Manufacturing Composites: Processes and Trends
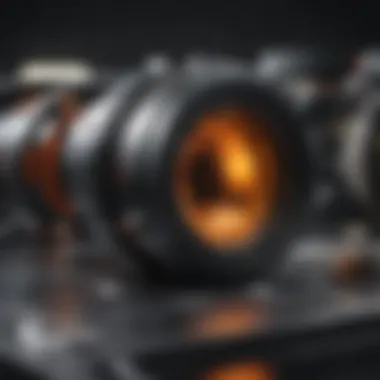
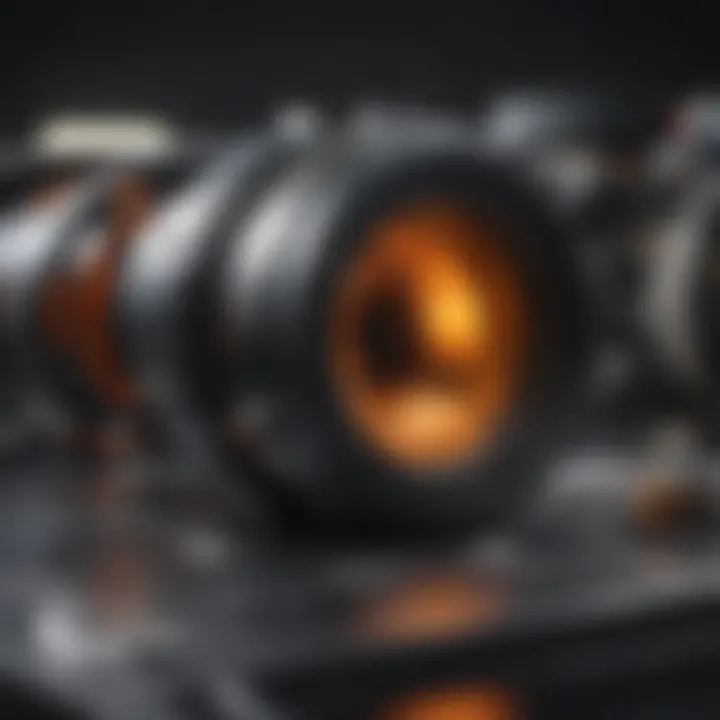
Intro
Composite materials play a critical role in modern manufacturing, offering superior properties such as strength, lightweight characteristics, and resistance to environmental factors. This makes them particularly useful across various industries, including aerospace, automotive, civil engineering, and consumer goods. Composites are produced through various processes that combine two or more distinct materials, resulting in a product that has improved performance compared to its individual components. The exploration of the manufacturing processes, applications, and emerging trends in composites is essential for students, researchers, educators, and professionals who wish to stay at the forefront of material technology.
Key Concepts and Terminology
Definition of Key Terms
Understanding the terminology used in composite manufacturing is crucial for grasping the complexities of the field. Key terms include:
- Composite Material: A material made from two or more constituent materials with significantly different physical or chemical properties.
- Matrix: The continuous phase in a composite material, which surrounds and supports the reinforcement materials.
- Reinforcement: The materials that provide additional strength and stiffness to the composite.
- Manufacturing Process: The methods used to create composite materials, including techniques like pultrusion, filament winding, and resin transfer molding.
Concepts Explored in the Article
The article dives into several important concepts:
- The various manufacturing processes used in producing composites.
- The diverse applications of composite materials in different industries.
- The challenges and limitations faced in composite manufacturing.
- The environmental impacts of composites and their sustainable alternatives.
- Future trends signaling advancements in composite technologies and applications.
Findings and Discussion
Main Findings
The exploration of composite manufacturing reveals several significant findings:
- Advanced Manufacturing Techniques: Techniques like additive manufacturing (3D printing) are revolutionizing how composites are made, allowing for more complex geometries and reduced waste.
- Diverse Applications: Composites are used in aircraft components, automotive parts, sports equipment, and environmentally sustainable construction materials.
