Exploring High Temperature Epoxy Adhesives

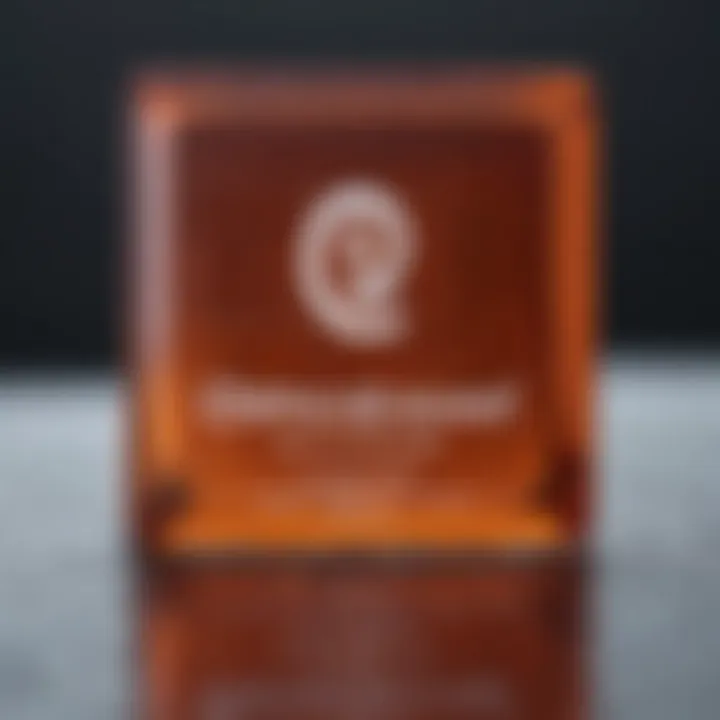
Intro
High temperature epoxy adhesives have gained considerable traction within various industries due to their robust performance under extreme conditions. Whether it’s the aerospace sector, automotive manufacturing, or electronics, these adhesives play a crucial role in ensuring structural integrity and reliability. As we delve into the complexities of these materials, we will unravel their unique characteristics, formulation techniques, and practical applications.
Understanding the science behind high temperature epoxy adhesives is essential for researchers and professionals alike. This discussion will highlight the importance of temperature resistance, chemical composition, and application techniques, ensuring a comprehensive view of why these adhesives are indispensable.
Key Concepts and Terminology
Definition of Key Terms
To navigate the intricate world of epoxy adhesives, it is paramount to familiarize oneself with some key terminology:
- Epoxy: A type of polymer that is made from the reaction of epoxide resins with hardeners.
- Thermal Resistance: The ability of a material to withstand elevated temperatures without losing its adhesive properties.
- Cure Time: The time required for an adhesive to reach its full strength after application.
Concepts Explored in the Article
In this article, we focus on:
- The formulation and composition of high temperature epoxy adhesives.
- Performance metrics that measure their effectiveness under unusual conditions.
- Application techniques that ensure optimal bonding strength and longevity.
- Real-world applications that showcase the utility of these adhesives, where they shine in extreme environments.
Findings and Discussion
Main Findings
Several critical observations emerge from the study of high temperature epoxy adhesives:
- Superior Performance: These adhesives maintain integrity above 200 degrees Celsius, far surpassing standard adhesives.
- Versatility: Suitable for diverse substrates, including metals, plastics, and composites, enhancing their usability.
- Chemical Resistance: Adaptable to corrosive environments, making them valuable in chemical processing sectors.
"The necessity of high temperature epoxy adhesives is underscored by their unparalleled resilience, which opens doors to innovations in manufacturing processes across various sectors."
Potential Areas for Future Research
While significant advancements have been made, there are still many avenues lacking exploration:
- Nanocomposite Enhancements: Investigating how the incorporation of nanomaterials could enhance thermal resistance.
- Bio-based Formulations: Exploring sustainable alternatives to traditional epoxy formulations.
- Long-term Performance Studies: Understanding how environmental factors impact the longevity of these adhesives in practical applications.
