In-Depth Analysis of Radiographic Weld Testing Techniques

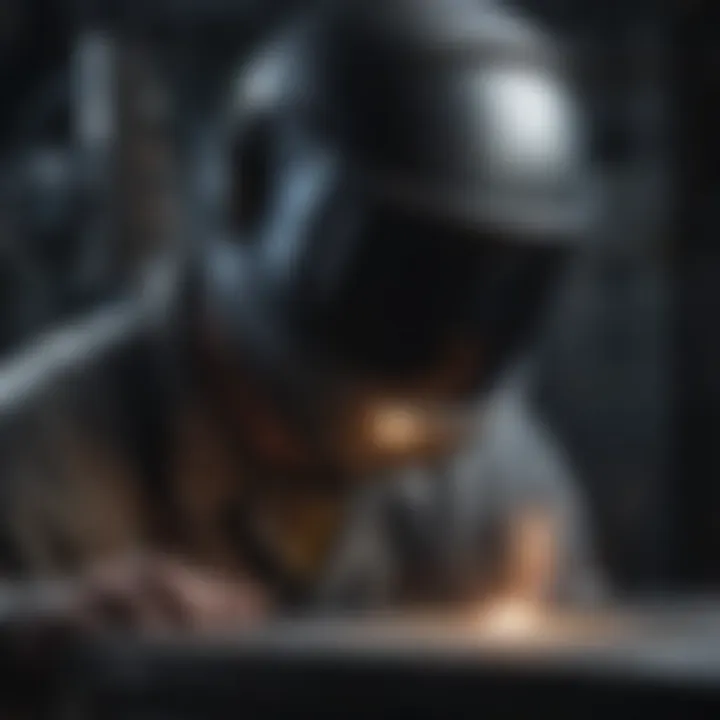
Intro
Radiographic weld testing stands out as a cornerstone in non-destructive evaluation (NDE) methods. This technique provides critical insights into the integrity and quality of welded joints without compromising their structure. Such assessments are vital in sectors like construction, manufacturing, and energy, where the slightest flaw can lead to catastrophic failures. The growing importance of safety and compliance within these industries necessitates reliable techniques for evaluating welds. Thus, understanding the fundamentals of radiographic weld testing becomes essential for professionals navigating this intricate field.
In this article, we'll unpack key concepts, methodological nuances, and explore how radiographic weld testing aids in enhancing overall weld integrity. Not only will we delve into its operational principles, but we will also touch upon its advantages, challenges, and the pertinent regulatory standards that govern its application. Prepare to embark on a journey through the technical depths of this indispensable practice.
Key Concepts and Terminology
Definition of Key Terms
- Radiographic Testing (RT): This is an inspection method that uses X-rays or gamma rays to view the internal structure of a weld joint. The resulting images help identify imperfections such as cracks, voids, and porosities in the weld cross-section.
- Weld Integrity: Refers to the ability of a welded joint to perform its intended function without experiencing failure under service conditions. It encompasses both physical and chemical properties.
- Non-Destructive Testing (NDT): A suite of evaluation techniques employed to assess material properties without causing damage. It includes methods like ultrasonics, dye penetrant testing, and radiographic testing.
Concepts Explored in the Article
The conversation around radiographic weld testing weaves through various aspects:
- Implementation of RT: We examine how radiographic testing is executed, including equipment necessary and procedural steps.
- Benefits of Using RT: Highlighting the advantages of RT can reveal why it is preferred in many scenarios, such as its ability to pin point flaws.
- Challenges faced in RT: No technique is without its complications. We'll explore obstacles surrounding interpretation and limitations of equipment.
- Regulatory Compliance: Understanding the standards that govern radiographic weld testing is crucial for ensuring quality and safety.
Findings and Discussion
Main Findings
Radiographic weld testing has multiple strengths, such as:
- Precision: It offers unmatched clarity in identifying internal flaws that other methods may overlook.
- Documentation: The capability to maintain a visual record of weld quality for audits enhances accountability.
- Adaptability: Suitable for various materials and complex geometries, RT can be effectively utilized across industries.
However, along with these upsides come certain challenges:
- Interpretation complexities: Reading radiographs requires skilled professionals, and misinterpretation can result in costly errors.
- Exposure risks: Handling radiation poses safety risks for technicians and necessitates stringent safety protocols.
Potential Areas for Future Research
Innovative advancements in technology often shift landscape within industries. Here are some potential avenues that may warrant further exploration:
- Automation in RT: With the rise of artificial intelligence, automated systems for interpreting weld images could enhance speed and accuracy.
- Material-Specific Techniques: Developing methods tailored to new materials that are common in modern applications can increase the effectiveness of RT.
