Exploring Strain Gauge Materials for Engineering
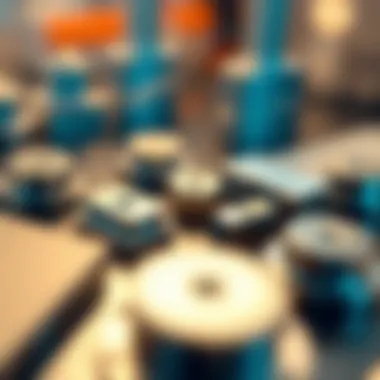
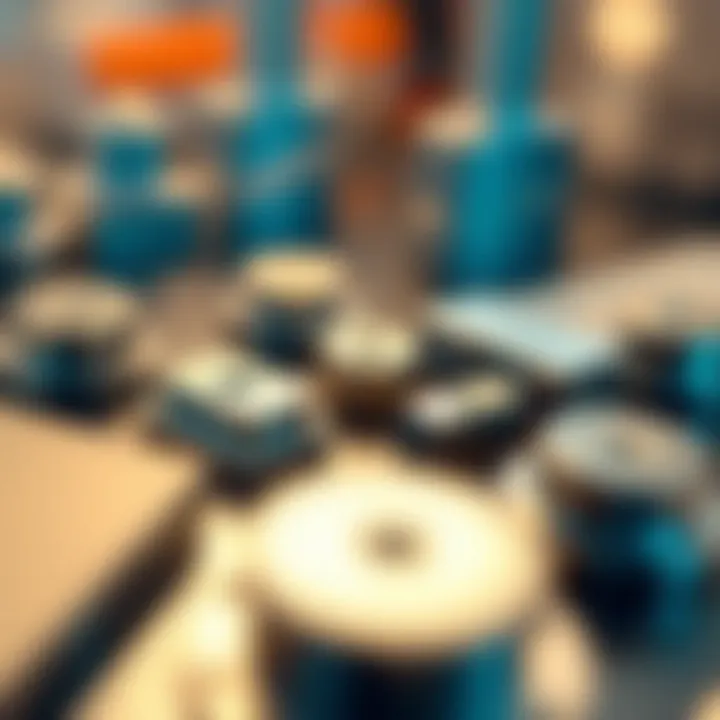
Intro
Understanding the materials that make up strain gauges is more than a technical endeavor; it touches various sectors—engineering, manufacturing, and material science. Strain gauges, when employed correctly, can provide precision measurements that are invaluable in a plethora of applications ranging from structural health monitoring to biomechanical assessments. As one dives into the realm of strain gauges, it is essential to dissect the mechanical properties, electrical characteristics, and material suitability for different engineering challenges.
This exploration opens doors to innovative applications, allowing professionals and researchers alike to deepen their understanding of both traditional and contemporary materials used in strain gauges. The evolution of materials utilized in these devices signals not just a change in technology, but a broader transformation occurs in how we measure and understand strain, deformation, and ultimately, structural integrity.
Key Concepts and Terminology
Definition of Key Terms
When discussing strain gauges, it’s beneficial to clarify some fundamental terms that lay the groundwork for further exploration:
- Strain: This refers to the deformation of materials when subjected to stress. It is typically expressed as a ratio of change in length to original length.
- Gauge Factor: This is a critical metric that indicates how sensitive a strain gauge is. A higher gauge factor means that the gauge produces a larger output for a given change in strain.
- Resistance Change: Often a key measurement, indicating how the resistance of a material will change in response to applied stress.
Concepts Explored in the Article
Throughout this discussion, various aspects related to strain gauge materials will be elaborated, including:
- The mechanical and electrical properties specific to materials selected for strain gauges.
- Comparative advantages and disadvantages of each material in practical applications.
- Criteria that engineers and researchers should consider when selecting gauges for different scenarios.
- Advancements in technology that impact material science, potentially re-shaping how strain measurement is approached.
"Understanding the material properties of strain gauges lays the foundation for their effective application in real-world scenarios."
