In-Depth Look at 1018 Cold Rolled Steel Properties
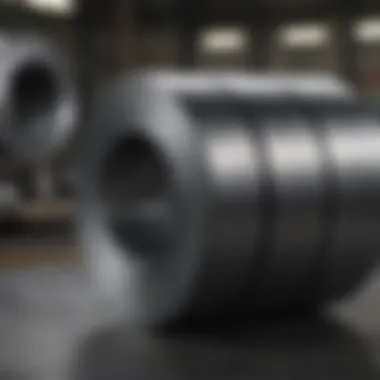
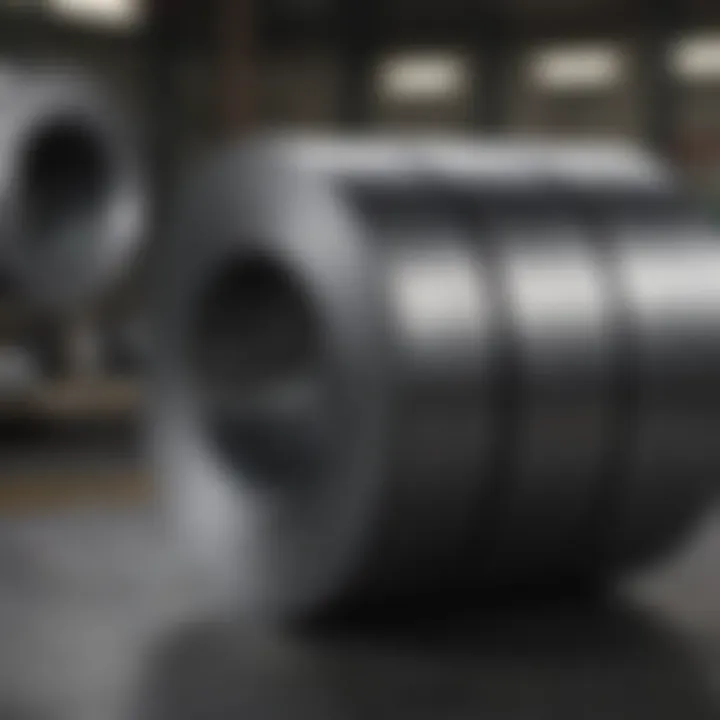
Intro
Understanding the properties of materials is crucial, particularly in fields like engineering and manufacturing, where precision and performance hold paramount importance. Among a multitude of materials, 1018 cold rolled steel stands out due to its favorable characteristics and versatility. This steel type, known for its excellent combination of strength, ductility, and machinability, is widely adopted across various applications.
Through this article, we aim to dissect the nature of 1018 cold rolled steel, leading readers to a greater appreciation of what makes this material pivotal in the industries it serves. We delve not only into the fundamental properties and mechanical traits but also into the intricacies of its chemical composition. This exploration sheds light on how each element contributes to the overall performance of the steel, equipping both novices and skilled professionals alike with a necessary understanding of this essential material.
With the groundwork laid, we will venture into key concepts, terminology, and findings that underpin the significance of 1018 cold rolled steel.
Foreword to Cold Rolled Steel
The exploration of 1018 cold rolled steel is crucial in understanding its pivotal role in various engineering applications. This steel grade, known for its strength and versatility, forms the backbone of countless industrial, commercial, and construction projects. It is not merely a component; it is often the foundation upon which larger constructs are built, serving as a critical element across a range of fields. By delving into the specifics of this material, from its historical roots to its present-day applications, we can better grasp its significance and utility.
Historical Context
1018 cold rolled steel has a rich history that dates back to the post-industrial revolution era, a time when the demand for materials with enhanced mechanical properties surged. Originating from the basic composition of iron with a small percentage of carbon—typically around 0.18%—this steel provided the necessary strength without making it overly brittle.
In earlier times, when construction relied heavily on wrought iron, the advent of cold rolled processes allowed for improved hardness and surface finishes. Blacksmiths and metal workers alike hailed the better workability and predictability that 1018 offered. It set a benchmark for subsequent steel grades, paving the way for innovations in both metallurgy and manufacturing.
Interestingly, the historical landscape of steel manufacturing reflects shifts in society's needs, whether it be for the war machine in the mid-20th century or the skyscrapers that now dominate our metropolis skylines. As industries evolved, so did the characteristics and applications of 1018 steel, making it indispensable through decades of change.
Relevance in Modern Applications
In today’s landscape, 1018 cold rolled steel remains a go-to choice due to its remarkable properties, which lend it well to a myriad of applications. From automotive parts to machinery components, the relevance of this steel in modern engineering cannot be understated. Here are a few areas where its impact is especially salient:
- Industrial Uses: The strength of 1018 makes it ideal for manufacturing gears and axles that require reliability under stress.
- Construction Applications: Beams and structural supports often leverage the properties of this steel to ensure safety and durability.
- Automotive Industry: It finds a home in the automotive sector for producing parts that demand precision and resilience.
