Exploring Rotomolded Plastic: Applications and Innovations
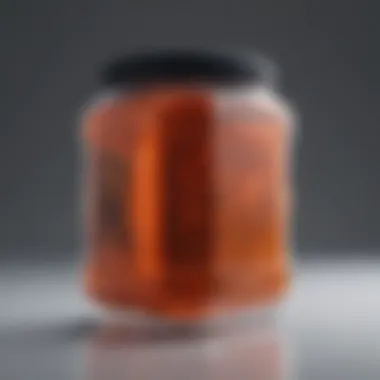
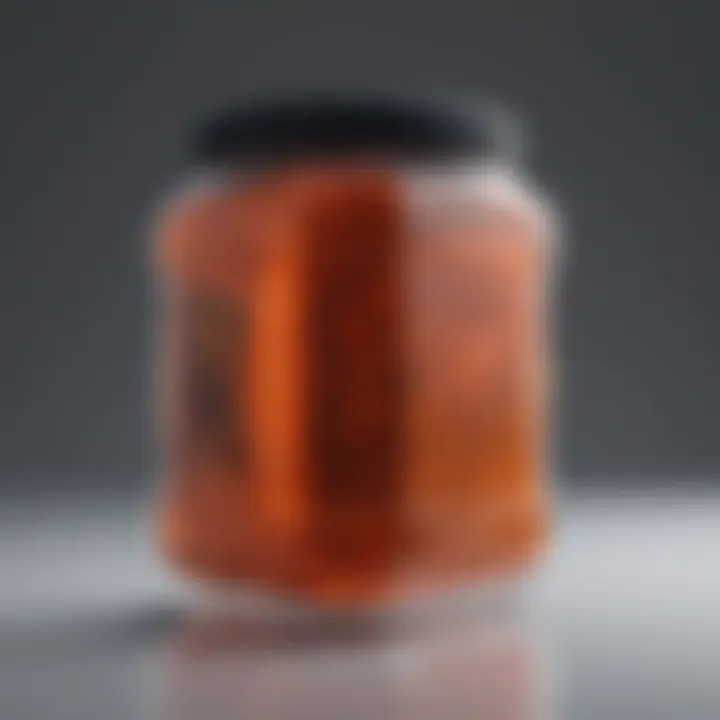
Intro
Rotomolded plastic has become an increasingly significant material in various industries. It refers to a particular manufacturing process that involves rotating a mold while heating it, leading to the distribution of plastic evenly within the mold. This leads to robust and lightweight products suitable for diverse applications, from toys to industrial containers.
Understanding rotomolded plastic necessitates a closer examination of its intrinsic properties and production methods. Factors such as cost-effectiveness, durability, and flexibility stand out, making it an ideal choice for both manufacturers and consumers.
In the upcoming sections, we will delve into key concepts and terminology relevant to rotomolded plastic, explore its wide-ranging applications, analyze its advantages, and discuss innovations that are poised to shape its future in the market.
Prelims to Rotomolded Plastic
Rotomolded plastic represents a significant development in material science. Its relevance is pronounced in the manufacturing sector where versatility and functionality are paramount. This section will provide an overview of this innovative material, highlighting its key aspects and applications. It is crucial for readers to understand what rotomolding entails, as it lays the foundation for the subsequent discussions on its properties and uses.
Definition of Rotomolding
Rotomolding, or rotational molding, is a manufacturing process that involves shaping plastic into a desired form using heat and rotation. The process begins with a hollow mold that's filled with plastic powder. The mold is then heated while being rotated along two perpendicular axes. This rotation allows the material for to coat the inner surface of the mold uniformly. After sufficient heating, the mold is cooled, solidifying the plastic into the mold's shape. Rotomolding is especially noted for producing large, hollow items with a seamless finish. This process is suitable for various types of plastics, predominantly polyethylene due to its favorable properties.
