The Role of Electric Submersible Pumps in Oil and Gas
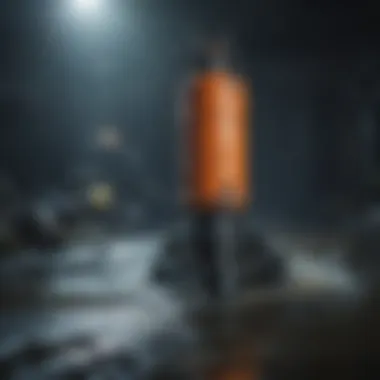
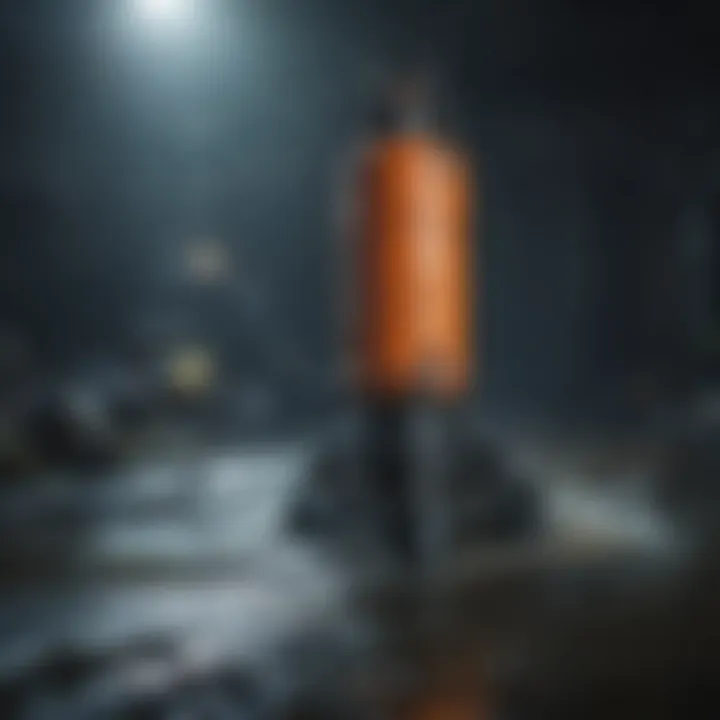
Intro
Electric submersible pumps (ESPs) are hydraulic devices that play a pivotal role in the oil and gas industry, particularly for extracting oil and natural gas from deep underground reservoirs. They operate by using an electric motor situated within the pump assembly, driving the movement of fluids from a significant depth to the surface. This technology has evolved over the years, making it an indispensable tool for energy production and resource management in various oilfield settings.
In this article, we will delve into the mechanics of ESPs, the advantages they offer, and their limitations. We will also discuss recent technological advancements that improve their efficiency and reliability. Lastly, we will cover installation procedures, routine maintenance practices, and the economic considerations involved in deploying ESPs. Through this comprehensive analysis, the objective is to enhance understanding of how ESP technology impacts energy production in today's dynamic market.
Key Concepts and Terminology
Definition of Key Terms
To grasp the nuances of electric submersible pumps, it is vital to familiarize oneself with specific terminology commonly used in the industry. Below are some essential key terms:
- Pump Better Efficiency (PBE): A measure indicating the efficiency of a pump in converting mechanical energy into fluid flow.
- Suction Conditions: Refers to the pressure and temperature conditions at the feed end of the pump, significantly influencing performance.
- Specific Speed: A dimensionless value that characterizes the pump design, permitting comparison among different pump types regardless of size.
Concepts Explored in the Article
The article will cover various concepts critical to understanding ESPs:
- Functionality and Operational Mechanism: Insight into how these pumps work, including their components and dynamics.
- Advantages and Disadvantages: An objective look at the positive attributes of ESPs, alongside potential drawbacks.
- Technological Advancements: Recent improvements in ESP technology that help optimize performance and extend operational life.
- Installation and Maintenance: Detailed procedures ensuring proper setup and upkeep, addressing factors that affect longevity and efficiency.
- Economic Impact: Evaluation of the cost-effectiveness of ESP deployment in various oilfield scenarios.
"Electric submersible pumps are not just tools; they are lifelines for modern energy production, threading together the deep reservoirs of our earth and the ever-hungry markets above."
Findings and Discussion
Main Findings
In the course of our exploration, we will highlight extensive findings, such as:
- The ability of ESPs to dramatically increase production rates in comparison to conventional pumping methods, effectively reducing operational downtime.
- How advancements in materials and designs contribute to enhanced durability, particularly in harsher environments.
- A thorough evaluation of how ESPs can be fine-tuned according to specific well conditions, maximizing efficiency while minimizing costs.
Potential Areas for Future Research
Looking ahead, several opportunities for deeper investigation into ESP technology emerge:
- Integration with Renewable Energy Sources: Examining how ESPs can evolve alongside the transition to renewable energy.
- Optimization Algorithms: Developing more precise algorithms for real-time monitoring and control of ESP systems.
- Remote Operations: Investigating how automation and artificial intelligence can further augment the deployment and monitoring of ESPs.
As we embark on this comprehensive examination of electric submersible pumps, it is evident that these vital components assure a fine balancing act between effective resource extraction and sustainable practices.
Preface to Electric Submersible Pumps
In the complex world of oil and gas extraction, electric submersible pumps (ESPs) have carved out a critical niche. These devices are not merely mechanical contraptions but lifelines of modern production techniques. By functioning submerged in fluids, they provide a means to elevate hydrocarbons from deep within the earth to the surface. This process is essential, particularly in fields where conventional pumping methods may falter.
Understanding electric submersible pumps is vital for professionals navigating the oil and gas industry. These pumps greatly influence efficiency, safety, and cost-effectiveness. When utilized appropriately, they can significantly bolster productivity and operational longevity. The advanced technology behind ESPs allows them to adapt to varying well conditions, presenting opportunities to extract resources more effectively than ever before.
Defining Electric Submersible Pumps
Electric submersible pumps are essentially devices that use electrical energy to move liquids, often from depths that gravity alone can't come close to addressing. They consist of several components: a pump, a motor, and a seal for protection against fluid intrusion. Once installed, these pumps are submerged in the liquid they are designed to transport, typically oil or water. The main advantage of this setup is that it eliminates the need for surface machinery, thereby reducing land footprint, and enhancing operational safety.
