Understanding Sheet Metal Hem Rollers: Design and Uses
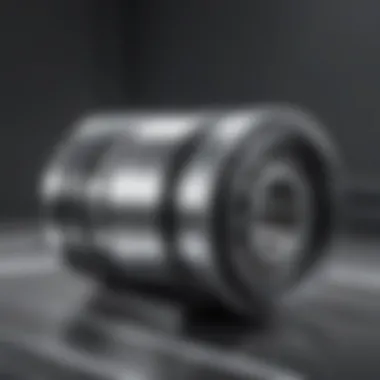
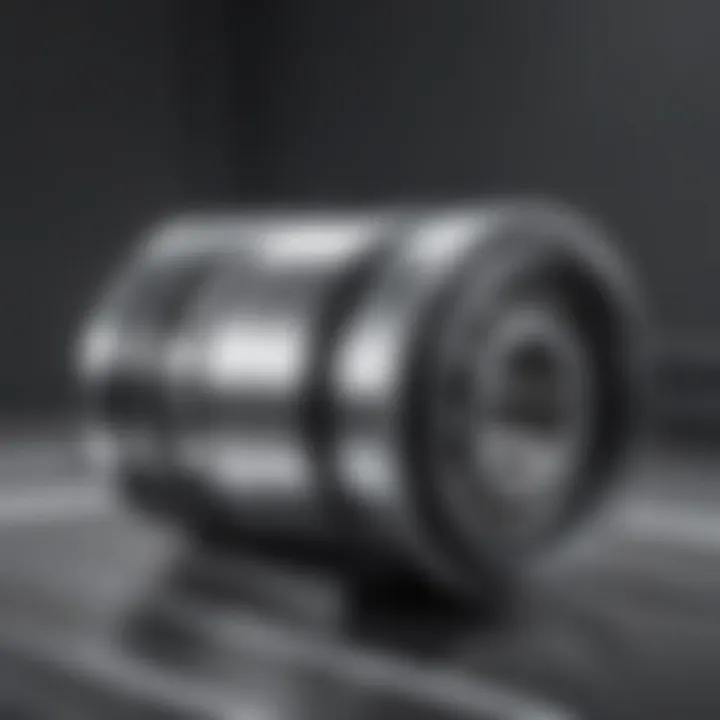
Intro
In the realm of metalworking, the sheet metal hem roller serves a critical function. Not just a mechanical wonder, it’s a tool that plays an important role in achieving precision in metal fabrication. As industries shift towards more automated and efficient processes, understanding this tool assumes a prominent place in the toolkit of those engaged in metal crafting.
The use of hem rollers is not merely a whim of technological advancement but a response to growing needs for both aesthetic and functional finishes in sheet metal applications. From automotive manufacturing to architectural design, incorporating a hem roller can make a significant difference in the final outcome of a product.
Diving deeper into the hem roller's architecture reveals not just how it works but also why it's indispensable in various sectors. It's not all about bending metal; it’s about bending it right. The article will unfold the intricacies of this tool, from its core components to its varied real-world applications, demonstrating its complex yet fascinating role in the metalworking industry.
Foreword to Sheet Metal Hem Rollers
In the realm of metalworking, sheet metal hem rollers hold a pivotal role, serving both functional and aesthetic purposes. Understanding their design and mechanics isn't just beneficial for practitioners; it’s essential for anyone involved in manufacturing, construction, or engineering.
These tools transform otherwise sharp or unappealing edges into neat, functional seams. This not only enhances the visual appeal of metal components but also ensures durability, thus extending the lifespan of products. Artists, builders, and fabricators all mark the importance of employing hem rollers effectively in their work, as they infuse both efficiency and precision into the manufacturing process.
Here, we will break down the essentials of what hem rollers are, how they evolved, and the enormous impact they have across various industries. Additionally, we will explore the mechanics of operation, their practical applications, and why they’re indispensable in the toolbox of a metalworker.
