Enhancing Productivity Through OEE Analysis
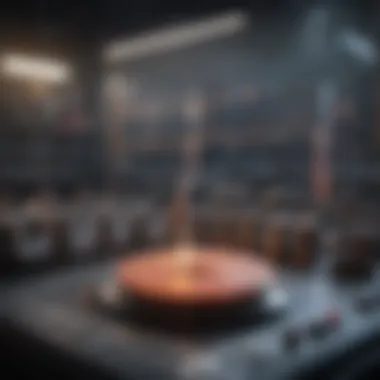
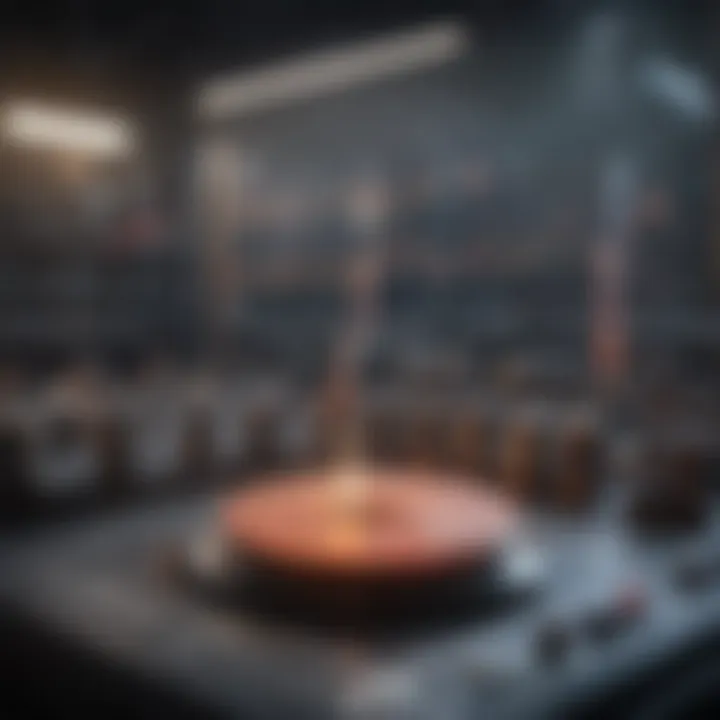
Intro
Overall Equipment Effectiveness (OEE) emerges as a pivotal metric for gauging manufacturing productivity. As industries face increasing pressures to optimize resources and improve efficiency, understanding OEE becomes essential. This section sets the foundation for comprehending how OEE can enhance productivity through effective management practices and data-driven strategies.
OEE is calculated by multiplying three essential factors: availability, performance, and quality. Each of these factors provides insight into different aspects of equipment utilization and operational effectiveness. Organizations prioritizing OEE can uncover hidden costs and inefficiencies, ultimately leading to increased production and enhanced profitability.
In a landscape where competition is fierce, it's crucial for those involved in manufacturing to grasp the nuances of OEE. It is not merely a theoretical concept but a practical tool that can be leveraged to generate significant operational improvements. Through this article, professionals will uncover methodologies for measuring OEE, explore improvement strategies, and acknowledge the vital role of OEE analytics in continuous enhancement processes.
With productivity as a cornerstone of economic success, understanding and implementing OEE creates vast potential for organizations and individuals alike.
Key Concepts and Terminology
Definition of Key Terms
To engage in a thorough analysis of OEE, it is necessary to define key terms that populate this discourse:
- Overall Equipment Effectiveness (OEE): A metric that determines the efficiency of a manufacturing process by evaluating available time versus operational time.
- Availability: Refers to the percentage of scheduled time that the equipment is available for production. High availability indicates minimal downtime due to maintenance or breakdowns.
- Performance: Measures the speed at which the equipment operates compared to its designed capacity. If a machine runs slower than expected, it impacts overall performance negatively.
- Quality: Represents the fraction of products manufactured that meet quality standards. Defects in the product decrease quality and thus reduce the effective output of production.
Concepts Explored in the Article
This article delves into various elements crucial for enhancing manufacturing productivity using OEE:
- Measuring OEE: Discusses various methodologies used for accurate OEE calculation—emphasizing the importance of precise data collection methods.
- Improvement Strategies: Provides insights into various practices and techniques that can be employed in order to boost OEE scores.
- Leveraging Analytics: Explores how data analytics can identify patterns, inefficiencies, and opportunities for enhancing equipment effectiveness.