The primary function of an ESP can be boiled down to lifting fluids through a series of stages—each stage enhancing the pressure and allowing the liquid to reach the surface. This functionality becomes especially crucial in high-viscosity applications or in locations characterized by challenging geological formations where traditional techniques would struggle.
The Historical Context of ESPs
The journey of electric submersible pumps spanned several decades, marking significant advancements in extraction technology. The inception of ESP technology traces back to the early days of the 20th century. Initially, they gained traction alongside the discovery of oil in Texas during the 1920s. At that time, they were relatively rudimentary, primarily used to boost production in oilfields where conventional methods proved inadequate.
Fast forward to the mid-20th century, the invention of high-capacity electric motors and improved materials propelled ESP development further. By the 1960s and 70s, the oil industry's demand for efficient and reliable extraction methods saw a surge in ESP deployment across various geographic regions. Not only were they environmentally resilient, but they also started to gain recognition for their ability to adapt to complex well conditions.
In more recent years, the push for sustainability and lower carbon footprints has transformed the landscape once again. Today, ESPs leverage advanced technologies like telemetry and predictive analytics to optimize their performance. They are no longer just pumps; they are sophisticated systems that respond intelligently to the demands of their environments. This historical perspective sheds light on the evolution of ESPs and highlights their growing importance in the sustainability conversation within the oil and gas sector.
How Electric Submersible Pumps Operate
Understanding the operation of electric submersible pumps (ESPs) is crucial for grasping their effectiveness and versatility in the oil and gas industry. The unique engineering behind these pumps allows them to efficiently transport fluids from deep underground to the surface. This section delves into the essential components and operating principles that define ESPs, thereby highlighting their significant role in resource extraction.
Basic Components of ESPs
Electric submersible pumps are not just a single entity; they are assemblies of various parts that work harmoniously to perform the critical task of lifting fluids from wells. Among the most notable components are:
- Pump: The heart of the ESP, typically consisting of multi-stage centrifugal pumps which are responsible for lifting the fluid against pressure gradients.
- Motor: Located at the bottom or at the top, this component drives the pump and is often a submersible electric motor that operates effectively underwater.
- Seal Section: Essential for preventing fluid from entering the motor, it ensures reliability by protecting sensitive components from reservoir fluids and gases.
- Power Cable: Supplies electricity to the motor, often requiring careful material selection to withstand harsh environments.
- Flow Tube: This transports the pumped fluid to the surface and can sometimes integrate sensors that provide real-time data on performance and status.
Each of these components plays a vital role in ensuring that the ESP functions efficiently, marking the beginning of the lifting process.
Operating Principles
The operating principle of electric submersible pumps can be summarized as a system of interconnected mechanisms that convert electrical energy into hydraulic energy. The process kicks off with the motor, which is ignited by the power supplied through the cable. Once activated, the motor drives the pump impellers that are designed to create pressure differentials, effectively lifting the fluid upwards.
In the core of this operation rests Bernoulli’s principle, suggesting that as the velocity of a fluid increases, its pressure decreases. Thus, as the pump impellers spin, they impart velocity to the fluid, which subsequently translates into pressure, enabling the fluid's ascent through the flow tube.
One must also be aware of the effects of fluid characteristics and well conditions on pump performance. High-viscosity fluids, varying temperatures, and improper positioning of the pump can all impact efficiency. As a best practice, comprehensive monitoring through telemetry systems is often employed. This data-driven approach allows for optimizing performance and promptly addressing any operational hiccups.
In summary, mastering the mechanics behind electric submersible pumps empowers industry professionals to harness their full potential, ensuring an efficient and effective extraction process.
The Role of ESPs in Oil Extraction
Electric submersible pumps (ESPs) play a pivotal role in the oil extraction process, proving their worth in various applications and dramatically shaping the efficiency of operations. These pumps are integral to maximizing oil production and ensuring consistent output in some of the most challenging environments. By understanding the unique challenges faced during extraction, one can truly appreciate why ESPs have become a go-to solution in modern oil fields.
ESPs are designed to handle a range of conditions, from low to moderate flow rates, which makes them particularly valuable in production wells. They have the capability to lift fluids from significant depths, making them essential in locations where traditional methods might fail. Their reliability in fluctuating production scenarios underscores their importance, as oil wells often experience variable flow due to changing geological conditions.
Applications in Production Wells
The application of ESPs in production wells is perhaps their most recognized use. When the natural pressure in a well diminishes, which is common over time, ESPs come into play. These pumps can maintain production levels by artificially lifting oil to the surface, which is critical for ensuring that output remains economically viable.
- High Volume Production: With the capability to move large volumes of fluid, ESPs are suited for wells requiring a substantial lift capacity. They can handle heavy oil as well, which presents a unique challenge due to its viscosity.
- Long Operating Life: Designed for extended service, many ESP systems can operate effectively for several years before needing replacement or significant maintenance. This longevity is crucial in keeping operational costs manageable.
- Adaptability: ESPs can be tailored to meet specific operational parameters, allowing for modifications that suit the ever-changing dynamics of oil extraction processes.
In essence, the role of ESPs in production wells cannot be overstated. They stand at the forefront of modern extraction technology, continually evolving to meet the demands of the industry.