This discourse aims to deepen understanding of high temperature epoxy adhesives, guiding professionals and researchers in making informed choices and advancing their work within their respective fields.
Preamble to High Temperature Epoxy Adhesives
Understanding high temperature epoxy adhesives is crucial in a world where materials are constantly facing extreme environmental conditions. These adhesives offer remarkable advantages, particularly in industries where high performance is non-negotiable. From aerospace to automotive and electronic sectors, high temperature epoxies are pivotal in ensuring structural integrity and longevity.
Defining Epoxy Adhesives
At their core, epoxy adhesives are thermosetting polymers created from a chemical reaction between epoxide resins and hardeners. Their formation results in a cross-linked molecular structure that grants them superior rigidity and thermal stability. Unlike traditional adhesives, epoxies withstand higher temperatures, making them indispensable for applications where heat resistance is paramount.
The chemistry behind epoxy formulations is intricate, involving a variety of resins and hardeners that can be tailored to specific needs. This adaptability allows them to bond dissimilar materials effectively. Take, for example, an aerospace component that needs to join metal and composite materials. An appropriate epoxy adhesive can provide the necessary bonding strength without compromising structural performance under load.
Importance of Temperature Resistance
The ability to resist high temperatures is not just a bonus; it's a requirement in many applications. High temperature epoxy adhesives can maintain their bond strength and structural integrity in environments exceeding 150°C or even 200°C. This capability not only extends the life of the components they bond but also ensures reliability under challenging conditions.
"In industries where failure is not an option, choosing the right adhesive can make or break a project."
Consider the automotive sector, where engine parts are subjected to extreme temperatures and pressures. Here, the choice of adhesive is critical—using a high temperature epoxy can prevent delamination or separation, which would otherwise lead to catastrophic failures. Similarly, in electronic applications, adhesives must withstand thermal cycling, preventing components from cracking or losing adhesion over time.
Meeting operational demands often involves understanding the thermal history of materials and their predicted conditions. Hence, high temperature epoxy adhesives are not just about sticking things together; they are engineering solutions designed to meet specific performance objectives.
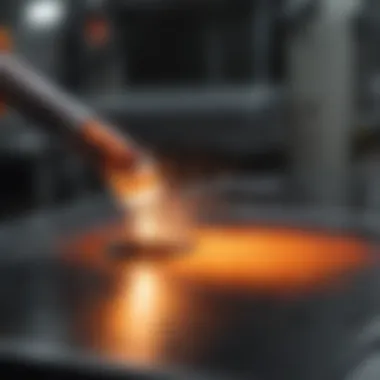
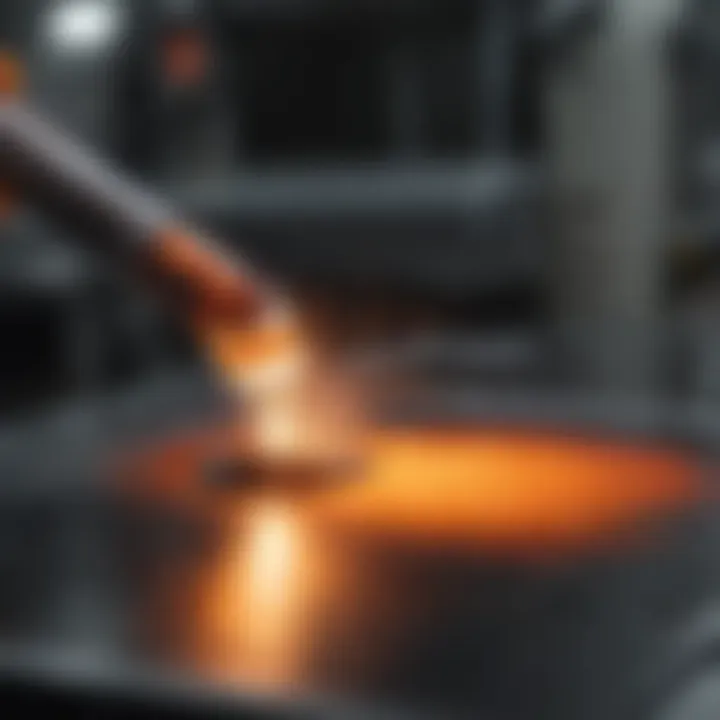
In summary, the importance of high temperature epoxy adhesives extends far beyond their basic defining characteristics. The intricate relationship between their composition and performance impacts a wide array of industries, presenting opportunities for innovation and meeting evolving manufacturing challenges.
