The Evolution of 3D Printed Generators in Energy
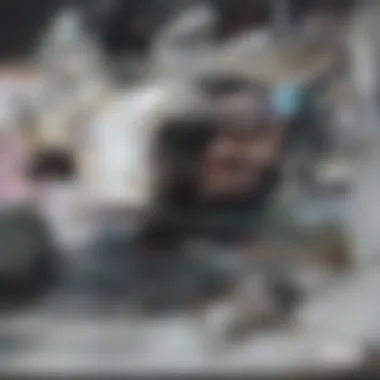
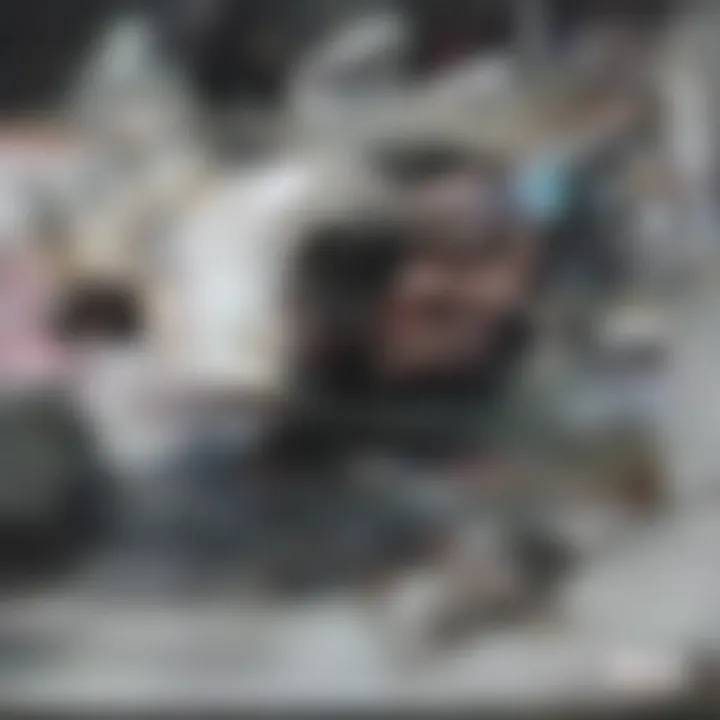
Intro
The discussion surrounding energy production has gained momentum, especially with advancements in technology. Among these advancements, 3D printing emerges as a transformative force in generator manufacturing. This article aims to delve into the implications and developments of 3D printed generators, capturing the nuances of their design principles, material usage, and efficiency metrics.
Technological innovations influence our approach to sustainable energy. By leveraging 3D printing, manufacturers can create more efficient, cost-effective, and tailored generators. This is essential as the world seeks sustainable alternatives to traditional energy sources. In the sections that follow, we will explore key concepts related to 3D printed generators, examine significant findings, and identify areas ripe for further research.
Key Concepts and Terminology
Definition of Key Terms
Understanding the technical language surrounding 3D printed generators is critical. Here are some key terms:
- 3D Printing: A process that creates a three-dimensional object based on digital models, layer by layer.
- Generator: A device that converts mechanical energy into electrical energy.
- Additive Manufacturing: A synonym for 3D printing that focuses on building objects by adding material rather than subtracting it.
Concepts Explored in the Article
The discussion will cover several core concepts:
- The importance of design flexibility in 3D printing.
- The role of sustainability in modern energy production.
- Innovations in materials that enhance generator performance.
Findings and Discussion
Main Findings
Research indicates that 3D printing significantly reduces lead times in generating prototypes. This efficiency fosters rapid innovation, particularly in generator design. By utilizing lightweight materials, such as thermoplastics or metals, printed generators exhibit enhanced efficiency and performance in diverse conditions.
Moreover, studies show that 3D printed components can sometimes be more durable than traditionally manufactured parts, which leads to reduced maintenance costs. The layered manufacturing process also facilitates complex geometries that can improve airflow or heat dissipation.
Potential Areas for Future Research
Exploration into this technology is ongoing. Possible areas for future research include:
- Material Development: Investigating new composites that could further enhance the efficiency of generators.
- Application of AI: Utilizing artificial intelligence to optimize generator designs based on operational data.
- Environmental Impact Analysis: Conducting studies to better understand the lifecycle impact of 3D printed generators.
The intersection of engineering advancements and sustainable energy solutions is crucial for the future of energy production.
