Building a Motorless Conveyor Belt: Step-by-Step Guide
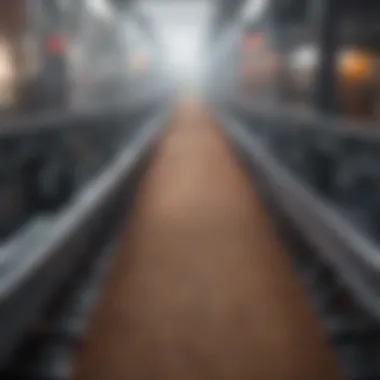
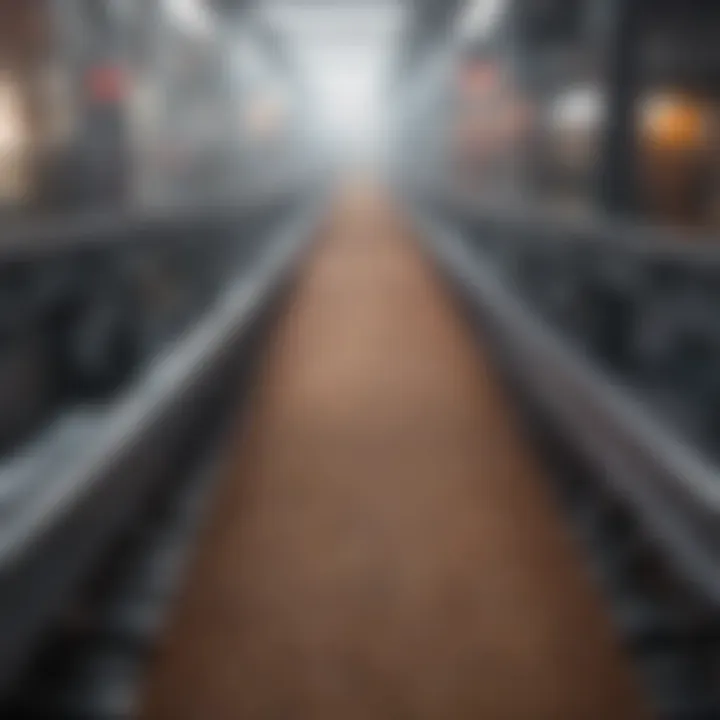
Intro
In industries where automation is prevalent, conveyor belts have become indispensable. However, depending on the context, constructing a conveyor belt without a motor can provide unique advantages. This guide elucidates the methodology behind creating a motorless conveyor system. By understanding its design, assembly process, and various applications, individuals can appreciate the value of manual operation. Furthermore, this approach serves as an excellent base for learning about mechanical systems.
Key Concepts and Terminology
Understanding the basics is crucial before diving into the specifics of construction. Below are some key concepts and relevant terminology.
Definition of Key Terms
- Conveyor Belt: A continuous loop of material designed to transport goods or products from one point to another.
- Manual Operation: The technique of running a machine without automated power sources, relying instead on human effort.
- Friction Drive: A method that utilizes friction between surfaces to create movement.
Concepts Explored in the Article
This article covers several essential concepts:
- The principles behind manual movement in a conveyor system.
- Selection criteria for materials that actively affect the performance and durability of the belt.
- Step-by-step assembly instructions ensuring efficiency and safety.
Practical Considerations
When constructing a conveyor belt without a motor, several practical considerations are essential.
- Materials: Choosing robust materials is vital. Options include wood, metal, and even recycled materials for sustainability.
- Design: The design should be intuitive, with clear dimensions that promote ease of assembly and operation.
- Safety: Adequate safety measures must be in place to prevent accidents during manual operations.
Findings and Discussion
Main Findings
Conveyor systems are not limited to motorized options. Manual options provide flexibility, especially in settings where electrical power is unavailable or undesired. The performance of manual conveyor belts can be commendable when designed appropriately, with friction working effectively to move products along the belt.
Potential Areas for Future Research
Further exploration can be conducted into enhancing the efficiency of motorless conveyor systems. Innovations in materials technology, frictional surfaces, and ergonomic designs could yield better results. The impact of different manual operation techniques on the overall system performance can also be a rich area for future study.
"A motorless conveyor belt opens a dialogue about alternative methods of production and transport in a world leaning towards automation."