- Challenges in the Sector: The industry faces challenges related to high production costs, recycling difficulties, and the need for better quality assurance are pertinent to the advancement of composite materials.
"The adaptability and lightweight nature of composite materials position them as key materials for the future of high-performance applications."
Potential Areas for Future Research
Future research may focus on:
- Improving biodegradable composite materials to reduce environmental impact.
- Exploring new manufacturing methods that enhance efficiency and reduce costs.
- Investigating the long-term performance and recyclability of existing composite materials.
- Developing standard testing methods for improved quality assurance in composite products.
Prelims to Composite Materials
Composite materials play a fundamental role in various industries, combining different materials to achieve superior performance characteristics that cannot be obtained from a single component. Understanding composite materials is crucial for engineers, researchers, and students who seek to innovate and optimize design and manufacturing processes.
The importance of composites lies in their unique properties, which include high strength-to-weight ratios, corrosion resistance, and flexibility in design. These features enable the use of composites in critical applications ranging from aerospace to automotive engineering. As industries continue to demand materials that enhance efficiency while reducing weight and cost, the relevance of composites becomes increasingly prominent.
Definition of Composites
Composites are materials formed by two or more constituent materials with significantly different physical or chemical properties. This combination produces a material with characteristics different from the individual components. Commonly, a composite consists of a matrix, which supports and binds the reinforcement material, enhancing its overall performance.
History and Evolution
The development of composite materials has deep historical roots, starting from natural compounds like wood and straw used in ancient structures. Over time, the evolution accelerated with the introduction of synthetic materials in the 20th century. The aerospace and automotive industries quickly adopted these materials due to performance advantages. Significant innovations such as fiberglass and carbon fiber composites have transformed manufacturing processes, leading to greater efficiency and sustainability.
Types of Composites
Different types of composites have emerged, each with unique characteristics and applications. The primary categories include:
- Metal Matrix Composites: These composites include metals like aluminum or titanium combined with reinforcing materials such as ceramic or carbon fibers. They offer numerous advantages, such as higher melting points, thermal stability, and increased stiffness. Their unique property of excellent wear resistance makes them valuable in automotive and aerospace applications.
- Polymer Matrix Composites: Often referred to as polymer composites, they are made of polymer resins reinforced with materials like glass or carbon fibers. Their lightweight nature, resistance to corrosion, and ease of manufacturing contribute to their popularity across industries. They are extensively used in the automotive sector for producing lightweight vehicle components, leading to improved fuel efficiency.
- Ceramic Matrix Composites: These composites are made from ceramic materials that are reinforced with other materials, providing high thermal stability and strength. They are particularly beneficial where high-temperature resistance is required, such as in aerospace and defense applications. Their brittleness presents a trade-off with enhanced performance, making them specialized but crucial in certain sectors.
Raw Materials in Composite Production
The choice of raw materials is crucial in the field of composite production. Each material has distinct properties that determine its suitability for specific applications. Understanding these materials allows engineers and manufacturers to optimize performance and enhance the quality of the composites produced. The benefits of careful selection include improved durability, increased strength-to-weight ratios, and overall cost-effectiveness.
Fibers: Types and Characteristics
Fibers form the backbone of composite materials, contributing significantly to their strength and stiffness. There are several types of fibers used in composite production, each with unique characteristics and benefits.
Glass Fibers
Glass fibers are one of the most widely used fibers in composite manufacturing. They provide excellent tensile strength and are resistant to chemical attack. Their low cost and good availability make them a popular choice for various applications.