Applications in Water Injection and Disposal
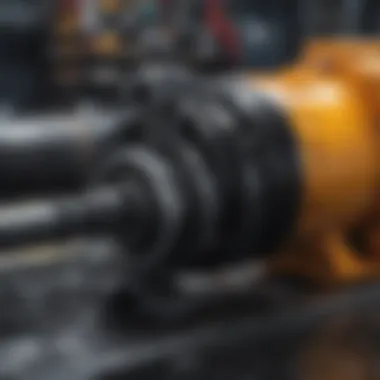
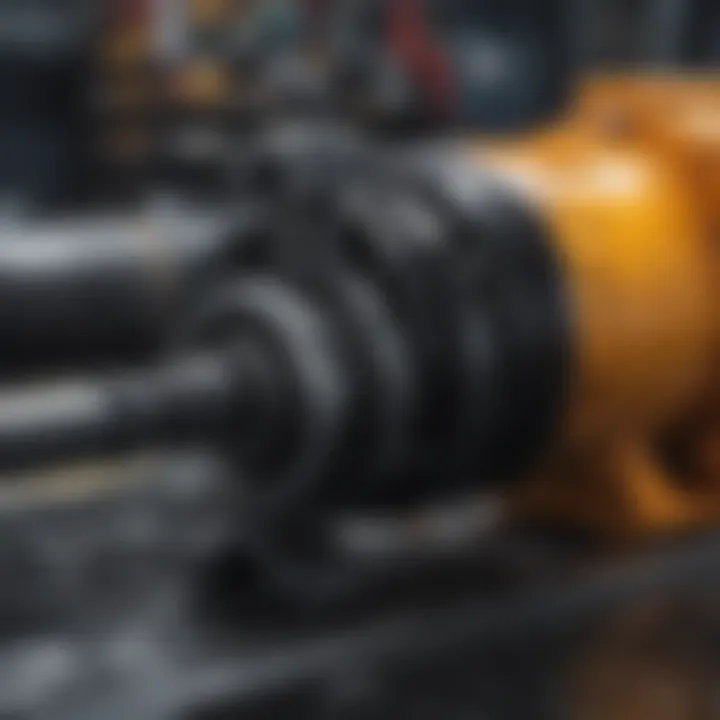
Water injection and disposal represent another crucial application of ESPs in the oil and gas sector. This method is fundamentally relevant to maintaining reservoir pressure and ensuring continuous oil production. It involves injecting water into the reservoir to maintain pressure, thereby enhancing oil recovery.
- Pressure Maintenance: As oil is extracted, the decline in pressure can lead to reduced oil flow. Injecting water helps maintain reservoir pressure, preventing geological issues that can arise from significant pressure drops.
- Enhanced Oil Recovery: The integration of ESPs in water injection systems can lead to improved oil recovery rates. By infusing water at calculated intervals, operators can increase the displacement of oil, leading to higher productivity.
- Efficient Waste Disposal: ESPs also play a vital role in the transfer of produced water, brine, and other waste materials from extraction sites. Efficiently managing these fluids reduces environmental impacts, ensuring compliance with regulations and promoting sustainable practices in the field.
In summary, the versatility of electric submersible pumps in both production wells and water injection systems validates their importance in the oil extraction process. Their ability to adapt to different operational needs while enhancing production efficiency positions them as indispensable tools in the oil and gas industry.
"The deployment of ESPs has transformed the landscape of oil extraction, enabling operators to optimize production while managing operational challenges seamlessly."
As technology advances, the applications and efficiency of ESPs will continue to evolve, solidifying their essential role in meeting global energy demands.
Advantages of Using Electric Submersible Pumps
Electric submersible pumps (ESPs) have become crucial players in the oil and gas industry. Their significance goes beyond mere function; they offer a range of benefits that can substantially enhance production efficiency and operational effectiveness. Understanding these advantages helps professionals in the field make informed decisions about their pumping solutions.
High Efficiency and Reliability
One of the standout features of ESPs is their high efficiency when it comes to extracting fluids from deep well formations. Unlike traditional pumping systems, which often struggle with depth and pressure differences, ESPs excel in these challenging conditions. They can operate effectively at great depths, extracting hydrocarbons at a consistently high rate.
Factors contributing to this efficiency include:
- Multi-stage design: The unique construction of ESPs allows for multiple impellers to increase pressure and flow rate while maintaining energy efficiency. This multi-stage capability enables the pumps to handle varying fluid dynamics without significant energy loss.
- Direct drive systems: Many modern ESPs are equipped with direct drive motors that minimize mechanical losses associated with gearboxes, thereby increasing their reliability and long-term performance.
The reliability of ESPs also cannot be overlooked. They are built to withstand harsh environmental conditions, including high temperatures and corrosive substances. With routine maintenance and proper installation measures, these pumps can operate effectively for extended periods, reducing downtime and associated costs. This is a significant consideration, as an interruption in production can lead to substantial economic repercussions.
"High efficiency and reliability are not just buzzwords; they are crucial performance metrics that can dictate the success or failure of oil extraction programs."
Operational Flexibility in Varying Conditions
Another critical advantage of ESPs is their operational flexibility. They are designed to adapt to a range of conditions, making them suitable for diverse applications across different oilfield environments. This versatility is vital for oil producers who may encounter fluctuating well conditions, such as changes in fluid viscosity, volume, or even unforeseen geological barriers.
Key elements that illustrate this flexibility include:
- Variable speed drives: Many modern ESPs come equipped with variable speed drives, allowing operators to adjust flow rates and performance in real time. This adaptability means that the systems can respond swiftly to variations in reservoir characteristics, optimizing extraction processes.
- Integration capabilities: ESPs can be integrated with advanced technologies like sensors and monitoring tools that provide data analytics. This integration enables proactive adjustments to be made, enhancing performance even in fluctuating operational environments.
Moreover, the ability of ESPs to function equally well in different scenarios — be it in production wells or during water injection processes — highlights their multi-faceted applications. By using ESPs, producers can optimize water management strategies, thereby enhancing the overall sustainability of extraction operations.
In sum, as the oil and gas industry evolves, the advantages of electric submersible pumps stand out as critical factors that drive operational success. Their efficiency, reliability, and adaptability make them indispensable in the pursuit of stable and profitable energy production.
Challenges and Limitations of ESPs
Electric submersible pumps (ESPs) have transformed the oil and gas industry, but they don't come without their own set of challenges and limitations. Understanding these factors is crucial for engineers, operators, and project managers to enhance deployment strategies and improve overall efficiency. Not every situation favors the use of ESPs, which makes it imperative to address their drawbacks in a detailed manner. This section delves into the specific challenges related to operational risks, environmental concerns, and economic constraints, shedding light on elements that stakeholders must navigate.
Operational Risks and Failures
One of the most pressing issues surrounding ESPs is the potential for operational risks and failures. Depending heavily on multiple components—such as motors, cables, and pumps—these systems can face unexpected behaviors during their operation. Failure of any critical component can lead to costly downtime, and when you consider the intricacies of downhole environments, the stakes get even higher.
For example, pump burnouts, which occur when the motor overheats due to prolonged operation at scheduled settings, can lead to catastrophic failures. Additionally, issues like gas locking—where gas accumulates in the pump, disrupting fluid flow—also hinder efficiency and can cause mechanical damage.
Regular monitoring and maintenance practices are vital, but even then, these scenarios underline a precarious balance; any lapse could mean a significant loss of production. This speaks to an industry-wide necessity—refining installation protocols and bolstering real-time diagnostic tools could mitigate these risks substantially.
