Exploring SDR Roughness: Definitions and Applications
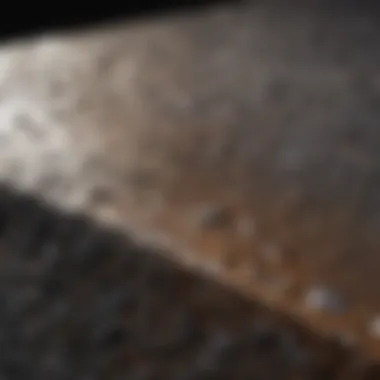
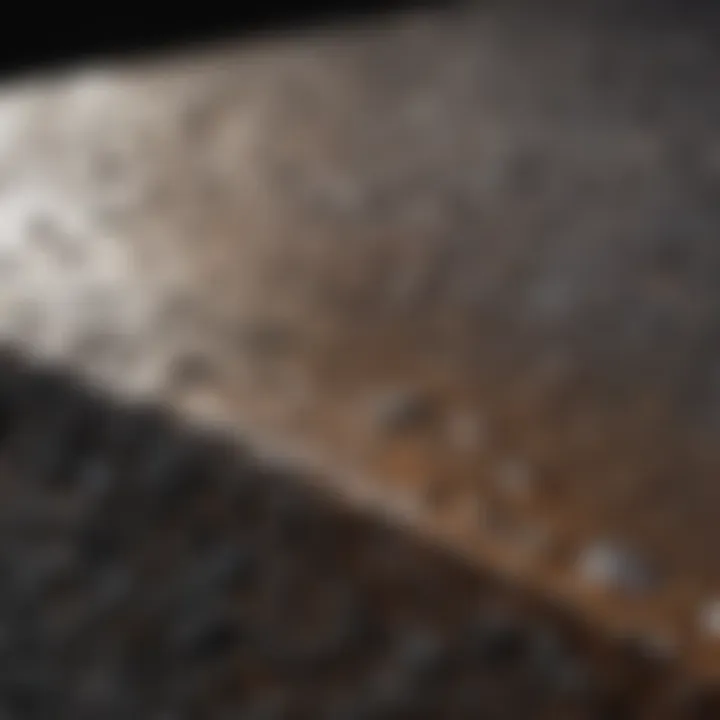
Intro
Surface roughness plays an essential role in various scientific and engineering disciplines, influencing material properties, manufacturing processes, and the performance of finished products. In the realm of Spatial Domain Reflectometry (SDR), understanding this concept is not just advantageous but crucial. By leveraging SDR techniques, researchers can accurately assess surface features that might otherwise remain obscured.
In this exploration, we aim to unpack the complexities of SDR roughness. We'll delve into its definition, measurement techniques, and the critical implications it holds for both material behavior and practical applications. This narrative is tailored for students and professionals seeking to deepen their comprehension of how surface roughness impacts their fields.
Key Concepts and Terminology
In this section, we clarify some fundamental aspects that underpin our discussions about SDR roughness. Understanding the language of this field is imperative for grasping the larger picture.
Definition of Key Terms
- Surface Roughness: A quantitative measure of the texture of a surface, often described by the vertical deviations of a real surface from its ideal shape. Roughness can significantly affect phenomena such as adhesion, wear, and fluid flow.
- Spatial Domain Reflectometry (SDR): A technique used to assess the characteristics of a material’s surface by reflecting light waves off it, allowing for the analysis of surface roughness at different scales.
- Topography: Refers to the arrangement of the natural and artificial physical features of an area. When discussing surface roughness, we are typically interested in the microscopic or nanoscopic topographical characteristics that influence material interactions.
Concepts Explored in the Article
This article tackles various dimensions of SDR roughness, covering:
- The importance of accurate surface measurement in material science.
- Different methodologies for evaluating roughness and the technologies involved in SDR.
- The relationship between surface roughness and material properties like mechanical strength and adhesion.
- Future directions for research, including innovative technologies and methods that will further the understanding of surface characteristics.
Findings and Discussion
Main Findings
Through careful analysis, several significant findings emerge:
- Roughness and Performance: The roughness of a surface can dramatically influence its performance in applications such as microelectronics, biomedical devices, and mechanical engineering. For example, in medical implants, smoother surfaces often promote better biocompatibility, whereas rough surfaces might enhance cell attachment, depending on the application.
- Measurement Techniques: Technologies like atomic force microscopy (AFM) and optical profilers are pivotal in accurately measuring surface roughness. Each method offers distinct advantages and limitations, making the choice of technique fairly critical.
- Material Properties: It’s evident that variations in surface roughness can lead to observable changes in a material’s strength, fatigue behavior, and resistance to wear and corrosion.
Potential Areas for Future Research
As we look ahead, several areas warrant exploration:
- Nanostructured Materials: Investigating how advancements in nanotechnology affect surface roughness and, consequently, material properties.
