Implementation of MRP: A Comprehensive Guide
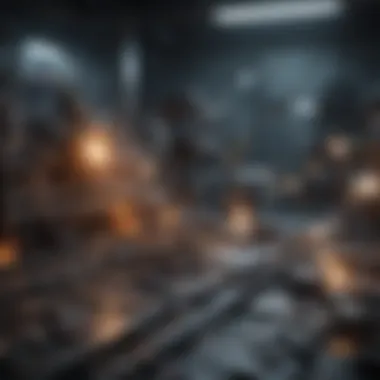
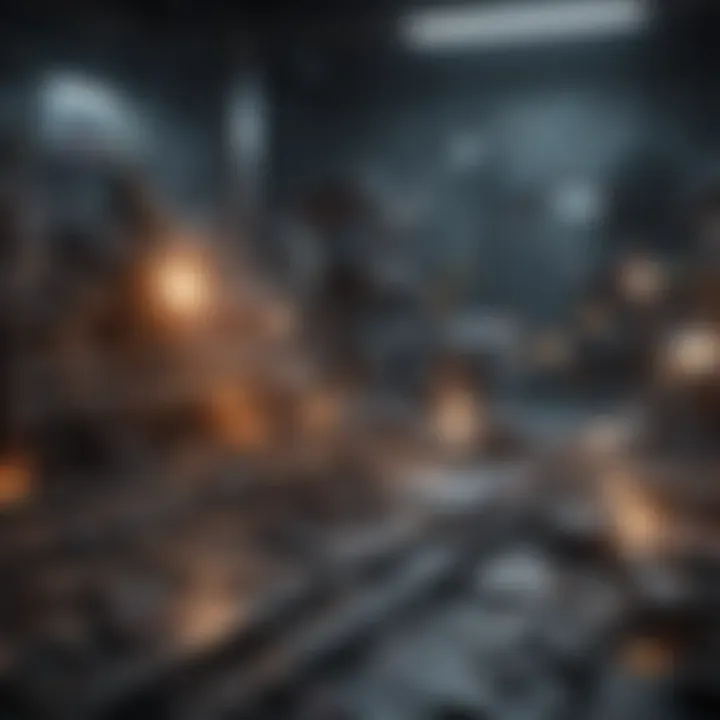
Key Concepts and Terminology
Definition of Key Terms
Material Requirements Planning (MRP) is a system that helps manufacturers manage inventory and production schedules efficiently. MRP operates on fundamental concepts such as lead times, bill of materials, and demand forecasting. Lead time refers to the time between ordering and receiving materials, while a bill of materials lists all components needed to produce a product. Demand forecasting predicts future product demand, essential for planning inventory levels.
Concepts Explored in the Article
This article will encompass several core ideas surrounding MRP. These include the importance of integrating MRP within supply chain management and its role in optimizing inventory control. The text also discusses how production planning aligns with MRP principles to enhance overall efficiency. Throughout the article, we will cover implementation strategies, the necessary tools for MRP, and challenges commonly faced in real-world applications.
Findings and Discussion
Main Findings
The implementation of MRP reveals several key insights. Organizations that adopt a well-structured MRP system often show improvements in inventory accuracy and production efficiency. These improvements result in reduced lead times, lower carrying costs, and better alignment of production schedules with actual demand. Furthermore, the integration of software solutions tailored for MRP has demonstrated significant ability to streamline processes.
"An effective MRP system does not merely track inventory; it creates a unified approach to meeting production demands."
Potential Areas for Future Research
There are notable gaps in the current MRP literature. Future research could delve into the role of emerging technologies like artificial intelligence and machine learning. These technologies may further enhance MRP systems and address challenges such as demand uncertainty and real-time data integration. Additionally, studies could investigate the effect of MRP adoption in diverse manufacturing sectors to understand broader implications across different supply chains.
Understanding Material Requirements Planning
Understanding Material Requirements Planning (MRP) is critical for enhancing operational efficiency within organizations. This section delves into the essence of MRP, shedding light on its definitions, purposes, and components. Grasping these fundamental aspects is essential for anyone involved in supply chain management or production processes. MRP serves as a backbone in efficiently addressing materials and scheduling needs, minimizing waste, and optimizing resources.
