Fast Pneumatic Actuator: Mechanisms and Advances
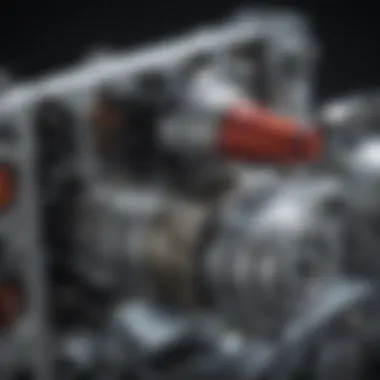
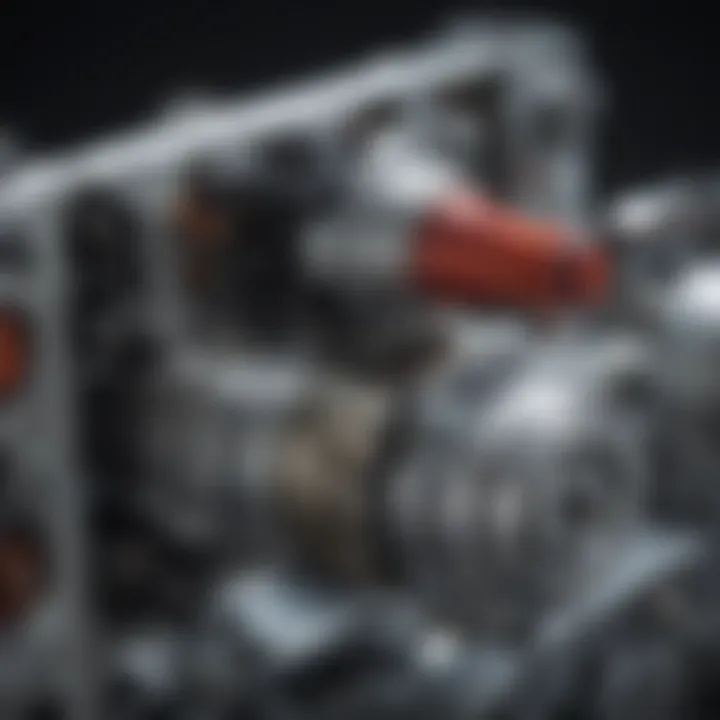
Key Concepts and Terminology
Understanding the basic terminology and concepts surrounding fast pneumatic actuators is crucial for a comprehensive grasp of their application and performance. This section elucidates the foundational elements that form the basis of further exploration into these devices.
Definition of Key Terms
- Pneumatic Actuator: A device that uses compressed air to create mechanical motion. Fast pneumatic actuators are designed for quick response times and high-speed operations.
- Cylinder: A critical component of pneumatic actuators. It houses a piston that moves back and forth when air pressure is applied.
- Pressure Regulator: A device used to control the pressure of the air supplied to the actuator, ensuring optimal performance.
- Control Valve: This regulates the airflow to the actuator, determining the speed and direction of the movement.
Concepts Explored in the Article
This article focuses on several key concepts:
- Operational Principles: Understanding how fast pneumatic actuators function through the dynamics of compressed air.
- Applications: Various industries that utilize these actuators, emphasizing their versatility and efficiency.
- Advantages and Limitations: Evaluating the benefits, such as speed and reliability, against potential drawbacks, like maintenance needs.
- Technological Advances: Recent innovations that enhance the performance and application of fast pneumatic actuators.
Findings and Discussion
In discussing fast pneumatic actuators, several main findings emerge that highlight their relevance and utility across multiple sectors.
Main Findings
- Fast pneumatic actuators are favored in automotive and manufacturing industries for their rapid response times, which improve efficiency and productivity.
- Secondary applications can be found in robotics, where precision and speed are essential.
- Integration of smart technology and sensors has led to improved reliability and functionality in fast pneumatic actuators, making them more adaptable to changing operational demands.
Potential Areas for Future Research
- Sustainability: Investigating more eco-friendly pneumatic systems that maintain performance while reducing environmental impact.
- Smart Integration: Exploring how IoT can transform actuator functionality, enhancing automation processes.
- Advanced Material Use: Researching new materials that could enhance durability and reduce maintenance costs.