Furthermore, the cold rolling process contributes to a thinner, more manageable material without sacrificing its inherent strength. The result is a steel that is not only functional but also efficient in terms of cost, which, in a market driven by budget considerations, enhances its attractiveness.
In summary, the journey of 1018 cold rolled steel from its historical origins to its invaluable role in contemporary applications underscores its importance in materials science. By understanding its evolution, properties, and ongoing relevance, we can appreciate why this particular grade of steel stands the test of time.
Chemical Composition of Steel
Understanding the chemical composition of 1018 cold rolled steel is crucial for anyone looking to grasp its potential and limitations in various applications. The blend of elements in this steel not only defines its physical properties but also impacts its performance in real-world scenarios. Key elements like carbon, manganese, phosphorus, and sulfur each bring unique features that cater to specific uses of the steel in industries ranging from automotive to manufacturing.
Elements and Their Functions
In the realm of 1018 steel, several elements play a pivotal role. Each contributes to the overall characteristics of the steel, as outlined below:
- Carbon (C): At about 0.18% composition, carbon is the heart and soul of steel. It enhances tensile strength and hardness but can also affect ductility if present in excess.
- Manganese (Mn): Manganese is included at approximately 0.60% to 0.90%. It acts as a deoxidizer and helps in improving hardness and strength. Manganese also enhances the steel's hardenability.
- Phosphorus (P): This element typically appears in very small amounts (around 0.04%). While it can strengthen steel, excess phosphorus can lead to brittleness, making it a double-edged sword that manufacturers must manage carefully.
- Sulfur (S): Likewise, sulfur is present in very minute quantities (up to 0.05%), mainly to enhance machinability. Too much sulfur, however, can negatively impact ductility.
- Iron (Fe): The bulk of the composition is, of course, iron, which forms the base of steel, contributing to its percentage and overall formation.
The interaction between these elements results in a material that balances various essential properties, making 1018 cold rolled steel a versatile choice in many applications.
Impact of Alloying Elements
Alloying elements in 1018 steel affect how it behaves under different conditions. Here’s what you need to know about their impact:
- Strength and Ductility: The interplay of carbon and manganese is critical. More carbon improves hardness but could compromise ductility. Therefore, careful concentration is essential for achieving the right balance.
- Machinability: Sulfur enhances machinability, allowing for easier shaping and cutting. This feature is vital for manufacturing components where precision is key.
- Heat Treatment Respond: Elements like manganese and carbon also influence how 1018 steel responds to heat treatment, determining resilience and performance in high-temperature environments.
- Corrosion Resistance: While 1018 does not have significant inherent corrosion resistance, knowing the balance of alloying elements helps engineers predict how the steel might react when exposed to harsh environments.
Ultimately, recognizing how these elements contribute to the properties of 1018 cold rolled steel allows materials engineers and fabricators to leverage its benefits and mitigate any drawbacks effectively.
Mechanical Properties
Mechanical properties of 1018 cold rolled steel are crucial to understanding its practical applications and its performance in diverse environments. These properties dictate how the material behaves under various stresses and conditions, making them vital for engineers and manufacturers who rely on informed material selection.
The key mechanical properties include tensile strength, ductility, toughness, and hardness. Each of these aspects plays a significant role in determining the suitability of 1018 cold rolled steel for specific uses. For instance, its tensile strength informs us about how much load the steel can bear without failing, while ductility and toughness shed light on how the steel performs under bending or impact. Together, they reflect how this steel can be manipulated during processing and how it will endure in real-world applications, ensuring reliability and safety.
Tensile Strength
In simple terms, tensile strength represents the maximum stress that a material can endure while being stretched or pulled. For 1018 steel, this property is particularly significant; it generally exhibits a tensile strength that ranges from 440 to 640 megapascals (MPa).
This level of strength is often sufficient for a variety of applications, making 1018 steel a favored choice in manufacturing gears, shafts, and general fabrication work. When pulling the steel apart, the ability of the material to withstand high stress levels before yielding ensures that it can perform in demanding situations without compromising structural integrity.
In industries where performance matters, understanding the tensile strength of materials like 1018 steel allows for better design and product development.
Ductility and Toughness
Ductility refers to the material's ability to deform under tensile stress, while toughness combines ductility with resistance to fracture. 1018 cold rolled steel offers a good balance between these two characteristics. The ductility of this steel allows for significant deformation before rupture occurs, an important trait for manufacturing processes such as welding, bending, and machining.
However, toughness is equally important — especially for components exposed to impact or dynamic stresses. 1018 steel has a Charpy impact value that indicates it can absorb energy without fracturing, which makes it more reliable in applications where resilience to shocks is necessary, like in automotive frames or heavy-duty equipment parts.
