Flow Safety Valves: Key Insights for Industry Applications

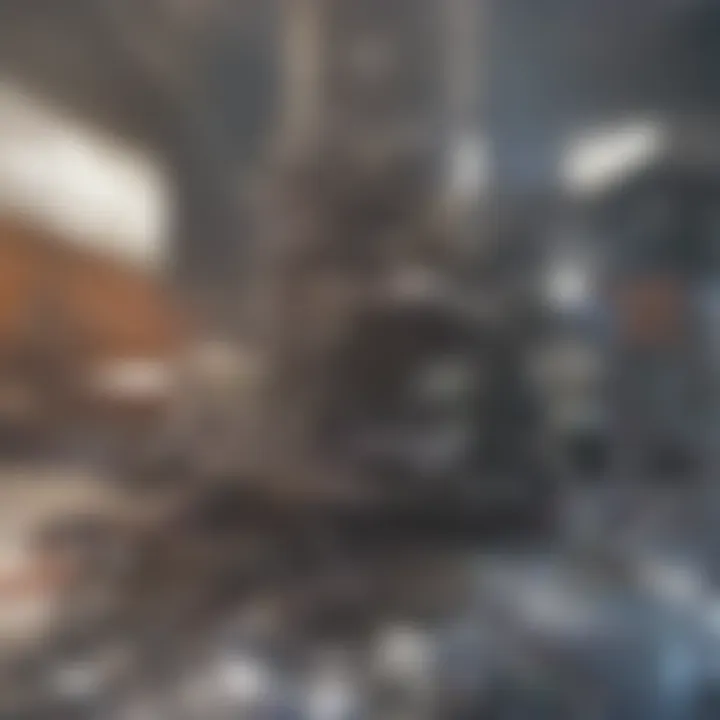
Intro
Flow safety valves are crucial components in various industrial systems. These devices play an essential role in preventing overpressure conditions that can lead to equipment failure or catastrophic incidents. Their proper function ensures safety and efficiency within operating systems. Understanding flow safety valves requires more than just knowing their types; one must grasp their design, operational principles, and maintenance requirements.
In this guide, we will explore the key aspects associated with flow safety valves. This includes definitions of important terms, a discussion of their applications, and a look at modern standards and emerging technologies. By doing so, we aim to provide substantial insight that professionals and researchers can leverage to optimize their systems.
As we move through the article, we will identify relevant concepts and findings in the realm of flow safety valves to enhance comprehensibility and application in real-world scenarios.
Understanding Flow Safety Valves
Flow safety valves are critical components in various industries, serving to protect systems from unexpected pressure spikes and ensuring safe operations. Understanding flow safety valves is essential for engineers and professionals who work in sectors like oil and gas, chemical processing, and water treatment. Their correct selection and placement can significantly enhance the safety and efficiency of industrial processes.
Moreover, flow safety valves function as a first line of defense against potential hazards. They prevent catastrophic failures that can lead to property damage, environmental harm, and even loss of life. Thus, the importance of flow safety valves cannot be overstated; they are often mandated by regulatory standards to ensure compliance and operational reliability.
Definition and Purpose
A flow safety valve, commonly known as a pressure relief valve, is designed to automatically release excess pressure from a system to maintain safety. The main purpose of these valves is to protect equipment and personnel from the dangers associated with overpressure. By allowing controlled discharge of fluids—be it gas or liquid—these valves prevent potential explosions or equipment damage.
Flow safety valves are utilized in a variety of applications across multiple industries. For instance, in the oil and gas sector, they are vital for managing pressure in pipelines, while in chemical processing, they help maintain the integrity of reactors. All in all, these valves are indispensable for ensuring the safety of complex industrial systems.
Working Principle
The working principle of flow safety valves is relatively straightforward but varies slightly depending on the type of valve in question. Most flow safety valves operate based on the concept of set pressure.
- Set Pressure: Each valve is designed to open at a predetermined pressure level. When the pressure exceeds this value, the valve engages, allowing fluid to escape, thereby reducing the pressure within the system.
- Closing Mechanism: Once the pressure drops back to a safe level, the valve will close automatically, allowing the system to resume normal operation.
