Rubber Adhesives: Properties, Applications & Trends
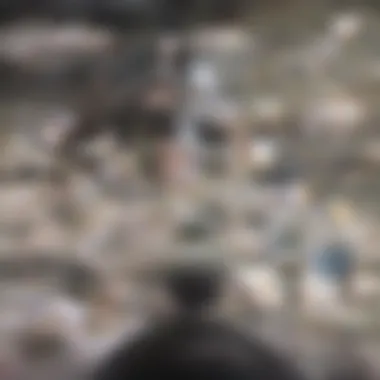
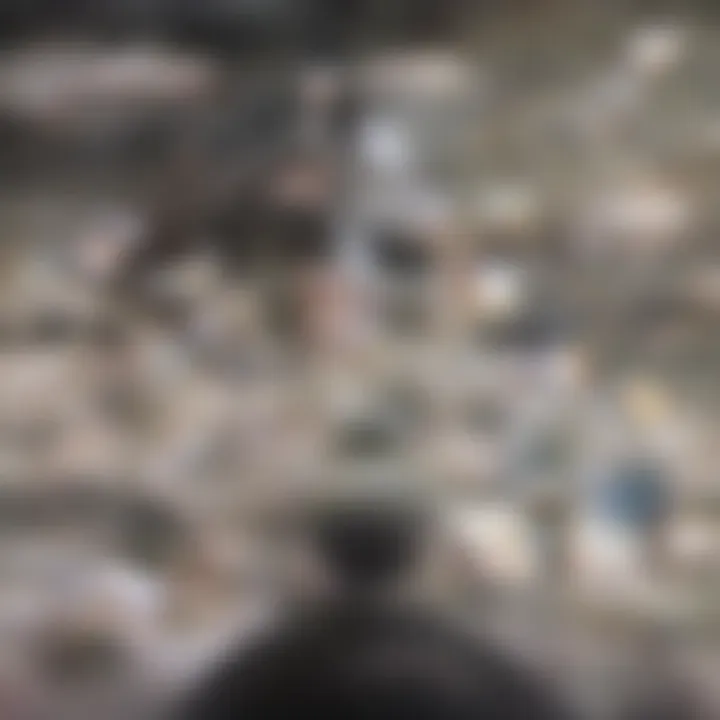
Intro
Rubber adhesives are widely used in various industries due to their unique properties. They possess excellent adhesion characteristics, flexibility, and resistance to weather and aging. Understanding their composition and functionalities is essential for students, researchers, and professionals engaged in fields such as engineering, design, and chemistry. This article aims to provide an in-depth overview of rubber adhesives, discussing their properties, applications, and future trends that may influence their development and usage.
By exploring the chemical makeup, physical properties, and manufacturing processes of rubber adhesives, it highlights their significance in modern applications. We will also address environmental considerations and the innovations that are reshaping this industry. Throughout this exploration, we seek to bridge the gap in knowledge regarding rubber adhesives and their role in technological advancements.
Key Concepts and Terminology
Definition of Key Terms
In order to fully grasp the nuances associated with rubber adhesives, it is necessary to clarify several key terms:
- Adhesive: A substance that binds two surfaces together through surface attachment.
- Elastomer: A polymer with viscoelasticity, exhibiting both viscosity and elasticity, often used in rubber adhesives.
- Curing: The process of hardening the adhesive through chemical reactions or evaporation of solvents.
- Substrate: The underlying material the adhesive is applied to.
Concepts Explored in the Article
The article delves into various concepts related to rubber adhesives, including the following:
- The chemical composition of rubber adhesives, which typically includes natural rubber or synthetic rubber mixed with additives.
- The mechanical properties, such as tensile strength and elasticity, which determine how well the adhesive can perform in different environments.
- Various applications across industries, showcasing how rubber adhesives are utilized in automotive, construction, and consumer goods.
Findings and Discussion
Main Findings
This examination reveals critical insights regarding rubber adhesives:
- Rubber adhesives are valued for their capability to bond dissimilar materials.
- Their flexibility allows them to maintain adhesion even when subjected to thermal or mechanical stress.