Prologue to Conveyor Belts
Conveyor belts are integral to the movement of products in various industries. Understanding their structure and functionality provides a foundation for exploring motorless options. Conveyor belts allow for continuous transportation of materials, enhancing efficiency in production processes. This section will cover essential concepts that are crucial for a comprehensive grasp of conveyor systems.
Definition and Functionality
A conveyor belt is a mechanical apparatus designed to transport materials from one location to another. Its primary function is to facilitate the movement of goods in an efficient and consistent manner. Conveyor belts reduce the physical effort required to move products, allowing for quicker processing times and improved productivity.
The functionality of these systems relies on a few basic elements: the belt itself, rollers, and a frame. These components work together to create a continuously moving surface. The design allows for variations in speed and load capacity, making them adaptable to different tasks in manufacturing and logistics.
Types of Conveyor Systems
Conveyor systems can be categorized into several types based on their design and mechanism. Three of the most common types are the belt conveyor, roller conveyor, and chain conveyor, each serving specific purposes in material handling.
Belt Conveyor
Belt conveyors are widely known for their simplicity and effectiveness. They consist of a continuous loop of material, typically rubber or fabric, which moves over a series of rollers. The key characteristic of a belt conveyor is its ability to transport goods of various sizes, shapes, and weights over long distances. This versatility makes belt conveyors a popular choice for multiple applications, from warehouse logistics to manufacturing lines.
One unique feature of belt conveyors is their capability for incline transportation. They can be designed to move materials uphill, which is advantageous in many settings. Despite their benefits, they do have limitations; for instance, they can require more maintenance due to wear on the belt over time.
Roller Conveyor
Roller conveyors provide an alternative with a different operational mechanic. Instead of a continuous belt, this system uses individual rollers to move items along the conveyor. The key characteristic here is its ease of manual loading and unloading, making it especially beneficial in environments requiring frequent access to loads.
Unlike belt conveyors, roller conveyors work best with flat-bottomed items and can be designed to function at varying angles. While they are easy to repair and maintain, they might not be suitable for all product types, particularly those that are not stable or need a consistent controlled motion.
Chain Conveyor
Chain conveyors utilize a series of connected chains to move products along the conveyor. This system is particularly advantageous for heavy items and in harsh environments. The key characteristic of chain conveyors is their durability and strength; they can transport products that are heavier or have a rugged structure without concern for damage.
A unique feature of chain conveyors is their ability to operate in high-speed applications, which can significantly enhance productivity. However, they may have a restricted range of applications due to the specific loading requirements and the complexity of their design compared to other types.
In summary, understanding these different types of conveyor systems will help in the construction of a motorless conveyor. Each type brings its own set of advantages and disadvantages, which should be carefully considered when planning a conveyor system that meets specific operational needs.
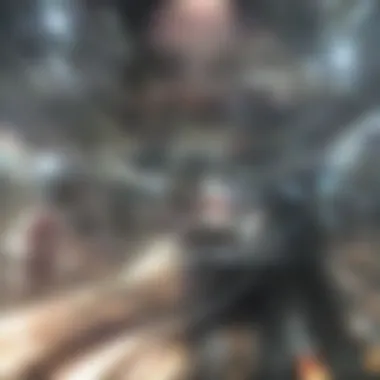
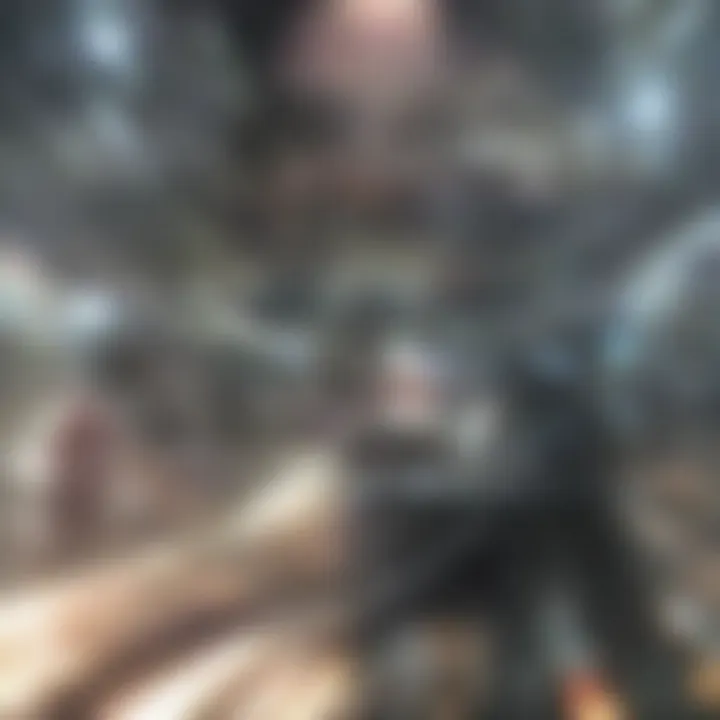
Understanding Motorless Conveyors
Motorless conveyors play a significant role in various applications, from industrial settings to educational projects. They offer a functional alternative to powered models, emphasizing mechanics driven by manual effort or natural forces. Understanding motorless conveyors is essential for those looking to leverage simplicity and cost-effectiveness in their material handling solutions.
