Exploring Quality Concrete: Standards and Innovations
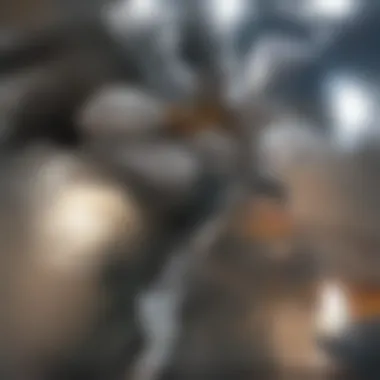
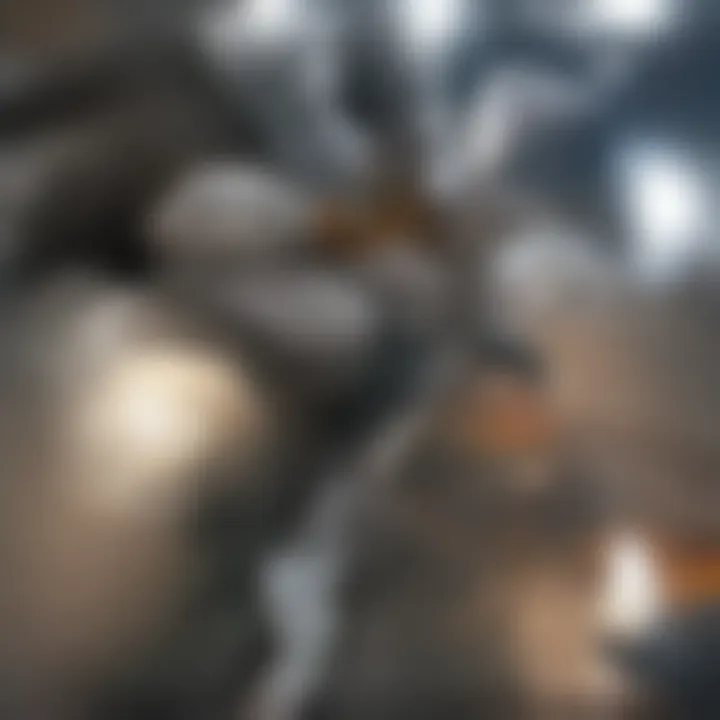
Intro
Concrete is a fundamental material in construction and engineering. Understanding what quality concrete is and how to ensure its production is essential for successful projects. Many factors define the quality of concrete, including its composition, mixing processes, and final application. This segment aims to clarify critical terms and concepts related to concrete quality, laying the foundation for subsequent discussions on standards, applications, and innovations.
Key Concepts and Terminology
Definition of Key Terms
Quality concrete refers to concrete that meets specific performance requirements for strength, durability, and workability. Some essential terms include:
- Compressive Strength: The ability of concrete to withstand axial loads without failure. Measured in megapascals (MPa), higher values indicate stronger concrete.
- Workability: This describes how easily concrete can be mixed, placed, and finished. Workable concrete is crucial for achieving proper consolidation and surface finish.
- Durability: The ability of concrete to resist weathering, chemical attack, and abrasion over time. Durable concrete ensures longevity and reduces the need for repairs.
Concepts Explored in the Article
In this article, we will explore several key concepts:
- Criteria for Quality: Identifying what makes concrete effective for specific uses. This includes evaluating materials, mixing techniques, and curing processes.
- Assessment Methods: Discussing various techniques for testing concrete properties, such as slump tests for workability, and compression tests for strength.
- Innovations: Examining recent advancements in concrete technology aimed at enhancing performance and sustainability.
Findings and Discussion
Main Findings
Research suggests that selecting high-quality raw materials is the first step in producing quality concrete. Aggregates, water, and cement must meet stringent specifications to ensure the final product's performance. Additionally, the mixing process significantly influences the concrete's properties. For example, achieving the ideal water-to-cement ratio is crucial for optimizing strength and workability.
"Quality assurance in concrete production must involve stringent material selection and precise mixing processes to meet engineering standards."
Innovations are changing how the industry approaches concrete. Emerging materials such as fiber-reinforced concrete and self-healing concrete promise improved durability and lower maintenance costs. Also, considering sustainability, recycled materials are increasingly used to reduce environmental impact while maintaining performance.
Potential Areas for Future Research
There remain gaps in the field that warrant further investigation:
- Long-term Durability Studies: More research could help understand how different mixes perform over decades in various environmental conditions.
- Sustainability Metrics: Developing standardized ways to measure the environmental impacts of concrete production, including lifecycle assessments.