Findings and Discussion
Main Findings
The exploration of strain gauge materials reveals a landscape rich in diversity yet complex in selection criteria. Different materials possess distinct mechanical properties, for instance:
- Metal Foils: These are widely used for their consistent results and reliability. Common choices include constantan and nickel-chromium alloys.
- Semiconductor Strain Gauges: They offer larger gauge factors compared to metallic counterparts. However, they can be sensitive to temperature changes and require careful handling.
- Polymer-based Strain Gauges: Emerging materials like conductive polymers are gaining ground due to their flexible nature and ease of integration with irregular surfaces.
Aspects such as temperature stability, sensitivity, and form factor play a pivotal role in determining the appropriate strain gauge material for a given application.
Potential Areas for Future Research
While substantial advancements have been made, potential areas for future research include:
- Developing hybrid materials that combine the mechanical advantages of different substances for enhanced performance.
- Investigating eco-friendly and sustainable alternatives that can lessen environmental impact while maintaining accuracy.
- Exploring nano-materials and their applications in highly sensitive strain measurement techniques.
Foreword to Strain Gauges
Understanding strain gauges is pivotal for grasping the nuances of modern engineering practices. These devices play a critical role in measuring stress and deformation in various structures and materials, enabling engineers and researchers to gather essential data. Without strain gauges, predicting failure modes in materials or ensuring the integrity of structures would pose a significant challenge. As the world increasingly relies on data-driven decision-making, the functionality that strain gauges provide becomes all the more critical.
Definition and Functionality
At its core, a strain gauge is a device that measures the amount of deformation or strain experienced by an object. When an object is subjected to external forces, it deforms; a strain gauge detects this deformation by altering its electrical resistance. This change in resistance correlates to the amount of strain being experienced. A common application for these devices is in force measurement—when a load is applied, the strain gauge converts the physical change into an electronic signal that can be quantified, allowing for precise readings.
"Strain gauges transform mechanical strain into quantitative electrical signals, marrying physics with engineering in a unique way."
Often made from conductive materials, strain gauges can be bonded to a variety of surfaces, enabling a wide range of applications—from monitoring the health of bridges to sensing pressure in aerospace components. Strain gauges can adapt to various measurement needs, necessitating a thoughtful discussion about their types and the materials they are composed of.
Historical Context
To appreciate the importance of strain gauges today, it’s useful to look back. The origins of strain measurement date to the early 20th century when scientists were exploring how materials react under stress. The concept of using electrical resistance to measure strain took form in the 1930s with the introduction of the first wire strain gauge by Edward E. Simmons and his collaborator. This innovation opened the door to modern strain gauge technology, evolving through decades of refinement.
In the 1950s and 60s, advancements continued as materials science evolved, allowing for the development of more sensitive gauges with varied application potential. Each decade has brought innovations—from the introduction of semiconductor strain gauges to polymeric versions, all providing enhanced responsiveness under different conditions. Today, strain gauges have solidified their position as indispensable tools in engineering, manufacturing, and scientific research, showcasing a remarkable journey of scientific inquiry and technological advancement.
Fundamental Principles of Strain Measurement
Understanding strain measurement is fundamental to various engineering and scientific disciplines. It’s not just about quantifying deformation, but also about how this deformation correlates to material properties, structural integrity, and overall performance in real-world applications. In strain gauges, strain measurement becomes pivotal for feedback in mechanical design and quality assurance.