Definition and Overview
A sheet metal hem roller is a specialized tool designed to bend the edges of sheet metal into a hem. This process not only smooths out sharp edges but also reinforces the material. In simple terms, a hem roller allows one to roll the edges of metal sheets inward or outward, creating a finished edge.
Commonly used in the fabrication of various components—from ductwork in HVAC systems to intricate parts in automotive or aerospace applications—hem rollers can vary widely in terms of design and complexity. You can find manual versions that require physical effort, as well as more advanced electric or hydraulic models that offer powered assistance.
Such versatility makes these machines essential for both small workshops and large manufacturing facilities alike. Their ability to enhance both durability and aesthetic appeal is a boon for anyone dealing with sheet metal.
Historical Context
The origins of sheet metal hemming can be traced back centuries, even before industrialization took hold. Blacksmiths and metal workers crafted various tools by hand, using rudimentary techniques that set the foundation for modern practices. Unfolding the narrative of hem rollers reveals a fascinating journey through technology and craftsmanship.
As time progressed, innovations in metallurgy and machining propelled hem rolling into a more systematic approach. The Industrial Revolution marked a significant turning point, allowing for the mass production of metal components with greater precision. Traditional methods transformed, leading to the mechanized tools employed today.
With advancements in technology, the emergence of specialized hem rollers took place in the late 19th to early 20th century, as metalworking industries exploded in growth. This shift not only improved productivity but also laid the groundwork for today's intricate applications in sectors ranging from aerospace to construction.
"The evolution of hem rollers reflects the broader shifts in metalworking, showcasing how necessity drives innovation."
Reflecting back, understanding the history of these tools can provide invaluable insight into their significance and the ongoing advancement of technology in sheet metal fabrication.
Types of Sheet Metal Hem Rollers
When delving into the world of sheet metal hem rollers, understanding the different types serves as a foundational step. Each variant has its own unique features and advantages that cater to various applications. From manual to hydraulic options, the choice of hem roller significantly impacts efficiency and precision in metalworking processes. This section will explore these types, shedding light on their specifications, benefits, and considerations.
Manual Hem Rollers
Manual hem rollers stand out for their simplicity and cost-effectiveness. These tools rely predominantly on human force to operate, making them ideal for workshops where productivity does not require the speed found in automated systems. The design typically involves a pair of adjustable rollers, allowing the operator to guide the metal sheet through a predetermined shape.
- Benefits:
- Low initial investment cost compared to electrical or hydraulic models.
- Excellent for small-scale or custom projects where flexibility is paramount.
- Provides the operator a sense of tactile feedback and control over the shaping process.
Overall, manual hem rollers are a practical choice for hobbyists and small businesses focusing on precision and craftsmanship.
Electric Hem Rollers
Electric hem rollers mark a significant leap in efficiency and productivity. These machines utilize electric motors to rotate the rollers, allowing for a steadier and faster processing of metal sheets. They are often equipped with advanced controls for programming various bending angles and dimensions, making them suitable for medium to heavy-duty applications.
- Benefits:
- Enhanced speed significantly reduces time spent on production tasks.
- Increased repeatability ensures consistent results across large batches.
- Reduced operator fatigue since it requires less manual effort.
