Comprehensive Study of Quench Towers in Industry
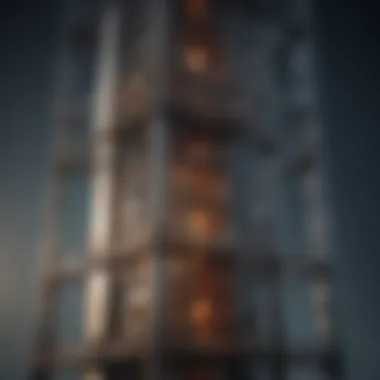

Intro
In the realm of industrial processes, the quench tower stands out as a pivotal component for achieving thermal management. This apparatus is more than just a cooling unit; it represents a sophisticated integration of engineering principles that significantly affects production efficiency and safety. Understanding its operational principles and design features is essential for those involved in various sectors like chemical manufacturing, metals processing, and even thermal energy management.
Quench towers are not merely boxes of pipes and cooling water but are intricately designed to handle specific tasks, contributing to both energy efficiency and process control. In this article, we will dissect the various aspects of quench towers, examining their terminology, findings from recent studies, and paths for future exploration.
Key Concepts and Terminology
Definition of Key Terms
Before diving deeper into the discussion, it’s vital to clarify some terms that will frequently be used:
- Quench Process: A fast cooling method often used for metals or chemical reactions.
- Thermal Equilibrium: The state where the temperature throughout a system is uniform, crucial for optimal quenching.
- Cooling Load: The amount of heat energy that must be removed to maintain a desired temperature in a process.
Concepts Explored in the Article
In our examination of quench towers, we will tackle several key themes:
- Types of Quench Towers: Discussing differences based on their specific applications in the industry.
- Construction materials: Consideration of what materials offer the best efficiency and durability.
- Efficiency metrics: Evaluating how different designs perform concerning energy consumption and thermal performance.
Findings and Discussion
Main Findings
The research unveils the complexity behind quench tower design. Contrary to conventional wisdom, it’s not merely about pumping water through a tower; many factors come into play:
- Material Selection: Often overlooked, the choice of materials impacts not just efficiency but also longevity. For example, stainless steel quench towers show impressive resistance to corrosion, ensuring lower maintenance costs over time.
- Flow Dynamics: The arrangement of the flow of the cooling medium can alter performance dramatically. Proper design minimizes turbulence and maximizes heat transfer, achieving that sweet spot of thermal management.
- Environmental Considerations: Modern quench towers often incorporate sustainability practices, utilizing recycled water to cut down on freshwater usage and reduce operational costs.
This nuanced understanding of quench tower operation directly correlates to quantifiable benefits in industrial settings. Potential case studies have shown that optimizing these systems can lead to energy savings of 10% to 20%, a significant figure considering the cumulative operational costs in large facilities.
Potential Areas for Future Research
Future explorations in quench tower technology should not be taken lightly. The following areas merit attention:
- Advanced Materials: Researching new composite materials that could potentially improve efficiency or reduce costs has potential.
- Smart Monitoring Systems: Implementing IoT technology to monitor real-time performance metrics can enhance responsiveness and preventive maintenance.
- Regulatory Adaptations: As environmental regulations become tighter, adaptations in quench tower designs to comply with legal standards will also be an important focus.
“Understanding quench towers and their applications in modern industry could unlock new potentials for energy management and efficiency.”
As we look to the future of thermal management in industrial processes, quench towers will undoubtedly play a central role. The continuous evolution of this technology will require professionals and researchers alike to stay informed and adaptable to these advancements.
Prelims to Quench Towers
Quench towers play a vital role in the thermal management landscape of industrial processes. These structures are designed to rapidly cool down various materials, enhancing their stability and usability across different sectors. Understanding quench towers is crucial for engineers and professionals in the chemical and metallurgical industries, as these systems are integral to both safety measures and efficiency in operations. With the increasing demands for effective cooling solutions and environmental considerations taking center stage, the importance of optimizing quench tower designs cannot be overstated.
Definition and Purpose
A quench tower, in essence, serves the primary function of cooling hot materials quickly, typically using water or other coolants. This process is essential in several industrial applications, such as in the production of steel, where molten metal needs rapid cooling to obtain the desired structural properties. The fast transfer of heat helps prevent unwanted structural deformations and promotes safety in operations.
In broad strokes, the purpose of quench towers extends beyond mere cooling; they also contribute to the overall efficiency of the manufacturing process. By allowing for rapid temperature reduction, these systems minimize thermal gradients that can lead to cracks or failures in materials. Furthermore, quench towers aid in waste heat recovery, capturing and reusing thermal energy, which can translate to substantial cost savings and reduced environmental impact.