- Eco-friendly options are becoming increasingly available as manufacturers seek sustainable solutions.
Potential Areas for Future Research
Future research may focus on these areas:
- Development of bio-based rubber adhesives to reduce environmental impact.
- Investigation of new curing methods that enhance performance and applicability.
- Exploring the integration of smart technologies into adhesive formulations to improve functionality.
The exploration of rubber adhesives is essential for understanding their pivotal role in various technological advancements.
By formalizing our knowledge around these aspects, we aim to contribute significant insights into the rich field of rubber adhesives, ultimately guiding future innovations.
Prolusion to Rubber Adhesives
Rubber adhesives represent a vital segment of adhesive technologies that merit comprehensive understanding. Their unique properties and versatility find applications across various sectors clearly demonstrating their relevance in modern manufacturing and daily use. This section serves to introduce rubber adhesives, highlighting their significance and certain characteristics that make them essential in multiple industries.
Definition and Overview
Rubber adhesives are formulated to bond materials using rubber-based polymers. This category of adhesives can be either synthetic or natural. The main characteristic of rubber adhesives is their elasticity, which provides an ability to withstand stress and movement without losing their adhesive properties. They find usage in diverse applications such as automotive assembly, electronic devices, and even footwear production. The effectiveness of rubber adhesives largely depends on their composition and the conditions of application, including surface preparation and environmental factors. Their unique qualities include strong adhesion, resistance to impact, and flexibility.
Historical Development
The history of rubber adhesives dates back to the early 20th century when researchers began exploring the properties of rubber as bonding agents. Initially, natural rubber was the primary material used. Over time, the development of synthetic rubber, particularly during and after World War II, allowed for increased performance and versatility. Synthetic options like styrene-butadiene rubber and polyisoprene emerged, enhancing application potential. This evolution led to widespread adoption in industries such as automotive and construction, where strong, reliable adhesion is crucial. Today, continuous advancements in formulation practices are driving further innovations within the sector, responding to evolving market demands and environmental considerations.
"Rubber adhesives have significantly transformed industries by providing flexible and durable bonding solutions."
By understanding the foundational aspects of rubber adhesives through their definition and historical context, we lay the groundwork for exploring their chemical composition, physical properties, and diverse applications in the following sections.
Chemical Composition
In understanding rubber adhesives, it is crucial to examine the chemical composition. The specific elements that make up rubber adhesives have a significant impact on their characteristics and performance. The composition influences properties like strength, flexibility, and durability. Awareness of these elements helps in selecting the right adhesive for various applications.
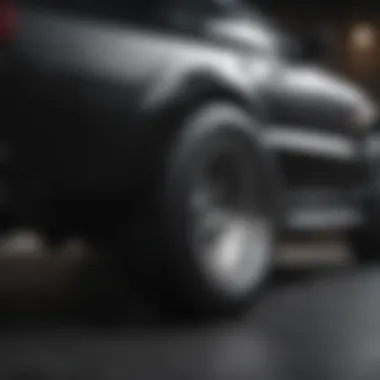
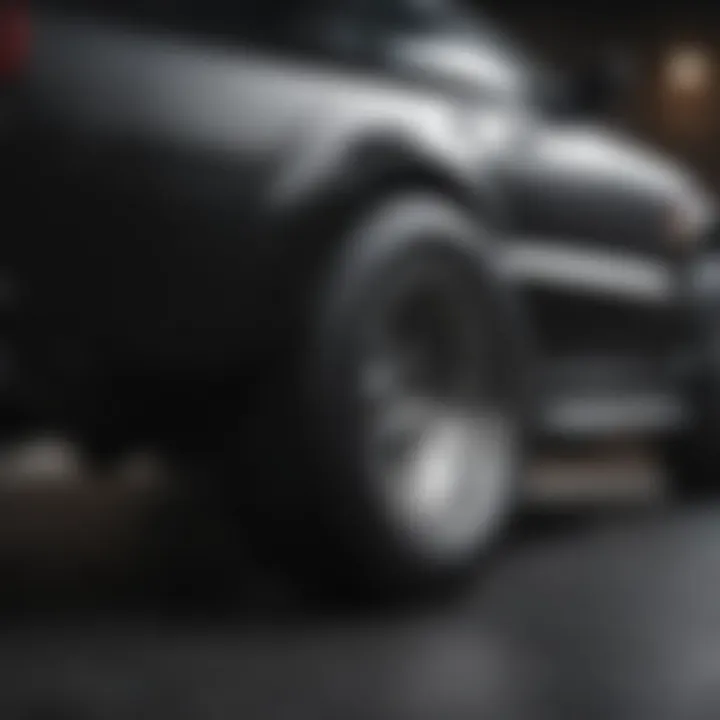
Types of Rubber Used
Synthetic Rubber
Synthetic rubber is an essential component in many rubber adhesives. It is produced through the polymerization of various monomers and has unique properties that enhance adhesive performance. The key characteristic of synthetic rubber is its ability to provide excellent elastic recovery and resistance to degradation due to environmental factors. This makes it a popular choice in industries such as automotive and construction, where durability is paramount.