- Continuous Improvement Culture: Underlines the significance of fostering a culture that continuously seeks operational improvements, crucial for maximizing the benefits of OEE metrics.
Findings and Discussion
Main Findings
Analyzing OEE and its components leads to several important findings. Firstly, companies that implement effective OEE management can significantly reduce waste and operational costs. Organizations often find that simple adjustments in scheduling and equipment maintenance can lead to notable gains in productivity.
Secondly, the clarity offered by OEE analytics aids decision-makers in recognizing root causes of inefficiencies. By understanding specific bottlenecks and limitations within the production line, targeted strategies can be developed for addressing them.
Potential Areas for Future Research
Future research could delve deeper into several aspects of OEE. For instance, exploring how emerging technologies, such as artificial intelligence and machine learning, can further enhance analytics capabilities could be valuable. Additionally, studying the interplay between employee training initiatives and OEE outcomes may yield insights that drive productivity improvements.
Investigation into specific case studies of successful OEE implementation across various industries could also add richness to this field of study. Understanding the unique contexts and strategies utilized in these cases can provide actionable insights for professionals pursuing operational excellence.
Preamble to OEE
Understanding Overall Equipment Effectiveness (OEE) is crucial for enhancing productivity in the manufacturing sector. OEE serves as a barometer for measuring how effectively a manufacturing operation is utilized. It encompasses various elements that provide insight into efficiency and performance, enabling organizations to identify areas for improvement. By focusing on OEE, manufacturers can streamline processes, reduce waste, and ultimately increase profitability.
The relevance of OEE in today's highly competitive landscape cannot be understated. Organizations that monitor and enhance OEE are better equipped to meet customer demands while optimizing resource use. This section will provide a foundational understanding of OEE, setting the stage for a comprehensive analysis of its components and significance.
Definition of Overall Equipment Effectiveness
Overall Equipment Effectiveness is defined as a metric that evaluates the efficiency of a manufacturing process. Specifically, it quantifies the ratio of productive time to total available time, incorporating three key factors: Availability, Performance, and Quality. Each of these components plays a vital role in determining OEE and together they provide a complete picture of operational effectiveness.
The formula for OEE can be expressed as:
[ OEE = Availability \times Performance \times Quality ]\
This straightforward equation captures the essence of manufacturing productivity. Thus, understanding each aspect of OEE is essential for any entity aiming to optimize their operations.
The Historical Context of OEE
The concept of Overall Equipment Effectiveness emerged from the Total Productive Maintenance (TPM) philosophy in the late 20th century. Organizations began recognizing that equipment failure and inefficiencies significantly impacted production quality and timelines. With rising global competition, the need for systematic approaches to maximize machinery performance became apparent.
Initially, OEE was predominantly adopted in Japan, particularly in automotive manufacturing. Its success led to its wider application across various industries. As companies continued to refine their manufacturing processes, OEE evolved into a valuable tool for continuous improvement. Today, it is recognized as an industry standard for measuring and enhancing manufacturing effectiveness. Understanding this historical context gives deeper insight into how OEE has shaped modern manufacturing practices.
Key Components of OEE
Understanding the key components of Overall Equipment Effectiveness (OEE) is essential in enhancing productivity in manufacturing. These components help businesses identify where improvements can be made. By focusing on availability, performance, and quality, organizations can pinpoint inefficiencies and optimize their operations. This section will detail each component's aspects, discussing their importance and influence on OEE.
Availability
Definition of Availability
Availability refers to the percentage of time that a manufacturing unit is actually operational compared to the total planned operational time. High availability indicates that machines are running efficiently and that there are minimal unplanned stoppages. This metric plays a pivotal role in the overall assessment of a manufacturing system. When availability is high, it means that the production process can continuously run, maximizing output.
Key Characteristic of Availability: The primary characteristic of availability is its focus on uptime. A high availability rate ensures that production can meet demands without significant delays. This is a popular choice for many organizations as it focuses on machine reliability and downtime reduction.
Unique Feature: A unique aspect of availability is its ability to highlight both scheduled and unscheduled maintenance issues. This feature often leads to actionable strategies for improving operations. Understanding availability can help identify if available time is being utilized effectively, thus providing insights for necessary adjustments.
