Ultrasonic Examination of Welds: Techniques and Standards
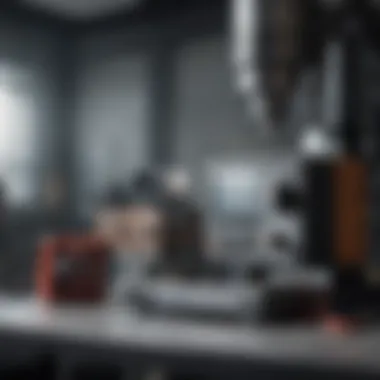
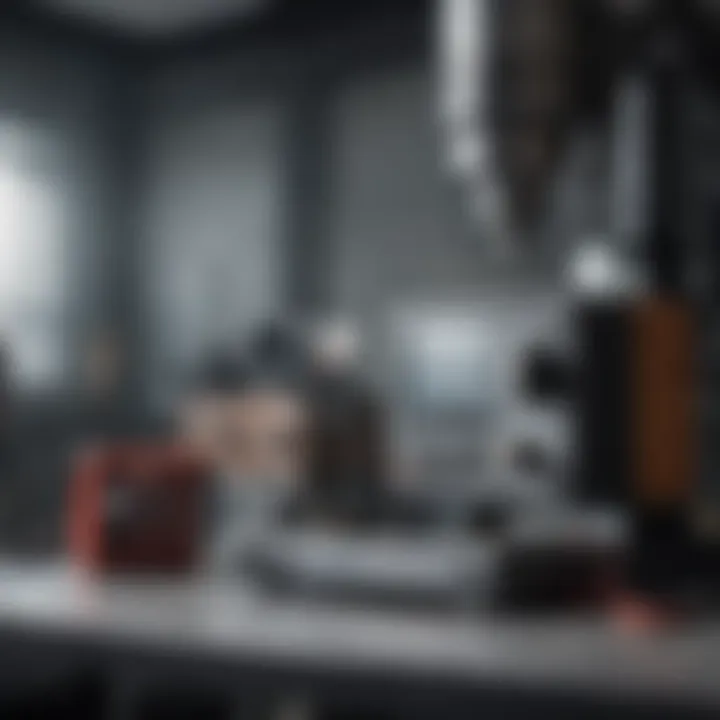
Intro
Ultrasonic examination of welds is a vital technique in non-destructive testing (NDT). It offers the ability to assess weld quality without damaging the material. This method employs high-frequency sound waves to detect defects that may not be visible to the eye. Understanding ultrasonic testing is crucial for students, researchers, and professionals in engineering and fabrication sectors.
The necessity for high-quality welds cannot be overstated. Poorly executed welds can lead to product failure, resulting in significant financial loss and safety hazards. By utilizing ultrasonic examination, industries can ensure the integrity of welds and maintain high standards.
The article will delve into essential concepts related to ultrasonic testing. It will also address its applications in various fields as well as the standards that guide the evaluation process.
Key Concepts and Terminology
Definition of Key Terms
- Ultrasonic Testing (UT): A non-destructive testing method that uses high-frequency sound waves to detect imperfections in materials.
- Weld Flaw: Any discontinuity in a weld, such as cracks, porosity, or incomplete fusion, that can compromise its strength and integrity.
- Calibration: The process of adjusting the ultrasonic equipment to ensure accurate measurements and interpretations of weld quality.
Concepts Explored in the Article
This article explores various aspects of ultrasonic examination, including:
- Principles of Ultrasonic Testing: Understanding how sound waves propagate through materials and how reflections help identify flaws.
- Techniques Used: Different approaches within ultrasonic testing, such as pulse-echo and through-transmission methods.
- Factors Influencing Assessment: Elements such as material type, thickness, and weld geometry that affect the outcome of ultrasonic tests.
- Standards and Recommendations: Industry standards governing ultrasonic testing, which ensure reliability and consistency in weld assessments.
Findings and Discussion
Main Findings
The exploration reveals significant insights into ultrasonic examination techniques. One notable finding is the adaptability of ultrasonic methods across various industries—ranging from manufacturing to aerospace. Each sector utilizes ultrasonic testing to ensure product integrity and safety.
Moreover, the exploration of advancements in technology showcases improvements in ultrasonic testing equipment, leading to higher precision and efficiency in weld assessments.
Potential Areas for Future Research
There are several areas that warrant further investigation to enhance ultrasonic testing:
- Integration with AI: Exploring the potential for artificial intelligence to analyze ultrasonic data more effectively.
- Advanced Materials: Investigating how newer materials impact ultrasonic testing efficacy.
- Automated Systems: Studying the development of automated ultrasonic testing systems for increased efficiency in high-volume production environments.
"The constant advancement of ultrasonic technologies ensures that weld examination remains at the forefront of quality assurance."
