Liners for Discharge: Innovations and Applications
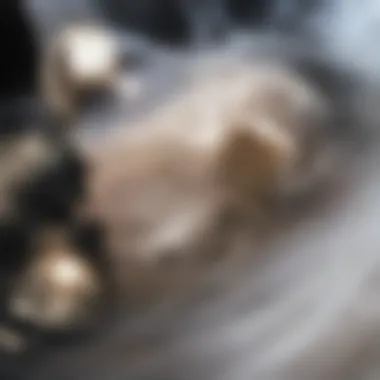

Intro
Liners for discharge play a critical role in multiple industries, presenting an essential mechanism for managing the flow of various substances. Understanding their significance begins with a grasp of the basic concepts and terminology involved in their application. This section will delve into the definitions and concepts necessary to appreciate the innovative applications and recent developments of discharge liners.
Key Concepts and Terminology
Definition of Key Terms
Liners for discharge typically refer to materials engineered to contain and direct fluids in various processes. Commonly utilized in areas like wastewater treatment and mining, these liners are designed to withstand specific environmental conditions while minimizing leakage.
Common terms include:
- Liner material: These can range from geomembranes, concrete, and polymers to more specialized materials, depending on the application.
- Permeability: A measure of how easily a fluid can pass through a material. Lower permeability in liners is usually desired to reduce fluid loss.
- Environmental impact: This refers to the interactions between the liners and surrounding ecosystems, critical when considering material choices and designs.
Concepts Explored in the Article
The article sheds light on several aspects of discharge liners including:
- Material Composition: Different materials possess distinct properties impacting the performance of the liners in various scenarios.
- Design Considerations: The design process entails assessing factors from fluid characteristics to environmental conditions to ensure efficiency and safety.
- Technological Advancements: Recent innovations enhance durability and functionality, paving the way for more effective utilization in diverse sectors.
Findings and Discussion
Main Findings
The significance of liners for discharge extends beyond their basic function; they directly contribute to the overall efficiency of many industrial processes. The choice of materials and design has a strong correlation with the longevity and efficacy of these systems. Studies indicate that modern polymers outperform traditional materials under specific stressors, leading to lower maintenance costs and higher safety standards.
Potential Areas for Future Research
Further exploration could be beneficial in several domains:
- Material Innovation: Researching bio-based alternatives for liners could alleviate some negative environmental impacts.
- Long-term Performance Studies: Longitudinal studies into the degradation and performance of various liner materials could provide deeper insights.
- Integration with Smart Technology: Developing smart liners equipped with sensors could streamline monitoring processes, enhancing safety and efficiency.
Understanding Liners for Discharge
Liners for discharge play a critical role in various industries. They assist in controlling the flow of substances while minimizing risks associated with leakage and contamination. The selection and performance of these liners can have significant implications for safety, environmental protection, and operational efficiency.
In this article, we will discuss comprehensive insights about liners for discharge, focusing on their definitions, historical context, material selection, design considerations, applications, and more. This information serves as a valuable resource for students, researchers, and professionals in related fields.
Definition and Purpose
Liners for discharge are specialized materials designed to contain and manage the flow of liquids or solids in various operational environments. Their primary purpose is to prevent leakage and facilitate safe transport.
These liners are employed in numerous applications, including waste management, mining, and oil production. Effective liners must adhere to specific standards and regulations, ensuring that they are suitable for the materials they will contain. They also need to possess qualities such as durability and resistance to chemical degradation.
Historical Context
The use of liners dates back several decades. Initially, rudimentary materials were implemented in discharge systems. Over time, advancements in materials science led to the development of more sophisticated options. Innovations have driven the evolution of liners to respond to diverse industrial needs.
Historically, industries such as construction and extractive sectors originally relied on basic liners, often leading to significant spills and environmental destruction. A transition took place as regulations tightened. Authorities began mandating the use of improved liner technologies.