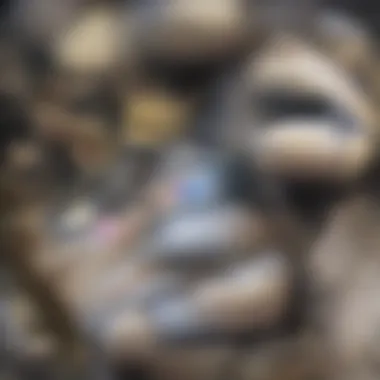
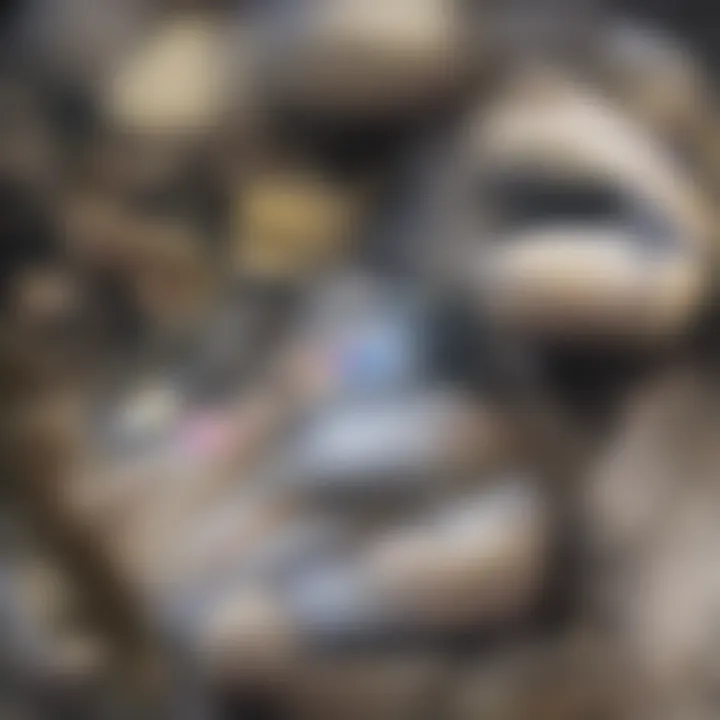
Key characteristic: Glass fibers have a high strength-to-weight ratio, making them valuable in industries where weight reduction is crucial.
Unique feature: They can be easily molded and shaped, allowing for complex structures. However, glass fibers are not as stiff as carbon fibers, which limits their performance in highly demanding applications.
Carbon Fibers
Carbon fibers are favored for their superior mechanical properties, particularly their high stiffness and low density. This makes them ideal for high-performance applications such as aerospace and automotive sectors.
Key characteristic: Carbon fibers have a remarkable strength-to-weight ratio that exceeds that of glass fibers, making them a top choice for situations requiring lightweight materials without compromising strength.
Unique feature: They are more expensive than glass fibers but offer better performance. The downside includes their brittleness, which can lead to failures under certain conditions if not properly managed.
Natural Fibers
Natural fibers have gained attention for their sustainability and environmental benefits. Materials such as hemp, jute, and flax are used increasingly in composite applications.
Key characteristic: Natural fibers are renewable and biodegradable, making them an eco-friendly option.
Unique feature: They provide a good balance of weight and strength but can have variable properties depending on the source. Their primary disadvantage is moisture absorption, which can affect the overall performance of the composites in humid environments.
Resins: Role and Types
Resins act as the matrix in composite materials, binding the fibers together. They contribute to the overall strength and durability of the composite. Two main types of resins are used in the production of composites.
Thermosetting Resins
Thermosetting resins, such as epoxy, polyester, and vinyl ester, are used extensively in composite manufacturing. Once cured, these resins do not melt again. This property makes them robust and heat resistant.
Key characteristic: They provide excellent adhesion and mechanical integrity, supporting high-performance composites.
Unique feature: Their cross-linking structure enhances the durability of the composites. The downside is that their manufacturing process can be time-consuming due to the curing process, which requires heat.
Thermoplastic Resins
Thermoplastic resins, like polyethylene and polypropylene, are gaining popularity due to their reworkability. They can be melted and reshaped multiple times without losing their fundamental properties.
Key characteristic: This property allows for easier recycling and manufacturing.
