Hard Anodising Aluminium: Principles and Applications
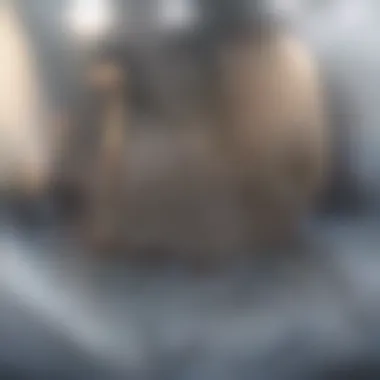
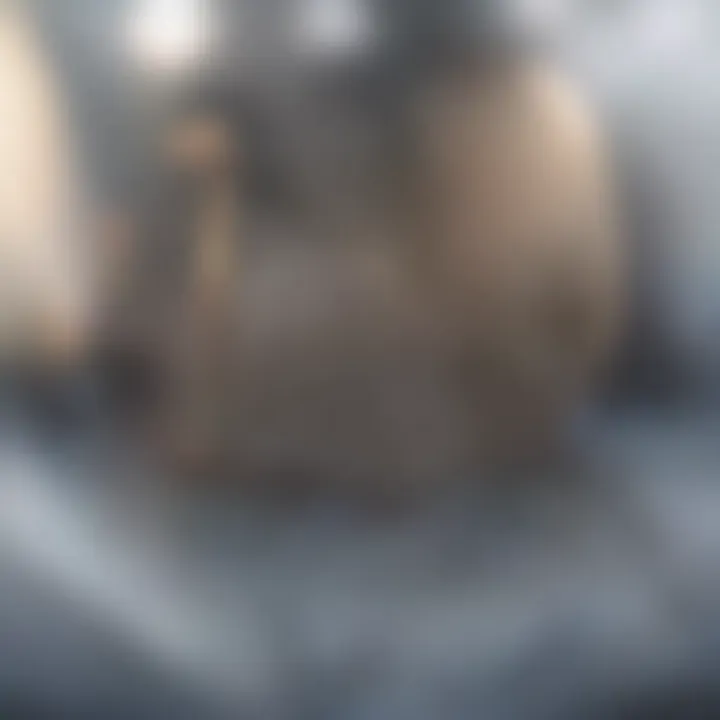
Intro
Hard anodising aluminium has become an essential process in various industries, particularly where durability and resistance to wear are paramount. This surface treatment enhances the inherent properties of aluminium, making it more suitable for demanding applications. In this article, we will explore the key concepts, processes involved, and the significant advantages offered by hard anodising. A deeper understanding of this treatment will benefit students, researchers, educators, and professionals alike, providing insight into its current relevance and potential future developments.
Key Concepts and Terminology
Definition of Key Terms
Hard anodising refers to a specific type of anodic oxidation process. It aims to produce a thick and hard oxide layer on aluminium and its alloys. The key terms associated with this process include:
- Anodising: An electrochemical process that converts the metal surface into a decorative, durable, corrosion-resistant, anodic oxide finish.
- Oxide Layer: A protective coating formed during the anodising process, increasing hardness and corrosion resistance.
- Electrolyte: A solution that enables the flow of electric current during the anodising process, usually composed of sulfuric acid in hard anodising.
Concepts Explored in the Article
This article elaborates on the principles of hard anodising, the chemical and physical reactions involved, and comparisons with traditional anodising methods. Additionally, it covers the impacts of this process on various industries and highlights recent technological advancements that influence hard anodising practices.
Findings and Discussion
Main Findings
Hard anodising has shown to increase the thickness of the oxide layer compared to standard anodising, leading to superior wear resistance. The key findings of this article include:
- The enhanced hardness of the treated aluminium, making it ideal for applications such as aerospace, automotive, and electrical components.
- A discussion on how the oxide layer provides excellent resistance to corrosion, thus prolonging the life of aluminium components in harsh environments.
- Recent innovations in hard anodising technology contribute to elevated performance, cost-effectiveness, and sustainability in manufacturing.
Potential Areas for Future Research
The field of hard anodising presents numerous opportunities for future investigation. Areas worth exploring include:
- Optimizing the process parameters for different aluminium alloys to achieve desired properties.