Through these explorations, we seek to illuminate both theoretical frameworks and practical applications, guiding students, researchers, educators, and professionals in navigating the evolving landscape of energy technology.
Foreword
The evolution of 3D printed generators is critically important in understanding the future of energy production. This technology represents a significant shift in how generators are designed, produced, and deployed. Traditional manufacturing methods often entail lengthy processes, extensive material waste, and higher costs. In contrast, 3D printing stands out due to its additive nature, which allows for precise control over material usage and design complexity. Thus, 3D printed generators not only promise increased efficiency but also lower the overall environmental impact of production.
The benefits of exploring this topic are manifold. First, it opens doors to innovative designs that can potentially surpass the limitations of conventional generators. These include enhancements in modularity and customization, allowing for tailored solutions based on specific energy needs. The implications for sectors such as renewable energy are particularly noteworthy, as 3D printing can enable more accessible and sustainable energy solutions in various contexts.
Additionally, understanding the technological underpinnings and the evolving landscape of 3D printing will aid researchers and professionals in evaluating its significance within energy systems. By recognizing the capabilities and limitations of this technology, stakeholders can make informed decisions, whether they are involved in research, policymaking, or practical applications.
In summary, the examination of 3D printed generators is not just a technical discussion; it involves an intricate analysis of design innovations, energy efficiency, and environmental sustainability. By delving into this topic, we can grasp how these factors interconnect to shape the future of energy production.
Historical Context of Generator Technology
The history of generator technology highlights the pivotal transformations in energy production. By tracing the journey of mechanical and electrical generators, we see the gradual evolution of concepts that lay the groundwork for modern energy systems. Understanding this historical context is essential for grasping the significance of 3D printed generators in today's energy landscape.
Early Mechanical Generators
Before the rise of electricity, mechanical generators powered various applications. The earliest examples include waterwheels and windmills, which transformed kinetic energy from nature into usable mechanical energy. These machines were simplistic, relying on physical movement to generate power. They played a crucial role in agricultural societies, significantly enhancing productivity. The reliance on mechanical elements limited the scale and versatility of energy production.
The development of steam engines by inventors like James Watt in the 18th century marked a turning point. These engines harnessed heat energy to create motion, allowing for the mechanization of numerous tasks. This shift from purely mechanical energy sources signaled the beginning of more advanced generator technologies.
Rise of Electric Generators
The transition to electric generators fundamentally changed how energy was produced and consumed. In the late 19th century, innovators like Michael Faraday developed the principles of electromagnetic induction. This discovery laid the foundation for electric generators that converted mechanical energy into electrical energy, dramatically increasing the efficiency and scope of energy production.
The introduction of devices like the dynamo revolutionized industry and everyday life. Electric generators became the backbone of power plants, supplying electricity to homes and industries. This era also marked the expansion of the electrical grid, as regions became interconnected to distribute power more effectively. With the growing demand for electricity, the race for more efficient electric generators began, driving innovation and competitiveness in the market.
Impact of Technological Advances
The evolution of generator technology is closely tied to broader technological advances. Innovations in materials, engineering design, and manufacturing processes have continually enhanced the efficiency and performance of generators. The adoption of advanced materials like high-performance alloys and composite materials allowed for lighter and more durable generator components.
Moreover, the digital age has ushered in advancements in control systems and automation. Sophisticated software tools facilitate real-time monitoring and optimization of generator performance, ensuring they operate at peak efficiency. These developments not only improved energy output but also contributed to the reliability and sustainability of power generation.
As we move towards 3D printed generators, it is crucial to acknowledge the foundations laid by these historical technological advances. They provide context for how current innovations can further transform energy production, making it more sustainable and adaptable to modern needs.
Understanding 3D Printing Technology
In the context of 3D printed generators, understanding the technology behind additive manufacturing is crucial. This knowledge provides insights into how generators can be designed, produced, and optimized more efficiently than traditional methods. The significance of this topic extends to the environment, cost-effectiveness, and the potential for innovation in energy production.