Recent advancements in actuator design have opened up exciting possibilities for automation and efficiency across various fields, making it an engaging area for ongoing research and development.
Foreword to Fast Pneumatic Actuators
Fast pneumatic actuators offer significant value across various industrial applications. Their rapid actuation capabilities enhance productivity and efficiency, making them essential in modern automation systems. In this article, we will explore their mechanisms, applications, and the latest advancements.
Definition of Pneumatic Actuators
Pneumatic actuators are devices that convert compressed air into mechanical motion. The air pressure acts on a piston, resulting in linear or rotary motion. This simple yet effective operation makes pneumatic actuators widely used. They can be found in machines, production lines, and even consumer appliances.
The primary components of these actuators include:
- Air cylinder: Where the piston moves
- Air supply: Compressed air source for operation
- Control valves: Directing airflow to control speed and direction
These components work together, providing the necessary forces to perform different tasks in automation.
Importance of Speed in Actuation
The speed of pneumatic actuators plays a crucial role in their effectiveness. Rapid response times lead to increased production rates and improved operational efficiency. In industries like manufacturing, even a small increase in speed can result in significant gains in output.
Moreover, fast actuation can enhance safety. Quick and precise movements reduce the risk of accidents or equipment damage.
"The developments in fast pneumatic actuators have led to innovations that supply both speed and reliability."
Speed also supports better control in applications, allowing for more complex movements and tasks. As automation continues to evolve, the demand for efficient and speedy actuators will only increase.
Operational Principles of Fast Pneumatic Actuators
Understanding the operational principles of fast pneumatic actuators is essential for grasping their functionality and relevance in various industrial applications. This section explains the mechanisms that underpin pneumatic actuation and how control systems are integrated to optimize performance. These principles are not only fundamental to designers and engineers but also to anyone interested in automation technology.
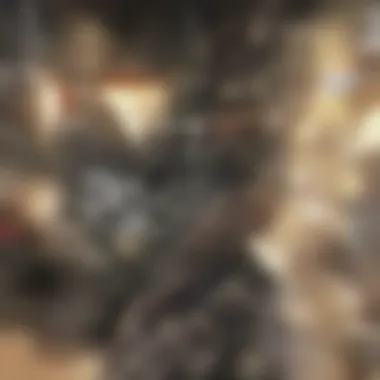
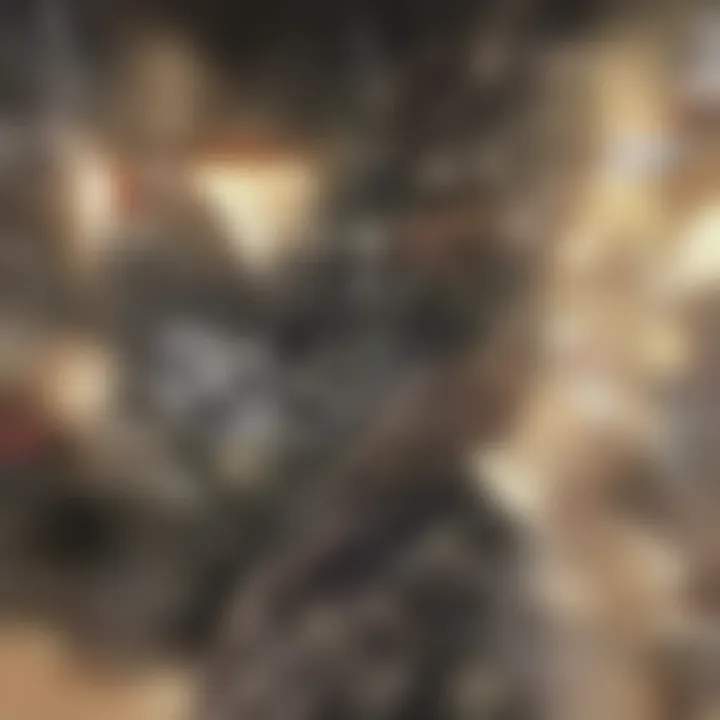
Mechanics of Pneumatic Actuation
Pneumatic actuators convert compressed air into mechanical motion. The basic mechanism involves a cylinder, a piston, and the surrounding air pressure. When air is supplied to the cylinder, it forces the piston to move, thus producing linear or rotary motion. The design can vary, but the essential elements remain consistent. Two key types of pneumatic actuators are linear actuators, which move in a straight line, and rotary actuators, which generate rotary motion.