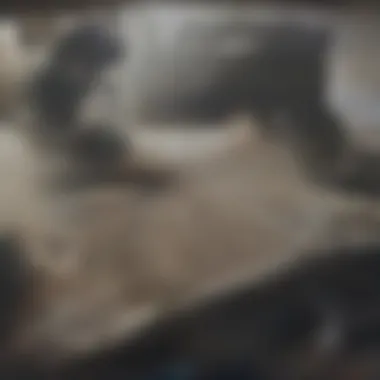
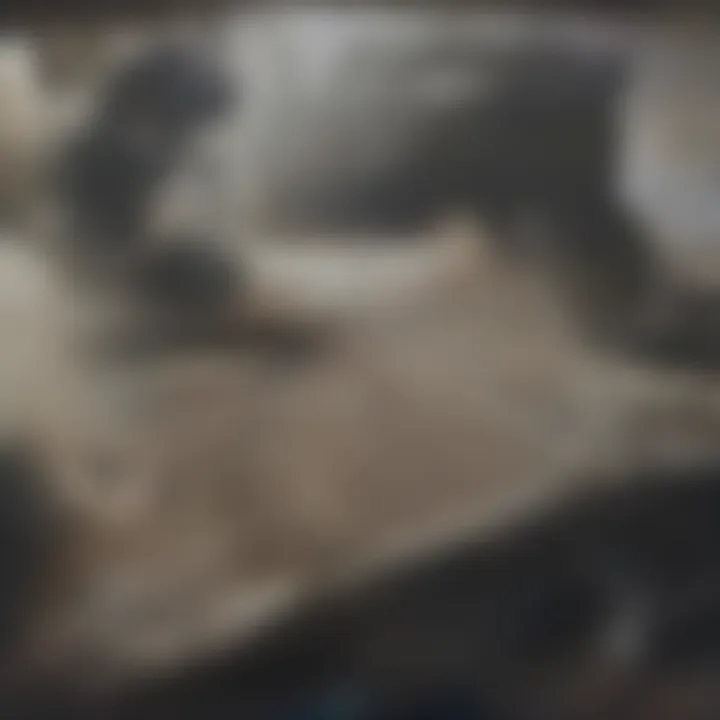
Factors Affecting Availability
Several factors affect availability in a manufacturing environment. These include equipment breakdowns, maintenance schedules, and workforce efficiency. Understanding these factors is crucial to enhancing OEE.
Key Characteristic of Factors Affecting Availability: The ability to assess both internal and external influences on equipment performance characterizes this aspect. Effectively managing these factors can lead to a smoother and more productive operation.
Unique Feature: One advantage of focusing on the factors that affect availability is it provides clear insights for operational improvements. By targeting these areas, companies can prioritize maintenance efforts and better allocate resources to enhance productivity.
Performance
Definition of Performance
Performance measures the speed and efficiency of manufacturing processes when they are running. It evaluates how quickly a machine operates compared to its maximum capacity. Optimizing performance is critical as it directly correlates with achieving production goals efficiently.
Key Characteristic of Performance: The emphasis on speed is a defining characteristic of performance. A well-optimized performance can greatly reduce cycle times and increase production output. This is particularly valuable in competitive manufacturing environments.
Unique Feature: Some organizations use performance as a benchmark against capabilities of machinery. This comparison helps in setting realistic standards and expectations for production output.
Performance Metrics and Benchmarks
Performance metrics provide quantitative data that organizations can use to evaluate effectiveness. This includes measures like cycle time, production rate, and throughput. By establishing benchmarks, companies can assess their current performance against industry standards.
Key Characteristic of Performance Metrics: They provide a quantitative foundation for evaluating production efficiency. The reliance on factual data makes this an effective tool for identifying weaknesses.
Unique Feature: The primary advantage of employing performance metrics is their ability to introduce objectivity into performance evaluation. Organizations can track improvements over time and make data-driven decisions to enhance productivity.
Quality
Definition of Quality
Quality refers to the conformance of products to specifications and standards. It is a crucial aspect of OEE, as poor quality leads to waste and rework, impacting both productivity and costs. Understanding quality helps organizations maintain high standards and minimize defects.
Key Characteristic of Quality: Focus on defect reduction and customer satisfaction defines quality. Ensuring the final product meets specified standards is crucial to maintaining operational excellence.
Unique Feature: Quality not only enhances customer satisfaction but also reduces costs associated with waste and rework. Investing resources in quality assurance practices typically results in long-term savings.
Impact of Quality on OEE
Quality has a direct impact on OEE, often highlighted through the quality rate. When products are consistently produced within specifications, the overall effectiveness of the manufacturing process improves substantially.