- Integration with Machine Learning: Using data analytics and machine learning to predict how surface roughness affects material performance across a range of industries.
- Sustainable Practices: Researching how surface treatments and modifications can be adapted in a sustainable way to enhance roughness without compromising environmental standards.
Understanding surface roughness in SDR is akin to grasping the language of materials; it opens many doors in design and functionality.
This article aims to bridge the gap between theoretical knowledge and practical applications, emphasizing how an accurate understanding of SDR roughness is paramount for advancing technology and material science.
Prelims to SDR Roughness
In the realm of material science and engineering, the concept of surface roughness embedded within Spatial Domain Reflectometry (SDR) serves as a cornerstone for ensuring optimal functionality and performance in various applications. Surface roughness is not merely an academic term; it's a practical consideration that defines how materials interact with their environment. A comprehensive grasp of SDR roughness can open doors to innovation in manufacturing processes, coating technologies, and the development of new materials.
Defining SDR and Surface Roughness
To fully appreciate the nuances of SDR roughness, it’s essential to lay a solid foundation. SDR, or Spatial Domain Reflectometry, is a technique used for analyzing the characteristics of surfaces by measuring the reflections of light. Essentially, it allows us to visualize and quantify surface features, which is crucial since the roughness of a surface often dictates its properties. In tandem, surface roughness refers to the small, irregular deviations from an ideally flat surface, characterized by peaks and valleys. These deviations can significantly affect a material’s strength, wear, and even its aesthetic appeal.
In practical terms, think of a basketball court’s playing surface. A smooth finish allows for quicker dribbling and consistent play, whilst a rough surface could change the dynamics of a game by affecting ball bounce and player traction. Similarly, the definition of SDR roughness comes into play across industries such as aerospace, automotive, and electronics, where precision is of the utmost importance.
The Importance of Surface Characterization
Understanding surface roughness and proper characterization is akin to having the right recipe for a complicated dish. If the ingredients—light, pressure, and material—are without proper measurements and comprehension, the final outcome can be less than satisfactory.
Surface characterization provides critical insights into how materials behave under stress and how they respond to environmental factors. For instance, in manufacturing, a smooth surface might be ideal for reducing friction during operation. Conversely, a textured surface can enhance adhesion or provide necessary grip. Here are a few points illustrating the role of surface roughness characterization:
- Affecting Friction: Surfaces that are too smooth may slip, while excessively rough surfaces can lead to increased wear.
- Modulating Light Interaction: Surface roughness influences how light interacts with materials, affecting applications in optics and packaging.
- Corrosion Resistance: Rough surfaces can trap moisture and contaminants, leading to quicker degradation.
The significance of surface characterization extends deeper than mere aesthetics; it influences mechanical performance and lifecycle longevity.
Through this introduction to SDR roughness, readers are encouraged to appreciate its relevance, not only as a theoretical concept, but as a practical element with real-world implications. Understanding these foundations sets the stage for further exploration into measurement techniques, physics, and industry applications that underscore the importance of surface roughness in contemporary materials science.
Measurement Techniques for SDR Roughness
Understanding the measurement techniques for Surface Roughness in the realm of Spatial Domain Reflectometry (SDR) is pivotal. These measurements not only help in characterizing surfaces but also directly influence performance in various applications. The choice of technique can determine how accurately we can assess roughness, impacting material selection, processing methods, and even the efficacy of coatings applied. With a myriad of options ranging from traditional contact methods to advanced optical techniques, each has its merits and trade-offs that are worth exploring.
Contact vs. Non-contact Methods
When we discuss measuring surface roughness, we can't ignore the big debate: contact versus non-contact methods.
