include its ease of use and availability of data, while a potential disadvantage could be its applicability limited to basic systems which may not factor in all variables present in more complex scenarios.
Simple Calculations for Small Boilers
When dealing with small boilers, the calculations can be more straightforward, such as:
[ Capacity (BTU/hr) = BTU per gallon \times GPM ]
This method helps in obtaining a rapid estimate specific to small-scale systems. A key aspect is the focus on BTU and gallons per minute, which are accessible metrics for those who may not have advanced technical backgrounds. This formula's simple nature makes it popular for residential and light commercial applications.
However, while its simplicity is an advantage, it may not adequately capture nuances in steam conditions and heat losses, which could influence performance.
Advanced Calculations for Large Systems
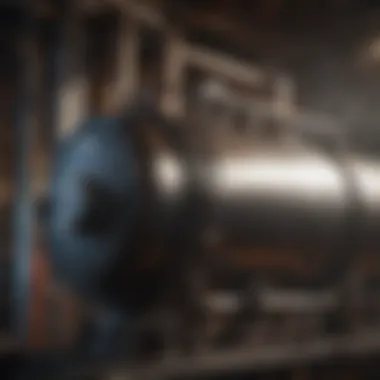

Larger boiler systems necessitate more sophisticated calculations, taking into account all variables, including feedwater conditions, steam quality, and operational pressures. Formulas that integrate these facets are vital. One such formula could look something like this:
[ Capacity (lb/hr) = \left(\fracPressure (psi) \times 3.73 \times 181000 \right) \times Boiler Efficiency ]
This equation highlights the importance of pressure and efficiency in ensuring accurate capacity estimations. The essential feature of such advanced calculations is the detailed adjustments they allow based on varying operational conditions. This depth makes it a beneficial choice for larger industrial applications where accurate modeling can significantly impact operational costs and safety. The complexity, however, requires a certain level of expertise, which can act as a barrier for some individuals or smaller operations without the proper resources.
Utilizing Software for Accurate Calculations
In today’s digital age, leveraging software tools for boiler capacity calculations has become commonplace. Programs specifically designed for this purpose are currently available, providing users with an efficient method to run scenarios at varying inputs. These software solutions streamline the calculations, ensuring that various aspects such as energy input, type of fuel, and system efficiency are seamlessly integrated.
The benefits extend to enhanced accuracy and ease of use. While the initial learning curve might present challenges, the long-term gains in reliability and decreased manual error are well worth the investment. Often, these programs also come equipped with compliance and regulatory tracking features, keeping users informed about industry standards efficiently.
Common Mistakes in Capacity Calculations
Understanding the common pitfalls in boiler capacity calculations is paramount for anyone involved in the selection, operation, and maintenance of boilers. Errors in calculating capacity can lead to undesirable consequences, from inefficiencies in energy use to potential safety hazards. Addressing these pitfalls not only improves operational effectiveness but also ensures compliance with safety regulations, optimizing the both performance and reliability of boiler systems. Below are three prominent mistakes commonly observed in practice.
Underestimation of Steam Demand
Underestimating steam demand is one of the more frequent errors that boiler operators encounter. When calculating the needed capacity, one might misjudge the actual steam requirements of a facility. This miscalculation can stem from various factors such as:
- Inaccurate Assessment of Processes: Sometimes, the complexities of different processes requiring steam aren't fully understood. This leads to errors in assessing the real demand, causing a potential deficit during peak operational times.
- Neglecting Future Expansion: Operators may focus on present needs without considering future growth. Businesses might expand, leading to increased steam needs that an underestimated boiler immediately cannot meet.
If the steam demand is consistently underestimated, it can lead to:
- Inadequate supply for heating or process needs.
- Increased stress on the boiler system.
- Potential safety risks due to fluctuating pressures.
Ignoring Heat Losses
Another crucial mistake is the outright neglect of heat loss during the calculations. Heat losses can occur through various channels, including:
- Insulation Inefficiencies: Poorly insulated pipes and system components can release heat, diminishing overall efficiency.
- Ventilation Losses: Systems that vent steam unnecessarily contribute to lost energy and resources.
Ignoring these losses can result in significant overestimation of the boiler capacity needed, leading to:
- Oversized equipment, which might operate inefficiently.
- Increased operational costs due to wasted energy.
- Challenges in maintaining optimal temperature levels within the system.