- Integration with Other NDT Methods: Studying how RT can complement other non-destructive techniques to provide a more holistic view of weld integrity.
"In the field of industrial assessment, precision and safety are paramount. Radiographic testing stands as a pillar of such evaluations, providing insights that ensure structural stability and compliance with industry standards."
Understanding radiographic weld testing equips professionals with critical insights necessary for maintaining quality in industrial applications. As the industry evolves, so too must the methods we utilize in pursuing exceptional weld integrity.
Foreword to Radiographic Weld Testing
In the realm of industrial quality assurance, the significance of radiographic weld testing cannot be overstated. This method plays a pivotal role in the assessment of weld integrity, helping to ensure that structures and components meet stringent safety and performance standards. As industries continue to evolve, the demand for reliable testing methods, like radiographic testing, has surged, making it indispensable across various sectors including construction, aerospace, and manufacturing.
Definition and Purpose
Radiographic weld testing refers to the process of using x-rays or gamma rays to inspect the internal quality of welds in metallic components. The principal aim is to detect any flaws such as cracks, porosity, or incomplete fusion that can compromise the strength and safety of a welded joint. By providing a comprehensive internal view, this technique allows professionals to make informed decisions regarding the integrity of the weld without causing any damage to the component itself.
- Key definitions include:
- Radiography: A technique that utilizes radiation to create images of the interior structure of an object.
- Weld Testing: The evaluation of welds for defects and overall quality.
This non-destructive evaluation (NDE) method is crucial in enhancing the durability of welds and ultimately supporting the safety of the structures they form part of.
Historical Development
The roots of radiographic testing can be traced back to the early 20th century. The advent of x-ray technology revolutionized many fields, including medicine and industrial testing. Initially used for medical diagnostics, the application of x-rays for weld inspection began shortly thereafter, as engineers recognized the potential of this powerful tool to visualize internal weld structures.
As industries expanded, so did the complexities of welding techniques and materials, necessitating the development of more sophisticated radiographic methods. The introduction of digital radiography in the 21st century marked another significant leap forward. This technology not only improved the quality and speed of imaging but also reduced the exposure to harmful radiation.
Today, radiographic weld testing stands as a testament to the commitment to quality and safety in engineering practices, driven by the very foundations laid down over a century ago. As we delve deeper into the fundamental principles and applications of this important technique, it becomes clear that its evolution continues to shape the industry positively.
Fundamental Principles of Radiographic Testing
Understanding the fundamental principles of radiographic testing is essential for evaluating weld integrity effectively. This section dives into the physics behind radiation, imaging techniques used, and how these principles support reliable testing in the field.
Basic Physics of Radiation
Radiographic testing hinges on the basic physics of radiation. To grasp its significance, one must first explore the types of radiation involved and how they interact with matter.
Types of Radiation
In radiographic applications, the principal types of radiation are X-rays and gamma rays. X-rays are generated from high-energy electrons in X-ray tubes, while gamma rays emanate from radioactive materials. The key characteristic of X-rays is their ability to penetrate various materials, which makes them particularly useful in inspecting welds and detecting internal flaws.
One unique feature of X-ray radiation is its remarkable precision. When directed at a weld, the penetrative capacity offers insight not visible to the naked eye. This quality not only enhances the reliability of the results but also facilitates a safer inspection regimen. However, the production of X-rays often demands additional safety measures due the high energy involved, which is a consideration for professionals in the field.