- Investigating the long-term performance and stability of the anodised coatings under various environmental conditions.
- Exploring alternative electrolyte solutions that may reduce environmental impact while maintaining effectiveness.
Preamble to Hard Anodising
Hard anodising of aluminium plays a crucial role in various industrial applications. Its significance lies in its ability to enhance the physical properties of aluminium, making it more suitable for demanding environments. This section delves into the fundamental aspects of hard anodising, explaining its definition and tracing its historical development.
Definition and Overview
Hard anodising, also known as hard anodization or thick anodizing, is an electrochemical process that transforms the surface of aluminium into a durable and corrosion-resistant oxide layer. This thicker anodic layer, typically measuring between 25 and 150 micrometers, is significantly thicker than standard anodising layers. The process involves immersing aluminium components in an acid electrolyte bath while passing a direct current. It not only improves wear resistance and enhances electrical insulation but also increases aesthetic qualities, making it a preferred choice in various industries.
The increased hardness from the anodic layer can reach levels of about 60 HRC, which contributes to its suitability for applications where wear and tear are prevalent. Furthermore, hard anodised surfaces can be dyed for aesthetic purposes without compromising their technical characteristics, thus adding value in sectors like consumer electronics and automotive.
Historical Development
The concept of anodising aluminium dates back to the 1920s, with standard anodising processes gaining popularity during World War II for military applications. However, hard anodising emerged as a distinct technique in the 1970s. At that time, the demand for highly durable materials prompted research into improving anodising processes. This version of anodising provided a method to create thick, protective layers for aluminium, thus addressing the challenges of material degradation.
As industries evolved, so did the processes related to hard anodising. The realisation of its benefits in aerospace applications led to further refinements in the method. Manufacturers began to focus on optimising parameters like electrolyte composition, temperature, and voltage to maximise the properties of the anodic layer. Nowadays, hard anodising is standard in sectors requiring high-performance materials, and ongoing innovations continue to enhance its capabilities further.
Fundamentals of Anodising
The fundamentals of anodising provide essential insights into the chemical and physical processes that define the treatment of aluminium surfaces. Understanding these principles is crucial, as they lay the groundwork for recognizing how anodising enhances the properties of aluminium components. The anodising process plays an invaluable role in extending the life of products, improving aesthetics, and ensuring superior durability against wear and corrosion.
Electrochemical Basis of Anodising
The anodising process is primarily an electrochemical reaction. It begins with the creation of an anodic layer on the aluminium surface when it is immersed in an electrolytic solution. Here, an electric current is passed through the solution, which typically consists of acids. The aluminium acts as an anode, while a cathode is placed in the solution. As current flows, oxygen is generated at the anode, which reacts with the aluminium to form aluminium oxide. This oxide layer is integral, as it significantly improves the surface hardness and resistance to corrosion of the underlying metal.
The thickness and quality of the anodic layer depends on various factors, including:
- Electrolyte composition: Different acids can produce varying characteristics in the oxide layer.
- Current density: The amount of current flowing can affect the growth rate of the anodic layer.
- Temperature: Higher temperatures can accelerate the reaction and influence the layer's properties.
Understanding these parameters is important for optimizing the anodising process in various applications.