Key Characteristic of Impact of Quality: The relationship between quality and productivity is fundamental. Higher quality levels often lead to reduced downtime due to fewer defects and less rework, thus improving OEE.
Unique Feature: This relationship makes quality a critical leverage point for manufacturers. By focusing efforts on enhancing product quality, organizations can see significant improvements in overall equipment effectiveness.
Importance of OEE in Manufacturing
The concept of Overall Equipment Effectiveness (OEE) is vital in the manufacturing sector. It serves as a key metric to assess how effectively a manufacturing operation is utilized. Understanding OEE can yield significant benefits, not only improving production processes but also aligning them with broader business objectives.
OEE acts as a bridge between operational performance and business success. When manufacturers can accurately measure OEE, they can identify inefficiencies that impact their productivity. This identification leads to targeted improvements, which enhance overall performance. OEE is not just a metric; it is a lens through which businesses can view their manufacturing effectiveness.
Linking OEE to Business Goals
Linking OEE to business goals is crucial for ensuring that operational improvements contribute to wider organizational objectives. For example, if a company's goal is to enhance profitability through increased production, monitoring OEE can reveal where bottlenecks occur. By improving these areas, manufacturers can better align their output with market demand, ultimately driving revenue.
To successfully link OEE to business goals, companies must first articulate clear objectives. This can include:
- Increasing production capacity: By identifying factors that lead to downtime, businesses can streamline operations.
- Enhancing product quality: Tracking quality issues through OEE metrics can address root causes and reduce defects.
- Reducing operational costs: Continuous monitoring of OEE can help in identifying wasted resources and improve cost-effectiveness.
By focusing OEE improvements directly on these targets, organizations can boost both operational efficiency and financial performance.
The Financial Implications of OEE
The financial implications of na increased OEE cannot be overstated. High OEE scores often correlate with reduced costs and increased profitability. For instance, when equipment is running at peak efficiency, manufacturing costs decrease due to less waste and rework. Furthermore, a higher OEE can lead to faster production cycles, allowing companies to respond to market demands more quickly and effectively.
Investing in OEE initiatives may require upfront costs, such as purchasing new technology or training staff. However, the long-term financial benefits frequently outweigh these initial investments. Considerations in financial analysis include:
- Return on Investment (ROI): Comparing the cost of OEE-related improvements to the financial gains from increased production.
- Cost Savings: Identifying reductions in labor, materials, and overhead through efficient operations.
- Market Competitiveness: Greater efficiency often leads to better pricing strategies and improved product delivery times which enhance competitive positioning.
*"By measuring OEE and linking it to financial performance, companies can uncover powerful insights that drive sustainable improvement."
In summary, OEE is essential for the manufacturing industry. It provides a framework for defining and achieving business goals, while also delivering measurable financial benefits. With a focus on both operational enhancement and financial efficiency, companies can harness the full potential of OEE.
Measuring OEE
Measuring Overall Equipment Effectiveness (OEE) is a critical aspect of optimizing manufacturing productivity. The importance of measuring OEE lies in its ability to provide a clear and quantifiable indication of how well a manufacturing operation is performing. By understanding OEE, companies can identify specific areas for improvement, align these improvements with strategic goals, and enhance overall efficiency. OEE measurement not only aids in operational analysis but also fosters informed decision-making by providing insights into equipment performance, production processes, and product quality.