This automatic response mechanism is crucial for minimizing human intervention and ensuring timely protection. The rapid action taken by flow safety valves mitigates the chances of serious accidents, thus highlighting their essential role in the engineering landscape.
Types of Flow Safety Valves
Understanding the different types of flow safety valves is crucial for professionals involved in system design and safety management. Each type offers unique advantages and specific applications, making it essential to select the right valve according to operational requirements. The effective implementation of flow safety valves directly impacts safety and efficiency in various industrial sectors. This section will explore four primary types of flow safety valves: spring-loaded safety valves, pilot-operated safety valves, diaphragm safety valves, and electronic safety valves.
Spring-Loaded Safety Valves
Spring-loaded safety valves are a traditional and widely used type. They rely on a spring mechanism to hold the valve closed against internal pressure. When the pressure exceeds a predetermined limit, the spring compresses, allowing the valve to open and release excess pressure. This operation is simple, reliable, and cost-effective, making it a preferred option in many applications, especially in the oil and gas industry.
Here are some key aspects to note about spring-loaded safety valves:
- Reliability: They have been used for decades and have proven their reliability over time.
- Cost: Generally, they are lower in cost compared to other valve types, making them accessible for various applications.
- Maintenance: They require regular maintenance to ensure proper functionality, as the spring may degrade over time.
"Spring-loaded valves are particularly effective in systems where pressure spikes are occasional but need immediate response."
Pilot-Operated Safety Valves
Pilot-operated safety valves offer enhanced performance for high-capacity applications. Unlike spring-loaded valves, these utilize a pilot valve to control the main valve. The pilot valve monitors pressure and opens to allow system pressure to control the opening of the main valve. This design provides greater accuracy and responsiveness to pressure changes, which makes them suitable for larger systems.
Advantages of pilot-operated safety valves include:
- Efficiency: They can handle larger flow rates more effectively, making them ideal for heavy-duty applications.
- Precision: Provide precise pressure control, essential in chemical processing and power generation.
- Reduced Leakage: Improved sealing reduces the risk of fluid loss and enhances overall system efficiency.
Diaphragm Safety Valves
Diaphragm safety valves operate on a completely different principle. A flexible diaphragm serves as the barrier between the system pressure and the actuator. When pressure exceeds a specific threshold, the diaphragm flexes, allowing fluid to escape. These valves are often used in applications where cleanliness is crucial, such as in pharmaceuticals or food processing, because there is no direct contact between the fluid and the valve actuators.
Essential points about diaphragm safety valves:
- Clean Operation: The design minimizes contamination risks of the fluid being controlled.
- Sensitivity: They are extremely sensitive to pressure changes, providing rapid response.
- Versatility: Adaptable to a wide range of applications due to their ability to handle different fluids, including gases and corrosive substances.
Electronic Safety Valves
Electronic safety valves represent the future of flow control technology. These valves integrate electronic controls that allow for monitoring and adjusting valve operation in real-time. They can be connected to control systems using IoT technology, enabling advanced features such as predictive maintenance and automated functionality.
The benefits of electronic safety valves are substantial:
- Automation: They can be fully automated, requiring minimal human intervention.
- Data Monitoring: Real-time data collection provides valuable insights into system performance.
- Enhanced Control: Their capability to operate under various conditions enables superior control over fluid flow.