Components of Pneumatic Actuation:
- Cylinder: The cylinder houses the piston and is where air pressure acts.
- Piston: The piston moves within the cylinder, converting air pressure into movement.
- End Stops: These prevent the piston from moving beyond desired limits.
The interaction of these components illustrates the balance between speed and force. Faster actuation can often mean a compromise in force output or stability, which must be carefully managed in applications that require precision.
Control Systems for Actuators
Control systems are integral to the operation of fast pneumatic actuators. These systems regulate the flow of air to the actuator, ensuring that response times are quick and movements are precise. Various control methods can be employed, ranging from simple on-off control to complex programmable logic controllers (PLCs).
Key Aspects of Control Systems:
- Feedback Loops: Incorporating sensors provides real-time data on actuator performance. This data influences adjustments in air pressure and flow rates to maintain optimal operation.
- Solenoid Valves: These valves enable rapid control of air supply, allowing for precise and timely actuation.
- Variable Frequency Drives (VFDs): In some cases, VFDs play a role in adjusting the actuator's speed by modulating the power supply.
"The efficiency of a pneumatic system directly correlates with the sophistication of its control mechanisms."
By optimizing control systems, users can achieve significant improvements in speed and accuracy. Understanding these operational principles helps demystify the advanced functionalities of fast pneumatic actuators and provides a solid foundation for investigating their real-world applications.
Key Components of Fast Pneumatic Actuators
Understanding the key components of fast pneumatic actuators is crucial to grasp their operational efficiency and application across various fields. Each part plays a significant role in achieving swift and reliable actuation, which is paramount for industries such as manufacturing, aerospace, and robotics.
Many factors influence the effectiveness of these actuators, including material properties, design intricacies, and control methodologies.
Air Supply and Compression Systems
The air supply system is foundational to the performance of pneumatic actuators. It provides the necessary compressed air that powers the actuator's movement. Compressed air is generated through a compressor, which converts ambient air into high-pressure air. The efficiency and reliability of this system bear directly on the actuator's responsiveness.
- Types of Compressors: Different compressors can be employed, such as rotary screw compressors, reciprocating compressors, and scroll compressors. The choice depends on the required pressure levels and flow rates for specific applications.
- Pressure Regulation: Maintaining optimal pressure is crucial. Regulators are used to adjust the pressure to suitable levels, ensuring that the actuator functions correctly without risk of damage due to overpressure.
Valves and Flow Control
Valves are integral components that manage the flow of compressed air into and out of the actuator. Proper flow control impacts speed and responsiveness.
- Types of Valves: Common types include solenoid valves, pneumatic control valves, and flow control valves. Each type has specific applications depending on the required features, such as rapid actuation speed or precise flow regulation.
- Flow Rate and Speed: Essentially, the valve's design also governs the actuator's cycling speed. A valve that allows higher airflow can facilitate faster movement, but it may compromise precision. Balancing these elements is key for designers and engineers.
Actuator Design and Materials
The design and materials chosen for a pneumatic actuator significantly influence its efficiency, durability, and overall performance. The following aspects are essential:
- Design Configuration: Various configurations, such as single-acting and double-acting actuators, are available, each offering different benefits depending on application needs. Double-acting actuators typically provide greater force and control.
- Material Selection: The choice of materials for components must ensure longevity and reliability. Lightweight alloys, durable plastics, and corrosion-resistant materials are often used. The right choice affects not only the actuator's life but also its servicing requirements.
The selection of components in fast pneumatic actuators is vital. It impacts performance, service life, and maintenance needs, which must be carefully considered in design and application strategies.
In summary, key components such as air supply, valves, and actuator design form the backbone of fast pneumatic actuators. Their thoughtful integration ensures high speed, reliability, and precision necessary to meet industrial demands.
