Metal Design Machines: An In-Depth Exploration
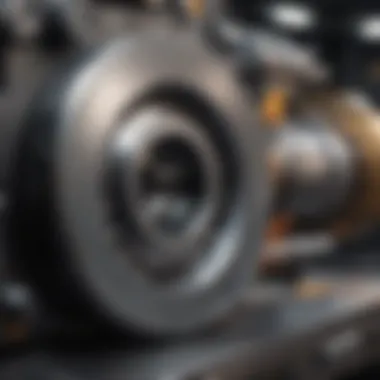
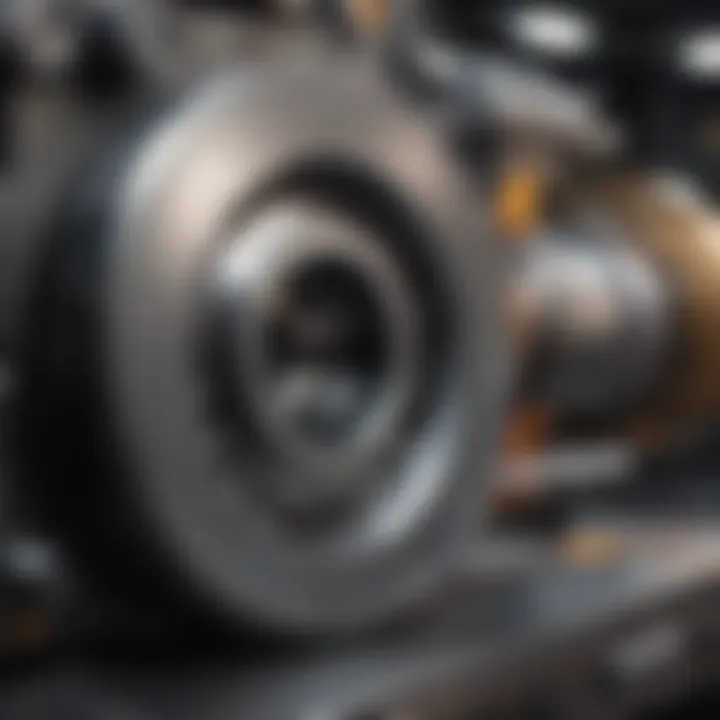
Key Concepts and Terminology
Understanding the intricate world of metal design machines requires familiarization with specific terminology and concepts. This section aims to provide clarity on key terms and ideas that will aid in comprehending the operational principles and applications of these machines.
Definition of Key Terms
- Metal Design Machines: These are specialized tools used in the design, fabrication, and processing of metal components. They include a range of machinery such as CNC lathes, milling machines, laser cutters, and additive manufacturing systems.
- CNC (Computer Numerical Control): This technology allows machines to be controlled via a computer, enhancing precision and automation in manufacturing processes.
- Additive Manufacturing: A process of creating objects by adding material layer by layer, commonly known as 3D printing. This method contrasts traditional subtractive manufacturing techniques, where material is removed from a solid block.
- Laser Cutting: A method that utilizes lasers to cut materials with high precision, often used in metal work due to its accuracy and clean edges.
- Sheet Metal Fabrication: The process of converting flat sheets of metal into final products through cutting, bending, and assembling.
Concepts Explored in the Article
The article delves into various concepts that underpin metal design machines. These include:
- Technological Evolution: An exploration of how metal design machines have advanced over the years in terms of efficiency and capabilities.
- Applications Across Industries: Investigation into how these machines are utilized in sectors such as automotive, aerospace, and machinery.
- Material Processing Capabilities: A detailed look at different materials these machines can work with and the implications for design and manufacturing.
- Challenges and Innovations: Discussion of current challenges in the industry, including sustainability, and the innovative solutions being developed in response.
Findings and Discussion
Main Findings
Through analysis, several key findings emerge:
- Metal design machines are integral to modern manufacturing, significantly improving efficiency and precision.
- The transition towards automation and digital technologies, such as CNC and additive manufacturing, is reshaping the industry landscape.
- There is a growing importance placed on sustainability, leading to innovations that minimize waste and energy consumption.
Potential Areas for Future Research
A closer examination of the future of metal design machines reveals multiple avenues for research:
- Sustainability Practices: Investigating methods to improve the environmental impact of metal fabrication processes.
- Integration of AI and Machine Learning: Exploring how these technologies can further enhance the capabilities of metal design machines.
- Material Science Advancements: Analyzing how new materials and composite technologies can expand the applications of metal design machines.
Future developments in metal design machines will depend on a blend of technological innovation and sustainable practices.
By understanding these key concepts and the findings derived from current practices, students, researchers, and professionals can gain a comprehensive insight into the importance of metal design machines in today's industrial environment.