Chemical Composition of Epoxy Adhesives
Understanding the chemical composition of epoxy adhesives is essential to grasping their vast applicability and effectiveness in various environments. The unique molecular structure and the materials utilized significantly influence their performance characteristics under extreme conditions. A solid grasp of this topic not only provides insights into why certain formulations excel but also aids in selecting the right adhesive for specific tasks. Therefore, whether you are in a lab conducting intense research or in an industrial setting preparing for critical applications, knowing the nuances of epoxy chemistry can make all the difference.
Base Resin Types
When diving into epoxy adhesives, the base resin is the foundational element that dictates much of its performance and application suitability. There are primarily two types of base resins utilized: bisphenol-A and bisphenol-F. Bisphenol-A resins are traditionally favored, thanks to their resilience and strong adhesion capabilities. They’re like the reliable workhorses of the adhesive world, known for their durability in demanding settings.
- Bisphenol-A: This type often offers high thermal resistance and is usually found in many standard epoxy formulations. These adhesives are suitable for temperature exposure ranging up to approximately 120°C. Plus, they tend to show good chemical resistance, making them versatile across various industries.
- Bisphenol-F: Slightly different in formulation, bisphenol-F resins provide even better heat resistance and lower viscosity, which enhances their application properties. Their ability to withstand temperatures upwards of 150°C makes them a top choice for advanced engineering solutions.
Additionally, specialty resins like novolac and phenolic formulations are engineered for high-temperature applications. These resins often enhance the curing process and overall toughness, though they might require more precise handling due to their unique properties.
Curing Agents and Hardeners
The choice of curing agents or hardeners is another critical aspect in the makeup of epoxy adhesives. These agents interact with the base resin to form a solid structure upon curing. The importance of choosing the correct curing agent cannot be overstated; they greatly influence the adhesive’s performance once set. Here are a few noteworthy agents:
- Aromatic Amine Hardener: Often utilized for their superior bonding capabilities, these hardeners create a tough, heat-resistant bond. They are particularly effective for applications exposed to high thermal loads.
- Aliphatic Amine Hardener: These tend to cure at room temperature and are usually selected for applications requiring good clarity and UV resistance. However, their thermal resistance may not be as robust as their aromatic counterparts.
- Polyamide Hardener: These are notable for their flexibility. They are often deployed in applications where some degree of elongation and ductility is essential, providing balance in environments where materials might expand and contract.A good hardeners selection ensures that the final adhesive will perform optimally under intended conditions, preventing premature failures.
"Choosing the right base resin and curing agent can be as vital as picking the right tool for the job; it’s about not just fitting, but thriving in the task ahead."
In summary, the selection of both base resins and curing agents is crucial. The chemical composition directly correlates to the adhesive’s final properties, including its thermal performance and durability in application. As the field of epoxy adhesives continues to evolve, staying abreast of these chemical intricacies will reward practitioners with better results and optimized formulations.
Thermal Properties of High Temperature Epoxy Adhesives
When it comes to high temperature epoxy adhesives, understanding their thermal properties is not just academic; it’s fundamental for ensuring performance in harsh environments. These adhesives find their place in a multitude of industries where the ability to maintain integrity under elevated temperatures is non-negotiable. The right combination of thermal stability and heat deflection temperature can mean the difference between success and failure in applications ranging from aerospace components to automotive parts.
Thermal Stability
Thermal stability refers to an adhesive’s capability to withstand high temperatures without degrading. This quality is crucial for any application subjected to extreme thermal conditions. For instance, when we talk about thermal stability in high temperature epoxies, we aren't just considering how long they can endure heat; we're also examining their mechanical performance and adhesive strength at elevated temperatures.
