Types of Rock Crushers and Their Industrial Applications
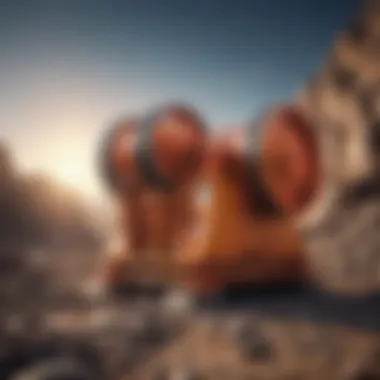
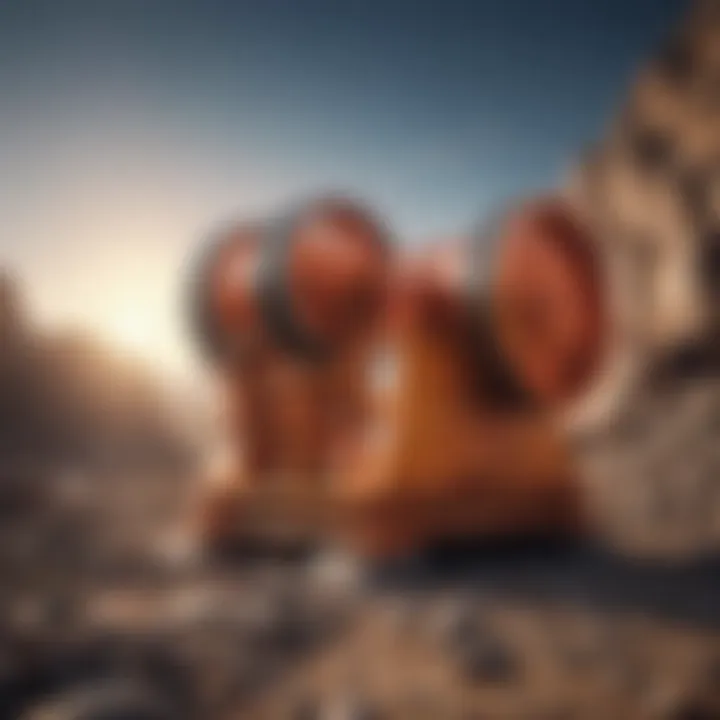
Key Concepts and Terminology
Understanding the landscape of rock crushers necessitates clarity on certain key concepts and terminology. These tools, integral to the mining and construction sectors, are based on various operational mechanisms, each tailored to meet specific application needs.
Definition of Key Terms
- Rock Crusher: A machine designed to reduce large rocks into smaller rocks, gravel, or rock dust. These crushers facilitate the process of material handling and can significantly impact resource management.
- Jaw Crusher: This type uses a pair of opposing jaws to crush rock, with one jaw fixed while the other oscillates. It's known for its ability to handle larger pieces of material.
- Cone Crusher: Characterized by its conical shape, this crusher employs a gyrating spindle, which crushes material against a static wall. They excel in producing finer materials and are favored in secondary and tertiary crushing stages.
- Impact Crusher: Utilizing high-speed impact to break materials, these crushers are prominent for their capacity to produce irregular shapes and are often found in recycling operations.
Concepts Explored in the Article
This article delves into distinct kinds of rock crushers including jaw, cone, and impact crushers, examining their operational intricacies and suitability across various industries. The discussion outlines not only their functions but highlights the advantages and disadvantages associated with each type. Understanding these concepts helps in selecting the right machinery for specific tasks, ultimately enhancing efficiency and quality in material processing.
Findings and Discussion
Main Findings
- Operational Mechanisms: Each type of rock crusher operates uniquely. For instance, jaw crushers are robust and well-suited for primary crushing, while cone crushers are ideal for achieving a refined output with consistent sizes.
- Applications Across Industries: Different sectors utilize various crushers based on specific requirement. Mining operations predominantly favor jaw and cone crushers, whereas construction and recycling often employ impact crushers due to their efficiency in processing mixed materials.
- Material Quality and Efficiency: The choice of rock crusher can directly influence the quality of the output material. A more efficient machine not only improves throughput but also reduces waste.
Potential Areas for Future Research
Research into advanced rock crushing technologies can lead to better energy efficiency and reduced operational costs. Additionally, exploring automation in rock crushing might streamline processes, enhance safety, and further improve material output.
"Choosing the right rock crusher is crucial; it's not just about size, but about application and efficiency."
Intro to Rock Crushers
Rock crushers hold a pivotal spot in the realm of construction, mining, and recycling industries. These machines are integral for the effective processing of a multitude of materials such as stone, gravel, and concrete, transforming them into finer particles for varied uses. The focus of this article revolves around demystifying the various types of rock crushers, detailing their mechanisms, applications, and overall importance in industrial settings.