Principles of Additive Manufacturing
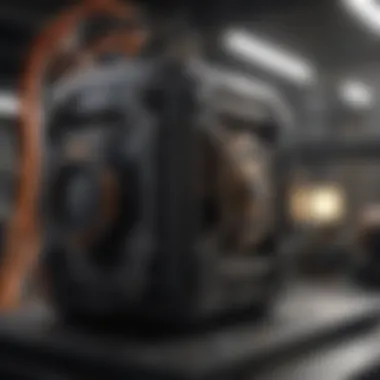
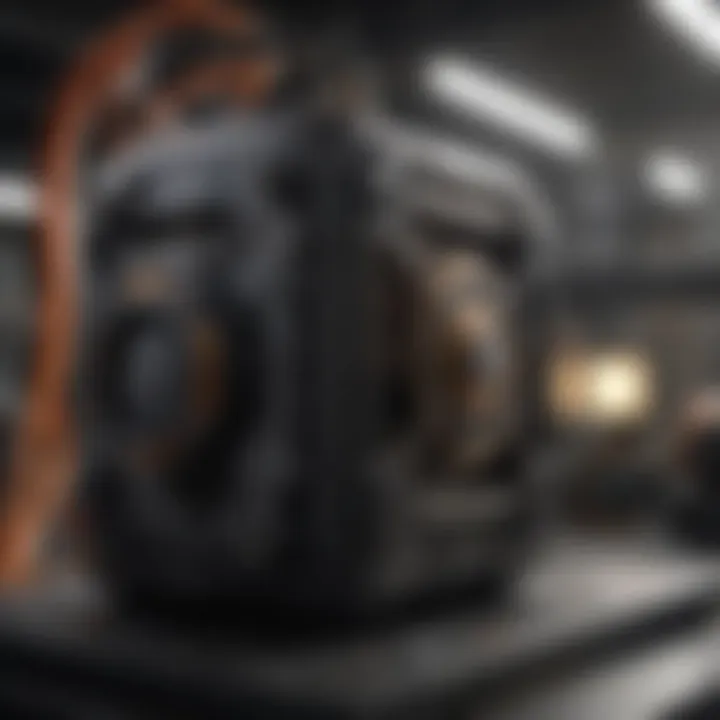
Additive manufacturing is fundamentally different from conventional subtractive manufacturing. It builds objects layer by layer, using materials such as plastics, metals, and ceramics. This principle allows for the creation of complex geometries that would be difficult or impossible to achieve with traditional machining methods.
One of the main advantages of additive manufacturing is the reduction of waste. Since material is only added where needed, safety and efficiency increase. This approach can lead to significant cost savings and quicker production times, making it particularly attractive for energy-producing devices like generators.
Types of 3D Printing Methods
There are various types of 3D printing methods that apply to the production of generators.
- Fused Deposition Modeling (FDM): This is one of the most commonly used methods, where thermoplastic materials are heated until they melt and are extruded in layers.
- Selective Laser Sintering (SLS): This method uses a laser to fuse powdered materials, suitable for creating robust parts.
- Direct Metal Laser Sintering (DMLS): DMLS is a specialized method for metal parts. It offers high strength and durability;
Each method has its pros and cons, depending on application and materials used.
Material Considerations
Plastics
Plastics play an important role in 3D printed generators. They are lightweight, versatile, and often cost-effective. The main characteristic of plastics is their ease of use during the printing process. They allow for the production of intricate designs with minimal energy input. However, their main disadvantage lies in thermal and mechanical properties when compared to metals and ceramics.
For instance, materials like Acrylonitrile Butadiene Styrene (ABS) offer good strength but may not withstand high temperatures as well as metals. Nonetheless, plastics are prevalent due to their availability and reduced production costs.
Metals
The use of metals in 3D printed generators introduces greater strength and resistance to wear. Materials like aluminum and titanium are commonly used. The key characteristic of metals is their high performance under extreme stress and temperatures.
Metal parts, produced through methods such as DMLS, can achieve complex structures, which enhance the generatorβs efficiency. However, the drawback lies in the higher costs of metal powders and the lengthy printing process, which may not be suitable for all applications.
Ceramics
Ceramics are another material option in the realm of 3D printed generators. Their main contribution is their excellent thermal resistance and durability. Ceramics facilitate the fabrication of components that operate under harsh conditions, making them a preferred choice for specialized applications.
The unique feature of ceramic materials is their ability to withstand high temperatures without deforming. Nonetheless, they tend to be more brittle than metals and are susceptible to cracking, limiting their use to specific generator designs.
3D Printed Generators: Design and Functionality
The design and functionality of 3D printed generators are integral to their role in reshaping energy production. This technology allows for innovative engineering solutions that directly address the challenges of traditional generator designs. By utilizing 3D printing, engineers can create components with enhanced efficiency that were previously difficult or impossible to manufacture. The flexibility in design means that alterations can be made quickly and easily, which leads to reduced time in production and the ability to adapt designs to specific energy needs.