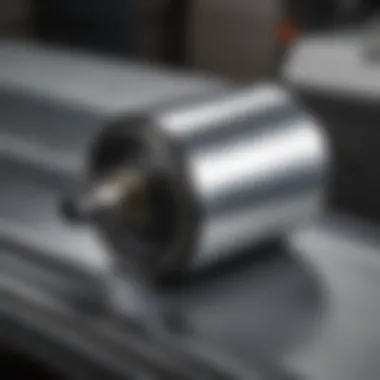
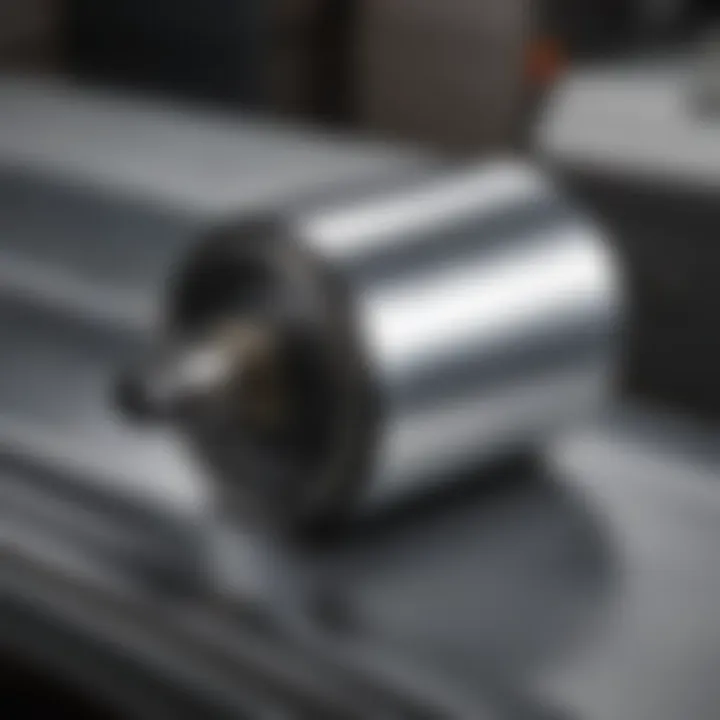
These hem rollers find their niche in industries where production speed and precision are critical, such as automotive manufacturing and large-scale fabrication shops.
Hydraulic Hem Rollers
Hydraulic hem rollers are the heavyweights of the sheet metal bending world. Utilizing hydraulic power, these machines can handle thicker and harder materials with ease. This capability makes them integral to industries that require intricate shapes and forms in their metal parts. The hydraulic system provides a controlled and powerful force, allowing for greater customization in the bending process.
- Benefits:
- Exceptional capacity for bending heavy gauges and tough materials without compromising quality.
- Ability to execute complex shapes and extensive cycles without overheating the machine.
- Often equipped with digital readouts and precise controls for exact measurements.
The hydraulic option is preferred in high-demand settings such as heavy machinery manufacturing and architectural applications where metal bending must meet stringent standards.
Through understanding these various types of sheet metal hem rollers, professionals can select the tool that perfectly aligns with their production needs. Each model provides distinct advantages tailored to specific tasks, influencing both the workflow and the final product's quality.
Mechanics of Operation
Understanding how a sheet metal hem roller operates is crucial for professionals who aim to maximize efficiency and precision in their work. The mechanics of operation provide insight into the intricate processes that enable the bending and shaping of metal sheets. Knowledge in this area not only helps in improving the quality of the finished product but also enhances productivity across various applications.
Understanding the Rolling Process
At the heart of the hem roller's functionality is the rolling process itself. The action begins with placing the metal sheet between the rollers, which are often constructed from robust materials to withstand high levels of pressure. As the rollers rotate, they progressively bend the edges of the metal sheet into a hem. This can occur in multiple passes, each refining the bend until it reaches the desired angle and uniformity.
What's noteworthy here is the interplay between the metal’s properties and the machine's settings. The width of the hem, the thickness of the material, and the type of bend impact how the metal reacts under pressure. For instance, aluminum sheets, known for their malleability, can be shaped more easily than stronger materials like stainless steel which requires careful adjustment of roller tension and speed to prevent cracking.
"Grasping the rolling process is essential in understanding the versatility and capability of hem rollers in the metalworking sector."
Key Components of a Hem Roller
The effectiveness of a hem roller lies within its key components. Each element plays a pivotal role in achieving precise and consistent results. Major components include:
- Rollers: Typically three in number, they guide the metal through the machine. The material and diameter of the rollers affect the bending capability.