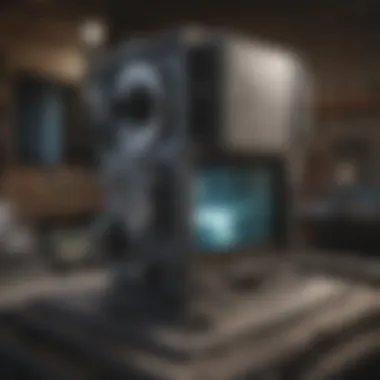
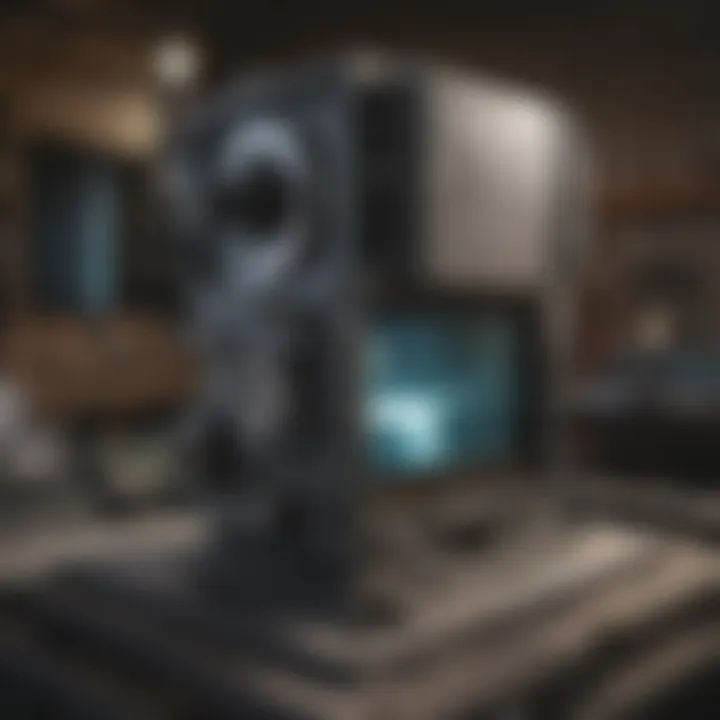
Interaction of Radiation with Matter
The interaction of radiation with matter is crucial in determining the quality of the results in radiographic testing. As radiation passes through materials, it is absorbed, scattered, or transmitted depending on the density and composition of the material. Understanding how radiation interacts with different materials allows for more accurate interpretations of the images produced.
A pivotal aspect of this interaction is the photoelectric effect, which occurs when X-ray photons collide with atoms in the weld and transfer their energy, leading to electron emissions. This interaction can significantly impact how defects are identified in welds, prompting the necessity for skilled interpretive analysis to assess the results accurately. The unique interplay of radiation and material ultimately enables professionals to ascertain the integrity and safety of welds.
Radiographic Imaging Techniques
Effective weld evaluation wouldn't be feasible without suitable imaging techniques. Radiographic imaging methods are primarily classified into Film Radiography and Digital Radiography.
Film Radiography
Film radiography has been a mainstay in the industry for decades. The technique employs film that is sensitive to radiation. When exposed to X-rays, the film captures the patterns of exposure, developing the likeness of the weld in question.
A notable characteristic of film radiography is its ability to create permanent records of weld integrity. The physical film serves as a historical archive, important for quality assurance in various domains. However, one must acknowledge the somewhat lengthy turnaround time needed for film development, which can hinder immediate analysis.
Digital Radiography
In contrast to its film counterpart, digital radiography employs sensors to convert X-ray input into digital data. This method significantly enhances workflow by allowing immediate image retrieval and analysis. A key advantage is the increased sensitivity and flexibility in image processing.
The unique feature of digital radiography lies in its adaptability—it permits dynamic manipulation of images to highlight potential defects, which makes interpretations more straightforward and precise. Nonetheless, this approach generally requires an investment in technology and training, which can deter some organizations from its adoption.
The choice between film and digital methods often boils down to specific project requirements, operational capacity, and budget considerations.
Equipment Utilized in Radiographic Weld Testing
In radiographic weld testing, the equipment used plays a pivotal role in ensuring the quality and accuracy of weld integrity assessments. A well-functioning system is essential for producing reliable images that can reveal imperfections, thereby safeguarding the structural integrity of components across various industries. Each piece of equipment, from radiation sources to detection devices, contributes to the overall efficacy of radiographic testing, making understanding these components crucial for any industry professional.
Radiation Sources
Radiation sources are the heart of radiographic testing, as they produce the exposure needed to penetrate materials and create images of hidden flaws.
X-ray Tubes
X-ray tubes dominate the landscape of weld testing, serving as a primary source of radiation. The key characteristic of X-ray tubes is their ability to generate high-energy radiation through the acceleration of electrons towards a target. One significant aspect of X-ray tubes is their versatility; they can be easily adjusted to accommodate different material thicknesses and densities, thus providing flexibility in various applications.
Their ability to produce high-resolution images makes them a popular choice. However, it’s worth acknowledging that X-ray tubes require careful handling and maintenance, as the equipment can be sensitive to wear and tear. Moreover, the initial setup and calibration may take time, which can be seen as a downside in fast-paced environments.
Gamma Ray Sources
On the other hand, gamma ray sources offer another viable radiation option. These sources emit gamma rays spontaneously, providing a continuous stream of radiation. A notable characteristic of gamma ray sources is their high penetrating power, which allows them to inspect denser materials with ease.
This feature is particularly advantageous in industries where thick welds are common, such as construction and large-scale manufacturing. However, the disadvantage lies in their need for strict regulatory compliance and careful handling due to the radioactive nature of the source. The cost of licensing and safety measures can be a barrier for some organizations looking to adopt gamma ray technologies.