Mechanics of Manual Conveyance
Gravity-Based Operation
Gravity-based operation depends on the fundamental force of gravity to move objects along a conveyor. This mechanism allows materials to flow downwards on an incline, making it particularly useful for transporting bulk goods.
The key characteristic of gravity-based operation is its reliance on gravitational potential energy. As objects descend an incline, they convert this potential energy into kinetic energy, resulting in movement. This method is often seen in chutes or sloped belts where heavy items can be moved effortlessly.
One unique feature of gravity-based systems is that they require no external power source, making them an environmentally friendly and cost-effective solution. However, the disadvantage is that they might not be suitable for all materials or applications, as the incline must be carefully calculated to prevent jams or damages.
Human-Powered Movement
Human-powered movement is another aspect of manual conveyance where individuals provide the necessary force to move objects along the conveyor. This method can utilize a variety of mechanics, such as manual cranks or lever systems.
The key characteristic of human-powered movement is the manual effort exerted to transfer materials. This approach is often employed in smaller settings or for tasks where the speed of movement is less critical. Due to its manual nature, this method allows for greater control over the operation.
A unique feature of human-powered systems is their adaptability. They can be tailored for specific needs, allowing users to design a system that functions efficiently within their constraints. However, it might not be the best option for large-scale operations since it relies heavily on human effort, which may lead to fatigue and decreased productivity over time.
Advantages of a Motorless Design
Cost Efficiency
Cost efficiency makes motorless conveyors highly attractive for budget-conscious projects. Without the need for motors or electrical inputs, the initial setup cost can be significantly lower than that of powered systems. This aspect is critical for small businesses looking to optimize their expenses without compromising on functionality.
The unique feature of cost-efficient designs is that they provide essential material handling functionalities with minimal investment. However, it’s worth noting that operational costs may vary depending on the manual labor needed to operate these systems.
Simplicity in Design
Simplicity in design is another advantage of motorless conveyors. These systems often consist of fewer components than their powered counterparts, which streamlines both the construction and operation process. Simplified designs can also ease troubleshooting and repairs if issues arise.
A key characteristic of this simplicity is the straightforward assembly process, which allows individuals with basic skills to build and maintain the conveyor. The downside is that while simpler systems reduce potential complications, they may also lack some advanced features afforded by motor-driven models, such as speed adjustments or automated controls.
Reduced Maintenance Needs
Reduced maintenance needs offer another strong point for motorless conveyors. By eliminating motors and electrical components, the frequency and complexity of maintenance tasks are decreased significantly. This factor is advantageous in everyday use since minimal upkeep leads to less downtime and increased productivity.
The unique feature of lower maintenance requirements means fewer interruptions in operations. On the contrary, users must remain conscious of mechanical wear related to manual handling, as excessive use can lead to other issues that may arise without regular monitoring.
Key Components Needed for Construction
Building a motorless conveyor belt requires careful consideration of its components. Each part plays a crucial role in ensuring functionality, efficiency, and durability. Understanding these elements is key to a successful project.
Selecting the Right Materials
Belting Material
Belting material is central to the operation of a conveyor belt. A good choice often depends on the intended use. Common materials include rubber, PVC, and fabric. Rubber is known for its grip and durability, making it a beneficial option. It withstands wear and tear better than many other materials.
Furthermore, the flexibility of rubber allows it to adapt to various belt configurations. However, it can become susceptible to UV damage over time.
Frame Support
The frame support is essential for stability. It provides a structural base that holds all other components in place. Steel is often used because it is strong and can handle significant weight. This characteristic makes steel a popular choice among builders.
One unique feature of steel frame support is its capacity for customization. It can be cut and welded to fit specific applications. However, metal frames may require more maintenance to prevent rusting compared to plastic alternatives.