Foreword to Ultrasonic Examination
Ultrasonic examination plays a significant role in the realm of non-destructive testing (NDT), particularly when it comes to evaluating weld integrity. The importance of this technique cannot be overstated. It provides crucial insights into the quality and reliability of welds, ensuring that they meet rigorous safety and performance standards. By utilizing ultrasonic testing, professionals can detect flaws that may otherwise go unnoticed in traditional inspection methods.
Understanding ultrasonic examination begins with recognizing its various applications and the distinct advantages it offers. Unlike other testing methods, ultrasonics allow for immediate feedback regarding weld defects. This can include internal cracks, voids, and inclusions, all of which may compromise the structural integrity of a joint. With increasing demands for safety and sustainability in industries such as construction, aerospace, and manufacturing, ultrasonic testing serves as an essential tool.
In this section, we delve deeper into the two subsections that underpin this method: a comprehensive overview of non-destructive testing and the specific importance of ultrasonic testing in weld evaluation. These critical elements will establish the foundation of understanding necessary for further exploration of ultrasonic techniques, applications, and standards.
Overview of Non-Destructive Testing
Non-destructive testing encompasses a suite of methodologies aimed at evaluating materials and structures without causing physical damage. This type of testing is essential in various fields, including manufacturing, construction, and aerospace. The fundamental advantage of NDT lies in its ability to assess the performance and safety of critical components while keeping them intact. Some common NDT methods include visual inspection, radiographic testing, magnetic particle testing, and ultrasonic testing.
Each of these techniques has its own strengths and limitations. Ultrasonic testing stands out due to its ability to provide detailed information about internal flaws. It utilizes high-frequency sound waves to identify defects within materials, offering a depth of insight that is often not achievable with surface-level assessments. As industries evolve, the demand for reliable and efficient NDT methods continues to rise. Ultrasonic examination thus emerges as a pivotal approach in maintaining quality assurance in welding and fabrication processes.
Importance of Ultrasonic Testing in Weld Evaluation
The significance of ultrasonic testing in weld evaluation is marked by its precision and reliability. Welds are critical junctures in countless engineering applications, and defective welds can lead to catastrophic failures. Ultrasonic testing provides a methodical approach to ensuring weld quality through the detection of subsurface imperfections, such as porosity, inclusions, and cracks.
- Real-Time Results: One of the primary advantages of ultrasonic testing is the capability for immediate results. This expeditious feedback allows engineers to make necessary alterations in real-time, enhancing the overall welding process.
- Versatile Application: Ultrasonic methods are versatile, applicable to various materials, and effective in a range of situations. This adaptability makes it an ideal choice for industries such as aerospace and automotive, where material integrity is paramount.
- Cost-Effective: Although initial setup costs may seem high, ultrasonic testing can ultimately save money by preventing failures that compromise safety and require costly repairs or replacements.
Ultrasonic testing comprehensively evaluates welds, allowing for an advanced understanding of material integrity. Its integration into quality assurance protocols fortifies safety standards across multiple industries.
Fundamental Principles of Ultrasonic Testing
The fundamental principles of ultrasonic testing provide a critical foundation for understanding how this non-destructive method evaluates weld integrity. Mastery of these principles is essential for professionals who perform assessments of welded joints. The principles encompass various concepts related to sound wave behavior, the design and function of ultrasonic equipment, and the method of interpreting the resulting data. In this section, we will explore these elements and their importance to ultrasonic examination.
Sound Wave Propagation
Sound wave propagation is a core aspect of ultrasonic testing. Ultrasonic waves, which are sound waves with frequencies higher than the audible range, travel through materials. These waves are generated by a transducer and enter the test material. As the waves move through the material, they encounter different interfaces, such as where two pieces are welded together.
The behavior of these waves is influenced by several factors, such as the material's density and elastic properties. When waves reach a boundary within the material, a portion of the wave may reflect back to the transducer, while others continue through the material. This characteristic is crucial for detecting flaws within welds. Detecting signals from both reflections and transmissions allows inspectors to evaluate weld quality.
Transducer Functionality
The transducer is a vital component in ultrasonic testing. Its functionality is twofold: it converts electrical energy into ultrasonic waves and vice versa. There are various types of transducers, such as piezoelectric and electromagnetic ones, each designed for specific applications.
When selecting a transducer, factors such as frequency, sensitivity, and beam angle must be considered to ensure optimal performance in evaluating welded joints. For example, high-frequency transducers provide better resolution for detecting small defects, while lower frequencies can penetrate thicker materials. Properly functioning transducers are essential for obtaining reliable data during inspections.
