Non-Destructive Pipe Testing: Techniques and Implications
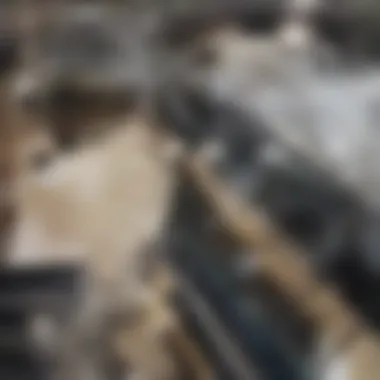
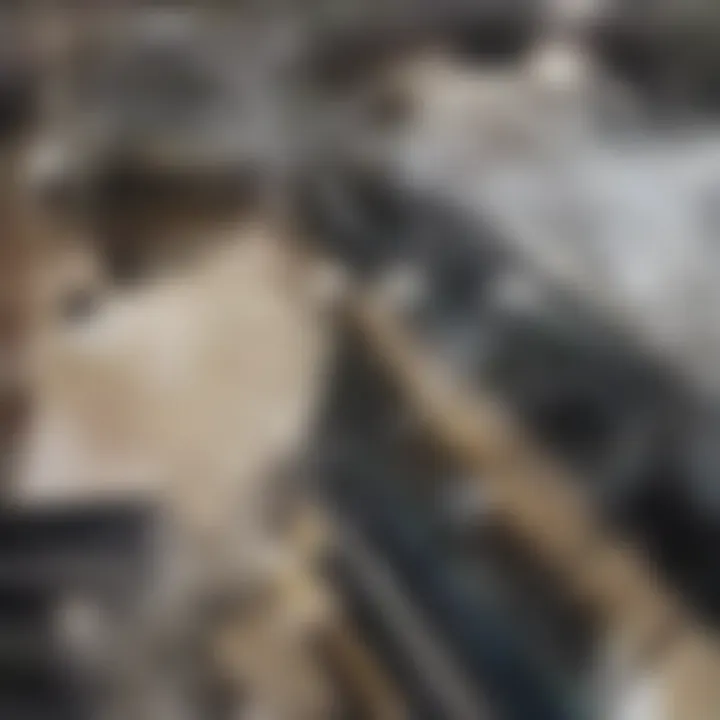
Intro
Non-destructive pipe testing (NDPT) is an essential procedure in various industries, ensuring the integrity of pipelines without causing any harm to the materials. Industries such as oil and gas, water supply, and manufacturing heavily rely on keeping pipelines functional and safe. This article analyzes non-destructive testing methods, detailing the importance of these technologies for safety, compliance, and environmental sustainability. In doing so, it seeks to offer an insightful exploration of the area, designed for engineers, researchers, and safety professionals.
Key Concepts and Terminology
Understanding the key concepts and terminology is vital in grasping the nuances of non-destructive pipe testing. Here we define several important terms:
Definition of Key Terms
- Non-Destructive Testing (NDT): A range of techniques used to evaluate the properties of a material, component, or system without causing damage.
- Pipe Integrity: The condition of a pipeline to safely transport its intended contents without leakage or failure.
- Ultrasonic Testing: A method that utilizes high-frequency sound waves to detect imperfections in materials.
- Radiographic Testing: This involves using X-rays or gamma rays to examine the internal structure of the pipe for flaws.
Concepts Explored in the Article
- The diverse techniques employed in NDPT and how they cater to various industry needs.
- Methods for assessing the reliability and safety of pipelines while promoting environmental sustainability.
- The ongoing advancements in technologies and practices associated with non-destructive testing, keeping pace with industry demands
- The implications of NDPT for future pipeline management, maintenance routines, and regulatory compliance.
Findings and Discussion
Main Findings
The exploration of non-destructive pipe testing showcases that using NDT significantly enhances safety and efficiency. Techniques such as Ultrasonic and Radiographic Testing allow for early detection of potential failures, minimizing downtime and associated costs. Moreover, they help in meeting all relevant regulatory standards, making NDPT a cornerstone for responsible facility management.