Detection Devices
After generating radiation images, the next step is utilizing detection devices to capture and analyze these images effectively.
Film and Screens
Film and screens have long been the staple in radiographic imaging, known for their simplicity and effectiveness. The traditional process involves exposing the film to radiation, which then creates a latent image that can be developed into a visible form. A key characteristic of film and screens is their capacity to provide detailed contrasts among different materials, making it easier to identify flaws.
Despite their capabilities, reliance on film entails some challenges. Developers must be proficient in time-sensitive processes to ensure image quality, and the need for darkroom facilities can make them less convenient in modern testing environments. Also, film can become cumbersome for large-scale projects due to physical storage needs.
Digital Detectors
Digital detectors represent the modern advancement in radiographic testing. By converting radiation into digital signals, they offer faster processing and immediate image review. The distinct feature of digital detectors is their ability to apply advanced image processing techniques to enhance the visibility of potential flaws in the welds.
This quick turnaround can lead to significant time savings in inspection processes. Nevertheless, digital detectors can be more expensive initially and may require training for personnel to navigate effectively. Balancing these costs against the benefits requires careful considerations by organizations.
Support Equipment
Support equipment enhances the utility of the primary testing tools, furthering the effectiveness of radiographic weld testing.
Film Viewing Equipment
Film viewing equipment plays a crucial role in the analysis of traditional film-based radiography. A primary feature of this equipment is its capacity to magnify images, allowing inspectors to detect slight imperfections that could be missed by the naked eye. This ability is particularly important when evaluating critical welds where minor flaws can lead to catastrophic failures.
However, the need for a controlled lighting environment can limit the practicality of this equipment in some settings.
Processing Facilities
Processing facilities are essential for developing images from film and screens. The characteristic of these facilities is their ability to ensure consistent results through controlled development times and temperatures. They offer a systematic approach to image processing, eliminating uncertainties associated with manual development.
Despite their contributions, setting up such facilities can be costly, and they demand regular maintenance to keep operational throughout testing rountines. Moreover, the time taken for processing can lead to delays in project timelines, which is a consideration for fast-paced industries.
In summary, the equipment utilized in radiographic weld testing spans a range of devices, from radiation sources to detection and support equipment. Each plays an integral part in shaping the efficiency and accuracy of weld testing. A thorough understanding of these components is vital for ensuring the quality and safety of the inspections performed.
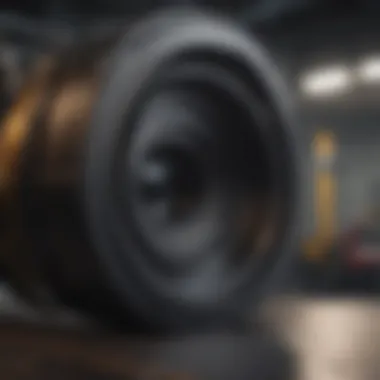
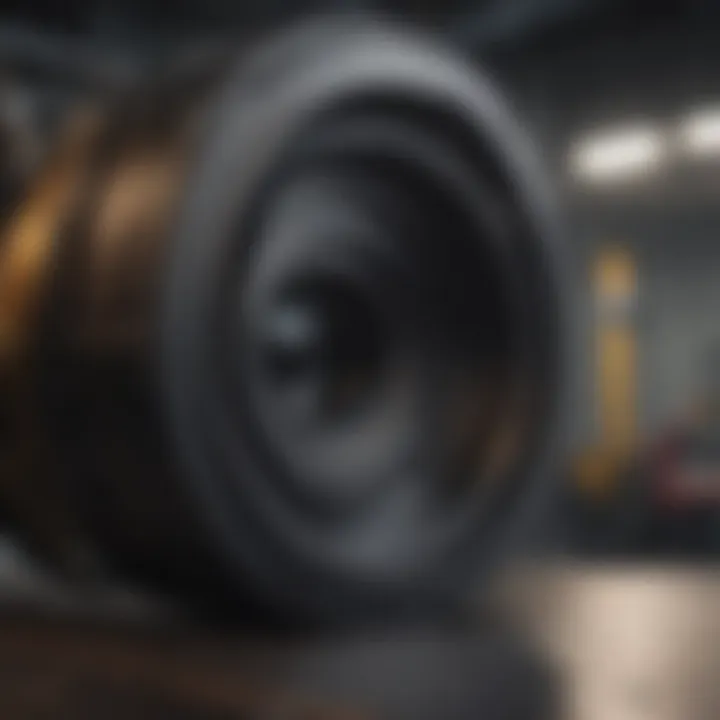
Application Domains of Radiographic Testing
The application domains of radiographic testing play a pivotal role in ensuring the safety and integrity of welds across various industries. In essence, these domains encompass the specific environments where radiographic techniques are essential for evaluating weld quality. By leveraging the strengths of this evaluation method, industries can identify faults, mitigate risks, and maintain high standards of safety and performance in their operations.