The unique feature of synthetic rubber lies in its tailored properties. Polymer blends can be designed to specific requirements, providing versatility in application. However, synthetic rubber often has a higher cost of production due to the complex processes involved, which can be a disadvantage for budget-sensitive projects.
Natural Rubber
Natural rubber is derived from the sap of rubber trees, making it biodegradable and more environmentally friendly. Its primary contribution is its superior elasticity and tensile strength, which makes it valuable for numerous applications. The key characteristic of natural rubber is its outstanding adhesion to various substrates, enhancing overall performance. This property makes natural rubber a favored choice for industries where flexibility and bond strength are critical, such as in footwear manufacturing.
One unique feature of natural rubber is its sustainability. As demand for eco-friendly products grows, natural rubber fills the niche. Nonetheless, it can be less resistant to heat and certain chemicals compared to its synthetic counterpart, which may limit its uses in harsh environments.
Additives and Modifiers
Fillers
Fillers are a crucial addition to rubber adhesives as they modify the adhesive's properties and cost-effectiveness. They often improve the bulk and reduce the overall production costs of adhesives. The key characteristic of fillers is their capacity to enhance the mechanical strength of the adhesive while maintaining flexibility. This is beneficial for industrial applications that require durable performance at lower costs. Fillers such as carbon black and silica are commonly used.
A unique feature of fillers is their ability to improve adhesion traits by reinforcing the rubber matrix. However, an excessive amount may lead to a decrease in other important properties, like flexibility, thus careful balance is required.
Plasticizers
Plasticizers are used in rubber adhesives to increase flexibility and reduce brittleness. This gives the adhesive improved handling and application characteristics. The central characteristic of plasticizers is their ability to lower the glass transition temperature of the rubber, which leads to a more pliable adhesive. This trait is particularly beneficial in applications requiring a high degree of movement or flex.
One unique feature of plasticizers is their ability to extend the life of the adhesive by preventing it from becoming rigid over time. However, overuse can lead to migration issues, which may impact the adhesive's performance over long periods.
Stabilizers
Stabilizers are important for maintaining the physical integrity of rubber adhesives over time. They play a significant role in protecting the adhesive from degradation caused by environmental factors such as UV light and heat. The key characteristic of stabilizers is their ability to extend the shelf life of adhesives, ensuring efficacy during use. This is especially important for manufacturers who require reliable performance from their products.
A unique feature of stabilizers is their dual functionality. They help to maintain color and structure while preventing the rubber from breaking down. However, some stabilizers can introduce complexity to the formulation, which can pose challenges during production.
Physical Properties
Understanding the physical properties of rubber adhesives is crucial as it directly influences their effectiveness and applicability in various industries. Physical properties determine how well these adhesives bond materials together, how they perform under stress, and their long-term stability in diverse environments. When discussing rubber adhesives, the focus generally lies on adhesive strength, flexibility and elasticity, and temperature resistance. Each of these properties is a significant consideration for manufacturers and end-users alike, impacting both product performance and the specific choices of adhesive for particular applications.