Historical Development
The origins of rotomolding can be traced back to the mid-20th century. In the 1950s, manufacturers began to explore this technique as a way to create large plastic components efficiently. Unlike other manufacturing methods at the time, rotomolding allowed for a level of design flexibility that was previously unattainable. As the technology advanced, so too did the applications for rotomolded plastics. By the 1970s and 1980s, industries such as toys, automotive, and marine began to extensively utilize these materials due to their durability and cost-effectiveness.
Today, rotomolding continues to evolve, driven by innovations in materials and technology. Manufacturers are finding new ways to improve efficiency and expand the range of products made using this method. Besides, the demand for environmentally friendly practices is influencing the development of more sustainable rotomolding processes. As the industry advances, the historical context remains essential to appreciate the current state and future of rotomolded plastics.
The Rotomolding Process
The rotomolding process is a critical component in the production of rotomolded plastic products. Understanding every aspect of this process is essential for anyone interested in its applications and benefits. Rotomolding allows for the creation of complex shapes and large components with relatively low capital investment. Moreover, the process is known for its design flexibility and ability to produce hollow structures that are both durable and light.
Materials Used
Polyethylene
Polyethylene stands out as one of the most commonly used materials in rotomolding. Its popularity can be attributed to its excellent impact resistance and flexibility, making it suitable for various applications. This material is particularly beneficial because of its low density, which contributes to lightweight products without sacrificing sturdiness.
One unique feature of polyethylene is its resistance to moisture and a variety of chemicals. This trait makes it a versatile choice for items such as storage tanks and outdoor furniture. However, it is worth noting that polyethylene can be less rigid compared to some other materials, limiting its use in specific high-stress applications.
Polypropylene
Polypropylene is another crucial material in the rotomolding process. It offers a higher melting temperature than polyethylene, which allows it to withstand higher temperature environments. Polypropylene’s key characteristic is its superior fatigue resistance, making it a viable option for functional parts that experience repeated stress.
The unique feature of polypropylene is its ability to maintain integrity in challenging conditions. However, it may not provide the same level of impact resistance as polyethylene, which can be a deciding factor in material selection, depending on the product requirements.
Other Variants
In addition to polyethylene and polypropylene, several other material variants can be used in rotomolding. These include materials such as PVC and certain engineering-grade plastics that offer distinct benefits. The key characteristic of these materials lies in their enhanced properties, such as increased rigidity or specialized chemical resistance.
Considering other variants expands the possibilities for rotomolded products. However, these materials may introduce additional challenges in processing and cost, potentially offsetting their advantages in specific applications.
Manufacturing Steps
Heating
Heating is a fundamental step in the rotomolding process. The raw material is first heated in a mold until it reaches a pliable state. This stage is crucial as it ensures even melting and distribution of the material within the mold.
The primary advantage of heating is its ability to produce consistently high-quality products. However, overheating can lead to degradation of the material and affect the final product’s properties.
Cooling
Cooling follows the heating process and is essential for setting the material into its final shape. During this step, the mold and its contents are cooled, allowing the polyethylene or polypropylene to harden. The cooling must be controlled carefully to avoid warping or undesirable surface features.
A significant advantage of effective cooling techniques is that they can influence cycle times directly, enhancing the overall efficiency of the manufacturing process. Yet, improper cooling can result in inconsistent product quality.