Unique feature: Their flexibility offers an advantage in applications requiring resilience, such as sports equipment. However, they may not provide the same level of thermal or chemical resistance as thermosetting resins.
Additives and Fillers
Additives and fillers play a significant role in enhancing the properties of composite materials. They can modify mechanical, thermal, electrical, and aesthetic properties. The use of these components can lead to improved performance at a reduced cost. Typical additives include flame retardants, UV stabilizers, and colorants.
By understanding the functionalities of raw materials, manufacturers can create composites tailored for specific applications, enhancing their performance and sustainability.
Manufacturing Processes for Composites
The manufacturing processes for composites are pivotal in determining their final properties and performance. These processes not only define the structural integrity of the composite material but also influence factors such as weight, durability, and cost. The selection of an appropriate technique can lead to enhanced production efficiency and a significant reduction in waste, vital considerations in today’s manufacturing landscape. Composites are tailored for specific applications, and effective manufacturing processes help in fine-tuning these materials according to industry requirements. Understanding these processes allows students, researchers, and professionals to make informed decisions regarding material selection and application.
Hand Lay-Up Technique
The hand lay-up technique is one of the most traditional methods for manufacturing composite materials. This process involves manually placing layers of reinforcement material, typically fiberglass or carbon fiber, in a mold. Then, a resin is applied to these layers, soaking them to form a solid piece once cured.
One of the key advantages of the hand lay-up technique is its flexibility. It allows for the creation of complex shapes and sizes, which is beneficial in applications like boat hulls and large structural components. However, the technique can be labor-intensive and may lead to inconsistency in thickness, which affects the mechanical properties of the finished product.
Filament Winding
Filament winding is a highly efficient manufacturing process, particularly suitable for producing cylindrical or spherical parts, such as pressure vessels and pipes. In this method, continuous fibers are saturated with resin and wound under tension around a rotating mandrel in a predetermined pattern.
This technique allows for precise control over fiber orientation, resulting in improved mechanical properties and reduced weight. Filament winding is valued for its ability to create strong, lightweight structures. It also minimizes material waste, making it an attractive option for large-scale production.
Resin Transfer Molding
Resin transfer molding (RTM) is a closed-mold process that allows for high production rates and consistent quality. In RTM, dry reinforcement materials are placed in a mold, which is then closed. Liquid resin is injected under pressure into the mold, saturating the fibers and solidifying upon curing.
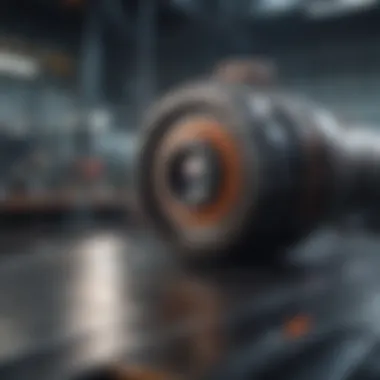
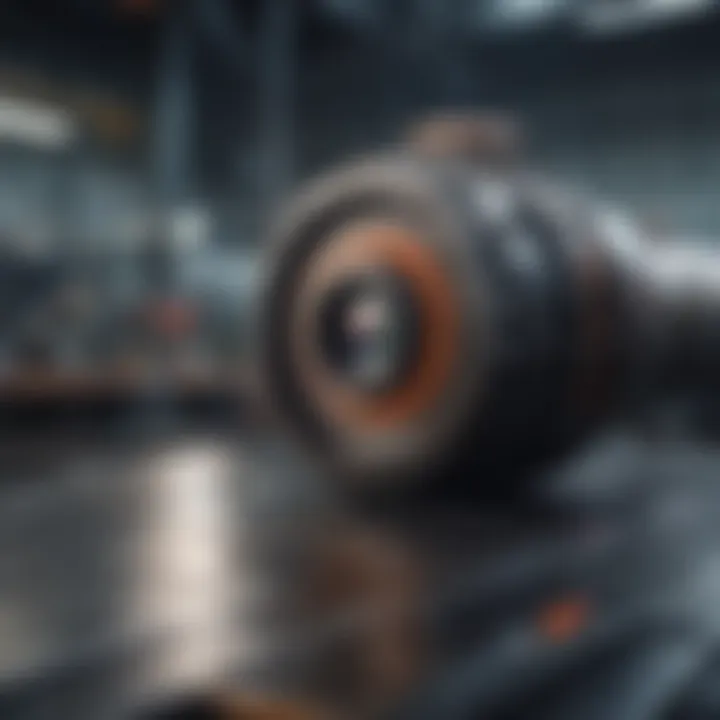
This method offers several advantages, such as reduced VOC emissions compared to open processes and improved surface finish. It can be used for large components and complex geometries, making it suitable for the automotive and aerospace industries.