Understanding Strain
Strain refers to the deformation experienced by a material when subjected to external forces. It is a measure of how much a given material distorts under load, relative to its original length. Mathematically, strain is defined as:
Strain Strain (ε) = Change in Length (ΔL) / Original Length (L0)
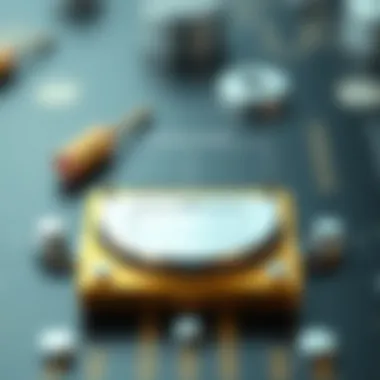
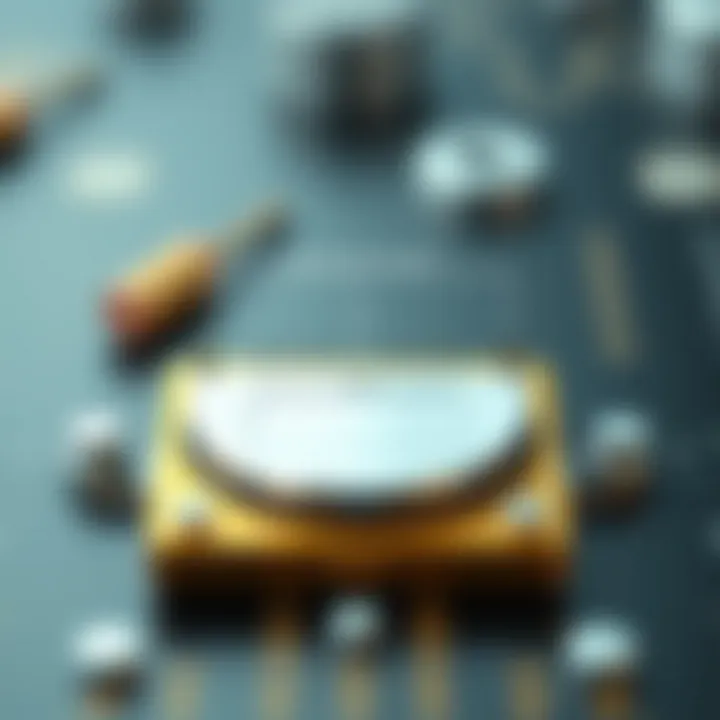
This formula highlights how materials behave under stress, informing engineers about whether a specific material can withstand certain loads without failing. Strain can be categorized into tensile strain, compressive strain, and shear strain, each representing different deformation modes. Grasping these differences is crucial, as it influences the choice of materials and strain gauge configurations employed in various applications.
Benefits of Understanding Strain
- Enables prediction of material failure.
- Informs design criteria for safety and performance.
- Assists in optimizing materials for specific applications.
When one understands how materials will respond to forces, it sets the stage for effective engineering processes. This knowledge allows for tailor-made solutions that not only perform but also ensure safety and efficiency.
Working Mechanism of Strain Gauges
Strain gauges operate on a straightforward yet effective principle—variation in electrical resistance due to strain. When a material deforms, the electrical resistance of the gauge also changes. This relationship is expressed in the form of the gauge factor, the sensitivity of the gauge, which is defined as:
Gauge Factor (GF) = (ΔR / R0) / (ΔL / L0)
Where ΔR is the change in resistance, R0 is the original resistance, ΔL is the change in length, and L0 is the original length. This relationship is the foundation for converting physical strain into measurable electrical signals.
Steps in Strain Gauge Operation
- Application: Strain gauge is adhered to the test specimen where monitoring is needed.
- Deformation: Once the specimen is subjected to a load, the strain gauge deforms along with it.
- Resistance Change: This deformation leads to a change in the resistance of the strain gauge.
- Signal Capture: The change in resistance is captured by a measuring system, often linked to data acquisition systems for further analysis.
Key advantages of this mechanism include high sensitivity to minute deformations, making them essential tools in diverse fields, ranging from civil engineering to biomedical applications. Proper understanding of how strain gauges convert mechanical principles into electrical readings significantly enhances their effectiveness in real-world use.
Key Materials Utilized in Strain Gauges
In the realm of strain measurement, the choice of materials is paramount. Different materials bring distinct characteristics to the table, which directly influences the accuracy, sensitivity, and robustness of the strain gauges. This section pulls the curtain back on the various materials used in constructing strain gauges, highlighting the essential elements, benefits, and considerations for each type. Whether it’s the reliability of metallic gauges, the heightened sensitivity of semiconductors, or the unique properties of polymers, the right material can make a world of difference in application performance.