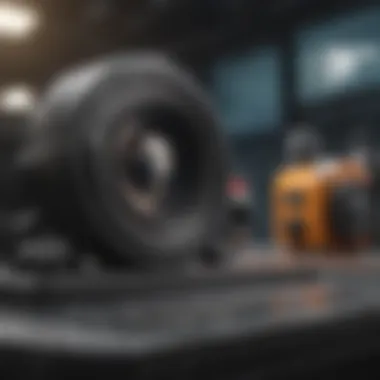
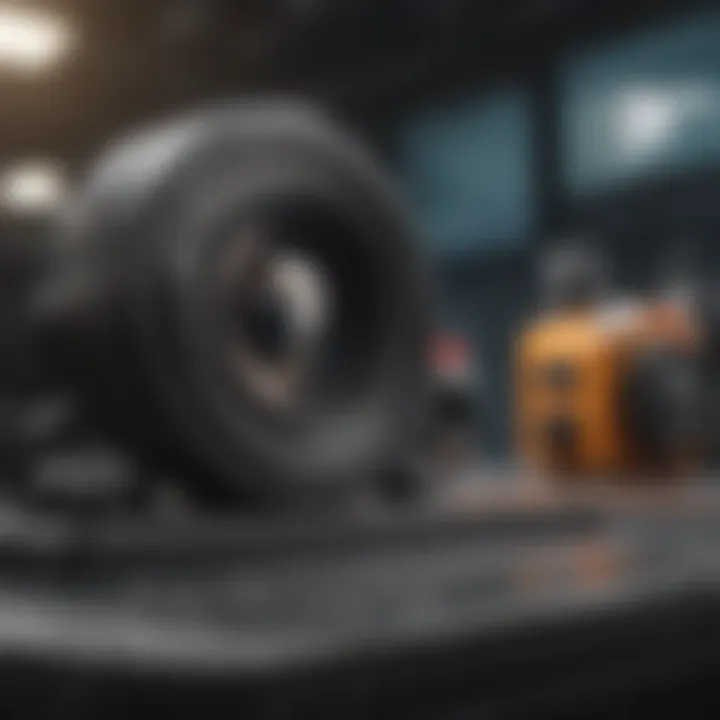
Data Collection Techniques
Data collection is the backbone of OEE measurement. Accurate data is essential to obtain reliable OEE figures, and two primary methods for data collection are commonly utilized: manual data collection and automated data capture.
Manual Data Collection
Manual data collection involves recording operational data by hand, often using spreadsheets or paper forms. This method is beneficial for several reasons. First, it is relatively simple to implement and does not require significant investment in technology. Organizations can quickly start collecting data without a steep learning curve.
However, manual data collection has distinct drawbacks. The main disadvantage is the potential for human error. Additionally, it can be time-consuming as operators may not consistently enter data in real time. The unique feature of this approach is its flexibility; operators can customize data points to gather specific information pertinent to their operations. Nonetheless, the accuracy and timeliness of the data can be compromised, leading to skewed OEE metrics.
Automated Data Capture
Automated data capture is becoming a popular choice due to its efficiency and accuracy. This method utilizes technology, such as sensors and machine interfaces, to gather production data in real time. The key characteristic of automated systems is their ability to eliminate human error, providing highly accurate data for OEE calculation.
One significant advantage of automated data capture is the speed with which data is collected. This enables companies to react quickly to operational changes and inefficiencies. However, the initial cost of implementing such a system can be high, and there may be a learning curve for staff to become familiar with new technologies. The unique feature of automated capture is its integration with existing manufacturing systems, allowing for seamless data flow and analysis.
Calculating OEE
Calculating OEE is a vital step that turns the collected data into actionable insights. The calculation itself is straightforward, yet understanding its nuances can greatly impact productivity strategies.
OEE Formula
The OEE formula is defined as:
[ OEE = \fracAvailability \times Performance \times Quality100 ]\
This formula provides a clear picture of how each component influences overall effectiveness. The key characteristic of this formula is its ability to break down OEE into three distinct yet interconnected elements: availability, performance, and quality. This breakdown allows companies to pinpoint specific inefficiencies.
OEE formula helps in quick assessments but requires careful data collection for accuracy. While it is beneficial in identifying problem areas, it can oversimplify complex issues if taken at face value. The unique feature of the OEE calculation is its holistic view, encapsulating multiple factors influencing productivity.
Case Study on OEE Calculation
A case study exemplifying OEE calculation can provide invaluable insights into its application in real-world scenarios. For instance, consider an automotive manufacturing plant that gathered OEE data over a six-month period. After applying the OEE formula, the results highlighted severe downtime due to maintenance issues, revealing a 15% loss in availability.
The significance of this case study is twofold. Firstly, it illustrates how calculated OEE figures can surface previously unnoticed inefficiencies. Secondly, it shows the potential for improvement. By addressing the maintenance problems identified through OEE analysis, the plant was able to increase its overall productivity by 20% within the following quarter.
This case study emphasizes the practical benefits of OEE calculation, demonstrating its usefulness in driving meaningful operational improvements.
Strategies for Enhancing OEE
Enhancing Overall Equipment Effectiveness (OEE) is vital in any manufacturing environment. These strategies help identify inefficiencies while maximizing resource utilization. Focused implementation sets the stage for sustainable productivity improvements. Each strategy not only targets OEE but also aligns with broader organizational goals. This leads to improved operational efficiency, cost savings, and ultimately a stronger competitive advantage.