Historical Context
To fully appreciate modern quench towers, one should consider their evolution through history. The roots of these systems can be traced back to the early industrial age when manufacturers first grappled with the challenges of heat management. Initially, rudimentary methods involved soaking materials in water or using air cooling, which often resulted in inconsistent results and sub-optimal material characteristics.
As industries grew and technology advanced, engineers began developing more structured cooling solutions. By the mid-20th century, quench towers emerged as standardized cooling systems. With advancements in materials science, control technologies, and fluid dynamics, contemporary quench towers are now sophisticated machines that can handle variable flow rates and provide precise cooling profiles tailored to specific materials.
Today, innovative designs are continuously developed, reflecting the ongoing quest for efficiency and sustainability in industrial practices. This historical context underscores not just the significance of quench towers in current applications but also how they have been shaped over time by the prevailing technological landscape.
Operational Principles of Quench Towers
Quench towers sit at the crossroads of thermal management and safety in industrial processes. Understanding their operational principles is critical not just for the design and effectiveness of these systems, but also for optimizing processes where heat removal is a priority. Quench towers play a fundamental role, especially in industries such as chemical processing and metallurgy. They ensure products maintain structural integrity, reduce risks of thermal shock, and enhance the efficiency of cooling operations.
Thermodynamics of Quenching
The thermodynamic principles that underlie quenching are pivotal. Quenching refers to the rapid cooling of a material, usually metal, by immersing it in a cooling medium. This process drastically alters the material's microstructure, leading to enhanced mechanical properties, such as increased hardness and strength. The effectiveness of quenching can be significantly influenced by several factors, including:
- Cooling Rate: The rate at which heat is removed from the material. A fast cooling rate can lead to significant changes in microstructure but may also cause cracking due to thermal stresses.
- Cooling Medium: The choice of quenching medium — whether water, oil, or specialized polymers — dramatically affects the cooling efficiency. For instance, water has a higher heat capacity compared to oil, thus providing a more rapid heat extraction.
- Initial Temperature: Starting temperatures of the material before quenching can greatly affect the outcome. Higher starting temperatures may require different cooling strategies.
By optimizing these elements, industries can achieve desired material properties while minimizing risks associated with uneven cooling.
Heat Transfer Mechanisms
Heat transfer in quench towers operates on three basic mechanisms: conduction, convection, and radiation. Each plays a unique role in how heat is dissipated from hot materials to the cooling medium:
- Conduction: This is the transfer of heat through solids. In quench towers, the solid material being cooled conducts heat to the surrounding medium.
- Convection: As the cooling medium moves, it takes away heat from the surface of the material. Forced convection, often achieved through pumps or fans in quench towers, increases efficiency by enhancing fluid movement and heat extraction.
- Radiation: Though often negligible at high temperatures, radiation can contribute to heat loss, especially when objects are at elevated temperatures.
The interplay of these mechanisms defines the overall efficiency of the quenching process. A well-designed quench tower will optimize these heat transfer mechanisms to ensure effective cooling.
Fluid Dynamics Considerations
Fluid dynamics is a cornerstone of quench tower design and operation. Understanding how fluids behave within the tower impacts efficiency and performance. Considerations include:
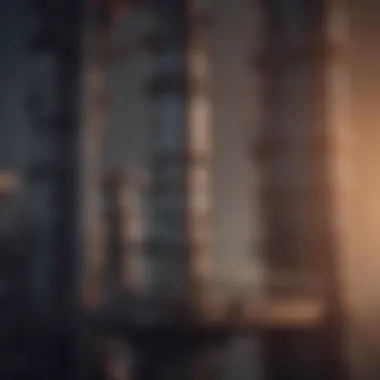
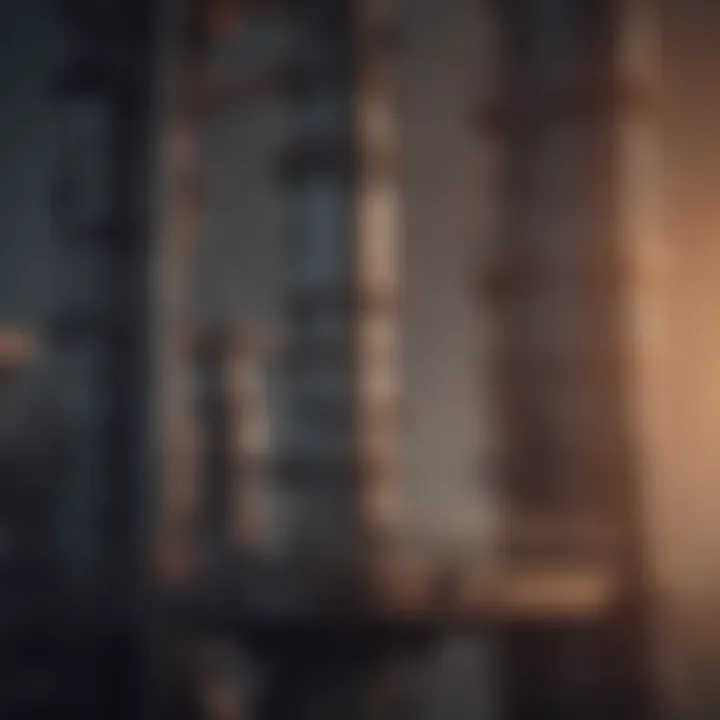
- Flow Patterns: The configuration of quench towers, whether counterflow or crossflow, will dictate how fluids interact and transport heat. Knowing these patterns helps in designing for even distribution and minimizing hot spots.