Metallic Strain Gauge Materials
Common Metals in Use
Common metals used in strain gauge construction include copper, aluminum, and constantan. They possess essential conductive properties that facilitate accurate strain measurements. The significant aspect of these metals is their stability under various conditions. Constantan, for instance, is particularly noted for its resistance to changing temperatures and its linear response to deformation. This predictable behavior makes it a popular choice among engineers aiming for precision.
- Aluminum: Known for its light weight and excellent conductivity, aluminum is often favored when minimizing weight is a priority.
- Copper: While it offers superb conductivity, its susceptibility to oxidation can diminish performance over time, making proper treatment necessary.
In essence, the availability and mechanical characteristics of these metals contribute greatly to their widespread use in strain gauge applications.
Advantages of Metallic Gauges
One of the primary advantages of metallic gauges is their durability. They can withstand a range of mechanical stresses while providing reliable performance. This characteristic is crucial in environments prone to fluctuations, as metallic gauges maintain integrity over prolonged periods. Moreover, they are straightforward to manufacture, which often translates into lower production costs. However, one must note that while metallic gauges excel in certain areas, they generally exhibit lower sensitivity than semiconductor-based gauges.
- Cost Efficiency: The widespread availability of metals often keeps costs down, benefiting large-scale projects.
- Reliability: When it comes to stability under a range of environmental conditions, metallic gauges usually take the cake.
Overall, metallic strain gauges strike a balance between practicality and performance, making them a staple in many industrial applications.
Semiconductor Strain Gauge Materials
Characteristics of Semiconductor Gauges
Semiconductor strain gauges utilize materials like silicon or germanium. They are recognized for their ability to achieve greater sensitivity compared to their metallic counterparts. The main feature of these materials lies in their unique electrical properties that change dramatically with even slight deformations. This characteristic allows semiconductor strain gauges to detect smaller changes in strain, which makes them invaluable in high-precision applications.
Their nonlinear response can be a bit tricky to manage, but it’s precisely this sensitivity that elevates their status when precision is paramount.
Comparative Sensitivity
When discussing comparative sensitivity, semiconductor strain gauges emerge as a clear winner. They can detect changes with the slightest shifts in applied force, often leading to sensitivity levels ten times greater than metallic gauges. This allows for an enhanced level of detail during measurements, crucial for high-end applications like aerospace or medical devices.
- Amplification Ability: A smaller strain can lead to a significant output change, making them suitable for delicate environments.
- Complexity in Calibration: Despite their advanced capabilities, these gauges require meticulous calibration, which can complicate their implementation.
Just remember, while semiconductor gauges pack a punch in terms of sensitivity, their nuanced nature requires expert handling.
Polymeric Strain Gauge Materials
Properties of Polymer Materials
Polymeric materials like polyimide are gaining traction for use in strain gauges. Their primary characteristic is flexibility, which can adapt to different applications without losing functional integrity. This malleability allows for the creation of gauges that can be applied to curved or irregular surfaces seamlessly.