Advantages of Fast Pneumatic Actuators
Fast pneumatic actuators are essential in many modern mechanical systems. Their benefits extend across various industries, highlighting their effectiveness in numerous applications. Understanding these advantages is key to appreciating their growing use in both automation and other fields.
Speed and Precision
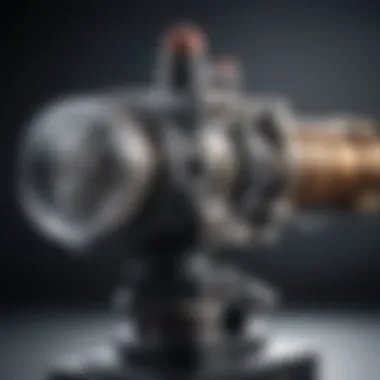
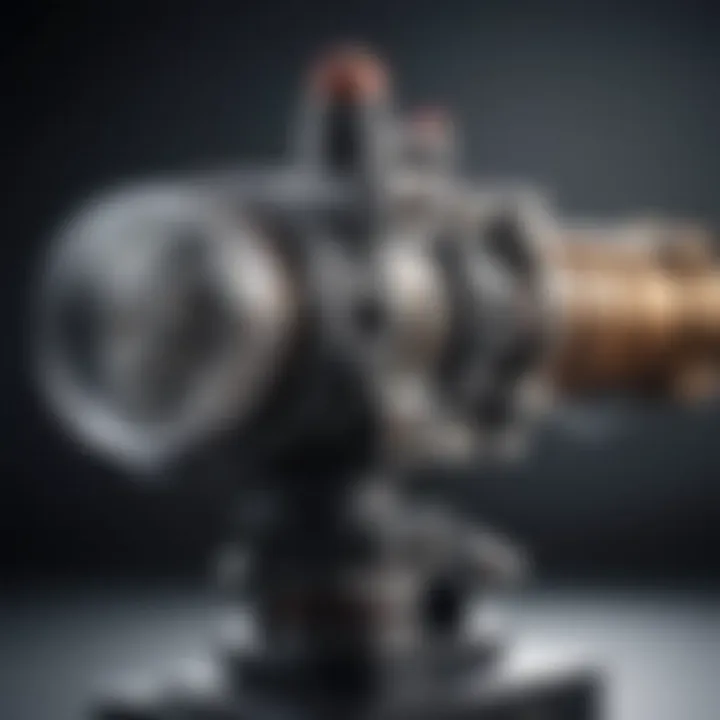
The main advantage of fast pneumatic actuators lies in their quick response times. Unlike other actuating systems, these actuators can manipulate components swiftly, enhancing overall system performance. Their ability to operate rapidly makes them especially valuable in scenarios requiring high-speed actions, such as assembly lines. In these applications, precision is equally important. Fast pneumatic actuators provide precise movements, allowing for accurate positioning of parts. This is crucial when working with intricate machinery or tasks that demand a high degree of accuracy, such as in medical devices or robotics. Moreover, advancements in control systems have further improved the speed and precision of these actuators, enabling even greater performance in dynamic work environments.
Efficiency in Resource Use
Fast pneumatic actuators are known for their operational efficiency. They consume less energy compared to electric actuators, particularly in applications needing quick cycling. This results in lower operational costs, as less energy means reduced utility bills. Additionally, these actuators are designed to minimize air consumption, which is another factor that contributes to their efficiency. The use of pneumatic systems allows for faster cycling times without compromising the effectiveness of the overall machinery. In sectors such as manufacturing, this efficiency can translate to significant productivity gains. As industries become increasingly conscious of resource use, pneumatic actuation offers a sustainable solution that does not sacrifice performance.
Safety in Operation
Safety is a paramount concern in the design and operation of industrial equipment. Fast pneumatic actuators contribute positively in this regard. They are generally considered safe due to their inherent simplicity. The lack of complicated electronics reduces the chances of malfunction. In many industries, certain pneumatic systems include fail-safe mechanisms, which add another layer of safety. Unlike electrical systems, pneumatic actuators do not produce sparks, making them safer in explosive environments. Furthermore, the lightweight materials often used in actuator design enhance their safety profile by reducing the risk of heavy machinery hazards. Companies can thus operate these actuators with a reduced risk of accidents and failures, promoting a safer workplace environment.