As a result, modern liners are often engineered with a combination of metals, polymers, and composite materials. This shift has not only improved the safety of operations but also enhanced environmental stewardship.
In summary, the understanding of liners for discharge is essential for ensuring compliance, protecting the environment, and enhancing operational efficiency. This foundational knowledge sets the stage for further exploration into material selection, design considerations, and applications across various industries.
Material Selection
Material selection plays a crucial role in determining the effectiveness and longevity of liners for discharge. Choosing appropriate materials ensures that liners can withstand operational challenges and environmental conditions. It involves careful consideration of characteristics that affect performance, such as durability, flexibility, and resistance to various stressors including chemicals and temperature fluctuations. As industries continue to demand higher efficiency and safety standards, understanding the specific materials used in liners for discharge is essential for optimizing performance and longevity.
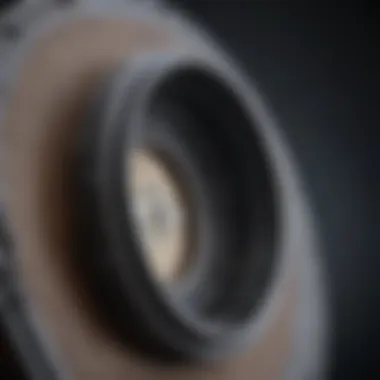

Common Materials Used
Metals
Metals are widely used in liners for their strength and durability. Their structural integrity allows them to bear heavy loads and resist deformation under stress. Steel is particularly notable for its high tensile strength which makes it effective in demanding applications such as mining and construction. However, it is essential to consider factors like corrosion. While steel performs well in many conditions, it may require coatings or treatments to enhance its corrosion resistance.
Polymers
Polymers represent another critical category in the material selection for liners. They are appreciated for their ease of fabrication and versatility. Polyethylene and polypropylene are common choices due to their lightweight nature and resistance to chemical degradation. One compelling aspect of polymers is their ability to absorb impacts, making them suitable for applications where vibration or shock is a factor. However, certain polymers may not resist extreme temperatures, limiting their use in high-heat environments.
Composites
Composites combine the best properties of several materials. They often feature a matrix of polymers reinforced with fibers such as carbon or glass. This combination results in a product that is lighter than metals while still exhibiting high strength and stiffness. Composites are particularly beneficial in specialized applications where reducing weight is critical, such as aerospace or certain automotive configurations. Nonetheless, the production of composites can be more complex and costly compared to traditional materials.
Properties of Effective Liners
Durability
Durability focuses on the ability of liners to withstand wear and tear over time. A durable liner withstands impacts and environmental stresses without compromising its structural integrity. The longevity of a liner directly influences maintenance costs saving resources in the long run. Metals usually excel in durability, but specific polymers can also provide a high level of resilience against abrasion.
Chemical Resistance
Chemical resistance is a key property for liners operating in environments where exposure to corrosive substances occurs. Materials with high chemical resistance maintain structural and functional integrity, preventing degradation that can lead to failure. For example, polymers like PVC are often selected for their excellent resistance to chemicals, making them suitable for applications in wastewater treatment. However, not all materials provide the same level of protection against chemical exposure, thus necessitating careful material selection based on the specific environment.
Thermal Stability
Thermal stability refers to the ability of a liner to maintain its properties when subjected to temperature fluctuations. Effective thermal stability allows for consistent performance in various conditions, which is particularly critical in industries such as oil and gas. Materials like certain composites possess superior thermal properties that enable operational reliability at high temperatures. However, it is crucial to understand that while some materials excel in one area, they might fall short in others, requiring a balanced approach toward material selection.
Design Considerations
Design considerations play a crucial role in the efficiency and longevity of liners for discharge. Proper design ensures that the liners perform optimally under various conditions, reducing the risk of failures and enhancing safety across applications. Understanding how engineering principles and customization intersect allows professionals to innovate and adjust their strategies to meet specific needs.