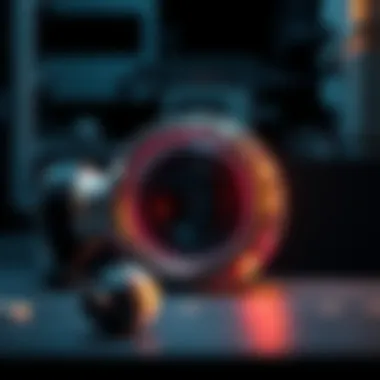
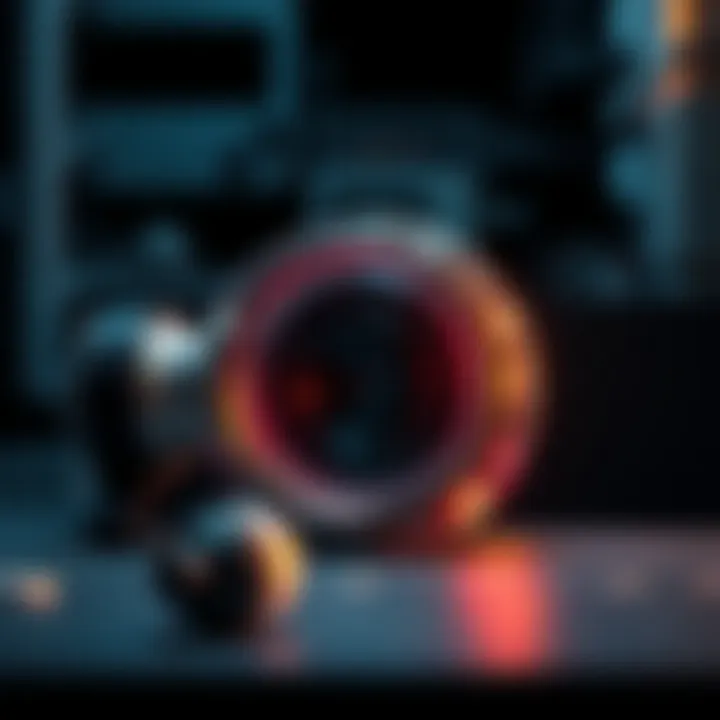
- Lightweight Nature: Being significantly lighter compared to metals and semiconductors, polymer gauges excel in applications where weight-saving is crucial.
- Chemical Resistance: Polymer materials exhibit good resistance to various chemicals, making them suitable for hostile environments.
However, it’s important to bear in mind that while polymers excel in several areas, their mechanical strength might not match that of metals.
Applications of Polymeric Strain Gauges
Polymeric strain gauges find a niche in applications where traditional materials may falter. For instance, they are well-suited for wearable technology due to their conformability and lightweight design. This opens doors to applications in the medical field, where monitoring patient movement without discomfort is a priority.
- Versatile Use: Their adaptability means they can be utilized in diverse settings, from biomedical devices to structural health monitoring.
- Cost Considerations: While potentially more expensive than metallic options, the benefits in certain applications often justify the investment.
Comparative Analysis of Strain Gauge Materials
The comparative analysis of strain gauge materials forms a pivotal component of this article. It serves to distinguish how different materials perform under various conditions, enabling engineers and researchers to make informed choices tailored to their specific applications. Understanding the trade-offs between strength, sensitivity, temperature stability, and environmental resistance is essential when selecting a suitable strain gauge. This analysis not only elucidates the pros and cons of each material type but also highlights thier practical implications in real-world scenarios.
Strength vs. Sensitivity
When it comes to strain gauges, the interplay between strength and sensitivity often emerges as a critical consideration. Strength refers to a material's ability to withstand external loads without undergoing permanent deformation, while sensitivity measures the gauge's responsiveness to changes in strain. The delicate balance between these two attributes is vital, especially in applications subject to fluctuating mechanical loads.
For instance, metallic strain gauges typically boast high strength, making them suitable for heavy-duty applications. However, they may be less sensitive relative to their semiconductor counterparts, which, although fragile, offer outstanding sensitivity. This discrepancy becomes crucial in precision engineering tasks or aerospace applications where microstrain needs to be detected accurately.
Some practical considerations include:
- Application Requirements: For structural health monitoring, a gauge with high sensitivity is often prioritized.
- Measurement Environment: In high-stress environments, strength might outweigh sensitivity as long-term durability is a priority.
Temperature Stability
Temperature fluctuations can wreak havoc on strain measurements, making temperature stability a critical factor in the selection of strain gauge materials. Different materials exhibit varying levels of thermal expansion, which can lead to measurement inaccuracies if not properly addressed.
Metallic strain gauges generally perform well in diverse temperature ranges but can still experience shifts in their resistance due to thermal variations. Semiconductor gauges, on the other hand, provide superior sensitivity but may exhibit greater temperature drift, which requires compensation.