Prelude to Metal Design Machines
Metal design machines play a crucial role in modern manufacturing and engineering. They are essential for creating complex metal components used across various industries. Understanding these machines helps one appreciate their impact on productivity, precision, and efficiency in metal manufacturing. This section sheds light on the fundamental aspects of metal design machines, their significance, and their historical progress.
Definition and Importance
Metal design machines are machines specifically designed for shaping, cutting, and forming metals into desired configurations. These machines include CNC mills, laser cutting systems, and 3D metal printers, each serving unique purposes. Their importance cannot be overstated.
Metal design machies enhance precision in manufacturing, reducing waste and improving quality control. They allow engineers and designers to bring their concepts to life with high accuracy. This precision is critical in sectors such as aerospace and automotive, where even the smallest error can lead to significant issues.
Companies benefit from adopting these machines. They experience increased efficiency, reduced labor costs, and faster turnaround times for projects. Furthermore, as industries evolve, metal design machines continue to innovate to meet new demands in functionality and design.
Historical Development
The history of metal design machines traces back to the industrial revolution. Early methods relied on manual labor and rudimentary tools. The advent of mechanization marked the beginning of a new era. In the late 19th and early 20th centuries, advancements in machining technology emerged. Machines became more sophisticated, incorporating steam power and later electricity.
By the mid-20th century, numerical control (NC) systems were introduced. This technology allowed machines to be operated using codes to dictate cutting patterns. It was a pivotal point that led to the development of computer numerical control (CNC) machines.
CNC machines revolutionized the industry. They provided unprecedented precision and the ability to automate complex tasks. Over the years, additional enhancements such as laser cutting and 3D printing entered the scene, offering even more capabilities.
In summary, metal design machines have evolved significantly since their inception. Their development reflects a continuous push towards automation, precision, and innovation, defining the landscape of modern manufacturing.
Types of Metal Design Machines
Understanding the types of metal design machines is critical for any one involved in the metalworking or manufacturing sectors. These machines not only dictate the efficiency of production but also influence the quality and precision of the final product. By familiarizing ourselves with the different machine types, professionals can make informed decisions regarding their applications, thereby optimizing their metal design processes. Six primary categories dominate the landscape of metal design machines: CNC machines, laser cutting machines, and 3D metal printers. Each presents unique benefits and considerations, underscoring the diversity of technologies available.
CNC Machines
CNC (Computer Numerical Control) machines have transformed the landscape of metal design. These machines operate based on computer-generated commands, allowing for high precision and repeatability in machining operations. They encompass a range of tools such as lathes, mills, and routers. The use of CNC machines enhances operational efficiency by streamlining the manufacturing process. Without them, achieving the necessary precision across various applications would be significantly more difficult.
One of the primary advantages of CNC machines is their ability to handle complex geometries. As industries demand intricate designs, these machines allow for detailed cuts and high tolerances. The programming aspect also provides flexibility; if a design changes, the CNC machine can be quickly reprogrammed to accommodate new specifications. However, there are some challenges associated with CNC machines. Initial setup costs can be high, and they require skilled operators to maximize their potential.
Laser Cutting Machines
Laser cutting technology offers another significant method for metal design. Utilizing focused laser beams, these machines cut through various metal types with exceptional accuracy. The process involves directing a laser at the material, leading to melting or vaporization of the metal, resulting in clean edges without mechanical stress. This capability makes laser cutting machines preferred in multiple sectors, including automotive and aerospace.
One major benefit of laser cutting machines is their speed. They can produce parts in less time compared to traditional methods, helping companies meet tight production schedules. Additionally, the precision offers yields of smaller tolerances, reducing material waste. Nonetheless, challenges such as the initial capital investment and the limitations of thickness in some metal types should be considered before implementation.
3D Metal Printers
3D metal printing is a relatively new entrant in the field of metal design machines. This revolutionary technology allows for the additive manufacturing of metal products by layering material to build a part from the ground up. The process not only supports complex geometries but also encourages design innovation, as traditional constraints on manufacturing are minimized.
The advantages of 3D metal printers include rapid prototyping and customization. They enable businesses to develop parts tailored to specific needs without needing extensive retooling. However, limitations exist, such as slower production speeds compared to other machines. The material costs can also be higher, requiring a careful balance in selecting applications for this technology.
In summary, the realm of metal design machines is diverse, each type offering distinct advantages and challenges. The choice of machine depends on production requirements, cost considerations, and design intricacies. By understanding these various technologies, professionals can better navigate the complexities of metal design, leading to improved outcomes in their projects.
Operational Principles of Metal Design Machines
Understanding the operational principles of metal design machines is crucial for grasping how these intricate systems work. The interaction between technology and metal can result in significant advancements in manufacturing and design efficiency. This section will cover two key areas: Computer Numerical Control (CNC) and Material Interaction Dynamics. Each plays a vital role in ensuring that metal design machines operate effectively and achieve their intended goals.