Engineering Principles
Engineering principles form the foundation of effective liner design. One key principle is understanding the operational environment where the liner will function. There are important factors to evaluate, including:
- Load Distribution: Liners must be designed to distribute loads evenly to prevent stress concentrations that can lead to cracks or failures.
- Fluid Dynamics: Knowledge of how fluids flow and interact with materials is essential for minimizing erosion and wear, which are common issues with discharge operations.
- Thermal Management: Liners may experience significant temperature fluctuations. Designing for thermal expansion and contraction is necessary to ensure durability.
Applying these principles can significantly improve the performance of discharge liners. For instance, engineered grooves can help manage fluid flow more efficiently, leading to lower wear rates and extended service life.
Customization and Adaptability
In today’s diverse industrial landscape, the capacity for customization and adaptability is vital in liner design. Industry-specific needs vary widely, requiring tailored approaches to liner solutions. Some of these considerations include:
- Material Selection: The choice of materials can be customized based on specific environmental exposures, such as corrosive substances or high temperatures. For instance, a liner used in chemical processing should have enhanced chemical resistance.
- Size Adjustments: Custom sizing can enhance fit and performance. Liners that match specific dimensions of equipment minimize leakage and capacity issues.
- Modularity: Designing liners for easy replacement or integration with existing systems can reduce downtime and maintenance costs.
Customizable liners allow industries to meet unique specifications while ensuring compliance with safety standards.
Customization ensures that discharge liners are not only functional but also effective in a variety of contexts.
In summary, both engineering principles and customization are integral to the field of discharge liners. They offer the ability to create tailored solutions that align with operational requirements, thereby improving reliability and efficiency. With the advancement of technology, these considerations must evolve to include adaptability to rapid changes in industry standards and practices.
Applications in Various Industries
The use of liners for discharge is essential across multiple sectors. Each industry has distinct needs that these liners address effectively. This section examines the varied applications of discharge liners in construction, mining, environmental management, and the oil and gas industry. Understanding these applications highlights the value and impact of discharge liners in real-world scenarios.
Construction and Infrastructure
In construction, liners are significant for controlling water flow and managing waste. They provide barriers to prevent contamination of soil and groundwater. Liners help in creating efficient drainage systems and stormwater management designs, which are crucial for urban planning. Their versatility allows for the adaptation to specific site requirements. This adaptability ensures that construction projects are resilient and compliant with environmental regulations.
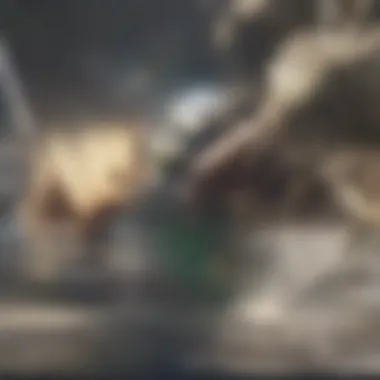

Mining and Resource Extraction
Mining activities involve the handling of hazardous materials. Liners serve to contain tailings and prevent pollutants from leaching into surrounding ecosystems. In resource extraction, the use of durable and chemically resistant materials is vital. These liners reduce the environmental impact of mining operations, helping companies meet regulatory standards. Their proper implementation can lead to increased recovery rates of valuable minerals, contributing to economic sustainability in mining practices.
Environmental Management
As society becomes increasingly conscious of environmental challenges, the role of discharge liners in environmental management cannot be overstated. These liners play a pivotal role in waste management, especially in:
Wastewater Treatment
Wastewater treatment relies heavily on effective liners to manage and contain liquids. Liners prevent leachate from contaminating nearby water sources. They enhance the efficiency of treatment facilities by improving the quality of treated water before it is released back into the environment. A key characteristic of wastewater treatment liners is their chemical resistance. This ensures they withstand various contaminants, thus ensuring operational success. However, high installation and maintenance costs can be a concern in some regions.