Consider these points:
- Compensation Techniques: Using temperature compensation methods can mitigate potential inaccuracies from material expansion.
- Material Selection: Choosing materials known for better thermal stability, such as some specialized alloys, can improve overall performance in temperature-variable environments.
In sum, selecting strain gauges that maintain their operational stability across expected temperature ranges is vital in ensuring accurate measurements over time.
Environmental Resistance
Environmental factors play a considerable role in the long-term performance of strain gauges, rendering environmental resistance an indispensable aspect of material selection. Strain gauges can be exposed to a variety of harsh environmental conditions, including moisture, corrosive substances, and extreme temperature changes.
The resilience of a strain gauge material directly correlates to its longevity and reliability in the field. For instance, polymeric strain gauges can offer remarkable resistance to corrosion and moisture, making them ideal for applications in humid or chemically aggressive environments. Conversely, metallic gauges might succumb to oxidation in such settings without proper encapsulation.
Key considerations include:
- Encapsulation Technology: Utilizing barriers or coatings can significantly enhance durability against environmental stresses.
- Application Suitability: In undertaking projects like offshore structures, selecting materials with superior environmental resistance can be crucial to ensure consistent data.
Overall, engineers need to employ a thorough assessment of environmental factors, guiding them in selecting a material that can endure the specific conditions the gauge will face during its operational life.
Selecting the Right Strain Gauge Material
Choosing the most suitable strain gauge material is a pivotal aspect of achieving precise measurements in many engineering applications. This selection impacts not only the sensitivity and accuracy of the measurements but also the overall performance of the system where strain gauges are employed. Factors such as application requirements, environmental conditions, and mechanical loads dictate the right material. By understanding these elements and how they interact, engineers can make informed decisions that maximize the longevity and efficacy of their strain measurement systems.
Application-Specific Considerations
Mechanical Loading Conditions
Mechanical loading conditions refer to the types of stresses and strains the strain gauge will need to endure. These can vary widely, encompassing tension, compression, and shear forces. Understanding these conditions is crucial as it directly impacts the choice of material.
A key characteristic of mechanical loading is dynamic versus static loads. For example, in scenarios where frequent load changes occur, a strain gauge must demonstrate not only sensitivity but also resilience. This is why metallic strain gauges are often favored for heavy machinery applications; they provide reliable performance under continuous stress and have well-documented linearity in their response to load changes.
The uniqueness of mechanical loading conditions lies in their variability. Some gauges might excel under specific loading scenarios but falter under others, leading to incorrect readings and potential failures in critical applications. Therefore, selecting a gauge material that aligns with these loading conditions ensures accurate data collection and longevity of the strain gauge itself.
Environmental Factors
Environmental factors, such as temperature, humidity, and exposure to corrosive substances, significantly impact the performance of strain gauges. It’s essential to consider these elements when selecting materials for specific applications. Certain materials are more resistant to environmental stressors than others and can maintain accuracy even in extreme conditions.