The Importance of Rock Crushing in Industry
Rock crushing plays a crucial role in several sectors beyond basic material processing. For instance, in construction, the granularity of the crushed material affects concrete quality, leading to durability and resilience of structures. In mining, efficient crushing can significantly impact the extraction of valuable minerals and metals. Moreover, with the rising emphasis on recycling, rock crushers facilitate the processing of concrete and asphalt, allowing materials to be reused and reducing landfill waste. The effective operation of these machines not only ensures higher productivity but also contributes to sustainability efforts across industries.
Overview of Crushing Processes
Crushing is a process that involves the reduction of large particles into smaller fragments. The choice of the crushing method depends on the material to be processed and the desired output size. Generally, the main crushing processes include:
- Primary Crushing: This initial stage focuses on breaking down large rocks into more manageable sizes. Common equipment used includes jaw crushers and gyratory crushers, which can handle heavier loads.
- Secondary Crushing: Once the material is sufficiently reduced, secondary crushers such as cone crushers and impact crushers take over, producing finer particles.
- Tertiary Crushing: For even smaller aggregate sizes, the tertiary stage utilizes more specialized tools, often aimed at creating sand-like materials.
The overall crushing circuit is orchestrated to optimize efficiency and material quality. By understanding the processes involved, one can make informed choices about the type of rock crusher suitable for a particular application, ensuring that operational goals are met systematically.
Jaw Crushers
Jaw crushers serve as fundamental tools in various material processing industries, primarily due to their robust design and effectiveness in crushing larger pieces of rock into smaller fragments. Their significance in this article stems from their popularity and common use in mining, construction, and recycling applications. As a versatile machine, they can handle a wide range of materials, from the hardest granite to softer minerals, making them a well-suited choice for many operations. Understanding jaw crushers is crucial not just for selecting the right crusher but also for optimizing the efficiency and quality of material being processed.
Working Principle of Jaw Crushers
Jaw crushers operate on a simple principle: a fixed and a moving jaw work together to crush material. The fixed jaw remains stationary while the moving jaw oscillates back and forth. This motion allows the material to be fed into the crushing chamber and squeezed between the jaws. As the moving jaw pushes the material down, it is progressively crushed until it falls through the discharge opening.
The design of jaw crushers enables a crushing ratio typically ranging between 4:1 to 6:1, meaning they can reduce material size efficiently. One critical aspect of this mechanism is the toggle plate, which not only maintains the required angle between the jaws but also acts as a safety device to prevent damage from uncrushable material.
Applications of Jaw Crushers
Jaw crushers find a variety of applications across different industries, demonstrating their adaptability. Here’s a brief overview of their most common uses:
- Mining: Used to process boulders and ores before further refinement. This includes crushing gold, copper, and iron ores.
- Construction: Essential in preparing building materials like concrete, brick, and asphalt aggregate.
- Recycling: Efficient at crushing waste materials, such as old concrete and asphalt, facilitating the reuse of materials.
- Industrial Applications: These may involve crushing larger pieces into manageable sizes for laboratory testing or production of smaller aggregates.
"Jaw crushers have proven to be reliable and robust machines, offering significant advantages in size reduction processes across various sectors."
Advantages and Disadvantages
Like any machinery, jaw crushers have their pluses and minuses. Here’s a closer look:
Advantages:
- High Efficiency: Capable of crushing tough materials with minimal energy consumption.
- Ease of Maintenance: Less complex compared to other types, leading to lower operational costs.
- Durability: Built to withstand heavy loads, resulting in long service life.
Disadvantages:
- Limited Material Size: Not suitable for extremely hard or sticky materials, which can lead to inefficient operation.
- Size and Weight: Larger footprint requiring more space, making transport and installation challenging.
- Potential for Over-crushing: If not monitored properly, smaller particles may further be reduced, leading to loss of material.
In summary, jaw crushers play a crucial role in the processing of various materials, making them a key component of many industries. Their operating principle, combined with versatile applications, makes them particularly valuable even amidst some operational drawbacks.
Cone Crushers
Cone crushers serve a pivotal role within the rock crushing landscape, especially in applications where efficient material handling, size reduction, and cost-effectiveness are crucial. Their design, which features a conical head in a fastened bowl, makes them suitable for tackling a range of materials from hard rock to compressible substances.
The strength of cone crushers lies in their unique crushing mechanics and versatility in various applications. These machines are known for their high throughput, making them a favored choice in mining and quarry operations, where large volumes of material need to be processed efficiently. In the complex world of material processing, understanding the ins and outs of cone crushers is fundamental for optimizing operations and ensuring quality output.
