Understanding Heat Exchanger Bellows Expansion Joints
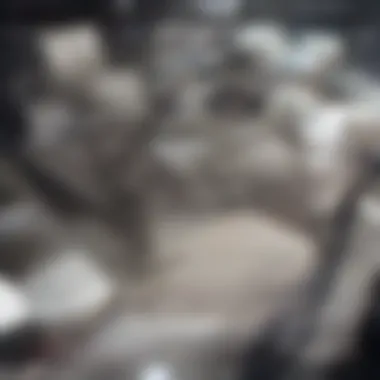
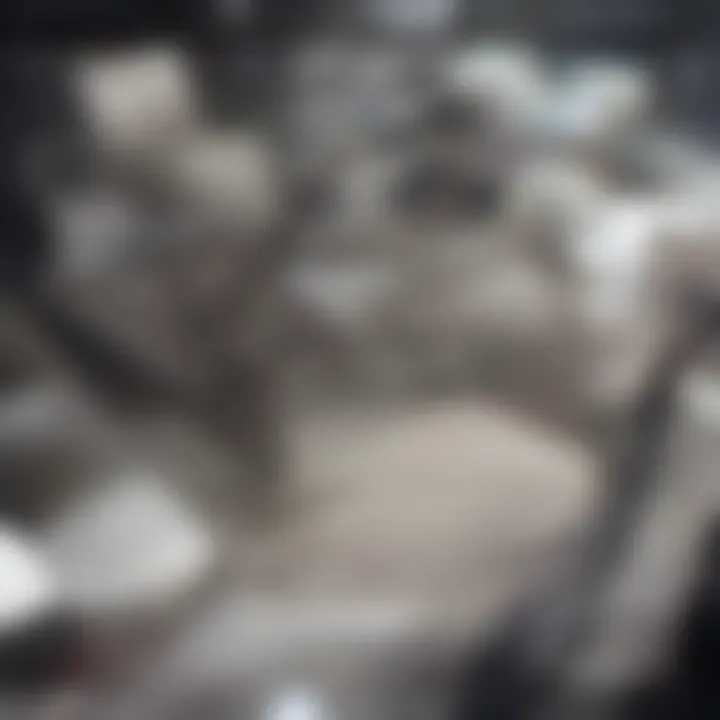
Intro
Heat exchanger bellows expansion joints play a significant role in thermal management systems, allowing for flexibility and accommodating thermal expansion. These components are crucial for maintaining the integrity of thermal systems by mitigating stresses caused by temperature variations and mechanical movements. Understanding the importance of bellows expansion joints is essential for engineers and operators who are involved in the design, selection, and maintenance of thermal systems.
Key Concepts and Terminology
Definition of Key Terms
- Bellows Expansion Joint: A flexible component designed to absorb thermal expansions and contractions within piping systems.
- Thermal Expansion: The increase in length, area, and volume of materials due to temperature increase.
- Pressure Drop: The loss of pressure as fluid passes through a system, often influenced by friction and changes in flow direction.
Concepts Explored in the Article
In this article, we explore various aspects of heat exchanger bellows expansion joints. The main topics include:
- The design principles that govern the development of these joints.
- An examination of materials used in manufacturing expansion joints and their properties.
- Operational characteristics and how they affect system performance.
- Applications across different industries such as oil and gas, power generation, and HVAC.
Findings and Discussion
Main Findings
Heat exchanger bellows expansion joints are vital for ensuring system longevity and efficiency. Key findings from the analysis include:
- Flexibility: Allows for movement in pipelines without damaging connections.
- Material Selection: Different materials like stainless steel and rubber offer various benefits depending on system requirements.
- Maintenance Considerations: Regular inspections help identify wear and prevent system failures.
โProper understanding and maintenance of bellows expansion joints can prevent costly downtimes and repairs.โ
Potential Areas for Future Research
Future inquiries could focus on:
- The development of advanced materials that reduce fatigue and enhance lifespan.
- Improved design methodologies that allow for easier integration into existing systems.
- Impact of innovative manufacturing techniques on performance and reliability.