Definition of MRP
Material Requirements Planning (MRP) is a system used for production planning, scheduling, and inventory control. Its primary aim is to ensure that materials are available for production and products are available for delivery to customers. MRP operates by determining the quantity and timing of materials needed to fulfill production schedules. This definition highlights MRP's role in synchronizing materials with production processes, which ultimately impacts overall business performance.
Purpose of MRP
The main purpose of MRP is to enhance efficiency in manufacturing and supply chain operations. By accurately planning material needs, businesses can reduce both excess inventory and shortages. This strategic approach ensures that firms can respond to customer demands effectively and maintain production flow. When implemented correctly, MRP leads to cost savings, improved decision-making, and better customer service.
Key Components of MRP
The effectiveness of MRP hinges on several crucial components, each playing a unique role in the overall functionality.
Inventory Management
Inventory management is a vital aspect of MRP as it involves tracking materials across all stages of production. A key characteristic of this component is its focus on maintaining optimal inventory levels. This balance is beneficial because it prevents overstocking or stockouts, which can disrupt production. However, maintaining such levels requires accurate data and continuous monitoring to adapt to changing demands.
Production Planning
Production planning under MRP allows organizations to schedule their manufacturing processes effectively. This component stands out due to its emphasis on aligning production processes with demand forecasts. As a beneficial choice, it helps companies allocate their resources efficiently. One unique feature is its adaptability to fluctuating demand, which can be both an advantage and a challenge. The challenge lies in accurately predicting demand to avoid production delays.
Demand Forecasting
Demand forecasting is essential within the MRP framework. This component analyzes data to predict customer demand accurately. Its key characteristic is its reliance on historical data trends to inform future production needs. Demand forecasting is a beneficial method since it supports strategic decision-making. However, the uniqueness of this approach involves balancing accuracy with volatility in market conditions, making it a complex yet vital element of MRP management.
The Importance of MRP in Supply Chain Management
Material Requirements Planning (MRP) plays a crucial role in supply chain management by ensuring that the right material is available at the right time. Implementing MRP systems can lead to several noticeable benefits for organizations. It aids in creating a seamless connection between procurement, production, and customer demand.
One of the primary benefits is the optimization of inventory levels. With MRP, businesses can reduce carrying costs by maintaining only the necessary stock. This leads to fewer capital tied up in excess inventory, which can improve overall cash flow. The system provides better visibility into stock availability and usage, helping managers make informed decisions regarding reorder points and quantities.
Moreover, the enhancement of production efficiency cannot be overlooked. MRP minimizes the risks of overproduction, material shortages, or delays. This efficiency helps to streamline production schedules, allowing companies to fulfill customer orders more swiftly. The coordination of materials with production processes leads to smoother operations and reduces idle time.
Another critical element is the overall improvement in customer satisfaction. By aligning production schedules with demand and ensuring timely delivery of products, MRP contributes to fulfilling customer expectations. Improving responsiveness to market changes and accurately forecasting demand enhances trust and loyalty among consumers. Companies can pivot quickly to meet evolving needs, solidifying their position in a competitive landscape.
In summary, MRP is indispensable for optimizing resources, improving operational efficiency, and enhancing customer relationships in supply chain management. The ability to forecast accurately and manage inventories effectively transforms how businesses operate in today’s fast-paced environment.
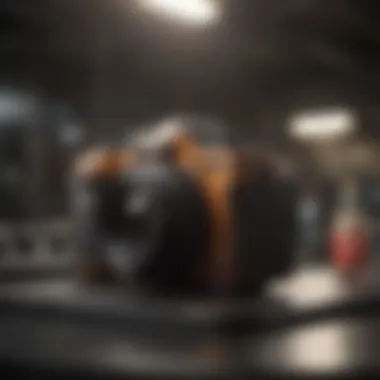
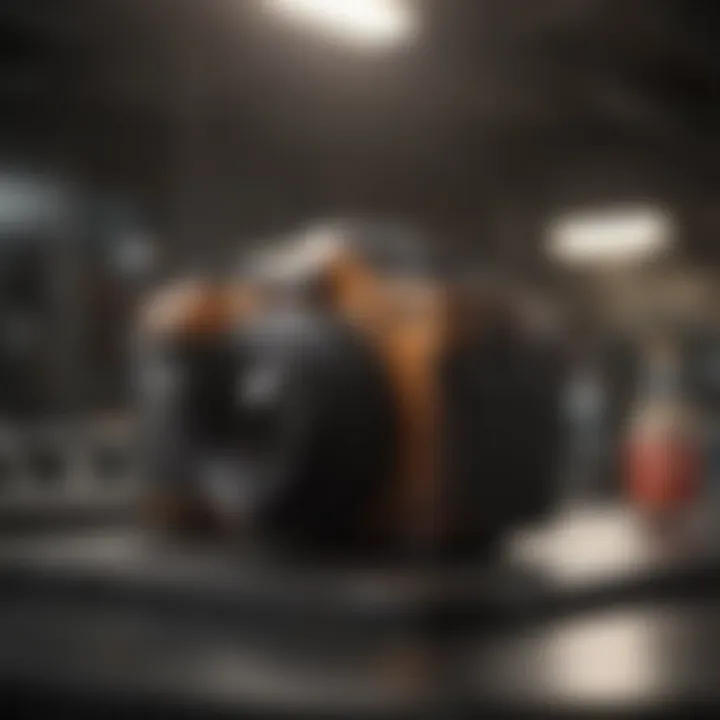
"MRP is not just a tool; it is an integral framework that supports smart decision-making across supply chains."