Demolding
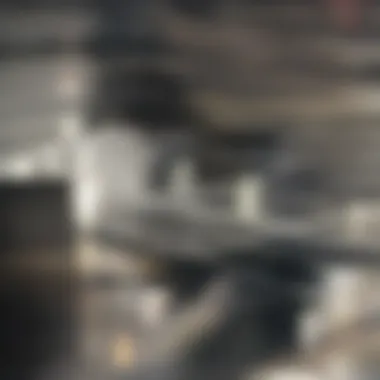
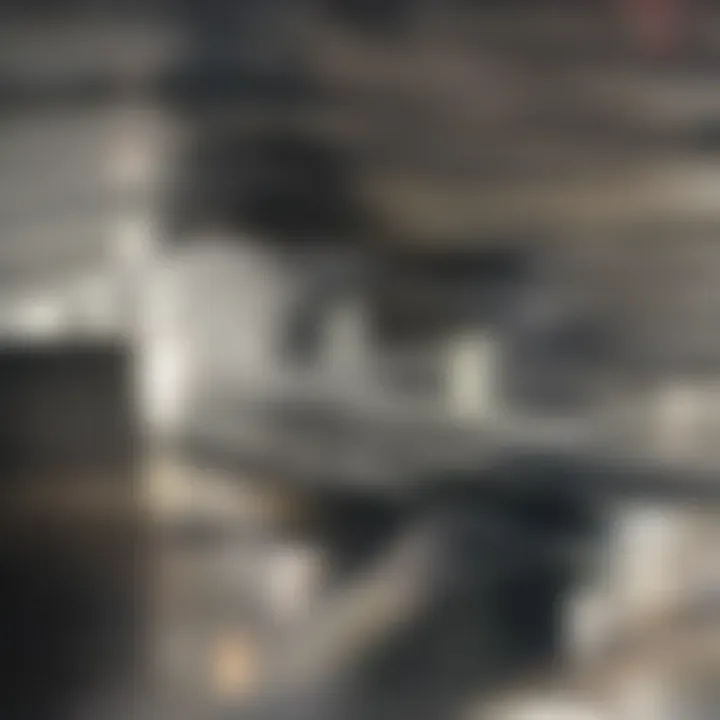
Demolding is the final step in the rotomolding process. It involves removing the hardened product from the mold. A successful demolding process is vital as it prevents damage to the product and the mold itself.
One key characteristic of a well-executed demolding process is its ability to maximize production efficiency. A smooth demolding minimizes labor costs and reduces wear on molds. A drawback, however, can be the complexity that arises from intricate mold designs, which may increase the risk of product damage during removal.
Material Properties of Rotomolded Plastic
Understanding the material properties of rotomolded plastic is essential, as these characteristics determine its effectiveness across various applications. This section delivers insights into the key properties such as mechanical strength, chemical resistance, and durability. The importance of these aspects cannot be overstated, particularly when considering the material's versatility and longevity. Manufacturers choose rotomolded plastic primarily due to these properties that support both robust design and functional performance.
Mechanical Strength
Mechanical strength refers to the ability of rotomolded plastic to withstand forces without breaking or deforming. This property is crucial for applications requiring components to endure physical loads or impacts, making it applicable in both industrial and consumer sectors.
Rotomolded plastics, often made from high-density polyethylene, exhibit impressive tensile and flexural strength. They are less prone to cracking under stress compared to other plastic variants due to their seamless construction, which allows for uniform distribution of stress. Some critical applications include storage tanks, automotive parts, and playground equipment, where strength is non-negotiable.
Chemical Resistance
Chemical resistance indicates how well a material can withstand exposure to various chemicals, including acids, bases, and solvents. The chemical structure of rotomolded plastic contributes to its high resistance to corrosion and degradation, making it a preferred choice in technical fields such as chemical processing, water treatment, and medical equipment manufacturing.
The impermeability of rotomolded plastics reduces the risk of chemical permeation, safeguarding the integrity of products and processes. This feature is a compelling factor in maintaining safety standards in environments where chemicals are prevalent, allowing for more versatile design and application.
Durability and Longevity
Durability reflects the lifespan of a material under normal usage conditions. Rotomolded plastics stand out for their exceptional durability, characterized by resistance to wear and tear. Their innate ability to endure environmental stressors, such as ultraviolet rays and temperature fluctuations, enhances their longevity compared to many other materials.
Components made from rotomolded plastic can last for years, even decades, with minimal degradation. This aspect not only supports sustainability through reduced waste but also diminishes the need for frequent replacements. Sectors like transportation, agriculture, and consumer goods benefit greatly from this quality, providing a viable solution for long-term applications.