Design Elements
Modularity
Modularity refers to the capacity to create generators in separate, distinct sections. This aspect is vital because it enables easy upgrades and repairs. A modular system allows for an efficient way of addressing performance issues without needing to replace an entire generator.
One key characteristic of modularity is its scalability. As energy needs increase, additional modules can be added. This adaptability is a major benefit, promoting longer-lasting equipment and decreasing waste. However, one drawback can be the upfront cost associated with comprehensive modular designs.
By utilizing modular designs, companies can personalize energy solutions for varied applications and environments.
Customization
Customization is fundamental to the appeal of 3D printed generators, allowing unique specifications to fit specific applications. This aspect enables engineers to tailor each generator to its intended use, ensuring optimal performance.
A primary feature of customization is the ability to select materials and dimensions based on environmental conditions and performance metrics. This individualization makes it a valued choice in the energy sector. The downside is that highly customized systems may encounter difficulties in sourcing compatible replacement parts.
Overall, customization offers substantial benefits. It leads to efficiency improvements and greater satisfaction for end-users who have specific energy requirements.
Functional Components
Stators
Stators play a crucial role in any generator's operation. They are the stationary parts that create a magnetic field when electricity is supplied. In 3D printed generators, the design of stators can significantly enhance efficiency.
One of their most important characteristics is their structural stability. A well-designed stator helps produce consistent energy output, making it a reliable choice in diverse applications. The disadvantage can sometimes be found in complex shapes resulting from 3D printing. If not designed properly, it may affect the magnetism.
The integration of advanced designs can enhance the overall functionality of stators in 3D printed generators.
Rotors
The rotor is the moving component within a generator, responsible for interacting with the stator to generate electricity. The advancement in rotors through 3D printing has led to developments in aerodynamics and weight reduction.
One key characteristic of rotors is their optimized rotation speed. This can lead to higher energy output without substantial increases in input energy. However, challenges exist in achieving perfect balance. Unbalanced rotors can lead to mechanical failures and inefficiencies.
Significantly, 3D printing allows for rapid prototyping, helping identify and correct rotor issues before final production.
Windings
Windings in a generator are the coils of wire that convert magnetic energy into electrical energy. The design of windings can have a profound effect on both performance and efficiency.
One major feature of windings is their arrangement. This impacts how the magnetic field is induced. Creative winding designs can improve energy conversion rates, making them a favorite in 3D printed generator applications. A challenge arises in managing thermal output. Excessive heating can reduce the lifespan of the windings, necessitating careful thermal management strategies.
Innovative configurations and materials used in windings can enhance overall generator performance, making them an essential consideration in design.
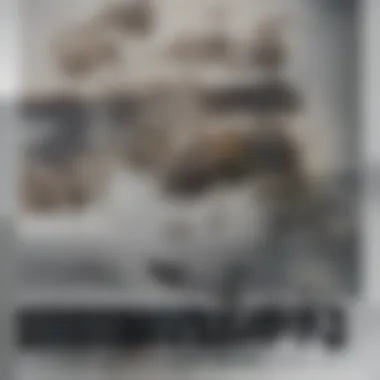
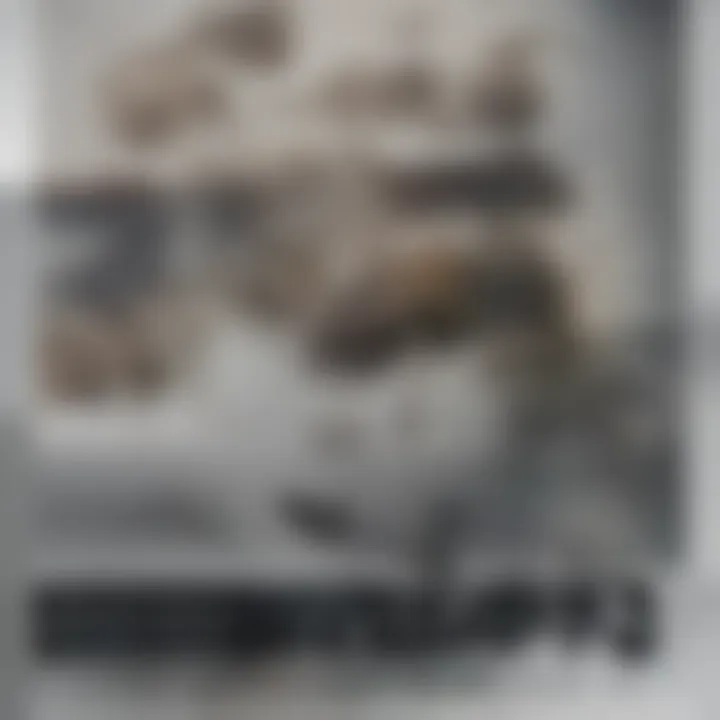
By understanding and optimizing these design elements and functional components, 3D printed generators can achieve enhanced efficiency and adaptability, reinforcing their role in the future of energy production.