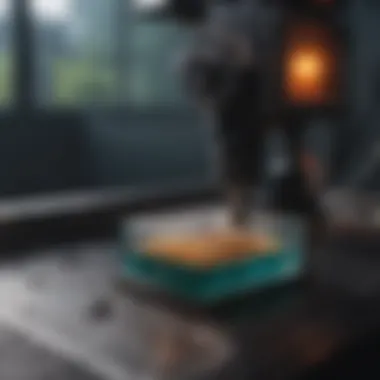
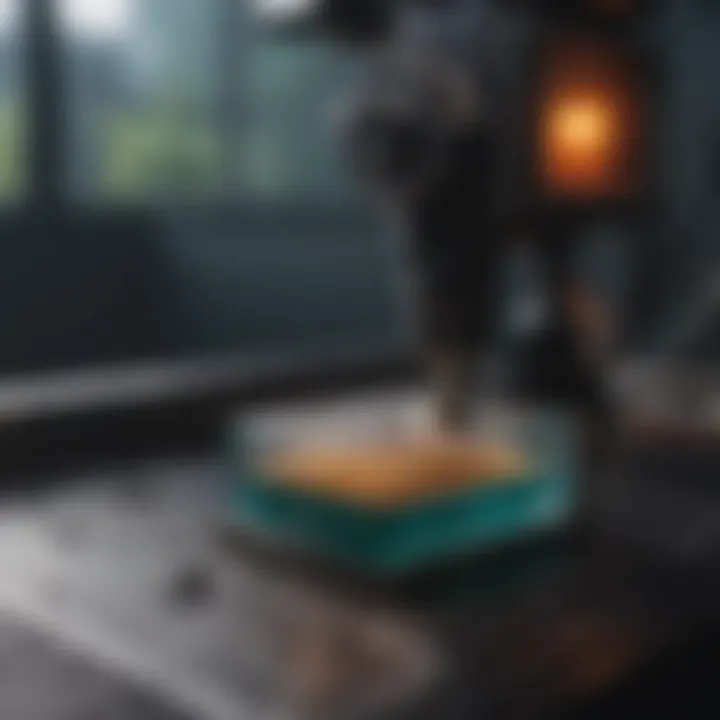
Contact methods typically involve using a stylus or probe that physically touches the surface. This technique, although precise, has downsides, such as potential alterations to the surface due to wear or damage. For instance, using a stylus might be like trying to glean insights about a painting by running your fingers across it, which can indeed scratch the surface.
On the flip side, non-contact methods leverage light, lasers, or other technologies to gather information without physically interacting with the surface. A classic example here would be using laser scanning to map roughness. This method minimizes the risk of damaging the material and is generally well-suited for soft or delicate surfaces. However, it often comes with challenges in terms of precision when dealing with highly reflective or transparent materials.
"The choice of measurement method can significantly skew results, impacting research outcomes and industrial applications."
In summary, while contact methods might offer great accuracy under certain conditions, non-contact alternatives are indispensable in scenarios where surface integrity matters. The insights gleaned from each technique can guide decisions around manufacturing and material utilization.
Advanced Optical Techniques
Delving deeper, advanced optical techniques represent a significant leap in the quest for accurate surface measurement. Techniques such as confocal microscopy and white light interferometry come into play here. Each approach uses light in innovative ways, allowing for exceedingly detailed examinations at the microscopic level.
Confocal microscopy works by focusing light onto the sample and capturing images from various depths. This capability allows for creating three-dimensional representations of the surface, providing a wealth of data on roughness profiles and features. It's like peeling back the layers of an onion—seeing beneath the surface offers unique insights.
White light interferometry, on the other hand, exploits the principle of interference to produce highly accurate measurements of surface profiles. By examining the interference patterns produced when light reflects off the rough surface, researchers can calculate the degree of roughness with impressive precision. These techniques, however, can be limited by their sensitivity to environmental factors. For instance, vibrations or temperature fluctuations can affect results. Thus, careful consideration of the laboratory setup is critical when opting for these methods.
Interferometry in Surface Measurement
Interferometry has carved a niche for itself in precision surface measurements due to its inherent capability for high-resolution data gathering. This technique involves splitting a beam of light, allowing one portion to reflect off a reference surface while the other interacts with the test surface. When these beams recombine, they create an interference pattern that researchers analyze.
This method fills in the gaps left by traditional measurements, often exhibiting advantages in speed and accuracy. Not only can it analyze a broad surface area quickly, but it also identifies minute changes in surface texture that other methods might overlook. Such detail is indispensable for industries where even the slightest variations can lead to significant performance discrepancies—think of aerospace components where precision is a matter of safety and reliability.
However, like any technique, it has limitations, such as requiring stable environmental conditions and the necessity for a smooth reference surface. The trade-off between results and setup complexity keeps researchers and engineers on their toes, navigating the landscape of measurement techniques with care and precision.
The Physics of Surface Roughness
Understanding the physics behind surface roughness is crucial for several reasons. For one, the roughness characteristics of a surface relate directly to its physical properties and performance in various applications. Surface irregularities can influence how materials interact with each other, often dictating their behavior under different environmental conditions.
This section will delve into the underlying principles of surface roughness, emphasizing not only its theoretical aspects but also its practical implications in engineering and material science. Examining these aspects can provide suggestions for optimizing designs, enhancing efficiencies, and reducing costs related to surface preparation and treatment.
Underlying Principles of Roughness
Surface roughness arises from the microscopic and macroscopic features that characterize a material's surface. It results from a combination of factors such as the manufacturing process, material properties, and external conditions. These roughness features can include scratches, pits, and other irregularities that are usually measured in terms of average roughness (Ra), root mean square roughness (Rq), or peak-to-valley height (Rz).
Key Factors that Affect Surface Roughness:
- Manufacturing Process: Different techniques like milling, grinding, or casting create distinct roughness profiles. For instance, a ground surface might exhibit different characteristics compared to a surface produced by 3D printing.