By addressing these aspects, professionals can enhance their knowledge of heat exchanger bellows expansion joints, leading to improved operational efficiency and reliability in thermal systems.
Prolusion to Heat Exchanger Bellows Expansion Joints
Heat exchanger bellows expansion joints play a pivotal role in the functioning of thermal systems. These components are designed to manage the physical stresses that occur due to temperature changes and pressure variations within heat exchanger systems. Understanding the mechanics of these joints is crucial for engineers, operators, and anyone involved in thermal management.
Definition and Purpose
Heat exchanger bellows expansion joints are flexible connectors that accommodate movements in piping systems. Their primary purpose is to absorb thermal expansion and contraction, as well as to mitigate vibrations and misalignments. This flexibility allows the system to maintain integrity without compromising safety or functionality.
The design of bellows expansion joints involves a series of convoluted metal or other material layers. This design allows for multidirectional movement. This makes them suitable for various applications, including power plants and chemical processing facilities.
Importance in Thermal Systems
The significance of bellows expansion joints in thermal systems cannot be overstated. They preserve the overall structural integrity of the system by absorbing significant stresses that arise from heat and pressure variations. Without these joints, systems would be prone to leakage, cracking, and eventual failure, leading to costly downtime and repairs.
"Bellows expansion joints are essential to the longevity and reliability of heat exchangers and related thermal systems. Their ability to accommodate movement is a crucial factor in system design."
Considerations such as the type of materials used, the design geometry, and installation practices are critical for the effectiveness of these joints. Properly selected and installed bellows expansion joints can enhance the lifecycle of thermal systems, contributing to efficiency and operational reliability.
In summary, a comprehensive understanding of heat exchanger bellows expansion joints is vital for achieving optimal performance in thermal applications. Their role in managing movement and stress makes them indispensable in maintaining the functionality and safety of these systems.
Fundamentals of Expansion Joints
Expansion joints play a pivotal role in thermal management systems, particularly in heat exchangers. Understanding their fundamentals is crucial for engineers and operators. They allow for movement that occurs due to thermal expansion and contraction, thereby maintaining system integrity and functionality. This section covers the basic principles and main types of expansion joints, setting the stage for deeper exploration in subsequent sections.
Basic Principles of Operation
Expansion joints are designed to accommodate movements caused by temperature changes. When heated, materials inside a thermal system tend to expand. Conversely, cooling causes contraction. Expansion joints handle such stresses by allowing the necessary movement without causing damage to other system components.
Their design includes features that permit bending, compression, and extension. This flexibility is key as it prevents excessive forces that can lead to leaks or failures. The joints also help to absorb vibrations and misalignment that may occur in the system. The proper sizing and material choice are critical to ensure reliable operation over the equipmentโs life.
Types of Expansion Joints
Expansion joints come in various forms, each serving distinct functionalities and application needs. The three main types of expansion joints are metallic, fabric, and rubber.