Adhesive Strength
Adhesive strength is a primary physical property of rubber adhesives that needs careful evaluation. It refers to the ability of the adhesive to bind surfaces together under various conditions. Strong ionic and covalent bonds formed during curing contribute to high adhesive strength, which is vital for ensuring that bonded materials hold securely over time.
In many applications, such as in the automotive and construction industries, the strength of the bond can directly influence safety and durability. Factors like surface preparation and environmental conditions during application also play roles in determining the adhesive strength. For example, a surface that is clean and suitably roughened can enhance the bonding strength.
Additionally, tests such as peel and shear strength are commonly used to quantify adhesive strength, providing metrics that reflect how well an adhesive can withstand forces applied at different angles and stresses. These tests are essential for understanding the limits of an adhesive in practical use.
Flexibility and Elasticity
Flexibility and elasticity are critical characteristics of rubber adhesives that allow them to perform well under stretching and bending forces. These properties are particularly important in applications where materials may undergo movement or thermal expansions, such as in the automotive and footwear sectors.
Rubber adhesives typically exhibit a high degree of elasticity, allowing them to absorb shocks and vibrations. This is especially crucial in automotive applications where vehicles experience various dynamic forces while in motion. The flexibility helps maintain adhesive integrity even when subjected to fluctuating loads or impacts.
Furthermore, flexible adhesives help in maintaining the appearance and structural integrity of bonded materials. Rigid adhesives could crack or break when the materials shift or deform, leading to failure of the bond. Hence, asphalt-based or polyurethane-based rubber adhesives, which inherently incorporate flexibility, are favorable for applications requiring such properties.
Temperature Resistance
Temperature resistance indicates how well a rubber adhesive can sustain its performance in varying thermal conditions. This property is vital for applications that expose the adhesive to extremities in temperature, whether high heat or cold environments.
Rubber adhesives often show good temperature resistance due to their intrinsic properties. However, the specific formulation significantly influences this capability. For instance, neoprene and silicone-based adhesives are known for their exceptional high-temperature resistance, making them the materials of choice in demanding applications such as electronics and automotive engines. Conversely, low-temperature resistance is also a concern, as some adhesives may become brittle and lose adhesion under cold conditions.
Overall, the ability of rubber adhesives to retain adhesive properties across a range of temperatures ensures reliability in various applications and environments, further contributing to the versatility of these materials.
"The performance of rubber adhesives is largely dependent on their physical properties, which have significant implications on their application across numerous sectors."
Manufacturing Processes
Understanding manufacturing processes is crucial when discussing rubber adhesives. The methods used for production significantly affect the performance, efficiency, and applicability of these adhesives. The choice of process can determine the adhesive's characteristics, such as viscosity, drying time, and bonding strength. A well-managed manufacturing process not only ensures high-quality output but also addresses the complexities of large-scale production. With the increased demand for sustainable and effective adhesive solutions, the techniques employed have evolved to meet both industry and environmental standards.