Mechanics of Cone Crushers
The functioning of cone crushers is centered around a very straightforward yet effective concept. At their core, they employ a single or multiple cone designs that rotate within a bowl. The material is fed into the top of the machine, and as the inner cone spins, it exerts pressure on the material, compressing and breaking it down into smaller sizes. This can be seen as a two-step process:
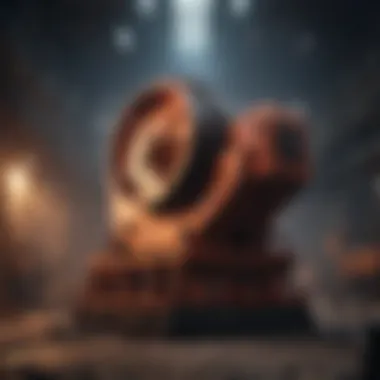
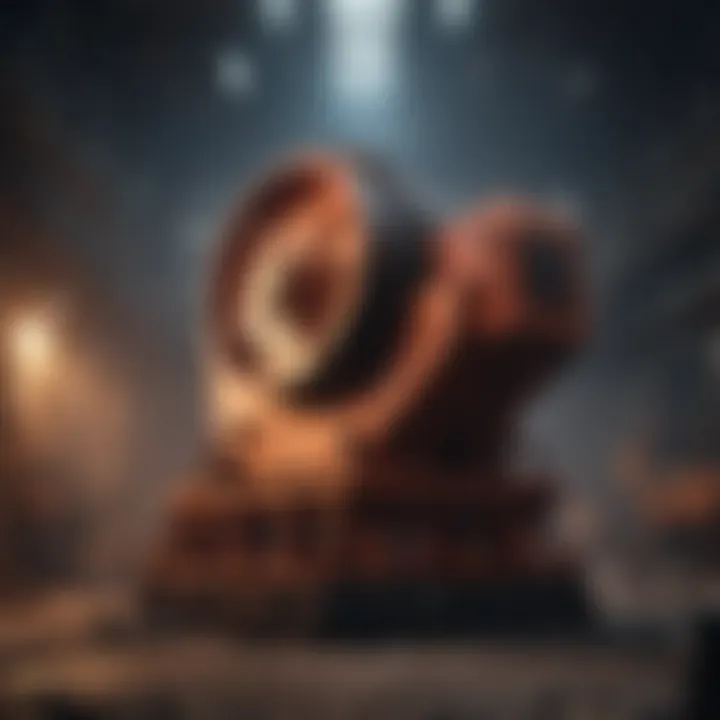
- Compression: As the material passes between the cone and the bowl, it experiences increasing pressure, which increases with the depth of the material.
- Shearing and Impact: The combined action of compression and rapid rotation creates forces that help in both breaking and reshaping the feed material.
This mechanical design allows for a steady flow of material, optimizing performance and reducing wear on parts that often plague other crushing methods.
Typical Use Cases for Cone Crushers
Cone crushers find their applications in varied fields, primarily due to their ability to handle different material types effectively. Here are a few typical scenarios:
- Mining Operations: Cone crushers are extensively used in mining, where their capability to crush large rock formations into manageable sizes is critical. They help in the extraction of metals from ore.
- Quarrying: In quarry settings, cone crushers produce aggregates, particularly for construction, where gravel and crushed stone are crucial.
- High-Quality Sand Production: Certain models are specially designed to produce high-grade sand, essential for cement production or asphalt mixing.
- Recycling: With growing environmental concerns, cone crushers are increasingly adapted to process recycled materials, like asphalt and concrete, supporting sustainable practices in construction.
Each application highlights the relevance of cone crushers, illustrating their capability to adapt to a multitude of processing demands.
Comparative Analysis: Cone vs. Jaw Crushers
When it comes to choosing between cone and jaw crushers, the decision often hinges on the specific needs of an operation. Below is a comparative analysis highlighting key differences:
| Feature | Cone Crushers | Jaw Crushers | | Crushing Mechanics | Uses compression and shearing forces. | Relies on compressive forces alone. | | Material Type | Suitable for medium to hard materials. | Best for larger, coarse particles. | | Output Shape | Provides more cubical-shaped product. | Produces coarse, angular fragments. | | Operational Cost | Generally higher due to complexity. | Often lower, but efficiency varies. | | Maintenance | More parts that may require change. | Simpler design, easier to maintain. |
"A well-chosen crusher can be the difference between profit and loss in material processing operations."
Whether through cone crushers or other types, the effective processing of materials is a cornerstone of numerous industries, making the understanding of these machineries essential for anyone engaged in material handling.
Impact Crushers
Impact crushers are a critical part of the rock crushing machinery landscape. Their ability to efficiently break down rocks and other materials makes them invaluable across various industries such as construction, mining, and waste management. This section will delve into the intricate workings of impact crushers, explore their multiple applications, and examine their unique strengths and weaknesses.
Understanding Impact Crushing Mechanisms
At the heart of impact crushers lies a relatively simple yet effective mechanism that relies on high-speed impact to break materials apart. The primary component consists of a rotor that spins at high velocities, usually between 900 to 1200 revolutions per minute. When materials enter the crushing chamber, they are struck by the hammers attached to the rotor, which generates a powerful impact.