Contaminated Land Remediation
Contaminated land remediation involves cleaning and restoring polluted sites. Liners are essential in containing contaminants during the cleanup process. They provide a physical barrier that limits the spread of pollutants, facilitating more effective remediation strategies. The unique feature of remediation liners is their multi-layer design, often incorporating advanced materials that provide durability and chemical resistance. While they offer significant benefits in managing risk, their long-term sustainability and environmental impact must be evaluated thoroughly.
Oil and Gas Industry
In the oil and gas sector, liners protect against spills and leaks. They are crucial in keeping hazardous materials contained during drilling and extraction. The resilient nature of these liners helps to mitigate risks associated with chemical exposure. Their application extends to storage tanks and pipelines, where they reduce the possibility of environmental contamination. The oil and gas industry benefits from innovations in liner technology, which continue to evolve under stringent safety regulations.
Manufacturing and Production Processes
The process of manufacturing and production of liners for discharge is critical for ensuring their effectiveness across various applications. These processes affect not only the quality and durability of the liners but also their overall reliability, safety, and performance in the field. Understanding these elements provides deeper insights into what makes a liner suitable for diverse environments, particularly those involving harsh conditions and varying loads.
Production Techniques
Production techniques for discharge liners encompass a range of advanced methodologies. These techniques may vary significantly based on the materials used, such as metals, polymers, or composites. Each material demands unique processing methods to achieve optimal performance.
- Casting and Molding: For materials like metals and certain polymers, casting and molding are commonly employed. These processes allow for comprehensive customization in shape and size, providing liners that fit specific applications effectively.
- 3D Printing: This innovative technique has seen an increased adoption in recent years. Detailed designs can be created rapidly, enabling the production of complex geometries that would be difficult or impossible to achieve through traditional methods. Moreover, 3D printing can facilitate small-scale production, making it feasible for specialized applications.
- Extrusion: Particularly prevalent in the production of polymer liners, extrusion involves forcing material through a mold to create consistent shapes. This method is efficient for producing long sections of liners that may be used in pipelines or similar applications.
- Assembly Lines: In large-scale production, assembly lines streamline the process. Workers or machines perform specific tasks in a systematic order, enhancing efficiency and throughput. This method ensures consistency and quality throughout the entire production.
These techniques also necessitate consideration of numerous factors, such as cost, time, and the environmental impact of the manufacturing processes.
Quality Assurance Practices
Quality assurance is essential in the production of discharge liners. It ensures that each product meets specific standards and regulations, which ultimately protects the end-user and the environment from potential failures. Key practices in quality assurance include:
- Material Testing: Before production, testing materials for durability, chemical resistance, and thermal stability is crucial. Only materials that pass stringent tests are used in the manufacture of liners.
- Dimensional Inspections: Throughout the production process, continual inspections assess the dimensions of the liners. Any deviations from the specified dimensions can lead to failure in application.
- Performance Testing: After manufacture, it's vital to conduct performance tests under conditions that mimic real-world scenarios. This ensures that liners will function as expected when deployed.
- Certification and Compliance: Manufacturers must adhere to various international standards, such as ISO or ASTM. Achieving certification demonstrates a commitment to quality and enhances the credibility of the product.
"Quality assurance procedures are crucial not just for manufacturer accountability but also for ensuring that the end product is reliable and safe for use."
Regulatory and Safety Considerations
Regulatory and safety considerations play a critical role in the design and implementation of liners for discharge. These factors not only ensure compliance with legal standards but also protect the environment and human health. In many industries, the use of discharge liners is monitored closely to prevent contamination, accidents, and environmental damage. This section discusses the key compliance standards and risk assessment procedures relevant to the use of liners.
Compliance Standards
Compliance standards serve as guidelines that organizations must follow when using discharge liners. These standards can vary by region and industry but generally focus on:
- Health and Safety Regulations: Standards set by agencies like the Occupational Safety and Health Administration (OSHA) in the United States dictate safe practices for employees working with discharge liners. These regulations may include proper handling, storage, and usage protocols to mitigate risks.