The Association of Oil and Gas Producers states that implementing non-destructive testing can reduce incidents by up to 25%.
Potential Areas for Future Research
There are several areas in non-destructive pipe testing ripe for further exploration:
- Integration of Artificial Intelligence: Developing systems that can analyze data faster and more accurately.
- Emerging Materials: Investigating how new substances used in pipelines interact with testing methods.
- Sustainability Practices: Exploring further methods on how NDT can promote eco-friendly initiatives in various industries.
This article will continue by analyzing specific methods used in NDPT, emphasizing their applications and benefits to various industries.
Foreword to Non-Destructive Pipe Testing
Non-destructive pipe testing has gained importance across various industries due to increasing demands for safety and efficiency. This topic is highly relevant for engineers, safety professionals, and researchers who seek to maintain the integrity of pipelines without compromising their functionality. Current regulations and technological advancements drive the need for effective testing methods.
Definition and Purpose
Non-destructive pipe testing refers to a set of techniques used to evaluate the integrity of pipes without causing any harm to the material. This means that the pipes can remain operational while being assessed for defects or weaknesses. The primary purpose is to ensure safety and reliability. Industries rely on these testing methods to prevent catastrophic failures that could lead to costly repairs and potential hazards. Key aspects include:
- Assessment of pipeline integrity
- Detection of flaws, corrosion, or defects
- Minimization of downtime and costs
The stakes are high, as failures in pipelines can result in environmental damage and loss of life.
Historical Background
The evolution of non-destructive testing (NDT) began around the early 20th century. Initially, methods such as visual inspection and basic auditory detection were used. However, as industrial processes advanced, the need for more sophisticated techniques became evident. World War II spurred innovations in NDT practices, particularly ultrasonic and radiographic testing, which allowed engineers to inspect components without disassembly.
In the decades that followed, regulatory bodies began to recognize the importance of these methods, leading to the establishment of standards and guidelines. The history of non-destructive pipe testing reflects the ongoing need for improved safety measures and technological advancements, setting the foundation for the state-of-the-art practices seen today.
"Non-destructive testing is essential for the maintenance and safety of infrastructure, ensuring that operation remains uninterrupted while risk is minimized."
Through this understanding, it becomes clear that non-destructive pipe testing is not just a technical requirement but a fundamental aspect of modern industrial operations.
Essential Principles of Non-Destructive Testing
Non-destructive testing (NDT) is a critical element in ensuring the integrity of pipes in various industries. This section discusses the core principles underlying NDT, its key concepts, and terminology, as well as the advantages of using these techniques.
Key Concepts and Terminology
In non-destructive testing, several concepts are fundamental to understanding the methods used. These include:
- Integrity: This refers to the structural soundness of a pipe and its ability to perform without failure.
- Defect: A defect is any imperfection that could compromise the pipe's integrity. Common types include cracks, corrosion, and weld discontinuities.
- Sensitivity: This indicates how well a specific testing method can detect defects. Higher sensitivity leads to more reliable results.
- Calibration: This process adjusts the equipment to ensure accurate readings. Proper calibration is essential for effective testing.
- Penetration depth: This term describes how deep a testing method can evaluate a material. Different techniques have varying penetration capacities.