Metallic Expansion Joints
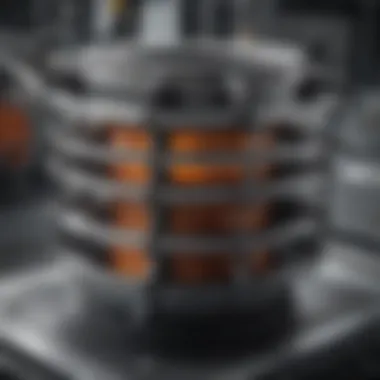
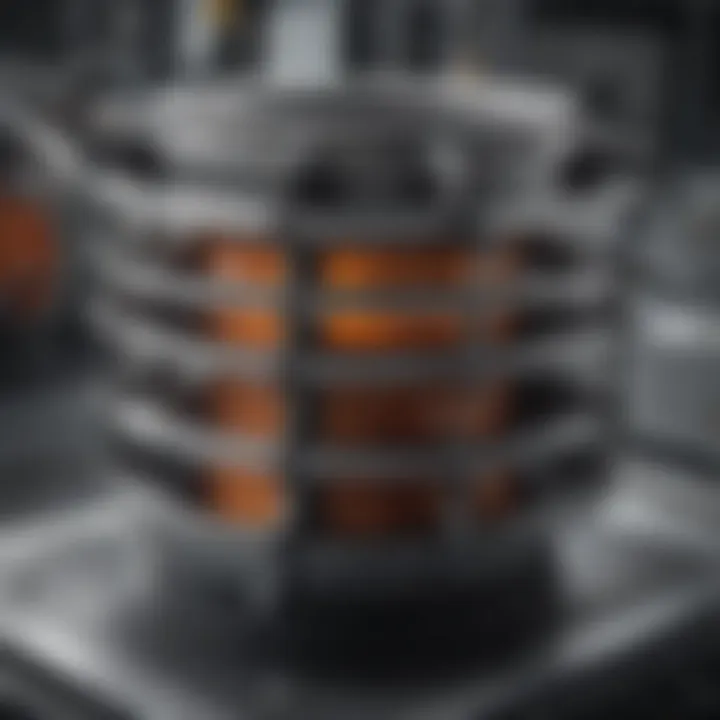
Metallic expansion joints are often the first choice in applications requiring strength and durability. They are built from metals such as stainless steel and alloys that resist corrosion. A key characteristic is their ability to withstand high pressures and temperatures, making them suitable for demanding environments.
Metallic joints can handle significant movements, and their design usually features convolutions that enhance flexibility. A unique advantage is their excellent fatigue resistance, which is vital in dynamic conditions. However, their rigidity can make installation complexities arise, particularly in tight spaces.
Fabric Expansion Joints
Fabric expansion joints provide a lighter alternative to metallic options. These joints are usually made from woven fiberglass or other heat-resistant materials. Their key characteristic is flexibility, allowing for larger movements and thermal deformations. This makes them beneficial in situations where space is limited.
They are particularly popular in industrial applications where chemical exposure is a concern. While they may not sustain extreme pressures, their ability to absorb vibrations and noise is advantageous in many settings. However, they require careful inspection to ensure integrity over time as they may degrade under harsh conditions.
Rubber Expansion Joints
Rubber expansion joints offer significant flexibility and ease of installation. Typically made from synthetic or natural rubber, they are excellent for absorbing shock and vibrations. A notable characteristic is their ability to accommodate misalignments, which is a common issue in thermal systems.
These joints are cost-effective, and their lightweight nature simplifies handling and installation. However, they have limitations in terms of temperature ranges and chemical resistance compared to metallic options. Depending on the application, their lifespan may be shorter than that of metal or fabric joints.
Each type of expansion joint has its specific functions and benefits. Choosing the right one ensures effective thermal management, contributing to the overall efficiency and reliability of thermal systems.
"Proper selection and installation of expansion joints can prevent costly downtime and enhance the longevity of thermal systems."
Understanding these fundamentals equips professionals with the knowledge needed to make informed decisions about expansion joint applications in various industries.
Design Considerations
Design considerations in heat exchanger bellows expansion joints play a pivotal role in ensuring optimal performance and longevity of thermal systems. Selecting the right materials and geometry impacts not just the operational efficiency but also the safety and reliability of the system. Various aspects such as material selection and geometric sizing must be thoroughly evaluated to align with specific operational conditions.
Material Selection
Material selection is critical when designing expansion joints. The chosen materials must endure harsh environmental conditions, including temperature variations, corrosive substances, and mechanical stresses.
Corrosion Resistance
Corrosion resistance is crucial for ensuring durability in heat exchanger bellows expansion joints. The capability of a material to resist corrosion extends its lifespan. Common materials include stainless steel and specific alloys that withstand oxidation and degradation. This characteristic is beneficial because it reduces maintenance costs and downtime due to failures caused by corrosion. Furthermore, corrosion-resistant materials can perform effectively under varied temperatures, showcasing versatility. A potential disadvantage might be the higher initial cost for premium materials, but the long-term benefits often justify this investment.