Types of Anodising Processes
There are several types of anodising processes, each with distinct characteristics and applications. The two primary categories include:
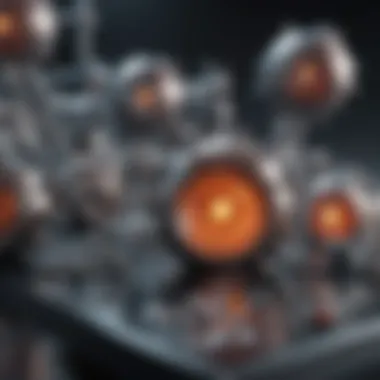
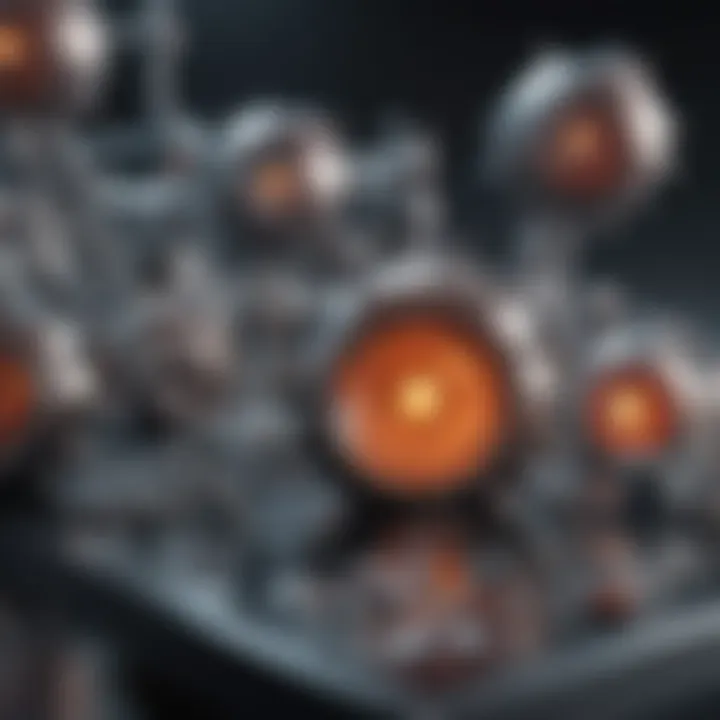
- Type I Anodising: This is a chromic acid anodising process, known for providing a thin oxide layer. It is often used in aerospace applications where minimal changes to dimensions are essential. Chromic acid anodising offers good corrosion resistance but can be less durable compared to other methods.
- Type II Anodising: This involves sulfuric acid and produces a thicker oxide layer, which is more robust than Type I. Type II anodising is the preferred method for many industrial applications as it provides excellent wear resistance and can be dyed for aesthetic purposes.
- Type III Anodising: This process creates a super-thick layer of anodic oxide, suitable for extreme environments. It is typically used in applications such as military gear, motorcycle parts, and other demanding industries.
Each of these processes has its own unique benefits and limitations, making it essential to choose the right one for specific applications. Understanding these differing methods assists in making informed decisions on materials and processes for engineers and manufacturers alike.
The Hard Anodising Process
The hard anodising process is pivotal in enhancing the performance characteristics of aluminium and its alloys. This specific method is a controlled electrochemical process that increases the thickness and density of the natural oxide layer on the surface of the metal. Such modifications confer notable durability and resistance to wear, making these materials suitable for a wide range of demanding applications. Understanding the nuances of this process is essential for professionals aiming to select the right surface treatment for their specific needs.
Process Parameters
Several key parameters dictate the effectiveness and outcomes of the hard anodising process. These parameters include current density, electrolyte composition, bath temperature, and process duration.
- Current Density: This refers to the amount of electric current applied per unit area during the anodising process. Higher current densities can expedite coating formation but may lead to less controlled growth, affecting the quality of the anodic layer.
- Electrolyte Composition: Commonly, sulfuric acid is used in hard anodising. The concentration of the acid influences both the coating thickness and the surface finish.
- Bath Temperature: The temperature of the electrolyte bath significantly affects the anodising rate. Typically, lower temperatures lead to tougher and denser oxide layers.
- Process Duration: This factor determines how long the aluminium is subjected to the anodising treatment. Extended durations generally yield thicker coatings, but this must be balanced with the desired properties of the finished product.
Equipment Used
Employing proper equipment is vital for conducting an efficient hard anodising process. The main components include:
- Rectifiers: Essential for providing a steady direct current to facilitate the anodising process.
- Anodising Tanks: Typically made from materials resistant to acid, such as polyethylene or fiberglass, these tanks are where the anodising treatment occurs.
- Cooling Systems: Maintaining a consistent temperature in the bath is critical to achieving desired outcomes.
- Filtration Systems: Used to filter out particulates and maintain the cleanliness of the electrolyte solution.
- Safety Gear: Personal protective equipment is necessary, given the corrosive nature of the chemicals involved.
Step-by-Step Procedure
The hard anodising procedure can be delineated into several clear steps:
- Surface Preparation: The aluminium parts are cleaned to remove any oxides, oils, or contaminants. This may involve chemical cleaning or mechanical processes like sanding.