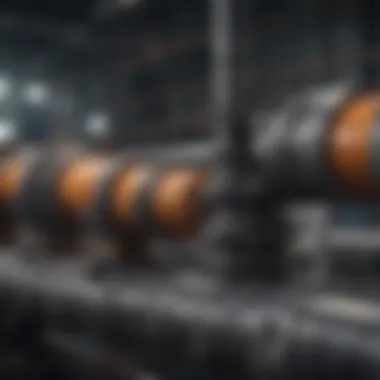
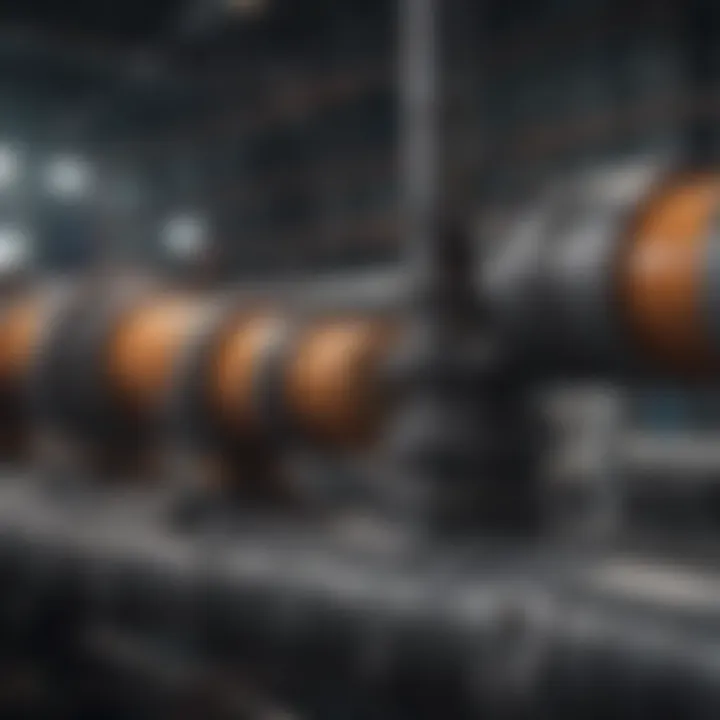
Understanding these key concepts aids professionals in selecting the right testing method and interpreting results accurately.
Advantages of Non-Destructive Testing
Non-destructive testing offers several advantages that are highly relevant to industry practices. The primary benefits include:
- Preservation of Material Integrity: Since NDT techniques do not damage the pipe being tested, they preserve its functionality and lifespan. This is crucial in industries where material replacement can be costly and time-consuming.
- Cost-Effectiveness: While some NDT methods may require significant upfront investment, they often reduce long-term costs associated with failures or leaks. This is because they detect potential issues early, preventing more extensive and costly repairs.
- Safety Enhancements: In industries such as oil and gas or nuclear power, safety is paramount. Non-destructive testing helps identify weaknesses before they lead to catastrophic failures, thus enhancing overall safety measures.
- Regulatory Compliance: Many industries are subject to strict regulations regarding pipeline safety. NDT helps organizations comply with these regulations, reducing the risk of penalties and enhancing credibility.
- Versatility: NDT methods can be used on various materials and in different environments. This versatility allows for broader application across various sectors, making it an invaluable tool for engineers and safety professionals.
Non-destructive testing is not just about detecting defects; it is also about ensuring that the infrastructure remains safe and sound for many years.
In summary, the essential principles of non-destructive testing play a vital role in the overall maintenance and safety of pipeline systems. By grasping the key concepts and recognizing the significant advantages, professionals can make informed decisions that enhance operational efficiency and regulatory compliance.
Common Techniques in Non-Destructive Pipe Testing
Non-destructive pipe testing is essential for ensuring safety and integrity in various industries. Understanding the common techniques used within this testing framework can help professionals make informed decisions regarding pipeline maintenance and safety measures. Each technique has its own specific advantages and methodologies, contributing distinctly to the overall process. This section will discuss four primary methods: Ultrasonic Testing, Magnetic Particle Testing, Radiographic Testing, and Liquid Penetrant Testing.
Ultrasonic Testing
Ultrasonic Testing (UT) is a widely used method that utilizes high-frequency sound waves to detect imperfections in materials. This technique has the advantage of being able to evaluate the thickness of pipes effectively. It is often used for detecting corrosion in pipelines. Sound waves are transmitted through the material. If there is an imperfection, the waves reflect back differently.
Benefits of Ultrasonic Testing:
- It is highly sensitive to small defects.
- Provides real-time results.
- Can measure wall thickness to assess corrosion.
Considerations include the need for skilled technicians and the material type being tested. Some materials may absorb sound waves differently, which can affect results. Nonetheless, UT remains an industry standard due to its effectiveness and versatility.