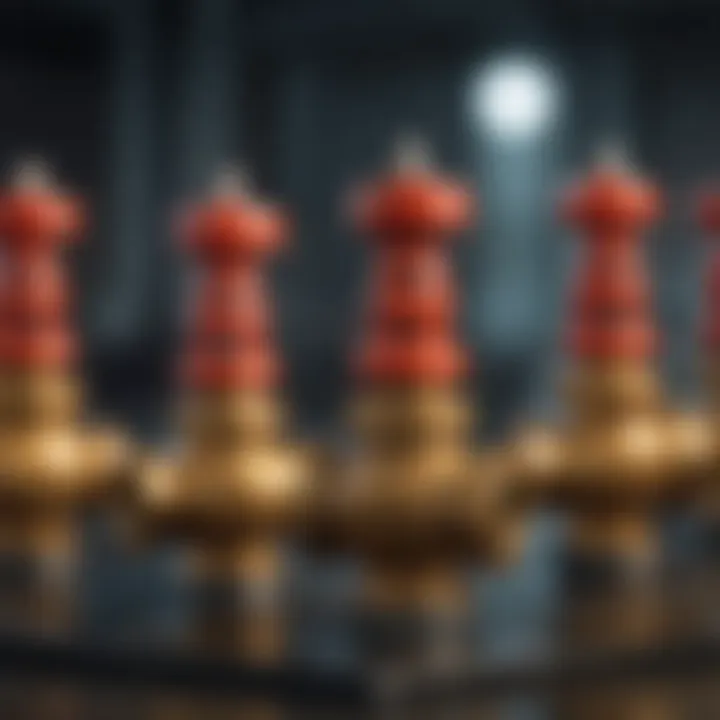
Design Considerations
The design of flow safety valves is critical to ensuring they perform effectively and reliably in varying industrial conditions. This section emphasizes key design elements that professionals must consider to optimize functionality, efficiency, and safety. The foundational aspects of material selection, sizing and flow capacity, and pressure and temperature ratings play a significant role in the performance and longevity of these valves.
Material Selection
Selecting the right materials for flow safety valves is essential. The material must withstand aggressive environments, including high pressures and corrosive substances. Common materials include stainless steel, brass, and various alloys.
- Corrosion Resistance: Stainless steel is often preferred due to its strength and resistance to corrosion.
- Temperature Tolerance: High-temperature alloys may be required for valves in thermal or chemical processes.
Today, manufacturers consider the whole lifecycle of the materials, ensuring they provide longevity, reduce maintenance costs, and support sustainability efforts.
Sizing and Flow Capacity
Proper sizing of flow safety valves is vital in ensuring optimal flow capacity without compromising safety. Each valve must match the flow requirements of its specific system, distinguishing between different flow rates. The following aspects are critical in this process:
- Flow Coefficient (Cv): This metric helps determine the capability of a valve to pass fluid. A well-calculated Cv value ensures maximum efficiency without risking overpressure scenarios.
- Pipe Size Compatibility: The valve must align with the existing pipe sizes to prevent bottlenecks and turbulence.
Underestimating the valve size can lead to significant safety risks, while oversized valves may operate inefficiently, leading to increased wear and tear.
Pressure and Temperature Ratings
Flow safety valves must be engineered to operate safely within specific pressure and temperature limits. Understanding these ratings is crucial to avoid valve failures:
- Pressure Rating: It indicates the maximum amount of pressure a valve can handle. Ratings are often marked by the American Society of Mechanical Engineers (ASME) and should be strictly observed.
- Temperature Rating: This defines the limits of operational temperatures. Exceeding these limits can cause materials to weaken, resulting in failures, leaks, or catastrophic events.
Properly assessing both ratings ensures that the valves function within safe parameters. This not only enhances safety but also assures operational efficiency under diverse conditions.
Proper design considerations minimize risks associated with flow safety valves while maximizing their reliability and performance in critical applications.
Applications of Flow Safety Valves
Flow safety valves are crucial components in various industrial applications, safeguarding equipment and ensuring operational safety. Their applications extend across multiple sectors, each requiring specialized usage and tailored solutions. Understanding these applications helps engineers and safety professionals make informed decisions regarding installations, inspections, and compliance with regulations.
Oil and Gas Industry
In the oil and gas sector, flow safety valves play a pivotal role in preventing catastrophic incidents due to pressure fluctuations. With pipelines carrying flammable materials under high pressure, a malfunction can lead to explosions or hazardous leaks. These valves serve as safety mechanisms to release excess pressure, maintaining system integrity.
Moreover, the oil and gas industry operates under strict regulations such as those implemented by the Occupational Safety and Health Administration (OSHA). Compliance with these regulations necessitates the use of reliable safety valves to mitigate risks associated with drilling, refining, and transportation.
Chemical Processing
Chemical processing facilities utilize flow safety valves to manage the complexities of various chemistries and high-pressure operations. These valves help in controlling chemical reactions by maintaining the desired pressure levels during production.
Accurate functioning of safety valves is essential. A valve failure can result in dangerous chemical spills or uncontrolled reactions, which can be harmful to workers and the surrounding environment. Proper installation, regular inspections, and the right choice of materials are essential for ensuring that these valves perform effectively in aggressive environments.