- Material Properties: The intrinsic characteristics of a material, such as its hardness and ductility, can influence the roughness. Softer materials might become more irregular during processing due to deformation.
- Environmental Impact: Exposure to elements like moisture and temperature can alter surface features over time, affecting roughness measurements.
Thus, it is essential to understand these principles when developing products or investigating material performance. This knowledge not only aids in selecting the right manufacturing process but also informs the design of components, ensuring they meet specific performance and durability requirements.
Impact on Light Scattering
Surface roughness does not just play a role in how materials adhere or wear; it also significantly affects light interactions with surfaces. When light encounters a rough surface, it scatters in various directions, which can alter optical properties such as reflectivity and absorption. This scattering effect is particularly critical in applications involving optics, coatings, or even electronics.
Factors influencing light scattering due to roughness include:
- Wavelength of Light: When the surface features are comparable to the light's wavelength, scattering can become significant, leading to various optical phenomena.
- Surface Texture: Different textures can direct light scattering in distinct patterns, which might be desirable or detrimental depending on the application. For example, a matte finish has different scattering properties than a polished one.
- Incident Angle: The angle at which light strikes the surface also determines how the irregularities will influence scattering.
"Understanding these physical dynamics is not just academic; it holds real-world implications across industries ranging from optics to aerospace."
Incorporating a deeper grasp of these principles can to great effect inform design choices, allowing for the optimization of surface properties to meet the specific needs of various applications. Awareness of how surface roughness affects light can also guide the development of better materials for coatings, improving not just aesthetic appeal but functional performance.
Applications of SDR Roughness in Industry
Understanding how surface roughness specifically within the realm of Spatial Domain Reflectometry (SDR) plays a role in various industries is paramount. Surface roughness has broad implications across material science, manufacturing processes, and coating technologies. Each of these elements provides critical insight into how and why roughness matters in practical applications.
Role in Material Science
Material science stands as a cornerstone of innovation and development across various industries. Surface roughness significantly influences the characteristics of materials, affecting not only their physical appearance but their functionality as well. Research has shown that the roughness at the micro and nano levels can lead to variations in properties such as friction, adhesion, and fatigue resistance.
When engineers formulate new materials, the surface finish cannot be an afterthought. Take for example the development of composite materials used in aerospace. These materials often require a specific roughness to enhance bonding between layers, while at the same time, keeping weight in check. The nuances in surface texture can consequently alter performance metrics—lightweight, high-strength materials depend on it.
In addition, measuring the roughness through tools like SDR can help scientists predict how materials will behave under different conditions. By better understanding these interactions, new materials can be tailored for specific applications, leading to advancements that range from longer-lasting components to innovative product design.
Effect on Manufacturing Processes
Manufacturing processes are fundamentally entwined with surface roughness considerations. It affects not just the aesthetics but also the operational performance of products. In sectors like automotive or electronics, the precision in surface finish directly correlates with product reliability and lifespan.
For instance, in machining processes, surface roughness must be controlled meticulously. A rough surface can lead to poor fitting of components, increased wear, and ultimately, failure of products in real-world scenarios. When roughness is well defined, it can enhance lubrication in bearing applications, leading to decreased friction and extended component life.
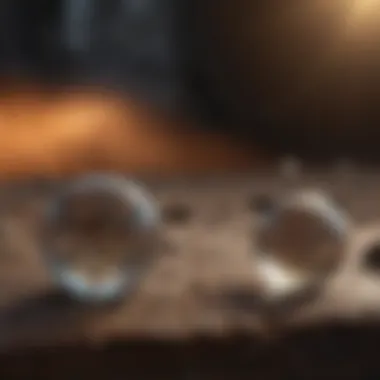
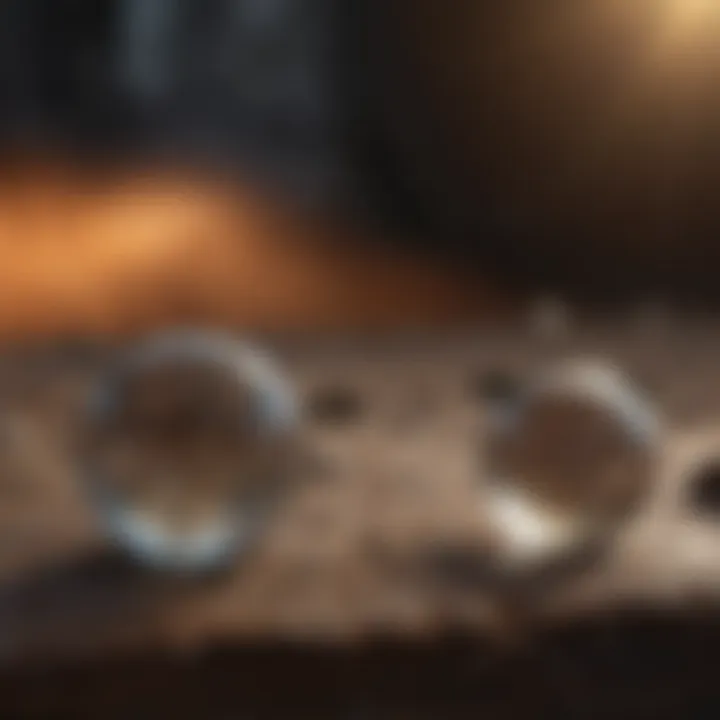
Moreover, embracing measurement techniques like SDR allows manufacturers to not just measure but analyze trends in surface roughness over time. This capability aids in preventive maintenance, reducing downtime caused by inappropriate surface finishes.