"The lasting nature of rotomolded plastics not only benefits manufacturers but also supports consumers looking for reliable and enduring products."
In summary, the material properties of rotomolded plastic play a pivotal role in its broad adoption across industries. The mechanical strength, chemical resistance, and durability together construct a robust profile that businesses rely on for innovative solutions.
Applications of Rotomolded Plastic
Understanding the applications of rotomolded plastic is crucial for grasping its significance in various sectors. This plastic serves different needs across industries, driving innovation while maintaining cost-effectiveness. Its versatility has led to widespread usage in products ranging from toys to industrial equipment.
Industrial Applications
Rotomolded plastic finds extensive use in industrial applications due to its robust properties and resiliency. Key industrial components include storage tanks, custom parts, and machinery casings. These applications benefit from the material's ability to resist chemicals and prolonged impact, ensuring longevity even under rigorous operational stresses. The production process allows for customized designs that cater to specific functions, which is often a necessity in industrial settings.
Consumer Products
Consumer products made of rotomolded plastic exemplify how this material meets everyday needs.
Toys
Toys constructed from rotomolded plastic are exceptionally durable and safe. One notable aspect is their resistance to moisture and ease of cleaning, making them attractive options for parents. Many toys offer vibrant colors and engaging designs, appealing to children and fostering creativity. Their moldability allows for intricate shapes that traditional materials might not achieve.
Furniture
Rotomolded plastic furniture is gaining popularity particularly due to its lightweight nature and resistance to weather elements. This makes it suitable for both indoor and outdoor use. The ease of maintenance plays a significant role in its acceptance. Unlike wood or metal, rotomolded pieces do not splinter or rust, which prolongs their usability. However, their aesthetic appeal may often be perceived as less sophisticated compared to other materials.
Containers
Containers made from rotomolded plastic serve a critical function in storage and transport. Their key characteristic is strength, which allows for safe handling of various materials. They can be designed to fit specific needs, such as stackability or portability. An advantage of rotomolded containers is their seamless construction, preventing leaks and enhancing durability. But, on the downside, they can be heavier compared to other container options.
Transportation and Automotive Industry
Rotomolded plastics are foundational in the transportation and automotive sectors, contributing towards innovation and efficiency.
Fuel tanks
Fuel tanks made from rotomolded plastic have become commonplace due to their lightweight and corrosion-resistant properties. These tanks are often custom-shaped to fit specific vehicle designs, optimizing space and functionality. This material reduces overall vehicle weight, which, in turn, can enhance fuel efficiency. However, strict regulations regarding safety and performance can limit the scope of materials used in production.
Component housings
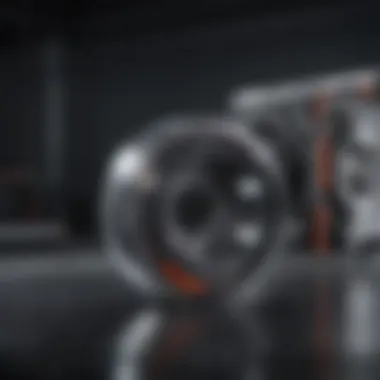
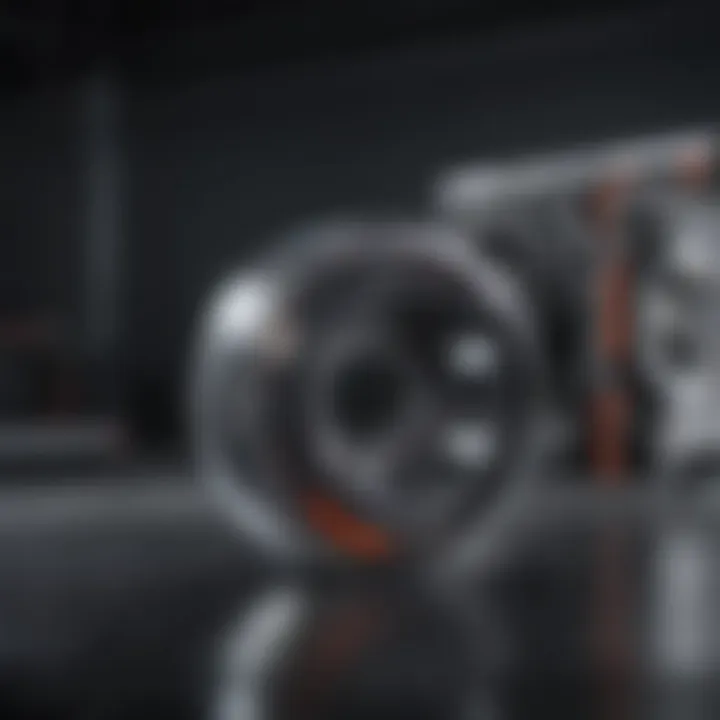
In the transportation sector, rotomolded plastic is also utilized for component housings. They provide adequate protection for sensitive parts from harsh environment conditions. Their resistance to impacts and chemicals is a key benefit. Additionally, the flexibility in design allows for precise fitting into complex structures. However, concerns about their long-term durability in specific applications may pose challenges for manufacturers, necessitating continuous advancements in material science and technology.