Thermal Conductivity
Thermal conductivity affects how heat is transferred through the expansion joints. Choosing materials with favorable thermal conductivity ensures efficient thermal management in the system. For instance, metals typically provide higher thermal conductivity compared to other materials. This property is beneficial because it can prevent overheating and promote effective heat exchange. However, one must consider that excessive thermal conductivity can lead to thermal fatigue if the material does not have complementary mechanical resilience. Thus, striking the right balance is essential.
Mechanical Properties
Mechanical properties such as tensile strength and elasticity are vital for the operational capabilities of expansion joints. These properties dictate how the material will respond to stress, impact, and strain. High tensile strength is particularly beneficial, as it allows for greater flexibility while preventing deformation. Unique features like elongation capacity are also significant, as they ensure the joint can accommodate movement without failure. However, materials with very high strength may become brittle at low temperatures, posing a risk in certain environments.
Geometry and Sizing
Proper geometry and sizing of the expansion joints are critical to accommodate operational factors like movement, temperature fluctuations, and pressure differentials. The right configuration ensures that the joints can effectively absorb these changes without compromising the integrity of the system.
Bellows Design
Bellows design involves creating a flexible component capable of managing thermal expansion and contraction. A well-designed bellow can significantly enhance a system's ability to cope with movements due to temperature changes. Key characteristics include the number of convolutions and the material thickness. A greater number of convolutions can absorb more significant movements, providing more flexibility. Yet, too many convolutions can lead to increased pressure drop and decreased efficiency. Therefore, ideal designs must balance movement accommodation with flow performance.
Length of Expansion Joint
The length of an expansion joint is also significant. Longer joints can better accommodate greater movements and thermal changes, providing versatility in design. However, excessively long joints can amplify pressure drops and introduce complexities in installation. Finding an appropriate length that meets operational demands while maintaining efficiency is essential for optimal performance.
Diameter Factors
Diameter factors directly influence the flow rate and pressure characteristics of the system. An appropriate diameter ensures there is sufficient flow area to minimize restriction while still providing the necessary flexibility. Wide diameters facilitate better flow rates. However, over-sizing may lead to mechanical instability and increased risk of failure during operation. Proper calculations and system analysis should guide the diameter selection.
In summary, design considerations such as material selection and geometric sizing are essential for effective heat exchanger bellows expansion joints, helping to optimize performance in thermal systems.
Applications in Industry
The role of heat exchanger bellows expansion joints is vital across various industries. Their functionality affects system efficiency, safety, and performance. This section explores the significant application areas of power generation, chemical processing, and HVAC systems. Understanding these applications helps professionals recognize the importance of proper design and selection of expansion joints to meet industry needs.
Power Generation
In power generation, maintaining efficiency and reliability is crucial. Heat exchanger bellows expansion joints assist in managing thermal expansion and contraction due to significant temperature changes. They help in connecting various sections of piping systems, allowing for relative movement without compromising the integrity of the system. These joints mitigate stress, thereby preventing failures that can lead to costly outages.