Influence on Coating Technologies
The role of coating technologies in relation to SDR roughness is profound. Coatings are often applied to enhance properties such as corrosion resistance, wear resistance, or aesthetic qualities. Yet, their performance can be drastically affected by the surface roughness of the substrate.
A smooth surface usually allows for a more uniform application of coatings, resulting in better adhesion and longevity. Conversely, overly rough surfaces can lead to poor adhesion, causing coatings to flake or wear away prematurely. This becomes especially critical in industries that rely on coatings for functional purposes—think of tools that endure rugged conditions or heavy-duty machinery.
Understanding the roughness can inform decisions about not just the choice of coating but also the application techniques employed. For example, in aerospace applications where weight savings are critical, coatings can be applied differently depending on the intended roughness characteristics of the underlying materials.
"Surface roughness must never be an oversight when it comes to the performance and longevity of any coated product."
Quantifying Roughness: Standards and Metrics
Understanding the quantification of surface roughness is crucial for anyone involved with SDR technology. This section dives into key parameters and normatives that ensure accurate measurements. Knowing how to quantify roughness not only paves the way for better product design but also enhances the reliability of results across various applications. By adhering to established standards, professionals can minimize errors, facilitating more robust quality control measures in manufacturing processes.
Common Parameters Used in Measurement
When it comes to measuring surface roughness, multiple parameters are commonly employed. These parameters offer different perspectives on the same surface, each contributing to a detailed understanding of roughness characteristics. Some primary parameters include:
- Ra (Arithmetic Average Roughness): This is perhaps the most widespread parameter used to quantify roughness. It's the average of the absolute values of the roughness profile's deviations from the mean line, providing a quick snapshot of overall surface texture.
- Rz (Mean Roughness Depth): Rz is the average of the maximum peak-to-valley heights in each sampling length. This metric gives insight into the vertical aspects of surface irregularities, making it vital for wear and tear considerations.
- Rq (Root Mean Square Roughness): Rq offers a more comprehensive analysis by considering the square root of the average of the squares of the roughness profile’s deviations. This can sometimes highlight subtler variations missed by Ra.
- Rt (Total Roughness Height): This measures the total height difference between the highest peak and the lowest valley within the evaluation length. While it offers a broad perspective, it can sometimes be misleading if deep valleys or high peaks are isolated features.
These parameters help craft a well-rounded view of surface characteristics and, importantly, ensure that different methodologies aren't apples to oranges. Utilizing a combination leads to a more precise understanding and ranking of surface qualities.
ISO Standards Relating to Surface Roughness
The role of ISO standards in quantifying surface roughness cannot be overstated. These guidelines provide a systematic approach for consistent measurement and reporting, ensuring that different laboratories and manufacturers can align their results. Notable standards include:
- ISO 4287: This standard focuses on the definitions and parameters related to roughness, which are fundamental to achieving comparability in measurements across applications.
- ISO 1302: This standard sets forth a standardized way of indicating surface texture in technical drawings. This clear communication helps engineers and technicians grasp surface requirements without ambiguity.
- ISO 25178: This is an umbrella standard covering 3D surface texture parameters, offering insights into more complex surface profiles encountered in advanced applications.
These standards not only facilitate measurement but also support the cross-industry adoption of common terminology and procedures.
In essence, the quantification of roughness is more than just a checkbox on a quality control sheet; it fundamentally affects product performance, durability, and customer satisfaction.
Roughness and Material Properties
Surface roughness plays a pivotal role in defining the overall performance and functionality of materials in various applications. When we talk about roughness, we are referring to the texture of a surface, which can significantly affect its physical properties. From the way materials interact with each other, to how they withstand hypothetical wear and tear, understanding SDR roughness is essential for engineers and researchers alike in predicting behavior in real-world applications.