"Incorporating fast pneumatic actuators into industrial processes can enhance safety, speed, and efficiency simultaneously."
Fast pneumatic actuators demonstrate clear advantages in speed, efficiency, and safety, making them an excellent choice for various applications. Their design, operational principles, and technological advancements ensure they meet the demanding needs of modern industries.
Applications of Fast Pneumatic Actuators
The application of fast pneumatic actuators is crucial in various domains. Their ability to provide quick and precise movements makes them highly valued in modern systems. Understanding these applications allows professionals and researchers to appreciate the role these devices play in enhancing efficiency and productivity. In manufacturing and automation, for example, speed is paramount. Fast pneumatic actuators facilitate rapid cycle times, contributing to increased output while reducing operational costs.
Manufacturing and Automation
In manufacturing environments, fast pneumatic actuators are integral. They enable automation in assembly lines, where tasks must be performed quickly and accurately. For instance, their use in robotic arms allows for smooth product handling. Such actuators can respond to control signals almost instantaneously, improving the overall speed of production. They can manage heavy loads while achieving precision critical for tasks like welding or component placement.
Medical Devices and Equipment
Fast pneumatic actuators find significant use in medical devices. They are applied in surgical robots that demand high accuracy and quick response time. For example, a fast pneumatic actuator can control the movements of robotic arms during delicate procedures like laparoscopic surgeries. This accuracy can lead to better surgical outcomes and quicker recovery times for patients. Additionally, these actuators are used in various medical imaging devices, aiding in the adjustment and positioning of heavy components without compromising safety or reliability.
Aerospace Applications
In aerospace, the application of fast pneumatic actuators is also noteworthy. They play a vital role in controlling movement in aircraft systems. For example, they are utilized in flaps and slats which are critical during takeoff and landing phases. The rapid response of these actuators ensures immediate adjustments according to flight conditions. This responsiveness improves safety and operational efficiency. Furthermore, their durability and reliability are essential in such demanding environments, making them a logical choice for high-stakes aerospace applications.
Entertainment and Robotics
Fast pneumatic actuators have unique applications in the entertainment industry. They enhance the functionality of animatronics in theme parks and movies, providing realistic movement. For instance, they can enable seamless and rapid actions that captivate audiences. In robotics, these actuators are employed in developing advanced robotic systems that mimic human motion. The precision and speed of actuators allow for better interaction in robots used for companionship or assistance.
Fast pneumatic actuators redefine speed and accuracy across various industries, enhancing both functionality and safety.
Limitations and Challenges
Understanding the limitations and challenges of fast pneumatic actuators is crucial. These factors can impact their overall effectiveness and sustainability within various applications. When evaluating the deployment of these actuators, it is important to consider the potential environmental impacts, maintenance requirements, and reliability issues that may arise. Addressing these challenges can enhance the performance and acceptance of pneumatic systems in industry.
Environmental Impacts and Regulations
Fast pneumatic actuators, despite their benefits, can pose certain environmental concerns. The air compressing process can generate noise pollution, which is often overlooked in industrial settings. This noise can be detrimental not only to worker health but also to the surrounding community. Moreover, there is a growing trend towards sustainability. Regulations regarding emissions and energy efficiency are increasingly scrutinizing pneumatic systems. To stay compliant, actuator systems must undergo modifications or improvements.
Additionally, the disposal of used components, such as end-of-life actuators and their associated materials, raises ecological questions. Improper disposal can lead to environmental degradation. Therefore, manufacturers are pressured to develop recyclable materials and environmentally friendly disposal methods.
"Mitigating the environmental impact of pneumatic systems is becoming a priority as industries strive for sustainability and compliance with regulations."
Maintenance and Reliability Issues
Reliability is a paramount concern when using fast pneumatic actuators. The mechanism relies heavily on compressed air, which necessitates a consistent supply. Variability in air pressure can lead to performance issues or actuator failure. Regular monitoring of air quality and pressure levels becomes essential in maintaining effective operation.
Maintenance can also be intensive. Although pneumatic actuators have fewer moving parts compared to electric or hydraulic options, they still require regular inspections and maintenance. This includes verifying the integrity of seals, hoses, and tubing that may degrade over time. Neglecting these regular checks can lead to leaks, affecting overall system performance.