Industrial Applications
Weld Inspection in Construction
Weld inspection in construction stands out as a cornerstone of radiographic testing. This aspect involves utilizing radiographic methods to check the quality of welds that are integral to structural safety, particularly in buildings, bridges, and other infrastructure. The major characteristic of this application is its ability to pinpoint internal defects such as cracks, porosity, or incomplete fusion which may not be visible externally.
The significance of weld inspection lies in its contribution to structural integrity, as it helps in preventing catastrophic failures that could arise from compromised welds. Radiographic methods are a popular choice here due to their non-destructive nature, allowing for comprehensive analysis without damaging the structure itself. This is particularly beneficial in construction, where the elimination of downtime is crucial.
One unique feature of this method is its capacity to provide permanent visual records, which can be invaluable for future inspections or assessments. However, there are downsides to consider, such as the potential exposure to radiation, which necessitates stringent safety protocols. Thus, while beneficial, ensuring proper regulatory compliance and the safety of workers is of utmost importance.
Aerospace Industry Standards
In the aerospace sector, stringent standards govern the inspection processes for materials and welds. The application of radiographic testing within this domain is characterized by its critical role in ensuring aircraft safety and performance. It allows for the detection of even the minutest flaws, which can be detrimental in aviation contexts.
The aerospace industry's reliance on radiographic methods underscores the importance of high-quality welds, as any compromise can lead to severe safety implications. Here, radiographic testing is favored due to its exceptional precision and reliability in revealing hidden defects, making it essential in components where structural failure is not an option.
A unique feature of this application is the requirement for compliance with international safety standards such as AS9100. This sets a high bar for inspections but also means that organizations must invest considerably in training and compliance processes. The challenges lie in balancing those rigorous standards while also managing costs and timeframe considerations.
Research and Development
Material Science Advancements
Material science has seen enormous growth thanks to advancements in radiographic testing. This aspect focuses on the role of radiography in understanding the properties and behaviors of various materials under different conditions. The key characteristic of this intersection is the in-depth information radiographic imaging can provide about material integrity, thus advancing research capabilities significantly.
This approach is particularly beneficial as it opens avenues for exploring new materials that might be stronger or lighter, pushing the boundaries of what's achievable in engineering. Radiographic testing facilitates the ongoing development and fine-tuning of materials by revealing how they respond to various stressors and environmental conditions. However, one downside is the necessity for highly specialized knowledge to interpret results accurately, often requiring inter-disciplinary collaboration.
Innovative Testing Techniques
Innovative testing techniques represent the forefront of radiographic weld testing. This aspect involves utilizing cutting-edge technology and methods to enhance the reliability and efficiency of inspections. The defining feature of these techniques is how they incorporate automation and digital advancements, making tests faster and more accurate.
The benefits of integrating innovative techniques into radiographic testing are numerous. For one, they can lead to significant reductions in human error, thus increasing the reliability of inspections while expediting results. Additionally, the real-time data analysis capabilities that come with these methods strengthen the overall insights gained from testing. On the flip side, the initial investment in new technologies and necessary training can pose challenges for adoption.
Overall, the application domains of radiographic testing illustrate its vital role across industries ranging from construction to aerospace, and in research and development initiatives. Each domain not only underscores the necessity of radiographic methods but also highlights the importance of continuous evolution to meet industry standards and safety demands.
Advantages of Radiographic Weld Testing
Radiographic weld testing presents a multitude of benefits, making it an essential tool within various industries. The significance of this testing method isn't just a matter of convenience; it encompasses reliability, accuracy, and adaptability, catering to diverse requirements across different sectors. As we dive into the specifics, the advantages can be classified into three main categories, particularly emphasizing the non-destructive nature, comprehensive visualization, and versatility across materials.
Non-Destructive Nature
One of the standout features of radiographic weld testing is its non-destructive approach. Unlike destructive testing methods that may compromise the integrity of the welded component, radiographic testing allows for thorough assessments without causing any damage. This is crucial in fields where the functionality of a component is paramount. In a nuclear power plant, for example, a weld must maintain its structural integrity throughout its operational life. With radiographic testing, inspectors can check for internal flaws without needing to dismantle assemblies or disrupt operations.
The implications are significant:
- Safety: Non-destructive testing enhances safety for both operators and equipment, as flaws can be identified and rectified before they result in failures.