Computer Numerical Control
Computer Numerical Control, or CNC, represents a critical technological advancement in the operation of metal design machines. CNC involves the use of computer systems to control the movements and functions of machinery. By translating computer-aided design (CAD) models into precise movements, CNC machines can produce complex parts with high accuracy.
This technology offers numerous benefits:
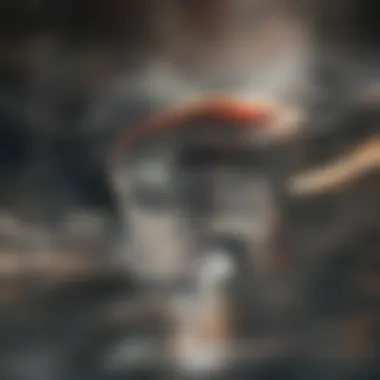
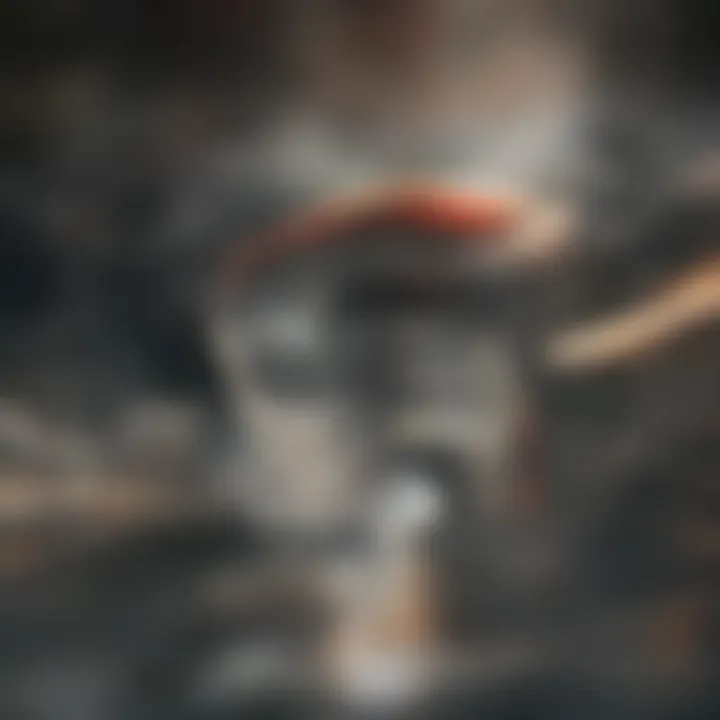
- Precision and Consistency: CNC machines operate with minimal human intervention, leading to a standardization of processes. This results in consistently high-quality outputs.
- Automation: CNC allows for extensive automation in production settings. This reduces the time required for manual setup and operator skill levels needed, leading to increased operational efficiency.
- Flexibility: With CNC, it is easy to switch between different designs and specifications without extensive downtime, making it highly adaptable in modern manufacturing environments.
Employing CNC technology also requires consideration of the programming aspect. G-code, a language used to create instructions for CNC machines, must be mastered to utilize these machines effectively. Operators must ensure that the environment is safe for using such machines, keeping in line with safety standards.
Material Interaction Dynamics
The dynamics of how materials interact with machines is another pivotal aspect in the metal design field. Understanding these dynamics can lead to better designs and improved machine capabilities. Materials behave differently under varied conditions, such as temperature and pressure. Metal design machines must accommodate these factors to avoid issues like material fracture or deformation.
Considerations for material interaction dynamics include:
- Thermal Effects: Different metals have distinct thermal properties. For example, aluminum expands more than steel when heated. Thus, understanding how heat affects metal performance during cutting or shaping operations is essential.
- Mechanical Properties: The strength, ductility, and hardness of metals can influence how a machine processes them. For instance, tougher metals may require more robust cutting tools or extended machining time.
- Surface Finishing: The way materials are machined can affect their surface characteristics. This is important in industries where surface integrity is critical.
To achieve optimal results, operators must consider both the physical properties of metals and the operational limits of their machines.
Applications of Metal Design Machines
Understanding the applications of metal design machines is crucial. These machines are not merely tools; they serve as the backbone of various industries. Their ability to create precise components is essential in meeting the demands of modern manufacturing. From automotive to aerospace, these applications illustrate the versatility and significance of metal design machines.
Automotive Industry
The automotive industry greatly relies on metal design machines. Modern vehicles consist of numerous metal parts. These machines enable efficiency in production. CNC lathes and milling machines play a key role in manufacturing engine components and frames. The precision offered by these machines ensures that parts fit perfectly, which enhances safety and performance.
Metal design machines also allow for rapid prototyping. Designers can create and test parts swiftly. This reduces time to market for new vehicle models. Additionally, with a focus on sustainability, manufacturers utilize 3D metal printing for creating lightweight components. This not only conserves materials but also improves fuel efficiency in vehicles.