Whether you are a student learning the concepts of supply chain management or a professional looking to refine operations, understanding MRP's importance is essential.
MRP Process Flow
The MRP process flow is critical in ensuring the effective implementation of Material Requirements Planning. Understanding this process allows businesses to streamline operations, maintain optimal inventory levels, and respond to market demands swiftly. The process flow encompasses various components, including data collection, calculations, and execution of plans. Without a clear flow, organizations may face inefficiencies that hinder productivity and increase costs.
Data Requirements for MRP
Data accuracy is vital for the MRP process. Proper data input forms the foundation for effective planning and decision-making.
Bill of Materials
The Bill of Materials (BOM) is essential in defining the components needed to manufacture a product. It lists the raw materials, subassemblies, and parts required. The key characteristic of a BOM is its ability to provide detailed itemization, which enables precise production planning.
BOMs are beneficial because they help avoid shortages and overproduction by clearly outlining what is needed at each production phase. A unique feature of BOMs is their structure, which often allows for multi-level hierarchies that represent complex products. A downside of BOMs is that they can become outdated if not regularly updated, leading to inaccuracies in requirements.
Inventory Records
Inventory records provide real-time visibility into stock levels and their turnover rates. This characteristic is paramount because it helps companies determine reorder points effectively, preventing stockouts or overstock situations. Maintaining accurate inventory records is critical for the MRP as it directly influences the ordering process and schedules.
One unique feature of inventory records is the integration with purchase orders, which allows for tracking inventory levels against expected shipments. However, if records are not maintained or updated frequently, they can lead to costly errors in planning.
Master Production Schedule
The Master Production Schedule (MPS) outlines what, when, and how much will be produced. This schedule is crucial for aligning production with demand. One key characteristic of the MPS is its ability to translate customer orders and forecasts into actionable production plans.
A beneficial aspect of having a well-defined MPS is that it aids in resource allocation, ensuring that materials and labor are available when needed. Its unique feature lies in its scheduling flexibility; it can be adjusted based on changing customer demands. Though, a disadvantage is that if the MPS is not closely aligned with actual demand, it can result in inefficiencies such as excess inventory or missed market opportunities.
MRP Calculations
Calculating material requirements accurately is central to an effective MRP. These calculations ensure that all components align with production capacity and lead times.
Net Requirement Calculation
Net Requirement Calculation determines the actual quantity of material needed after considering on-hand inventory and scheduled receipts. This calculation is crucial as it establishes a realistic overview of what needs to be ordered. The key characteristic of this calculation is its focus on real-time data to drive decisions. It is a popular choice in MRP because it aligns orders closely with actual needs, preventing excess inventory.
A unique feature of the net requirement calculation is its ability to accommodate variations in demand, allowing for adjustments in procurement. However, if input data is incorrect, the output can lead to significant discrepancies.
Lead Time Considerations
Lead time considerations are vital for ensuring that materials arrive when needed. This aspect includes understanding the time required for procurement, production, and delivery. The key characteristic is that it helps teams manage timelines effectively.
Considering lead times is beneficial as it allows organizations to set realistic production schedules and react swiftly to changes. A unique feature is the ability to analyze different lead times for various suppliers, allowing for better negotiations and planning. However, inaccurate lead time estimates can result in production delays or increased costs.
Ensuring that data integrity and accuracy in calculations remain top priorities is essential for the successful implementation of the MRP process flow.