Often, the resulting fragments are further accelerated as they collide with the impact plates located on either side of the chamber. This dual-action helps produce more finely crushed products. It’s noteworthy that there are two main types of impact crushers: horizontal shaft impactors (HSI) and vertical shaft impactors (VSI). Each type has its own specific design features tailored for particular applications, such as HSI being ideal for softer materials and VSI excelling in shaping and grading.
Industry Applications of Impact Crushers
Impact crushers find their footing in a diverse range of industries. Here are some key applications:
- Construction: They are extensively used to produce aggregates such as sand, gravel, and crushed stone for various construction projects.
- Mining: In this field, impact crushers often handle the primary or secondary crushing of ores, ensuring material is adequately size-reduced for further processing.
- Recycling: They are instrumental in processing materials like asphalt and concrete, allowing companies to recover valuable resources from waste.
- Cement Production: Impact crushers serve to crush raw materials to a suitable size before entering the kiln.
The versatility of impact crushers not only improves operational efficiency but also supports sustainability efforts by enhancing recycling processes.
Strengths and Limitations
Like anything in this world, impact crushers come with their own sets of advantages and challenges:
Strengths:
- Versatile Performance: Impact crushers can handle a wider variety of materials compared to other types, making them favorite choices in mixed material situations.
- High Reduction Ratios: They achieve significant size reduction, which can lead to less need for secondary crushing down the line.
- Low Operational Cost: Once operational, these machines require less frequent maintenance, reducing overall costs for businesses.
Limitations:
- Wear and Tear: The high-speed impacts can lead to quicker wear of the hammers and plates, necessitating more frequent replacements compared to other crushing equipment.
- Material Constraints: They perform better with friable and brittle materials. Struggling with more ductile or hard materials can lead to a decrease in efficiency.
- Dust Generation: The process can result in substantial dust creation, raising environmental concerns and necessitating dust control measures.
"Understanding the balance between advantages and limitations, operators can make informed choices to integrate impact crushers into their material processing strategies effectively."
Roll Crushers
Roll crushers serve a significant role in the world of material processing. Their design and operation factor into various stages of production across industries like mining, aggregate, and recycling. These crushers excel at producing a relatively uniform output product while minimizing the creation of fines during the crushing process. As the demand for efficient resource utilization and material quality rises, understanding roll crushers becomes imperative for professionals and educators alike.
The simple yet effective mechanism of roll crushers is what draws industries towards them. They typically consist of two heavily-built cylindrical rolls that rotate towards each other, effectively crushing the material between them. This design allows for a steady, controlled reduction of the material size, making it versatile for different applications.
Principles of Roll Crushing
The principle behind roll crushing is straightforward yet powerful in its simplicity. As the two rolls rotate, materials are fed between them. A combination of pressure and shear forces is applied, reducing the material size. The characteristic motion creates a specific size distribution of the finished product.
Roll crushers can be configured in various ways, such as:
- Single roll: One roll crushes the material against a fixed plate, often used for softer materials.
- Double roll: Two rolls crush materials against each other for more effective size reduction.
- Triple and four-roll designs: Utilized for tougher materials where additional size reduction is needed.
These configurations can also involve different ratios of speed, allowing for adaptability based on the material properties.
Applications in Material Processing
Roll crushers find their place in several significant applications across industries. Here are some of the key uses:
- Mineral processing: They effectively size minerals and ores like coal and gypsum, preparing them for further processing.
- Construction aggregates: Roll crushers help produce uniform gravel and stone products from larger rocks, ensuring a standard size for construction purposes.
- Recycling: In recycling facilities, they break down materials like glass and plastic, paving the way for reclamation processes.
One notable benefit of roll crushers is their capability to handle sticky materials. Their design minimizes blockages, making them a reliable choice when dealing with challenging materials.
Pros and Cons of Roll Crushers
Like any equipment, roll crushers come with their strengths and weaknesses that deserve a closer look:
Pros
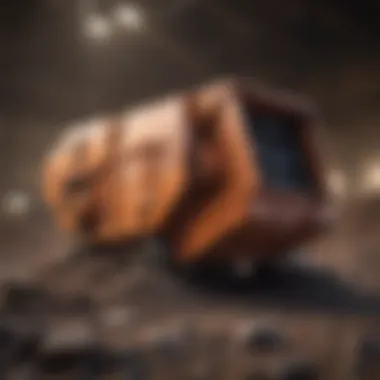
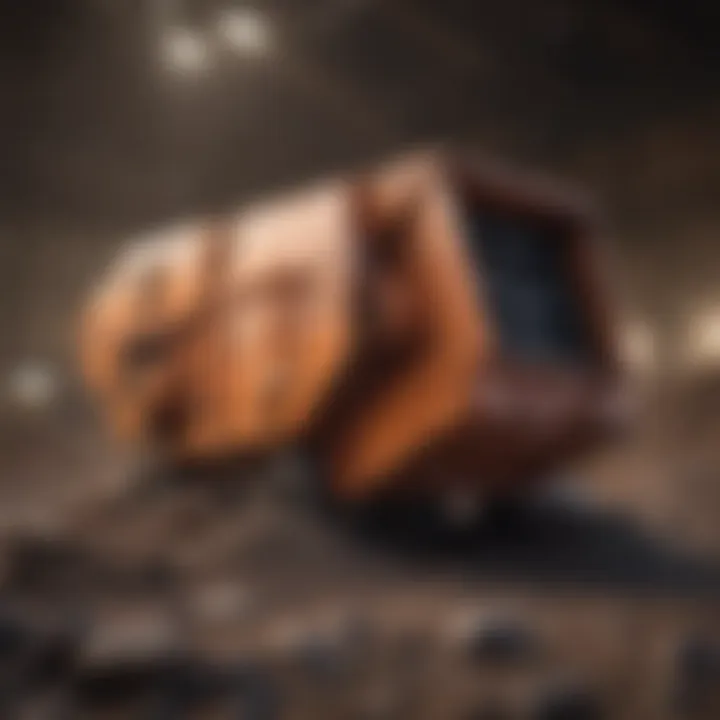
- Low operational costs: They require less energy due to their efficient crushing mechanism.