Key factors include:
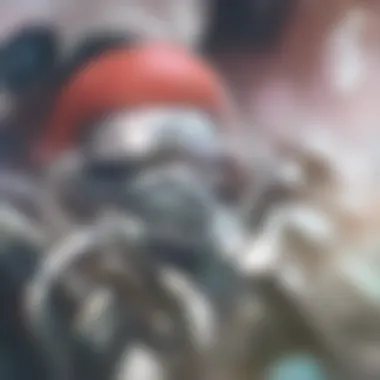
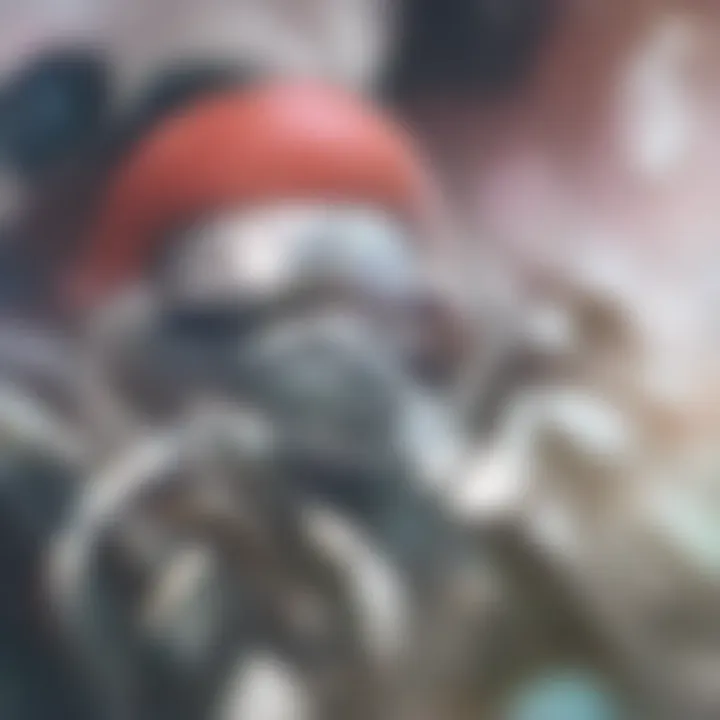
- Flexibility: They permit necessary movements, thus preventing undue stress on adjoining components.
- Durability: Made from strong materials, they withstand harsh conditions, including extreme temperatures and pressure variations.
Chemical Processing
Heat exchanger bellows expansion joints are essential in chemical processing plants. These joints handle the intricate needs of dynamic systems where thermal cycling occurs frequently. They provide safety by mitigating the risk of leaks or ruptures, which can have catastrophic consequences, especially when dealing with hazardous materials.
Elements to consider:
- Chemical Compatibility: Material choice is critical as it must resist corrosive substances to maintain functionality.
- Pressure Ratings: The joints should comply with pressure requirements relevant to specific processes, ensuring operational safety and efficiency.
HVAC Systems
In HVAC systems, bellows expansion joints contribute significantly to system longevity and performance. They accommodate movement due to thermal expansion and contraction in ducts, piping, and other HVAC components. This function enhances energy efficiency and reduces maintenance costs.
Important aspects include:
- Noise Reduction: They help in absorbing vibrations which contributes to a quieter environment.
- Leak Prevention: Properly designed expansion joints maintain the integrity of HVAC systems, preventing air leaks and optimizing energy use.
The successful integration of heat exchanger bellows expansion joints into various applications will lead to more efficient and safer industrial processes.
Understanding these applications provides valuable insights for engineers and decision-makers. It enables informed choices in selecting suitable products that enhance operational integrity across different sectors.
Operational Challenges
Understanding the operational challenges faced by heat exchanger bellows expansion joints is crucial for maintaining system integrity and ensuring efficient performance in thermal systems. These challenges can lead to failures or reduced efficiency, thus impacting the overall operational capabilities. Each of the challenges outlined here requires careful consideration, proactive management, and well-planned maintenance practices to mitigate risks effectively.
Thermal Stress and Fatigue
Thermal stress and fatigue in expansion joints result from repetitive heating and cooling cycles. These cycles induce cyclic loading which can cause material fatigue over time. It's essential to monitor these stresses to prevent failure of the bellows.
Factors contributing to thermal stress include:
- Temperature Fluctuations: Sudden changes in temperature can create thermal gradients that adversely affect bellows performance.
- Material Properties: The choice of materials significantly influences heat tolerance and fatigue resistance. Materials need to have adequate strength and flexibility.
- Operating Conditions: Higher pressure and temperature increase thermal stress, thereby affecting the lifecycle of the expansion joints.
Preventive measures include regular inspection and utilizing thermal compensations designs when creating the joint. Awareness of potential fatigue points can greatly enhance durability.
Pressure Variations
Pressure variations affect the operational stability of heat exchanger bellows expansion joints. These joints must withstand both high and low pressures, making them susceptible to deformation or even rupture under extreme conditions.
Key considerations include:
- Pressure Surges: Unexpected surges or spikes can lead to immediate failure if the expansion joint is not rated for such conditions.