- Innovative Admixtures: Exploring new chemical additives that may improve concrete properties without compromising workability or strength.
End
Understanding quality concrete involves recognizing the importance of materials and methods in production. As construction processes evolve, continuous research and innovation will be critical to improving this vital material. Engaging with these concepts is essential for anyone involved in civil engineering or construction management.
Understanding Quality Concrete
In the realm of construction and civil engineering, the term "quality concrete" encompasses a spectrum of factors that directly impact the overall integrity and longevity of structures. Understanding quality concrete not only involves an appreciation of the basic materials used but also an insight into the production process, testing methods, and application contexts. The ability to identify what constitutes quality in concrete is crucial for professionals who manage or influence construction projects.
One of the core elements of understanding quality concrete is recognizing the various properties that define it. Quality concrete must meet specific performance criteria such as compressive strength, workability, and durability. Each of these qualities contributes significantly to the functionality and safety of concrete structures. Thus, having a deep understanding of these properties helps architects, engineers, and contractors to make informed decisions during design and construction processes.
Furthermore, this understanding leads to better material selection, mixing techniques, and construction practices. When professionals grasp the significance of quality concrete, they are better equipped to avoid common pitfalls that can lead to structural failures or expensive repairs down the line. Therefore, it is essential to educate stakeholders on the nuances of concrete quality, which will ultimately drive improvements in construction standards and public safety.
Defining Quality in Concrete
Quality in concrete is primarily defined by its material composition and physical properties. Concrete is generally made from a mixture of water, cement, and aggregates. The ratios of these constituents and the quality of the materials directly influence the end product. For instance, the type of cement used, such as Ordinary Portland Cement or Sulfate-Resistant Cement, can alter the concrete’s performance in various environments.
Additional factors, such as the size and cleanliness of aggregates, play a significant role as well. Properly graded aggregates enhance the strength and workability of the mixture. Furthermore, having an appropriate water-cement ratio is critical, as too much water can lead to a decrease in strength, while too little can impede the mix’s ability to bind effectively. Effective monitoring of these constituents during mixing will ensure that the concrete achieves optimal quality characteristics.
Importance of Quality Concrete
Quality concrete is essential for a multitude of reasons, ranging from structural integrity to economic considerations. The foremost reason is that quality concrete provides safety for its users. High-quality concrete minimizes the likelihood of cracking, deformation, and structural failure, thereby safeguarding lives and investments.
In addition to ensuring safety, employing quality concrete can have economic implications. Structures built with high-standard concrete are typically more durable and require less maintenance. This longevity translates to reduced costs over the lifecycle of the project, making it a wise investment for contractors and clients alike. Moreover, societal perspectives on quality concrete play a role in shaping regulations and expectations in the construction industry, suggesting that quality standards may evolve over time.
In summary, recognizing and prioritizing quality concrete is not a mere technical detail; it is a critical component of reliable, safe, and economically viable construction. As technology and methodologies evolve, understanding the foundations of quality concrete will guide industry professionals through innovations and challenges alike.
Essential Properties of Quality Concrete
Concrete is a fundamental material in construction, and its properties determine the performance and longevity of structures. Understanding the essential properties of quality concrete is crucial for engineers, architects, and construction professionals alike. Each property impacts not only the immediate strength and usability of the concrete but also its future resilience under various conditions.
Here, we examine the core properties of quality concrete: compressive strength, durability, workability, and the phenomena of shrinkage and creep. Each of these factors plays a pivotal role in ensuring that a concrete structure meets its design objectives within the constraints of safety, costs, and environmental considerations.
Compressive Strength
Compressive strength is a primary measure of concrete quality, representing the ability of concrete to withstand axial loads without failure. This property is vital because it directly influences how concrete can be utilized in various structures, ranging from residential buildings to large-scale infrastructure projects.
In general, the higher the compressive strength, the more load the concrete can support. This strength is determined primarily by the mix design, which includes the ratio of cement, water, and aggregates. A well-balanced mix yields concrete that can endure substantial loads, thus enhancing the safety and integrity of structures. The compressive strength is usually expressed in megapascals (MPa) or pounds per square inch (psi).
Testing for compressive strength typically involves the use of standardized samples that are cured and then crushed to determine their load-bearing capacity. High-quality concrete can achieve compressive strengths exceeding 40 MPa in standard applications, while specialized mixes may reach upwards of 100 MPa or more.