- Pressure Drop: A critical factor, excessive pressure drop can fan out the system, leading to increased energy consumption. Balancing flow rates and designing for optimal channeling can mitigate this risk.
- Viscosity and Density: The properties of the cooling fluid affect its flow behavior. Heavier fluids with higher viscosity may lead to slower flow rates, which can hinder heat transfer performance.
In essence, fluid dynamics considerations also dictate how effectively heat is removed, solidifying the necessity of advanced modeling and simulations in quench tower design.
"The real power of a quench tower isn’t just in the cooling process, but in how it integrates with the whole system—a fusion of thermal physics, materials science, and fluid dynamics."
In summary, the operational principles of quench towers are intrinsically tied to thermodynamics, heat transfer mechanisms, and fluid dynamics. Understanding these elements thoroughly leads to the optimization of designs and processes, making them critical not just for producing better materials but also for enhancing safety and efficiency in industrial settings.
Types of Quench Towers
The variety of quench towers plays a pivotal role in optimizing thermal management across industries. Understanding the different types is essential for engineers and operators, as each has unique characteristics that suit specific applications. By recognizing the distinctions among counterflow, crossflow, and other specialized designs, professionals can tailor their cooling strategies to the demands of their respective processes.
Counterflow Quench Towers
Counterflow quench towers present a straightforward yet effective design where the cooling medium travels upwards against the flow of the hot gas. This configuration enhances heat exchange efficiency due to the temperature gradient. In a sense, it’s akin to how cold water meets the steam rising in a sauna; the cooler the water, the more effective the heat transfer becomes.
The advantages of counterflow towers include:
- Higher efficiency: Since the coldest water meets the hottest gases, heat exchange is maximized.
- Reduced energy consumption: As heat is removed more effectively, overall energy demands of the system may decrease, leading to diminished operational costs.
- Compact design: These towers often require less space, making them a preferred choice in tight or land-constrained environments.
However, a downside is the potential for flooding if the water distribution system isn't properly designed. This necessitates meticulous engineering to ensure balanced flow.
Crossflow Quench Towers
Crossflow quench towers, on the other hand, offer a different operational approach. Here, the cool water flows horizontally across the path of the ascending hot gases. This design can be visualized similarly to the wind mixing with a gentle river current. A vital characteristic of crossflow towers is their ability to handle varying flow rates and temperatures, which is crucial in systems where operating conditions can change unpredictably.
Key points of crossflow towers include:
- Flexibility: They can accommodate a wide range of process conditions and are often easier to maintain.
- Improved accessibility: Generally, their design allows for better access during inspections and repairs.
- Lower susceptibility to fouling: The transverse water flow can reduce the accumulation of debris and contaminants, resulting in fewer operational issues.
However, it may not achieve the same efficiency levels as counterflow towers in some situations. A nuanced understanding of fluid dynamics in design is crucial to optimizing the heat exchange in these systems.
Other Specialized Designs
Besides the popular counterflow and crossflow configurations, there's a range of specialized designs that cater to specific needs within industrial processes. These can include:
- Falling film quench towers: In this type, a film of water flows down the walls of the tower, ensuring maximum surface area exposure to the hot gases.
- Hybrid models: These combine features from both counterflow and crossflow systems, allowing for versatility and enhanced performance in multifaceted industrial settings.
- Modular towers: These designs permit customization of the tower size and shape based on operational needs, allowing operators to adapt as required.
Specialized designs are all about addressing particular needs—think of them as tailored suits. Not every business will need the same fit, and some may require adjustments for comfort and effectiveness in their specific environments.
Design Considerations for Quench Towers
When delving into the workings of quench towers, several design considerations must be taken into account, as these factors ultimately affect the efficiency, safety, and overall performance of the systems. A quench tower, serving as a crucial component in thermal management, requires meticulous planning and thorough understanding of the operational environment it will be used in.
Material Selection
Choosing the right materials for the construction of quench towers is not merely a matter of preference. The selection heavily influences the durability and effectiveness of the tower. Commonly employed materials include stainless steel and corrosion-resistant alloys due to their resilience against chemicals and varying temperatures.