Environmental Considerations
Considering the environmental impact of ESPs is a conversation no one can afford to ignore. As oil and gas production becomes increasingly scrutinized from an ecological standpoint, the industry faces heightened accountability. The first concern is often related to water usage—substantial amounts of water are extracted alongside oil, which can strain local resources.
Moreover, leakage and emissions from poorly maintained systems can further jeopardize surrounding ecosystems. Discharge from these systems must comply with environmental regulations, which are becoming progressively stringent. Therefore, an intricate understanding of the local environment becomes part of the pump selection and deployment strategy.
"While ESPs have revolutionized production, their deployment requires meticulous consideration of environmental impacts to ensure sustainable operations."
Design engineers are integrating environmentally sensitive technologies into ESP systems, but balancing economic constraints with sustainable practices remains a tricky proposition.
Economic Constraints
Lastly, economic constraints pose a significant barrier to the full-scale adoption and operation of ESPs. The initial setup costs can be staggering, especially in challenging terrains. Budget constraints compell companies to carefully weigh their options—operational efficiency vs. capital expenditure.
The maintenance costs, too, should not be overlooked. Components are subject to wear and tear, and spare parts can be expensive and slow to procure. Added to this mix, fluctuations in oil prices can cause financial disarray, affecting the ongoing investment in technology—an inopportune time when you need to sustain operations efficiently.
Stakeholders must ask themselves: are the upfront costs of ESPs justified by the long-term benefits? Economic evaluations that factor in such risks and potential for downtime will help in drawing clearer conclusions regarding the deployment of ESPs.
Technological Advancements in ESP Systems
The oil and gas industry constantly evolves, and among the most notable shifts in this sector is the advent of technological advancements in electric submersible pumps (ESPs). These developments not only enhance pump efficiency but also redefine how operators manage their resources. In a landscape where maximizing production while minimizing costs is paramount, understanding these advancements becomes essential for professionals in the field.
Smart Pump Technologies
In recent years, the introduction of smart pump technologies has transformed the way ESP systems function. These technologies enable pumps to operate autonomously, adjusting their performance based on real-time data. For instance, smart sensors embedded within the ESP can monitor flow rates, temperature, and even pressure changes. By doing this, they allow the pump to modify its speed or shut down if necessary, enhancing both efficiency and safety.
Moreover, these smart systems pave the way for predictive maintenance. Instead of relying on scheduled maintenance routines, operators can focus on data-driven insights to predict potential failures. This is more than just a trend; it drastically reduces downtime and maintenance costs, leading to significant savings over time.
Furthermore, smart technologies often include user-friendly interfaces, giving operators more control and better visibility into their system's performance. They can quickly assess if the pump is functioning optimally or if intervention is required. As this technology advances, operators who are slow to adapt risk falling behind in an environment that increasingly values innovation and efficiency.
Integration with IoT and Data Analytics
The integration of Internet of Things (IoT) and data analytics with ESP systems marks another significant leap forward. Thanks to the IoT, ESPs can now communicate with other equipment and platforms, gathering comprehensive insights that were previously unattainable. For example, data collected from pumps can be aggregated and analyzed alongside geological data, leading to more informed decisions on resource extraction.
- Real-Time Monitoring: IoT has enabled continuous real-time monitoring of pump performance, allowing operators to identify anomalies before they escalate into major issues.
- Data-Driven Decisions: By analyzing historical performance data, operators can pinpoint trends and derive insights, enabling them to optimize production strategies effectively.
- Remote Operation: With IoT integration, pumps can be controlled remotely. This is particularly beneficial for offshore operations where accessing equipment can be both costly and time-consuming.
The implications of these technological advancements in ESP systems extend beyond just operational efficiency. They influence safety protocols, environmental impact assessments, and even regulatory compliance. As organizations strive for heightened productivity, those who leverage these advancements effectively will likely see returns in their operational capacities and overall market competitiveness.
"Technological innovations in ESP systems are no longer optional; they're essential for sustained success in the oil and gas industry.”
In summary, the realm of electric submersible pumps is experiencing a revolution driven by smart technologies and IoT integration. As these advancements become more integrated into standard practices, the future of oil recovery looks not only more efficient but also more sustainable.
Installation and Commissioning of ESPs
When it comes to electric submersible pumps (ESPs) in the oil and gas industry, the significance of proper installation and commissioning cannot be overstated. The efficiency and longevity of an ESP ultimately depend on how well it's installed, making this stage a critical phase in the overall operation. The potential pitfalls of a hastily done installation can lead to reduced performance, equipment failures, and, in the worst case, costly operational downtime. Therefore, a meticulous approach is required to ensure that the pump operates optimally from the get-go.
The primary aim of this section is to guide readers through the specifics of site assessment and planning, as well as step-by-step installation procedures, ensuring that they possess the necessary knowledge to oversee successful ESP deployments.

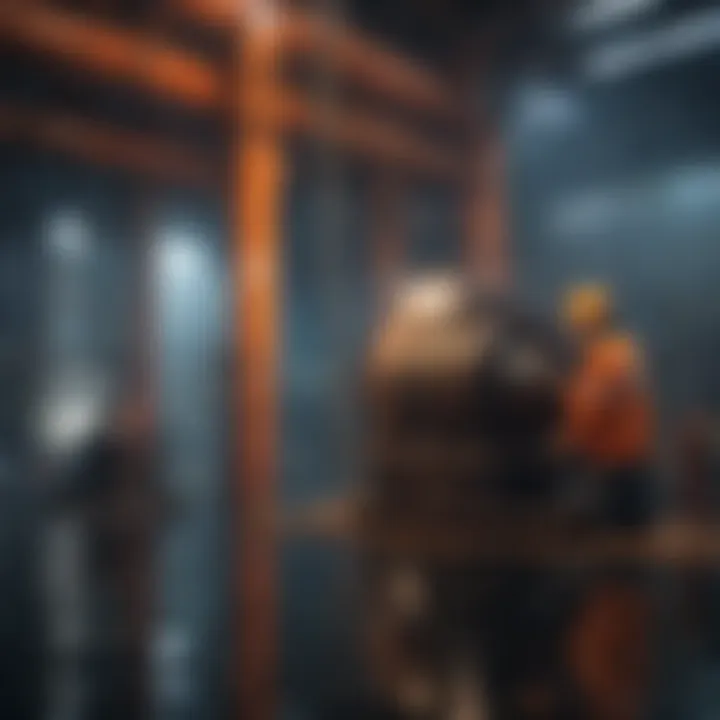
Site Assessment and Planning
Before any physical installation starts, a site assessment must be conducted. This involves evaluating the geographical and geological conditions of the proposed location. Here are some key points to consider:
- Geological Survey: Understanding the rock formations, soil type, and hydrology are essential for predicting how the pump will perform. For instance, a site with unstable geology might pose risks for the deployment and operation of an ESP.