- Cost Efficiency: By preventing potential failures through early detection, organizations can save substantial costs tied to repairs or, worse, catastrophic accidents.
- Regulatory Compliance: Many industries are under strict regulatory oversight. Using non-destructive methods helps companies adhere to safety standards without hindering operational flow.
Comprehensive Visualization
Radiographic welding testing provides comprehensive visualization of internal weld quality. By capturing an x-ray or gamma-ray image, technicians can observe structural anomalies that aren’t visible from the exterior. This clarity sets this method apart, revealing issues such as porosity, cracks, or inclusions that could lead to significant failures later on.
There's a clear distinction here:
- Detailed Inspection: Film or digital radiography generates sharp images that depict the intricate nuances of the weld structure, allowing for detailed inspection.
- Data Permanence: Radiographic records are permanent and can be archived for future reference, making it easy to track changes over time or verify compliance with testing standards.
- Improved Decision Making: With an enhanced understanding of weld integrity, decision-makers can proactively manage maintenance schedules and resource allocation more effectively.
"The clarity and permanence of radiographic images transform not just inspections but also decision-making processes in welded constructions."
Versatility Across Materials
Lastly, radiographic weld testing boasts versatility across various materials. This capability proves essential across a broad spectrum of sectors, including manufacturing, aerospace, automotive, and construction. The techniques used can be applied to a myriad of materials such as steel, aluminum, titanium, and even plastic composites.
- Material Adaptability: Whether inspecting a weld in a complex aircraft structure or evaluating construction beams, the methodology remains effective across materials.
- Global Applications: In power plants, pipelines, bridges, and more, radiographic testing continuously finds its place, ensuring that infrastructure meets the stringent standards expected.
- Customizable Techniques: Different materials may necessitate specialized approaches within radiographic testing, be it through the type of radiation used or detection methods employed, allowing inspectors to tailor their methods based on specific project demands.
In summary, the advantages of radiographic weld testing extend far beyond the promise of integrity. They encompass operational efficiency, enhanced safety, and adaptability in an ever-evolving industrial landscape. As industries aim for greater reliability and safety, these benefits mark radiographic testing as a crucial part of quality assurance in welding.
Challenges Encountered in Radiographic Testing
Radiographic weld testing, while a powerful tool for ensuring weld integrity, is not without its challenges. It's important to recognize these hurdles to adequately prepare for and address them. This section delves into two key areas of concern: radiation safety and the complexities of interpreting test results. Each poses unique challenges, but they also highlight the necessity for rigorous standards and skilled professionals in the field.
Radiation Safety Concerns
Ensuring safety in radiographic testing is paramount. Given the nature of the techniques used, understanding the associated risks is critical for workers and the surrounding environment. Radiation safety concerns can be divided into two critical components: regulatory compliance and personal protective equipment.
Regulatory Compliance
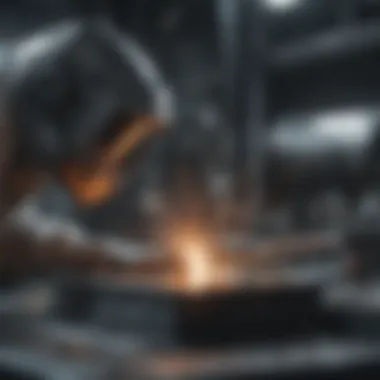
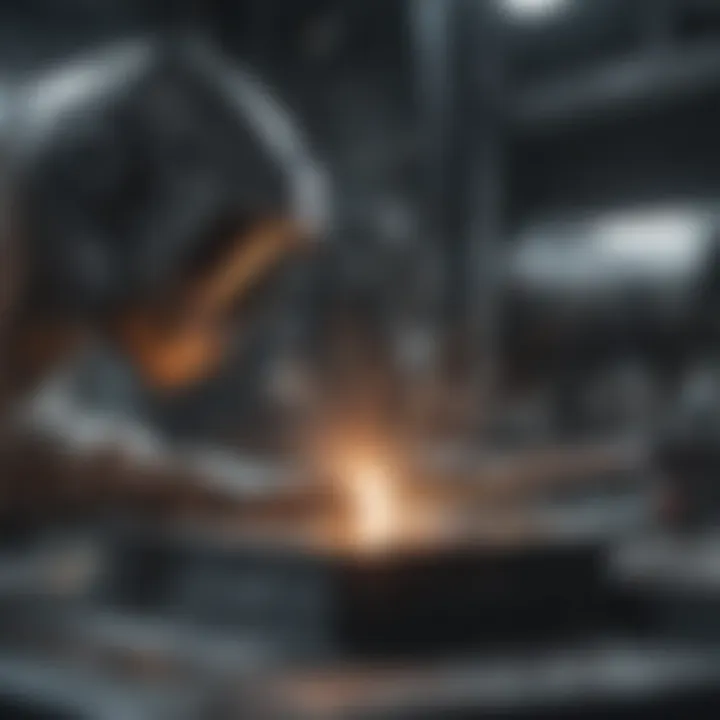
Regulatory compliance in radiographic testing refers to adhering to local and international regulations governing the use of radiation. These rules are designed to protect both personnel and the general public from harmful exposure. Compliance is not merely a checkbox; it's a significant contributor to safety practices in the industry. The key characteristic of regulatory compliance is its focus on standardization. It ensures that all professionals follow the same safety protocols, making it a dependable choice to safeguard health.