- Vacuum Conditions: Effective design is crucial when the systems operate under vacuum, as bellows need to handle external atmospheric pressure.
- Design Constraints: Ensuring proper sizing and selecting the right type of expansion joint are vital to accommodate pressure variations effectively.
Regular pressure assessments and adaptive designs can help in minimizing risks related to pressure fluctuations.
Misalignment Issues
Misalignment in piping systems can lead to uneven loading on expansion joints, compromising their integrity and leading to failures. Misalignment can stem from various issues, including:
- Installation Errors: If joint positions are not properly aligned during installation, premature failures can result.
- Thermal Expansion: Differential thermal expansion between connected pipes may cause misalignments.
- Foundation Settlements: A foundation that shifts or settles over time can influence the alignment of attached systems.
To counteract misalignment issues, it is advisable to:
- Implement alignment checks during installation and maintenance.
- Utilize flexible connectors that can absorb minor misalignments without damaging the joint.
- Monitor for signs of misalignment through regular system evaluations.
A proactive approach to managing these operational challenges can enhance the lifecycle and performance of heat exchanger bellows expansion joints, ensuring that systems function efficiently while minimizing the risks of failure.
Maintenance Practices
Maintenance practices for heat exchanger bellows expansion joints are crucial for ensuring their proper function and longevity. Regular upkeep can greatly enhance system performance and reduce the risk of unforeseen failures. These practices focus on both monitoring the condition of the joints and addressing potential issues before they escalate.
Inspection Procedures
Inspection is a systematic approach to evaluate the integrity of bellows expansion joints. This task should be conducted at predetermined intervals, set according to the operating environment and service conditions of the thermal system. The following key aspects should be included in an inspection checklist:
- Visual Examination: Inspect for steel-on-steel contact, unusual wear, or damage. Look for signs of corrosion or leaks, which may indicate failure points.
- Dimensional Checks: Measure the bellows for changes in size or shape. Any distortion can affect performance, so deviations must be documented.
- Functional Testing: Assess the performace under operational conditions. This can include monitoring expansion and contraction behaviors during normal cycles.
- Documentation: Keep systematic records of all inspections, including any noted issues and actions taken. This is valuable for future maintenance planning.
With maintenance records, professionals can identify patterns in wear and address recurring issues with the design or material selections.
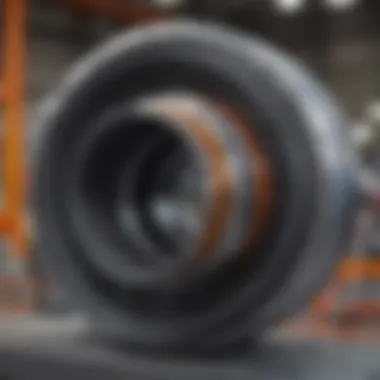
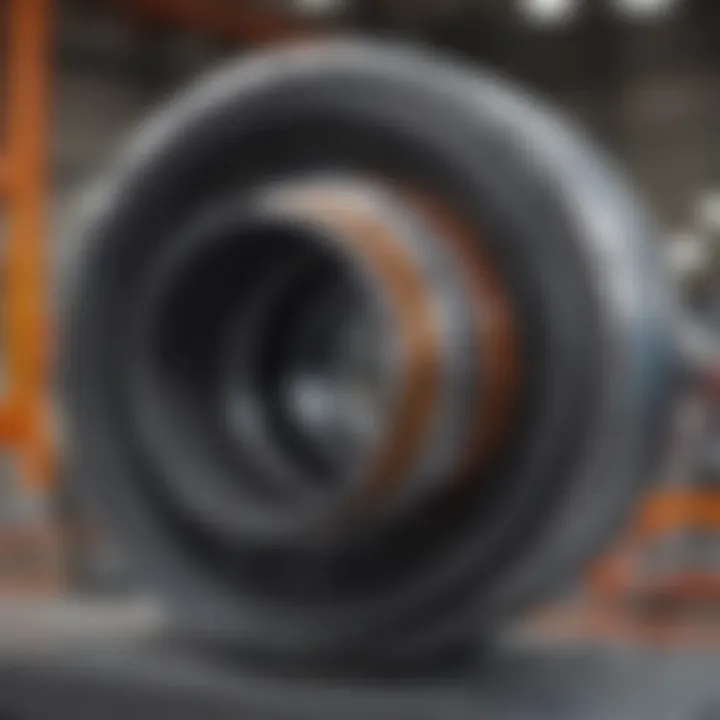
Common Failures and Remedies
Understanding potential failure modes of bellows expansion joints is vital for effective maintenance. Common failures include:
- Fatigue Cracking: Often a result of thermal cycling. Regular inspections help identify early signs before they develop further.