Durability
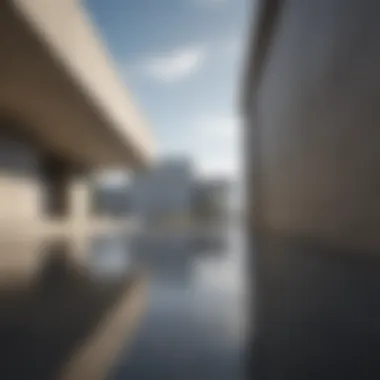
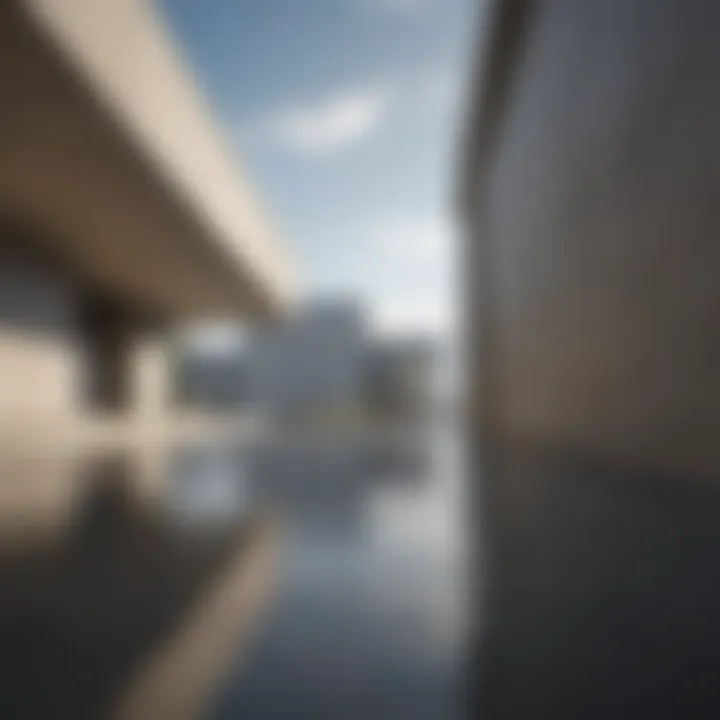
Durability is the ability of concrete to resist environmental factors that can cause deterioration over time. This property is particularly important in regions where concrete is exposed to harsh weather conditions, aggressive chemicals, or extreme temperature fluctuations. Evaluating durability allows professionals to predict the lifespan of a concrete structure and determine maintenance needs.
Several aspects contribute to the durability of concrete:
- Porosity: A lower porosity generally results in better resistance to water ingress and chemical penetration.
- Abrasion Resistance: Concrete needs to withstand mechanical wear in high-traffic areas, which may degrade its surface over time.
- Chemical Resistance: Concrete structures in industrial areas are particularly vulnerable to chemical attacks; hence, choosing appropriate cement types and additives is critical.
Investing in durable concrete leads to lower maintenance costs and a reduced failure rate, underscoring the importance of durability in quality concrete production.
Workability
Workability refers to how easily concrete can be mixed, placed, and finished. This property is essential for ensuring that the concrete reaches the desired shape and density without requiring excessive effort or risking the integrity of the material. Good workability facilitates proper placement in complex forms and reduces the likelihood of defects.
Factors affecting workability include:
- Water-Cement Ratio: A higher water content improves workability but can negatively impact strength.
- Aggregate Size & Grading: Smaller and well-graded aggregates help achieve better fluidity.
- Admixtures: Chemical admixtures can modify workability without altering the material's properties.
Proper attention to workability is essential; too stiff a mix leads to poor placement, while too fluid a mix may compromise strength.
Shrinkage and Creep
Shrinkage and creep are phenomena associated with the long-term behavior of concrete.
- Shrinkage refers to the reduction in volume as the moisture content decreases, which can lead to cracking if not addressed properly.
- Creep is the gradual deformation of concrete under sustained load over time, affecting structural performance.
Effective management of shrinkage and creep involves selecting appropriate materials and incorporating design strategies that accommodate these natural behaviors. Understanding these concepts is critical, especially in long-span structures where deformation can have significant implications for safety and serviceability.
In summary, the essential properties of quality concrete — compressive strength, durability, workability, and shrinkage/creep — are interrelated and play critical roles in the performance and longevity of concrete constructions. Incorporating a comprehensive understanding of these aspects into concrete production processes helps ensure the creation of robust and reliable structures.
Materials in Quality Concrete Production
The quality of concrete heavily relies on the materials used in its production. This section highlights the critical components—cement, aggregates, and water—and their roles in determining the overall performance of concrete. The correct choice and proportioning of these materials influence durability, strength, workability, and sustainability outcomes. By understanding these elements, professionals can make informed decisions, ensuring effective concrete solutions across various applications.