- Availability of Resources: Access to necessary utilities such as electricity and water can influence the location's suitability for an ESP installation. Determine whether existing infrastructure can meet the demands of the pump.
- Environmental Impact: Consideration of the ecological footprint is vital. It's prudent to conduct an initial impact assessment to identify how the deployment might affect local wildlife and ecosystems. This can help avoid complications later on.
- Technical Requirements: Each ESP has its own set of specifications regarding horsepower, pump type, and operating depth. Matching these requirements with site conditions is fundamental to ensuring longevity and efficiency of the equipment.
A properly executed site assessment forms the foundation for a successful installation process. Missteps made at this stage can cascade into larger issues down the line.
Step-by-Step Installation Procedures
Once a thorough site assessment is complete, the next phase is the actual installation of the ESP. Follow these step-by-step procedures to ensure a smooth setup:
- Preparation of the Site: Clear the area of any debris, and ensure that the site is accessible for equipment and personnel. A clean workspace minimizes risks and ensures efficiency during installation.
- Positioning the Pump: Carefully lower the pump into the wellbore. It's imperative to maintain alignment as misalignment can cause excessive wear and tear, leading to equipment failure.
- Cabling and Electrical Connections: This step involves securely attaching the power cable to the motor and ensuring that all connections are watertight. Water ingress into electrical systems can cause catastrophic failures.
- Testing Equipment: Before finalizing the installation, conduct tests to verify that everything is functioning correctly. This includes checking voltage levels and ensuring that the motor is capable of starting under load.
- Final Setup Adjustments: Adjust any settings as necessary, ensuring that the ESP is configured to meet the specific operational requirements dictated by the site conditions.
- Commissioning: After the installations are squaring away, start the ESP while monitoring its performance closely. Pay attention to flow rates, power consumption, and pressures to ensure everything operates smoothly. Any anomalies should be addressed immediately to prevent prolonged issues.
Following these steps should set up a robust foundation for the ESP’s operational life, guiding it toward effective energy extraction and maximized efficiency.
Maintenance of Electric Submersible Pumps
Maintenance is a crucial element in the lifecycle of electric submersible pumps (ESPs) within the oil and gas industry. These pumps often operate in demanding environments and under various physical stresses, making regular upkeep essential for their sustainability and performance. Efficient maintenance practices not only prolong the life of the equipment but also enhance operation costs and safety.
In the world of oil extraction, even minor failures can result in substantial financial losses and resource wastage. Thus, understanding the nuances of maintenance is pivotal for technicians and engineers alike. Implementing a systematic approach to maintenance ensures that pumps operate at peak efficiency, reducing the risk of untimely breakdowns.
Routine Maintenance Practices
Routine maintenance involves a series of scheduled checks and adjustments aimed at ensuring that electric submersible pumps function optimally. Here are some vital practices to follow:
- Regular Inspections: Make it a habit to carry out frequent inspections of pump components like cables, volutes, and impellers. Look for signs of wear or corrosion.
- Cleaning: Keeping the pump clean is essential. Remove debris that might have accumulated around the pump body or suction areas to prevent blockages and overheating.
- Lubrication: Ensure all moving parts are adequately lubricated. This reduces friction and prevents wear and tear, ultimately prolonging the lifespan of the pump.
- Check Electrical Connections: Loose or corroded connections can lead to inefficiencies or even equipment failures. Tighten connections and replace corroded wiring when necessary.
- Monitor Performance: Use performance monitoring tools to track flow rates, pressures, and energy consumption. This data can help detect changes in behavior that might indicate underlying issues.
Establishing a solid routine maintenance plan can yield considerable benefits, including lower operational costs and increased safety. As they say, an ounce of prevention is worth a pound of cure.
Troubleshooting Common Issues
Even with diligent maintenance, issues can arise. Knowing how to identify and troubleshoot common problems can make a significant difference. Here’s a breakdown of some frequent issues and their troubleshooting steps:
- Overheating: This can be caused by various factors such as high fluid viscosity or malfunctioning cooling systems. Check fluid temperature and ensure proper flow is maintained. If overheating persists, consider reducing pump speed or investigating cooling mechanisms.
- Reduced Flow Rate: A significant decrease in flow could stem from obstruction in the intake or complications with the pump impeller. Inspect the intake area for blockages and clean accordingly.
- Vibration or Noise: Unusual vibrations or noise may indicate alignment issues or wear in the motor bearings. Investigate to confirm alignment and replace any damaged bearings to restore smooth operation.
"A proactive approach in maintenance and troubleshooting not only saves resources but also enhances the reliability of electric submersible pumps."
- Leaking Seals: This can lead to catastrophic failure if left unaddressed. Monitor for fluid leaks around seals, and replace them when signs of wear are evident.
Conducting thorough troubleshooting effectively keeps the pumps running smoothly and minimizes errors in performance. It’s the smart way to ensure that every pump works like clockwork in the demanding scenarios of oil extraction.
Economic Implications of ESP Deployments
Electric submersible pumps (ESPs) are not merely technical marvels in the oil and gas sector; they hold profound economic implications that can influence the viability of projects and operational strategies. Understanding these implications is crucial for stakeholders who aim to maximize their investments while ensuring sustainable and effective resource extraction. These pumps can often mean the difference between profitable operations and financial disasters, making it paramount to evaluate their economic contributions thoroughly.
Cost-Benefit Analysis
In the realm of economic considerations, a cost-benefit analysis stands as the cornerstone for decision-makers. It serves as a systematic approach to evaluating the expected financial outcomes of deploying ESPs versus their associated costs.
Key aspects to evaluate include:
- Initial Investment: The upfront costs involve not just purchasing the pump but also installation expenses, electrical setup, and integration into existing systems. For instance, setting up an Halliburton ESP can necessitate substantial initial capital outlay, especially in remote locations.