- Leakage: This can occur due to improper fit, material degradation, or even thermal expansion exceeding limits. Monitoring for leaks should be performed frequently.
- Misalignment: Can arise due to thermal expansion or installation errors. Ensure proper alignment during installation and regular checks to maintain optimal performance.
Remedies for these issues involve:
- Replacing worn components with higher durability materials or newer designs that mitigate stress.
- Adjusting installation practices to ensure proper alignment. This includes tightening fittings and using appropriate gaskets and seals for added security.
- Implementing upgrades with advanced technology that may include IoT monitoring solutions for real-time assessment and data collection on joint performance.
In essence, proactive maintenance not only reduces costs but also enhances the reliability of thermal management systems.
By integrating these practices into the operational routine, significant benefits arise, such as improved efficiency and reduced downtime, making it essential for engineers and operators.
Future Trends in Expansion Joint Technology
The field of heat exchanger bellows expansion joints is constantly evolving. As technology advances, so do the materials and methodologies used in their design and implementation. This section will delve into two significant trends shaping the future of expansion joint technology: advancements in materials and the integration with Internet of Things (IoT) systems. Understanding these trends is crucial for engineers, designers, and maintenance professionals, as they carry implications for efficiency, reliability, and safety in thermal management systems.
Advancements in Materials
The materials used in expansion joints greatly influence their performance and longevity. Recent advancements focus on high-performance alloys and composites that offer enhanced resistance to thermal stress, corrosion, and fatigue.
- High-Performance Alloys: Alloys like Inconel and Hastelloy are becoming more common due to their ability to withstand extreme temperatures and corrosive environments. These materials extend the life cycle of the expansion joints, reducing the need for frequent replacements.
- Composite Materials: Innovations in composite manufacturing have led to the production of materials that are both lightweight and strong. These composites can provide significant advantages in reducing system weight while maintaining structural integrity.
- Coatings: Specialized coatings are being developed to enhance the surface properties of expansion joints. These coatings can provide additional protection against corrosion and wear, helping to further prolong their life.
With these advancements, the design of expansion joints is becoming more adaptive to the specific requirements of individual applications. This customization is essential for maximizing performance and ensuring reliability in various operating conditions.
Integration with IoT
The integration of IoT technology with heat exchanger bellows expansion joints marks a pivotal shift in their monitoring and maintenance. As industries increasingly adopt smart technologies, the ability to connect expansion joints to IoT systems opens new avenues for operational efficiency.
- Real-Time Monitoring: IoT devices can provide real-time data on operational conditions, including pressure changes, temperature variations, and vibrational analyses. This data is vital for predicting potential failures or maintenance needs, allowing for proactive measures.
- Predictive Maintenance: With data analytics, maintenance schedules can be optimized based on actual operating conditions rather than routine time intervals. This approach reduces downtime and can lead to significant savings in maintenance costs.
- Enhanced Safety: IoT integration can enhance safety protocols by providing alerts for abnormal conditions. Early detection of issues can prevent catastrophic failures, thereby safeguarding personnel and equipment.
By embracing IoT technologies, the realm of expansion joint management is evolving towards a data-driven future. This trend is not only beneficial but essential in the context of increasing thermal system complexities and operational demands.
"Understanding the importance of material advancements and IoT integration is key to developing robust thermal systems. These technologies will significantly impact the efficiency and reliability of future systems."