Relationship with Friction and Wear
The relationship between surface roughness and friction is quite intricate. In essence, rougher surfaces often result in increased friction because they create more contact points between two surfaces. When two materials rub against each other, the peaks of the rough surface can generate additional resistive forces, leading to potential changes in how the materials perform under load. Here are some key insights:
- Increased Surface Interaction: More peaks mean greater points of contact, leading to higher friction coefficients. In practical terms, this can lead to wear on both surfaces over time.
- Wear Mechanisms: Rougher surfaces can lead to different wear mechanisms. For example, adhesive wear can be more pronounced on rough surfaces, affecting the lifespan and efficiency of mechanical components.
- Real-World Applications: In automotive industries, where tire-road friction is crucial, maximizing or minimizing roughness can directly affect performance and safety. Understanding these relationships can aid in designing surfaces that either minimize friction in certain contexts (like bearings) or maximize it (like brake pads).
Effects on Mechanical Strength
Surface roughness does not just influence friction; it also has significant implications for the mechanical strength of materials. When assessing the integrity of components, engineers must consider how surface texture interacts with other material properties. This interaction can either enhance or compromise mechanical strength:
- Stress Concentration: Rough surfaces create zones of stress concentration, which can lead to premature failure if not carefully managed. Cracks can initiate and propagate more easily from surface defects.
- Fatigue Resistance: Materials with lower surface roughness typically exhibit better fatigue resistance. In conditions where cyclic loads are applied, smooth surfaces distribute stress more evenly, proving beneficial for components like turbine blades or airplane wings.
- Surface Treatments: Techniques such as grinding and polishing can reduce roughness, thereby enhancing strength properties. These surface treatments are vital in manufacturing processes where precision and longevity of parts are critical.
Key Insight: "The impact of surface roughness on mechanical properties is more than just academic; it has real-world consequences for product durability and efficiency."
To sum up, the understanding of roughness as it relates to material properties is not just an academic exercise. It's a fundamental aspect that can determine the success or failure of a designed product. Engineers and researchers need to consider these relationships carefully to innovate and improve materials across various applications.
Technological Advances in Roughness Analysis
In recent years, the landscape of roughness analysis has evolved significantly, influenced by emerging technologies. Understanding these advancements is paramount, as they hold the key to enhancing measurement accuracy, efficiency, and applicability across various fields, from material science to manufacturing processes.
Machine Learning Applications
Machine learning is reshaping how we approach data analysis in roughness measurement. By utilizing algorithms that can learn from and make predictions on data, researchers can now analyze surface roughness patterns far more effectively than traditional methods allow. Leveraging large datasets, machine learning models can identify relationships between surface features and their effects on material performance without requiring exhaustive manual processing.
For instance, a research team might apply a model to predict the wear resistance of a specific material based on its roughness profile. Such predictive capabilities expedite the design process in industries like aerospace or automotive, where material failure can be catastrophic. Additionally, machine learning can automate repetitive tasks in measurement, allowing engineers to focus on analysis and design rather than data collection and processing.
However, these advancements do come with considerations. Data quality is critical. If the training datasets are biased or not representative, the models can lead to misleading results. Hence, it’s essential for companies to maintain robust data generation practices to support their machine learning initiatives.
Real-time Measurement Systems
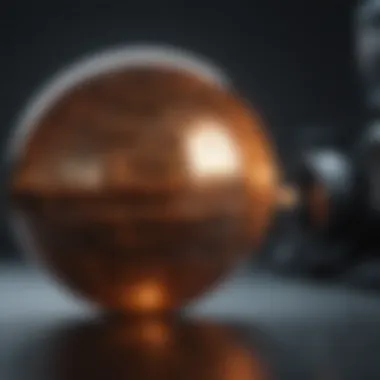
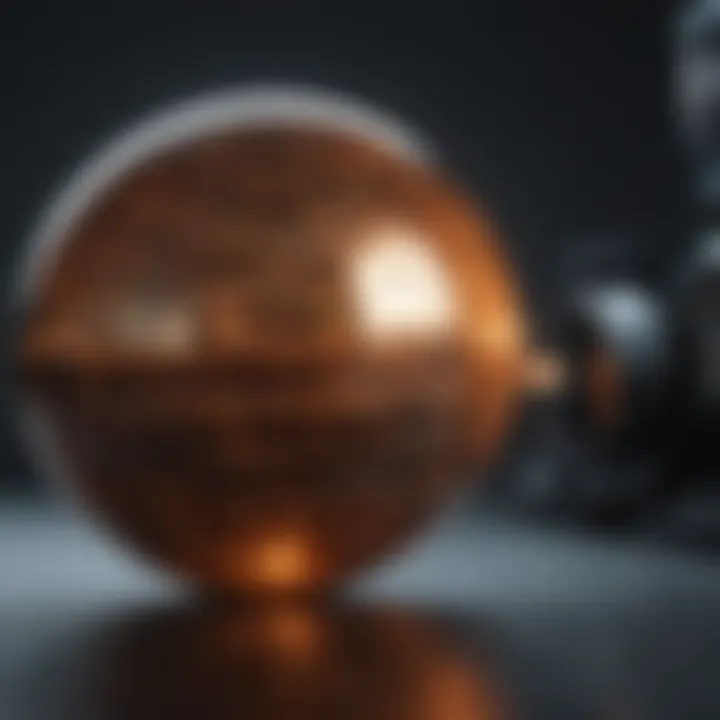
The advent of real-time measurement systems marks another pivotal advancement in the field. Traditional roughness measurement techniques often involve taking samples and analyzing them in a separate process. In contrast, real-time systems allow for continuous assessment of surface properties during production, which enhances control over manufacturing processes.