Power Generation
In power generation, especially in steam and gas turbines, flow safety valves ensure that pressure levels do not exceed safe limits. The failure to control pressure in these systems can lead to system failures or even total plant shutdowns, resulting in significant financial losses.
Here, safety valves not only protect the equipment but also ensure continuous power supply. Regular maintenance schedules and testing are standard practices to maintain the reliability of these safety solutions.
Water Treatment
Flow safety valves are integral to water treatment facilities. These systems manage the treatment processes to maintain optimal pressure conditions. Valve failures in water treatment systems can lead to contamination, affecting public health and safety.
Additionally, regulations governing water treatment ensure that these systems operate within specified pressure limits to avoid any backflow or contamination. Therefore, regular checks and adherence to maintenance protocols are a fundamental aspect of ensuring these safety valves fulfill their intended purpose.
"Flow safety valves are not just regulatory requirements; they are vital for operational integrity across multiple sectors, safeguarding lives and environments."
Regulatory Standards and Compliance
Understanding regulatory standards and compliance is crucial for the safe and efficient operation of flow safety valves. These frameworks ensure that safety valves meet specific performance requirements, protecting both equipment and personnel in various industrial environments. Adhering to these standards not only minimizes risk but also enhances the reliability and functionality of safety systems.
International Guidelines
Various international guidelines are established to regulate the design and operation of flow safety valves. Organizations such as the American Society of Mechanical Engineers (ASME) and the International Organization for Standardization (ISO) provide frameworks for safety and performance.
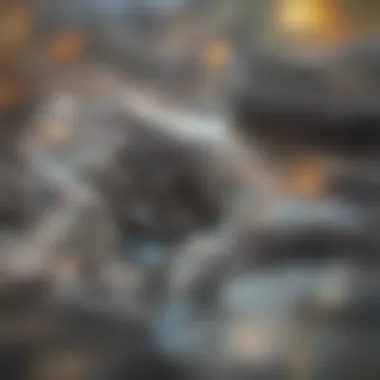
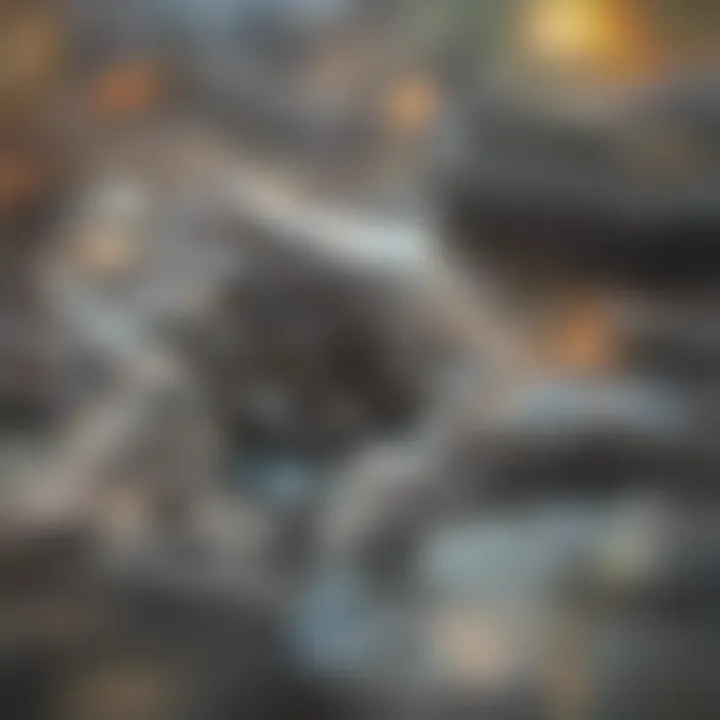
ASME’s Section VIII guidelines specify requirements for pressure equipment, while ISO 4126 pertains to safety valves specifications. Compliance with these standards ensures that safety valves can withstand the operational pressures and temperatures they encounter. This leads to reduced failure rates and longer service life, ultimately lowering maintenance costs and improving system reliability.