Rollers and Pulleys
Rollers and pulleys facilitate the movement of the belt. They reduce friction and allow smoother operation. High-density polyethylene (HDPE) is commonly used for rollers because it is lightweight. This makes it a favorable choice in many setups.
The unique aspect of HDPE rollers is their low wear rate. They can often last longer than metal rollers. But, they may not support extremely heavy loads as effectively.
Tools Required for Assembly
Measuring Tools
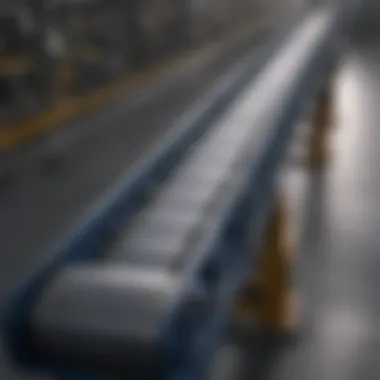
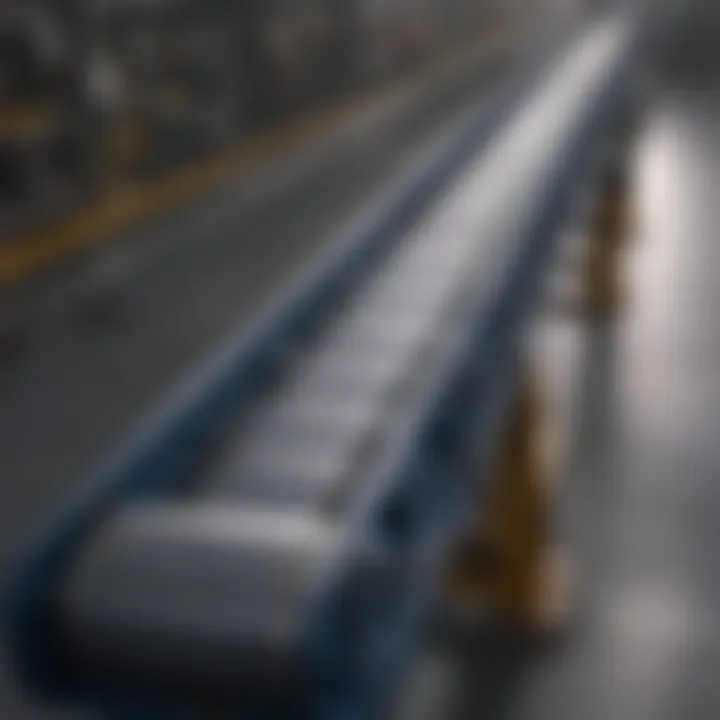
Measuring tools are vital in ensuring accuracy during construction. Tools like tape measures and calipers help in obtaining precise dimensions. This is essential for achieving a well-aligned conveyor.
Their key characteristic is the level of detail they can provide. Accurate measurements reduce errors that may occur during assembly. However, reliance on measuring tools requires a steady hand and clear eyesight to achieve optimal results.
Cutting Tools
Cutting tools are required for shaping materials, especially when frames and belts need to be resized. Common tools include saws and snips. A sturdy saw allows for clean cuts, which is beneficial for ensuring that components fit together seamlessly.
The unique feature of these tools is their ability to work with various materials. However, they can also present safety risks if not handled properly.
Joining Tools
Joining tools are necessary to connect different parts securely. Screws, bolts, and brackets are typical examples. The use of a power drill makes this task faster and more efficient.
Their key characteristic is the range of options for making strong connections. They allow flexibility in construction, accommodating different designs. However, choosing the right joining method is crucial to prevent future failures in the assembly.
Step-by-Step Construction Process
The construction of a motorless conveyor belt requires careful planning and execution. Each step in the process is crucial for ensuring the overall effectiveness and functionality of the system. This section will guide the reader through the methods of constructing such a conveyor belt, detailing the necessary steps and their individual significance. Achieving precision during construction is vital to ensure maximum performance. Moreover, a well-executed process minimizes problems that may arise with material efficiency and load handling.
Planning and Design
This initial stage lays the groundwork for a successful build. By establishing a solid plan, the builder can anticipate any challenges. Design choices made here affect every subsequent construction phase.