Using subpar materials can lead to premature wear and tear, causing structural failures that can be costly in time and resources. High-quality materials can ensure longevity, improved thermal conductivity, and resistance to fouling and scaling, which are vital considerations in maintaining optimal operational conditions.
Additionally, factors such as cost, availability, and regulatory compliance must also be examined prior to finalizing material choice. Environmental impact should be a concern as well, pushing designers to opt for sustainable materials whenever possible.
"Selecting quality materials is like laying a solid foundation for a house; it determines the longevity and safety of the structure."
Sizing and Configuration
Sizing and configuration are equally critical to the functional design of quench towers. The dimensions of the tower depend largely on the volume and temperature of the process fluids being handled. A larger volume typically requires more robust cooling structures, while the configuration must facilitate adequate fluid flow and air distribution.
Factors to consider here include:
- Flow Rates: The amount of fluid entering the tower affects both the internal design and the overall size.
- Cooling Requirements: Preliminary cooling requirements must align with the tower’s specifications to ensure efficient heat removal.
- Space Constraints: Physical limitations within the plant layout may dictate the shape or height of the quench tower, requiring creative approaches to cooling without sacrificing performance.
A proper sizing ensures that the cooling capacity is matched with the operational needs, preventing inefficiencies that could lead to downtime or increased operational costs. Misjudging the size can result in insufficient cooling, leading to process inefficiencies or even failure.
Safety and Regulatory Standards
Finally, safety is paramount in the design of quench towers. Regulatory standards dictate numerous aspects of the design, from material choice to operational thresholds. These regulations are set to protect not only the equipment itself but also the personnel and environment surrounding the operation.
Incorporating safety features like emergency shutdown systems, pressure relief valves, and monitoring sensors for detecting leaks or malfunctions can significantly mitigate risks. Designers must stay abreast of both local and international regulations, often consulting agencies or safety professionals to ensure compliance.
Regulatory bodies like the Occupational Safety and Health Administration (OSHA) in the U.S. offer guidelines that, if followed, can prevent the occurrence of catastrophic failures or accidents. Additionally, proper documentation and regular inspections can uphold safety standards throughout the operational life of the quench tower.
Overall, thoughtful consideration given to material selection, sizing, configuration, and adherence to safety standards forms the backbone of an efficient and reliable quench tower. Each project demands a tailored approach to fit specific operational needs while ensuring safety and compliance.
Applications of Quench Towers
Quench towers stand as crucial components in the realm of industrial processes, serving various purposes across multiple sectors. Given their ability to rapidly dissipate heat and control thermal dynamics, they play a fundamental role in maintaining process efficiency and safety. The significance of quench towers extends beyond mere cooling; they ensure that industrial operations run smoothly and comply with stringent safety regulations. Understanding their applications not only elucidates their functionality but also highlights their importance in optimizing production outcomes and enhancing environmental responsibility.
Chemical Processing Industries
In the world of chemical engineering, quench towers are vital for managing thermal stress during chemical reactions. Within these industries, chemical reactions often produce excessive heat, leading to potential thermal runaway situations if not carefully controlled. Quench towers facilitate rapid cooling of reactants, thereby stabilizing the reactions and ensuring the safety of personnel and equipment.
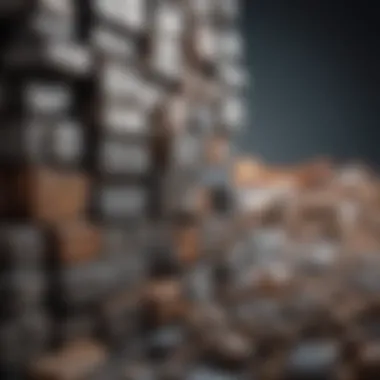
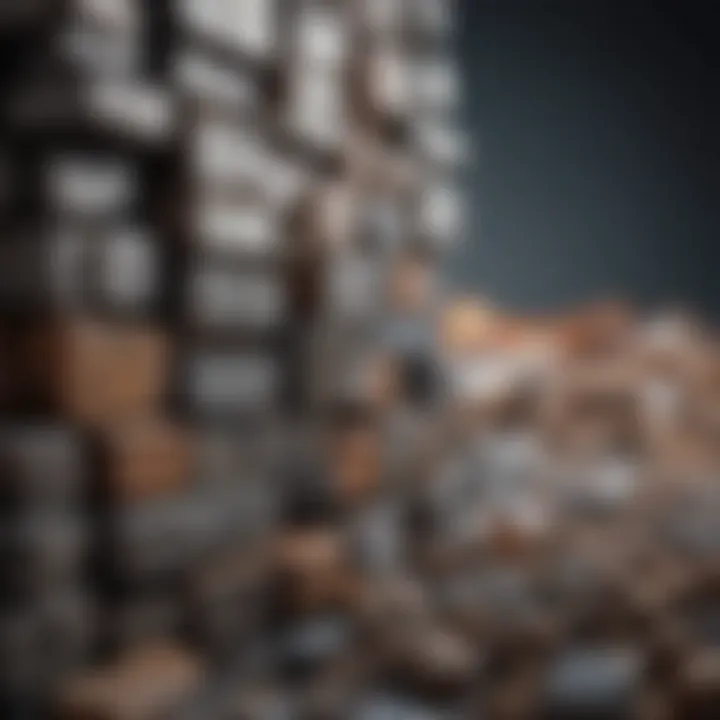
- Benefits of using quench towers in this context include:
- Mitigation of heat-related risks,
- Enhancing reaction kinetics,
- Improved separation processes by maintaining optimal temperatures.