- Setting Up the Anodising Tank: The tank is filled with an electrolyte solution, commonly sulfuric acid, prepared to the correct concentration.
- Connecting the Components: The aluminium parts are connected to the positive terminal of the rectifier and submerged in the electrolyte bath, while the cathode is typically made of lead or stainless steel.
- Initiating the Anodising Process: The current is turned on, beginning the anodising reaction. Monitoring of voltage and temperature should be performed continuously.
- Coating Development: As the process progresses, the anodic layer begins to form. Regular inspections can help gauge the coating's growth and uniformity.
- Post-Treatment Cleaning: Once the desired thickness is achieved, the parts are removed and rinsed thoroughly to halt the anodising reaction.
- Sealing: Finally, the anodised surface is sealed to enhance corrosion resistance. This can be done through boiling water or steam processes, among others, locking in the protective oxide layer.
The hard anodising process is essential for producing aluminium components that withstand extreme conditions, ensuring longevity and performance in various applications.
Chemical Mechanisms Involved
Understanding the chemical mechanisms involved in hard anodising aluminium is critical for grasping how this process enhances the material's characteristics. The hard anodising process alters the surface of aluminium through controlled electrochemical reactions, which lead to the formation of an anodic layer. This layer provides significant improvements in properties such as corrosion resistance and wear resistance, crucial for the durability and longevity of aluminium components. The effectiveness of hard anodising as a surface treatment is largely attributable to these underlying chemical mechanisms.
Oxidation of Aluminium
The oxidation of aluminium is the first step in the anodising process. When aluminium is exposed to an electrolytic solution, typically sulfuric acid, an electrical potential is applied. This causes oxidation to occur at the anode, which is the aluminium workpiece. During this reaction, aluminium atoms lose electrons and convert into aluminium ions, allowing them to combine with oxygen from the electrolyte. This step is essential because it initiates the formation of the oxide layer.
The relationship between the electrical current density and the rate of oxidation is significant. Higher current densities facilitate a faster oxidation rate, which contributes to thicker oxide layers. However, increased current density can also lead to heating effects that may compromise the quality of the anodic layer. Therefore, careful control of the process parameters is required.
Formation of the Anodic Layer
The formation of the anodic layer is the second key element in the hard anodising of aluminium. Following oxidation, the aluminium ions that have formed react with oxygen to create aluminium oxide. This process results in a porous oxide layer that forms over the surface of the aluminium substrate. The thickness of this anodic layer can vary depending on the process conditions, such as time, temperature, and current density.
A notable feature of this anodic layer is its microporous structure, which can be further enhanced by subsequent sealing processes. Sealing involves the hydration of the formed oxide, resulting in the closure of pores and improvement in corrosion resistance. This layer acts as a protective barrier against environmental factors such as humidity and corrosive substances.
In summary, the chemical mechanisms involved in hard anodising are crucial for enhancing the surface properties of aluminium. The controlled oxidation gives rise to a durable anodic layer that offers significant protection and functionality for various applications. Understanding these mechanisms can lead to better process optimization and improved material performance.
Properties of Hard Anodised Aluminium
The properties of hard anodised aluminium are critical for understanding its advantages and various applications. Hard anodising enhances the natural qualities of aluminium, making it suitable for demanding environments. This article illustrates several key properties that stand out and makes them important for different industries—especially where durability, strength, and reliability are paramount.
Enhanced Wear Resistance
Hard anodised aluminium exhibits remarkable wear resistance. The anodic layer formed during the process is considerably thicker compared to conventional anodised layers. This thickness results in a hard surface, effectively preventing damage from friction and abrasion. As a result, components made from hard anodised aluminium have an extended lifespan, which can significantly reduce maintenance costs.
Key benefits of enhanced wear resistance include:
- Increased durability: Hard anodised surfaces can withstand harsh operating conditions, making them ideal for mechanical parts.
- Lower friction: The smooth surface reduces friction in many applications, which is beneficial in moving parts.
- Cost effectiveness: While the initial investment may be higher, the reduced wear translates into longer service life and fewer replacements.
"The superior wear resistance of hard anodised aluminium opens doors to innovative applications across various fields, from aerospace to consumer goods."