- Operational Expenses: After installation, regular operational costs play a critical role. This includes maintenance, energy consumption, and potential downtime. Although ESPs boast efficiency, high energy costs can eat into profit margins significantly over time.
- Production Gains: Enhanced oil recovery rates facilitated by ESPs often lead to increased production. When comparing production yields pre- and post-ESP installation, the contrasting figures can highlight the economic thrusts pumps bring.
A well-executed cost-benefit analysis provides clarity on whether the expected production increase justifies the investments made. Without this assessment, organizations risk overspending and potentially straining their financial resources in the long run.
"A penny saved is a penny earned; hence, weighing each aspect of costs in energy extraction is no small feat."
Return on Investment Considerations
The return on investment (ROI) from ESP deployments is a vital metric, as it encapsulates the efficacy of the financial decisions made regarding these systems. Evaluating ROI involves looking at not just immediate gains but long-term benefits, too.
When assessing ROI, consider the following:
- Time Frame: The speed at which profits materialize is key. Some ESP systems may provide quick payoffs in established fields, while others may take longer in untested environments. Companies ought to project timeframes accurately for better planning.
- Revenue Generation: A tangible indicator of ROI, measuring the incremental revenue from oil extraction due to efficient pumping. For example, using Schlumberger's ESP systems in a mature field may yield significant returns that surpass traditional methods, showcasing the advantages of advanced technology.
- Impact of Market Fluctuations: The fluctuating prices of oil can heavily influence ROI calculations. A robust analysis will incorporate various price scenarios, projecting how profit margins adjust with market changes.
It's imperative for stakeholders to grasp the nuances of these financial tools. By dissecting costs and carefully analyzing potential ROI, organizations can make informed choices that align with both immediate goals and future sustainability.
As oil and gas ventures gear up for the complexities of the industry, having a solid understanding of the economic implications surrounding ESPs proves indispensable. This not only helps pull the strings of profitability but also sets the stage for more strategic long-term planning.
Case Studies of ESP Applications
Case studies are vital in illustrating the real-world applications and efficiency of electric submersible pumps (ESPs) within the oil and gas realm. They not only highlight how these systems operate under various conditions but also provide a deeper understanding of the challenges and successes associated with their deployment. In this section, we will delve into successful deployments across different regions and extract valuable lessons from failures encountered in the field.
Successful Deployments Across Different Regions
Across the globe, various oil fields have embraced the utilization of ESPs, demonstrating their adaptability and effectiveness. For instance, in the North Sea, ESPs have consistently showcased their performance in harsh environments characterized by high temperatures and pressures. Operators have recorded significant production increases when transitioning from traditional pumping methods to ESP systems. This transition often results in a noticeable uptick in recovery rates, making the switch economically viable despite upfront installation costs.
In the Middle East, particularly in Saudi Arabia, ESP systems are deployed in oil fields that require enhanced oil recovery methods. The integration of these pumps has allowed for optimized fluid extraction even from mature wells, significantly extending their productive lifespan. The flexibility of ESPs to manage fluctuations in production demands while ensuring minimal downtime is crucial in this context.
"Efficient deployment of ESPs can turn challenging oil fields into profitable ventures, showcasing their crucial role in maximizing oil recovery across the globe."
Meanwhile, in South America, countries such as Brazil are exploring the use of ESPs in offshore oil extraction. The deepwater conditions necessitate specialized equipment, and ESPs have proven resilient, showing adaptability to dynamic underwater pressures. The successful implementation here has highlighted how these pumps facilitate efficient extraction even in complex geological settings.
Lessons Learned from Failures
Despite the many successes associated with ESPs, the road has not been without its bumps. Each failure carries lessons that can enhance future deployments. For example, an operator in the Permian Basin faced premature pump failures due to sand production. This scenario underlined the necessity for thorough geological assessments before installation.
In some cases, improper sizing of the pump led to operational inefficiencies. Utilizing pumps that were either too small or oversized can exacerbate wear and tear, causing frequent outages and inflated maintenance costs. Lessons from these situations lead to the conclusion that meticulous planning and sizing are paramount.
Another significant learning curve has appeared in the realm of regular maintenance. Operators who underestimated the importance of routine checks and preventive maintenance often faced unexpected operational halts. These situations spotlight the need for a robust maintenance schedule tailored to the unique demands of each installation. Such practices can dramatically reduce the risk of failures and enhance overall system longevity.
Future Trends in ESP Technology
The rapid advancement of technology in various sectors has begun reshaping the landscape of electric submersible pumps (ESPs) in the oil and gas industry. As reservoirs become more complex and the demand for energy continues to grow, understanding the implications of these future trends is critical. Adopting new technologies not only enhances the operational efficiency of ESPs but also addresses environmental and economic challenges that arise in this field. With that said, there are key elements related to emerging technologies and the impact of renewable energy integration that deserve emphasis.
Emerging Technologies
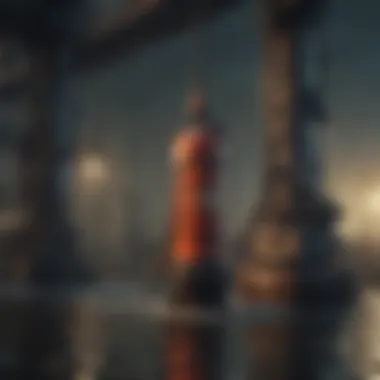
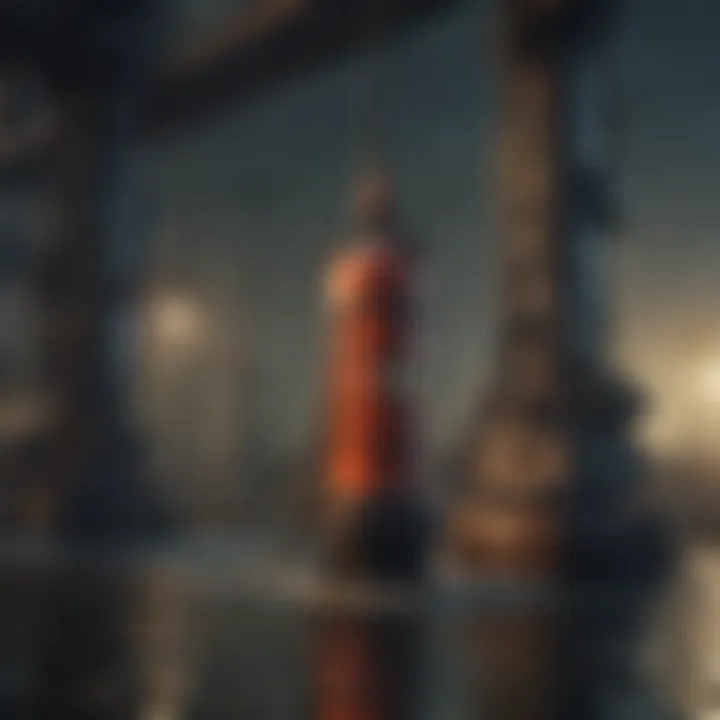
The future of ESP technology hinges on several innovative advancements designed to improve both performance and reliability. Some notable emerging technologies include:
- Smart Pump Systems: The integration of artificial intelligence can allow for real-time data analysis, continuously adjusting pump operations to optimize performance based on prevailing conditions. For example, a smart ESP could sense changes in fluid properties or flow rates and adjust its speed accordingly, minimizing operational disruptions.