Aerospace Sector
In aerospace, the stakes are higher. The need for precision is unmatched. Metal design machines, such as laser cutting machines and advanced CNC systems, are vital for producing components in aircraft and spacecraft. The performance of these machines can significantly influence the safety and functionality of the final products.
Furthermore, the aerospace sector utilizes high-strength alloys. Metal design machines must be capable of handling these tough materials. They also must adhere to stringent regulations. The reliability of components created by these machines can affect not just the mission of a spacecraft but also lives at stake during flights.
Prototyping and Mold Making
Prototyping and mold making benefit prominently from metal design machines. These processes demand precision and speed. 3D metal printers are particularly useful for creating prototypes quickly. This technology has transformed how companies approach product development. Engineers can iterate designs and test them in real-world conditions sooner.
Mold making is another area that relies heavily on these machines. High-precision molds are essential for mass production. Equipment like CNC milling machines produce molds with remarkable accuracy. This leads to consistent quality in products produced later.
Material Processing Capabilities
Material processing capabilities are essential for understanding the scope and effectiveness of metal design machines. These machines can manipulate various metals to create precise components and intricate designs. The significance lies in their ability to adapt to different materials and production needs. The advancement in processing capabilities has opened new avenues for industries ranging from automotive to aerospace.
Types of Metals Used
When considering the types of metals utilized in design and manufacturing, a wide range is available. Some common metals include:
- Aluminum: Lightweight and corrosion-resistant, suitable for applications where weight is a concern.
- Steel: Known for its strength and durability, it is frequently used in structures and heavy machinery.
- Copper: Excellent electrical conductivity makes it valuable in electrical applications.
- Titanium: High strength-to-weight ratio is useful in aerospace and medical implants.
- Alloys: Various combinations of metals can enhance specific properties, making them suitable for particular applications.
Knowing the characteristics of these metals can guide the choice during production processes. Each metal requires distinct handling and processing techniques depending on its properties.
Additive vs. Subtractive Manufacturing
Additive and subtractive manufacturing represent two primary methodologies in metal processing, each with unique strengths and considerations.
Additive Manufacturing involves building objects layer by layer. This method allows for:
- Increased design complexity with minimal waste.
- Customization to meet specific consumer needs.
- Utilization of materials only where needed, thus conserving resources.
However, it often comes with:
- Slower production speeds compared to traditional methods.
- Potential issues with material properties, depending on the additive technique.
Subtractive Manufacturing, on the other hand, is grounded in removing material from a solid block through processes like milling or turning. Its advantages include:
- High precision and surface finish.
- Faster production rates for larger quantities.
- Established technologies with a wide array of compatible machines.
Yet, it may have drawbacks such as:
- More significant waste of materials compared to additive techniques.
- Limitations on complexity in part design due to cutting constraints.
Both methodologies have their rightful place in the metal design realm, influencing decision-making depending on the specific project needs. Understanding the difference helps in optimizing the manufacturing process and achieving desired outcomes.
Challenges Faced by Metal Design Machines
The operation of metal design machines is not without its challenges. Understanding these challenges helps industry stakeholders stay informed and adaptive. The importance of addressing the obstacles faced by these machines cannot be overstated. An awareness of both material limitations and technological barriers offers insights into areas for innovation and improvement.
Material Limitations
The types of metals that can be processed by various machines often present a significant limitation. Each machine has specific capabilities, and some metals react poorly to certain techniques. For example, brittle materials can fracture easily under stress, while ductile metals may deform rather than cut. This requires engineers to select appropriate materials based on the machine’s specifications.
Another key aspect is the weight and thickness of materials. Machines designed for precision cutting may struggle with thicker metals, leading to subpar results. If the tolerance levels of a machine do not align with the material properties, it can result in defects.
Additionally, the cost of high-quality materials can restrict the range and type of projects undertaken. High-performance alloys, while ideal for certain applications, are often more expensive than standard materials. This can limit experimentation and innovation, as companies may hesitate to invest in unfamiliar metals that can increase production costs without guaranteed results.
Technological Barriers
Keepig up with technological advancements is a challenge in the metal design industry. Many older machines cannot often integrate with modern software systems, impeding productivity. This becomes an overarching problem as the industry increasingly relies on automation and data analysis. Older machines lack the capability to connect with advanced systems, becoming less efficient over time.
Moreover, rapid advancements in metal design technology mean continuous education is necessary for operators and engineers. Training programs must evolve with industry trends. Otherwise, companies risk losing skilled workers who cannot keep pace with changing technology.