Efficiency Metrics in 3D Printed Generators
Understanding efficiency metrics in 3D printed generators is pivotal. These metrics serve as benchmarks that enable comparison of performance, reliability, and effectiveness in energy production. Efficient generators play a crucial role in sustainability, providing cleaner energy while maximizing output. Advances in 3D printing technology not only enhance the performance of these generators but also present new challenges in measurement and standardization. This section will dissect these efficiency metrics in detail to illustrate their significance in the realm of energy production.
Performance Indicators
Performance indicators encompass various metrics such as power output, efficiency rate, and reliability. For 3D printed generators, key indicators might include:
- Power Output: The total energy generated under specific conditions. Higher output typically translates to better performance.
- Energy Conversion Efficiency: This indicates how effectively the generator converts mechanical energy into electrical energy. A high efficiency rate is desirable for reducing waste and enhancing sustainability.
- Durability: Materials and printing techniques greatly influence the lifespan of a generator. Understanding durability as a performance indicator is crucial, as it determines maintenance frequency and overall costs.
These indicators are critical for assessing generator efficiency, especially in renewable energy applications. They help visualize how well a design performs against traditional units and guide innovations.
Comparative Analysis
Comparative analysis of conventional generators and 3D printed generators is essential. Each type of generator has distinct characteristics that impact their application in various environments. In a direct comparison, several factors come into play:
Conventional Generators vs. 3D Printed Generators
Conventional generators are often large, bulky, and use traditional manufacturing techniques. They are generally well-established with optimized designs. However, they can lack customization and modularity often desired in modern energy solutions. On the other hand, 3D printed generators illustrate notable advantages:
- Customization and Modularity: Since they are produced layer by layer, specific demands for size, shape, and performance can be met more easily. This flexibility opens up new possibilities for different applications.
- Cost-Effective Production: Lower material waste in 3D printing can substantially reduce production costs and environmental impact compared to traditional methods.
- Quick Prototyping: The ability to rapidly prototype designs accelerates innovation, allowing developers to swiftly test and iterate their creations.
However, 3D printed generators face certain disadvantages, such as:
- Material Limitations: Not all materials used in 3D printing provide the same mechanical strength or resilience as traditional materials.
- Regulatory Hurdles: Certification and standardization of new designs can be challenging, impacting market acceptance.
"The transition from conventional to 3D printed generators reflects a significant change not only in technology but also in the approach to energy production itself."
This comparative analysis underscores the strengths and weaknesses of both types of generators. Understanding these dynamics is vital for stakeholders in the energy sector as they navigate the ongoing evolution of generator technologies.
Applications of 3D Printed Generators
The significance of 3D printed generators is profound in the landscape of modern energy production. These devices demonstrate versatility and innovation across various sectors. The applications of 3D printed generators extend from renewable energy systems to off-grid solutions, showcasing their benefit in enhancing energy accessibility and sustainability. This section will delve into specific areas where these generators manifest their utility, along with considerations for their practical use.
Renewable Energy Systems
3D printed generators play a crucial role in renewable energy systems. The integration of additive manufacturing allows for the creation of optimized designs tailored to specific energy production needs. This leads to significant reductions in production costs and time. They can be specifically designed for integration with solar panels, wind turbines, or hydroelectric systems.
- Customization: Each generator can be modified based on local environmental conditions. For instance, a generator used in a windy zone can be designed for better aerodynamics.
- Material Efficiency: The 3D printing process minimizes waste by using only the required material. This reduces the overall environmental impact.
- Deployment Speed: With the ability to print components rapidly, deployment of renewable energy solutions is quicker compared to traditional manufacturing methods.
In effect, 3D printed generators can significantly boost the efficiency and effectiveness of renewable energy systems.