Implementing MRP: A Practical Approach
The implementation of Material Requirements Planning (MRP) is crucial for organizations aiming to streamline their operations. A practical approach focuses on the steps needed for successful execution. This involves careful preparation, selection of suitable software, and effective training. Each of these elements contributes to overall system effectiveness and helps in overcoming common challenges.
Preparation and Planning
Preparation is the first step in the MRP implementation process. It involves several key actions.
Initial Assessment
The initial assessment is an evaluation process that identifies current capabilities and areas for improvement. This assessment is important as it lays the foundation for a smoother implementation. By understanding the existing systems and workflows, organizations can recognize specific needs and gaps. One key characteristic of an initial assessment is its comprehensive nature, addressing not only technological aspects but also human factors. The benefit of this assessment is that it produces a clear roadmap. However, it may require significant resources and time to gather accurate information.
Setting Objectives
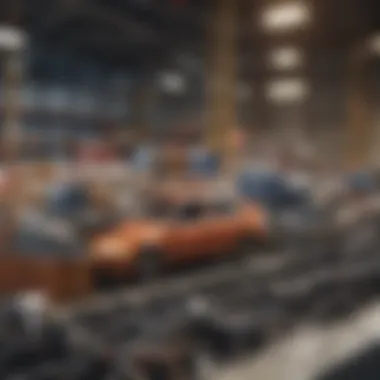
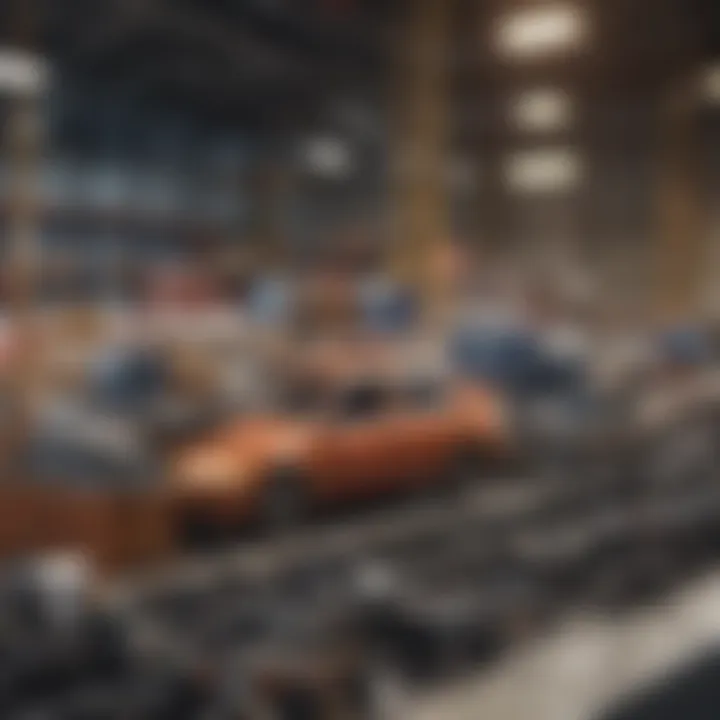
Once the initial assessment is done, setting objectives is essential. This involves defining what the organization hopes to achieve with MRP. Clear objectives guide the implementation process and help measure success. A key characteristic of setting objectives is its alignment with the company’s overall goals. This creates a focused approach, ensuring that every action taken is beneficial towards achieving those goals. One unique feature of this process is that it encourages stakeholder involvement, fostering collaboration. However, unrealistic or vague objectives can hinder performance and lead to dissatisfaction.
Choosing MRP Software
Selecting the right software is a pivotal component of MRP implementation. Not all software solutions are created equal, and this decision can impact the effectiveness of the system.
Criteria for Selection
Criteria for selection include functionality, ease of use, scalability, and cost. These factors contribute significantly to ensuring the software will meet the organization's needs. The primary characteristic of these criteria is their focus on business requirements. This selection process is beneficial, as it ensures compatibility with existing systems and workflows, which helps reduce disruption. On the downside, not adhering to robust criteria may lead to misalignment with the company’s needs.
Popular MRP Solutions
Popular MRP solutions like SAP, Oracle, and Microsoft Dynamics serve various businesses effectively. These tools are well-regarded for their extensive features and user support. The hallmark of these solutions is their capacity to integrate with other systems seamlessly. This integration is advantageous, as it allows for smoother data flow across different functions. However, these solutions can also be quite complex and require ample training and resources, potentially complicating the implementation process.