Miscalculating Thermal Efficiency
Miscalculating thermal efficiency is a mistake that can often go unnoticed but carries significant consequences. Factors that contribute to poor thermal efficiency include:
- Fuel Quality Variability: The energy content in different fuel types fluctuates. Not accounting for this can skew efficiency calculations.
- Combustion Issues: Inconsistent combustion conditions can lead to incomplete combustion and loss of heat energy.
Inaccurate thermal efficiency metrics can lead to:
- Improper sizing of the boiler.
- Increased fuel consumption, thus escalating costs.
- Difficulties in reaching and maintaining regulatory efficiency standards.
"The difference between a well-optimized boiler system and a poorly calculated one can be vast, affecting both the bottom line and regulatory compliance."
Recognizing these common pitfalls is essential for engineers, facility managers, and anyone involved in boiler applications. By actively addressing the underestimation of steam demand, heat losses, and thermal efficiency calculations, one can avoid costly mistakes and foster a safer, more efficient operational environment.
Applications of Boiler Capacity Calculations
Understanding the applicability of boiler capacity calculations is crucial in various contexts. These calculations are not just an academic exercise; they play a vital role in real-world situations impacting industries, households, and commercial entities alike. Precision in determining boiler capacity can lead to enhanced operational efficiency, better cost management, and compliance with safety regulations. Let's delve into specific areas where accurate capacity calculations matter greatly.
Industrial Usage of Boilers
In industrial settings, boilers are often the workhorses of the plant, providing steam necessary for numerous processes. However, the sheer scale of operations demands that boiler capacity be calculated meticulously. Where a miscalculation might seem trivial, in practice, it can lead to:
- Production Downtimes: Insufficient steam supply can halt production processes. Industries such as food and beverage, textiles, and pharmaceuticals rely heavily on precise steam availability for critical operations.
- Increased Energy Costs: On the flip side, oversized boilers can lead to unnecessary fuel consumption and higher utility bills. An accurately sized boiler optimizes fuel use, ultimately saving money.
- Equipment Longevity: A correctly calculated boiler minimizes operating stress and prolongs the life of both the boiler and associated equipment. This aspect is vital to maintain a reliable production environment.
Residential Heating Solutions
For homeowners, determining the right boiler capacity can be the difference between cozy winters and chilly discomfort. The application of boiler capacity calculations in residential settings manifests in several significant ways:
- Energy Efficiency: An accurately sized boiler ensures efficient heating while minimizing energy waste. Homeowners benefit from lower utility bills and reduced environmental impact.
- Comfort Levels: Whether it's heating water or maintaining comfortable indoor temperatures, the right capacity guarantees a consistent supply of warmth, enhancing comfort.
- Safety Considerations: A boiler that's too powerful for a home can create excessive pressure and present safety hazards. Knowing the accurate capacity helps maintain safe operating conditions and enhances household safety.
Commercial Applications
In commercial properties, boilers serve diverse functions – from providing hot water in restaurants to heating large office buildings. The nuances of commercial applications include:
- Operational Versatility: Various businesses may need differing amounts of steam or hot water depending on operations. Knowing how to calculate the right capacity ensures businesses remain responsive to dynamic demands.
- Regulatory Compliance: Businesses often face strict regulations regarding energy consumption and safety standards. Accurate capacity calculations aid in ensuring that commercial boilers comply with relevant local and federal laws.
- Cost Efficiency: Just like industrial applications, miscalculating boiler size in commercial setups can lead to inflated operating costs. Finding the balance between too little and too much capacity ensures financial feasibility.
Accurate boiler capacity calculations support a sustainable approach to energy use across all applications, from industrial plants to individual homes.
In summary, whether for industrial purposes, residential heating, or commercial needs, boiler capacity calculations shape the very foundation of effective boiler use. Each application underscores the importance of clarity and precision in ensuring operational success and safety. This critical focus not only guides immediate operational decisions but also informs long-term strategies and innovations in boiler technology.
Impact of Accurate Boiler Capacity Calculation
Accurate boiler capacity calculation is a cornerstone of effective boiler operation. This calculation does not just affect how much steam a boiler can produce; it plays a pivotal role in overall energy management within various systems. Proper capacity calculation ensures that the boiler matches the specific demands placed upon it, impacting operational performance, cost efficiency, and regulatory compliance.
Operational Efficiency
When it comes to operational efficiency, knowing the accurate capacity of a boiler can mean the difference between smooth sailing and a rough ride. A boiler that's undersized may struggle to meet the demands, leading to excessive wear and operational strain. This not only reduces the lifespan of the equipment but also results in increased maintenance costs.