Production Techniques
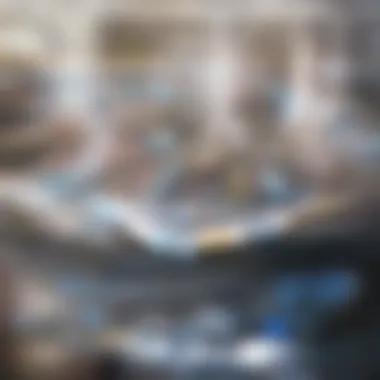
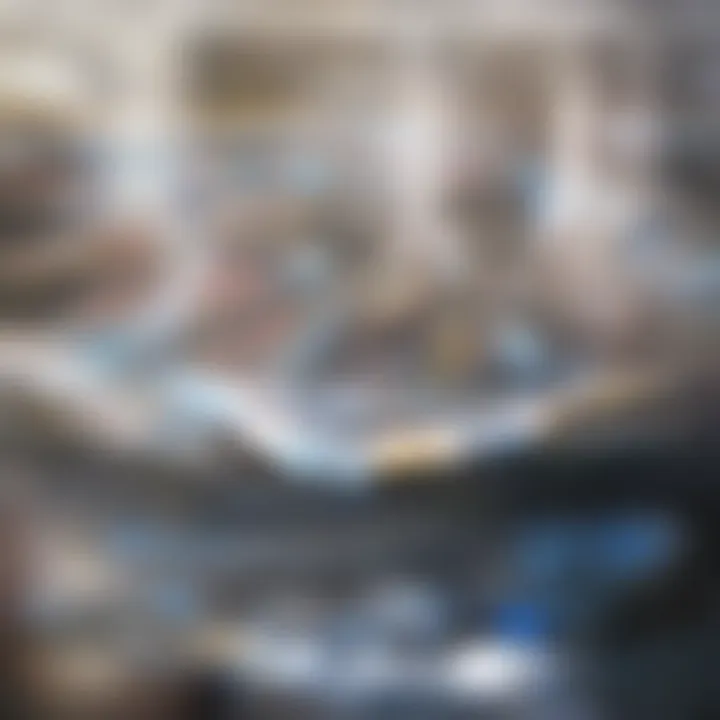
Solvent-Based Processes
Solvent-based processes for rubber adhesives have been widely recognized for their effective bonding capabilities. This method involves dissolving rubber in a solvent, creating a viscous adhesive that is easy to apply. Key characteristics of solvent-based adhesives include their strong initial tack and excellent adhesion strength on various substrates. This makes them favorable for many applications, such as automotive and packaging industries.
One unique feature of solvent-based processes is their rapid drying time, which can enhance production efficiency. However, this method also presents disadvantages, primarily related to the environmental impact of solvents. The use of volatile organic compounds can lead to air quality issues and regulatory challenges. Manufacturers must navigate these concerns while maximizing the benefits of this approach.
Water-Based Processes
Water-based processes have gained traction in recent years as a more environmentally friendly alternative to solvent-based methods. By formulating adhesives with water as the primary solvent, manufacturers can reduce the emission of harmful compounds. The characteristic of low toxicity makes water-based adhesives attractive for applications in sensitive environments such as food packaging and children's products.
The unique feature of water-based processes is their versatility. They can be modified with various additives to improve performance and accommodate different production requirements. However, these adhesives might not offer the same initial bonding strength as solvent-based ones. Their drying time can also be longer, which could affect manufacturing efficiency.
Heat Curing
Heat curing is a specialized technique utilized in rubber adhesive manufacturing that improves the adhesiveβs overall properties. This process involves applying heat to chemically crosslink the rubber components, enhancing durability and heat resistance. One of the key characteristics of heat curing is its ability to produce adhesives that can withstand high temperatures, making them suitable for demanding applications.
A unique feature of heat curing is the potential for improved mechanical properties in the final product compared to adhesives produced through other methods. However, the need for specialized equipment and monitoring can complicate this process. Additionally, the time needed for curing can slow down production rates.
Quality Control Measures
Quality control measures play a vital role in the production of rubber adhesives. They ensure that the final product meets the necessary specifications and standards. Implementing stringent quality control helps manufacturers identify defects early in the process, resulting in consistent and reliable adhesive performance.
Applications of Rubber Adhesives
Rubber adhesives are critically important across various industries, owing to their unique properties and reliable performance. They provide essential bonding solutions required in numerous applications. Understanding the applications of rubber adhesives is necessary to grasp their significance in todayβs market and environment. These adhesives exhibit notable flexibility, temperature resistance, and durability, making them suitable for both industrial and consumer products.
Automotive Industry
The automotive industry places a high demand on rubber adhesives for several applications. These products are used for assembling various parts like dashboards, trim, and weatherstripping. The strong bond provided by rubber adhesives contributes to vehicle durability and safety. Additionally, their flexibility allows them to withstand vibrations and impact, which are common in automotive environments. Moreover, the use of these adhesives can lead to weight reduction of components, which is increasingly important for fuel efficiency and performance. The growing trend of electric vehicles also sparks innovation in adhesive formulations, focusing on lightweight materials and better adhesion properties.