The unique feature of these regulations often lies in their adaptation to technological advancements. As new equipment and methods emerge, regulations evolve as well. This adaptability is beneficial because it helps to keep pace with the changes within the industry. Nonetheless, navigating these regulations can be a challenge for some, especially smaller firms that may lack expertise in compliance.
Personal Protective Equipment
Personal Protective Equipment, or PPE, is another vital aspect of radiation safety in radiographic testing. This equipment serves as a first line of defense against exposure. The essential characteristic of PPE is its ability to mitigate direct exposure to radiation, which makes it an indispensable choice in this field. Common items include lead aprons, safety glasses, and radiation dosimeters.
One unique advantage of PPE is its relatively straightforward implementation; it can be quickly adopted into daily operations and adjusted as needed. However, a notable downside is that while PPE can reduce risk, it cannot eliminate it entirely. Training workers to effectively use and monitor their PPE is crucial to enhancing safety measures.
Interpretation of Results
The interpretation of radiographic test results presents its own set of challenges. While advanced imaging techniques can yield clear images, understanding what they reveal requires specialized skills and experience. Two critical factors influencing interpretation are skill requirements and the inherent subjectivity involved in analysis.
Skill Requirements
The skill requirements for interpreting radiographic results are non-negotiable. Professionals need extensive education and experience to analyze these images correctly. The key characteristic of this requirement lies in the necessity for both theoretical knowledge and practical ability. This multifaceted skill set makes proper training an advantageous choice for organizations, as it ensures high-quality analysis.
A unique feature of skill requirements is the ongoing need for professional development. As technology evolves, so too must the capabilities of those working in the field. While this continuous learning benefits the industry by keeping professionals up-to-date on the latest methods, it also poses challenges for companies needing to allocate resources for staff training and education.
Subjectivity in Analysis
Subjectivity in analysis is an undeniable aspect of interpreting results. Different professionals might arrive at varied conclusions from the same radiograph. This characteristic of subjectivity can become a double-edged sword. On one side, it allows for multiple perspectives that can uncover insights missed by others. On the flip side, it risks inconsistency in evaluations, potentially leading to errors in judgment regarding weld integrity.
The unique feature of this subjectivity lies in the experience of the analyst. A seasoned expert may notice nuances that a less experienced technician might overlook. While experience is invaluable, the reliance on personal interpretation can complicate standardization efforts in the industry. Organizations often find it beneficial to implement checks and balances, such as peer reviews, to mitigate this risk.
Regulatory Standards and Quality Control
In the realm of radiographic weld testing, the establishment of regulatory standards and stringent quality control measures holds monumental importance. These elements not only ensure that testing meets industry benchmarks but also provide a framework that enhances the integrity and reliability of weld assessments. With a foundation based on robust standards, stakeholders can feel assured that safety, quality, and adherence to protocols govern the evaluation processes.
The integration of regulatory standards is crucial since it directly influences operational efficacy and legal compliance. Industries leveraging radiographic weld testing—in sectors such as construction and aerospace—depend on consistent quality assurance. It plays a vital role in obtaining certifications and maintaining operational legitimacy as well as preventing potential failures that can stem from subpar welds. By adhering to established guidelines, professionals mitigate risks and enhance the overall quality of their output.
International Standards
ISO Standards
ISO Standards are perhaps the cornerstone of quality assurance in radiographic weld testing. These internationally recognized norms dictate the methodologies and practices to be followed, ensuring that a universal level of quality is upheld. The key characteristic of ISO Standards is their comprehensive nature; they cover a wide range of criteria, from testing procedures to documentation requirements and equipment calibration.
One significant aspect of ISO Standards is their adaptability across various industries, which fosters a level of consistency that users appreciate. They are widely recognized and respected, making them a popular choice for entities looking to elevate their operational standards. The unique feature of these standards is their ability to accommodate new technologies, thus making them applicable even in the evolving landscape of weld testing.