Implementing Lean Manufacturing Principles
Lean manufacturing principles streamline processes and eliminate waste. This approach aligns with OEE by enhancing availability, performance, and quality. By applying techniques such as Value Stream Mapping and the 5S methodology, manufacturers can recognize areas for improvement. A crucial aspect of lean is minimizing downtime and optimizing resource allocation. It encourages teams to continuously assess their processes and make adjustments in real time based on feedback. A lean mindset fosters a culture where each employee feels responsible for productivity.
Utilizing Technology for OEE Improvement
Embracing technology is imperative for enhancing OEE. Digital tools can provide deeper insights and help automate data collection. This leads to quicker decisions based on accurate information. Below are two significant areas where technology plays a crucial role.
Software Solutions
Software solutions are critical for data management and analysis in OEE implementation. They simplify the collection process by providing user-friendly interfaces for inputting operational data. A strong characteristic of these software systems is their ability to integrate with existing manufacturing systems. This versatility makes them a popular choice among manufacturers.
Unique features often include customizable dashboards, allowing managers to visualize key metrics at a glance. This immediate access to data helps drive faster responses to any issues that arise on the production floor. However, challenges exist, such as potential complexities during initial setup and the need for user training. It is essential to address these factors to maximize the effectiveness of the software solutions.
Real-Time Monitoring Systems
Real-time monitoring systems are another pillar of technology in OEE enhancement. They provide continuous insights into equipment performance and operational efficiency. A key characteristic is their ability to alert personnel of potential issues before they escalate.
These systems enable manufacturers to monitor machinery remotely, thus reducing the need for manual checks. Unique features may include predictive maintenance capabilities, which can forecast potential failures based on historical data. Such foresight allows for proactive maintenance scheduling, reducing unplanned downtime.
While beneficial, real-time monitoring systems require robust data management strategies. An organization must ensure that the collected data is reliable and actionable. Accepting this technology demands commitment to proper installation and ongoing maintenance.
Cultivating a Continuous Improvement Culture
A culture of continuous improvement is essential for sustained OEE enhancement. It promotes an environment where employees are encouraged to contribute ideas for process improvements. Fostering this culture means involving team members at all levels in decision-making processes.
Workers who feel their input is valued are more likely to engage with OEE initiatives. Regular training sessions and workshops can nurture this mindset, helping employees understand the importance of maintaining high OEE standards. By committing to continuous improvement practices, organizations can adapt to changing market demands and stay competitive.
"A commitment to continuous improvement is key to unlocking the full potential of OEE."
In summary, the integration of lean principles, advanced technologies, and a culture of continuous improvement can significantly enhance OEE. Manufacturers that embrace these strategies are better equipped to achieve sustainable productivity improvements.
Challenges in OEE Implementation
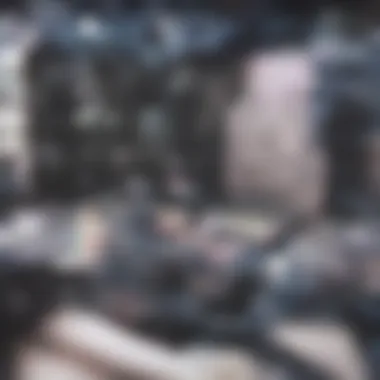
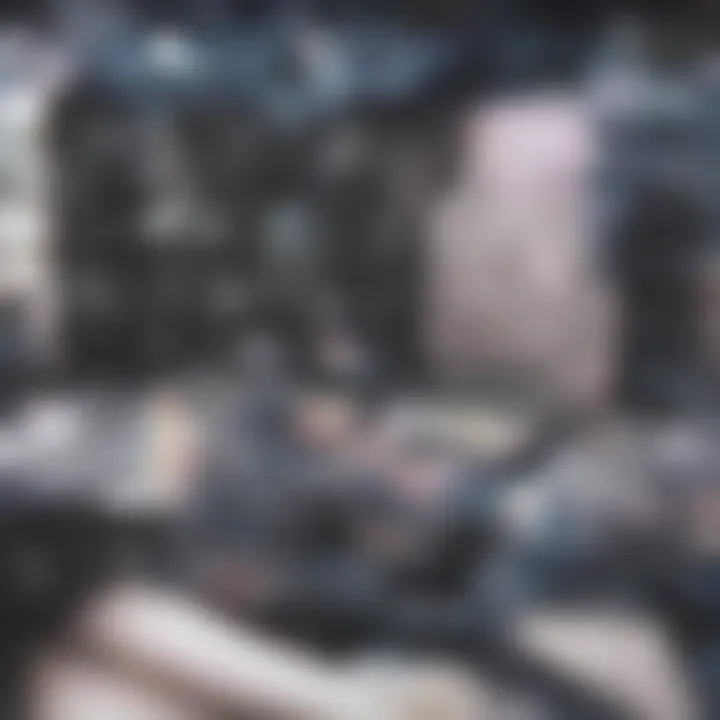
Implementing Overall Equipment Effectiveness (OEE) can significantly enhance productivity in manufacturing, but it is not without challenges. These hurdles can undermine the benefits of OEE if not properly addressed. Understanding these challenges is crucial for organizations aiming for sustainable improvements.