When properly formulated, these epoxy adhesives hold up well when temperatures escalate. They typically exhibit a gradual weight loss at high temperatures, which indicates good thermal stability. Poor thermal stability could lead to softening or complete breakdown of the adhesive, causing delamination, loss of mechanical strength, or even complete failure.
Key Points to Consider:
- Decomposition Temperature: The temperature at which an epoxy adhesive begins to chemically break down is crucial for evaluating its performance. It’s essential to choose an adhesive that provides a sufficient margin above the maximum expected operating temperature.
- Non-volatile Residue: A good epoxy should minimize residue that could affect bonding. Hence, understanding how an adhesive behaves under thermal stress helps in selecting materials suitable for high-tech applications.
"Selecting the right high temperature epoxy adhesive is as much about understanding its thermal properties as it is about application. Often, the performance will hinge on the decisions made upfront in material choice."
Heat Deflection Temperature
Heat deflection temperature (HDT) represents the temperature at which a polymer sample deforms under a specified load. It provides insight into how well an epoxy adhesive can endure heat without losing its shape or structural properties. A higher HDT indicates a more robust adhesive that can handle different thermal stresses encountered in service.
Most high temperature epoxy adhesives are engineered to have significantly higher HDTs—usually exceeding the operational needs of standard applications. This characteristic is particularly vital when considering structural bonding applications where mechanical loads are present.
Factors Influencing Heat Deflection Temperature:
- Curing Agents: The choice of curing agents significantly impacts the final properties of the epoxy. Some agents can enhance HDT and overall thermal resistance. A well-thought-out curing selection plays a pivotal role.
- Filler Materials: These materials can improve thermal conductivity and stability when added to epoxies. Certain fillers can provide reinforcement that significantly ups the HDT.
In essence, understanding thermal properties like thermal stability and heat deflection temperature in high temperature epoxy adhesives is paramount. It not only affects product lifespan and reliability but also plays a role in the safety of applications where failure could lead to dire consequences.
Mechanical Properties and Performance Metrics
When it comes to high temperature epoxy adhesives, understanding mechanical properties and performance metrics is not just academic; it’s a necessity for practical applications. The strength and durability of these adhesives under extreme conditions affect the reliability of any structures they’re used in, whether that be in the aerospace, automotive, or electronics sectors. This section delves into two vital aspects of mechanical properties: tensile strength and elongation, along with impact resistance. These metrics are crucial in evaluating how well an adhesive will hold up during real-world use.
Tensile Strength and Elongation
Tensile strength refers to the maximum amount of tensile (pulling) stress that a material can withstand before failure. High temperature epoxy adhesives are designed to maintain impressive tensile strength even when subjected to elevated temperatures. This characteristic becomes especially critical in high-performance manufacturing contexts.