Advantages of Rotomolded Plastic
The advantages of rotomolded plastic are numerous and play a significant role in various industries. This section explores the essential benefits offered by this manufacturing process, focusing on cost efficiency, design flexibility, and reduced waste. Understanding these advantages helps stakeholders appreciate why rotomolding is favored for producing plastic products.
Cost Efficiency
Cost efficiency is a primary reason companies choose rotomolding. This method often requires lower initial investments compared to other plastic manufacturing techniques such as injection molding. The machinery used in rotomolding is generally less complicated and cheaper. Additionally, the production cycle time can lead to significant savings. Since rotomolding can produce large hollow parts in one cycle, it reduces the need for assembly, which translates to lower labor costs.
Moreover, materials used in rotomolding, particularly high-density polyethylene, can be more affordable. Even though the plastic itself is cheaper, it is the ability to produce complex shapes without the need for secondary operations that truly boosts cost efficiency.
Design Flexibility
Design flexibility is another strong benefit of rotomolded plastic. Manufacturers can create intricate designs and shapes that may be challenging or impossible with other techniques. The process allows for uniform wall thickness, which enhances structural integrity without adding unnecessary weight.
This flexibility extends to colors and textures as well. Various pigments can be added during the mixing stage, resulting in vibrant colors. Textured finishes can also be achieved, which can enhance the visual appeal of the finished product.
In application, rotomolding allows for various sizes of products, from small components to large tanks, without the need for complex molds. This versatility makes rotomolding an attractive option for a wide range of industries, including automotive, furniture, and toys.
Reduced Waste
Another critical advantage of rotomolded plastics is the reduced waste in the production process. Unlike techniques that require pouring excess material, rotomolding is a closed-loop system, which minimizes the amount of unused material. This efficiency results in less scrap during production.
Additionally, rotomolding can utilize recycled materials, contributing to sustainability initiatives within manufacturing. This is an essential consideration for many companies today. Businesses can reduce their environmental footprint while still producing high-quality products.
The reduced waste and environmentally friendly practices in rotomolding make it a sustainable choice for modern manufacturing.
In summary, the advantages of rotomolded plastic, including cost efficiency, design flexibility, and reduced waste, make it a compelling option for businesses. Choosing rotomolding can significantly influence a company's operational efficiency and environmental impact.
Limitations and Challenges
Understanding the limitations and challenges of rotomolded plastic is crucial for professionals in many fields. While this manufacturing technique offers various advantages, recognizing its limitations can help manufacturers make informed decisions during product development. This section explores significant challenges associated with rotomolding, namely production speed, surface finish quality, and material limitations.