Cement Types and Their Qualities
Cement forms the binding agent in concrete. Different types of cement have unique properties tailored for specific applications. The most common types include Portland cement, blast furnace slag cement, and pozzolanic cement. Each possesses distinct characteristics that affect the concrete's performance.
- Portland cement is widely used due to its general applicability and strong binding capacity.
- Blast furnace slag cement is a sustainable choice, made from industrial by-products, offering improved resistance to sulfate attacks.
- Pozzolanic cement incorporates fly ash or silica fume, enhancing the long-term strength and durability of concrete.
Selecting appropriate cement depends on project requirements like exposure conditions, load-bearing needs, and environmental sustainability goals. Understanding cement types aids in achieving desired properties, minimizing issues later.
Aggregate Quality and Its Impact
Aggregates make up a significant portion of concrete, typically about 70-80% of its volume. The quality and characteristics of aggregates directly influence the performance and durability of concrete. Key considerations include:
- Size and Gradation: Proper size distribution enhances compaction and reduces voids.
- Shape and Texture: Angular aggregates provide better interlocking, improving strength.
- Cleanliness: Impurities like clay and silt can weaken the concrete mix.
Concrete containing high-quality aggregates enhances durability and reduces shrinkage and cracking. Inadequate aggregate quality can lead to compromised structural integrity over time, making material selection a critical factor in concrete production.
Water-Cement Ratio
The water-cement ratio is fundamental in determining the strength and durability of concrete. A lower water-cement ratio usually results in superior strength and durability, while an excessively high ratio can lead to weak and porous concrete. This ratio directly influences:
- Workability: Adequate water ensures the mix can be handled easily, but excess water reduces strength.
- Hydration Process: Proper hydration is necessary for achieving desired strength. Insufficient water can inhibit this process.
Achieving the correct water-cement ratio requires precise calculations during the mix design phase. Balancing water content with workability and strength goals is essential for producing quality concrete. Understanding this ratio enhances overall performance and longevity of concrete structures.
Testing and Assessment of Concrete Quality
The topic of testing and assessment of concrete quality is critical in the field of civil engineering and construction. Quality concrete is essential for ensuring the durability, strength, and overall longevity of structures. Therefore, understanding how to measure these parameters accurately is vital. Proper testing methods not only verify the compliance of concrete with required standards but also help to identify possible weaknesses in the mixture or application. Using the right assessment techniques can lead to substantial improvements in construction practices, reducing costs and enhancing safety.
In this section, we will explore the key aspects surrounding the testing and assessment of concrete quality, focusing on standard testing methods, field versus laboratory testing, and non-destructive testing techniques. Each of these methods provides unique insights into the performance characteristics of concrete under various conditions.
Standard Testing Methods
Standard testing methods constitute the backbone of concrete quality assessment. These methods ensure that concrete meets the required standards set by various engineering bodies. Some commonly used tests include:
- Compressive Strength Test: This test measures the concrete's ability to withstand axial loads. It is generally conducted using a cube or cylinder sample which is subjected to uniaxial compression until failure.
- Slump Test: This is a quick field test to determine the workability of fresh concrete. The result is an indication of how easily the concrete can be mixed and placed in its intended form.
- Air Content Test: This test helps to understand the amount of air trapped in the concrete mixture, which can affect durability and strength. It is essential for concrete exposed to freeze-thaw conditions.
- Flexural Strength Test: This test assesses the tensile properties of concrete by applying stress until the specimen fails. This metric is vital in evaluating how concrete performs under bending forces.
Each of these tests serves a distinct purpose and provides valuable information about the quality of the concrete used in various applications.
Field vs. Laboratory Testing
The choice between field testing and laboratory testing has significant implications for evaluating concrete quality.
- Field Testing: This approach allows for immediate assessment of fresh concrete. Tests such as the slump test or temperature measurement can be performed on-site. Field testing is beneficial for quick evaluations and can alert engineers to potential problems in real-time.
- Laboratory Testing: This is often more thorough and provides controlled conditions for accurate measurements. Concrete samples can be cured and tested under specific conditions to yield reliable performance metrics. This method allows for comprehensive analyses like compressive strength over time or durability assessments.