Construction Sector
In the construction sector, rubber adhesives are utilized for bonding flooring, roofing materials, and insulation panels. Their moisture resistance and longevity make them suitable for both indoor and outdoor applications. These adhesives can contribute to improved structural integrity and energy efficiency. Rubber adhesives also play a pivotal role in securing windows and doors. Their ability to maintain a strong bond under varying temperature and humidity levels enhances building comfort and safety. Greater emphasis is placed on sustainability, leading to the development of eco-friendly rubber adhesives that meet rigorous environmental standards.
Footwear Manufacturing
Footwear manufacturing employs rubber adhesives extensively for assembling various components, such as soles and uppers. The flexibility and comfort provided by these adhesives contribute significantly to consumer satisfaction. Ensuring durability is paramount, as footwear must withstand daily wear and tear. Rubber adhesives provide a secure bond that prevents delamination and enhances the overall lifespan of the product. Innovations in this sector now include the use of water-based rubber adhesives, which limit harmful emissions during production, aligning with sustainability goals.
Electronics and Electrical
In the electronics and electrical fields, rubber adhesives are essential for encapsulating sensitive components and providing insulation. These adhesives can withstand thermal cycling, protecting electronics from damage. Their dielectric properties ensure safe operation within electrical devices. Use in potting and encapsulation applications allows for enhanced protection against moisture and mechanical stress. This application aligns with the increasing miniaturization of electronics, as adhesives help secure components without requiring excessive space. Technological advancements in adhesive chemistry continue to drive improvement in performance criteria, aiding the design of smarter electronics.
"Rubber adhesives represent a cornerstone in manufacturing across various sectors, supporting innovation, sustainability, and reliability."
The wide-ranging applications of rubber adhesives illustrate their versatility. From enhancing vehicle safety to contributing to eco-friendly building solutions, they play a pivotal role in modern technology. As industries evolve, the demand for high-performance ruber adhesives will surely increase, fostering further advancements.
Environmental Considerations
In the context of rubber adhesives, environmental considerations play an increasingly vital role. The production and disposal of these adhesives can have significant ecological impacts. As industries prioritize sustainability, understanding these factors becomes essential for companies and research institutions alike.
Sustainability Issues
Sustainability issues related to rubber adhesives can be categorized into several key areas:
- Resource Extraction: Natural rubber is derived from rubber trees, which requires land and resources. Over-exploitation can lead to deforestation and habitat destruction. Ensuring sustainable sourcing practices is critical to mitigate environmental harm.
- Chemical Use: The manufacturing of rubber adhesives often involves various chemicals, some of which can be harmful to the environment. For instance, certain solvents contribute to pollution when not handled properly. Manufacturers face pressure to minimize such chemicals and explore eco-friendly alternatives.
- Waste Management: Improper disposal of rubber adhesives can harm ecosystems. Non-biodegradable materials create long-term waste issues in landfills, making recycling programs important. Implementing effective waste management strategies is critical to reduce environmental footprints.
Addressing these sustainability challenges requires innovation and a commitment to responsible practices. Companies may need to invest in new technologies to reduce the environmental impacts of their adhesives while maintaining performance.