For example, a manufacturing plant might implement a real-time roughness measurement system integrated into its production line. This capability enables immediate feedback, allowing operators to adjust parameters on-the-fly. As a result, the production of materials with optimal surface characteristics becomes more feasible, reducing waste and improving quality.
The implementation of real-time systems can also lead to cost savings in maintenance and operational efficiency. By detecting anomalies as they occur, repairs can be proactively managed before they lead to significant downtimes. This shift is crucial, especially in high-stakes environments where every second counts for both production and safety.
Challenges and Limitations in Roughness Measurement
When it comes to understanding the intricate nature of surface roughness, both for academic inquiry and practical applications, one can’t ignore the challenges and limitations inherent to measuring this phenomenon. The fidelity of measurement influences everything from aerospace engineering to nanotechnology. Despite advancements in measurement techniques, the reliability and accuracy that researchers and engineers vitally need can often be elusive.
The quest for precision in measuring surface roughness is key to ensuring that materials perform as expected in their respective contexts. Hence, identifying specific errors and understanding the constraints imposed by current technologies is crucial for improving future methods and applications.
Sources of Error in Measurement
In the realm of roughness measurement, even the smallest error can lead to significant implications. Here are some of the predominant sources of error to consider:
- Environmental Factors: Ambient conditions such as temperature and humidity can influence the results. For instance, a heat wave may alter the physical properties of the materials being measured, skewing the results.
- Instrument Calibration: Frequent use of measurement devices without proper calibration can result in drift, leading to inaccuracies. It's akin to trying to navigate a ship with a faulty compass; the direction may appear fine, but you’re bound to end up lost.
- Operator Skill: The experience and knowledge of the individual operating the measuring instruments play a significant role. An inexperienced operator may misinterpret data or mishandle tools, introducing errors.
- Surface Conditions: The roughness and cleanliness of the surface being measured can also significantly affect outcomes. Contaminants or residue left on the surface can lead to misleading readings, much like trying to measure the length of a dirty string; the dirt adds confusion to the true measurement.
In all, recognizing these errors can serve as the first step towards mitigating them and achieving greater accuracy in roughness measurement.
Limitations of Current Technology
While technological advancements have greatly enhanced how we measure surface roughness, certain limitations still persist. Here are a few key aspects that warrant attention:
- Resolution Limits: Some of the high-resolution techniques can still struggle with the nanoscale measurements necessary for cutting-edge applications. Achieving resolution in nanometers while maintaining a practical measurement time remains a challenge.
- Measurement Range: Many techniques are limited in the type of surfaces they can analyze. For instance, while laser scanning can provide excellent data, it may not work well for very rough or highly irregular surfaces.
- Speed of Measurement: Current systems can sometimes be cumbersome and slow in processing data, especially when handling extensive areas or multiple samples. This inadequacy can lead to bottlenecks in production where rapid surface characterization is required.
- Integration Challenges: Limited compatibility with existing systems can impede smoother operations. A roughness measurement tool that does not fit into an organization’s workflow creates friction, not just in operations but also in achieving valid results.
"Addressing the limitations imposed by current technology is critical for future advancements in surface roughness understanding."
Acknowledging and confronting these limitations head-on allows for more focused research and, ultimately, better techniques and tools designed to measure surface roughness effectively. Moving forward, interdisciplinary collaboration, innovation, and a willingness to adapt will be fundamental for overcoming these ongoing challenges.
Future Directions in SDR Roughness Research
Research on surface roughness, particularly in the context of Spatial Domain Reflectometry (SDR), continues to evolve. Looking ahead, this area promises exciting prospects that can significantly enhance not just theoretical knowledge but also practical applications across various fields. Understanding the future directions in SDR roughness research is crucial, as it can pave the way for advancements in technology, materials science, and engineering practices.
Emerging Trends
The landscape of SDR roughness research is witnessing several emerging trends driven by technological advancements and theoretical explorations. Some key developments to watch include:
- Integration of Advanced Imaging Techniques: As high-resolution imaging technology progresses, there's a growing emphasis on utilizing these methods to achieve finer measurements of surface roughness. Techniques that previously seemed to be science fiction, like digital holography and 3D optical inspections, are gaining traction.