For example, in the production of ammonia through the Haber process, the exothermic nature of the reaction necessitates efficient heat removal. A quench tower can effectively cool the product gas, allowing for optimal conditions for the subsequent recombination of reactants.
Power Generation
Quench towers also play a pivotal role in the energy sector, particularly in power generation plants. Here, they are primarily used to manage hot gases generated during combustion processes. By cooling these gases before they enter the turbine systems, quench towers help improve efficiency and extend the lifespan of equipment.
They are utilized in both traditional coal-fired power plants and modern combined-cycle systems.
- Applications in power generation include:
- Facilitating heat recovery,
- Complying with environmental regulations regarding emissions,
- Improving thermal efficiency through enhanced cooling methods.
In a combined-cycle plant, for instance, the integration of quench towers allows for capturing waste heat, which can then be redirected to generate additional electricity, thus maximizing resource utilization.
Metallurgical Applications
In metallurgy, quench towers are crucial during the cooling phase of metal processing. The need for precise thermal management is imperative to achieve desirable material properties, such as hardness and tensile strength. The rapid cooling provided by quenching can affect the microstructure of metals, ultimately influencing their mechanical properties.
- Key considerations when applying quench towers in metallurgical processes include:
- The selection of quenching media (water, oil, or air),
- Control of quench rates to minimize the risk of distortion or cracking.
When steel products undergo heat treatment, for instance, the quenching phase is essential to shape the final characteristics of the metal. Using a quench tower can enhance control over the cooling process, leading to improved performance of the final product in various applications such as automotive manufacturing and construction materials.
"Quench towers enable industries to fine-tune thermal processes, ensuring products meet rigorous standards and enhancing operational efficiency."
Overall, quench towers are indispensable across different sectors, and their application reinforces the need for effective thermal management solutions. Whether in chemical processing, power generation, or metallurgy, these systems epitomize the intersection of safety, efficiency, and innovation.
Efficiency Metrics of Quench Towers
Efficiency metrics of quench towers are essential in evaluating how effectively these systems perform in industrial settings. Understanding these metrics not only paves the way for optimized design and operation but also underscores the importance of quench towers in achieving overall thermal management and safety. Let's dive deeply into two crucial aspects: energy consumption analysis and performance indicators.
Energy Consumption Analysis
Analyzing energy consumption in quench towers is fundamental since the operational costs in industrial processes are often tied to the energy used during cooling. The correlation between energy efficiency and overall effectiveness is noteworthy. By minimizing energy usage, organizations can significantly reduce operational costs and enhance sustainability.
Several factors can affect energy consumption:
- Type of cooling medium: Water, air, or chemical solutions can have different thermal properties and varying impacts on energy requirements.
- System design: Counterflow systems generally outperform crossflow systems in terms of energy efficiency, particularly when dealing with large temperature differentials.
- Flow rates: Adjusting and optimizing flow rates to meet specific cooling demands can drastically change the overall energy consumed.
Efficient quench towers use modern technology to minimize waste of energy. Adaptive control systems can actively manage conditions within the tower, adjusting flow and cooling rates in real-time to keep energy use at a minimum. It pays off, as decreased energy consumption directly leads to cost savings, making it a winning formula for industries aiming to combine efficiency with sustainability.
Performance Indicators
Performance indicators serve as a critical benchmarking tool for understanding how well quench towers are functioning in practice. These indicators provide insights into the efficiency and reliability of cooling processes, guiding necessary adjustments.
Some key performance indicators to track include:
- Cooling capacity: The amount of heat removed from the process fluid, often measured in BTUs or kilowatts. This indicates whether the tower can meet its intended cooling requirements.
- Temperature differential: The difference in temperature between the inlet and outlet fluids; a larger differential generally suggests more effective cooling.
- Water usage efficiency: This metric assesses the volume of water consumed relative to the cooling achieved, essential in areas where water scarcity is a concern.