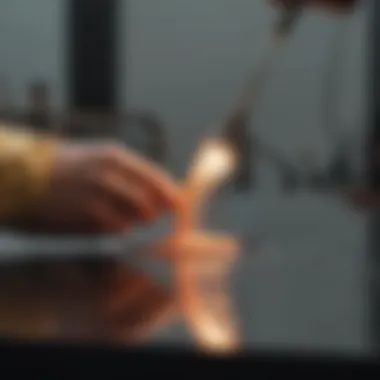
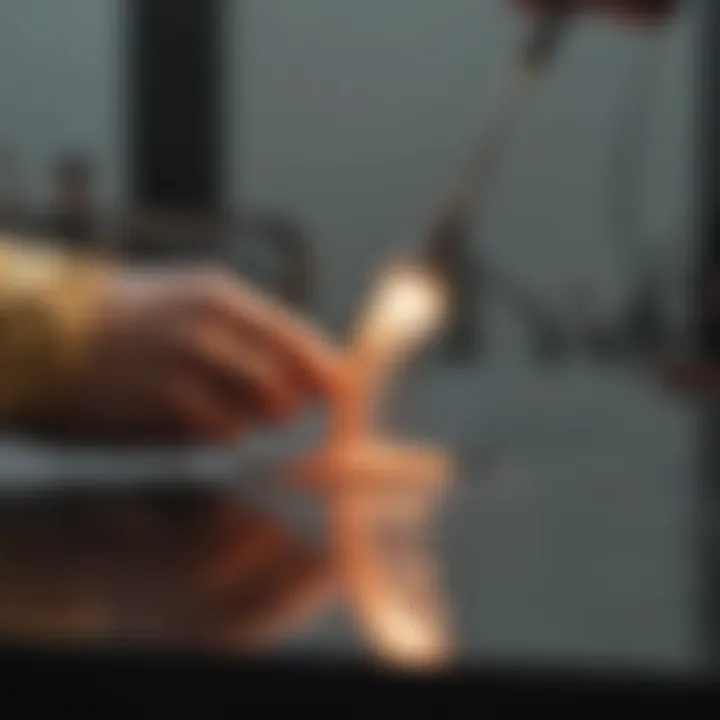
In applications such as aerospace, where components face tensile loads during flights, an adhesive that can withstand stress without losing its bond is indispensable. Typically, high temperature epoxies can have tensile strengths exceeding 20 MPa, which is conflictingly observed compared to standard epoxies that may falter at lower limits, especially when heat is introduced.
Alongside tensile strength, elongation measures the ability of an adhesive to stretch before breaking. This property is equally important; if an adhesive is too brittle, it can crack under stress. High temperature epoxies usually exhibit elongation rates ranging from 2% to 10% depending on the formulation, offering a balance of flexibility and rigidity.
- Benefits of Tensile Strength and Elongation:
- Enhances the durability of bonds in demanding environments.
- Provides reliability in applications subject to pull forces.
- Mitigates risks of failure due to material fatigue over time.
For industries that cannot compromise on strength, the right epoxy formulation can ensure components remain intact under intense strain.
Impact Resistance
Impact resistance is another pivotal performance metric that gauges how well an adhesive can endure sudden forces or shocks. This is particularly relevant in sectors such as automotive, where vehicles are regularly exposed to vibrations and potential collisions. In the context of high temperature epoxies, impact resistance reflects the adhesive's ability to maintain its bond even when subjected to sudden jerks or movements.
Adhesives with high impact resistance tend to behave more favorably under conditions of rapid temperature changes and physical disturbances. They typically feature a combination of flexibility and toughness, which allows for some deformation upon impact without fracturing. This characteristic enables high temperature epoxy adhesives to support critical structural components in numerous applications, from engine assemblies to battery packs.
In practical terms, measuring impact resistance usually involves calculating the energy absorbed when a standardized object strikes the bond. Adhesives that can absorb significant energy and still function effectively are invaluable in ensuring the longevity of materials they bind.
- Key Considerations for Impact Resistance:
- Choice of resin and hardener.
- Application method and surface preparation can affect performance.
- Environmental factors such as humidity and temperature limits.
To summarize, mechanical properties and performance metrics of high temperature epoxy adhesives extend far beyond mere numbers. A solid grasp of tensile strength, elongation, and impact resistance empowers engineers and researchers to make informed choices for specific applications. Ultimately, these elements contribute to the overall reliability and efficacy of adhesive solutions in demanding environments.
Applications of High Temperature Epoxy Adhesives
High temperature epoxy adhesives have carved a niche in various industries, proving their mettle in scenarios where ordinary adhesives would falter. Understanding the applications of these materials is crucial, as it opens the door to innovations that can enhance product reliability, durability, and performance. These adhesives are more than just bonding agents; they enable functionalities that can withstand extreme conditions such as elevated temperatures, harsh chemicals, and mechanical stresses.