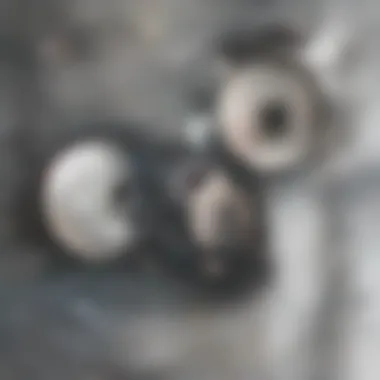
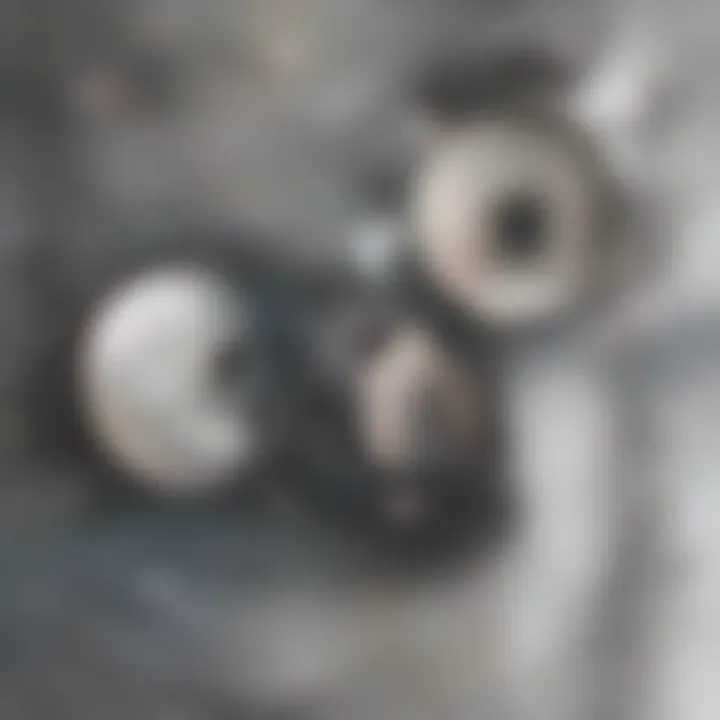
Both methods have their advantages and disadvantages. Choosing one over the other often depends on the project requirements and specific circumstances surrounding the construction efforts.
Non-Destructive Testing Techniques
Non-destructive testing (NDT) techniques play a pivotal role in assessing existing concrete structures without causing any damage. These techniques provide critical data regarding the condition of concrete in-service. Common methods include:
- Ultrasonic Pulse Velocity Test: This method evaluates the quality of concrete by sending ultrasonic waves through it. Variability in travel time can indicate voids or cracks within the material.
- Rebound Hammer Test: This is a portable tool used to provide a relative measure of the concrete surface hardness, which correlates to compressive strength.
- Ground Penetrating Radar (GPR): GPR is utilized to map the subsurface of concrete, identifying rebars, voids, and potential delaminations without disrupting the structure.
Using NDT techniques improves maintenance practices, allowing for timely interventions that can extend the lifespan of concrete structures.
"Quality concrete testing ensures safety and longevity in construction, highlighting essential features that may otherwise go unnoticed."
In summary, testing and assessment of concrete quality encompasses various methodologies, each tailored to meet specific project demands and conditions. By employing a combination of standard tests, field evaluations, laboratory assessments, and non-destructive techniques, engineers can acquire a comprehensive understanding of concrete performance. This knowledge ultimately contributes to the manufacturing of authentic quality concrete, crucial for all construction endeavors.
Quality Control in Concrete Production
Quality control in concrete production is a vital component in ensuring the final product meets required standards. This area focuses on maintaining and improving the qualities of concrete, which is essential for safety and longevity in construction projects. Concrete that is not produced under strict quality control may lead to structural failures, costly repairs, and potential hazards. Given its widespread use in various applications, understanding quality control processes is imperative for all involved in civil engineering and construction management.
Effective quality control incorporates several elements that impact both the production process and the final outcomes. This includes meticulous assessment of raw materials, adherence to mixing procedures, and regular testing of the final product. One significant aspect is the evaluation of materials used, especially cement types and aggregates, which greatly influence concrete properties. Ensuring a controlled environment during mixing helps achieve the desired consistency and workability.
Key benefits of implementing quality control in concrete production include:
- Improved durability of concrete in adverse conditions.
- Enhanced strength, leading to safer structures.
- Increased operational efficiency and reduced waste, saving costs in the long term.
- Compliance with regulatory standards, ensuring legitimacy and trust.
Moreover, maintaining quality control also involves documentation and traceability of production processes. A systematic approach allows for identification of discrepancies and facilitates corrective actions. This is crucial, especially in large-scale projects where multiple batches of concrete may be used. Effective record-keeping provides a historical account that programmers can refer back to, which is particularly useful during audits or quality assessments.