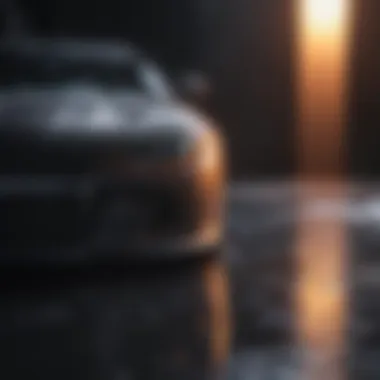
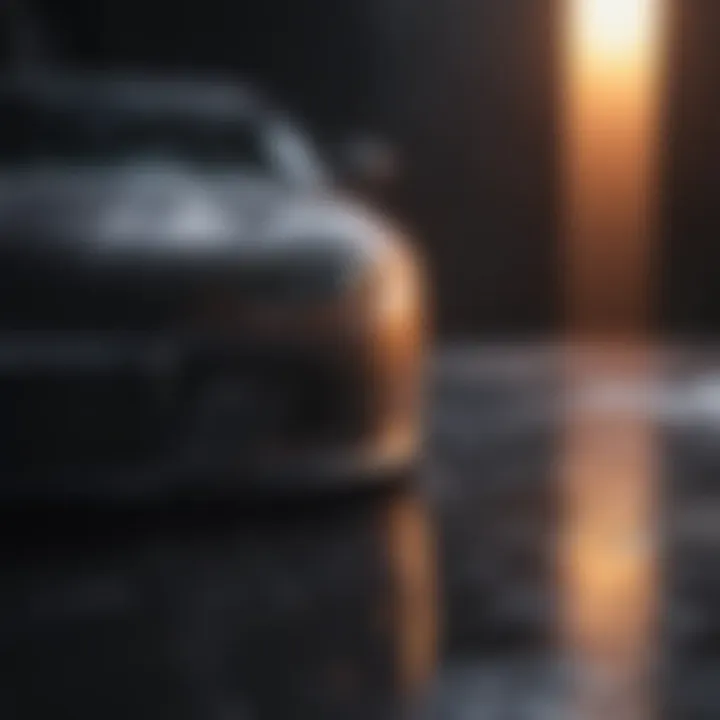
Regulations and Standards
Regulation and standards surrounding rubber adhesives are designed to ensure safe manufacturing practices and reduce environmental impacts. These frameworks exist at both international and local levels:
- Chemical Safety Regulations: Guidelines such as the REACH (Registration, Evaluation, Authorisation and Restriction of Chemicals) in Europe safeguard against harmful substances. Compliance ensures that harmful materials are minimized or eliminated throughout the lifecycle of rubber adhesives.
- Environmental Standards: Organizations like the ISO (International Organization for Standardization) promote standards for sustainable practices in the adhesive sector. These standards provide a benchmark for companies to measure their environmental impact and improve their processes.
- Local Legislation: Various countries enforce laws requiring businesses to reduce emissions and manage waste. Staying compliant is crucial for manufacturers wanting to operate in a responsible manner.
Adopting these regulations not only helps in minimizing environmental threats but also positions companies favorably in a market that values sustainability. As awareness grows, so does the demand for environmentally responsible products.
Challenges in the Industry
The rubber adhesive industry faces numerous challenges that impact its growth and sustainability. These challenges are pivotal to understanding the landscape of rubber adhesives and their applications. Tackling these issues is essential for enhancing product quality, ensuring competitive pricing, and maintaining market relevance.
Quality Consistency
Quality consistency is a fundamental challenge within the rubber adhesive market. Fluctuations in raw material quality can lead to variations in the final product. Manufacturers must ensure that every batch of adhesives meets specified standards to maintain customer trust and satisfaction. Suppliers of synthetic and natural rubber, along with chemical additives, can sometimes provide materials of varying quality, which complicates the production process.
To overcome these challenges, companies implement rigorous quality control measures. Techniques such as batch testing and continuous monitoring during production can help achieve uniformity. When consumers rely on a product, such as in the automotive or construction sectors, the predictability of performance becomes essential.
Furthermore, adherence to standards set forth by organizations like ASTM International plays a crucial role. These standards guide the expectations for adhesive performance and safety, ensuring that products are dependable across different applications. As manufacturers adhere to these guidelines, they position themselves to gain a competitive edge in the marketplace.
Market Competition
Market competition is another significant challenge in the rubber adhesive industry. With numerous manufacturers vying for market share, price pressure can affect profitability. New entrants often push prices down to gain entry, which can lead to a race to the bottom in quality and service.
Established companies must innovate continually and differentiate their products to maintain customer loyalty. Investing in research and development allows firms to explore new formulations that offer superior performance or sustainability advantages. For instance, eco-friendly rubber adhesives are gaining traction due to rising environmental awareness. Emphasizing greener products can attract a customer base that values sustainability.
Additionally, geographical shifts in production and supply chains can influence competition. Companies must be nimbler, adapting to changes in local economies and regulations. Understanding market dynamics, including consumer preferences and technological advancements, is crucial for long-term success.