- Operating Handles or Controls: Depending on the type—manual, electric, or hydraulic—these components allow for varying degrees of pressure and control for the hem formation.
- Base Frame: Provides stability during the rolling process, ensuring minimal vibrations that could affect the quality of the bend.
- Feed Mechanism: Aids in the safe introduction of the sheet into the machine while maintaining alignment.
Understanding these components allows users to tailor their approach based on material type and project requirements.
Material Considerations
Material selection plays a critical role in the operation of hem rollers. Different materials not only require distinct techniques but also have varied responses during the rolling process. Common materials like steel, aluminum, and copper exhibit different characteristics:
- Steel: Often utilized for its strength, but requires more force and precision during the rolling process to avoid indents or breaks.
- Aluminum: Preferred for lighter applications due to its malleability. Users can employ quicker rolling speeds without the risk of damage.
- Copper: Though less common, its ductility allows for intricate designs; however, it can present challenges such as increased wear on the machine components.
In summary, understanding material behavior is fundamental for optimizing the hem rolling process. Correct assessments can save time and resources while steering clear of potential pitfalls during metal fabrication.
Applications in Various Industries
Understanding the applications of sheet metal hem rollers across various industries is crucial for grasping their significance in modern manufacturing and fabrication processes. These tools facilitate precision bending and shaping of metal sheets, leading to enhanced product quality and structural integrity. The versatility of hem rollers allows them to adapt to numerous contexts, providing efficiency and functionality in sectors as varied as manufacturing, construction, and aerospace. By examining these applications, we can appreciate not only the mechanical capabilities of these tools but also their impact on overall productivity and craftsmanship.
Manufacturing Sector
In the manufacturing sector, sheet metal hem rollers play a pivotal role in producing components for a wide range of products. Whether it's automotive parts, appliances, or consumer goods, the precision offered by these machines is invaluable. They enable manufacturers to create seamless hems, which are essential for ensuring the strength and durability of metal panels.
- Quality Assurance: Using hem rollers, manufacturers can achieve precise bending angles. This is critical for maintaining tolerances in production runs, which leads to higher quality finished products.
- Mass Production: Hem rollers often come with the capacity for high-volume production. This efficiency reduces lead times and helps businesses meet demanding market needs without sacrificing quality.
Moreover, the integration of manual, electric, and hydraulic hem rollers allows for a range of applications within manufacturing processes, accommodating everything from small workshops to large industrial factories.
Construction Industry
In the construction industry, the importance of reliable sheet metal hem rollers cannot be overstated. These tools contribute to various structural applications, including roofing, siding, and custom metalwork. The ability to create clean, strong hems on metal sheets improves the overall aesthetics and functional performance of construction elements.
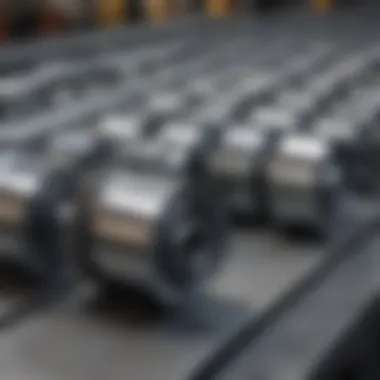
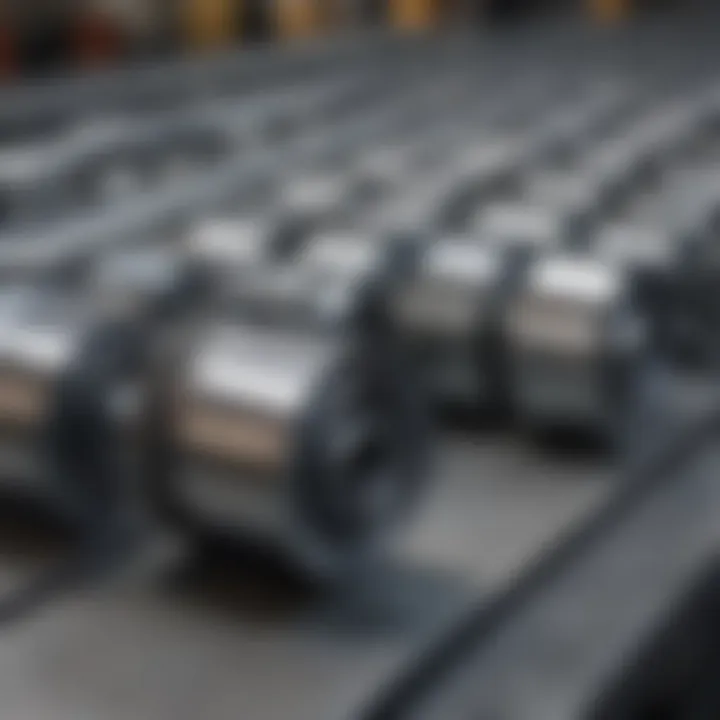
- Custom Fabrication: Hem rollers enable the production of custom metal pieces that fit specific architectural designs, offering flexibility for builders and contractors.