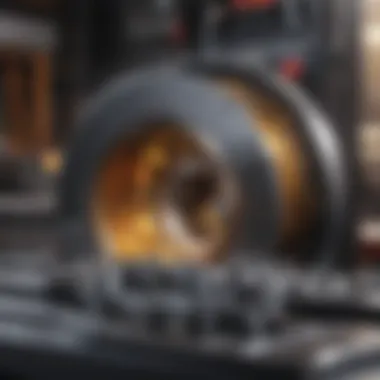
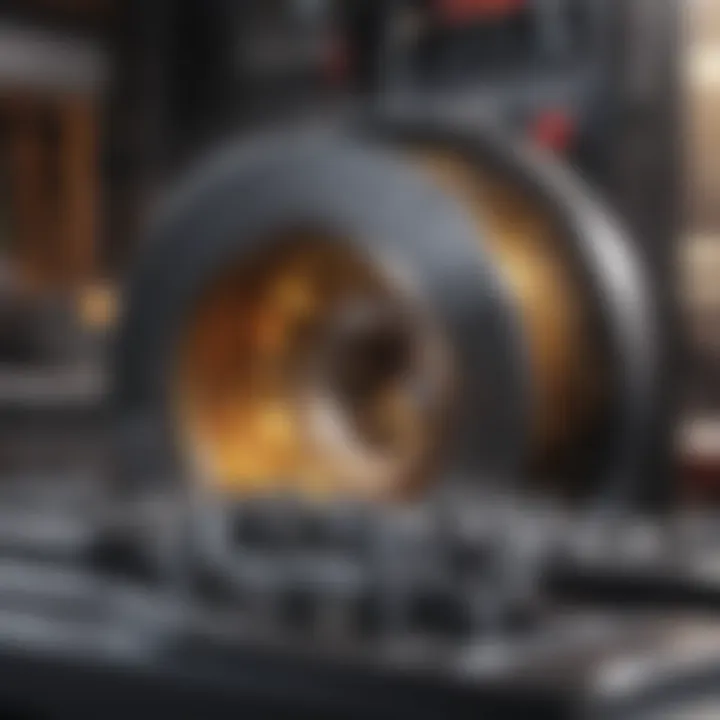
UI and UX concerns for machine interfaces can affect productivity as well. Complex or non-intuitive interfaces may lead to user error, causing costly delays in work.
"Understanding the challenges in metal design is essential for innovation and development in the field. Addressing material and technological barriers can lead to significant advancements and efficiency gains."
In summary, recognizing the challenges faced by metal design machines—both in terms of materials and technology—provides vital insights that can drive future advancements. By addressing these obstacles, the industry can come closer to achieving higher efficiency, adaptability, and quality in metal design processes.
Innovations Shaping the Future
Innovations in metal design machines are crucial for enhancing efficiency, productivity, and environmental sustainability. As industries evolve, technological advancements significantly impact how metal is processed and designed. In this section, we will explore two significant areas of innovation: the integration of artificial intelligence and automation, and the practices that promote sustainability in metal design.
Integration of AI and Automation
The integration of artificial intelligence (AI) in metal design machines is transforming production methods. AI technologies enable these machines to learn from historical data, detect patterns, and make adjustments in real time. This capability enhances precision while minimizing errors in manufacturing processes.
In practical terms, AI can optimize machine operations by analyzing the workflow to suggest improvements. For instance, predictive maintenance schedules can be established based on usage patterns, reducing downtime significantly. Furthermore, automation complements AI by streamlining tasks that were once labor-intensive and prone to human error. This shift not only improves efficiency but also allows skilled workers to focus on complex problem-solving instead of repetitive tasks.
"The integration of AI and automation is not just a trend; it is a fundamental shift in how metal design machines operate, fostering significant improvements in productivity and quality."
Key benefits of this integration include:
- Increased speed in production cycles.
- Enhanced quality control standards.
- Reduction in waste materials.
Sustainability Practices
As environmental concerns grow, the metal design industry is adapting by adopting sustainability practices. These practices are fundamental for reducing the ecological impact of metal manufacturing.
One critical aspect is the use of recycled materials. Many machines are now designed to work efficiently with scrap metals or alloys that require less energy for processing. Additionally, energy efficiency is becoming a priority; machines capable of operating at lower power rates not only save costs but also diminish harmful emissions.
Sustainable metal design also involves lifecycle assessment. This approach evaluates the environmental impact of products from initial design through to disposal. By understanding these impacts, companies can make more informed decisions, improving their outcomes in terms of sustainability and cost-effectiveness.
Ultimately, the adaptation of sustainable practices contributes positively to corporate social responsibility, aligning with global goals for climate change reduction. As a result, companies that invest in these innovations are likely to gain a competitive edge, appealing to a growing base of environmentally conscious customers.
Case Studies in Metal Design
Case studies in metal design serve as crucial illuminations of real-world applications and innovations in the field. They allow industry stakeholders—from educators to engineers—to gather insights from specific instances where metal design machines have significantly contributed to advancements in productivity, efficiency, and creativity.