- Enhanced Materials: Research into advanced materials can result in more durable components that are resistant to corrosive environments. For instance, using ceramic coatings on critical parts can significantly extend the lifespan of pumps, leading to lower maintenance costs in the long hauls.
- Modular Designs: These designs facilitate easier upgrades and repairs. This approach reduces equipment downtime significantly. If a specific part fails, it can be replaced without needing to replace the entire pump system, ultimately saving resources.
With these innovations, operators can expect enhanced efficiency and reduced operational risks while maximizing the value extracted from reservoirs.
Impact of Renewable Energy Integration
The oil and gas industry is increasingly turning its gaze towards sustainability. Integrating renewable energy sources into ESP operations not only helps in reducing carbon footprints but can also lead to cost savings and enhanced efficiency. Consider the following points:
- Hybrid systems: Pairing ESPs with renewable energy sources like solar or wind can lead to significant operational enhancements. For instance, a solar panel array could power the ESP, tapping into free energy. This approach not only reduces costs associated with electricity bills but also enhances energy independence.
- Grid-resilient Solutions: As electricity grids become more strained, having pumps powered by renewables contributes to energy security. In areas prone to outages, a well-developed renewable infrastructure ensures that pumps continue to operate smoothly, thereby avoiding costly downtime.
- Alignment with Regulatory Standards: The push for greener energy has led to tighter regulations on emissions. Adopting renewable energy for ESPs allows firms to meet or even exceed these standards, giving them a competitive advantage in the market.
"Embracing renewable energy not only represents a shift in how we power operations but also signifies a commitment to a sustainable future, crucial for the longevity of the industry."
In summary, the exploration of future trends in electric submersible pumps is not just an academic exercise; it’s a necessity. Understanding these developments can provide valuable insights for stakeholders within the industry, ensuring they stay ahead of the curve, embrace innovations, and adapt to the changing dynamics driven by environmental and economic factors.
Safety Standards and Regulations
The oil and gas industry operates in an environment laden with hazards, making safety standards and regulations crucial in mitigating risks associated with electric submersible pumps (ESPs). These pumps, while essential for optimizing oil extraction, come with their own set of safety challenges. Establishing a framework of rules and guidelines ensures not just the wellbeing of workers, but also the integrity of the environment and equipment involved. The significance of adhering to safety standards cannot be overstated as it plays a pivotal role in safeguarding personnel, minimizing environmental impact, and enhancing operational efficiency.
International Guidelines
International guidelines for safety standards regarding ESPs draw from a variety of sources, including the International Organization for Standardization (ISO) and the American Petroleum Institute (API). They outline best practices necessary for the design, operation, and maintenance of ESP systems.
- ISO 14001: This focuses on effective environmental management systems. Following these standards helps companies minimize their environmental footprint when deploying and operating ESPs.
- API 610: This specific guideline addresses the design and performance of centrifugal pumps, offering insights relevant to the design of ESPs. Compliance with API standards helps in ensuring the robustness of pump construction against routine operational stresses.
Furthermore, guidelines provide a framework for training and competency development for operators managing these pumps, fostering an environment of continuous improvement and safety awareness. Regular audits and assessments based on these international standards can aid in identifying inefficiencies and ensuring compliance, reducing the likelihood of accidents.
Compliance Challenges
Despite the structured approach to safety standards, numerous compliance challenges persist. Companies operating in remote locations or in regions with limited oversight might struggle to meet regulations, which can lead to serious consequences.
Some common compliance challenges include:
- Variability in Regulations: Different countries and regions can have varying safety regulations, causing confusion for multinational companies. Navigating this maze requires a thorough understanding of local laws and consistent practices across all locations.
- Cost of Compliance: Implementing stringent safety measures often comes with significant costs. Smaller operators may find it challenging to allocate resources for compliance training or equipment upgrades, potentially compromising safety.
- Technological Limitations: Not all companies have access to the latest technologies that facilitate compliance with safety standards. It requires a concerted effort to integrate such upgrades into existing infrastructures.
"Safety standards are not just regulations; they are commitments to preserve life and the environment."
Environmental Impact Assessment of ESPs
Environmental Impact Assessments (EIAs) of Electric Submersible Pumps (ESPs) are crucial for ensuring that these systems do not detrimentally affect the surrounding ecosystems. In today's oil and gas landscape, where scrutiny over environmental considerations has intensified, understanding the ecological implications of deploying ESPs can promote more sustainable practices and mitigate potential harm.
Assessing Ecological Footprints
When we talk about the ecological footprint of ESPs, we're delving into several layers. This assessment includes evaluating:
- Water Usage and Contamination: The operation of ESPs often involves interaction with groundwater resources. If leaks occur, they might contaminate local water supplies, jeopardizing both human health and wildlife.
- Alteration of Natural Habitats: Pump installations can lead to habitat disturbances for flora and fauna. Therefore, it’s important to identify sensitive zones prior to deployment.
- Energy Consumption: ESPs are electric-driven, and if their energy comes from non-renewable sources, the overall environmental advantage diminishes.When experts carry out these assessments, they use various tools and methodologies to gauge the impact. Satellite imagery, for example, allows researchers to observe changes in land use over time. Meanwhile, field studies help gather direct evidence of habitat disruption and wildlife behavior patterns.