Automated Fiber Placement
Automated fiber placement (AFP) is a high-tech method of laying down composite materials. This technique uses robotic systems to precisely place unidirectional tape on a mold surface. The automation leads to a reduction in labor costs and production time, while also enhancing repeatability and consistency of the layup process.
AFP is particularly beneficial for large aerospace components where weight reduction and strength are critical. The technology allows for complex shapes and geometries, meeting the stringent requirements of modern engineering.
3D Printing of Composites
3D printing, or additive manufacturing, is gaining traction in the composite sector. This innovative process allows for the creation of parts by adding material layer by layer, which can be particularly advantageous for rapid prototyping as well as complex designs.
Current advancements have enabled the use of composite materials in 3D printing, merging the benefits of design flexibility with the advantageous properties of composites. Industries such as aerospace and automotive are exploring this method for producing lighter and more intricate structures. However, challenges remain in terms of material compatibility and the optimization of mechanical properties.
Advances in composite 3D printing technology may enable custom designs that traditional methods cannot achieve, expanding the capabilities of manufacturers.
Quality Control in Composite Manufacturing
Quality control plays a crucial role in ensuring that composite materials meet stringent performance standards. This is essential due to the critical applications of composites in industries such as aerospace, automotive, and construction. Without proper quality control, the integrity and reliability of composite structures can be compromised, leading to potential failures. The primary goal of quality control is to guarantee that every stage of composite manufacturing adheres to defined specifications, resulting in high-performance end products.
Ensuring consistent quality protects both manufacturers and end-users. Effective quality control processes lead to reduced waste, lower costs, and enhanced customer satisfaction. In composite fabrication, quality issues often arise during material selection, combination of materials, and throughout the processing techniques. Therefore, monitoring and testing must be integrated at each stage of the production cycle for optimum results.
Inspection Techniques
Quality control in composites relies heavily on specific inspection techniques. These methods are employed to identify defects and assess the structural integrity of composite components. Two prominent inspection techniques are ultrasonic testing and X-ray inspection.
Ultrasonic Testing
Ultrasonic testing is a non-destructive testing method that utilizes high-frequency sound waves to detect internal flaws within materials. This technique is highly accurate in identifying defects such as voids, delaminations, and inclusions in composite materials.
A key characteristic of ultrasonic testing is its ability to provide real-time data about the material's internal structure. This makes it a popular choice for engineers and quality control professionals. One unique feature of this technique is its capacity to inspect large areas quickly, while still offering detailed analysis.
However, ultrasonic testing does have some disadvantages. It requires skilled operators to interpret the results accurately, and the complexity of the test setup might be a barrier in some cases. Still, its effectiveness in providing vital information about composite integrity cannot be overlooked.
X-Ray Inspection
X-ray inspection is another invaluable tool in the quality control of composite materials. This technique employs X-rays to create images of the internal structure, allowing for the detection of hidden defects. X-ray inspection is known for its detailed imaging capabilities, making it suitable for complex geometries often found in aerospace and automotive components.
What makes X-ray inspection particularly beneficial is its ability to visualize the entire volume of the composite. This enables more comprehensive assessments compared to surface-level inspections.