Hardness Characteristics
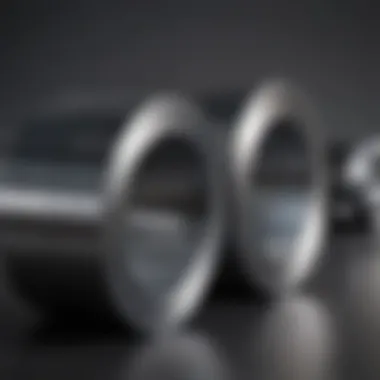
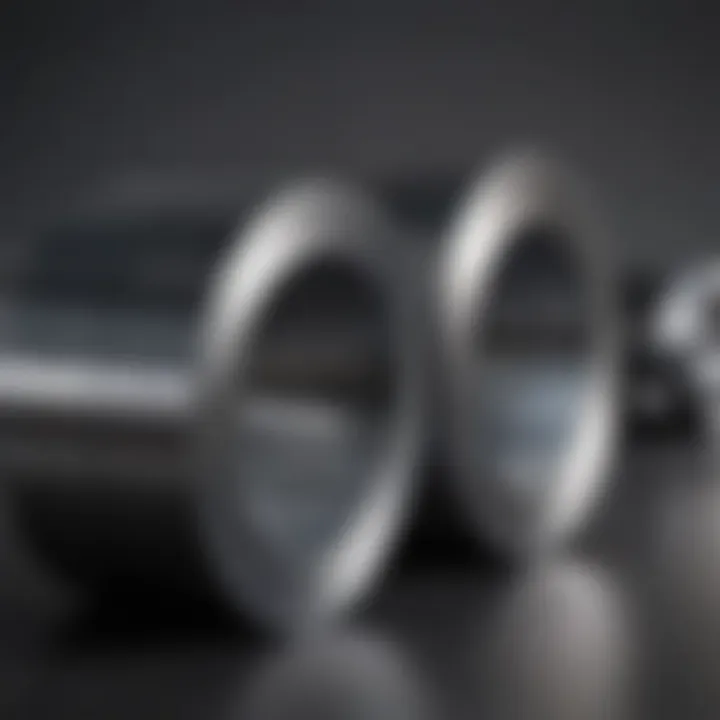
Hardness in materials like 1018 cold rolled steel usually refers to its resistance to deformation and wear. This steel typically has a Rockwell hardness value ranging around 70 to 90 HRB, indicating it can withstand various forms of mechanical wear and tear.
The hardness characteristic is beneficial for parts that need to endure abrasive conditions. And while high hardness can sometimes mean lower ductility, 1018 balances these traits effectively, ensuring it can be used in many situations without compromising overall performance. This balance enables precision machining, helping to achieve fine tolerances in production.
In summary, grasping the mechanical properties of 1018 cold rolled steel equips stakeholders with the information necessary for making informed decisions, whether for manufacturing purposes or structural applications.
Thermal Properties
Understanding thermal properties is crucial when it comes to working with metals like 1018 cold rolled steel. These properties significantly affect how the material performs under a range of temperatures, influencing both its usability in engineering applications and its behavior during manufacturing processes.
When it comes to thermal properties, consider the following points:
- Heat Treatment Capabilities: Heat treatment can enhance the mechanical characteristics of 1018 steel. The right heat treatment can improve its hardness, tensile strength, and ductility, making it more suitable for demanding applications.
- Thermal Conductivity: This property indicates how well 1018 steel can conduct heat. Knowing the thermal conductivity is essential for applications where heat dissipation is necessary, like in machinery components.
- Thermal Expansion and Contraction: Steel expands when heated and contracts upon cooling. If not properly accounted for, this can lead to structural issues.
These thermal characteristics contribute to the overall performance of 1018 cold rolled steel, making it a versatile choice for many applications.
Heat Treatment Effects
Heat treatment alters the physical and sometimes chemical properties of 1018 cold rolled steel, enhancing its performance for certain tasks. The process itself involves heating and cooling the material in a controlled manner. Here's a breakdown of some effects:
- Quenching: Rapid cooling from a high temperature increases hardening. This means after quenching, the steel can achieve higher hardness values, but it may become less ductile.
- Annealing: In contrast, annealing involves heating followed by a gradual cooling process. This step softens the steel, removing stresses and improving ductility while also enhancing machinability.
- Tempering: Post-quenching, tempering helps relieve internal stresses and reduce brittleness, striking a balance between hardness and toughness.
Overall, understanding the heat treatment effects allows engineers to tailor 1018 steel to meet specific demands in manufacturing or construction settings.
Thermal Conductivity
Thermal conductivity measures how effectively heat travels through a material. For 1018 cold rolled steel, this property is vital for several reasons:
- Efficiency in heat management: In applications where components are exposed to significant thermal loads, knowing thermal conductivity can guide design choices to prevent overheating.
- Material selection: When comparing 1018 to other materials, thermal conductivity can influence decisions. For example, its moderate conductivity compared to aluminum or copper might make it more suitable for structural parts instead of heat exchangers.
- Influence on processing: During processes such as welding, a keen understanding of thermal conductivity assists in predicting how heat will penetrate and affect the material.
Manufacturing Processes
The manufacturing processes of 1018 cold rolled steel are crucial to understanding how this material is shaped and transformed for use across various industries. These processes are not just about turning raw metal into usable forms; they also significantly influence the material’s mechanical properties and overall performance. Understanding the specific methods applied in manufacturing provides insight into how to best utilize this steel type in different applications.