- Data-Driven Approaches: The advent of big data analytics is transforming how researchers analyze surface roughness. Machine learning algorithms are streamlining the processing of substantial datasets, enabling more precise predictions and analyses of material behaviors in response to surface characteristics.
- Environmental Considerations: Research is increasingly focusing on the impact of surface roughness in relation to environmental factors, such as corrosion or biofouling. This trend underscores the need for surfaces that not only perform well but are also sustainable and environmentally friendly.
"The future of SDR roughness research is not just in optimizing for performance but also adapting to global sustainability challenges."
- Micro and Nanostructures: Investigations into micro and nanoscale surface structures are becoming a hot topic. Understanding how these tiny features affect overall material properties will be crucial as industries aim to innovate with advanced materials.
Interdisciplinary Approaches
One of the most promising avenues in SDR roughness research lies in interdisciplinary collaboration. By bridging knowledge and methodologies across fields, researchers can unravel complexities that single-discipline approaches may overlook. Notable aspects include:
- Combination of Physics and Material Science: Utilizing principles from physics to better model surface interactions can lead to new insights in material design. For instance, applying quantum mechanics to predict how surface roughness affects electronic properties of materials offers vast potential.
- Engineering and Computational Modeling: Structural engineering can benefit from advanced computational models that simulate how different surface textures influence performance under varied conditions. Such collaborations can help create robust structures that integrate optimal surface characteristics.
- Application in Biomedical Sciences: Exploring the intersection of surface roughness and biomedical applications is another frontier. Understanding how roughness affects cell adhesion and proliferation can lead to breakthroughs in implant technology and tissue engineering.
- Collaborative Industry Research: Partnerships between academic institutions and industries can foster practical innovations that directly respond to market needs. By sharing findings and conducting joint studies, both sectors can rapidly advance their understanding and the application of SDR roughness issues.
In summary, future research in SDR roughness is poised to transform not just academic knowledge but also industrial practices. By embracing emerging trends and interdisciplinary approaches, researchers can drive forward innovations that will define the future of material science and engineering.
Ending
The conclusion serves as a pivotal element in wrapping up the vast discussions surrounding surface roughness in the context of Spatial Domain Reflectometry (SDR). It brings together various threads of insight gained throughout the article, effectively highlighting their relevance. Understanding SDR roughness is not only an academic exercise but has practical implications that can significantly influence fields like material science, manufacturing, and coatings.
In the conclusion, we emphasize the following:
- Integration of Knowledge: Summarizing the key insights gathered, it bridges theoretical frameworks with real-world applications, ensuring that the reader walks away with a comprehensive understanding of the entire discourse on SDR roughness.
- Practical Implications: We reassert how SDR roughness affects performance in practical scenarios. This affects everything from product longevity to manufacturing efficiency.
- Challenges and Opportunities: By acknowledging the limitations and challenges identified in the discussions, future inclination can be pointed towards innovations that enhance measurement accuracy and reduce error sources.
Understanding these elements empowers engineers, researchers, and industry professionals to approach surface measurement with a sharper perspective, ultimately fostering progress and innovation.
Summarizing Key Insights
As we wrap this complex subject into a neat bow, it’s crucial to revisit some of the key insights acquired from our exploration of SDR roughness:
- Definition and Measurement: The precise definition of both SDR and surface roughness was established, with definitions grounded in scientific discourse, setting the stage for accurate measurements.
- Techniques and Standards: Variations in measurement techniques, including both contact and non-contact methods, were discussed, enabling practitioners to select appropriate tools for their needs.
- Role in Industry: The importance of SDR roughness in various industries was highlighted, indicating its significant effect on material behaviors and processes.
- Future Directions: The discussion on future research trends has opened avenues for interdisciplinary approaches and technological advancements, suggesting a collaborative effort in tackling complexities within the field.
Significance of SDR Roughness in Future Research
Looking ahead, the significance of SDR roughness extends beyond the immediate implications discussed. It holds a treasure trove of potential research avenues that can profoundly impact multiple disciplines.
- Interdisciplinary Nature: SDR roughness can offer vast opportunities for collaboration across fields such as physics, engineering, and material sciences. New methodologies and insights from one domain could breathe life into challenges faced in another.
- Technological Evolution: As measurement technologies advance, so too will our understanding of surface roughness. Embracing new approaches, like artificial intelligence or real-time measurement systems, can refine the current methodologies, making them more efficient and robust.
- Innovative Applications: The integration of SDR roughness insights can inform innovations in product design and quality management, ensuring that the end products meet precise specifications and performance standards.
In essence, the future research landscape surrounding SDR roughness promises to be rich with discoveries, paving the way for breakthroughs that could revolutionize industrial practices and enhance our general understanding of material sciences.