For instance, in industries like aerospace, automotive, and electronics, using high temperature epoxy adhesives can lead to effective weight reduction, improved thermal management, and enhanced assembly processes. They can withstand significant thermal shocks and offer superior adhesion to a multitude of substrates, which is paramount when considering the performance of complex systems. Here are some of the prominent sectors where these adhesives are making waves:
Aerospace Industry Uses
In the aerospace sector, the demand for reliable bonding solutions is paramount. High temperature epoxy adhesives are utilized in various applications including:
- Airframe Assembly: Used in bonding structural components, these adhesives can withstand the extreme conditions faced during flight, such as rapid changes in temperature.
- Engine Components: Parts exposed to high temperatures, like those within jet engines, benefit greatly from epoxy's exceptional heat resistance and adhesion strength.
- Composite Materials: Many airplanes utilize composite materials for weight savings. Epoxy adhesives play a significant role in bonding these materials without compromising structural integrity.
Greater durability translates to enhanced safety and performance, making high temperature epoxy adhesives a top choice for aerospace manufacturers. As one expert puts it, "> The selection of suitable adhesive can significantly influence the overall performance of an aircraft component."
Automotive Applications
The automotive industry has also embraced high temperature epoxy adhesives, primarily due to their capacity to withstand engine-related heat and vibration. These adhesives are often used in:
- Under-the-hood Applications: High temperature environments around engines necessitate the use of robust adhesives for bonding components like intake manifolds and exhaust systems.
- Structural Bonding: In vehicle manufacturing, these adhesives contribute to the lightweight construction essential for fuel efficiency without sacrificing safety.
- Electronics Encapsulation: Modern automobiles are brimming with electronics. High temperature epoxy adhesives protect sensitive parts from moisture and heat, ensuring longevity and reliability.
In this competitive landscape, the right adhesive choice can result in substantial cost savings and improved product life.
Electronics and Electrical Applications
In the world of electronics, high temperature epoxy adhesives are crucial for ensuring that devices maintain their functionality under stress. These applications include:
- PCB Assembly: Adhesives are essential in assembling Printed Circuit Boards, providing a secure bond that withstands thermal cycling.
- Potting and Encapsulation: High temperature epoxies are used to encase and protect sensitive electronic components from environmental conditions, thereby extending their operational life.
- Thermal Interface Materials: These adhesives serve as thermal management systems, enhancing heat dissipation in components like semiconductors.
The ability of these adhesives to withstand fluctuations while maintaining electrical insulation makes them indispensable in this sector.
Best Practices in Application and Handling
In the realm of high temperature epoxy adhesives, adhering to best practices during application and handling is critical. Proper procedures not only enhance the adhesive's performance but also extend its lifespan and reliability. This segment focuses on essential techniques and considerations that can maximize the effectiveness of these materials in demanding environments.
Surface Preparation Techniques
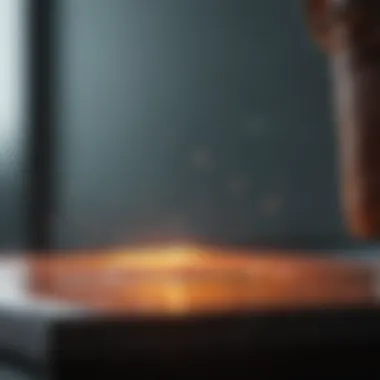
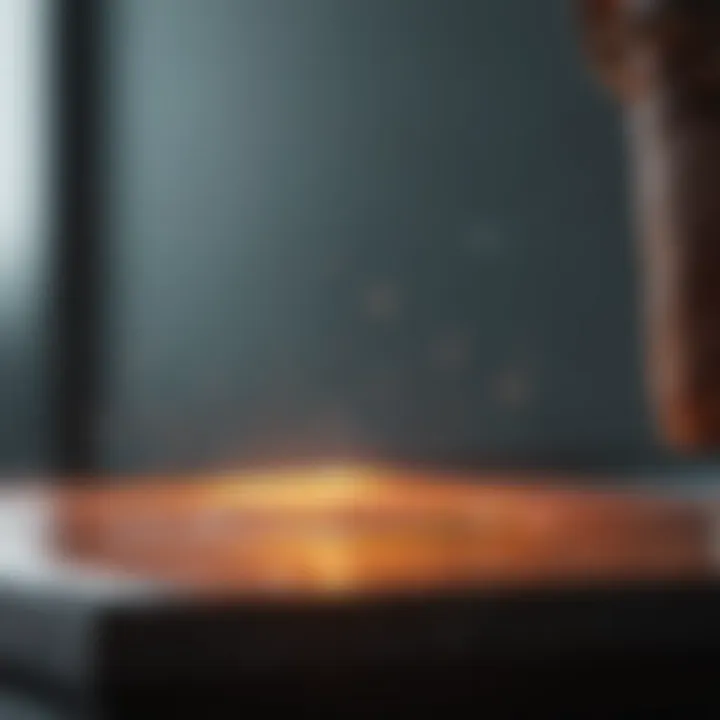
Surface preparation serves as the bedrock of effective adhesion. A surface that is well-prepped ensures that the epoxy can bond optimally to substrates, which is vital when dealing with extreme temperatures. The following steps are key:
- Cleaning: Removing dirt, oil, and contaminants from the surface is paramount. Sources of contamination such as dust and grease can compromise adhesive strength. Use solvents like acetone or isopropyl alcohol for a thorough clean, or blow dust away with compressed air.