Dimensions and Layout
Dimensions and layout are integral to the overall operation of the conveyor belt. The specific sizing will dictate how much space the conveyor will occupy and the type of materials that can be handled efficiently. By using standard dimensions, builders often benefit from the availability of pre-manufactured parts, which can streamline assembly. A common choice is to keep the width of the belt between 24 and 36 inches. This width accommodates a wide range of load capacities while remaining manageable for manual operations.
One key characteristic of dimensions is the length of the conveyor. Longer conveyors can transport items over significant distances, but they require more robust support systems. This factor must be considered to avoid sagging or misalignment. A layout that aligns not only with functional requirements but also with physical space available is the best approach.
Load Specifications
Load specifications inform the construction of the conveyor in terms of capacity and material choice. This aspect plays a significant role in determining the materials needed for both the belt and support structures. For instance, heavier items demand stronger belting material and additional reinforcements in the frame.
The central benefit of having clear and accurate load specifications is to prevent overloading. Exceeding the recommended weight limits can lead to conveyor failure or even personal injury during operation. Hence, it is important to specify the maximum load early in the construction phase. This preparation enables appropriate design choices that cater to the user’s specific needs.
Constructing the Frame
Building the frame is one of the most straightforward yet important steps. The frame serves as the foundation for the entire conveyor system. A well-constructed frame will ensure stability and alignment of the components. Standard materials include steel or aluminum, known for their durability and strength. The frame must be measured and cut accurately to allow for proper roller placement and belt alignment.
Installing the Roller System
The roller system supports the conveyor belt and facilitates the movement of goods. Installation must align with the pre-defined layout from the planning stage. Rollers should be mounted securely and evenly to minimize uneven wear on the belt. Proper alignment can also reduce noise and friction, leading to smoother operations.
Adding the Conveyor Belt
Once the rollers are in place, the conveyor belt can be attached. The belt should fit snugly without excessive slack. Proper tension ensures that the belt can bear the load while maintaining a consistent speed. Secure the ends of the belt to appropriate fixtures on the rollers to avoid slipping.
Testing the Mechanism
Testing the entire system is the final and essential step in this construction process. Begin by observing the system at lower loads to confirm the setup functions correctly. Ensure that the belt moves freely without obstruction and that the frame holds firm against the movement. Adjustments such as tension calibration and roller alignment may be needed based on these tests. Evaluating the functionality before full operation eliminates potential issues and enhances safety.
"A well-planned approach leads to successful implementations of motorless conveyor systems."
Following these steps carefully will result in a functional motorless conveyor belt suited for various applications. Building this conveyor requires attention to detail, proper calculations, and adherence to design specifications. A successful build can cater to industrial processes or educational projects alike.
Applications of a Motorless Conveyor
Understanding the applications of a motorless conveyor is crucial to grasping its utility and relevance in various contexts. This section will explore significant real-world uses of these systems, highlighting how they function efficiently without a motor. The primary benefit here is simplicity in design and operation, allowing for cost-effective transport solutions that can be implemented in numerous environments. Additionally, motorless conveyors present a unique opportunity for individuals and organizations looking to minimize energy consumption. They can be tailored to fit specific applications, making them a flexible choice in both industry and education.
Industrial Use Cases
Packaging
In the realm of packaging, motorless conveyors serve a pivotal role in streamlining workflows. These systems can transport products smoothly from one station to another with minimal energy consumption. The key characteristic of motorless conveyor systems in packaging lies in their ability to be integrated into existing workspaces without extensive modification. This makes them a beneficial and popular choice for companies aiming to improve efficiency while keeping costs down.
One unique feature of these conveyors in the packaging industry is their capability to leverage gravity. For instance, inclined surfaces can facilitate the movement of items downward, eliminating the need for powered motors entirely. However, this design choice comes with disadvantages; it limits the load capacity and may require careful planning to manage varying product sizes.