Local Regulations
In addition to international standards, local regulations play a vital role in safety valve compliance. Different countries may have specific laws and guidelines governing the use of safety valves in various industries. For instance, in the United States, the Occupational Safety and Health Administration (OSHA) outlines regulations that industries must follow to ensure worker safety.
Compliance with local regulations is a legal requirement. It often involves inspections, documentation, and adherence to specific material and manufacturing standards. Firms that neglect these regulations can face severe penalties, including fines and shutdowns. Therefore, understanding local legal obligations is essential for any organization utilizing flow safety valves.
Certification Bodies
Certification bodies are responsible for testing and certifying flow safety valves according to established standards. Organizations such as Underwriters Laboratories (UL) and the American National Standards Institute (ANSI) provide valuable services in this regard. These bodies conduct various tests to ensure that safety valves perform as expected under extreme conditions.
Obtaining certification from a reputable body reinforces the credibility of a product. It provides assurance to customers that the safety valves meet or exceed established performance criteria. Regular audits and re-certification processes also ensure ongoing compliance with changing standards, helping manufacturers maintain high levels of product safety and functionality.
Regulation and compliance are not just a check-box exercise; they are fundamental to operational safety and efficiency in any industry.
In summary, navigating regulatory standards and compliance is essential for the functionality and safety of flow safety valves. Through adherence to international guidelines, local regulations, and certification from recognized bodies, organizations can ensure their equipment operates efficiently and safely.
Maintenance Practices
Maintenance practices are crucial for ensuring the safe and efficient operation of flow safety valves. Regular maintenance minimizes risks, reduces the chances of failure, and extends the lifespan of these vital components in fluid systems. By instituting an effective maintenance regime, industries can prevent unexpected downtimes and costly repairs, leading to improved operational reliability.
Regular Inspections
Conducting regular inspections is a foundational aspect of maintenance for flow safety valves. These inspections should assess the physical condition of the valves, including checking for any signs of wear, corrosion, or leakage. It is especially important to verify that the valve opens and closes as intended, which verifies its responsiveness to pressure fluctuations.
During these inspections, technicians should also examine the surrounding systems. A thorough evaluation of piping, connections, and adjacent components of the valve system helps identify any issues that might impact the valve’s performance. Regular inspections can proactively catch problems, thus averting critical failures.
Key points during inspections include:
- Visual examinations for signs of damage
- Functional testing to verify precision in operation
- Calibration checks to ensure proper performance under specified conditions
Common Issues and Troubleshooting
Despite rigorous maintenance, flow safety valves may encounter issues. Common problems include sticking, inability to open, or failure to close after relieving pressure. Identifying these issues quickly is vital to maintaining system integrity. Troubleshooting involves a systematic approach to determine the root causes.
Common issues are often linked to:
- Debris accumulation: Particles may obstruct valve movement.
- Corrosion damage: Deterioration can affect seal integrity, leading to leaks.
- External pressures: Changes in the surrounding environment may impact valve function.
To troubleshoot:
- Review the system’s operating conditions.
- Analyze the valve’s history for previous failures.
- Employ diagnostic tools as necessary to assess performance.
Ultimately, the goal of troubleshooting is to rule out potential issues before they necessitate major repairs.
Replacement and Repair Protocols
When inspections and troubleshooting identify severe issues, replacement or repair of flow safety valves becomes necessary. Protocols must be in place to guide these processes effectively.
Replacement entails:
- Disconnecting the faulty valve from the system while ensuring that all residual pressures are mitigated.
- Installing a new valve that meets or exceeds the original specifications to maintain system integrity.
Repair procedures may involve:
- Replacing seals or gaskets.
- Reconditioning valves through welding or machining.
- Testing the repaired valve extensively before reintegrating it into the system.
It is critical to document all maintenance activities to maintain records for regulatory compliance. Having these records facilitates better decision-making when managing valve assets and enhances operational safety.
"Regular maintenance not only guarantees reliability but also saves costs in the long run."
Maintaining flow safety valves is not solely an operational task; it is a preventive measure that aligns with the overall safety and functionality of the industrial environment.