- Abrasion: Lightly abrading the surface is often necessary, especially for metals or plastics. Techniques might include sanding or using a wire brush, which creates a rough texture, allowing the epoxy to latch onto the surface more effectively.
- Drying: After cleaning, ensure that your work surface is completely dry. Moisture can lead to adhesion failure, particularly when temperatures fluctuate, so thorough drying is non-negotiable.
In summary, investing time in proper surface preparation pays off. It’s the kind of care that leads to a well-prepared base helping in achieving superior bonding of high temperature epoxy adhesives.
Mixing and Curing Guidelines
The way you mix and cure high temperature epoxy adhesives can greatly influence their performance. Proper mixing and curing are vital for developing the desired mechanical properties and thermal stability.
- Mixing Ratios: Always adhere to the manufacturer's recommended mixing ratios. Deviating from these ratios can significantly alter the properties of the adhesive, leading to potential application failures. A precise scale can help measure components accurately.
- Mixing Technique: When combining the resin and hardener, it’s crucial to mix thoroughly but gently. Vigorous stirring can introduce air bubbles that compromise the bond. A swirling motion followed by scraping the sides of the container helps achieve a uniform blend.
- Curing Conditions: Pay close attention to curing time and temperature. Most epoxy adhesives have specific curing conditions that optimize their performance. If a product requires a room temperature cure, avoid exposing the mixture to extreme heat or cold until it fully cures—altered conditions can lead to improper setting.
"An adhesive's strength is only as good as the preparation and application it receives."
Challenges and Limitations
In the realm of high temperature epoxy adhesives, understanding the challenges and limitations is crucial for their effective utilization across various industries. These adhesives, while possessing remarkable properties, are not without their flaws. This section delves into specific elements that can influence their performance, focusing on the behavior under temperature cycling and moisture sensitivity.
Behavior Under Temperature Cycling
Temperature cycling refers to the process of exposing materials to fluctuating temperatures, which can lead to expansion and contraction. This phenomenon is particularly relevant for high temperature epoxy adhesives, as repeated temperature changes can severely affect their structural integrity.
- Thermal Expansion: When subjected to a broad range of temperatures, these adhesives may undergo thermal expansion. If the components being bonded expand and contract at different rates than the epoxy itself, it can cause stress fractures or delamination over time.
- Fatigue Failure: Constant cycling can lead to fatigue failure. The repetitive stress can weaken the adhesive bond, potentially resulting in a complete loss of adhesion in extreme cases. It’s akin to a rubber band that snaps after being stretched too often; the materials can only handle so much wear and tear.
To mitigate these issues, it is essential to thoroughly evaluate the adhesive's thermal cycling characteristics during the selection process. Performing rigorous testing and utilizing formulation adjustments are also viable strategies.