The cold rolling of steel, for example, can enhance its strength without compromising its ductility, making it ideal for numerous applications where both properties are required. Moreover, exploring various fabrication techniques reveals the flexibility and adaptability of 1018 cold rolled steel in responding to specific industry demands.
Cold Rolling Techniques
Cold rolling is a method that involves passing steel through rolls at or near room temperature which reshapes the metal without heating it up first. This process brings a number of important advantages, such as improved tensile strength and surface finish. Here are some key highlights of cold rolling techniques:
- Strength Enhancement: Cold rolling increases the yield strength and hardness due to strain hardening, making it suitable for applications that require higher durability.
- Thickness Control: Manufacturers can achieve high precision in the thickness of the steel, allowing for better quality control in production.
- Surface Quality: Cold rolled steel generally presents a smoother surface compared to hot rolled steel, which is crucial for processes where aesthetics matter or the finish needs to be painted or coated.
- Less Waste: The cold rolling process can minimize material waste, ultimately lowering production costs.
While cold rolling has several benefits, it’s important to note that it can lead to residual stresses within the steel. Those stresses could have implications during subsequent fabrication or usage, necessitating proper handling and treatment.
Common Fabrication Methods
Once the cold rolling process is completed, several common fabrication methods can be employed to shape and adapt 1018 cold rolled steel to its intended application. Some of the most notable methods include:
- Cutting: Various cutting methods, like laser cutting and shearing, provide precise shapes and sizes necessary for component integration, impacting the overall performance of assembled products.
- Bending: Bending techniques, whether cold or hot, allow for the formation of components requiring specific shapes, such as brackets or frames. This alteration improves the versatility of 1018 steel in different structures.
- Forming: Processes such as stamping or rolling can create intricate shapes, further pushing the boundaries of material application and design possibilities.
- Machining: Employing techniques like milling or turning provides the precision necessary for tight tolerances, especially where intricacy is paramount, like in mechanical components.
- Welding: Joining different pieces of 1018 cold rolled steel is commonly done through welding, where considerations regarding heat input are critical to avoid compromising strength.
In light of these methods, the ability to adapt 1018 cold rolled steel through various means boosts its relevance in the manufacturing landscape. Thus, understanding manufacturing processes not only demystifies steel production but also enhances the ability to apply this material effectively across multifaceted applications.
"The precise understanding of manufacturing processes is key to maximizing material performance and longevity in demanding environments."
With continuous advancements in past and current manufacturing techniques, it's clear that 1018 cold rolled steel remains a competitive material suitable for both traditional and innovative applications.
Applications of Cold Rolled Steel
The applications of 1018 cold rolled steel are paramount in various fields, showcasing its versatility and practical benefits. In an era where the emphasis on efficiency and performance is more pertinent than ever, understanding where and how this material is utilized can shed light on its significance in everyday life and industrial practices.
Notably, 1018 steel is characterized by its balance of strength and ductility, making it a go-to choice for engineers and manufacturers. The material’s unique attributes allow for its use in both critical and non-critical applications, transcending beyond mere structural uses to more intricate designs in modern machinery and tools. Below is an in-depth exploration of its applications across different industries, covering specific elements and considerations that highlight its practicality.
Industrial Uses
In industrial settings, 1018 cold rolled steel plays a crucial role due to its ease of fabrication and ability to withstand various stresses. One of its most notable applications is in manufacturing components for machinery.
- Key Elements: The fine surface finish achieved through cold rolling enhances machinability and weldability, making it suitable for numerous components like shafts, gears, and brackets.
- Benefits: Utilizing 1018 in these applications allows for reduced wear and tear, ultimately leading to longer service life and lower downtime in manufacturing operations. This is especially relevant in environments where machinery is subjected to frequent use and varying load conditions.
Overall, its strong performance characteristics serve to fulfill stringent operational requirements while maintaining cost-effectiveness in production processes.
Construction Applications
1018 cold rolled steel is also a staple in the construction industry, where its properties contribute significantly to structural integrity. Engineered components made from this steel are found in various types of constructions, from residential buildings to complex infrastructure projects.