Another critical aspect is the need for specialized knowledge. Personnel operating pneumatic systems must have proper training to ensure both efficient use and maintenance. Inadequate knowledge can result in operational mishaps, costly downtimes, and safety risks.
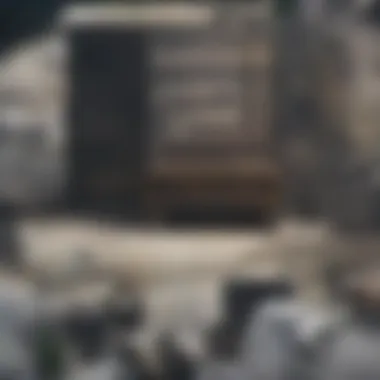
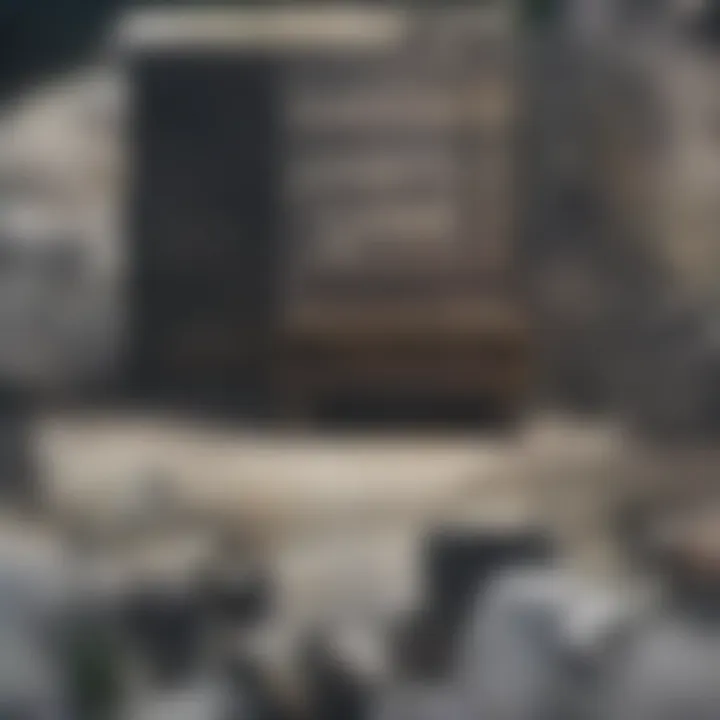
Technological Advancements in Fast Pneumatic Actuators
Understanding technological advancements in fast pneumatic actuators is vital for both current practices and future developments in the field. These advancements influence how efficiently and effectively actuators can perform in various applications. The integration of new technologies enhances their functionality, reliability, and usability. Moreover, these developments can lead to innovative applications across diverse industries, aiding in automation, speed, and precision tasks.
Smart Actuator Technologies
Smart actuator technologies represent a significant leap in the capabilities of fast pneumatic actuators. These systems employ sensors and advanced control algorithms to provide real-time data and feedback, allowing for more precise operation. For instance, integrating pressure sensors or position sensors can help monitor the actuator status. This aids in adjusting performance dynamically based on operational conditions.
- Benefits of Smart Actuator Technologies:
- Improved accuracy through real-time adjustments.
- Reduced energy consumption by optimizing operation.
- Enhanced diagnostics capability for better maintenance scheduling.
Implementing these smart systems can result in a more efficient workflow, reduced downtime, and longer service life for the equipment involved. As companies strive for operational excellence, smart actuator technologies will undoubtedly play a pivotal role in achieving those standards.
Integration with IoT Systems
The integration of fast pneumatic actuators with IoT systems offers a redesigned method of operation and control. By connecting these actuators to the Internet, operators can monitor and manage them remotely. This connectivity fosters an ecosystem where data from various sources can be aggregated and analyzed for optimal performance.
Several critical aspects are associated with IoT integration:
- Remote Monitoring: Operators can check actuator performance from anywhere, enhancing flexibility.