"Understanding the ecological impact of technologies like ESPs can provide pathways to improving energy practices across the industry.”
Mitigation Strategies
Developing effective mitigation strategies is essential for reducing the environmental consequences identified in the ecological footprint assessment. Some viable strategies include:
- Using Environmentally Friendly Materials: Opt for materials in the construction and operation phases that have lower impact on the environment. For example, choosing biodegradable lubricants can minimize pollution in case of leaks.
- Implementing Routine Monitoring: Regularly checking the ecological conditions around ESP installations can act as an early warning system for any adverse effects, allowing for swift action.
- Incorporating Renewable Energy Sources: Whenever feasible, sourcing the energy required for ESP operations from renewable platforms can dramatically reduce the carbon footprint.
- Engaging in Community Communication: Informing local communities about potential risks and mitigation strategies helps build trust and fosters collaborative efforts for observance and awareness.
By embedding these strategies into planning and operational phases, the oil and gas industry can secure the environmental integrity of sites utilizing ESPs, balancing energy needs with ecological responsibilities.
Comparative Analysis with Alternative Pumping Solutions
In the quest for efficiency in the oil and gas industry, evaluating the performance of electric submersible pumps (ESPs) against other pumping systems is crucial. This comparative analysis serves not just as a guide for selecting the optimal solution but also as a framework to understand the operational contexts in which each pumping type excels. It unveils the pros and cons of different systems, helping stakeholders make well-informed decisions that align with their operational needs and economic expectations.
Sucker Rod Pumps vs. ESPs
Sucker rod pumps have long been a staple in the oil extraction industry, particularly in shallow and moderately deep wells. They use a mechanical method of lifting fluids to the surface, relying on a series of rods that connect to a surface pump jack. While they are tried-and-true workhorses, their mechanical nature introduces points of wear and tear that can lead to downtimes and costly repairs.
On the flip side, electric submersible pumps present a different paradigm. They operate without the same mechanical complexities.
- Efficiency: ESPs generally offer higher efficiency than sucker rod pumps, especially in deep wells where a sucker rod system becomes less viable due to the weight and depth of the rods involved.
- Energy Consumption: ESPs use electrical energy, which can be more cost-effective over time, especially where renewable energy sources are available.
- Installation and Operation: Installing an ESP requires less surface equipment and can streamline the extraction process once operational. This contrasts with the more cumbersome sucker rod installations which may require significant surface infrastructure.
However, sucker rod pumps do have their perks. They can be simpler to maintain, and for operators familiar with them, there's a comfort in using a well-understood technology. In cases where production rates are lower, or well conditions favor less complexity, sucker rod pumps still find their space in oil fields.
Progressive Cavity Pumps vs. ESPs
Progressive cavity pumps are another alternative in the oil and gas sector, particularly effective in handling viscous fluids due to their unique design, which consists of a helical rotor that moves fluids through a series of cavities.
Their strength lies in their ability to maintain a consistent flow rate, which can be particularly valuable in processes requiring steady outcomes. However, the operational scope of progressive cavity pumps tends to be more limited compared to ESPs.
- Handling Viscosity: Progressive cavity pumps excel in applications where fluid viscosity is high, making them suitable for certain productions, like heavy crude oil. ESPs, while versatile, may face challenges in such conditions.
- Operational Reach: On the other side, ESPs significantly extend operational reach due to their ability to operate at greater depths and produce larger volumes of fluids. They can easily adapt to varying well conditions, going from low to high production scenarios without extensive adjustments.
- Cost Considerations: From an economic perspective, while progressive cavity pumps might have lower upfront costs, the electricity demands and potential downtime associated with maintenance can add up, tipping the scale back in favor of the ESPs, particularly where efficiency and downtime are concerns.
In sum, when weighing sucker rod pumps and progressive cavity pumps against electric submersible pumps, it's clear that ESP technology shines in many scenarios. Operators should closely consider their specific needs against the characteristics of each pump type to ensure they choose the best fit producing maximum productivity and cost efficiency.
"The best pumping solution often comes from understanding not just the equipment but the context in which it operates."
Engaging in a thorough analysis of these alternatives provides insight into optimizing operations and maximizing resource extraction. This understanding is vital for improved decision-making, contributing to better financial outcomes and system reliability.
Closure and Summary of Insights
Bringing together the various threads of this discussion, the conclusion on electric submersible pumps (ESPs) serves as a pivotal moment for both industry professionals and academic minds. The exploration of ESPs delves not just into their mechanics, but into the underlying impact they have on oil extraction efficiency and resource management. They are indeed the unsung heroes of the oil field, providing reliability under tremendous pressure, both literally and figuratively. Understanding their role can lead to improved operational strategies, reduction in costs, and ultimately, a more sustainable approach to energy production.
Recapitulation of Key Points
- Operational Efficiency: ESPs are designed to move large quantities of liquid efficiently, making them essential for various applications in oil extraction.
- Technological Integration: The advancement of smart technologies and IoT has brought real-time monitoring and data analysis to the forefront, allowing for enhanced decision-making.
- Challenges and Resolutions: While ESPs face challenges, including operational risks and environmental concerns, ongoing innovations continually seek to address these issues.
- Economic Considerations: Understanding the financial implications, such as cost-benefit analysis and ROI, is paramount as companies strive for both profitability and sustainability.
- Future Potential: Anticipating shifts in technology and energy production strategies positions ESPs as a key player in the evolving landscape of the oil and gas sector.
By surmising these essential aspects, readers can appreciate not only the mechanics behind ESPs but also their strategic position in today’s energy market.
Future Directions for Research
The exploration into electric submersible pumps is not a closed book. In fact, the horizon for research is vast and varied:
- Environmental Impact Studies: Investigating the long-term ecological footprints of ESPs can shed light on sustainable practices in oil extraction.
- Automation and AI: The integration of artificial intelligence with ESP technologies could revolutionize maintenance and operational efficiency.
- Alternative Energy Integration: As renewable energies become more mainstream, researching how ESPs can work in tandem with these technologies is critical.
- Global Best Practices: Comparative studies across different regions can reveal insights into how localized adaptation of ESPs can lead to success.
- Equipment Durability: Focused research on improving the lifespan and resilience of ESP components in harsh environments could enhance overall reliability.
It's evident that continual inquiry is vital, ensuring that the industry not only adapts to change but also anticipates it, aiming for an efficient and sustainable future in the oil and gas landscape.