Manufacturing
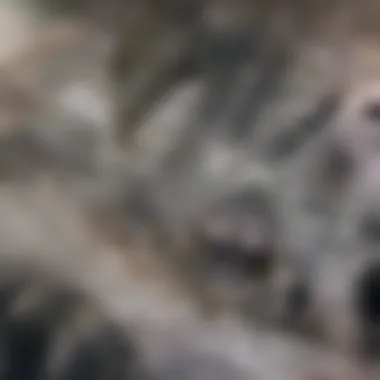
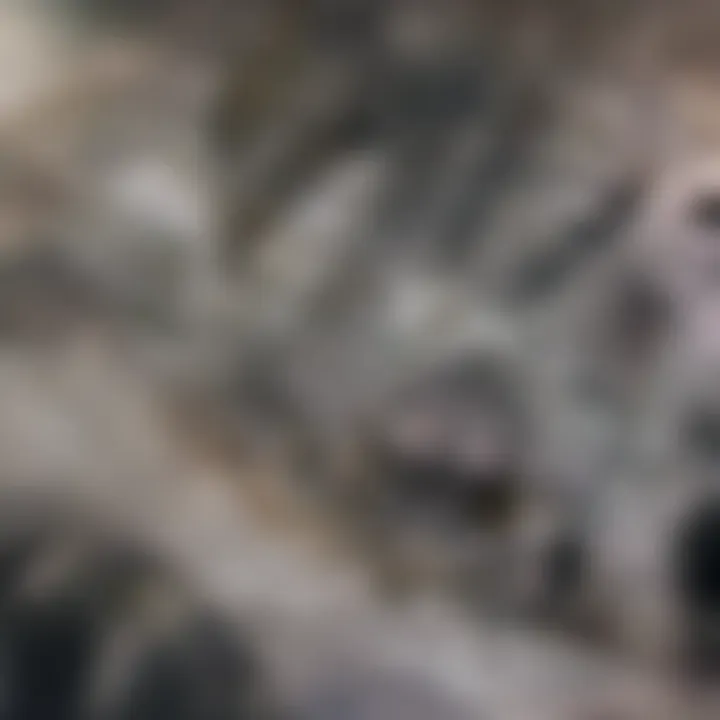
In manufacturing, motorless conveyors are a versatile application. They support processes such as assembly, inspection, and distribution of parts. The critical characteristic of motorless conveyors in this setting is their adaptability; they can work effectively in confined areas and can easily be moved between different workstations as needed.
A specific aspect of these systems in manufacturing is their reliance on manual or gravity-based movement. This not only reduces electricity costs but also enhances worker engagement. However, the downside can be a slower production rate compared to powered options, which may pose challenges in high-demand environments. Nonetheless, the rhythmic nature of manual operation can help in fostering better coordination among workers, leading to increased overall productivity.
Educational Projects
Motorless conveyors also find significant application in educational settings. These projects can aid students in grasping fundamental principles of mechanics and engineering in a tactile way. By constructing a motorless conveyor, learners engage directly with problem-solving and design processes. They can experiment with load capacities, materials, and construction techniques in a hands-on environment.
Moreover, these projects encourage creativity. Students can design systems tailored for specific tasks—whether that be transporting marbles, books, or other small items in a classroom setting. The insights gained through such activities allow for deeper understanding and retention of complex topics. Teaching with motorless conveyors enables educators to bridge theory and practice, fueling interest in science and engineering fields.
Potential Limitations
Understanding the potential limitations of a conveyor belt constructed without a motor is essential. These limitations can significantly influence the design and functional capabilities of such systems. Failing to account for these factors can lead to inefficiencies, safety risks, and suboptimal performance. Thus, it is vital to recognize and address the limitations associated with load capacity and manual operation as key components of this method.
Load Capacity Considerations
When building a motorless conveyor belt, one critical aspect is load capacity. This capacity refers to the maximum weight the conveyor can support without structural failure or performance degradation. The load capacity is contingent upon several factors:
- Material Strength: The materials chosen for the frame, belt, and rollers must possess adequate strength to bear the intended weight. Steel, for example, offers high tensile strength, but aluminum may be more appropriate for lighter loads.
- Design Configuration: The specific design of the belt and its components impacts how weight is distributed. A longer span between supports can compromise stability and increase the risk of bending or breaking.
- Wear and Tear: Continuous use affects the integrity of materials over time. It is crucial to consider the life cycle of the used materials and their ability to hold up under repetitive stress.
Following proper guidelines for calculating and testing load capacity is crucial. Employing a safety margin adds an extra layer of reliability to the setup. This strategy minimizes the risk associated with unexpected loads that could exceed your projections.
Impact of Manual Operation
Manual operation introduces various dynamics that can influence the overall effectiveness of the conveyor system. Unlike powered systems, a manual conveyor relies on human effort for movement. This reliance presents several challenges.
- Labor Intensity: Manual operation requires significant physical exertion, particularly if the load is substantial. This requirement can lead to operator fatigue, impacting productivity.