These studies help identify best practices and pitfalls encountered in the implementation of various technologies. Such reflections pave the way for enhanced operational standards and methodologies, which are particularly vital given the rapid technological evolution observed in today's market. Case thudies offer valuable lessons arising from the interplay between human skill and mechanical efficiency.
Successful Implementations
The success of metal design machines can often be attributed to their strategic implementation in diverse industries. For instance, a leading automotive manufacturer successfully employed CNC milling machines to optimize component production. By integrating advanced software to collaborate with hardware, they reduced waste while improving precision.
Another notable case is a biomedical company that adopted 3D metal printing technology. This allowed for the production of custom implants tailored for individual patients, significantly enhancing fit and improving patient outcomes.
Key aspects of successful implementations include:
- Clear Objectives: Establishing specific goals guides the machine selection and process optimization.
- Training and Facilities: Proper training for staff ensures that the machines are operated efficiently and safely.
- Continuous Feedback: Gathering data from the manufacturing process assists in adjustments and improvements.
Lessons Learned
Analyzing various case studies provides essential insights into challenges faced during implementation. For example, a manufacturing plant experienced downtime caused by outdated equipment. This highlighted the importance of maintaining and updating machinery in a timely manner.
Moreover, coordination between different departments is crucial. A prominent aerospace company found that improved collaboration between design and production teams led to optimized workflows, further enhancing production speed.
Lessons derived from case studies often include:
- Adaptability: Flexibility in adopting new processes is necessary to stay competitive.
- Prototype Testing: Initial prototyping reduces the risk of large-scale failures and mitigates costs.
- Investing in R&D: Companies that consistently allocate resources for research and development tend to lead in innovation.
"Every case study tells a story that illustrates the potential of metal design machines, informing future practices and innovations in the field."
Understanding these case studies offers a strategic advantage to stakeholders, enabling them to apply learned lessons to new challenges in metal design.
Comparative Analysis of Technologies
Comparative analysis of technologies is a critical component in understanding the diverse landscape of metal design machines. This analysis allows professionals to assess the strengths and weaknesses of various machines, leading to informed decisions based on specific project needs. By comparing factors like cost efficiency, speed, precision, and material compatibility, organizations can optimize their manufacturing processes and enhance productivity.
Analyzing different technologies also aids in identifying trends and innovations that may influence future developments. With a clear picture of how machines stack up against each other, businesses can adapt their strategies to stay competitive and compliant with industry standards. Furthermore, this analysis can highlight areas for improvement or investment in research and development.
Cost Efficiency
Cost efficiency is a central topic when discussing metal design machines. It involves evaluating the costs associated with equipment purchase, maintenance, operation, and the overall output quality. Organizations often seek machines that provide the best return on investment over their operational lifespan.
Cost efficiency can be influenced by multiple factors:
- Initial investment costs
- Energy consumption rates
- Material waste during processing
- Labor requirements
For example, CNC machines may have a higher upfront cost but can significantly reduce labor costs and material waste through automation. Conversely, older technologies might appear cheaper initially but can incur high operating costs over time.
A comprehensive understanding of cost efficiency helps businesses allocate resources effectively and plan budgets accurately. As the market evolves, organizations that leverage cost-efficient technologies will likely gain a competitive edge.
Speed and Precision
Speed and precision are arguably the two most critical performance metrics for metal design machines. These elements directly affect project timelines and the quality of the final product. In industries like aerospace and automotive, where tolerances can be extremely tight, the importance of precision cannot be overstated.
Speed relates to how quickly a machine can complete tasks, while precision concerns the accuracy of these tasks. Finding a balance between the two is essential. Here are some aspects to consider:
- Workflow efficiency
- Setup and changeover times
- Capability to handle complex designs
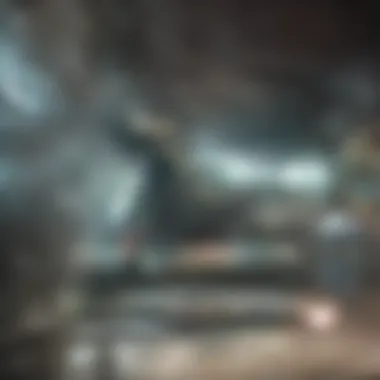
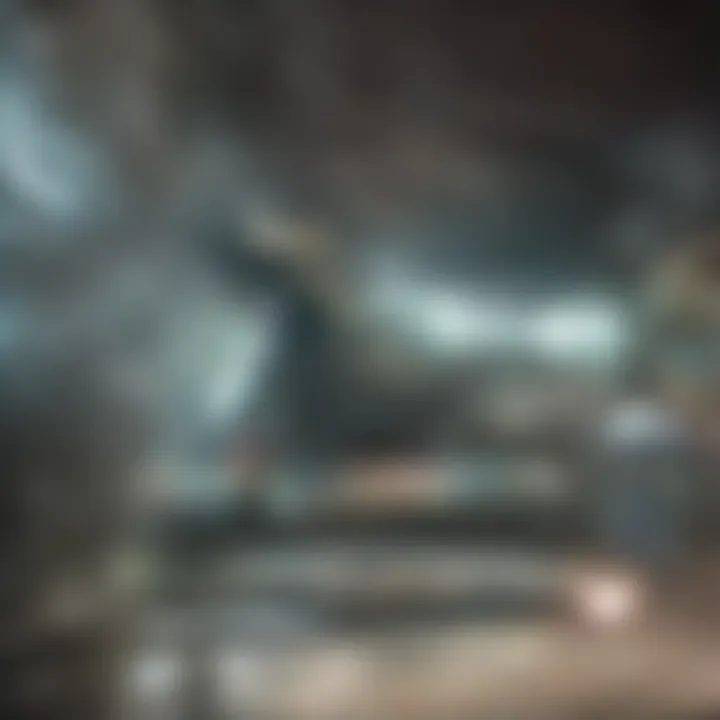
Modern laser cutting machines, for instance, often excel in speed, allowing for rapid production runs without sacrificing precision. On the other hand, 3D metal printers may offer exceptional precision for intricate components, but their speed can vary based on the complexity of the part being produced.