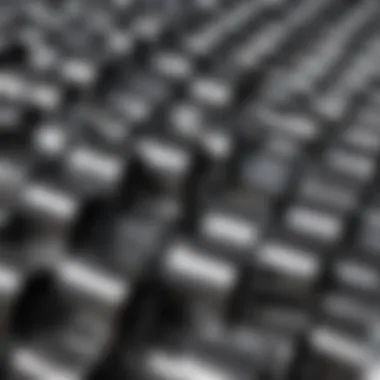
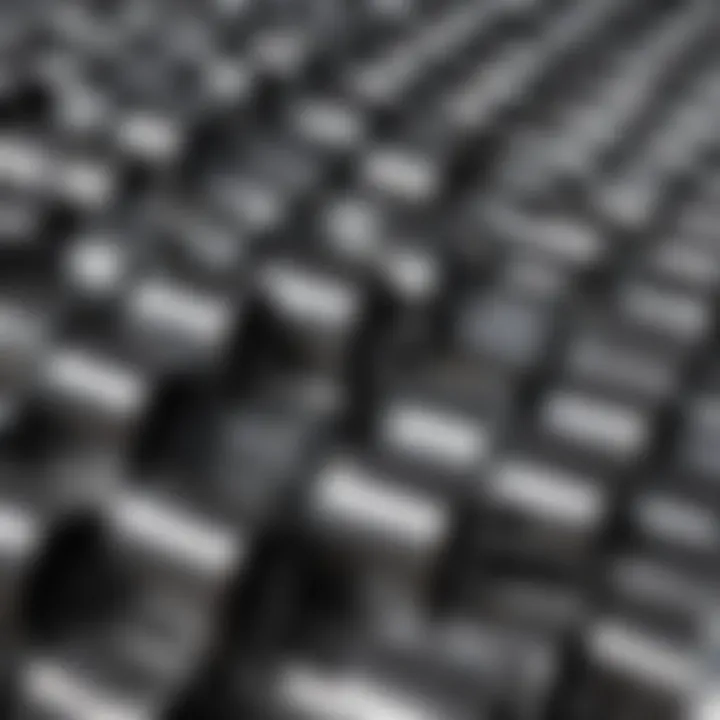
- Typical Uses: It’s commonly utilized for structural supports, reinforcements, and in the fabrication of frames for machinery that functions within construction sites.
- Considerations: When selecting materials, engineers must carefully weigh factors like load capacity and corrosion resistance, especially when the steel will be exposed to harsh weather conditions or varying environmental factors.
The adaptability of 1018 steel allows it to conform to different design specifications, thereby broadening its applicability in both new constructions and retrofitting existing structures.
Automotive Industry Applications
The automotive sector is another realm deeply reliant on 1018 cold rolled steel. From fabricating individual parts to entire assemblies, its influence is pervasive and essential for performance and safety.
- Components Utilized: Common applications include frames, axles, and suspension systems. The inherent strength of 1018 enables it to withstand the dynamic stresses experienced during vehicle operation.
- Industry Implications: Automakers seek materials that provide both safety and efficiency. Here, the properties of 1018 cold rolled steel play a pivotal role in enhancing vehicle durability while minimizing weight, ultimately aiding in fuel efficiency.
Comparison with Other Steels
The significance of comparing 1018 cold rolled steel with other steel grades is multi-faceted. By understanding the distinctions, advantages, and drawbacks of each type, one can make informed decisions in material selection for various applications. Comparison sheds light not only on mechanical properties but also on the economic implications, availability, and suitability for specific functions in real-world scenarios. In sectors like construction and manufacturing, where safety and performance hinge on material properties, this insight is invaluable.
Comparison with Steel
1010 steel, akin to its 1018 counterpart, is often used as a standard for low carbon steels. The main divergence lies in the carbon content—1010 steel has a carbon composition ranging around 0.10%, while 1018 steel floats between 0.15% to 0.20%. This seemingly minor difference has substantial impacts in practical applications.
- Strength: The higher carbon content in 1018 steel translates to increased tensile strength and hardness compared to 1010 steel. Consequently, 1018 is better suited for applications demanding higher wear resistance.
- Ductility: Despite being stronger, 1018 steel maintains good ductility, making it easier to form and shape without cracking, unlike some higher carbon steels.
- Machinability: When it comes to machinability, 1010 tends to be advantageous for certain tasks due to its lower hardness.
In selecting between these grades, one must consider the balance of strength and workability, tailoring the choice to the specific needs of the task at hand.
Comparison with Steel
Moving up the carbon content scale, 1020 steel incorporates around 0.20% to 0.25%. This increase aligns it closely with 1018 in terms of mechanical properties, yet the subtle differences make a noteworthy impact.
- Yield Strength: 1020 steel generally offers a slightly higher yield strength, enhancing its performance in load-bearing scenarios. However, this comes with a trade-off in ductility when compared to 1018.
- Thermal Treatment: Further heat treatments might elevate the performance of both grades, but their responses can vary significantly.
- Applications: 1020 is often favored in applications that demand higher strength and fatigue resistance, like parts subjected to dynamic loads. Alternatively, 1018 might still win out in flexibility and ease of fabrication.
In the grand scheme of things, the choice between 1018 and 1020 lies within the context of the intended application.
Advantages and Disadvantages
When assessing 1018 cold rolled steel against these other variants, it’s crucial to weigh the pros and cons. Here’s a quick rundown:
Advantages:
- Versatile: Adaptable for a variety of applications from simple structures to intricate machinery parts.
- Good Balance of Strength and Ductility: It provides a commendable mix of mechanical properties, making it user-friendly for both machining and forming processes.
- Cost-effective: Generally more affordable than higher-carbon counterparts, making it an attractive choice for budget-conscious projects.
Disadvantages:
- Limited Corrosion Resistance: It may require additional protective measures to fend off rust in humid or corrosive environments.
- Work Hardening: While it can take some abuse, repeated work hardening can make future machining more challenging, especially in complex parts.
- Brittleness in Extreme Conditions: In environments where temperatures plummet, its performance can wane, demanding careful engineering considerations.