- Emissions metrics: It’s pertinent to evaluate emissions from cooling processes to ensure compliance with environmental regulations and promote corporate responsibility.
"The true measure of efficiency in a quench tower lies not only in its cooling effectiveness but also in its sustainability and economic viability."
In summary, by closely monitoring energy consumption and leveraging performance indicators, industries can fine-tune their quench tower systems. This holistic approach offers multifaceted benefits—not just for today but also sets the groundwork for future innovations in thermal management.
Challenges in Quench Tower Technology
The technological landscape of quench towers is a complex one, requiring keen attention to both design and operational challenges. The performance of these cooling systems is often hindered by several factors that can degrade efficiency and impact safety. Understanding these challenges is crucial, particularly for professionals engaged in chemical processing and related fields, as it enables them to devise strategies for optimization and mitigation.
Scaling and Fouling Issues
Scaling and fouling are persistent thorns in the side of many industrial processes, quench towers included. These phenomena occur when minerals and particulates in the water used for cooling settle on surfaces within the tower. When this happens, the heat transfer efficiency diminishes. For instance, in a counterflow design, scaled surfaces can significantly impede the heat exchange between the hot gases and the cooling liquid.
Additionally, fouling can lead to more than just poor heat transfer; it can also create hotspots that may cause localized degradation of materials, ultimately leading to equipment failure. Some of the common culprits responsible for fouling include biological growths, sediment, and inorganic deposits. A common saying in industry goes, "An ounce of prevention is worth a pound of cure," which holds true here. Regular maintenance, including cleaning and checking the composition of the water used, can aid significantly in mitigating these issues. Some companies also invest in monitoring systems to keep an eagle eye on scaling and take corrective measures proactively.
Environmental Considerations
Another layer of complexity arises from environmental considerations in quench tower technology. The role of quench towers in manufacturing is not just related to efficiency and cost; the environmental footprint of these systems can have far-reaching implications. For instance, the water used in cooling processes often faces regulatory scrutiny, especially when it’s discharged back into natural water sources. It’s vital for operators to understand local regulations regarding water discharge quality and treatment requirements to avoid penalties and contribute positively to environmental conservation.
Moreover, audit studies show that quench towers can also be significant contributors to thermal pollution. If the water returned to the ecosystem is heated excessively, it can disrupt local aquatic life. To mitigate such impacts, the industry is increasingly exploring options for heat recovery and sustainable practices—whether that’s incorporating advanced cooling technologies or utilizing closed-loop systems to recycle water. As the awareness of climate challenges grows, it becomes paramount for operators to implement eco-friendly practices. Ultimately, investing in sustainable alternatives can bolster a company's reputation and foster goodwill among communities.
"Shifting focus from merely functional to environmentally friendly systems can save industries from costly repercussions."
Addressing these challenges in quench tower technology can remarkably enhance operational efficiency, lower maintenance costs, and fulfill regulatory obligations. As research paves the way for innovations in cooling system design and operation, industries that neglect these aspects may find themselves at a competitive disadvantage.
Recent Innovations in Quench Towers
Quench towers undergo continual advancements, partly due to the increasing demand for efficiency and sustainability in industrial applications. The push for innovation stems from both environmental regulations and the need for improved thermal management systems. New technologies are being developed to enhance the performance and reliability of these structures, making them more adaptable to a variety of processes.
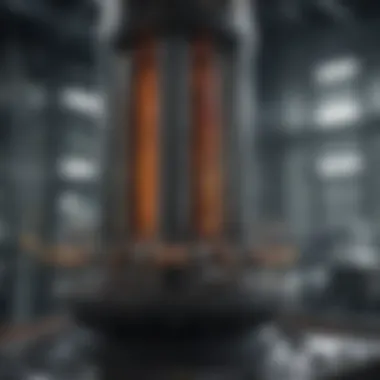
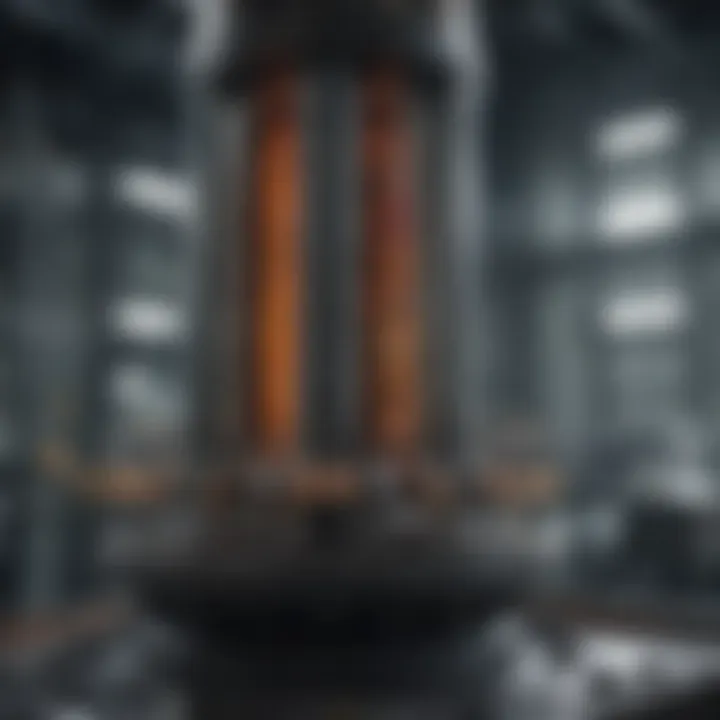
Adaptive Control Systems
Adaptive control systems represent a significant leap forward in the operation of quench towers. These systems allow for real-time monitoring and adjustment of operational parameters based on varying conditions. This means, for instance, that the temperature and flow rates can be fine-tuned on the fly, optimizing cooling performance without constant manual intervention.