The rubber adhesive industry is at a crossroads. Its challenges can either hinder growth or propel innovation, depending on how effectively companies respond to them.
Future Trends
The future of rubber adhesives stands at the intersection of emerging technologies and evolving market demands. Understanding these trends is essential for professionals in the adhesive industry. The importance of knowing where the rubber adhesive market is headed cannot be understated. Innovations and growing demand will play pivotal roles in shaping the landscape of rubber adhesives.
Innovations in Formulation
Innovations in formulation represent a significant breakthrough in the rubber adhesive industry. Advancements in polymer chemistry have introduced new formulations that enhance the performance characteristics of adhesives. The focus is now on developing products that deliver better adhesion, improved durability, and lower environmental impact. Companies are investing in research and development to create rubber adhesives that utilize bio-based materials, thus reducing reliance on petroleum-derived resources.
Moreover, advancements in nanotechnology have led to the incorporation of nanoparticles into rubber adhesives. These nano-fillers can greatly improve mechanical properties and thermal stability. The smart adhesive concept is also emerging. These adhesives can respond to environmental stimuli, such as temperature or moisture. The flexibility of formulations allows for customization to meet specific application requirements.
Growing Demand
The growing demand for rubber adhesives is driven by various factors across multiple industries. In the automotive industry, for instance, the move towards lightweight materials and high-performance solutions is increasing the need for specialized adhesives. As electric vehicles gain popularity, the demand for reliable bonding solutions for battery packs and structural components continues to rise.
In the construction sector, rubber adhesives are being widely used in flooring and roofing applications. This is due to their superior bonding capabilities and resistance to outdoor conditions. Additionally, the focus on sustainability is pushing manufacturers to seek eco-friendly adhesive solutions, further fueling the demand for innovative rubber adhesives.
Consumer awareness about product quality is also increasing. This trend is making manufacturers place a stronger emphasis on choosing high-performance adhesives, which meet strict safety and environmental standards.
"The future of rubber adhesives is shaped by the drive for innovation and the necessity for sustainability across all sectors."
In summary, the future trends in rubber adhesives highlight a promising trajectory driven by continuous improvement and adaptation to emerging market demands. Understanding these shifts is crucial for academics, industry professionals, and researchers as they navigate the complexities of this dynamic field.
Closure
The conclusion of this article serves to encapsulate the significance of rubber adhesives in various modern applications, alongside the critical points discussed throughout the text. Rubber adhesives present unique properties that make them reliable in a wide range of industries. Their ability to bond materials effectively, along with their flexibility and durability, directly affects quality and performance. Understanding the nuances of rubber adhesive is essential for professionals in manufacturing, engineering, and environmental sustainability.
Summary of Key Points
- Chemical Composition: The article discusses the types of rubber, including natural and synthetic rubber, and how additives like fillers and plasticizers enhance rubber adhesives.
- Physical Properties: Key characteristics such as adhesive strength, flexibility, and temperature resistance determine suitability for different applications.
- Manufacturing Processes: Various production techniques impact the quality and utility of rubber adhesives.
- Applications: Rubber adhesives are prevalent in sectors like automotive, construction, and electronics, demonstrating their versatility.
- Environmental Considerations: This includes sustainability issues and compliance with regulations, highlighting the need for responsible practices in production and use.
- Challenges in the Industry: Factors such as quality consistency and market competition pose ongoing issues for manufacturers.
- Future Trends: Innovations in formulation and growing demand indicate a dynamic future for rubber adhesives.
The Importance of Understanding Rubber Adhesives
Gaining an understanding of rubber adhesives is vital for many reasons. First, it allows professionals to make informed choices regarding material selection and application techniques. Second, knowledge of the properties and behaviors of these adhesives can lead to improved product performance and innovation. Lastly, addressing challenges like sustainability and regulatory compliance becomes manageable with a solid grasp of the subject.
In summary, rubber adhesives are integral to advancing technology in various fields. As the landscape evolves, staying informed about these materials ensures preparedness for future developments and challenges within the industry.