- Durability in Elements: Constructed elements with properly rolled hems withstand weathering and wear, contributing to the longevity of structures, especially in harsh environments.
The use of hem rollers can thus accelerate project timelines and reduce waste, leading to more efficient construction processes.
Aerospace Engineering
When it comes to aerospace engineering, precision is non-negotiable. Hem rollers are integral in the formation of lightweight, durable parts necessary for aircraft and spacecraft components.
- Weight Reduction: Since every ounce counts in aerospace design, hem rollers help fabricators create thin but strong profiles, which contribute to weight savings without compromising structural integrity.
- Compliance Standards: Aerospace components must adhere to strict safety and regulatory standards. The accuracy achieved through professional hem rolling ensures that components meet these high requirements, minimizing risks during production and operation.
In this industry, any enhancement in manufacturing capability can lead to significant advancements in technology and performance.
The applications of hem rollers are a testament to their significance in promoting efficiency and precision in metal processing across diverse sectors.
Advantages of Using Hem Rollers
Understanding the advantages of using hem rollers is crucial for both novices and seasoned professionals in the metalworking industry. These tools are not just about bending sheets of metal; they bring a whole collection of benefits to the table that can enhance both the quality of work produced and the workflows involved. Let's break down the key advantages into precise components that highlight their significance in various settings.
Enhancement of Precision
Precision is paramount when it comes to metal fabrication. Any slight misalignment can lead to faults that compromise the integrity of a project. Hem rollers excel in this domain by providing a consistent and repeatable process for bending metal edges. The design of these machines allows for fine adjustments, ensuring that every angle and curvature is exact. Unlike manual methods where human error can creep in, using a hem roller significantly minimizes risk.
For instance, a fabricator needs a hem on a piece of sheet metal for a structural application. Utilizing a hem roller guarantees that the bend meets the exact specifications required by engineering documents. Customers and builders alike find reassurance in knowing that each piece produced using these tools conforms to stringent quality controls. As the saying goes, "measure twice, cut once"; with hem rollers, the cutting is often unnecessary due to their precision capabilities.
Efficiency in Production
When you're aiming to keep production timelines tight while maintaining quality, hem rollers are a worthy ally. These tools drastically cut down the time spent on manual bending processes. Electric and hydraulic versions can handle larger volumes of metal, running through varying shapes in a fraction of the time it would take to achieve the same results manually.
Consider a busy manufacturing shop where many components are designed to the same specifications. A hem roller can churn through dozens of pieces in less time than it traditionally takes to perform a simple manual hem. This efficiency benefits all aspects of production, from labor costs to wastage rates. Also, regulars in the craft often point out that this capability enables more predictable workflow schedules, which is vital for any business’s bottom line.