Quality Management Systems
A robust quality management system (QMS) is essential for any concrete production facility. It encompasses a set of policies, processes, and procedures designed to ensure that quality standards are met consistently. The QMS framework aids in minimizing product variability, which can directly affect the overall quality of concrete. An efficient QMS should cover every stage of production—from the procurement of raw materials to delivery of the finished product.
The ISO 9001 standard is widely recognized and provides guidelines for establishing an effective QMS. Implementing such standards leads to improved operational efficiency, customer satisfaction, and regulatory compliance.
Elements of an effective QMS include:
- Document control to ensure all procedures are updated.
- Regular training for personnel on best practices.
- Internal audits to assess the efficiency of quality controls in place.
- Corrective actions for any issues identified in material quality or processes.
By focusing on these key areas, a concrete manufacturer can achieve higher production standards and reduce risks associated with poor quality.
Regulatory Standards and Compliance
Navigating regulatory standards and ensuring compliance is a critical aspect of quality control in concrete production. Various organizations and standards bodies set guidelines that help maintain safety and quality within the industry. For example, the American Concrete Institute offers standards that influence design and construction practices.
Compliance with these standards not only ensures the safety of structures but also protects producers from legal liabilities. Adhering to regulations can build trust with clients and stakeholders, reinforcing the reputation of a company within the industry.
Common regulatory standards include:
- ASTM C150 - Specifications for Portland Cement.
- ASTM C33 - Standard Specification for Concrete Aggregates.
- ACI 318 - Building Code Requirements for Structural Concrete.
Establishing a compliance program that encompasses training, internal audits, and quality assessments can greatly enhance the management of construction projects. This proactive approach towards compliance ensures that all aspects of concrete quality are consistently maintained.
Innovations in Concrete Technology
Innovations in concrete technology play a crucial role in the advancement of construction methods and material performance. The evolution of concrete is not just about improving strength; it is about increasing durability, reducing environmental impact, and enhancing functionalities. This section will delve into various innovations, particularly focusing on self-healing concrete, sustainable solutions, and the application of 3D printing techniques. Each of these areas presents unique benefits that can dramatically alter construction practices.
Self-Healing Concrete
Self-healing concrete represents a significant breakthrough in reducing maintenance costs and extending the lifespan of concrete structures. This type of concrete contains special agents, such as bacteria or chemical capsules, which activate upon cracking. As soon as a crack forms, the agents are released and react with moisture and carbon dioxide to fill the void, effectively healing the damage without human intervention.
The benefits are clear. It can reduce the need for repairs, which can be costly and labor-intensive. Moreover, self-healing concrete improves the structural integrity of buildings, leading to greater safety. It is particularly useful in infrastructure projects where monitoring and repair can be challenging and expensive.
Sustainable Concrete Solutions
Sustainable concrete solutions focus on minimizing the environmental footprint of concrete production and use. This involves various strategies, including the use of recycled materials, such as reclaimed concrete and industrial by-products like fly ash and slag. These materials can replace a portion of traditional cement, which reduces greenhouse gas emissions associated with cement production.
Additionally, innovations like geopolymer concrete offer an eco-friendly alternative. This type of concrete utilizes materials like fly ash or slag that are activated by alkaline solutions, emitting significantly fewer pollutants compared to ordinary Portland cement. The environmental advantages align well with global movements toward sustainability in construction.
3D Printing with Concrete
3D printing technology has begun to revolutionize the construction industry. By allowing for complex shapes and designs to be created more efficiently, 3D printing with concrete reduces material waste and can cut labor costs. The technology enables the construction of unique structures that would traditionally take longer and require more resources.
3D printing also facilitates on-demand construction. Buildings can be produced with speed and precision, lowering the barriers to custom design. Furthermore, it allows for innovative architectural possibilities, which can be combined with sustainable practices. The use of automated processes in 3D printing contributes to consistent quality in concrete structures.
Innovations in concrete technology not only enhance structural performance but also align with environmental and economic sustainability goals.