Training and Change Management
Training and change management are critical for easing the transition into MRP usage. Resistance to change can derail the implementation process, making these aspects vital.
Stakeholder Engagement
Stakeholder engagement is about actively involving everyone affected by the MRP implementation. This engagement cultivates a sense of ownership and reduces resistance. A key characteristic is its inclusive nature, allowing various voices to contribute to the process. This is beneficial as it ensures that diverse perspectives are considered. However, if not managed correctly, engaging too many stakeholders can lead to conflicts and indecision.
User Training
Lastly, user training is fundamental for operational success. Effective training ensures that employees feel confident in utilizing the new system. The characteristic of user training is its hands-on approach, allowing users to practice with the system. This is beneficial as it translates theoretical knowledge into practical skills. Nonetheless, insufficient training may lead to poor adoption rates, negating the efforts of the whole implementation.
In summary, implementing MRP is a multifaceted process. Preparation, software selection, and training contribute significantly to successful execution. Each element should be aligned with organizational goals to achieve the desired outcomes.
Challenges in MRP Implementation
The implementation of Material Requirements Planning (MRP) can yield substantial benefits for organizations, but it is not devoid of challenges. Understanding these challenges is crucial for ensuring a smooth transition to MRP. Organizations can face numerous obstacles that hinder effective implementation, ranging from technical issues to human factors. Addressing these challenges proactively not only enhances the likelihood of a successful MRP setup but also optimizes its advantages in inventory control and production planning.
Data Accuracy Issues
Data accuracy is fundamental in MRP systems. Inaccurate data can lead to significant problems, including overstocking or stockouts. This creates disruptions in production workflows and affects customer satisfaction. Key components that require precise data include the Bill of Materials, inventory levels, and lead times.
To tackle data accuracy issues, it is essential to conduct regular inventory audits and employ validation techniques to ensure the data used in MRP calculations is reliable. Additionally, investing in quality data management software aids in maintaining accuracy during data entry and updates. Without sound data accuracy, the integrity of the entire MRP process can be compromised, leading to increased costs and inefficiencies.
Integration with Existing Systems
Integrating MRP with existing systems poses a considerable challenge for many organizations. Often, companies rely on legacy systems that may not be compatible with modern MRP software. This can create silos of information and hinder collaboration between departments.
To achieve a successful integration, organizations should conduct a thorough assessment of current systems. It is vital to establish clear communication between IT departments and stakeholders to align system functionalities with MRP requirements. Also, engaging with software vendors who understand integration processes can be beneficial. Establishing a phased approach to integration can minimize disruptions in daily operations and allow for a more manageable transition process.
Resistance to Change
Resistance to change is a common human factor in MRP implementation. Employees may feel apprehensive about new processes and software, fearing that they might not adapt effectively or that their roles may change significantly. This resistance can lead to poor user adoption and eventually hinder the MRP system’s effectiveness.
To mitigate resistance, it is important to actively engage stakeholders throughout the implementation process. This can be achieved by providing proper training and emphasizing the benefits of MRP for both the organization and individual employees. Establishing a supportive atmosphere that encourages feedback can also enhance acceptance of new systems. Encouraging an open discussion about concerns can help build trust and foster engagement among employees, ultimately leading to a more successful MRP implementation.
"Embracing change is never easy, but with informed strategies to overcome obstacles, organizations can unlock the potential of MRP systems to enhance efficiency."
Best Practices for MRP Implementation
Implementing Material Requirements Planning (MRP) can be a complex task. Therefore, it is crucial to follow best practices that guide organizations toward successful deployment. By adhering to these best practices, companies can minimize errors, enhance productivity, and create an efficient manufacturing environment. The focus here is on continuous monitoring and feedback, iterative improvements, and cross-department collaboration.
Continuous Monitoring and Feedback
Continuous monitoring and feedback are essential in MRP implementation. This involves regularly reviewing the data input processes and the outcomes of the MRP execution. By establishing key performance indicators (KPIs), organizations can track aspects like inventory levels, production schedules, and purchase orders. Implementing feedback loops allows teams to adjust plans based on real-time data.
For example, if a certain material consistently runs low, the organization can analyze its usage more closely and adjust purchasing habits accordingly. This dynamic approach leads to better resource allocation and reduces the risk of production delays due to inventory shortages.