- Speed Limitations: The speed at which goods can be transported on a motorless conveyor is inherently slower than motorized systems. This slower movement may not be ideal for high-paced environments needing quick turnaround times.
- Consistency in Operation: Human operators may exhibit variability in performance, leading to inconsistent speeds and handling. Such fluctuations can result in process inefficiencies or potential bottlenecks.
Recognizing these impacts allows for better planning and adjustment when designing a manual conveyor. Operators are encouraged to practice ergonomics to reduce strain during operation.
In summary, while constructing a motorless conveyor can be beneficial, acknowledging its limitations ensures a more effective and sustainable operation overall.
Future Perspectives
The advancement of conveyor systems plays a crucial role in various industries and applications. As the demand for efficiency and sustainability increases, the importance of understanding future perspectives in conveyor technology becomes evident. This section highlights the emerging trends and considerations that impact not just the creation and use of conveyor belts, but also their long-term viability and potential innovations.
Innovations in Conveyor Technology
Recent years have seen notable technological innovations in conveyor systems. These advancements are largely driven by automation, robotics, and digital technologies. For instance, smart conveyor systems that utilize sensors can track products and adjust speed accordingly, optimizing flow and reducing bottlenecks.
Additionally, there are developments in modular conveyor design. This allows for rapid reconfiguration and scalability, making it easier to adapt to changing production needs. Businesses are increasingly interested in conveyors that can seamlessly integrate with their existing systems for enhanced operational efficiency.
Furthermore, the integration of AI and machine learning into conveyor operations is gaining traction. These technologies help in predictive maintenance, reducing downtime and ensuring that systems run smoothly. Companies can proactively address issues before they lead to significant disruptions in production.
Sustainability in Conveyor Design
Sustainability is no longer a secondary consideration in conveyor design; it is a necessity. The industry is shifting towards environmentally friendly materials and energy-efficient systems. The use of recycled materials in conveyor belt production is one example of how companies are reducing their ecological footprint.
Moreover, energy harvesting technologies are being explored. These allow conveyors to generate power from their own movement or from the items being transported, thereby decreasing energy consumption. This aligns with broader trends in industrial sustainability to reduce reliance on non-renewable energy sources.
Additionally, implementing maintenance-free components can enhance the sustainability of conveyor systems by reducing waste over the product's lifetime. Long-lasting parts decrease the need for replacements, which contributes to decreasing inventory waste and carbon footprints.
The integration of sustainable practices in conveyor design is imperative for meeting industry standards and regulations while also catering to a growing market demand for green technologies.
The exploration of these innovations and sustainability practices defines the future of conveyor technology. As these trends continue, they inform best practices while offering industry stakeholders numerous essential benefits, including improved operational efficiency and environmental responsibility. Understanding these future perspectives is important for anyone involved in the design and implementation of conveyor systems.
Finale
In this article, the exploration of constructing a conveyor belt without a motor demonstrates essential principles that can greatly benefit individuals in various fields. Understanding how to build a motorless conveyor is not just about creating a tool; it encompasses problem-solving, resource management, and engineering fundamentals. This knowledge is particularly valuable for students, educators, and professionals who seek practical applications of mechanical concepts.
Recap of Construction Steps
To summarize the construction process, a clear sequence was established in earlier sections. First, careful planning is crucial: conceptualizing dimensions and layout allows a tailored approach to meet specific needs. Next, sourcing the right materials, such as suitable belting and frame support, ensures structural integrity. The assembly involves creating the frame, then installing the roller system, culminating with the belt. Each step builds on the previous, resulting in a cohesive unit ready for practical use.
- Planning: Sketch the design and outline dimensions.
- Material Selection: Choose appropriate materials to suit the load specifications.
- Frame Construction: Build a sturdy frame to support the rollers.
- Roller Installation: Ensure rollers are well-aligned for smooth operation.
- Belt Addition: Attach the belt securely to allow for effective transport of materials.
Final Thoughts on Practical Implementations
The practical implementations of a motorless conveyor belt extend beyond education and DIY projects. Various industries could benefit from its simplicity and cost-effectiveness. For example, small factories can employ these systems for efficient material handling with reduced operational costs.
A motorless conveyor also promotes sustainability by relying on human effort or gravity. This aligns with modern techniques aimed at minimizing environmental impacts.
"Simplicity is the ultimate sophistication." - Leonardo da Vinci
As industries evolve, the principles laid out here serve as a foundation for future developments in conveyor systems, encouraging a blend of tradition with modernity.