- Data Analytics: By collecting performance data, operators can predict failures and schedule maintenance more effectively, reducing unexpected downtimes.
- Automation: Automating the actuation process through IoT can streamline production processes significantly.
"The future of pneumatic systems lies in their ability to communicate and adapt through interconnected technologies."
Technological advancements in fast pneumatic actuators thus represent a confluence of efficiency, reliability, and smart integration. In an age of rapid technological change, understanding these trends is crucial for stakeholders across various sectors.
Future Trends in Fast Pneumatic Actuator Design
Fast pneumatic actuators have gained significance across many industries due to their effectiveness and efficiency. As technology evolves, so do the design and application of these devices. Understanding future trends in their design is crucial for professionals, researchers, and students who seek to leverage the immense capabilities of pneumatic actuation. The focus is on integrating innovation with traditional principles to enhance performance, lower costs, and broaden functionality.
Developing bio-inspired actuator concepts represents a frontier in actuator design rooted in nature’s designs. These concepts mimic the functions seen in biological organisms, leading to more adaptable and efficient actuators. For instance, by studying the mechanics of venous pumps in certain species, engineers can create actuators that are more responsive to environmental changes. This not only improves efficiency but also creates more durable systems.
Another noteworthy progression is the rise of hybrid actuation systems that combine pneumatic technology with other mechanisms. These systems utilize the strengths of various types of actuation processes, such as electrical or hydraulic, achieving greater versatility. By fusing these technologies, engineers can design actuators capable of delivering high torque while maintaining the light weight and speed advantages of pneumatic systems. Hybrid designs can also cater to applications with stringent safety requirements, thereby enhancing reliability in critical scenarios.
"The combination of innovations in actuator technology paves a promising path toward higher efficiency and functionality. Hybrid systems are becoming increasingly prevalent."
The ongoing research is directed towards creating actuators that use less energy while offering superior functionality. Therefore, developments like smart sensors and IoT integration are pivotal. Smart sensors provide real-time data, promoting condition-based maintenance and enhancing safety. Moreover, communication with IoT systems can optimize operational parameters, improving both productivity and cost-efficiency.
In summary, tapping into future trends of fast pneumatic actuators involves a mix of innovation and practicality. The integration of bio-inspired concepts and hybrid systems will not only redefine the capabilities of actuators but also address current challenges in various industrial applications.
Epilogue
The conclusion of this article emphasizes the critical role of fast pneumatic actuators in modern industrial applications. Their ability to deliver rapid and precise motion transformation makes them indispensable across varied sectors. As illustrated throughout the article, the benefits of these actuators include improved efficiency, enhanced safety, and versatility in applications ranging from manufacturing to healthcare.
In summary, the operational principles guiding fast pneumatic actuators reveal their mechanics and the advanced control systems that optimize their performance. The key components, such as air supply systems and smart technology integrations, drive both their functionality and reliability. Moreover, the article outlines various real-world applications where these actuators excel, affirming their relevance in sectors like robotics and aerospace.
Importantly, challenges and limitations, including maintenance needs and environmental considerations, must be acknowledged. Recognizing these factors allows for more informed decisions when integrating pneumatic actuator systems.
Recap of Key Insights
- Mechanics and Efficiency: Fast pneumatic actuators convert energy efficiently, delivering high-speed operation crucial in fast-paced environments.
- Diverse Applications: Their versatility extends across manufacturing, healthcare, aerospace, and entertainment, demonstrating broad utility.
- Challenges: Environmental impacts and the need for maintenance emphasize the importance of strategy in technology implementation.
"Fast pneumatic actuators embody innovation in motion, merging speed with precision to meet growing industrial demands."
Call for Further Research
Continued study into fast pneumatic actuators is essential as technology evolves. Emerging areas of research could include:
- Advanced Materials: Investigating new materials for enhanced durability and performance under various conditions.
- Miniaturization: Exploring smaller designs that maintain power while saving space in applications such as medical devices.
- Autonomous Systems: Integrating artificial intelligence for smarter actuation solutions within the Internet of Things (IoT) frameworks.
The landscape of fast pneumatic actuation is dynamic. Ongoing research will support the adaption of these systems to address contemporary challenges and harness advancements in automation and control.