On the flipside, an oversized boiler can lead to short cycling—where the boiler starts and stops frequently, wasting fuel and causing irregular operation.
Furthermore, accurately calculating the required capacity can facilitate alignment with current and projected operational demands. For instance, industries that see variable peak usage, like food processing plants during harvest season, need their boilers to adapt accordingly. Efficient operations lead to fewer operational hiccups, effectively driving productivity and enhancing the bottom line.


Cost Management
Cost management is another significant consideration that ties intricately with accurate boiler capacity calculation. When a boiler meets its capacity requirements, fuel consumption can be optimized. Higher efficiency translates directly to lower fuel expenses, which can be substantial over time.
Consider this: if a facility uses natural gas as a fuel source and its boiler operates at only 70% efficiency due to miscalculations, it not only leads to higher costs but also squandered resources. This often leads to unforeseen costs in both fuel and maintenance, which can be avoided.
Additionally, accurate calculations can assist in planning and budgeting for future expansions or upgrades. Knowing the precise requirements allows businesses to make informed investments instead of embarking on guesswork, thus preserving capital and avoiding excessive expenditures.
Safety and Compliance Standards
In the realm of safety and compliance, accurate boiler capacity calculations are non-negotiable. Boilers must operate within specific parameters dictated by local, national, and international regulations. For example, the ASME Boiler and Pressure Vessel Code sets strict rules for ensuring safety in pressure vessels.
From a safety standpoint, if a boiler is loaded beyond its designed capacity, it can lead to hazardous situations, such as explosions or leaks. Within this context, correct capacity calculations contribute to risk management and minimize liabilities associated with unsafe operations. The regulatory bodies require documentation and evidence of adherence to these standards; accurate capacity calculations become a vital element of proof in compliance audits.
"An accurate boiler capacity calculation not only optimizes performance but also strengthens safety protocols, keeping compliance on point and ensuring operational integrity."
In summary, understanding the impact of accurate boiler capacity calculation goes far beyond simple metrics. It envelops operational efficiency, cost management, and adherence to stringent safety standards. By approaching boiler capacity calculations with diligence and precision, industries not only optimize their systems but also create pathways for sustainable and responsible energy use.
Regulatory Standards in Boiler Operation
Navigating the complex landscape of boiler operations requires a firm understanding of regulatory standards. These regulations ensure not only operational efficiency but also safety and environmental protection. Compliance with established guidelines is essential for anyone involved in boiler management, from engineers to operators. The importance of such regulations can't be overstated as they set the groundwork for safe practices and operational excellence.
Establishing clear regulatory standards for boiler operations offers several benefits. Firstly, it helps minimize hazards associated with high-pressure steam systems. Regulations outline safety protocols, maintenance schedules, and operational limits that protect both workers and equipment. A solid understanding of these regulations can also reduce the risk of fines and legal penalties for non-compliance, a concern that should be on everyone’s radar.
In addition to safety, compliance contributes to the overall efficiency of boiler systems. Regulatory standards often require regular monitoring and audits, which can identify inefficiencies and areas for improvement. This, in turn, can lead to better fuel usage, improved output, and increased sustainability, making compliance beneficial not just for the bottom line but also for environmental stewardship.
"Standards are like an umbrella; they provide a framework that keeps us safe from the storms of operational risk."
Moreover, understanding regulatory standards allows for strategic planning. For instance, industries can anticipate changes in regulations and adapt their operations pro-actively. Making room in operational budgets for compliance measures can lead to long-term financial savings and decrease the likelihood of costly downtime.
International Regulations
International regulations in boiler operation embody globally recognized standards that govern safety and efficiency. Organizations such as the International Organization for Standardization (ISO) provide guidelines that companies can adhere to in various jurisdictions.
These regulations often encompass everything from design specifications to material selection for components, influencing how boilers are constructed and operated. Moreover, international standards facilitate trade and commerce, allowing manufacturers and operators to engage in cross-border transactions with greater assurance of compatibility and safety.
Some notable international standards include:
- ISO 16528 - Classification of steam boilers
- ASME Boiler and Pressure Vessel Code (BPVC) - Setting safety standards for pressure vessels
- IEC standards for electrical components in boiler systems
By aligning with international regulations, businesses can not only enhance their reputations but also foster trust among clients and partners across the globe.
Local Compliance Requirements
On a more localized scale, compliance requirements vary widely based on jurisdiction and industry. Local governments set specific guidelines tailored to regional needs, climatic conditions, and applicable technologies. As such, operators must familiarize themselves with these unique requirements, ensuring their systems meet all standards before commencing operations.