Resistance to Change
Resistance to change is a common obstacle in any improvement initiative, OEE included. Employees might view OEE practices as a threat to their job security or as extra work. This perception can lead to skepticism regarding the goals of OEE initiatives. To mitigate this, organizations must foster an environment that encourages open communication. Education and training sessions related to OEE can play an important role here. By clarifying the benefits of OEE, such as improved working conditions and job stability, resistance can often be alleviated. Moreover, involving employees in the implementation process can result in a shared sense of ownership, which may help in easing their concerns.
Data Accuracy and Reliability Issues
Data integrity is vital for successful OEE implementation. If the data collected is inaccurate or unreliable, the resulting OEE measurements will not reflect the true performance levels. This can lead to misguided conclusions and poor decision-making. Manual data collection methods often introduce human errors. On the other hand, automated data capture systems, while more accurate, can also face issues like equipment malfunctions or software errors. Organizations should invest in robust data management systems to ensure accuracy. Regular audits of data collection processes and incorporating real-time monitoring tools can further enhance the reliability of the data used for OEE calculations.
Balancing Short-Term Goals with Long-Term Vision
The challenge of balancing short-term goals with long-term vision is a critical aspect in OEE implementation. Management may focus on immediate returns or quick wins, neglecting the strategic importance of OEE. While it is essential to demonstrate initial benefits, a narrow focus on short-term performance can detract from sustained growth. OEE requires a long-term commitment to continuous improvement. Companies need to integrate OEE into their overall operational strategy. This means aligning short-term objectives with the broader vision of efficiency and effectiveness. Establishing key performance indicators that reflect both immediate and long-term goals can help maintain this balance.
"The key to successful OEE implementation lies not only in addressing immediate challenges but also in establishing a framework for ongoing improvement and adaptation."
Addressing these challenges effectively allows organizations to harness the full potential of OEE. This leads not only to improved productivity but also to a more engaged workforce.
Case Studies in OEE Improvement
Understanding how Overall Equipment Effectiveness can direct real results in a manufacturing setting is essential. Case studies highlight practical applications and outcomes of OEE strategies in different industries. They provide tangible evidence of the benefits of OEE initiatives. By analyzing these implementations, we can uncover valuable insights applicable to various manufacturing environments. Furthermore, examining industry-specific challenges and solutions can inspire effective practices elsewhere.
Successful Implementation in Automotive Industry
The automotive industry is known for its robust production processes and high demand for efficiency. Companies like Toyota and Ford have successfully used OEE principles to optimize operations. For instance, Toyota's use of lean manufacturing principles has improved its OEE significantly. By identifying downtimes and analyzing the effectiveness of machinery, it successfully reduced waste.
A case study from Ford illustrates the implementation of OEE metrics in its production lines. This automaker focused on increasing availability and performance. By closely monitoring machine performance, Ford identified bottlenecks that led to production delays. Addressing these issues not only enhanced OEE but also resulted in shorter lead times.
Key Takeaways from Automotive Case Studies:
- Quantitative Metrics: Establish measurable objectives for availability, performance, and quality.
- Continuous Monitoring: Use real-time data to identify efficiency barriers and respond promptly.
- Employee Involvement: Engage workers in the OEE process to foster a culture of continuous improvement.
OEE Optimization in Food Manufacturing
Food manufacturing presents unique challenges, including regulatory compliance and perishability. Integrating OEE can support these industries in maintaining product quality while maximizing efficiency. A prominent example is Nestlé, which adopted OEE in its production processes.
Nestlé aimed to improve its factory efficiency by implementing OEE assessment tools. The company focused on quality checks at various stages of production. This proactive measure reduced waste and addressed quality faults early. Another example involves PepsiCo, where analyzing OEE metrics helped streamline operations. The company reduced downtime by implementing proactive maintenance strategies based on OEE findings.