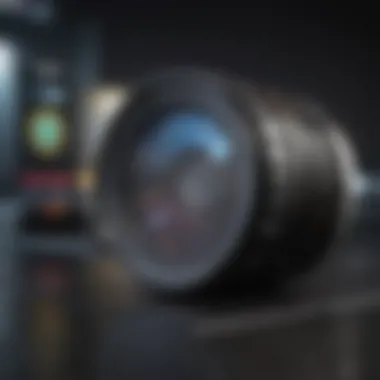
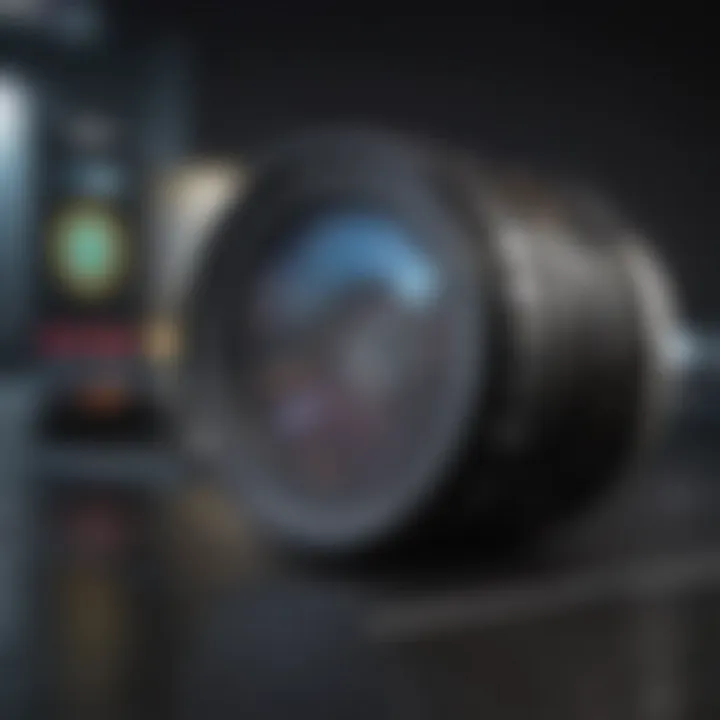
Iterative Improvements
MRP systems should not be static. It is crucial for organizations to embrace the iterative improvement process. This means consistently refining the practices in response to collected data and user experiences. After each cycle of MRP execution, analysis of outcomes should inform what strategies are effective and which need adjustments.
An effective method is to hold regular review meetings where teams can discuss observations and suggest alterations. This encourages a culture of continuous improvement that aligns with evolving business needs and market conditions. Ultimately, iterations in MRP can lead to refined forecasting accuracy and more reliable production planning.
Cross-Department Collaboration
Cross-department collaboration is one of the pillars of successful MRP implementation. Different departments, such as procurement, production, and sales, must engage with each other throughout the MRP process. Collaborative efforts ensure that exchange of information is timely and precise. For instance, the sales department can provide insight into market trends, which informs better demand forecasting.
Additionally, linking systems across departments promotes cohesiveness. Utilizing integrated software systems can help ensure that all stakeholders have access to real-time data. This helps in aligning departmental goals with overall business objectives, improving operational efficiency.
"Effective MRP implementation cannot occur in silos; it requires a unified effort across various functions within the organization."
By following these best practices, companies can navigate the complexities of MRP implementation and harness its full potential. Emphasizing continuous monitoring, iterative improvements, and fostering collaboration will ultimately contribute to operational excellence.
Evaluating MRP Effectiveness
Evaluating the effectiveness of Material Requirements Planning (MRP) is crucial for several reasons. Understanding how well your MRP system performs can lead to significant improvements in inventory management, production rates, and overall supply chain efficiency. An effective evaluation process helps identify areas of weakness and supports informed decision-making for future enhancements.
Specific Benefits of Evaluating MRP Effectiveness:
- Helps maintain optimal inventory levels.
- Assures production schedules align with actual demand.
- Provides insights into operational efficiencies that can be enhanced.
To gauge how well the MRP system is working, organizations must reflect on key performance indicators (KPIs) that measure success. This involves both quantitative and qualitative reviews, which can uncover patterns and trends that are not immediately visible.