Production Speed
Production speed is a major consideration in rotomolding. The process itself is relatively slower compared to other manufacturing methods such as injection molding. The reason is that rotomolding requires time-consuming heating and cooling cycles. Typically, each cycle can take anywhere from 30 minutes to several hours depending on the size of the part. This extended production time can lead to higher labor costs and limits the scalability of operations.
Manufacturers aiming for rapid production might find rotomolding less viable, especially when a larger number of components are needed quickly. This limitation can impact the overall competitiveness of businesses that rely on fast-turnaround products. Companies are typically required to find a balance between the number of parts produced and the time taken for each cycle.
Surface Finish Quality
Another challenge is achieving the desired surface finish quality. Rotomolded plastic often exhibits noticeable seams and joints because of the nature of the manufacturing process. These imperfections can be a point of concern, especially for products that need to meet high aesthetic standards. While additional processes like sanding or painting can improve surface finish, they also add time and cost to production.
Moreover, maintaining uniformity across large production runs can be difficult. Inconsistent finishes can affect customer satisfaction and product performance. This inconsistency often steers manufacturers to consider alternative methods, which may not offer the same cost benefits as rotomolding.
Material Limitations
Rotomolded plastics also come with inherent material limitations. The types of materials used in rotomolding, such as polyethylene and polypropylene, may not suit every application. These materials often lack the mechanical properties of others, like engineering plastics. Their lower resistance to heat and chemicals can restrict their usage in certain applications, such as those in demanding environmental conditions.
In addition, variability in material properties can lead to differences in performance. Different grades of polyethylene, for example, can have different impacts on durability and flexibility. It's important for manufacturers to thoroughly evaluate their material choices within the context of their specific applications. Relying solely on rotomolding without understanding these limitations may lead to failures in very critical applications.
In summary, while rotomolding presents unique advantages in design flexibility and cost efficiency, it is not free from limitations. Acknowledging these challenges allows both manufacturers and consumers to make informed decisions that enhance the efficacy and reliability of rotomolded products.
Recent Innovations in Rotomolding
In the evolving landscape of manufacturing, recent innovations in rotomolding stand out as pivotal advancements that enhance the capabilities of this process. The significance of these innovations lies not only in improving efficiency but also in expanding the potential applications of rotomolded plastics. As industries grapple with sustainability and performance demands, the ability to integrate new technologies and materials becomes essential.
Advanced Materials
The introduction of advanced materials in rotomolding has revolutionized the manufacturing process. Materials such as high-density polyethylene (HDPE) are now being combined with additives that enhance strength and chemical resistance. These materials permit the production of complex shapes while retaining durability. Innovations also include biobased plastics, which contribute to reducing carbon footprints. These materials not only satisfy environmental regulations but also appeal to eco-conscious consumers.
The use of innovative composites, such as fiberglass-reinforced plastics, enhances the structural properties of the final product. Additionally, advanced formulations allow for faster production cycles, which is crucial in meeting high market demands.
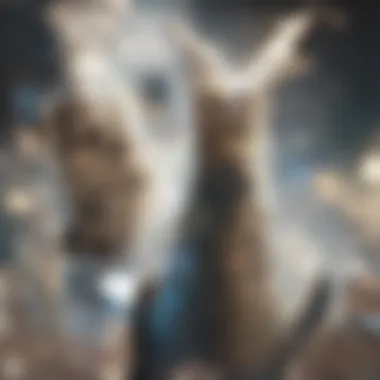
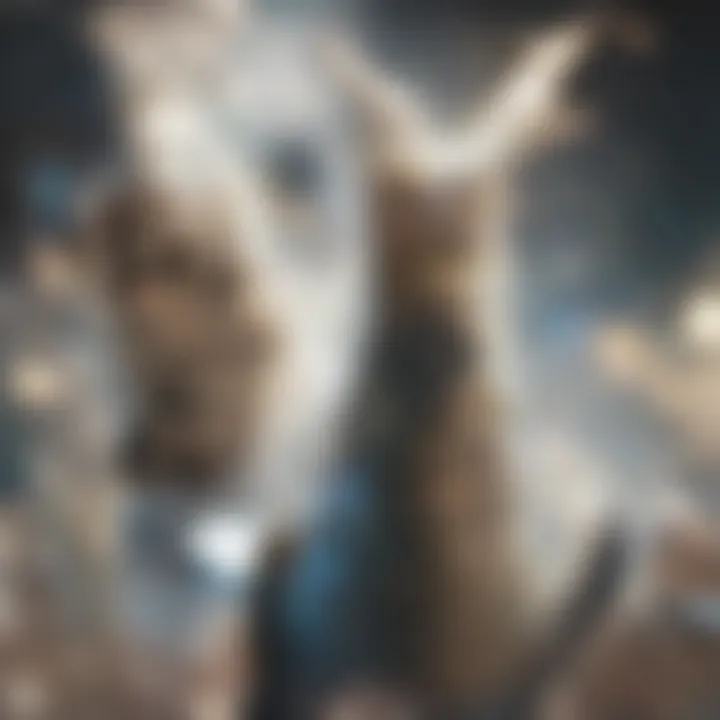
"Advanced materials in rotomolding signify a shift towards sustainability, pushing manufacturers to innovate for a greener future."