Off-Grid Solutions
The application of 3D printed generators in off-grid scenarios is another vital area. Rural areas often face challenges in accessing reliable power. 3D printed technology allows for the development of small-scale generators that are easy to transport and install.
- Scalability: These generators can be produced in various sizes, making them suitable for both homes and larger community projects.
- Cost-Effective: Reduced manufacturing costs lead to cheaper energy solutions for remote regions.
- Simplicity of Maintenance: The modular nature of 3D printed generators facilitates easier repairs and replacements, encouraging local servicing.
This adaptability addresses specific needs of isolated environments, making power generation accessible.
Urban and Rural Deployments
3D printed generators have unique applications in both urban and rural settings. Cities can utilize these generators to supplement the existing energy grid while rural areas can depend on them for independent power.
- Urban Adaptations: In urban environments, generators can be integrated with building designs, ensuring that urban infrastructure benefits from renewable energy sources without major overhauls.
- Rural Empowerment: For rural populations, these generators provide an opportunity for energy autonomy, reducing dependency on centralized energy systems.
"The expansion of 3D printed generators bridges the gap between advanced technology and everyday energy needs, facilitating a transition towards more sustainable practices in energy production."
By addressing both urban and rural demands, 3D printed generators pave the way for broader energy solutions aligned with modern needs.
Environmental Implications
The discussion of environmental implications in the context of 3D printed generators is vital, as it touches on various aspects of sustainability and ecological impact. As energy production continues to evolve, understanding the environmental footprint of new technologies like 3D printing becomes increasingly important. This section investigates how these advancements can lead to reduced waste, improved energy efficiency, and a lower overall impact on the environment.
Lifecycle Analysis
A thorough lifecycle analysis (LCA) evaluates the environmental effects of a product over its entire lifespan, from material extraction to disposal. In the case of 3D printed generators, this analysis can highlight several significant benefits:
- Reduced Resource Consumption: Compared to traditional manufacturing, 3D printing often requires less material to produce the same amount of functional components. This decrease in wastage is critical because it reduces the strain on natural resources.
- Energy Efficiency in Production: The additive manufacturing process allows for the creation of complex geometries that are typically difficult to achieve with conventional methods. This efficiency can lead to more effective designs that optimize the generator's energy output.
- End-of-Life Considerations: 3D printed parts can often be designed with disassembly in mind, allowing easier recycling at the end of a generator's lifecycle. This focus can help minimize the amount of waste that ends up in landfills.
"Understanding the lifecycle of 3D printed generators provides insight into their potential for reducing waste and enhancing energy efficiency."
By adopting lifecycle analysis for 3D printed generators, stakeholders can make informed decisions about materials, processes, and designs that align with sustainability goals.
Sustainability of Materials
Material choice plays a crucial role in the environmental sustainability of 3D printed generators. The following factors demonstrate how responsible material selection can lead to reduced environmental impacts:
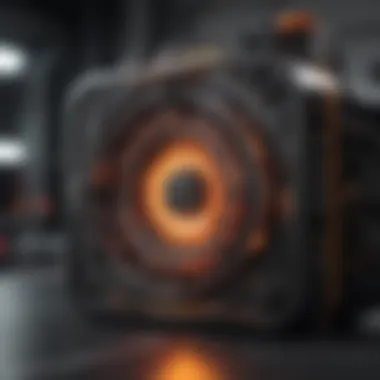
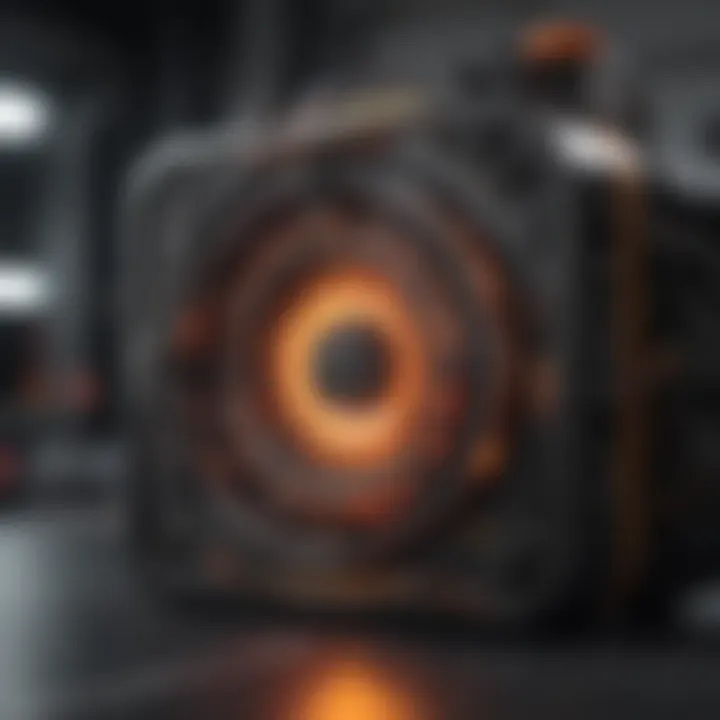
- Recyclability: Many materials used in 3D printing, such as certain plastics and metals, can be recycled. This capability of recycling helps maintain a circular economy, where resources are reused rather than discarded.