Applications of Quality Concrete
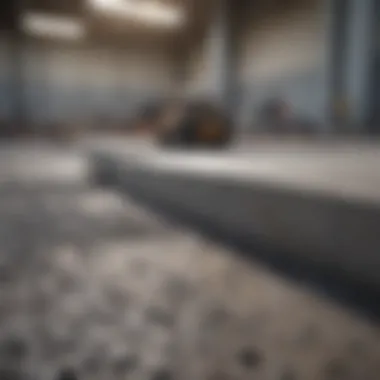
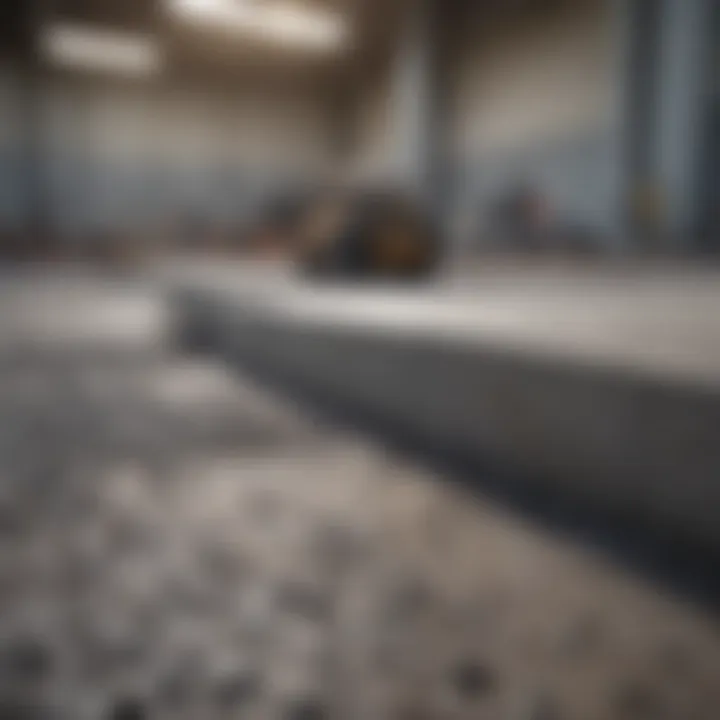
The applications of quality concrete are vast and pivotal within the construction industry. Understanding where and how quality concrete is utilized provides insights into not only its importance but also its functionality and adaptability. Quality concrete plays a crucial role in ensuring durability, structural integrity, and efficiency. Each application has specific requirements that must be met, and the benefits derived from using quality materials are substantial.
Residential Construction
In residential construction, quality concrete forms the backbone of homes, providing strength and stability. Foundations, walls, and driveways benefit significantly from high-quality concrete mixtures. One critical element is ensuring that the concrete mix adheres to regional building codes and standards. Using quality concrete enhances the longevity of the structures, reducing long-term maintenance costs. Additionally, it can improve energy efficiency, as insulating concrete forms create a barrier that minimizes energy loss. For homeowners, investing in quality concrete means fewer repairs over time, which ultimately adds value to their property.
Considerations in residential concrete applications include:
- Climate Adaptability: Selecting appropriate concrete types for various weather conditions can prevent issues like cracking.
- Aesthetic Options: Different finishes and treatments can be applied to concrete surfaces, enhancing visual appeal while maintaining the foundational benefits.
Commercial and Industrial Uses
The commercial and industrial sectors rely heavily on quality concrete for a myriad of applications. Factories, warehouses, and commercial buildings often require substantial load-bearing capacity and resilience. Quality concrete is critical in constructing heavy-duty floors that must withstand constant wear and tear. Furthermore, safety regulations necessitate high standards in concrete for industrial applications.
An additional benefit is the speed of construction. Using pre-mixed quality concrete allows for quicker setting times, accelerating project completion. Without compromising on safety or quality, businesses can reduce downtime, leading to increased productivity.
"Quality concrete not only meets the structural needs of commercial establishments but also enhances their operational efficiency."
Key benefits in this sector involve:
- Cost-Effectiveness: Long-lasting quality minimizes repairs, contributing to lower operating costs over time.
- Design Flexibility: Quality concrete can accommodate various architectural designs, providing the versatility required in modern commercial aesthetics.
Infrastructure Projects
Infrastructure projects such as bridges, highways, and public facilities are perhaps the most critical applications of quality concrete. These structures face immense stress and require unwavering durability. The longevity and safety of infrastructures depend on the quality of materials used during construction.
In this realm, monitoring standards is of utmost importance. Tests such as compressive strength assessments ensure that concrete can endure environmental stressors. Moreover, with innovations in concrete technology, such as self-healing concrete, there are opportunities to enhance infrastructure resilience, combating deterioration over time.
Important aspects of concrete in infrastructure include:
- Public Safety: Quality concrete provides necessary support in crucial areas, minimizing risks of structural failure.
- Sustainability: There is a growing trend towards using recycled materials and blends that maintain quality while promoting environmental sustainability.
Challenges in Achieving Quality Concrete
Achieving quality concrete is pivotal for the strength and durability of structures. However, various challenges complicate the production process. It is critical to understand these challenges to improve outcomes in construction projects. The importance of this topic lies in recognizing the nuances involved and addressing them systematically.