Local compliance requirements typically include aspects such as:
- Permitting processes
- Emission limits
- Inspection and maintenance schedules
- Training and qualification standards for personnel
Ignoring local compliance can lead to serious consequences, including operational shutdowns, hefty fines, or, worse yet, accidents that could threaten lives and property. Therefore, thorough knowledge and active engagement with local authorities regarding these requirements are fundamental to successful boiler operations.
By integrating both international and local standards into operational frameworks, businesses can create a robust structure that supports safety, efficiency, and environmental responsibility. Proper diligence in understanding and implementing these standards sets the stage for not just compliance, but for achieving operational excellence.
Future Trends in Boiler Technology
The field of boiler technology is constantly evolving, responding to the demands of modern energy systems and tightening regulations. Future trends are not just pivotal for manufacturers and engineers; they are crucial for ensuring that industries can operate efficiently and sustainably. As environmental concerns grow, the integration of newer technologies is not only a smart move but a necessary one. This section explores advancements that influence energy efficiency and the integration of smart technologies in boiler systems.
Advancements in Energy Efficiency
Energy efficiency stands out as a primary focus in boiler technology. With the growing emphasis on sustainability, manufacturers are designing boilers that consume less fuel while providing superior output. Several advancements highlight this trend:
- Condensing Technology: Boilers equipped with condensing technology maximize energy extraction from flue gases, often achieving efficiency ratings over 90%. This significant boost minimizes energy waste and lowers operational costs.
- High-Efficiency Burners: These burners finely control the air-fuel mix, allowing for optimal combustion. This results in lower emissions and improved energy consumption rates.
- Improved Insulation Materials: The use of advanced materials helps reduce heat loss, further enhancing overall boiler efficiency. Insulating boilers effectively is essential to maintain desired temperatures without wasteful heat dissipation.
A study on energy performance improvement in heating systems indicates that organizations adopting high-efficiency systems can see a notable 20% reduction in energy costs, leading to quicker ROI. Thus, energy efficiency advancements are not merely beneficial; they are essential for competitive viability in the market.
Integration of Smart Technologies
As industries continue to embrace the Internet of Things (IoT), the integration of smart technologies into boiler systems offers unprecedented capabilities. These innovations not only streamline operations but also facilitate better decision-making and resource management. Consider the following aspects of smart technology integration:
- Real-Time Monitoring: Smart boilers are equipped with sensors that monitor various parameters like pressure, temperature, and efficiency metrics in real-time. This ongoing analysis allows for immediate response to any irregularities, preventing potentially costly downtimes.
- Predictive Maintenance: Using data analytics, modern boiler systems can predict maintenance needs before failures occur. This preemptive approach significantly reduces the risks of unexpected breakdowns and the associated financial loss.
- Remote Control and Automation: Operators can manage boiler functions remotely via smart interfaces, accessing insights and making adjustments without needing to be physically present. This streamlining can enhance overall operational efficiency.
In sum, integrating smart technologies into boiler systems represents a new frontier aimed at achieving better sustainability goals and operational effectiveness.
"The future of boiler technology lies in its ability to adapt and evolve with energy efficiency and smart integration at its core."
Closure
At this stage of our exploration into boiler capacity calculation, we find ourselves at a pivotal moment. The conclusions drawn from the discussions throughout this guide offer substantial insights into the importance of precise capacity calculations. These insights not only underscore the necessity of technical accuracy but also reflect on real-world implications.
Recap of Importance
To recap, accurate boiler capacity calculation serves as the backbone of effective thermal system design. As we’ve seen, it impacts various aspects such as:
- Operational Efficiency: An accurately sized boiler functions optimally, minimizing energy waste and promoting overall system performance.
- Cost Management: Correct calculations can significantly reduce operational costs by preventing over-specification that leads to unnecessary fuel consumption.
- Safety and Compliance: Following established capacity standards ensures compliance with industry regulations, which safeguards personnel and equipment.
The interplay of these components illustrates why neglecting boiler capacity determination isn’t just an oversight; it’s a path fraught with potential consequences that can ripple through operations.
Final Thoughts
Ultimately, these calculations are more than just numbers on a page—they represent a commitment to efficiency, safety, and responsible engineering practices. With the right knowledge and tools, you can ensure that every boiler operates within its optimal capacity, directly contributing to a sustainable future in energy management.
"In the realm of thermal systems, accuracy is not just a luxury; it is a necessity that drives success."