Corrosion Resistance
Corrosion resistance is another significant property of hard anodised aluminium that sets it apart from untreated aluminium. The anodic layer serves as a protective barrier against environmental factors such as moisture and chemicals. This is particularly valuable in industries where equipment is subject to harsh environments.
The key aspects of corrosion resistance include:
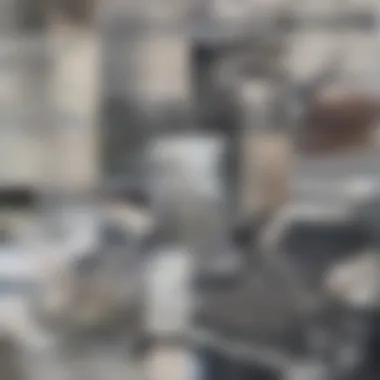
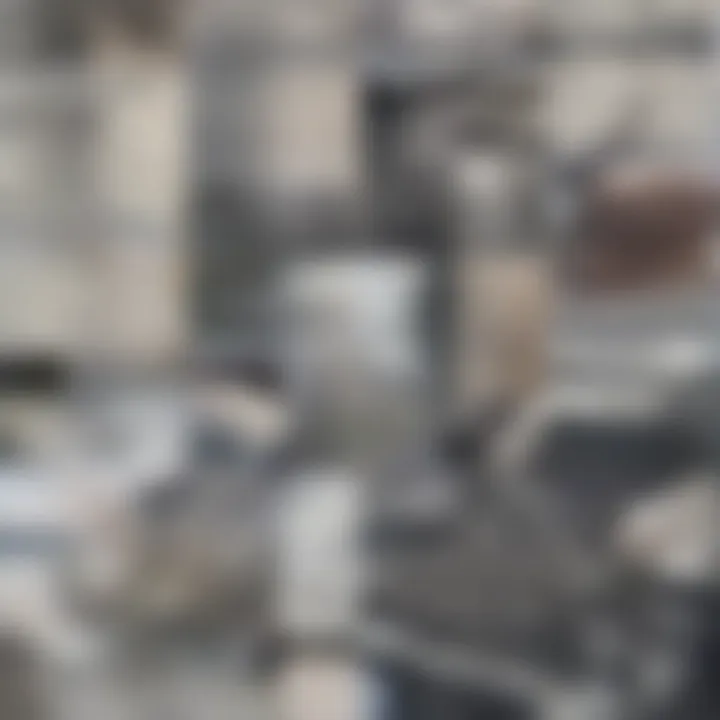
- Protection from oxidation: The hard anodised layer effectively limits further oxidation of the aluminium.
- Reduced maintenance: The surface does not require frequent protective coatings, simplifying upkeep.
- Suitability for varied applications: This property makes hard anodised aluminium useful in marine, chemical, and construction industries, where exposure to corrosive agents is common.
Thermal and Electrical Insulation
Hard anodised aluminium also provides notable thermal and electrical insulation properties. The anodic layer acts as an insulator, reducing heat transfer and limiting electrical conductivity. This characteristic is crucial in applications where temperature control and electrical isolation are necessary.
Some relevant points about insulation include:
- Thermal control: This property is valuable in heat-sensitive applications, ensuring that components do not overheat.
- Electrical safety: It provides a shield against electrical currents, which helps in protecting sensitive equipment.
- Design flexibility: The insulation allows for more innovative designs, where mixed materials can be used without the risks associated with electrical conduction.
Applications of Hard Anodising
Hard anodising of aluminium plays a crucial role in various industries due to its exceptional properties. This process enhances aluminium products through increased wear and corrosion resistance, making them suitable for demanding applications. Understanding these applications offers insight into the significance of hard anodising in today’s manufacturing landscape.
Aerospace Industry
The aerospace industry is one of the foremost sectors to utilize hard anodised aluminium. Components like aircraft frames, engine parts, and landing gear often undergo this treatment. The primary advantage here is the weight-to-strength ratio it achieves. Hard anodised aluminium is lightweight yet incredibly strong, crucial for aerospace applications, where excess weight can reduce fuel efficiency and performance.
Furthermore, the corrosion resistance of hard anodised surfaces is critical in this industry. Aircraft are continually exposed to harsh environmental conditions, such as moisture, salt, and temperature extremes. Protecting metal surfaces from these elements is vital to ensure safety and functionality.