- Gentle on materials: Roll crushers can crush without excessive fines, preserving more of the desired particle size.
- Versatility: They can handle a wide range of materials with varying properties.
Cons
- Limited reduction ratio: Compared to other crushers, roll crushers may not reduce large material sizes to an extremely fine output.
- Wear and tear: The rolls can experience significant wear over time, particularly with harder materials.
"The key to successful material processing often relies on choosing the right tool for the job. Roll crushers represent a balanced approach to achieving efficiency while maintaining material integrity."
Understanding the operational principles, applications, and advantages of roll crushers allows stakeholders to appreciate their importance in modern industry. As advances in technology continue to reshape material processing, staying informed about roll crushers and their capabilities will enable better decision-making and optimal resource management.
Vertical Shaft Impact (VSI) Crushers
Vertical Shaft Impact (VSI) Crushers have gained attention for their unique operating principles and versatility in various industrial applications. In the realm of rock crushing, these machines are invaluable due to their ability to create high-quality crushed materials that meet stringent standards. Their role in sectors like construction, mining, and recycling is crucial, as they offer effective solutions to material processing without compromising on quality.
VSI Mechanism and Design
VSI Crushers operate on a principle distinct from traditional crushers. Instead of applying pressure as with jaw or cone crushers, a VSI utilizes high-speed rotor technology to accelerate materials before impacting them against a hard surface. This can be seen in the centrifugal force generated by the rotor, which allows the material to continuously hit against a stationary anvil. This violent collision breaks down the material into fine aggregate while preserving desired shapes and consistency.
The design often features a modular configuration, simplifying maintenance and adjusting parts. This modularity is beneficial for users needing to replace specific components without overhauling whole systems. It also emphasizes adaptability in production, allowing operators to switch between different material types with ease.
VSI Applications Across Industries
The ability of VSI Crushers to create exceptionally fine aggregates makes them indispensable across multiple industries:
- Construction: In constructing roads or buildings, high-quality aggregates are essential. VSI outputs sands and gravels with consistent shapes, suited for making concrete and asphalt.
- Mining: Often used post-primary crushers, they refine materials into desirable formats to enhance extraction processes further. They can efficiently handle ores, ensuring a high recovery rate with minimal degradation.
- Recycling: VSI technology is pivotal in processing recycled materials. They can handle concrete scraps or asphalt efficiently, breaking them down into reusable aggregates while minimizing environmental impact.
Analyzing VSI Effectiveness
The effectiveness of VSI Crushers can be evaluated through various metrics, notably efficiency, product quality, and operational costs. One of their paramount advantages is their capacity to generate cubical-shaped end products, which is often desired in construction applications. Technical data frequently supports this, showing that VSI-produced aggregates often have higher strength characteristics than those produced by other crushing methods.
"When it comes to the type of final product, VSI crushers stand out. They deliver aggregates that not only meet but often exceed industry standards. This factor can significantly impact overall project success, especially in construction where material quality is king."
However, as with any technology, there are considerations to be mindful of. The initial investment and operational costs might be higher than traditional crushers, but the long-term benefits, including reduced material loss and refined product quality, often outweigh these costs. Additionally, maintaining operational a VSI requires monitoring wear parts due to the wear and tear from high-speed operations.
In summary, Vertical Shaft Impact Crushers play a pivotal role in modern rock crushing strategies, balancing quality and efficiency in a way that resonates throughout various industrial sectors.
Specialized Crushers
Specialized crushers play a critical role in the intricate landscape of material processing. Their unique designs target specific needs in various industry applications, allowing for tailored solutions that enhance operational efficiency.
Rock crushers, while effective as general tools, may not always meet the complex demands of every project. Enter specialized crushers, which include Hammer Mills, Gyratory Crushers, and Mobile Crushers. Each has evolved to address particular challenges, optimizing the crushing process for different materials.