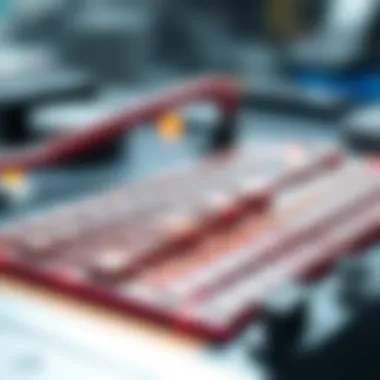
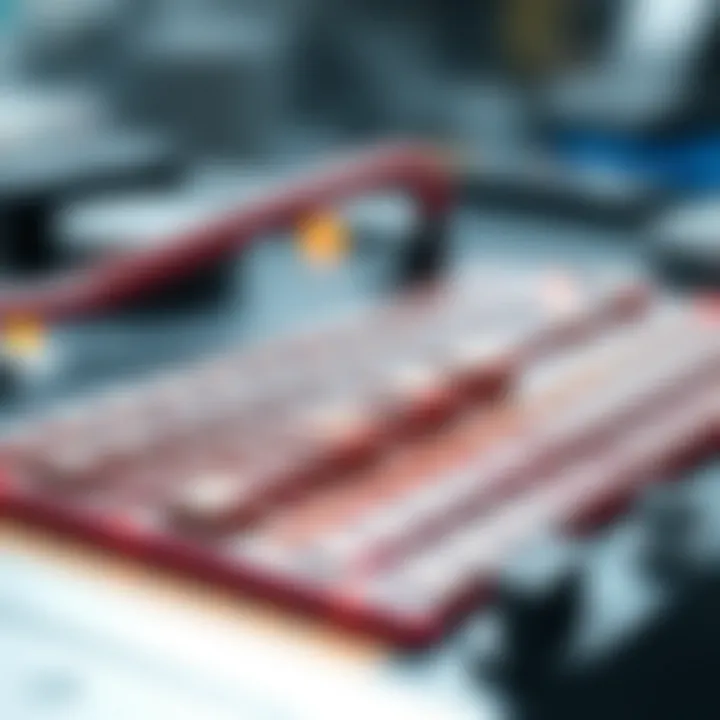
One of the most significant aspects of environmental considerations is temperature stability. Temperature fluctuations can alter the mechanical properties of materials, affecting their performance. For instance, semiconductor strain gauges are highly sensitive but can become unreliable outside a specific temperature range. On the other hand, metallic gauges often perform better across a broader spectrum of environmental conditions, making them a more attractive choice in industrial settings where conditions can change dramatically.
The major takeaway here is that understanding environmental influences allows for a more informed choice of strain gauge material, thus improving measurement reliability in diverse conditions.
Practical Choice Guidelines
When faced with the myriad options available for strain gauge materials, adhering to a set of practical guidelines can simplify the selection process. Here are several strategies to consider:
- Understand Your Application: Define the specific application requirements in detail; knowing if the gauge will encounter high-speed loads or extreme temperatures will guide your choice.
- Assess the Environment: Evaluate the working environment, as this can dictate the material's durability and reliability.
- Milestones on Performance: Look for gauges that have established performance metrics according to your application, ensuring they meet industry standards.
- Cost vs. Accuracy: Weigh the balance between budget and precision; sometimes, opting for a slightly pricier but more accurate gauge pays off in the long run.
"Selecting the right material is always a balancing act between the ideal conditions and the practical limitations of the application."
Choosing the perfect strain gauge material can be a daunting task, but taking these considerations into account can lead one to higher accuracy and reliability in measurements.
Advancements in Strain Gauge Technology
The field of strain gauge technology is evolving at a rapid pace, driven by innovations in materials science and engineering practices. As we explore advancements in this area, we discover critical aspects that enhance the performance, accuracy, and utility of strain gauges across various applications. Advances are not just limited to the materials themselves; they encompass innovative manufacturing processes and integration with modern technologies. These enhancements open doors for more precise measurements in fields ranging from structural engineering to biomedical applications.
Emerging Materials Research
Nanomaterial Applications
Nanomaterials are revolutionizing strain gauge technology in profound ways. These materials generally possess heightened strength-to-weight ratios, enabling extremely sensitive strain measurements while reducing the overall mass of the gauge. For instance, carbon nanotubes and graphene-infused materials are gaining traction for their exceptional tensile strength and electrical conductivity.
One of the most notable characteristics of nanomaterial applications is their remarkable ability to increase sensitivity. This heightened responsiveness makes them ideal for applications where minute changes in strain need to be detected. Consequently, they lend themselves well to usage in advanced aerospace components, where structural integrity is paramount.
However, these sophisticated materials are not without drawbacks. The fabrication process might be more complex and expensive than traditional methods, posing questions about scalability and cost-effectiveness. Yet, the unique feature of nanomaterials—capable of yielding real-time data while being remarkably lightweight—positions them favorably for future developments in strain gauges, making them a popular choice in research circles.