In summary, using hard anodised aluminium helps in achieving a longer lifespan of aircraft components, reduced maintenance costs, and improved safety standards.
Automotive Sector
In the automotive sector, hard anodising is utilized mainly for lightweight parts like wheels, trim, and engine components. Here, durability becomes a significant factor. The automotive industry faces numerous wear challenges, from high-speed conditions to continuous exposure to chemicals. Hard anodised finishes provide a tough exterior resistant to scratches and chemicals, thus extending the lifespan of car parts.
Moreover, the aesthetic appeal is enhanced through hard anodising. Many automotive manufacturers prefer this surface treatment as it can produce various colors and finishes, giving vehicles a modern and appealing look. Thus, not only does it serve a protective purpose but also adds value through design considerations.
Consumer Electronics
Hard anodising has found substantial applications in the consumer electronics sector as well. Products such as mobile phones, laptops, and other gadgets often use aluminum as a primary material due to its light weight and strength. The hard anodised finish provides multiple advantages, including improved surface hardness and resistance to wear and tear, which is essential for products exposed to daily use.
Additionally, anodised aluminium can effectively dissipate heat, making it preferred for housing components where overheating is a concern. The insulating properties also prevent electrical interference, which enhances device performance.
An additional aspect is the aesthetic appeal. Hard anodising allows for a variety of colors and finishes, contributing to the sleek, modern design of consumer electronics. Moreover, the increasing need for environmentally friendly products makes hard anodising an advantageous choice, as it can be done without harmful chemicals.
Advantages of Hard Anodising
Hard anodising serves as a critical process in the aluminium treatment industry. It not only enhances the physical and chemical properties of aluminium but also extends its applications across various sectors. This section delves into the specific advantages that make hard anodising a preferred choice for many industries.
Durability Comparison
Hard anodising significantly boosts the durability of aluminium. The anodic layer created during the process is much thicker than standard anodising treatments. This thicker layer provides a high degree of resistance to scratching, abrasion, and wear. In practical terms, this means components treated with hard anodising can endure harsher environments and have a longer operational lifespan compared to untreated aluminium or those processed with conventional anodising methods.
When comparing durability, hard anodised aluminium demonstrates:
- Higher hardness: The hardness of the anodic layer can exceed that of most steel materials, often reaching scores of 60-70 on the Mohs hardness scale.
- Enhanced impact resistance: Structures created with hard anodised aluminium can better withstand impacts and mechanical stresses, making them ideal for industrial uses.
- Resilience against wear: The features of hard anodised aluminium are advantageous in applications with sliding or frictional contact, such as in automotive parts or machinery components.
By mitigatig normal wear and extending performance life, hard anodising stands out as a superior choice for many heavy-duty applications.
Environmental Impact
The environmental impact of hard anodising is an important consideration that cannot be overlooked. Firstly, the process itself is generally more eco-friendly than alternative surface treatment methods. Hard anodising uses sulphuric acid or chromic acid to generate the anodised layer, leading to a minimal ecological footprint when properly managed.
Several points illustrate the environmental benefits of this technique:
- Reduction in toxicity: Modern hard anodising facilities often incorporate closed-loop systems that recycle waste materials and chemicals, limiting toxic emissions and reducing waste.
- Energy efficiency: Advances in technology have led to more energy-efficient processes that lessen carbon output, compared to traditional methods.
- Non-toxic finished product: Hard anodised surfaces do not release harmful substances, making them safe for a variety of environments, including consumer electronics and components used in food processing.
Overall, the favorable environmental profile of hard anodising aligns well with contemporary sustainability goals, making it a sensible option for conscientious manufacturers.
In essence, hard anodising not only enhances durability but also supports environmentally responsible practices. For industries aiming to balance performance with ecological considerations, hard anodising presents a compelling solution.