Magnetic Particle Testing
Magnetic Particle Testing (MPT) is another essential technique, where fine ferrous particles are applied to the surface of a material. When a magnetic field is introduced, the particles will accumulate at areas of defect, revealing surface and near-surface discontinuities. This method is particularly useful for detecting cracks.
Key factors of Magnetic Particle Testing:
- Ideal for ferromagnetic materials like steel and iron.
- Provides visual representation of defects.
- Fast process with little setup time.
However, this method does have limitations. For example, it cannot detect defects beneath the surface and is ineffective for non-magnetic materials. Despite these limitations, MPT is valued for its simplicity and speed, making it a common choice for surface testing.
Radiographic Testing
Radiographic Testing (RT) employs ionizing radiation, typically X-rays or gamma rays, to inspect materials. This method involves exposing a photographic film to radiation passing through the material. Denser areas will appear darker on the developed film, highlighting flaws and voids.
Advantages of Radiographic Testing:
- Effective for detecting internal defects.
- Provides permanent record of inspections.
- Applicable to a wide range of materials.
On the downside, RT requires stringent safety precautions due to the hazardous nature of radiation. Training and careful handling of equipment are vital. Moreover, RT is more time-consuming and requires considerable preparation compared to other methods.
Liquid Penetrant Testing
Liquid Penetrant Testing (LPT) is a method for detecting surface breaking defects. It involves applying a penetrant dye to the surface of a material, allowing it to seep into any imperfections. After a dwell time, excess penetrant is removed and a developer is applied to highlight any detected flaws. This method is cost-effective and straightforward.
Important aspects of Liquid Penetrant Testing:
- Works on a variety of non-porous materials.
- Suitable for complex geometries.
- Requires minimal equipment.
However, it is limited to surface defects and is not applicable to porous or absorbent materials. LPT is frequently used in industries such as aerospace and automotive for maintenance and quality assurance.
In summary, these common techniques in non-destructive pipe testing offer a variety of options depending on the specific requirements of the inspection. Each method comes with its own strengths and limitations. Selecting the appropriate technique is essential for effective results.
Application Areas of Non-Destructive Pipe Testing
Non-destructive pipe testing (NDPT) plays a crucial role in various industries. It ensures the reliability and safety of critical infrastructure without causing any damage. The application areas are numerous. Each sector requires specific methods tailored to its unique challenges. Understanding these applications is essential for engineers, safety professionals, and researchers.
Oil and Gas Industry
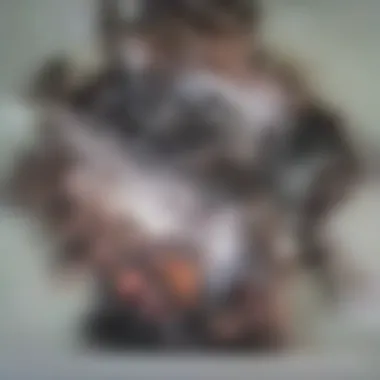
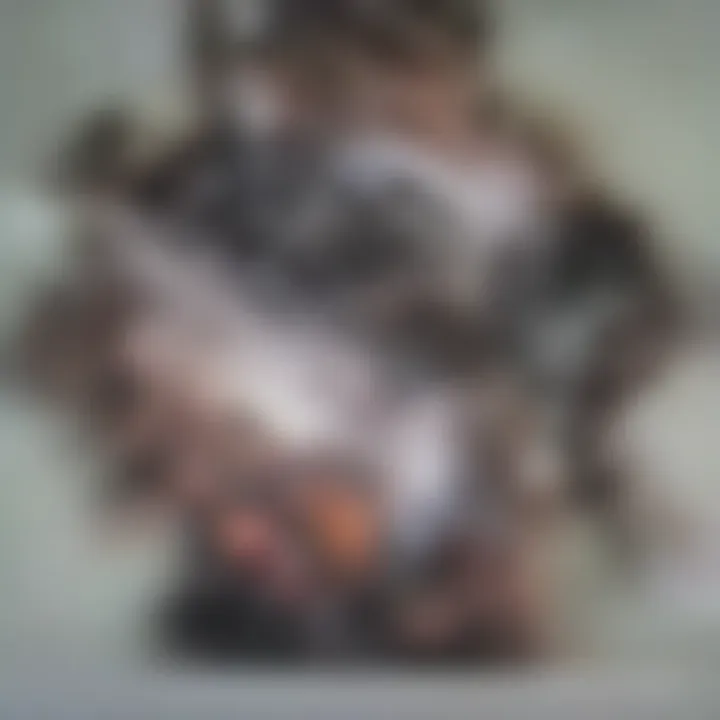
The oil and gas industry heavily relies on non-destructive pipe testing. Pipelines transport valuable resources over long distances. Any malfunction or leakage can result in severe environmental and financial damages. NDPT techniques, such as ultrasonic testing and radiographic testing, monitor pipe integrity effectively.