Smart Technologies in Rotomolding
Smart technologies also play a critical role in modernizing the rotomolding process. The integration of automation and data analytics leads to higher efficiency and lower production costs. Smart sensors embedded in machinery provide real-time data, enabling manufacturers to monitor the rotomolding process closely. This capability reduces errors and waste during production, allowing for a more streamlined workflow.
Moreover, software applications can optimize design parameters, allowing for intricate mold designs that were not previously possible. The connection of these automated systems with cloud technology enables remote monitoring and control. Thus, manufacturers can ensure quality and precision without being physically present on the production floor.
As smart technologies continue to advance, the potential for innovations in rotomolding will only grow. These systems not only enhance product quality but also foster a culture of ongoing improvement and adaptability within manufacturing settings.
In summary, the recent innovations in rotomolding are reshaping the industry by introducing advanced materials and smart technologies. These developments enhance the efficiency and sustainability of the manufacturing process while expanding the scope of applications for rotomolded plastics.
Environmental Considerations
Environmental sustainability is becoming an essential aspect of modern manufacturing practices, and rotomolded plastics are no exception. The production and use of rotomolded plastic not only cater to diverse industries but also come with environmental implications that need to be addressed. The significance of evaluating environmental considerations lies in their impact on sustainability and resource optimization. This section explores the recyclability of rotomolded plastics and the sustainable practices in manufacturing that can reduce the ecological footprint of this production technique.
Recyclability of Rotomolded Plastics
Recyclability is a crucial factor when discussing environmental considerations of rotomolded plastics. Unlike some other plastic forms, rotomolded products can be made from recyclable materials, mainly polyethylene. This increases the potential for closed-loop recycling, whereby post-consumer products can be reprocessed into new raw materials.
- The recyclable nature of these plastics is significant. The process can reduce waste in landfills and conserve natural resources by producing new products from recycled materials.
- However, it is important to note that the recyclability rates vary based on the product and its condition. Contaminated or complex plastics can pose challenges during the recycling process.
- Efforts are being made to develop better recycling technologies to improve the efficiency of rotating molds recycling and ensure more of these plastics can be reused.
In summary, the recyclability of rotomolded plastics represents a critical opportunity for enhancing ecological sustainability.
Sustainable Practices in Manufacturing
In addition to recyclability, sustainable practices during the manufacturing of rotomolded products are necessary to mitigate environmental impact. By adopting eco-friendly methods, manufacturers can significantly reduce waste and energy consumption.
Some key sustainable practices include:
- Energy Efficiency: Utilizing advanced energy-efficient machinery can minimize electricity usage during production.
- Material Sourcing: Choosing sustainable raw materials that are recycled or bio-based can lower the carbon footprint associated with extraction and transportation.
- Waste Management: Implementing systems to recycle scrap materials generated during production helps in reducing overall waste.