Important Lessons from Food Manufacturing:
- Customer-Centric Approach: Focus on quality to ensure customer satisfaction while improving efficiency.
- Regulatory Compliance: Ensure OEE initiatives align with industry regulations and standards.
- Adaptability: Be prepared to adjust OEE approaches based on product variations and market changes.
Case studies are not merely examples; they offer a roadmap for improvement and insights into practical application of OEE principles in diverse settings.
Future Trends in OEE
The landscape of manufacturing is continuously evolving. In this context, understanding future trends in Overall Equipment Effectiveness (OEE) becomes essential for maintaining competitive advantage. As technologies advance, OEE metrics will become increasingly integrated with automated systems and data analytics. This integration can enhance decision-making processes, optimize asset utilization, and ultimately drive productivity.
The Role of Industry 4.
Industry 4.0 represents a significant shift in manufacturing processes, focusing on data exchange and automation. Its impact on OEE is profound. With the advent of the Internet of Things (IoT), machines can communicate with each other. This connectivity offers real-time monitoring capabilities. Companies can track equipment performance instantaneously. The result is greater visibility throughout production processes.
Moreover, integrating OEE with Industry 4.0 technologies leads to higher efficiency. Real-time data allows for quicker reactions to production issues. Manufacturers can pinpoint problems earlier, reducing downtime and inefficiencies. This proactive approach minimizes waste, keeping the production schedule on track.
Predictive Analytics and OEE
Predictive analytics plays a crucial role in shaping the future of OEE. Through the analysis of historical data, manufacturers can predict potential failures and maintenance needs. This data-driven decision-making reduces unplanned downtime. The key benefits include enhanced production continuity and improved resource allocation.
Utilizing predictive analytics helps in maintaining high equipment effectiveness. By forecasting when equipment may fail, companies can schedule maintenance activities strategically. This ensures that productivity remains unaffected. Furthermore, predictive models can refine OEE by identifying patterns that lead to downtime or inefficiency.
End
In summary, the exploration of Overall Equipment Effectiveness (OEE) provides valuable insights into enhancing manufacturing productivity. This article emphasizes several critical elements that underscore the importance of OEE. First, we have identified that OEE acts as a key performance indicator that reflects the efficiency of manufacturing processes. Understanding the three main components of OEE — Availability, Performance, and Quality — helps in pinpointing specific areas for improvement in operations. Each of these components plays a unique role in affecting the overall productivity of a manufacturing unit.
Moreover, this article has outlined the methodologies for measuring OEE effectively. By utilizing both manual and automated data collection techniques, organizations can quantify their OEE accurately. The calculation and interpretation of OEE is also a focal point, providing a clear view of current performance levels. This clarity enables companies to implement targeted strategies aimed at increasing efficiency.
Another significant point discussed is how to foster a culture of continuous improvement. Organizations that embrace ongoing assessment and refinement of their processes are more likely to realize the full potential of OEE. The benefits of adopting a continuous improvement mindset are numerous, ranging from enhanced team engagement to substantial financial gains.
As we conclude, it is evident that OEE is more than just a metric; it is a comprehensive framework that, when correctly applied, can lead to sustained improvement in manufacturing productivity.
Recap of Key Insights
- Understanding OEE: Recognizing the definition and historical context of OEE is foundational for its effective implementation.
- Key Components: Familiarity with Availability, Performance, and Quality enables targeted strategies.
- Measuring OEE: Accurate data collection and analysis are vital for assessing effectiveness.
- Improvement Strategies: Applying lean principles and utilizing technology contribute to OEE optimization.
- Challenges and Solutions: Acknowledging potential challenges such as resistance to change and data issues is crucial for addressing them.
- Future Perspectives: Trends like Industry 4.0 and predictive analytics are reshaping the landscape of OEE.
Call to Action for Continuous Improvement
To truly harness the power of OEE, organizations must commit to continuous improvement. This commitment entails fostering a company-wide understanding of OEE principles among employees at all levels. Practical steps can include:
- Training Programs: Regular training sessions aimed at educating the workforce about OEE and its benefits.
- Engagement Initiatives: Encouraging all employees to contribute ideas for improving equipment effectiveness.
- Monitoring Progress: Establishing real-time monitoring systems to track OEE metrics.
Emphasizing these actions helps in maintaining a focus on productivity and encourages a proactive approach toward continuous improvement. Companies should not only aim for immediate gains but also set long-term goals that align with OEE principles. Such an approach will transform the operational landscape, leading to heightened productivity and long-lasting success in manufacturing.