Ultimately, the right combination of speed and precision is determined by the specific needs of the project and the industry standard practices. Companies must perform thorough analyses to identify the machine that will best meet their operational requirements.
Future Trends in Metal Design Machinery
Exploring future trends in metal design machinery reveals crucial developments that are shaping the industry and extending its capabilities. Understanding these trends is vital not just for professionals currently operating within the sector, but also for students and educators who will guide future generations. These trends touch on emerging technologies and market projections that significantly influence how metal design processes evolve, fostering expansion and innovation.
Emerging Technologies
Emerging technologies play a prominent role in redefining metal design machinery. As industries demand higher efficiency, precision, and adaptability, manufacturers are leaning towards automation and artificial intelligence. Automation in metal design machines enhances precision and speeds up production cycles. Integrating AI helps predict maintenance needs, reducing unplanned downtimes.
Another significant development is the increased utilization of 3D printing technology, especially in aerospace and automotive sectors. 3D metal printing allows for complex designs that traditional methods cannot achieve. This flexibility opens opportunities for creating lighter and stronger components, which leads to improved overall performance. Moreover, hybrid machines combining both additive and subtractive manufacturing techniques are emerging. These models can handle various processing demands without the need to switch equipment, thus increasing workflow efficiency.
In addition to automation and 3D printing, the implementation of Internet of Things (IoT) technologies is on the rise. IoT enables devices to communicate with each other, allowing for real-time monitoring and adjustments. This could drastically reduce waste and enhance quality control in metal design processes.
Market Projections
Market projections for metal design machinery indicate a strong growth trajectory over the next decade. According to recent analyses, the global market is poised to expand at a compound annual growth rate (CAGR) of over six percent. Factors influencing this growth include increased demand from the automotive and aerospace sectors, which continuously seek innovative manufacturing solutions to improve product quality and reduce costs.
Furthermore, sustainability is becoming a key driver of market changes. As regulations tighten and consumer preferences shift towards eco-friendly practices, companies are investing in technologies that promote materials recycling and energy efficiency. The focus on sustainability will influence future designs and functionalities of metal design machines, pushing manufacturers to innovate continuously.
"Companies that adapt to these emerging trends will likely position themselves ahead of the competition, gaining not just market share, but also trust from increasingly conscious consumers."
In summary, future trends in metal design machinery carry significant implications. Understanding emerging technologies and comprehending market projections will be essential for stakeholders in the metal design field. Companies and individuals who stay ahead of these trends will not only improve operational efficiency but also contribute to a more sustainable future.
The Role of Education in Advancing Metal Design
The field of metal design necessitates a strong educational framework to keep pace with technological advancements. The dynamic nature of metal design machines means that continuous education is essential for professionals, educators, and students alike. Understanding the complexities and innovations of this industry is vital for fostering skilled practitioners and researchers. Educational programs provide an essential base for developing not just skills but also critical thinking and problem-solving abilities in this sector.
Curriculum Development
Creating a robust curriculum for metal design education involves several critical elements. These programs must evolve with the industry to ensure they remain relevant. Key elements of curriculum development include:
- Industry Collaboration: Engaging with industry stakeholders ensures that curriculum reflects current practices and technologies. Input from experts can help shape course content that aligns with market needs.
- Hands-On Learning: Practical experience is indispensable. Integrating lab sessions and workshops enhances theoretical training, allowing students to apply their knowledge in real-world scenarios.
- Interdisciplinary Approach: Metal design intersects with multiple fields, such as engineering, materials science, and computer science. An interdisciplinary curriculum encourages holistic understanding, preparing students for diverse challenges.