- Biodegradable Options: The development of biodegradable materials offers a promising avenue for sustainable manufacturing. Using materials that break down naturally can diminish the long-term environmental impact of waste associated with generator production.
- Local Sourcing: 3D printing can facilitate local production, reducing transportation emissions. By sourcing materials closer to the site of manufacturing, businesses can further minimize their carbon footprint.
Challenges in Implementation
The emergence of 3D printed generators holds significant promise for diversifying energy production. However, the path to widespread adoption is fraught with challenges. The implementation of this technology requires careful navigation through various obstacles that can hinder progress. Understanding these barriers is critical for researchers, engineers, and policymakers aiming to integrate 3D printed generators into the energy landscape.
Technical Barriers
One of the foremost technical barriers is the current limitations in 3D printing technology itself. While additive manufacturing has advanced significantly, it still cannot match the precision and durability of traditional manufacturing methods for some components. This is especially evident in the production of functional parts that require high levels of reliability under stress. 3D printed materials may not withstand extreme temperatures or pressures, limiting their applications in certain environments.
Moreover, the process of designing and fabricating a generator using 3D printing requires expertise in both the fields of electrical engineering and additive manufacturing. Engineers must ensure that the designs not only maximize efficiency but also account for potential issues in material behavior, which adds complexity to the development phase.
Regulatory Considerations
Another layer of complexity lies in regulatory considerations. As 3D printed generators differ from conventional units, they may not fit neatly into existing regulatory frameworks. Standards for safety, performance, and environmental impact must be established specifically for 3D printed devices. This lack of standardized guidelines can result in delays in certification and approval processes, dissuading companies from investing in this technology.
Furthermore, especially in regions with strict energy regulations, the introduction of 3D printed generators may necessitate new laws or amendments to current legislation. Navigating these regulatory landscapes is vital for facilitating market entry and ensuring consumer safety.
Market Acceptance
Finally, market acceptance remains a critical challenge. Consumer perception of 3D printed generators plays a significant role in their adoption. Many potential users may be hesitant to trust new technologies that differ markedly from well-established practices. Public understanding of the benefits and capabilities of 3D printed generators is essential for fostering acceptance.
Education and outreach efforts must be prioritized to demonstrate the efficiency, sustainability, and economic advantages of this technology. Potential users should be informed about case studies and success stories to build confidence in transitioning to 3D printed solutions. Ultimately, overcoming these challenges and cultivating a positive reception in the market could determine the future trajectory of 3D printed generators.
Case Studies
The inclusion of case studies in this article on 3D printed generators is essential for multiple reasons. These exemplars showcase real-world applications and actual deployments of technology. They allow us to observe how theoretical concepts align with practical execution. Through specific examples, we capture the nuances, successes, and setbacks that come with innovation in the field.
Benefits of Analyzing Case Studies:
- Contextual Understanding: They provide a context that theoretical discussions often lack.
- Learning from Experience: Each study reveals lessons learned, which can guide future projects.
- Technology Evolution: Case studies illustrate how 3D printing technology has matured and adapted in energy production.
- Diverse Applications: They reflect a variety of applications, from renewable systems to off-grid solutions, broadening the scope of understanding.
"Case studies play a pivotal role in bridging the gap between theory and practice. They provide a window into the challenges and successes of implementing cutting-edge technologies."
Understanding these projects offers valuable insights into the mechanics and complexities involved in deploying 3D printed generators. Next, we look at some innovative projects that have utilized this technology.
Innovative Projects Using 3D Printed Generators
Various innovative projects have harnessed the power of 3D printing to create generators that meet unique energy needs. For instance, researchers at the University of San Diego have developed lightweight, portable generators tailored for emergency situations. These generators can be rapidly produced on-demand, minimizing the wait time in crisis scenarios.