Corrosion Resistance Factors
Corrosion resistance is an indispensable aspect to consider when dealing with 1018 cold rolled steel. This property defines how well the steel can withstand degradation caused by environmental elements, an important factor especially for applications in hostile settings. Rust can sneak in quietly, but once it takes its grip, it can lead to structural failures and potentially costly repairs. Accordingly, understanding corrosion resistance factors is vital for maintaining the longevity and performance of this steel in various applications.
Impact of Environmental Factors
Environmental factors can play a significant role in the corrosion resistance of 1018 cold rolled steel. Several elements contribute to this, including exposure to moisture, temperature variations, and even the atmospheric composition where the steel is situated.
- Moisture: Water is a prime catalyst for rust. When 1018 steel is exposed to moisture, especially when in contact with salts or acidic substances, this can accelerate its corrosion process. This is often seen in coastal areas where saline environments prevail.
- Temperature: Fluctuations in temperature can also affect corrosion rates. Higher temperatures may increase the speed of electrochemical reactions that lead to rust formation.
- Atmospheric Composition: Industrial areas may have higher levels of pollutants, which can create aggressive conditions for corrosion. For instance, the presence of sulfur dioxide in the air can generate acids when combined with moisture, thus enhancing the corrosive potential on steel.
It is not just about the steel itself; understanding the surroundings is crucial. It’s like trying to protect a delicate flower; knowing the climate helps to choose the right care tips.
Protective Coatings
To counteract the risks posed by corrosion, various protective coatings can be utilized with 1018 cold rolled steel. These coatings function as a barrier, shielding the underlying metal from environmental hazards. Some of the most commonly used protective coatings include:
- Paint Systems: Applying a robust paint system can offer a reliable line of defense against moisture. Selecting high-quality paints designed for metal surfaces may drastically reduce the risk of rust. However, these need to be reapplied periodically to maintain their effectiveness.
- Galvanization: This method involves coating the steel with zinc, which acts sacrificially. Even if the zinc layer gets scratched, it will corrode before the steel does, thus prolonging the life of the steel underneath.
- Epoxy Coatings: These coatings provide excellent adhesion and resistance to chemical attack. An epoxy layer can withstand harsh conditions and significantly improves the service life of 1018 steel.
Protective coatings not only enhance the lifespan but also help maintain the aesthetic appearance of the steel structures.
In summary, understanding both environmental factors that impact corrosion and the protective measures we can use is critical in ensuring that 1018 cold rolled steel serves its purpose effectively and efficiently. Without attention to these points, one might as well be throwing good money after bad, watching their investment erode over time.
Joining Techniques
Joining techniques play an integral role in the application of 1018 cold rolled steel, as they dictate how various components are united to create finished products. Understanding these methods is paramount for professionals in engineering and manufacturing fields, as the chosen technique can significantly affect the material’s final properties, structural integrity, and overall performance. Each method has its own sets of benefits and considerations, which one must be thoroughly aware of when working with this versatile steel.
Welding Considerations
Welding is often the go-to method for joining metals, thanks to its ability to produce strong, durable bonds. When working with 1018 cold rolled steel, several important factors must be taken into account to ensure a successful weld:
- Material Preparation: The surfaces that will be joined need to be clean and free from contaminants. Removing rust, grease, or any residue is essential to achieving a good weld. Even the slightest impurity can create weak points.
- Welding Technique: Different welding techniques, such as MIG (Metal Inert Gas) or TIG (Tungsten Inert Gas), can be applied to 1018 steel, each offering unique advantages. MIG is often favored for its speed and ease, while TIG delivers precision that’s invaluable in intricate projects.
- Heat Affected Zone (HAZ): When welding, the heat can change the properties of the steel in the surrounding area. Becoming familiar with managing the HAZ ensures that the weld retains its strength and that the material nearby is not compromised by excessive heat.
- Filler Material: Selecting an appropriate filler material is crucial, especially if the applied filler has differing properties. The compatibility of the filler with 1018 steel lies at the heart of achieving uniform strength across the joint.