Environmental Factors
Environmental factors play a significant role in concrete quality. Temperature variations can drastically affect the curing process. For instance, high temperatures can lead to quick evaporation of water from the mix, compromising hydration and, consequently, the final strength of the concrete. Cold weather, on the other hand, can slow down curing, leading to potential freezing of the mix. This affects the chemical changes necessary for achieving strength.
Moreover, adverse weather conditions such as rain can introduce excess water into the mix, altering the water-cement ratio. Without strict controls, these environmental influences can lead to deficiencies like cracking or a reduction in compressive strength. Mitigating these risks involves planning site operations according to weather forecasts and modifying mix designs to suit specific environmental conditions.
Economic Considerations
Economic considerations are also integral to the challenges faced in concrete quality assurance. The cost of raw materials has seen fluctuations which can impact the choices available for concrete mixes. For example, high-quality aggregates may be more expensive, yet their use can substantially enhance durability, leading to better long-term performance and less maintenance.
Additionally, the pressure to minimize costs can lead to compromises. Some contractors may opt for lower-grade materials to reduce expenditure, unknowingly jeopardizing not only the quality of concrete produced but also the safety and longevity of the structure. Investing in quality materials, despite the upfront costs, can save significant amounts in future repairs and replacements.
To address these economic challenges, it is essential to balance budget constraints with the need for quality. Awareness of life-cycle costs can guide better decisions about material selection and investments in quality assurance practices.
Technological Limitations
Technological limitations present another barrier to achieving superior concrete quality. While advances in concrete technology have been substantial, not all producers have access to the latest equipment or methods for testing and quality control. For example, the use of innovative admixtures to enhance workability or durability relies on sophisticated knowledge and facilities that may not be available in all markets.
Moreover, there is often a gap between research and practical application. New technologies, like advanced non-destructive testing methods, may not be utilized broadly in the industry due to resistance to change or lack of training. This limits the ability to assess concrete quality accurately and efficiently throughout the production process.
Overall, confronting these technological challenges is vital. Greater investment in training, equipment, and research can improve the quality of concrete significantly.
"Understanding the challenges is the first step to enhancing concrete production methods and ensuring the delivery of quality structures."
By recognizing these challenges, stakeholders can develop strategies to improve the quality of concrete, ensuring the safety and durability of structures for future generations.
The End
The conclusion of this article serves as a vital summary of discussions surrounding the quality of concrete. It ties together the insights on standards, applications, and innovations that impact concrete in construction. A clear comprehension of these elements is critical for stakeholders across the civil engineering landscape.
First, recognizing the importance of quality concrete cannot be understated. Quality concrete not only assures structural integrity but also ensures the longevity and sustainability of constructions. This article has outlined how compressive strength, durability, and workability contribute to the overall performance of concrete. In addition, understanding the influence of materials and environmental factors is paramount.
By adopting rigorous standards and innovative approaches, the industry can tackle the challenges associated with concrete production. Quality control and regulatory compliance stand as pillars that safeguard the interests of both producers and consumers alike. Therefore, continuous improvement in methodologies and technologies will foster advancements that maximize the potential of concrete as a material.
"Adhering to quality standards in concrete production is essential for achieving long-lasting infrastructure that meets the needs of society."
Summary of Key Points
- Defining Quality: Quality concrete is characterized by its strength, durability, and workability, among other factors.
- Importance: It plays a crucial role in ensuring safety and longevity in construction projects.
- Materials Matter: The selection of materials such as cement, aggregates, and water must be managed to achieve desirable properties.
- Testing and Standards: Various testing methods are necessary to assess concrete's quality effectively, both in the field and in labs.
- Control Systems: Structured quality management systems ensure compliance with regulatory standards and maintain high production standards.
- Innovations: Advances in technology, such as self-healing and sustainable concrete solutions, represent significant leaps forward.
- Applications: Quality concrete finds critical use in residential, industrial, and infrastructural projects.
- Challenges: Environmental, economic, and technological factors present hurdles that must be navigated.
Future Directions in Concrete Research
Looking forward, the field of concrete research must integrate more sustainable practices. This includes exploring renewable materials and methods that reduce carbon emissions associated with concrete production. Further investigation into high-performance mixtures and innovative manufacturing processes will be invaluable.
Additionally, research needs to focus on enhancing the durability of concrete in varying climates. Long-term studies assessing the lifecycle performance of concrete structures can provide essential insights for future applications. Overall, the movement towards resilient and environmentally-friendly concrete aligns with global sustainability goals, setting the stage for impactful advancements in construction.