A well-rounded curriculum can significantly improve graduate employability and innovation within the sector. Hence, continuous updates and revisions are important to stay aligned with changing technologies.
Workforce Training Programs
The advancement of metal design machinery is not solely reliant on formal education. Workforce training programs play a crucial role in skill enhancement for current professionals. These initiatives can take various forms:
- Certification Courses: Offering specific technical certifications helps professionals gain expertise in precise areas. For example, certifications in CNC machining or laser cutting can be pivotal for career progression.
- On-the-Job Training: Practical experience is invaluable. Employers should implement structured training programs that allow employees to learn while working with the latest technologies. This practice not only boosts competency but also leads to innovation within the company.
- Online Learning Platforms: Digital education has become more accessible. Utilizing platforms such as LinkedIn Learning or Coursera can supplement traditional training methods, providing flexibility and targeted learning opportunities.
In summary, workforce training programs deepen knowledge bases and skill sets, allowing professionals to adapt to rapid changes. The ongoing development of expertise fosters a more innovative and skilled workforce, ultimately benefitting the metal design industry as a whole.
"Education is the most powerful weapon which you can use to change the world."
- Nelson Mandela
Regulatory Considerations
The regulatory landscape governs the operation of metal design machines significantly. Compliance with regulations is vital for manufacturers, educators, and operators in the industry. It ensures that the machines are not only effective but also safe for users and environmentally responsible. Understanding these regulations is crucial as it directly influences design, production, and operational protocols. Consequently, organizations must keep abreast of changing regulations to avoid non-compliance, which could lead to severe penalties.
Health and Safety Standards
Health and safety standards oversee the protection of workers involved in the operation of metal design machines. In this field, machines can pose various risks such as sharp edges, high temperatures, and heavy machinery accidents. *
Organizations such as the Occupational Safety and Health Administration (OSHA) set guidelines to mitigate these risks. Adherence to these standards includes:
- Ensuring proper training for operators on machine usage.
- Implementing regular maintenance checks to prevent machinery failure.
- Including safety guards and emergency shut-off switches on machines.
- Using appropriate personal protective equipment (PPE).
By following these standards, businesses not only protect their workers but increase productivity and reduce the likelihood of costly accidents. It is an ongoing responsibility that contributes to the overall workplace safety culture.
Environmental Regulations
Environmental regulations are also pivotal in the metal design machines arena. These regulations target the reduction of harmful emissions and waste generated during manufacturing processes. The fabrication of metals can release toxic substances and produce considerable waste. As a result, compliance is necessary for sustainable operations.
Key aspects of environmental regulations include:
- Proper waste disposal methods for hazardous materials.
- Implementing recycling programs for scrap metals.
- Limiting harmful emissions through better technology and processes.
- Conducting environmental impact assessments prior to major operational changes.
Understanding these regulations can lead to enhanced reputation and competitiveness within the market. It also encourages innovation in processes to comply with sustainability goals. By following environmental regulations, organizations reinforce their commitment to operating responsibly, thus appealing to consumers who prioritize sustainable practices.
Compliance with health and safety and environmental regulations is not just about avoiding penalties. It represents a commitment to social responsibility and ethical business practices.
Epilogue and Future Directions
The examination of metal design machines highlights their pivotal role in modern manufacturing. As industries increasingly rely on advanced technology, it becomes essential to understand not only the current state but also the future directions of these machines. This section outlines the significance of reflective conclusions and anticipatory insights regarding metal design technologies.
Summary of Findings
Throughout this article, we have explored several vital aspects of metal design machines. Key findings include:
- Technological Evolution: Metal design machines have evolved dramatically from basic tools to complex, highly automated systems. Innovations such as CNC machines, laser cutters, and 3D printers exemplify this progress.
- Diverse Applications: These machines serve multiple sectors, including automotive, aerospace, and mold making, underscoring their versatility.
- Material Processing: The distinction between additive and subtractive manufacturing sheds light on how different techniques affect material choices and design outcomes.
- Challenges and Innovations: Although we face challenges like material limitations and technological barriers, advancements in AI, automation, and sustainability practices pave the way for future enhancements.
These findings emphasize the dynamic nature of metal design machinery and its continual adaptation to meet industrial demands.
Final Thoughts
Looking ahead, the future of metal design machines holds great promise. As researchers and practitioners explore new materials and technological capabilities, the industry will likely witness revolutionary breakthroughs. Understanding regulations and developing educational paths remain essential to ensure a competent workforce ready to tackle emerging challenges.
Consequently, stakeholders must adopt a proactive mindset. The successful integration of innovative practices will be crucial for maintaining competitive advantages. As the landscape evolves, it is important for students, educators, and industry professionals to remain engaged with ongoing advancements in metal design technology.