These methods help detect flaws, corrosion, and other issues early. Regular inspections using NDPT enhance safety measures. Companies can ensure compliance with stringent regulations while protecting their assets and the environment.
Water Supply Systems
In the context of water supply systems, non-destructive pipe testing is vital. Aging pipes often lead to leaks and contamination risks. NDPT techniques help assess the condition of drinking water pipelines. By identifying weaknesses without excavation, it minimizes disruption.
Regular assessments provide crucial information. Utilities can prioritize repairs and replacements efficiently. This proactive approach helps maintain quality and reliability. It also safeguards public health by preventing waterborne diseases.
Chemical Processing
The chemical processing sector involves handling hazardous materials. Non-destructive pipe testing is essential for ensuring operational safety. NDPT methods help detect leaks in pipelines carrying corrosive substances. This process is critical for avoiding accidents that could harm workers and the environment.
By utilizing techniques like magnetic particle testing and liquid penetrant testing, facilities can be inspected regularly. This ensures compliance with safety standards and regulations. Moreover, it extends the lifespan of critical infrastructure, reducing overall costs associated with maintenance.
Nuclear Facilities
In nuclear facilities, maintaining strict safety protocols is paramount. Non-destructive pipe testing contributes significantly to this objective. The potential consequences of failures in piping systems are grave. Therefore, organizations implement rigorous inspection regimes.
Techniques such as ultrasonic and radiographic testing are common in this sector. They detect structural integrity issues before they escalate. The ability to conduct regular assessments without interrupting operations is a key advantage. Hence, non-destructive testing techniques prove invaluable in maintaining safety within nuclear reactors.
"Non-destructive testing is not just a choice; it's a necessity in maintaining safety across various sectors."
Each application of non-destructive pipe testing showcases its importance in preventing failures and ensuring compliance. Understanding these areas helps professionals implement the right methodologies and maintain high standards in their operations.
Regulatory and Compliance Standards
In the domain of non-destructive pipe testing, regulatory and compliance standards play a pivotal role. They ensure that testing meets certain minimum levels of safety and performance. These standards not only protect the integrity of the pipelines but also safeguard public health and the environment. Businesses and organizations must adhere to various regulations to maintain operational efficiency and reduce liabilities.
Compliance with these standards also enhances credibility among stakeholders. It builds trust between service providers, clients, and regulatory bodies. Therefore, understanding and implementing these regulations can offer significant advantages in non-destructive testing practices.
Industry Regulations Overview
The oil and gas, water supply, and chemical processing industries are among the most heavily regulated sectors. Each of these industries has its own set of regulations aimed at ensuring that all aspects of infrastructure, including pipelines, operate effectively and without risk. Important regulations often include requirements for regular inspections, maintenance routines, and testing protocols.
For instance, the U.S. Department of Transportation has established the Pipeline and Hazardous Materials Safety Administration (PHMSA) which outlines rules specifically targeting pipeline integrity management. This requires operators to develop programs that assess pipeline safety through systematic inspections. Such regulations are vital for minimizing accidents and environmental hazards.