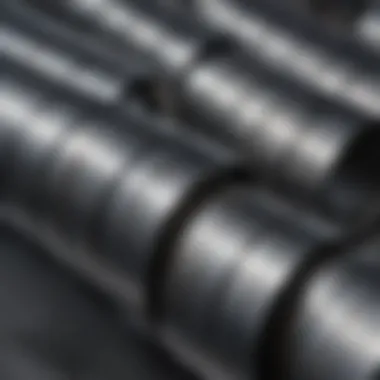
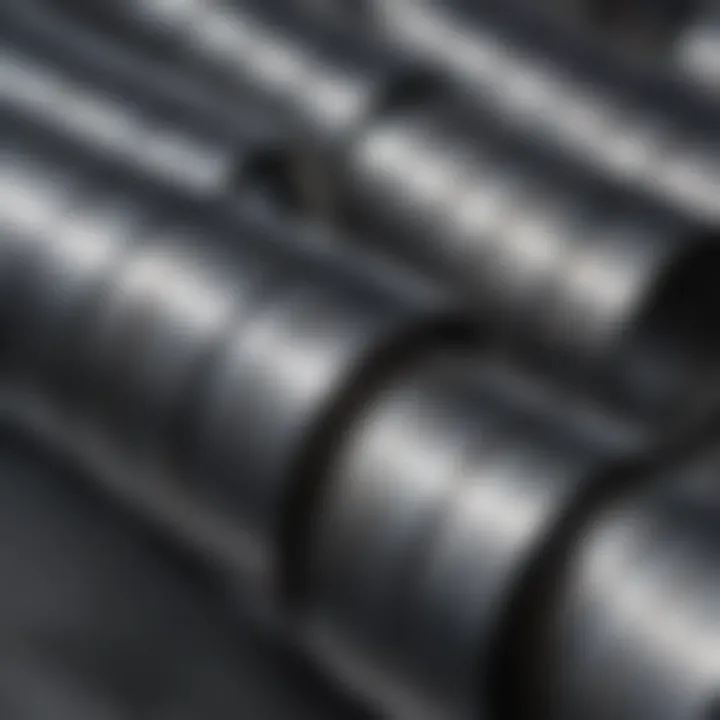
These considerations represent just the tip of the iceberg, but they highlight why welding demands skilled hands and a practiced eye. A slight oversight can lead to defects that are costly to rectify.
Brazing and Soldering
Brazing and soldering are alternative joining techniques that can also be utilized with 1018 cold rolled steel, especially in situations where welding might not be viable or desirable. Each of these methods offers distinct benefits:
- Brazing: This method utilizes a filler metal that melts above 450 °C without melting the base materials. Brazing promotes a joint that can withstand high temperatures and resist thermal shock. The process allows for greater design flexibility, a crucial element when dealing with various geometries.
- Applications: It finds prevalent usage in situations like joining dissimilar metals where welding would lead to complications. One common use case is assembling piping systems where different materials might be combined, minimizing corrosion risk.
- Soldering: Generally used for lower strength requirements, soldering involves a filler metal that melts at lower temperatures (below 450 °C). This method is useful for electronic and electrical applications, offering an effective bond while ensuring heat-sensitive components aren't damaged.
- Ease of Execution: Brazing and soldering can often be accomplished with simpler equipment compared to welding, making them accessible for smaller shops or DIY enthusiasts. However, it’s necessary to ensure that the joint does not become compromised, particularly in high-stress applications.
In both brazing and soldering, attention to detail is crucial to ensure that a strong bond is achieved while maintaining the integrity of the steel. Understanding the thermal properties of 1018 cold rolled steel in these processes aids in making informed decisions, ultimately leading to successful applications.
Economic Considerations
The economic aspects of 1018 cold rolled steel are crucial not just for manufacturers but also for anyone involved in industries that rely on this material. Understanding these elements can help in making informed decisions about procurement, production, and overall project management.
Cost Analysis
When we talk about the costs associated with 1018 cold rolled steel, several factors come into play. The price of steel, including 1018, can fluctuate based on market demand, raw material availability, and economic conditions around the globe.
- Material Costs: The base price of 1018 cold rolled steel is fundamental. Factors such as the cost of iron ore, labor, and energy influence this directly. In a market where iron ore prices soar, the cost of steel could follow suit, impacting the budgets of projects dependent on this material.
- Processing Costs: The techniques applied during manufacturing, like cold rolling, also add to the expenses. Cold rolling involves significant energy expenditure and specialized machinery which can ramp up production costs. As a result, it's vital for manufacturers to weigh these costs against the final product's pricing strategy.
- Transportation Costs: Given that steel is often shipped over long distances, transportation can play a significant role in the overall cost structure. Factors such as fuel prices, freight rates, and logistics efficiency can greatly affect the final cost of acquiring 1018 steel.
- Market Fluctuations: Keeping an eye on the steel market trends is essential. During periods of high demand, prices tend to rise, making it important for businesses to time their purchases wisely and consider stockpiling when prices are lower.
Market Demand Trends
Examining market demand trends provides insights that are beneficial not only for those involved in the steel industry but also for businesses that utilize 1018 cold rolled steel in their operations.
- Industry Growth: Sectors such as automotive, construction, and manufacturing continuously drive demand for 1018 steel. As automakers innovate their designs and as infrastructure projects burgeon, the appetite for high-quality steel grows correspondingly.
- Emerging Technologies: Advancements in technology can lead to changes in demand patterns. For instance, trends like lightweight vehicle manufacturing might alter the preference for different steel grades, but the consistent need for 1018 remains due to its versatile properties.
"As the landscape of industry shifts, staying abreast of market demand trends ensures businesses adapt without losing ground."
- Economic Cycles: Demand for 1018 steel often reflects broader economic conditions. In booming economies, such demand typically rises sharply, while recessions can lead to significant slowdowns. Thus, manufacturers need to strategize by monitoring economic indicators that influence steel demand.
- Global Trade Dynamics: Trade agreements and tariffs can also have an impact on the availability and pricing of cold rolled steel. Keeping a close watch on international regulations will enable manufacturers to navigate these waters more effectively.