Utilizing these specialized crushers not only improves material quality but also contributes to a more sustainable approach in development. Understanding their values and operational nuances is essential for industries looking to maximize output while minimizing costs.
Hammer Mills and Their Role
Hammer mills are a unique type of crusher that uses high-speed rotating hammers. They break down materials into smaller, more manageable sizes. A primary feature of hammer mills lies in their versatility; they can process a range of materials, from soft biomass to harder substances. This flexibility makes them invaluable in recycling operations, agricultural applications, and even in certain mining settings.
Key advantages of using hammer mills include:
- Fine Output: They can produce a very fine material that other crushers may struggle with.
- Low Operational Costs: The maintenance on hammer mills is relatively low, leading to cost savings over time.
- Energy Efficiency: They can be designed to use less power, making them an environmentally friendly option in many scenarios.
However, hammer mills aren’t without drawbacks. They can be limited in the size of materials they can effectively process, and frequent use of materials that are comparatively hard might require more frequent maintenance or replacement of hammers.
Gyratory Crushers: An Overview
Gyratory crushers represent another specialized type designed chiefly for primary crushing. Their conical shape provides a unique crushing arrangement, which allows for effective breaking of large rocks into smaller aggregates. With the ability to handle a significant throughput, gyratory crushers are commonly employed in mining, quarrying, and even large-scale recycling operations.
Here are some key points regarding gyratory crushers:
- High Capacity: They can process large volumes of materials quickly.
- Robust Design: Built to withstand the challenges posed by the toughest materials.
- Adjustable Settings: Some models allow operators to adjust the size of the output, which adds a layer of versatility to their operation.
On the downside, the initial investment for a gyratory crusher can be steep. They can also require substantial space and maintenance due to their size and complexity.
Mobile Crushers: Flexibility in Application
Mobile crushers have changed the game when it comes to rock crushing. Unlike stationary models, they offer the benefit of flexibility, allowing operators to transport equipment directly to the job site. This mobility translates into significant time savings and reduced transportation costs associated with moving raw materials.
Applications of mobile crushers include:
- Construction Sites: They break down rubble and asphalt on-site, streamlining the recycling process.
- Quarries: Extracting material from challenging locations becomes feasible without needing to set up permanent structures.
- Remote Mining Areas: They allow access to hard-to-reach locations, increasing productivity in challenging terrains.
While mobile crushers offer substantial advantages, they do face challenges like:
- Power Loss: Operating off-site may sometimes result in less optimized power systems compared to fixed designs.
- Operating Limits: They might not handle as high volumes as fixed crushers.
"Understanding and selecting the right specialized crusher can lead to a significant shift in operational efficiency and cost-effectiveness in the industry."
Correctly recognizing the potential of these specialized crushers can pave the way for innovative solutions that deliver on increasing demands across different sectors.
Choosing the Right Crusher
Selecting the right rock crusher is critical for the success of any project, whether in mining, construction or recycling. The type of crusher you choose not only influences operational efficiency but also impacts the end product’s quality. For a project manager or engineer, understanding the nuances between different crushers is crucial to avoid missteps that could lead to financial losses or operational downtimes.
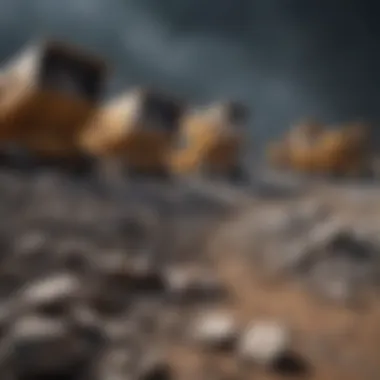
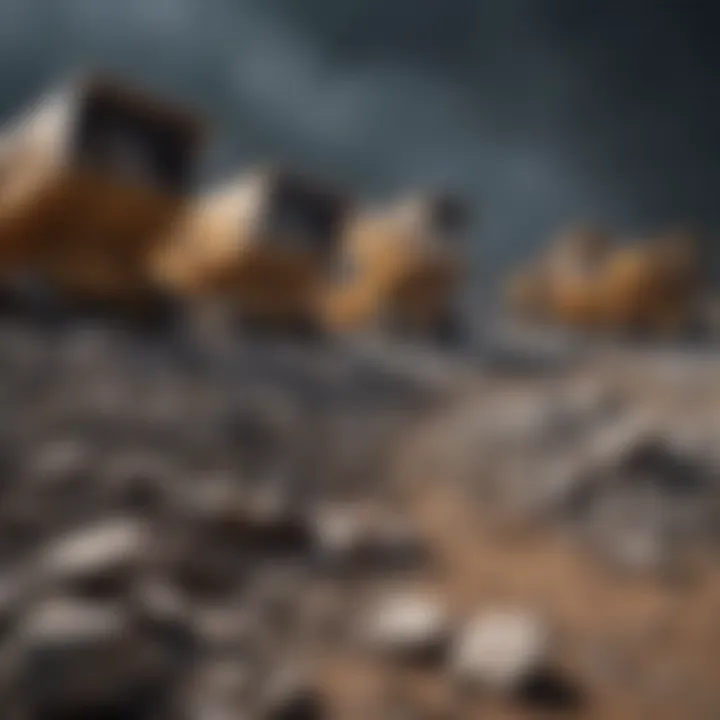
There are multiple elements that play into the decision-making process, and it's essential to weigh them carefully. A slight oversight can have significant ramifications down the road.