Emerging Technologies in Flow Safety Valves

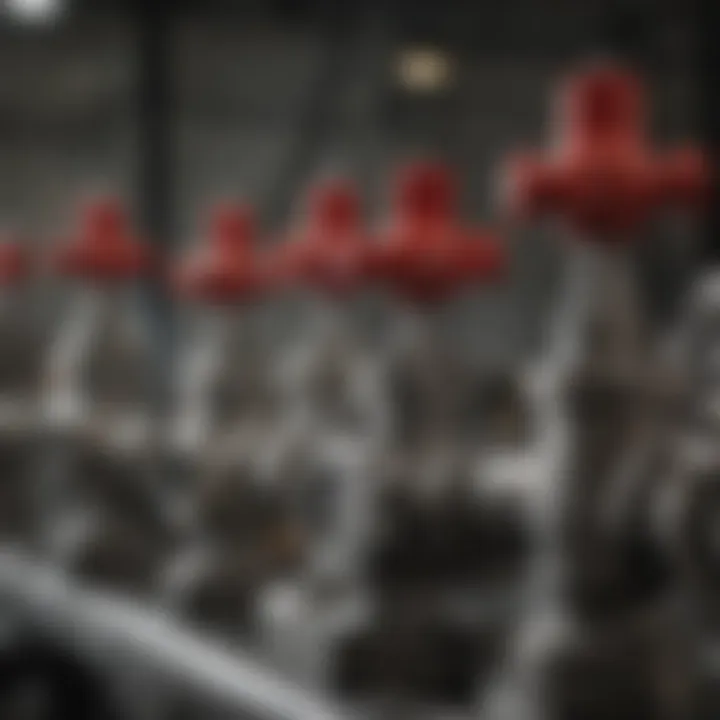
Emerging technologies within flow safety valves represent a critical advancement in enhancing efficiency and safety across various industries. These innovations include smart technologies, integration with the Internet of Things (IoT), and advancements in materials science. Understanding these elements is important for professionals aiming to optimize safety systems in response to increasing complexity in industrial processes. This section will explore these technologies, discussing their benefits and considerations.
Smart Safety Valves
Smart safety valves leverage digital technology and automation to improve operational safety and efficiency. The key features of smart valves include real-time monitoring, predictive maintenance, and enhanced control capabilities. By incorporating sensors and data analytics, these valves can detect anomalies and adjust accordingly.
- Real-Time Monitoring: This allows for continuous assessment of valve performance, leading to more proactive maintenance strategies.
- Predictive Maintenance: By analyzing data trends, potential failures can be anticipated, reducing unexpected downtime.
These features enhance system reliability, allowing operators to focus on other priorities while ensuring that safety measures are in place.
Integration with IoT
The integration of flow safety valves with IoT technologies paves the way for a connected ecosystem of industrial machinery. This connection enables seamless communication between devices, facilitating better decision-making and operational efficiency. IoT integration allows for data collection and analysis at a scale that was previously unattainable.
Some benefits include:
- Data-Driven Insights: Real-time data from valves can feed into broader system analytics.
- Remote Monitoring: Operators can monitor system performance from any location, enabling quicker responses to potential threats.
- Collaborative Systems: Multiple devices can work together to optimize overall system performance, improving safety outcomes across various sectors.
Advancements in Materials Science
Material innovations are critically reshaping flow safety valves. Improvements in material science result in valves that can withstand extreme conditions without compromising integrity. New composites and alloys can offer enhanced resistance to corrosion and high temperature, suitable for demanding environments. This advancement results in:
- Extended Lifespan: Improved materials can prolong the life of safety valves, reducing the frequency of replacements and maintenance.
- Enhanced Performance: Valves made from advanced materials can maintain functionality under more severe operational conditions.
- Sustainability: New materials can also be designed to be more environmentally friendly, aligning with industry trends towards sustainability.
The intersection of smart technology and advanced material science not only improves operational efficiency but also solidifies the role of safety valves in smart industrial environments.
By integrating smart technologies, IoT, and advanced materials, flow safety valves are evolving beyond traditional functions. These emerging technologies are essential for addressing modern industrial challenges while promoting safety and efficiency in operations.
Case Studies
Case studies serve a vital function in understanding the real-world implications of flow safety valves. They not only reveal how different valves operate under diverse conditions but also showcase both successes and failures within various industries. This section focuses on the significance of learning from past experiences. Moreover, case studies highlight the necessity for ongoing research and innovation in the design and implementation of flow safety valves. They provide specific examples that illuminate best practices while also shedding light on areas in need of improvement.