Moreover, regulations can vary significantly by country and region, making it essential for firms to be well-informed about local legal frameworks. Staying compliant also helps organizations avoid hefty fines and enhances their safety record.
International Standards and Guidelines
Internationally recognized standards provide a framework for non-destructive testing, promoting adherence to best practises across borders. The American Society for Testing and Materials (ASTM) and the International Organization for Standardization (ISO) offer comprehensive guidelines that help standardize testing methods and procedures.
For example, ISO 9712 outlines the certification requirements for non-destructive testing personnel, ensuring that only qualified individuals conduct inspections. This is crucial for maintaining quality and consistency in testing results.
In addition to ASTM and ISO, organizations like the American Society of Mechanical Engineers (ASME) publish standards that focus specifically on the testing of piping systems. These standards detail acceptable practices that companies must follow for various testing techniques, ensuring a high level of safety and reliability.
It is important for firms to not just be aware of these standards but to actively integrate them into their operations. Doing so improves overall safety and can enhance corporate reputation in a competitive market.
"Adhering to regulations and standards is not just a legal obligation, but a commitment to safety and quality in non-destructive pipe testing."
Challenges in Non-Destructive Pipe Testing
Non-destructive pipe testing serves a vital role in several industries to ensure safety and reliability. However, this method does face certain challenges that need careful consideration. Addressing these challenges is essential for optimizing testing processes and improving accuracy in results. In this section, we will explore two significant challenges: technical limitations and material compatibility issues.
Technical Limitations
One major challenge in non-destructive pipe testing is the technical limitations associated with the different methods available. Each testing technique comes with its own set of constraints and effectiveness which can impact assessment accuracy. For example:
- Detection Range: Some techniques, such as ultrasonic testing, may struggle with detecting flaws in pipes that have complex geometries or varying wall thicknesses. This limitation might lead to undetected issues that could result in failures down the road.
- Testing Environment: External factors like temperature and humidity can interfere with the accuracy of readings. This can especially be true for methods like radiographic testing, where environmental conditions may affect the quality of the imaging.
- Skill and Experience: The effectiveness of non-destructive testing often hinges on the skill level of the technician performing the test. Inadequate training can lead to misinterpretation of results or even overlooking critical anomalies.
Maintaining awareness of these limitations is essential for professionals in this field. Regular updates in training procedures and technological advancements are critical to enhance the efficiency and reliability of testing methods.
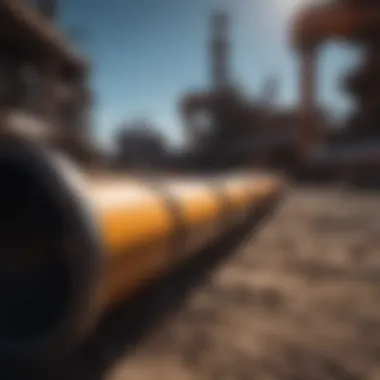
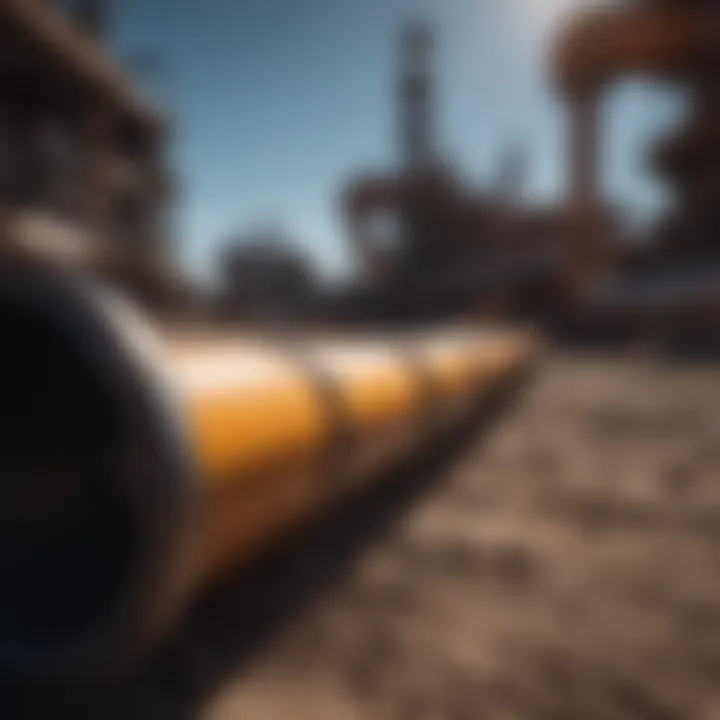
Material Compatibility Issues
Material compatibility is another significant challenge in non-destructive pipe testing. Different materials respond differently to testing methods. For example:
- Surface Treatments: Pipes with coatings and surface treatments may hinder some inspection techniques, such as magnetic particle testing. These treatments can mask defects that need to be identified.