In summary, the economic considerations related to 1018 cold rolled steel encompass a multitude of factors affecting its cost and demand. By understanding these elements, industries can strategize effectively, ensuring they remain competitive and capable of meeting future challenges.
Future Prospects and Innovations
As industries continually evolve, the future prospects of 1018 cold rolled steel hold significant implications for engineering and manufacturing. This section delves deep into advancements in material science and sustainability aspects, exploring how these elements contribute to the future utility of this versatile steel. The ongoing efforts to improve performance, safety, and environmental benefits keep 1018 steel at the forefront of industry developments.
Advancements in Material Science
Material science is an ever-expanding field, and it's making waves when it comes to the enhancement of 1018 cold rolled steel. Researchers are looking into developing alloys that retain the core properties of 1018 while simultaneously improving its performance metrics.
One of the promising directions is alloying 1018 with elements such as titanium and vanadium. This could potentially elevate its strength-to-weight ratio without sacrificing ductility—a critical factor in applications where weight savings are essential. Furthermore, innovations in heat treatment processes could lead to novel techniques that refine the grain structure of 1018 steel, allowing for superior toughness and hardness. This addresses the need for materials that not only withstand high-stress environments but also have increased lifespans.
In addition to alloying and heat treatments, advancements in 3D printing technology are another angle of exploration. With the rise of additive manufacturing, there's potential for producing intricate steel components directly from powdered 1018 material. Such techniques might open doors to customized designs that traditional methods struggle to achieve, paving a new pathway for bespoke solutions in engineering.
Sustainability Aspects
In today’s climate-conscious world, sustainability isn't just a trend—it's a necessity. The manufacturing process of 1018 cold rolled steel is already being scrutinized, as companies strive to adopt greener practices. Reducing the carbon footprint during production processes can significantly enhance the sustainability of steel products.
One notable approach is the reclamation of scrap steel, which not only minimizes waste but also reduces energy consumption in production—creating a win-win situation. As companies become more mindful of their environmental impact, the circular economy model is gaining traction, promoting recycling and reusing materials wherever possible.
Moreover, innovations in eco-friendly coatings are emerging. These coatings can improve the corrosion resistance of 1018 steel while being less harmful to the environment compared to traditional options. Not only do these developments help in terms of sustainability, but they also extend the lifecycle of products made from 1018 steel, reducing the need for frequent replacements and further conserving resources.
"The steel industry faces challenges, but with innovation and commitment, the future of 1018 cold rolled steel looks promising for both performance and the planet."
In summary, the advancement in material science combined with a keen focus on sustainability paves the way for the continued relevance of 1018 cold rolled steel across diverse sectors. Engaging with these innovations ensures that the material not only meets current demands but is also well-prepared for the challenges of tomorrow.
By staying attuned to these developments, engineers, researchers, and students alike can grasp the significance of evolving materials like 1018 cold rolled steel in shaping the future of manufacturing.
Culmination
In wrapping up our exploration of 1018 cold rolled steel properties, it's pivotal to spotlight its importance not just as a material, but as a cornerstone in the world of engineering and manufacturing. The material's versatility stems from its balanced mechanical properties and its responsive nature to various treatments and processes—think about how critical these factors are when selecting materials for specific applications.
A comprehensive understanding of 1018 steel equips professionals and enthusiasts alike with the skills to make informed decisions. Insights into its chemical composition shed light on how individual elements play a role in the overall performance. This isn’t just academic; these insights can translate directly into more efficient, cost-effective applications in real-world scenarios.
Moreover, the ongoing innovations in material science promise exciting advancements, making it essential to stay abreast of trends in both the development and practical application of 1018 steel. Rounding off with considerations such as environmental impacts and sustainability, it's clear that the implications are far-reaching, informing not just manufacturing processes but broader industry practices as well.
Key Takeaways
- Versatility of 1018 Steel: This steel's unique balance of properties allows for diverse applications across various industries.
- Understanding Chemical Composition: Recognizing how each element contributes to performance can enhance material selection and processing.
- Innovation and Sustainability: The future of materials is moving toward sustainable practices, making it important to consider these aspects for long-term use.
- Practical Applications: Its role in automotive, industrial, and construction sectors represents a vital intersection of theory and practice that needs to be continuously refined.
Implications for Future Use
The prospects for 1018 cold rolled steel are promising, particularly as the world pivots toward more sustainable manufacturing practices. As researchers and engineers experiment with blending 1018 with newer materials or refining its properties through advanced techniques, we can expect to see enhanced performance characteristics.
Furthermore, understanding the adaptability of 1018 within various contexts can lead to more innovative designs and applications. For example:
- The potential for improved machining techniques to reduce waste during production.
- Exploration of new coatings or treatments that can enhance corrosion resistance without compromising mechanical properties.
Ultimately, keeping an eye on future trends will not only ensure that 1018 steel remains relevant but also help shape the innovations that drive the industry forward. It’s a dynamic field, and being well-informed can lead professionals to make smarter choices, steering projects towards success.