Challenges in Hard Anodising
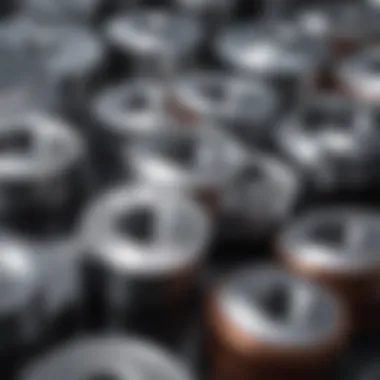
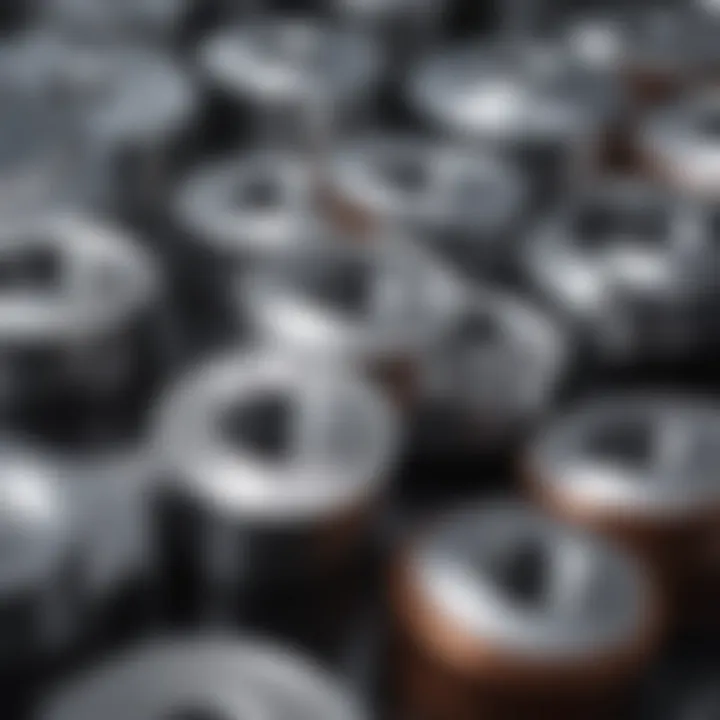
Hard anodising aluminium presents distinct challenges that can affect the quality and overall success of the process. Understanding these challenges is essential for researchers, engineers, and production managers working with anodised materials. Failing to address these issues can lead to defects in the coating, increased costs, and delays in production.
Quality Control Issues
Quality control is crucial in hard anodising aluminium because the process requires precise parameters to achieve the desired coating characteristics. Variations in temperature, voltage, and time can lead to inconsistencies in the anodic layer, affecting properties such as hardness, thickness, and corrosion resistance.
- Monitoring Critical Parameters: It is vital to continually monitor the parameters during the anodising process. Automated systems that track voltage and solution composition help to maintain consistency.
- Inspection Techniques: Different inspection techniques, such as surface roughness measurements and thickness assessments, can help identify defects early.
- Documentation: Proper documentation of the anodising parameters and outcomes ensures traceability and accountability. This allows companies to compare batches and spot potential issues.
"Effective quality control during hard anodising not only enhances the performance of the final product but also reduces the risk of costly reworks."
Cost Considerations
Cost considerations play a significant role in the decision to implement hard anodising in production processes. The process can incur high operational costs due to several factors:
- Initial Investment: Setting up anodising facilities requires considerable investment in equipment. The machinery must be specifically designed to handle the electrochemical processes effectively.
- Chemical Costs: The chemicals used in the anodising bath have associated costs. They must be replaced regularly to ensure the quality of the anodised layer.
- Maintenance Expenses: Regular maintenance of equipment is essential to prevent downtime, but it adds to the overall cost. In addition, any failures caused by equipment issues can lead to wastage of materials.
Recent Innovations in Hard Anodising
Recent innovations in hard anodising aluminium are reshaping the landscape of this vital surface treatment. As industries evolve, the demand for advanced performance characteristics necessitates ongoing development. Innovations in hard anodising not only enhance the durability and versatility of aluminium but also open new avenues for application, making it increasingly relevant in modern engineering and manufacturing processes.
Technological Advancements
Technological advancements in hard anodising have led to more efficient and effective processes. One notable development is the use of high-voltage anodising, which produces a thicker anodic layer at a faster rate. This method enables enhanced wear resistance and improves thermal stability under extreme conditions.