Regulatory Standards and Compliance
Regulatory standards and compliance play a crucial role in the functionality and reliability of heat exchanger bellows expansion joints. These standards ensure that the components meet safety, performance, and design specifications. Compliance with regulations helps manufacturers and engineers create systems that not only operate efficiently but also protect workers and the environment. Adhering to these standards can minimize risks associated with mechanical failures, leaks, and other operational hazards.
Industry Regulations Overview
In the realm of industrial applications, various regulations oversee the design and use of expansion joints. These may include standards set by organizations such as the American Society of Mechanical Engineers (ASME) and the American National Standards Institute (ANSI). Key regulations often pertain to:
- Material Standards: Specify the types of materials that can be used in manufacturing expansion joints, ensuring durability and resistance.
- Design Criteria: Outline acceptable design practices that maximize performance while ensuring safety under different operational conditions.
- Testing Protocols: Define testing methods to verify the integrity and functionality of the expansion joints before installation.
By following these guidelines, engineers can ensure that their systems are compliant, which aids in preventing potential liabilities and fostering trust in product quality.
Safety Considerations
Safety is a significant aspect when discussing heat exchanger bellows expansion joints. Proper adherence to regulatory standards enhances the safety of these components in thermal systems. Critical safety considerations include:
- Regular Inspection: Ensuring that expansion joints are routinely checked can detect wear or fatigue early. This preventative measure avoids failures that could lead to hazardous situations.
- Pressure Limits: Operating within the specified pressure limits is essential. Exceeding these limits can result in catastrophic failure.
- Leak Prevention: Compliance with sealing standards is necessary to prevent leaks of hazardous fluids that can pose risks to operators and the environment.
"Understanding and implementing safety protocols within regulatory frameworks is vital for maintaining system integrity and worker safety."
In summary, adhering to regulatory standards and safety considerations not only enhances the reliability of heat exchanger bellows expansion joints but also protects human lives and the environment. These aspects are essential for anyone involved in the selection, design, or maintenance of thermal systems.
Epilogue
The conclusion section plays a pivotal role in summarizing the intricate features and significance of heat exchanger bellows expansion joints. This article has navigated through various aspects of these components, illustrating their critical function in thermal management systems. Understanding these joints not only enhances technical expertise but also underscores their importance in ensuring system reliability and efficiency.
In summary, heat exchanger bellows expansion joints help absorb thermal expansion and contraction, protecting equipment from undue stress and preventing failure. They facilitate smoother operation within challenging industrial environments, contributing to enhanced performance and longevity of systems.
Summary of Key Points
- Definition and Purpose: Heat exchanger bellows expansion joints serve to accommodate movement due to temperature changes, preventing potential damage to thermal systems.
- Material Selection: Choosing the right materials is vital to ensure durability and resistance to environmental factors like corrosion and thermal cycles.
- Applications: These components find use in various industries, including power generation, chemical processing, and HVAC systems, proving their versatility and importance.
- Operational Challenges: Engineers must consider wear from thermal stress, pressure variations, and misalignment issues to maintain system integrity.
- Future Trends: Advancements in materials and integration with IoT technologies open new avenues for monitoring and improving performance in real-time.
The understanding of these key elements not only provides a wrap-up of the topic but also emphasizes ongoing challenges and innovations impacting the future of heat exchanger bellows expansion joints.
The Future of Heat Exchanger Bellows Expansion Joints
The future of heat exchanger bellows expansion joints appears promising, driven by advancements in technology and materials. As industries continue to evolve, there is a growing need for more efficient and reliable thermal management solutions. Engineers and manufacturers are exploring innovative materials that offer superior performance and longevity, addressing issues like corrosion and fatigue.
Furthermore, the integration of IoT technology into maintenance practices is revolutionizing how these systems operate. Sensors can collect critical data regarding stress levels, temperature changes, and overall health of the expansion joints. This data is invaluable, facilitating predictive maintenance strategies that reduce downtime and extend the lifespan of equipment.