While theoretical knowledge about flow safety valves is essential, practical examples bring that knowledge to life. When a case is documented thoroughly, it offers a valuable reference point for both engineers and safety managers. Thus, case studies act as educational tools that foster better decision-making and risk management.
"Understanding past failures in flow safety valves can help prevent future incidents and save lives."
Failures and Lessons Learned
Analyzing failures of flow safety valves gains importance due to the consequences it involves, often leading to catastrophic results. A notable example is the failure of safety valves in a petroleum refining unit, which resulted in significant leakage of gases. This incident emphasized the need for regular inspections and adherence to mandated safety protocols.
Key lessons drawn from failures include:
- Material Integrity: Ensuring that materials used can withstand the operating environment.
- Installation Practices: Proper positioning and alignment can affect the valve's performance.
- Calibration: Frequent recalibration of valves is crucial to their efficient functioning.
Failures often reveal unforeseen problems that can be rectified. Incorporating findings from these instances contributes to enhanced designs and manufacturing standards.
Successful Implementations
In contrast to failures, successful implementations of flow safety valves illustrate the effectiveness of proper design and maintenance protocols. For instance, in the chemical processing industry, certain facilities have successfully integrated electronic safety valves, significantly enhancing operational efficiency and reducing risks.
Advantages of such successful cases include:
- Increased Automation: Electronic valves often have real-time monitoring systems, facilitating proactive maintenance.
- Efficiency Gains: These valves operate more accurately, which optimizes the entire process.
- Regulatory Compliance: Successful implementations often come with improved adherence to safety regulations.
Documented success stories can act as templates for best practices within various sectors. By studying these cases, professionals can gather insights that inform future projects, ultimately improving safety standards industry-wide.
Finale
The conclusion of this article on flow safety valves serves as an essential synthesis of the topics addressed throughout. It encapsulates the myriad of concepts presented, highlighting the critical function that flow safety valves play in various industrial environments. These devices are not merely components but pivotal elements ensuring safety and operational efficiency in systems where the risk of overpressure can lead to catastrophic outcomes.
Summary of Key Points
- Definition and Purpose: Flow safety valves are designed to protect systems from excess pressure, ensuring both safety and stability in operations.
- Types of Valves: Various designs, including spring-loaded, pilot-operated, and electronic valves cater to specific operational needs across industries.
- Design Considerations: Proper selection of materials, sizing for flow capacity, and adherence to pressure and temperature ratings are crucial for optimal performance.
- Applications: Flow safety valves find utility in diverse fields such as oil and gas, chemical processing, and water treatment, reflecting their versatility and necessity.
- Regulatory Compliance: Understanding and adhering to international guidelines and local regulations is imperative for successful implementation and operation.
- Maintenance Practices: Regular inspection and timely repairs are vital to prolong the lifespan of these critical components.
- Emerging Technologies: Innovations such as smart safety valves and IoT integration represent the future of flow safety technology, enhancing reliability and operational efficiency.
- Case Studies: Analyzing failures and successful implementations provides invaluable lessons for future applications.
Future Trends in Safety Valves
As industries evolve, flow safety valves are set to undergo transformative changes driven by technological advancements. Here are some trends to consider:
- Increased Integration with Smart Systems: The rise of smart manufacturing involves harnessing data analytics, enabling predictive maintenance of safety valves.
- Advanced Materials: Research and development in materials science are producing stronger, more corrosion-resistant options, further enhancing safety measures.
- Regenerative Technologies: There is a growing interest in applying regenerative concepts to valves, optimizing energy usage while maintaining safety standards.
- Adaptation to Cybersecurity: As flow safety valves become more connected, the focus on cybersecurity will be paramount to protect these systems from digital threats.
The future landscape of flow safety valves is not only about safety but also about boosting efficiency and adapting to new industrial demands.
In summary, understanding and implementing flow safety valves is a cornerstone of safety in various industries. Adapting to emerging technologies and trends will be crucial for professionals in ensuring their systems remain safe and compliant with evolving standards.