On the contrary, one notable disadvantage of X-ray inspection is the exposure to radiation, both for operators and the environment, which necessitates stringent safety measures. Additionally, the process can be time-consuming and costly if extensive scans are required. Despite these hurdles, X-ray inspection remains a preferred option in many critical applications due to its high level of accuracy and depth of analysis.
Standards and Certifications
Adhering to industry standards and certifications is vital in the realm of composite manufacturing. These guidelines ensure that materials and processes meet accepted performance and safety requirements. Organizations such as the American Society for Testing and Materials (ASTM) and International Organization for Standardization (ISO) provide frameworks that guide manufacturing practices.
Compliance with these standards not only enhances product quality but also instills confidence in consumers and stakeholders. Certification processes often involve rigorous testing and documentation, which can contribute to higher production costs initially. However, they are essential for long-term sustainability and reputation in the competitive market of composite materials.
Applications of Composite Materials
Composite materials have gained significant traction across various industries, offering unique properties that enhance performance and efficiency. Their application transcends mere material utility; it embodies the essential evolution in engineering solutions adapted to current demands. The integration of composite materials in several sectors brings forth numerous benefits, such as reduced weight, increased strength, and improved resistance to environmental challenges. Furthermore, as industries strive for more sustainable practices, composites present viable alternatives that can align with these goals.
Aerospace Industry
Within the aerospace sector, composites play a pivotal role in revolutionizing aircraft design and performance. The use of light-weight materials such as carbon fiber reinforced polymers allows for substantial weight reductions. This translates to fuel efficiency and enhanced payload capacity. The composite structures also offer superior strength-to-weight ratios, essential for maintaining safety standards while optimizing performance. Modern aircraft, such as the Boeing 787 Dreamliner, showcase the extensive utilization of advanced composite materials, illustrating their importance in the industry.
- Additionally, composites provide better resistance against corrosion and fatigue, leading to longer service life and reduced maintenance costs.
- The capability to mold composites into complex shapes grants designers greater freedom to innovate.
Automotive Sector
In the automotive sector, the application of composite materials contributes significantly to fuel efficiency and performance enhancement. Cars today are increasingly being designed with components made from reinforced polymers and metal matrix composites. These materials, by reducing the overall weight, improve fuel consumption and lower emissions.
- The shift towards electric vehicles (EVs) has further increased the reliance on composites, as lighter vehicles lead to improved battery life and efficiency.
- Safety is another consideration; composites can absorb impact better than traditional materials, offering enhanced protection for passengers in case of accidents.
Civil Engineering and Construction
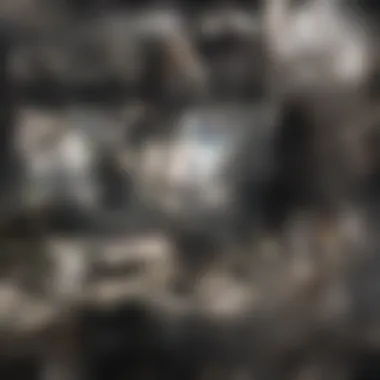
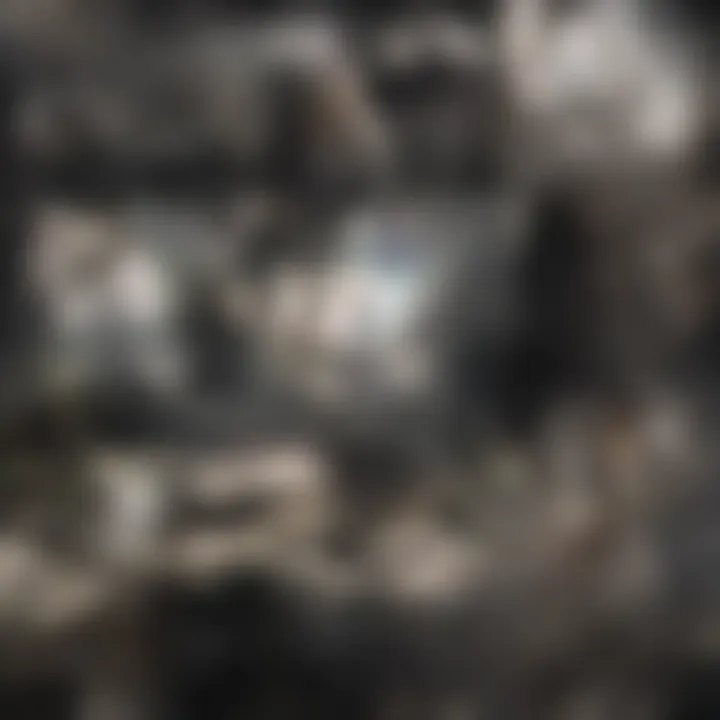
Composite materials have found their footing in civil engineering and construction, where durability and stability are paramount. Structures utilizing fiber-reinforced polymers are increasingly common, particularly in seismic retrofits and bridge renovations. These composites provide exceptional tensile strength and resistance to environmental degradation, making them ideal for long-lasting infrastructure.