Factors Influencing Selection
When it comes to selecting a rock crusher, several factors come into play. Here are some prime considerations:
- Material Characteristics: The physical properties of the rock or material being crushed—such as hardness, size, and moisture content—can dictate the cutting method best suited for the job.
- Desired Product Size: The end product's specifications are directly tied to the choice of crusher. For example, if you need a finer particle size, it’s crucial to choose a crusher that specializes in that range.
- Production Capacity: Understanding the required output per hour helps narrow down options. Different crushers offer varied capacities.
- Cost of Operation: Besides the initial purchase price, the ongoing operational costs—like energy consumption and maintenance—are vital to factor in.
- Environmental Considerations: Regulations for noise and dust emissions are becoming stricter, thus requiring careful selection of a crusher that meets those environmental standards.
Operational Considerations
Once the factors influencing selection are clarified, operational considerations come next. It's not merely about picking a type but understanding how it fits into the larger scheme of the project. Here are some operational aspects that must be thought of:
- Ease of Installation: A rock crusher may be technically sound but difficult to install, which can delay your project. Selecting a model that integrates well with existing machinery is key.
- Maintenance Requirements: Regular upkeep is a must. Some crushers require frequent parts replacements and specialized services. Opting for a machine with lower maintenance needs can save time and resources in the long run.
- Operation Training: If your team isn’t trained to operate a chosen crusher, you could run into problems. Ensure that operators are comfortable and knowledgeable about how to use the machinery.
Material Type and Crusher Compatibility
The type of material being processed is one of the most pivotal aspects of equipment selection. Not all crushers perform alike when faced with different materials. Here’s how to navigate this aspect:
- Hard vs. Soft Materials: For instance, jaw crushers excel at breaking down hard rocks, while impact crushers perform better on softer materials.
- Moisture Content: If the material contains high moisture, there is a risk of clogging. Hence, understanding what your crusher can handle is crucial.
- Over-sized Materials: If you're dealing with oversized contaminant materials, a pre-crusher or primary feeder can make all the difference. You don’t want a bottleneck in your production line, so knowing your incoming material size ahead of time will guide your decision.
Properly matching materials to the right type of crusher can dramatically enhance efficiency and product quality.
These considerations foster a holistic view of your operation and offer significant insight into how strategic selections can affect productivity and output quality. By taking the time to understand what factors influence your choice and how it ultimately aligns with the end goal, the selection process transforms from mere choice to a meticulous strategy.
Maintenance of Rock Crushers
The crux of keeping rock crushers in prime condition cannot be overstated in any industry that uses them. Proper maintenance extends operational life, enhances efficiency, and minimizes downtime. For practitioners in construction, mining, or recycling—all fields where crushers are indispensable—understanding the maintenance protocols can make or break productivity.
One key element of maintenance is that it not only helps in preventing unexpected costs due to breakdowns but also ensures that the machine operates within safety regulations. Regular checks encourage adherence to operational standards, which is vital in maintaining workplace safety and compliance.
Routine Maintenance Practices
Scheduled maintenance is a standard practice that every user should implement. Here are some essential routine maintenance tasks to adhere to:
- Daily Inspections: Conduct visual checks for wear and tear. Look for any unusual vibrations or noises when running the machine.
- Lubrication: Keeping the moving parts well-lubricated is crucial. It reduces friction and helps in preventing overheating.
- Filter Changes: Air filters should be replaced regularly to ensure that the engine receives clean air. Clogged filters can dramatically reduce efficiency.
- Belt Check: Inspect belts for signs of wear or slippage. A damaged belt can severely impair performance.
- Cleaning: Keep all parts, especially the crushing chamber, clean to avoid blockage that can lead to overheating and even fires.
In addition, familiarizing yourself with the machine's manual can alert you to specific maintenance needs unique to the model you are using.
Common Issues and Solutions
Even with diligent maintenance, rock crushers are not immune to problems. Here is a rundown of some common issues and practical solutions:
- Overheating: Caused by excessive dust and debris buildup. Solution: Regular cleaning and proper ventilation can mitigate this issue.
- Blockages: Material can get stuck, especially in jaw and cone crushers. Solution: Perform regular checks and keep the machine clean to ensure smooth operation.
- Worn Out Parts: Bearings and hoppers can wear down over time. Solution: Regularly replace worn components and keep emergency replacements within easy reach.