Moreover, automation in the anodising process has gained traction. Automated systems ensure consistent quality and reduce human error. Programmable logic controllers and advanced monitoring systems help maintain precise parameters, leading to uniform anodised surfaces. Techniques like ultrasonic cleaning before anodising further contribute to the quality of the final product by removing contaminants that can interfere with the anodising process.
"The integration of automation and monitoring technologies has revolutionized the hard anodising process, enhancing both efficiency and product quality."
Sustainability Efforts
Sustainability is becoming a significant consideration in the hard anodising industry. Innovations focus not only on performance but also on reducing environmental impact. Recent developments include the exploration of eco-friendly electrolytes, which replace conventional acids, minimizing hazardous waste. Additionally, advancements in recycling techniques for used anodising baths are contributing to resource conservation.
Another sustainability effort includes improving energy efficiency during the anodising process. Electric current control systems are now commonly employed to maximize efficacy while conserving energy. Companies are also investigating the use of renewable energy sources, which reduces their carbon footprint.
In summary, the current trajectory of hard anodising innovations reflects a commitment to enhancing performance while addressing environmental concerns. These advancements ensure that hard anodising remains a sought-after process for countless applications in diverse industries.
Future Outlook for Hard Anodising
The future of hard anodising aluminium is an essential subject worth exploring in detail. As industries continue to demand materials with higher durability and efficiency, the role of hard anodising will only become more significant. Innovations in technology, shifts in market trends, and the growing emphasis on sustainability are reshaping how this process is viewed and implemented.
Market Trends
Recent tendencies indicate a robust growth in the hard anodising market. This growth can be attributed to several factors, including:
- Increased Demand: Various sectors such as aerospace, automotive, and consumer electronics are expanding rapidly. Each sector requires more sophisticated materials for parts and components.
- Focus on Performance: Companies place greater value on the performance characteristics of materials. Hard anodised aluminium is particularly noted for its resistance to wear and corrosion, which makes it an attractive option.
- Regulatory Standards: Stricter regulations on material resistance and weight laws drive the adoption of advanced treatment processes like hard anodising. As manufacturers comply with these standards, hard anodising becomes a preferred choice.
This trend is likely to continue, as the demand for lightweight yet robust materials ascends. Manufacturers are expected to advance their processes and refine their techniques. The integration of automation and AI in anodising lines is also a notable trend seen in the industry.
Emerging Applications
The applications of hard anodising are no longer confined to traditional industries. Some emerging applications include:
- Medical Devices: The need for biocompatibility and durability is setting a new standard in the medical field. Hard anodised components are being utilized in surgical instruments and implants.
- Renewable Energy Systems: Solar panel frames and wind turbine components increasingly employ hard anodised aluminium due to its lightweight properties and resistance to environmental degradation.
- Telecommunications: With the rise of 5G technology, hard anodised materials are used in antenna infrastructure for their durability and thermal management capabilities.
The diversity of applications highlights the material's versatility and potential for growth in niche markets.
The End
The conclusion section serves as a critical juncture in this article, summarizing the comprehensive explorations and insights offered throughout various aspects of hard anodising aluminium. Importantly, it consolidates essential themes about not just the technological processes involved, but also the profound implications for industries reliant on durable, high-performance materials.
Summary of Key Points
In reviewing hard anodising aluminium, several key points emerge:
- Definition and Process: Hard anodising is an electrochemical oxidation process that creates a thick layer of oxide on aluminium, enhancing its durability and resistance.
- Properties: The resulting anodised layer exhibits improved wear resistance, corrosion resistance, and excellent thermal and electrical insulating properties.
- Applications: Industries such as aerospace, automotive, and consumer electronics benefit from hard anodised components due to their longevity and performance efficiency.
- Advantages vs Challenges: While this technique provides significant durability and environmental benefits, obstacles such as quality control and associated costs must be strategically managed.
- Future Trends: Recent innovations point towards enhanced processing technologies and sustainability efforts, shaping the future landscape of hard anodising applications.
Final Thoughts
Hard anodised aluminium not only exemplifies superior material characteristics but also reflects the intersection of technology and environmental consciousness within modern manufacturing.
Ultimately, this article should inspire deeper inquiry and encourage further exploration into the fascinating world of aluminium anodising for researchers and practitioners who aim to leverage its benefits.