Moisture Sensitivity
Moisture sensitivity is another significant concern pertaining to high temperature epoxy adhesives. While many adhesives are designed to resist the harshest of conditions, exposure to high humidity or water can adversely impact their effectiveness.
- Hydrolytic Degradation: Certain types of epoxies might undergo hydrolytic degradation when exposed to moisture, leading to a decline in mechanical properties. Think of it like a sponge gradually losing its shape when soaked; the structure alters as the moisture works its way in.
- Adhesion Loss: Water can infiltrate the bond line, weakening the adhesion and making it susceptible to peeling or breaking apart. In high-stakes applications, such as in aerospace or automotive sectors, this can lead to catastrophic failures.
"Knowledge is power, especially when it comes to optimizing the use of materials in demanding conditions."
By being mindful of these potential pitfalls, engineers and manufacturers can make more informed decisions, enhancing both safety and efficacy in their projects.
Finale and Future Directions
High temperature epoxy adhesives serve not just as functional materials but also as critical components that enable today's high-performance applications across various industries. Their versatility, strength, and thermal stability are essential to maintaining integrity in environments where traditional adhesives might fall short. This article has outlined the significant advantages and challenges associated with these materials. As we look to the future, several key elements stand out that professionals in engineering and materials science should consider.
Summary of Key Findings
Throughout this discourse, several key takeaways emerged about high temperature epoxy adhesives:
- Thermal Stability: These adhesives maintain their properties under extreme temperature conditions, vital for industries like aerospace and automotive.
- Mechanical Performance: They exhibit remarkable tensile strength and impact resistance, making them suitable for demanding applications.
- Chemical Composition: Understanding the role of base resins and curing agents is crucial for optimizing adhesive properties.
- Application Techniques: Proper handling and preparation can enhance performance, addressing issues such as moisture sensitivity.
This combination of properties not only underscores their importance but also highlights that attention to detail in application can lead to vastly improved performance outcomes.
Innovations in Epoxy Adhesive Technologies
Looking ahead, researchers and industry experts are continually striving for advancements in epoxy adhesive technology. Several promising innovations are already making waves:
- Enhanced Formulations: New mixtures that incorporate nano-materials have shown to bolster the thermal and mechanical properties of adhesives, leading to even greater durability.
- Smart Adhesives: The development of adhesives that can respond to changes in temperature or other environmental factors is on the rise. Such materials could revolutionize application methodologies.
- Biocompatible Options: With an increasing focus on sustainability, there’s a growing trend toward creating high-temperature adhesives from renewable resources, which could address both performance and environmental concerns.
The ongoing exploration in these areas promises to not just improve existing products but also open up new applications, extending the utility of high temperature epoxy adhesives far beyond current horizons.
“The future of epoxy technology is not just about meeting today’s requirements, but anticipating the demands of tomorrow’s innovative applications.”
Citing Research Material
When discussing a complex topic like high temperature epoxy adhesives, citing research material becomes essential. It allows for a well-rounded discourse by bringing various perspectives and findings into the conversation. Here are some key points to consider regarding the significance of citations in this field:
- Enhancing Authoritativeness: Citing peer-reviewed studies or established texts lends authority to your claims. This is especially important when discussing technical properties or applications of high temperature epoxy adhesives.
- Providing Context: References situate your discussion within the broader scientific dialogue. They can illustrate how current findings build upon previous work or highlight where gaps may exist.
- Encouraging Practical Applications: By referencing case studies or practical findings, professionals in the industry can better appreciate how theoretical concepts translate into real-world use.
- Documentation of Progress: Maintaining a rigorous citation regime helps track advancements in epoxy technologies over time, showcasing trends, challenges, and innovations that contribute to the field's progression.
- Facilitating Further Research: Well-cited work serves as a launchpad for further inquiry. Researchers can pick up where others left off, sparking new ideas or refining existing methods.
In sum, when committing to a discussion about high temperature epoxy adhesives, it’s imperative to engage with credible sources. This ensures that the insights shared are not just opinions but are grounded in tangible, verifiable research—thus amplifying both the depth and the utility of the material presented.