However, there are disadvantages to consider as well. For instance, the rigorous compliance paperwork can be daunting, especially for smaller companies. Nevertheless, the advantages of quality assurance and international recognition generally outweigh these challenges.
ASNT Qualification
The ASNT Qualification represents another vital component in the framework of radiographic weld testing. The American Society for Nondestructive Testing (ASNT) outlines a series of qualifications which are paramount for personnel conducting these inspections. A noteworthy characteristic of ASNT Qualification is its focus on ensuring that individuals possess the required skills to interpret radiographic images accurately.
This qualification has become a benchmark for professionals seeking credibility in the field. It is a beneficial option because it builds trust among employers and clients, showcasing a commitment to maintaining high technical standards. The unique aspect of ASNT Qualification lies in its structured training programs, which prepare individuals for the complexities associated with radiographic testing.
The downside, however, can be the associated costs and time commitment required to complete these training programs, which may deter potential candidates. Ultimately, the advantages of sky-high skill levels and professional recognition significantly bolster the overall credibility of those in the field.
Quality Assurance Protocols
Quality assurance protocols are fundamental in ensuring that every step of the radiographic weld testing process adheres to established standards. These protocols incorporate a mix of systematic checks and validations throughout the testing phases. From selecting appropriate materials and equipment to documenting results methodically, the defined protocols guide practitioners to maintain high quality.
Effective quality assurance also encourages continuous improvement and learning, which are vital to adapting to industry shifts and enhancing testing accuracy. This structured approach transforms each testing endeavor into a learning opportunity, thus fostering a culture of excellence within organizations. Furthermore, by documenting every procedure, organizations not only streamline their workflows but also create a repository of knowledge that can be leveraged for future projects.
Future Trends in Radiographic Weld Testing
As technology advances rapidly, the landscape of radiographic weld testing is also undergoing significant transformations. This section delves into future trends poised to influence this pivotal evaluative process. Understanding these trends is crucial for professionals who wish to stay ahead in the field and adapt to necessitating changes in techniques and regulations. It encompasses not only emerging technologies but also evolving industry standards that dictate how testing is to be performed, ensuring compliance, safety, and efficiency in various applications.
Emerging Technologies
Automation in Testing
Automation in testing signifies a shift towards increasing efficiency and accuracy in radiographic weld testing. In this context, automated systems can conduct tests with minimal human intervention, thereby reducing the potential for errors caused by manual oversight. The main characteristic of automation is its ability to perform repetitive tasks consistently and reliably. This makes it a favorite among industries where time is money and precision is paramount.
One standout feature of automation in radiographic weld testing is, notably, speed. Tasks that previously required considerable time can now be completed much faster without sacrificing the quality of results. However, it's important to recognize that while automation enhances efficiency, it also demands a high level of initial setup and maintenance to ensure systems function properly. Ultimately, the discussion regarding automation continues—balancing the desire for faster results with the importance of training personnel to oversee these systems remains a pivotal consideration.
AI Integration
Artificial intelligence integration is another game-changer in the radiographic weld testing arena. By employing sophisticated algorithms, AI can assist in identifying potential flaws more effectively than traditional methods. The defining aspect of AI is its capability to learn from vast data sets, which leads to increased accuracy in readings and interpretations.
One unique attribute of AI is the capacity for predictive analysis. Instead of merely identifying existing weaknesses within welds, AI can foresee potential areas of concern through pattern recognition in data. This predictive capability not only enhances the proactive approach of maintenance schedules within industries but can potentially save costs associated with repairs and downtime. Although challenges, such as the need for significant data training and the potential for over-reliance on technology, exist, the benefits suggest AI's role will be paramount moving forward.
Evolving Industry Standards
As radiographic testing integrates new technological innovations, industry standards must evolve correspondingly. Regulatory bodies will need to adapt guidelines to encompass new methods and technologies, ensuring that quality and safety measures keep pace with advancements. For instance, organizations might find themselves developing new criteria to assess the performance of automated systems and AI-driven analysis.
It's also worth noting that as these standards shift, there may be additional training requirements for professionals in the field. Adapting to new technologies means updating skill sets continually. Hence, the ongoing evolution of industry standards not only assures compliance with safety regulations but also promotes continuous professional development.
Aligning technological advances with industry standards is vital. Staying informed on these trends is not merely an option; it becomes an imperative for success in Weld Testing.
In summary, the future trends in radiographic weld testing revolve around the critical themes of automation and AI integration, along with adaptive industry standards. Each of these elements promises to redefine how weld integrity is assessed, ultimately leading to improvements in safety, efficiency, and reliability across various sectors.