Key benefits of implementing adaptive control systems include:
- Reduced Energy Consumption: By efficiently regulating cooling processes, energy waste is minimized.
- Enhanced Safety: Real-time monitoring helps in early detection of potential issues, allowing for timely interventions that can avert accidents.
- Improved Product Quality: Precise control of operational parameters leads to more consistent output, reducing variability in industrial products.
An example of this innovation can be seen in the recent deployment of a smart quench tower in a petrochemical plant. Through sensors and supporting algorithms, the system was able to adjust its performance according to real-time data, leading to a remarkable increase in cooling efficiency.
"Adaptive control not only improves efficiency but offers unprecedented flexibility."
Nanotechnology Applications
The integration of nanotechnology within quench tower design is another frontier that showcases the inventive spirit of the industry. Utilizing materials at the nanoscale can lead to significant enhancements in heat transfer and material strength.
The key approaches include:
- Nanofluids: By incorporating nanoparticles into the quenching fluid, thermal conductivity can be dramatically improved. This grants quicker and more effective heat dissipation.
- Coating Technologies: Nanocoatings can increase corrosion resistance and reduce fouling, extending the operational life of the towers and lowering maintenance costs.
- Smart Materials: Certain nanomaterials can adapt their properties in response to temperature changes, allowing quench towers to self-regulate under diverse conditions.
One notable instance of nanotechnology in action is the use of copper oxide nanoparticles in the cooling fluids of quench towers. Tests have shown a leap in thermal conductivity, translating to improved cooling capacity without needing additional energy input.
The investments in adaptive systems and nanotechnology not only pave the way for more resilient industrial processes but also contribute to a more sustainable future.
Case Studies of Quench Tower Implementation
The significance of case studies within the realm of quench towers cannot be overstated. These real-world examples serve as an invaluable resource, offering insights into practical applications and the nuances of operational challenges. By examining specific instances of quench tower implementations, professionals can glean lessons about efficiency, compatibility with varying industrial processes, and innovative solutions that have emerged in the field. Furthermore, case studies can inform stakeholders about the tangible benefits associated with effective quenching processes, ultimately encouraging further investment and research in thermal management technologies.
Success Stories
Across various industries, numerous success stories highlight the effective integration of quench towers into workflows, illustrating their transformative impact. One such case involves a chemical manufacturing facility that faced recurrent downtime due to overheating issues. The installation of a counterflow quench tower allowed the company to dramatically reduce temperature spikes during their production cycle. The integration not only stabilized the process but also led to a notable increase in output by around 20% within several months.
Another remarkable example can be found in the power generation sector. A coal-fired power plant implemented a state-of-the-art crossflow quench tower designed to handle extreme temperatures. This upgrade enabled the plant to not only meet environmental regulations more effectively but also enhance the overall efficiency of heat dissipation. The owners reported a significant decrease in emissions due to more thorough cooling, as well as an improvement in plant reliability, ultimately reflecting positively on their operational costs.
Lessons Learned
While success stories are uplifting, it's equally crucial to discuss the lessons learned from these implementations. For instance, in the case of a metallurgical facility that introduced a quench tower as part of their steel manufacturing process, initial assessments did not thoroughly consider the corrosive nature of the cooling agents. As a result, the quench tower experienced unexpected maintenance issues. This incident serves as a reminder that material selection and a deep understanding of the process are paramount when designing these systems.
Moreover, addressing operational considerations such as space availability and setup configurations can’t be overlooked. In another instance, a petrochemical plant installed a new quench system in an already congested facility. The space constraints led to difficulties in accessing the tower for maintenance.