- Water Conservation: Effective management of water resources helps to minimize water usage and pollution in manufacturing processes.
Sustainable practices not only benefit the environment but can also lead to cost savings for manufacturers in the long run.
As the industry shifts towards greener solutions, it is essential to consider both the recyclability of rotomolded plastics and sustainable manufacturing practices. This dual approach holds the key to making rotomolded plastic a more responsible choice in contemporary product design and manufacturing.
Future Trends in Rotomolding
The future of rotomolding is a fascinating domain that warrants attention. With a multitude of factors driving innovation, the industry is poised for growth and transformation. Key elements such as market demand, technological advancements, and sustainability considerations are critical to understanding future trends. These trends not only shape the manufacturing landscape but also influence how rotomolded plastics are perceived in various applications.
Market Growth Projections
The market for rotomolded plastics has shown significant promise, with projections indicating continued expansion. According to various industry reports, the market is expected to grow at a compound annual growth rate (CAGR) of around 6% over the next few years. This growth is largely fueled by increasing demand from sectors such as consumer products, automotive, and industrial applications.
The geographic distribution of demand also plays a role in this growth. Regions such as North America and Asia-Pacific are leading in production and consumption of rotomolded products. Companies are now placing more emphasis on regional supply chains to mitigate risks and understand local market requirements better. This adaptability to market dynamics is vital for businesses seeking to capitalize on the upward trend in rotomolding.
"As industries innovate, rotomolded plastics stand at the forefront, providing solutions that meet evolving consumer demands."
Emerging Applications
Emerging applications for rotomolded plastics are cropping up across different fields. Some of the notable areas where rotomolding is making strides include:
- Medical Equipment: The healthcare sector is exploring rotomolded plastics for components that require precision and durability, such as medical carts and storage solutions for pharmaceuticals.
- Sports and Recreation: Equipment such as kayak and canoes benefits from the customizability and durability that rotomolding offers, allowing for high-performance products tailored to avid sports enthusiasts.
- Agriculture: Storage tanks and agricultural equipment make use of rotomolded designs that are lightweight yet robust, fitting the unique needs of the agriculture sector.
- Construction: Rotomolded plastics are finding their way into construction materials, providing utility in tools, storage solutions, and protective gear that withstand harsh conditions.
The versatility of rotomolded plastics means that innovation continues to drive new opportunities, allowing industries to utilize these materials in innovative ways.
The End and Summary
In this article, we have delved into the multifaceted world of rotomolded plastics. The analysis reveals that this material is not just a simple option for manufacturers but a critical player in modern manufacturing landscapes. The viability of rotomolded plastic across various industries highlights its adaptability and efficiency. As discussed, the rotomolding process ensures that the products exhibit a unique combination of strength, durability, and design flexibility.
Environmental considerations are also significant. The potential for recycling and the implementation of sustainable practices are becoming vital for ensuring long-term industry viability. Rotomolded plastics play a noteworthy role here. The innovations within this field further amplify its importance, allowing for advancements in material composition and application that align more closely with global sustainability goals. Overall, our exploration of rotomolded plastics showcases its relevance in achieving cost-effective, sustainable manufacturing while fostering creativity in design.
Key Takeaways
- Rotomolded plastics provide excellent mechanical strength and chemical resistance.
- Their manufacturing process results in cost efficiency, making them attractive for various applications.
- Environmental sustainability is becoming increasingly prioritized, with recycling initiatives gaining ground.
- Advanced technologies are reshaping how rotomolded products are designed and made.
Final Thoughts on the Role of Rotomolded Plastics
Rotomolded plastics have established themselves as integral to various industries, from consumer products to transportation components. Their advantages, such as cost-effectiveness and design flexibility, present diverse opportunities for innovation. As the demand for sustainable practices increases, their adaptability to new materials and technologies will likely enhance their significance further. Thus, rotomolded plastics are positioned to play a crucial role in the future of manufacturing and environmental stewardship.