- Material Composition: Variations in material composition, such as the presence of different alloys, can affect how sound waves or magnetic fields penetrate a pipe. This difference can change the sensitivity of certain tests.
- Environmental Fluctuations: Factors such as corrosion, temperature variations or chemical exposure can influence the integrity of testing methods. Technicians must adjust their testing strategies to account for these factors to avoid inaccurate assessments.
"Understanding these challenges allows professionals to implement better strategies for detection and assessment, ultimately leading to improved safety and efficiency."
Future Trends in Non-Destructive Testing
The landscape of non-destructive testing (NDT) is evolving rapidly, driven by advancements in technology and growing emphasis on sustainability. This section outlines the key trends shaping the future of non-destructive pipe testing (NDPT). Not only do these trends enhance the testing processes, but they also contribute to safer and more efficient operations.
Technological Advancements
Recent advancements in technology are playing a pivotal role in non-destructive testing. Innovative methods such as digital radiography, phased-array ultrasonic testing, and automated inspection systems are gaining traction. These technologies facilitate more accurate and faster assessments of pipeline integrity.
- Digital Radiography: This method utilizes digital sensors instead of traditional film, significantly improving image quality and reducing processing times. The ability to instantly view results reduces downtime and allows for quicker decision-making.
- Phased-Array Ultrasonic Testing: This advanced form of ultrasonic testing employs multiple elements and electronic time delays to create a more detailed image of the pipe structure. This method is especially beneficial for detecting flaws in complex geometries.
- Automated Inspection Systems: Automation in NDT is reducing human error and enhancing efficiency. These systems are designed to conduct tests without continuous operator input, allowing for consistent and reliable results.
Beyond these specific methods, emerging technologies such as artificial intelligence and machine learning are finding applications in data analysis, helping to predict potential failures before they occur. This proactive approach not only ensures safety but also optimizes maintenance schedules.
"The integration of AI into non-destructive testing can vastly improve predictive maintenance strategies."
Sustainability Considerations
Sustainability is becoming an integral part of non-destructive testing practices. As industries face increasing pressure to reduce their environmental footprint, NDT methods are adapting. The focus is shifting towards both minimizing waste and enhancing resource efficiency.
- Eco-Friendly Materials: There is a growing trend towards using environmentally safe materials in testing processes. This not only reduces pollution but also aligns with broader corporate sustainability goals.
- Energy Efficiency in Testing: Newer technologies aim to lower energy usage during testing operations. For example, digital techniques generally consume less energy compared to traditional methods, contributing to a reduced carbon footprint.
- Lifecycle Management: NDT contributes significantly to lifecycle management by ensuring pipes are monitored throughout their operational lifetime. This proactive monitoring can extend the life of materials and reduce the need for replacements, thereby conserving resources.
Case Studies of Non-Destructive Pipe Testing
The case studies in non-destructive pipe testing (NDPT) serve as vital sources of knowledge and insight for professionals across various industries. By examining real-world applications, we can assess the effectiveness and practicality of different testing methods. These studies illuminate the successes and failures encountered in actual scenarios, providing invaluable lessons that enhance the understanding of non-destructive testing (NDT) protocols.