Ultimately, these learnings emphasize the importance of a thorough preliminary analysis and multidimensional planning before quench tower installation. Collaborating with designers and engineers can streamline the integration and ensure that all variables are accounted for, thereby enhancing the effectiveness and longevity of the quench system.
Key Takeaway: Successful implementation of quench towers hinges on meticulous planning, awareness of specific process dynamics, and responsive adjustment mechanisms to adapt to changing conditions.
By reflecting on both the triumphs and the setbacks encountered in these case studies, professionals can craft a more informed approach to quenching processes that not only optimizes performance but also anticipates challenges that may arise.
Future Directions for Quench Tower Research
As industries advance and expand, the need for innovative solutions in thermal management grows. This section touches upon the future directions for quench tower research. Understanding these developments not only enhances operational efficiency but also boosts sustainability frameworks across various sectors. It's essential to grasp how these new paths in research can improve both safety and performance in quench tower applications.
Technological Advancements
Technological advancements offer remarkable promise for the evolution of quench towers. One such area is the integration of artificial intelligence (AI) and machine learning. By utilizing data analytics, operators can predict equipment behavior and optimize cooling processes more effectively. This leads to more precise control systems, reducing waste and enhancing energy efficiency.
Another area of advancement relates to the materials used in quench tower construction. Researchers are investigating advanced composites that possess better thermal performance, durability, and resistance to corrosive environments. For instance,
- Carbon fiber-reinforced polymers (CFRP) are lighter and stronger than traditional materials, which might reduce the structural load and cut installation costs.
- High-temperature alloys offer enhanced performance, allowing quench towers to operate at higher temperatures without failure.
These innovations help ensure that quench towers can cope with the increasing demands of modern manufacturing processes.
Research Gaps and Opportunities
While advancements are clear, there remain significant gaps in current research. Many existing studies do not comprehensively address the environmental impacts associated with quench tower operations. There is an urgent need for more innovative designs that focus on minimizing resource consumption and promoting sustainable practices. The integration of renewable energy sources, such as solar or wind, in powering these cooling systems is yet to be fully explored.
Additionally, the lack of standardized testing protocols for different types of quench towers means that comparative evaluations are often flawed. Establishing such standards can provide an excellent opportunity for academia and industry to collaborate; this can lead to improved designs that enhance both safety and efficiency.
Another avenue worth exploring is the effect of climate change on cooling requirements. With changing weather patterns, thermal management systems may need recalibrating to ensure they remain effective. Understanding how quench towers respond to more extreme temperatures and variations in humidity is crucial for future resilience.
"Research should not only focus on what is currently feasible but must also embrace what could be possible."
Closure and Summary
In wrapping up our exploration of quench towers, it becomes abundantly clear that these structures are not just metal and pipes; they are pivotal elements in the intricate workings of industrial processes. Quench towers serve a fundamental role in thermal management, regulating temperatures that can spell the difference between success and disaster in chemical engineering. They stand at the intersection of efficiency, safety, and innovation, making their analysis not only relevant but crucial in various sectors.
The importance of understanding quench towers lies in recognizing their impact on process optimization and environmental sustainability. As industries increasingly face scrutiny on their energy consumption and emissions, effective cooling strategies provided by quench towers can lead to significant advancements. This knowledge matters, bridging the gap between theory and application, allowing professionals to devise solutions that are not only economical but also ecologically responsible.
Key Takeaways
- Role in Cooling Processes: Quench towers are essential in cooling down heated fluids quickly, ensuring stability in chemical reactions. Their design and operation significantly influence overall system efficiency.
- Diverse Applications: These towers are versatile, finding use in fields ranging from chemical processing to power generation, demonstrating their critical role across various industries.
- Technological Evolution: Innovations such as adaptive control systems and the integration of nanotechnology are shaping the future of quench tower deployment, paving the way for improved performance and efficiency.
- Challenges Ahead: Despite their importance, issues like scaling and environmental impacts remain persistent challenges, necessitating ongoing research and development in quench tower technology to address these hurdles.
Implications for the Industry
The implications of quench towers extend well beyond mere functionality. For industries, they represent a key strategy for achieving regulatory compliance regarding emissions and waste management. As environmental laws tighten, the efficiency of cooling systems can directly correlate with a company’s ability to operate within these frameworks.
Furthermore, quench towers can lead to reduced operational costs. By improving energy consumption and recovery, industries can save significantly over time while also enhancing the sustainability of their processes.
Ultimately, understanding the dynamics of quench towers equips professionals with the tools needed to optimize their operations. As these technologies advance, they will likely become even more integral to the future of industrial processes, where efficiency and sustainability are not just goals but necessities.
"In an age where every resource counts, mastering cooling processes with quench towers could very well be the differentiator for survival in competitive markets." Besides, investing in research and technology can pave the way for groundbreaking advancements that elevate industry standards.