- Environmental Guidelines: Organizations must comply with environmental regulations designed to protect ecosystems. The Environmental Protection Agency (EPA) and similar entities outline how discharge liners should function to minimize leakage, prevent contamination, and support safe disposal methods.
- Industry-Specific Standards: Different sectors may have unique compliance requirements. For example, the oil and gas industry adheres to guidelines from the American Petroleum Institute (API), while the construction industry might follow standards set by the American Concrete Institute (ACI).
These standards not only aid in achieving operational excellence but also enhance the credibility of the businesses by demonstrating a commitment to safety and environmental responsibility.
Risk Assessment Procedures
Conducting risk assessments is essential for understanding potential hazards associated with discharge liners. These procedures typically involve several key steps:
- Hazard Identification: Determine the possible risks tied to the use of liners, including chemical exposure, structural failure, or environmental contamination.
- Risk Analysis: Evaluate the likelihood and consequences of identified hazards. This might involve quantitative methods, such as statistical analysis, or qualitative methods relying on expert judgment.
- Control Measures: Identify and implement strategies to mitigate or eliminate risks. Options may include improved liner materials, enhanced containment systems, or revised operational procedures.
- Review and Monitoring: Establish a framework for continuous evaluation of the risks and effectiveness of control measures. Regular audits and assessments can help uphold safety standards and compliance.


By integrating these risk assessment procedures, organizations can reduce liability and improve overall safety, creating a safer environment for workers and the surrounding community.
"Compliance and risk assessment are integral to ensuring discharge liner effectiveness and safety across varied applications."
Recent Developments and Innovations
Recent advancements in the field of discharge liners are reshaping industry standards and practices. As technology evolves, so does the demand for more efficient, durable, and sustainable materials. The emergence of novel materials and innovative techniques signifies a transition toward enhanced performance and reduced environmental footprint. This section delves deeper into the latest research and technological integration that is pivotal for the future of discharge liners.
Advanced Materials Research
The study of new materials has taken center stage in the development of discharge liners. Researchers are increasingly focusing on enhancing properties such as durability, chemical resistance, and thermal stability. For instance, advanced polymers are being engineered to withstand harsher operating conditions, which improves their resilience against wear and tear.
Some promising directions include the use of nanomaterials which contribute to superior performance characteristics. The incorporation of carbon nanotubes or graphene can lead to lightweight yet extremely strong liners, capable of supporting heavy loads while minimizing energy consumption during production and use.
Moreover, researchers are also investigating biodegradable materials for certain applications. The shift towards sustainable practices is crucial, especially in industries like construction and environmental management, where traditional materials contribute to pollution and waste. By adopting biodegradable or recyclable options, companies can meet regulatory requirements while aligning with corporate social responsibility goals.
"The materials of tomorrow are not just improvements but represent a fundamental shift in how we perceive and utilize discharge liners in various applications."
Technological Integration
Technological advancements play a crucial role in enhancing the efficiency of discharge liners. Automation and data analytics are being utilized throughout the manufacturing process. Intelligent machinery can monitor production in real-time, ensuring consistency and quality while reducing human error.
In addition, the integration of the Internet of Things (IoT) into discharge liner systems allows for greater operational insight. Sensors embedded in the liners can provide immediate feedback regarding performance metrics, enabling proactive maintenance before issues escalate into costly repairs. This predictive approach not only prolongs the lifespan of the liners but also decreases downtime in industrial settings.
Another notable development is the application of 3D printing technology. This innovative technique allows for the rapid prototyping of liner designs and enables customization to meet specific project requirements. The ability to produce complex shapes reduces waste and enhances the efficiency of material usage.