In DNPT, case studies exemplify the benefits of using such methods, showcasing their ability to detect flaws that could lead to catastrophic failures. Moreover, they reveal how test outcomes can inform maintenance strategies, compliance with regulatory standards, and improvements in pipeline safety practices.
Successful Applications
Successful applications of NDPT are numerous, illustrating the technique's versatility and reliability. In the oil and gas sector, for instance, ultrasonic testing has been utilized to inspect sub-sea pipelines. A case involving a large offshore oil platform highlighted how ultrasonic testing identified critical wall thickness loss due to corrosion, allowing for timely repairs before a potential leak occurred.
Another notable example involves the water supply industry, where radiographic testing was employed to assess the integrity of a series of water mains in an urban setting. The tests revealed multiple areas of concern, enabling city officials to prioritize replacements and thus prevent disastrous water main breaks. This not only saved money but also ensured the continued delivery of safe drinking water to residents.
In the chemical processing sector, liquid penetrant testing played a crucial role in the inspection of storage tanks that housed hazardous materials. A case study documented how penetrant testing effectively detected cracks and flaws within the tank structure, which might have led to leaks if left unaddressed. The outcome reaffirmed the importance of routine inspections and highlighted the need for rigorous application of NDPT methodologies.
Lessons Learned
The lessons drawn from these case studies reinforce the critical nature of continuous improvement within non-destructive pipe testing protocols. One significant takeaway is the importance of training personnel who perform the tests. In one case, insufficient training led to a misinterpretation of results, delaying necessary repairs and creating safety concerns.
Additionally, these studies suggest that integrating advanced technologies can yield better outcomes. For instance, the adoption of automated ultrasonic testing systems has proven to increase accuracy and reduce human error in assessment processes. Moreover, the use of data analytics and modeling can enhance predictive maintenance capabilities, allowing operators to make informed decisions based on tested data rather than waiting for failures to occur.
Furthermore, the knowledge gathered from these case studies emphasizes the importance of regular maintenance and re-testing in various applications. Infrastructure age, environmental factors, and changes in service conditions can all affect pipeline integrity over time, necessitating ongoing vigilance to ensure safety and compliance.
Ending
The conclusion serves as a vital component in this article, providing a comprehensive wrap-up of the discussions on non-destructive pipe testing. A summary brings together the insights gained through the examination of various techniques and their applications across different industries. In doing so, it reinforces the importance of maintaining pipeline integrity without causing any damage to the materials.
Summary of Key Points
In this exploration of non-destructive pipe testing, several key points emerge:
- Definition and Purpose: Non-destructive testing (NDT) is employed to assess the integrity of materials while keeping them functional.
- Techniques: Various methods such as ultrasonic testing, magnetic particle testing, and radiographic testing are critical in revealing hidden defects and ensuring pipelines operate safely.
- Industry Application: This testing approach is prevalent in oil and gas, water supply, and chemical processing, highlighting its versatility.
- Challenges: Issues with material compatibility and technical limitations pose significant hurdles in the execution of NDT.
- Future Outlook: Advancements in technology and an increasing emphasis on sustainability indicate a promising future for non-destructive testing methodologies.
The Future Outlook of Non-Destructive Testing
The future of non-destructive testing appears bright as industries increasingly strive for safety and compliance. Innovations in technology, such as automation and artificial intelligence, can enhance existing testing methodologies. These advancements will likely improve accuracy and reduce the time required for testing.
Furthermore, sustainability is becoming a crucial consideration. Non-destructive testing contributes to reducing waste by extending the lifespan of pipelines and systems. As regulations become stricter, industries will seek out non-destructive techniques to ensure compliance with environmental standards.
"As we look towards the future, the integration of modern technology with traditional methods will redefine the landscape of non-destructive pipe testing, making it more efficient and impactful."
In closing, grasping the significance of non-destructive pipe testing allows industries to not only ensure safety but also embrace responsible practices. The insights presented underline its essential role in ongoing operations, indicating it will remain a cornerstone in maintaining pipeline integrity.