- Their lightweight nature simplifies handling and installation, reducing labor costs and project timelines.
- The versatility in design also allows for creative architectural outcomes, pushing the boundaries of conventional construction methods.
Consumer Goods
In the domain of consumer goods, composites are redefining product standards. From sporting equipment to electronics, the advantages of using composite materials are unmistakable. For instance, items like bicycles or high-performance golf clubs incorporate composite materials to enhance durability while minimizing weight.
- This also applies to products such as smartphones and laptops, where composite casings provide strength without adding bulk.
- The trend towards eco-friendly materials has prompted manufacturers to explore bio-composites, which offer a sustainable alternative that aligns with consumer demands for environmentally responsible products.
The applications of composite materials are vast and continually evolving, addressing key challenges faced by industries today. As research advances and technology progresses, composites are positioned to play an even more significant role in future innovations.
Challenges in Composite Manufacturing
The manufacturing of composite materials presents significant challenges that impact their widespread adoption and effectiveness. As industries increasingly lean towards composites due to their favorable properties, they also encounter several barriers that merit careful consideration. This section delves into the primary challenges in composite manufacturing, emphasizing cost implications and environmental concerns, both of which play pivotal roles in shaping the future of this technology.
Cost Implications
Cost is a critical factor in the composite manufacturing process. The intricate production methods and specialized materials involved make composites more expensive compared to traditional materials like metals or plastics. High initial investment in equipment and technology is often required. This leads to several economic challenges:
- Material Costs: The raw materials, such as advanced fibers and resins, skew towards higher price points than conventional options, making initial production costs steep.
- Processing Costs: Techniques like automated fiber placement and resin transfer molding demand significant capital. Coupled with the expertise needed to operate advanced machinery, operating costs rise.
- Economies of Scale: Many companies struggle to achieve the volume necessary for significant cost reductions. Small production runs mean that costs do not decrease as they would with large-scale production.
Despite these barriers, it is crucial for manufacturers to analyze their operations to identify potential areas for cost savings. Companies can consider partnerships for bulk material purchasing or invest in technology that enhances efficiency in the long term.
Environmental Concerns
Environmental issues are increasingly coming to the forefront of composite manufacturing discussions. As sustainability becomes a focal point in industry, several key concerns arise:
- Waste Generation: The production process often yields significant waste material, which presents a challenge for sustainable practices.
- Recycling Difficulties: Many composite materials are not easily recyclable. The combination of different materials complicates reprocessing efforts and contributes to landfill concerns.
- Chemical Use: Some resins involve volatile organic compounds, which can have detrimental environmental effects during both production and disposal phases.
"Addressing environmental concerns in composite manufacturing is not just a compliance issue; it's fundamental for the long-term viability of the industry."
Industries are hence urged to innovate, seeking out new materials and methods that minimize waste and promote recyclability. The exploration of biodegradable resins and closed-loop systems can present viable strategies to mitigate environmental impact.