Versatility in Applications
The versatility of hem rollers can not be overstated. They are not restricted to just one type of application but rather adapt to a multitude of projects across several industries. Whether it’s automotive, aerospace, construction, or even home improvement, these devices can handle different materials and types of bends with relative ease.
For example, an aerospace manufacturer might require specific tolerances and material thicknesses to fit precise engineering designs. Hem rollers can cater to these varying requirements by simply adjusting settings or changing out components like rolls. This adaptability allows companies to diversify their offerings without investing in a myriad of machines for each specific application. As a result, businesses equipped with hem rollers can attract a broader range of clientele.
In summary, the advantages of using hem rollers extend beyond basic utility. With enhancements in precision, efficiency, and versatility, these machines represent a significant asset in the metalworking industry, streamlining operations and ensuring high-quality output.
By adopting hem rollers, manufacturers not only become more competitive but also enhance their production capabilities to meet ever-evolving industry demands.
Limitations and Challenges
Understanding the limitations and challenges associated with sheet metal hem rollers is crucial for those working in the metalworking and fabrication industries. By acknowledging both the constraints of these tools and the skills required to use them effectively, users can maximize their capabilities while being aware of the potential pitfalls. This section offers a closer look at two primary areas of concern: material limitations and the technical skills required for optimal operation.
Material Limitations
Sheet metal hem rollers are designed to handle a variety of materials, but not all metals are created equal. Knowledge of material limitations is essential when selecting the right type of hem roller for a specific application. Factors like thickness, yield strength, and metal type play integral roles in determining whether the roller will perform effectively.
Some points to consider include:
- Material Thickness: Hem rollers are often rated for specific thicknesses. Using materials outside of this range can lead to poor results or even damage the tool.
- Metal Types: While rollers can process metals such as aluminum and stainless steel, they may struggle with harder alloys. This could result in inadequate bending or distortion.
- Surface Coatings: Coatings on metal sheets can affect the performance. Rollers may not grip coated surfaces effectively, leading to slippage during operation.
In short, insufficient understanding of these material limitations can impede efficiency, leading to wasted time and resources. Consequently, it's vital for operators to assess their metal choice thoroughly before beginning any work.
Technical Skills Required
Using a sheet metal hem roller isn't exactly as simple as turning a crank. Acquiring the necessary technical skills is paramount for anyone looking to get the most out of this equipment. Operators should have a baseline understanding of machinery, material properties, and operational techniques to ensure successful outcomes.
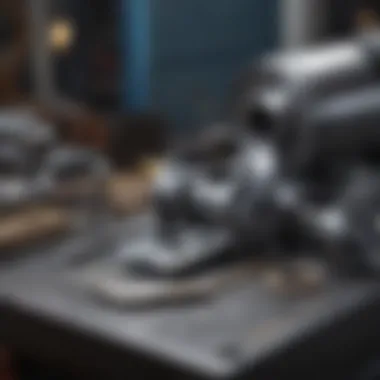
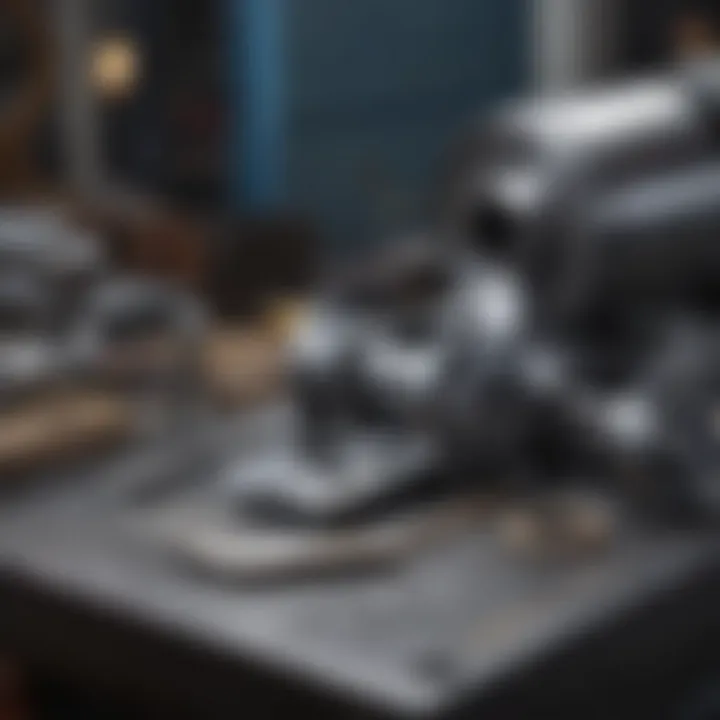
Some essential skills include:
- Understanding Mechanics: Knowing how different components of the hem roller work together is vital. An operator should understand the relationship between roller pressure and metal deformation.