Biocompatible Gauges
The leap towards biocompatible gauges represents another significant advancement in strain gauge technology. These gauges are specifically designed to interact harmoniously with biological tissues, making them indispensable in medical applications. Their primary characteristic—their ability to be safely integrated into the human body—highlights their importance in fields like prosthetics and surgical monitoring.
One defining feature of biocompatible gauges is their low toxicity, which allows for prolonged implantation without adverse effects. This makes them an attractive option for long-term monitoring purposes, such as tracking the strain on orthopedic implants or measuring pressure in blood vessels.
Nevertheless, challenges persist with biocompatible materials, particularly regarding their mechanical durability and stability over time once inside the body. Strain gauges must withstand various forces and environmental conditions while maintaining performance, which can be a tricky balance. Yet, their burgeoning use in real-world medical scenarios underscores their potential and appeal.
Innovative Fabrication Techniques
In addition to advancements in materials, innovative fabrication techniques have transformed the landscape of strain gauge production. New methods allow for the creation of gauges that are not only more reliable but also offers enhanced customization possibilities. Techniques such as 3D printing hold promise, enabling more complex geometries and designs that align precisely with specific measurement needs.
These techniques can reduce manufacturing costs while improving the speed of production, crucial factors in today’s fast-paced market. Moreover, with advanced software and modeling tools, developers can simulate how these new designs perform under various conditions, thus refining their end product before the actual manufacturing process even begins.
"With the integration of innovative fabrication techniques, we can create strain gauges that were previously unimaginable, expanding the potential for strain measurement in numerous fields."
Finale
The conclusion serves as a pivotal touchpoint in this exploration of strain gauge materials. It synthesizes the intricate details discussed throughout the article, emphasizing the criticality of choosing the right strain gauge materials tailored to specific applications. This final section not only encapsulates the key findings but also opens the door to future considerations and advancements in the field.
In the realm of engineering and technology, strain gauges play an instrumental role in the accurate measurement of structural deformation. Hence, understanding the various material properties and their associated applications becomes paramount. Appropriate selection not only enhances measurement accuracy but also ensures reliability under varying operational conditions, ultimately impacting the design and functionality of engineering projects.
The benefits of using advanced strain gauge materials extend beyond mere technical performance. Industry professionals, researchers, and educators gain invaluable insights from these materials, fostering a deeper understanding of material science and its capability to influence the development of innovative solutions.
Future Directions in Strain Gauge Materials
Implications for Industry
Future directions in strain gauge materials are a testament to how innovation can redefine industry standards. The implications for industry are vast, particularly as new materials emerge with enhanced properties such as increased sensitivity and durability. One of the primary characteristics that makes these materials stand out is their ability to operate effectively in diverse environments.
For instance, the use of graphene-based strain gauges is gaining traction due to their exceptional mechanical strength and electrical conductivity. This unique feature not only provides a high sensitivity level but also positions them as ideal candidates for applications where precision is non-negotiable, such as aerospace and civil engineering.
However, the integration of these advanced materials can pose some challenges. For instance, while they can significantly improve performance, the cost and complexity of implementation can be dissuading factors. Balancing these trade-offs is key to leveraging the advantages while mitigating potential setbacks in the industry.
Impact on Research and Development
The impact of strain gauge materials on research and development is equally profound. As academics and innovators push the boundaries of material science, there's a growing emphasis on developing biocompatible strain gauges for medical applications. Their ability to interface directly with biological systems is a crucial characteristic, allowing for real-time monitoring of health metrics.
The unique feature of biocompatibility in strain gauge technology not only underpins a new era in medical diagnostics but also enhances the scope of human-machine interaction. This new wave of research contributes immensely to the overall goal of advancing healthcare technology.
Though, as with any emerging technology, careful attention must be paid to the regulatory hurdles that often accompany new materials in healthcare. The balance between innovation and compliance remains a pressing challenge for researchers in this sector.
"The path of innovation is seldom linear; it requires navigating through challenges and seizing opportunities to advance technology."