Another significant project is run by a team in the Netherlands which focused on integrating 3D printed components into wind turbines. By customizing parts through additive manufacturing, they achieved better performance and efficiency, leading to increased energy output.
In an environment where conventional manufacturing constraints often limit design, 3D printing allows for creative freedom. This adaptability results in generating solutions that traditional approaches would not easily achieve. As such, 3D printing aligns with the growing global demand for sustainable energy solutions and off-grid capabilities.
Analysis of Successes and Limitations
Analyzing the successes and limitations of 3D printed generators presents a balanced view of their viability. Successful projects showcase how 3D printing can address specific challenges, such as resource scarcity and time constraints. Remote communities, for example, have gained better access to power through customized, 3D printed solutions tailored to their local conditions.
However, limitations exist, including material constraints that affect durability and efficiency. While certain materials have proven effective, others may not withstand the test of time or operational stress. The manufacturing process itself can also present challenges, such as quality control and scalability. These aspects need careful consideration for broader deployment.
In summary, case studies on 3D printed generators reveal both the potential and hurdles of this emerging technology. Emphasis on innovative projects illustrates how adaptability meets the demand for efficient energy solutions. Meanwhile, understanding the limitations helps refine future approaches to design and implementation.
Future Directions
The trajectory of 3D printed generators is at a pivotal moment. Understanding the future directions of this technology is crucial, as it shapes both the capabilities and accessibility of energy production. These advancements could lead to innovations that not only enhance efficiency but also democratize energy access on a global scale.
Technological Advancements
3D printing technology continues to develop rapidly. These advancements are opening new avenues for generator production. One area of enhancement is in material science. New materials, such as advanced thermoplastics and metal alloys, are being tested for better strength and thermal stability in generator components. This can lead to more reliable and efficient performance under varied operating conditions.
Moreover, improved printing techniques like multimaterial 3D printing allow for the creation of complex geometries that were previously impossible using traditional manufacturing methods. This can lead to generators that are lighter, more compact, and tailored for specific energy needs.
In addition, software advancements play a significant role. Enhanced simulations and AI-driven design software enable engineers to optimize generator layouts. This facilitates a more efficient design process and quicker prototyping, reducing development time and costs.
Potential Innovations in Design
The design of 3D printed generators is ripe for innovation. One significant area is modularity. Future designs may prioritize modular components, making it easier to replace or upgrade parts. This not only enhances maintenance but also allows for greater customization based on user requirements or evolving energy needs.
Another promising direction is the integration of smart technologies. By embedding sensors within 3D printed components, generators can monitor their performance in real-time. This capability supports predictive maintenance, significantly reducing downtimes and extending the lifespan of equipment.
In terms of aesthetics and consumer appeal, there is potential for incorporating design customization for consumer preferences. Users might choose generators that fit personal or business visual styles without compromising functionality, expanding the market reach of 3D printed energy solutions.
"The future is not something we enter. The future is something we create."
β Leonard I. Sweet
Ending
The conclusion of this article serves several important roles. First, it synthesizes the information presented in the preceding sections, emphasizing the evolutionary journey of 3D printed generators in the field of energy production.
Understanding this technology matters for several reasons. The article highlights the transformation in design and functionality that 3D printing offers. This method allows for more efficient use of materials, enhanced customization, and modularity in generator design. As demands for sustainable energy solutions increase, adopting 3D printed generators could play a crucial role in meeting energy needs with decreased environmental impact.
Additionally, this conclusion addresses the benefits of integrating 3D printing into the generator manufacturing process. For instance, it enables rapid prototyping, reducing development time and costs. Such advancements broaden access to innovative energy solutions, particularly in remote or underserved areas. Thus, enhancing energy decentralization becomes a viable option.
Moreover, the conclusion reflects on the technical and regulatory challenges that still need overcoming. Awareness of these obstacles is necessary for practitioners, researchers, and policymakers aiming to implement 3D printed generator technologies effectively. Addressing these issues can lead to smoother transitions and wider adoption in various applications.
Ultimately, the journey of 3D printed generators underscores a significant shift in energy production paradigms. As technology continues to develop, the implications for efficiency, sustainability, and accessibility grow increasingly profound. Engaging with this knowledge equips readers with a deeper appreciation for how engineering innovations can redefine our approach to energy generation.