- Calibration Aptitude: Proper calibration is key for accuracy. Being able to set up and adjust the roller according to the specific material and thickness ensures precision.
- Problem-Solving Skills: Issues may arise during the rolling process, such as misalignment or material jamming. Operators need to think critically to address and resolve these setbacks quickly.
A skilled worker can turn what seems like a simple task into a precise science, elevating the quality of output significantly.
Maintenance and Care
Maintaining sheet metal hem rollers is crucial for ensuring their longevity and optimal performance. Just like any piece of machinery, regular attention to these devices can mean the difference between smooth operation and unexpected breakdowns. The mechanical precision and the heavy-duty nature of hem rollers necessitate a maintenance routine that not only extends the lifespan of the equipment but also enhances the quality of the metalworking processes. For professionals in industries ranging from manufacturing to aerospace, neglecting maintenance can lead to costly errors and downtime.
Regular Checks and Balancing
Regular checks on a hem roller involve a systematic inspection of its components to identify any wear or potential failures before they escalate. This process can include:
- Inspecting belts and gears for signs of wear or misalignment.
- Examining the rollers for flatness and surface integrity.
- Checking for any rust or corrosion, especially if the machine operates in a humid environment.
- Ensuring the bolts and nuts are tight and secure.
Balancing is an equally vital aspect. An unbalanced hem roller can cause vibrations that lead to inaccurate rolling or even damage to the material being processed. These vibrations may also contribute to long-term wear on the machine itself. It's best practice to use precision equipment to check the balance of the rollers and make necessary adjustments to keep the entire setup steady.
Lubrication Techniques
Lubrication plays a pivotal role in the maintenance of sheet metal hem rollers. Proper lubrication reduces friction, which not only decreases wear on the moving parts but also improves the overall efficiency of the machine. Here are some techniques to ensure your hem roller stays well-lubricated:
- Regularly apply oil or grease: Depending on the design, some hem rollers may require specific types of lubricants. It's important to refer to the manufacturer's guidelines when choosing the lubricant to ensure compatibility and effectiveness.
- Use a lubricant applicator: Tools like brushes or spray nozzles can help direct lubricant more precisely to critical components without excessive over-application.
- Check lubrication points: Regularly inspect grease fittings to ensure they're operational and that the bearings receive adequate lubrication.
Proper maintenance, including checks and lubrication, will enhance the performance and lifespan of your sheet metal hem roller, keeping it in good shape for all your metalworking needs.
In summary, maintenance and care are not just about keeping machines running; they are about creating a reliable and productive work environment. For those invested in metalworking, understanding the essentials of maintenance will pay off with smoother operations and improved outcomes.
Future Trends in Sheet Metal Hem Rolling
As we stand on the brink of a new era in manufacturing, the trends shaping the future of sheet metal hem rollers signal profound shifts in technologies and methodologies. Embracing these shifts is crucial for industries that rely heavily on metalworking processes. The following sections will delve into specific advancements and innovations that are set to redefine the landscape for hem rollers.