- Vibrations: Indicate lash in the bearings or a misaligned rotor. Solution: Tighten all components and readjust settings as needed.
It's important to document maintenance activities. Having a log aids in recognizing patterns in machine performance and helps predict future issues.
In summary, a well-rounded maintenance practice doesn't just enhance equipment longevity but also boosts operational efficiency and helps in reducing unplanned downtimes. This proactive approach pays dividends down the line.
The Future of Rock Crushing Technology
The realm of rock crushing is on the cusp of a transformation, driven by rapid technological advancements and the growing emphasis on environmental sustainability. As industries evolve, the need for more efficient, less wasteful practices becomes paramount. Understanding the future of rock crushing technology is essential, not just for innovation’s sake, but for enhancing productivity, reducing operational costs, and minimizing ecological footprints. Notably, these technological evolutions will impact mining, construction, and recycling sectors profoundly.
Innovations and Trends
In the ever-evolving world of rock crushing, innovation is the name of the game. Cutting-edge technologies are not just enhancing the efficiency of crushers, but they are also driving the adoption of smarter systems. For instance, a notable trend is the rise of automated crushers equipped with artificial intelligence. These machines can predict necessary maintenance, adjust settings dynamically, and even monitor material quality in real time. Such advanced features can significantly minimize downtime and optimize the crushing process.
- Remote Monitoring: Modern crushers can be equipped with sensors that allow operators to monitor performance remotely. This advancement not only boosts safety but also enhances data collection for future operations.
- Hybrid Technology: Hybrid crushers that utilize both electric and diesel power sources are gaining traction. They offer flexibility and often lead to lower fuel consumption.
- Advanced Materials: The development of new materials for crusher components can result in significant life expectancy and durability, ultimately saving costs and enhancing performance.
These trends represent just the tip of the iceberg. As research and development continue, we can expect to see more revolutionary advancements reshaping the industry.
Sustainability in Crushing Operations
Sustainability is more than just a buzzword in today’s industrial landscape; it's a crucial element shaping the future of rock crushing technology. Companies are beginning to recognize that by adopting sustainable practices, they not only contribute to environmental preservation but can also cut costs in the long run.
Key aspects of sustainability in rock crushing include:
- Energy Efficiency: Modern rock crushers are being designed with energy-saving features, which significantly reduce overall power consumption. Efficient motors and variable speed drives are making a huge difference.
- Recycling Materials: There is increasing emphasis on recycling demolition waste and recycling materials, which can lead to reduced demand for fresh raw materials. By crushing and reusing materials, companies can lower costs and lessen their environmental impact.
- Minimizing Waste: Advanced crushing technologies are designed to minimize material waste. This approach enhances recycling rates and reduces the amount of waste sent to landfills.
- Cleaner Operations: Top-notch designs are also focused on reducing dust and noise pollution, creating a healthier work environment and adhering to stricter regulations.
"The shift towards sustainability is not just a trend; it’s an industry necessity that fosters innovation while protecting our planet for future generations."
The End
In closing, this article has navigated through the intricate world of rock crushers, shedding light on their diverse types and applications. Understanding these machines is not merely academic; it holds significant value for industries that rely on crushed materials. Each type of rock crusher, from jaw to cone and impact variants, plays a vital role in material processing, shaping the overall landscape of fields like mining, construction, and recycling.
Recapping the Key Insights
To sum it up, several key points stand out:
- Diverse Functionality: Each rock crusher type serves its unique purpose and excels in specific scenarios. For example, jaw crushers are optimal for primary crushing, while impact crushers are preferable when dealing with softer materials.
- Operational Mechanisms: Grasping how these machines work can aid in selecting the right equipment for a particular task. The mechanics—be it compression, impact, or shear—determine both the efficiency and the final product quality.
- Applications Across Industries: From aggregate production to recycling waste materials, rock crushers are instrumental in various sectors. Different industries exploit specific features of each crusher type to suit their needs.
It's crucial for professionals and stakeholders to recognize these insights. They guide choices and strategies both in equipment procurement and operational execution.
Final Thoughts on Rock Crusher Selection
When it comes to choosing the appropriate rock crusher, there are several considerations to keep in mind:
- Material Type: The characteristics of the material being processed are paramount. Hardness, abrasiveness, and size can dictate the choice of crusher. For instance, softer materials might fare better under impact crushing than harder rocks.
- Desired Output: Understanding the required end product is essential. Different crushers produce varying particle sizes and shapes, making it vital to align the crusher's capabilities with project specifications.
- Operational Environment: The location and context of use also play significant roles. Mobile crushers offer flexibility, while stationary models are better suited for high-volume tasks where space is a premium.
In essence, making an informed decision about rock crusher selection can optimize not only production rates but also the sustainability of operations. The alignment of equipment features with operational goals can lead to enhanced efficiency, cost savings, and ultimately, a more productive workflow.