Future Trends in Composite Manufacturing
The landscape of composite manufacturing is undergoing significant transformation as various industries embrace cutting-edge technologies and materials. This section critically examines the future trends set to affect the production, application, and market dynamics of composites. Recognizing these trends is essential for stakeholders, including engineers, researchers, and industry professionals, who aim to stay ahead in this rapidly evolving field.
Sustainability in Composites
Sustainability has become a pivotal focus in composite manufacturing. With increasing environmental awareness, there is a pressing need for materials and processes that reduce carbon footprints and promote eco-friendliness. Composites, traditionally known for their durability and strength, are now being designed with sustainability in mind.
- Biodegradable Materials: Research into biodegradable composites is gaining traction. These materials aim to minimize environmental impact after their lifecycle. Products utilizing elements like natural fibers and bio-resins are examples of this trend.
- Recycling Techniques: Innovative methods for recycling composite materials are emerging. Advances in chemical recycling allow for the breakdown of composites into their original components, reusable for new manufacturing processes.
"The integration of sustainability into composite manufacturing not only addresses environmental concerns but also enhances product appeal in a market that increasingly values eco-conscious practices."
Innovations in Materials Science
The field of materials science is pivotal in defining the characteristics and capabilities of composites. Ongoing research is unveiling new composite formulations that enhance performance metrics drastically, responding to demands for lighter, stronger, and more functional materials.
- Nanocomposites: Incorporating nanomaterials can significantly improve the mechanical properties of composites. These materials exhibit extraordinary strength-to-weight ratios, enhancing applications in industries like aerospace and automotive.
- Phase Change Materials: The development of phase change composites is another innovation. These materials can absorb and release heat, providing thermal management solutions in diverse applications from electronics to construction.
Automation and Industry 4.
The advent of Industry 4.0 is reshaping the manufacturing landscape, including composite production. The integration of automation technologies and data-driven processes is streamlining manufacturing, increasing efficiency, and reducing costs.
- Smart Manufacturing: By employing Internet of Things (IoT) devices, manufacturers can gain real-time insights into production processes. This leads to better quality control and reduces the likelihood of defects in composite products.
- Robotics in Production: The use of robotics in composite manufacturing processes, such as automated fiber placement, is becoming more commonplace. Robots can execute repetitive tasks with high precision, thereby improving output consistency and efficiency.
Incorporating these trends into composite manufacturing practices presents unique opportunities and challenges. As industries continue to innovate, understanding these developments is crucial for adapting to the future landscape of composite materials.
End
The topic of composite manufacturing is pivotal in understanding the intersection of advanced engineering and material science. In this article, we examined various aspects of composites, emphasizing their significance in today’s industries. As we have seen across the sections, composite materials are not merely alternatives to traditional materials; instead, they provide unique properties that enhance performance.
Firstly, the manufacturing processes discussed, such as hand lay-up, resin transfer molding, and automated fiber placement, are vital methodologies that shape the characteristics of composites. Each process has its own set of advantages and limitations, making it significant to select the right method based on the application. For instance, 3D printing of composites represents one of the innovations that can revolutionize the production landscape, allowing for intricate designs and reduced waste.
Moreover, the applications outlined in sectors like aerospace, automotive, and civil engineering showcase the versatility of composites. This versatility brings about benefits, such as weight reduction, improved strength-to-weight ratios, and enhanced durability. As the demand for lightweight, strong materials increases, the applications of composites are expected to expand further.
However, challenges exist, including cost implications and environmental concerns. The need for sustainable practices and more eco-friendly materials is growing. Understanding these challenges enables professionals in the composite industry to strategize effectively.
Looking forward, the trends in sustainability, innovations in materials science, and the influence of Industry 4.0 position composites as a key focus for future developments in manufacturing. These trends will not only enhance production efficiency but also address the increasing global demand for sustainable and high-performance materials.