Technological Advancements
The integration of cutting-edge technology into sheet metal hem rollers is perhaps the most pivotal trend observed in recent years. The rise of automation and digitalization in the manufacturing sector is revolutionizing how these machines operate. For instance, smarter software algorithms can optimize the rolling process, calculating parameters such as speed and pressure based on the material type and thickness. This not only enhances precision but also minimizes waste, which makes the overall operation more efficient.
Moreover, the advent of Industry 4.0 has introduced the concept of "smart factories." In these environments, machines are interconnected with data analytics platforms, which further promotes real-time monitoring and predictive maintenance.
"Technological advancements are enabling a seamless blend of traditional craftsmanship with modern precision, thus paving the way for innovation in manufacturing practices."
Additionally, the evolution of materials used in hem rollers is noteworthy. The use of durable, lightweight composites is becoming commonplace, offering advantages such as reduced energy consumption and increased lifespan of the tools. Hence, when considering the future, it is clear that enhanced functionality and efficiency through these technologies mean that businesses will remain competitive in a demanding market.
Eco-friendly Innovations
With increased awareness of environmental issues, the emphasis on sustainable practices in manufacturing has never been stronger. Innovations in eco-friendly materials and processes for sheet metal hem rollers are gaining traction. Manufacturers are now focusing on low-energy technologies and recyclable materials, which significantly reduce the carbon footprint associated with metalworking.
For instance, some companies are opting for hydraulic systems that consume less power and utilize eco-friendly hydraulic fluids. This change not only aligns with environmental standards but also saves costs in the long run.
Furthermore, employing renewable energy sources to power these machines is becoming a standard practice in progressive facilities. Solar panels and wind turbines are being integrated into the energy supply systems, which can cut down operational costs further. Therefore, businesses can adopt a greener approach while also enjoying the associated economic benefits.
In summary, the trends in technological advancements and eco-friendly innovations signify a future where sheet metal hem rollers are not only more efficient but also more aligned with global sustainability goals. As these industries evolve, embracing these changes will be crucial for staying ahead in an increasingly competitive landscape.
End
In wrapping up our exploration of sheet metal hem rollers, it becomes evident that these tools are not merely mechanical devices but rather indispensable instruments shaping the landscape of metalworking. Their design, functionality, and wide-ranging applications underscore their significance in numerous industries.
Summary of Key Points
- Design and Configuration: Hem rollers come in various types, including manual, electric, and hydraulic. Each type caters to different needs and requirements, making it essential for users to choose wisely based on their specific applications.
- Functionality: The process of rolling metal sheets to create hems is intricate. A well-designed hem roller ensures uniformity and precision, which is crucial for the structural integrity and aesthetic appeal of finished products.
- Applications Across Industries: From manufacturing to aerospace engineering, the relevance of hem rollers transcends sector boundaries. No matter the field, the ability to create seamless, strong edges on sheet metal is a common necessity.
- Benefits: Efficiency and versatility stand out as major advantages when employing hem rollers. The right roller can significantly enhance productivity while reducing waste during fabrication processes.
- Challenges: Despite their benefits, challenges persist. Material limitations and the technical skills required pose hurdles for certain users, thereby necessitating careful consideration and training.
- Future Trends: Ongoing technological advancements are set to revolutionize hem rollers. Innovations geared towards eco-friendliness not only appeal to the industry's growing consciousness around sustainability but also improve the overall efficiency and performance of these tools.
Final Thoughts
As we consider the journey and evolution of sheet metal hem rollers, it's important to recognize their dual role as pivotal tools in the metalworking realm and as examples of technological advancement. Continuous innovation ensures that these tools not only keep pace with contemporary demands but also pave the way for future developments in metal fabrication. Equipped with a deeper understanding of their design and applications, users can make better informed decisions when integrating hem rollers into their operations. Embracing these advancements can translate into tangible benefits in productivity and output quality, serving the interests of metalworkers and industries alike.
"In the hands of skilled operators, sheet metal hem rollers can be the difference between a mediocre product and one that excels in both quality and appearance."