Key Performance Indicators for MRP
Key performance indicators (KPIs) are essential for assessing MRP effectiveness. These metrics not only track operational efficiency but also provide insights into customer satisfaction and cost management. Some of the important KPIs include:
- Inventory Turnover Rate
This metric measures how often inventory is sold and replaced over a specific period. A higher turnover rate often indicates effective inventory management. - Order Fulfillment Rate
This indicates the percentage of customer orders that are completed on time. A high rate suggests that the MRP system effectively matches production with demand. - Cycle Time
Evaluating the total time taken from order receipt to delivery can illustrate efficiency, helping identify bottlenecks in the process. - Production Schedule Adherence
This KPI measures how well the production activities align with the planned schedules. Improved adherence reflects efficient planning and execution. - Percentage of Stockouts
Tracking stockouts reveals gaps in inventory that could lead to missed sales opportunities. Lower percentages indicate a more responsive MRP system.
Regular review of these KPIs can facilitate ongoing adjustments to processes and strategies, all aimed at optimizing MRP performance.
Regular System Audits
Conducting regular system audits forms an integral part of evaluating MRP effectiveness. Audits help ensure that the data driving your MRP decisions remains accurate and relevant. An effective audit will focus on key areas such as:
- Data Integrity: Ensuring that inventory records, production schedules, and demand forecasts are accurate and up-to-date.
- Process Compliance: Evaluating whether the established procedures are followed consistently across departments.
- Performance Metrics: Regularly reviewing KPIs to check for any trends that need attention.
"Routine audits reveal insights that can lead to more efficient inventory management and production processes."
These audits can highlight discrepancies and potential issues before they escalate.
By understanding where the MRP system excels or lags, companies can adapt strategies accordingly. Overall, this practice supports not just immediate improvements but also long-term sustainability in MRP operations.
In summary, evaluating MRP's effectiveness through KPIs and regular audits will help organizations to sharpen their operational strategies, promoting better alignment between supply and demand.
Future Trends in MRP
As industries evolve, so does the approach to Material Requirements Planning (MRP). Understanding future trends in MRP is vital for organizations aiming for competitive edge. Companies must adapt to technological advancements and changing market demands. The integration of innovative solutions not only increases efficiency but also improves accuracy in resource planning. Moreover, future trends will shape how businesses manage their supply chains, influencing decisions around procurement, inventory, and production.
Integration with AI and Machine Learning
The integration of Artificial Intelligence (AI) and Machine Learning (ML) into MRP systems presents numerous advantages. AI can analyze vast amounts of data with speed and precision, identifying patterns that inform demand forecasts. For instance, instead of relying solely on historical data, AI systems can consider current market trends and consumer behaviors. This leads to more accurate predictions of material requirements, ultimately reducing excess inventory and minimizing stockouts.
Machine Learning algorithms can also improve over time by learning from real-time data inputs. With continuous analysis, these systems can optimize production schedules, ensuring that materials are available exactly when needed. This adaptability is crucial in dynamic markets where consumer preferences can shift rapidly. Businesses leveraging AI and ML can improve decision-making processes, leading to enhanced operational efficiency.
Additionally, the use of automation in MRP tasks can significantly reduce human error. AI-driven systems can facilitate smarter ordering processes, wherein they place purchase orders based on predefined conditions. This automates the replenishment process, streamlining operations, and allowing staff to focus on more strategic tasks.
"Adopting AI into MRP is not just an option; it is a necessity for firms wishing to stay relevant in their industries."
Evolution of Cloud-Based Solutions
Cloud computing marks a notable shift in how MRP systems operate. Traditionally, MRP software required significant local infrastructure and maintenance. Today, cloud-based solutions offer flexibility and scalability that on-premises systems cannot match. With a cloud-based MRP system, businesses can access their data and services from anywhere with an internet connection.
This accessibility allows for real-time data sharing across departments and locations. Teams from production, inventory, and sales can collaborate seamlessly when working with a unified platform. Thus, it enhances cross-departmental transparency and decision-making, which is crucial for smooth operations.
Moreover, cloud MRP solutions often come with subscription-based pricing, reducing the upfront costs associated with traditional systems. As operational needs change, businesses can adjust their capacity, ensuring they pay only for what they use. This flexibility can be particularly beneficial for small to medium-sized enterprises which face fluctuating demands.
Cloud computing also provides robust options for disaster recovery and data security. Providers often implement stringent security measures that exceed what many organizations can offer internally. Consequently, businesses benefit from better protection of sensitive information while focusing on their core activities.