Overall, the intersection of advanced materials research and cutting-edge technology marks a significant progress in the effectiveness and reliability of discharge liners. This ongoing evolution speaks to a future where discharge liners are not only functional but also integral to the sustainability of industrial operations.
Future Trends and Perspectives
The section on future trends and perspectives is essential for understanding how liners for discharge will evolve in the coming years. As technology advances and industries adapt to ever-changing environmental regulations, it is critical to assess potential developments in the design, materials, and applications of discharge liners. Emphasizing both sustainability and safety will be central to these trends, allowing industries to meet demands while minimizing their environmental footprint.
Emerging Technologies
Emerging technologies play a vital role in reshaping discharge liners. Innovations in manufacturing processes, such as additive manufacturing or 3D printing, enable the creation of complex liner geometries that were previously difficult or impossible to achieve. These technologies not only reduce material waste, thus supporting sustainability, but also lower production costs.
Additionally, advancements in sensor technology can be integrated into discharge liners. Embedding sensors would provide real-time data on the condition of the liner, allowing operators to monitor wear and tear. This could lead to improved maintenance strategies, enhancing longevity and performance.
Moreover, materials science is making significant strides. Research into nanomaterials and smart materials could deliver liners with enhanced properties—higher resistance to chemicals, better thermal stability, and increased flexibility. Such innovations hold promise for industries requiring high-performance liners under extreme conditions.
Sustainability Considerations
Sustainability is no longer a choice; it is a requirement. The future trends for liners will heavily emphasize sustainable practices. This includes the selection of materials that ensure a lower environmental impact throughout their life cycle. For instance, the use of biodegradable materials or recycled composites can significantly reduce pollution and waste.
Additionally, reducing resource consumption during production is also a key point. Utilizing technologies like lean manufacturing can help minimize energy use, thereby supporting environmental objectives. Companies are increasingly looking at their supply chains to make sure every part of the process aligns with these goals.
The regulatory landscape is also evolving, with stricter guidelines focusing on environmental protection and sustainability. This shift means that companies manufacturing discharge liners need to be proactive in adapting to these changes, ensuring compliance and promoting sustainability.
Sustainability is integrated not just as a goal but as an essential aspect of the design, production and deployment of discharge liners.
In summary, the future of liners for discharge is bright with advancements in technology and a strong focus on sustainability. Companies must remain agile to adopt these changes and innovations. By doing so, they can enhance their product performance while contributing positively to the environment.
Epilogue
The conclusion of this article wraps up the critical aspects concerning liners for discharge. These components play a significant role across various sectors, ensuring both efficiency and safety in applications. With a focus on materials, design, and the latest innovations, understanding liners for discharge becomes essential for professionals involved in multiple industries.
Summary of Key Points
- Definition and Purpose: Liners for discharge serve specific functions, such as protection against corrosive substances and facilitating the smooth flow of materials.
- Material Selection: The choice of material—be it metals, polymers, or composites—affects durability, chemical resistance, and thermal stability, thereby influencing the overall performance of the liners.
- Design Considerations: Engineers must account for various factors, including the environment and use-case scenarios, to ensure the liner's functionality and longevity.
- Applications in Various Industries: From construction and mining to oil and gas, the applications of discharge liners are vast and varied, showcasing their importance in multiple contexts.
- Regulatory and Safety Considerations: Compliance with standards and thorough risk assessments are crucial for ensuring that these liners perform safely and effectively.
- Recent Developments and Innovations: Ongoing research into advanced materials and technology enhances the efficiency and effectiveness of liners, making them vital in contemporary practices.
- Future Trends: The industry is witnessing a drive towards sustainability, prompting the integration of eco-friendly materials and processes.
Final Thoughts
"Innovations in discharge liners can significantly reduce environmental impact while improving safety and efficiency across sectors."
For anyone involved in the selection, design, or application of liners for discharge, continually engaging with recent studies and advancements will be crucial. The insights provided here can serve as a springboard for deeper exploration into this vital aspect of industrial design and application.