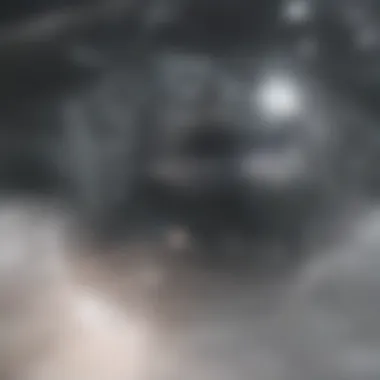
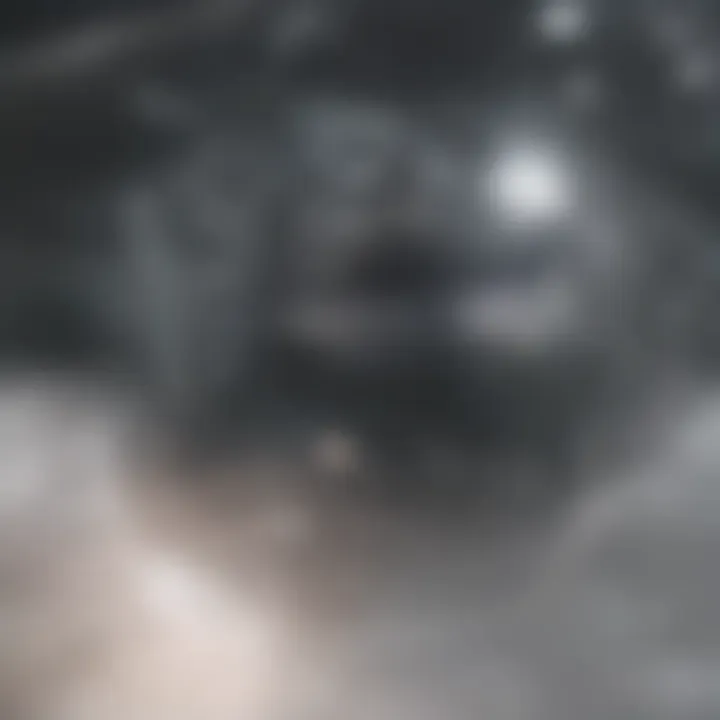
Echo Interpretation
Echo interpretation refers to the process of analyzing the information received from reflected ultrasonic waves. This consideration is crucial because the resulting echoes provide insight into the material's internal structure and reveal potential defects. An inspector must be skilled in differentiating between proper echoes generated by sound wave reflection from flaws in materials.
Visualizing the data generally involves using an oscilloscope, which displays amplitude versus time graphs. Interpretation of these graphs requires a solid understanding of what the signals represent and how to distinguish between them. Factors such as the distance to defects, their size, and shape can often be inferred from the data on the scope.
It is vital to understand that echo interpretation can significantly influence the quality assessment of welds. Inaccurate interpretations may lead to overlooking critical defects, posing risks to safety and structural integrity.
In summary, the fundamental principles of ultrasonic testing encompass sound wave propagation, transducer functionality, and echo interpretation. Understanding these principles is essential for ensuring accurate evaluations of weld integrity.
Ultrasonic Testing Techniques
The exploration of ultrasonic testing techniques is critical in understanding how to effectively evaluate weld integrity. Utilizing these methods allows for the detection of flaws in welds without damaging the structures being assessed. The techniques are focused on providing accurate results, making them indispensable for industries like manufacturing and aerospace, where safety and reliability are paramount.
Pulse-Echo Method
The pulse-echo method is one of the most widely used techniques in ultrasonic testing. In this approach, a pulse of sound is transmitted into the material. When this sound wave encounters a boundary, part of the energy reflects back to the transducer. This reflection provides valuable information about the structure of the weld.
Key Benefits:
- Real-Time Feedback: Inspectors receive immediate feedback on the weld integrity without the need for multiple tests.
- High Sensitivity: The pulse-echo method is sensitive to defects that might be missed by other techniques, allowing for a thorough examination.
- Adaptability: This method can be tailored for a variety of materials and geometries, enhancing its applicability.
Considerations:
- Surface Preparation: The quality of results can depend significantly on how well the surface of the weld is prepared for the test. Any contaminants may interfere with the sound wave's travel, leading to inaccurate readings.
Through-Transmission Method
The through-transmission method differs significantly from the pulse-echo approach. Here, two transducers are used on opposite sides of the weld. One transducer sends sound waves, while the other receives them. This technique is especially effective for detecting larger flaws or voids within the weld.
Key Benefits:
- Flaw Detection: This technique excels in identifying significant discontinuities, making it easier to ensure weld safety.
- Straightforward Interpretation: The lack of reflected energy reduces ambiguity in data interpretation compared to other methods.
Considerations:
- Material Thickness: This technique may not be effective for very thick materials, as the sound waves might not successfully transmit through the weld.
Time of Flight Diffraction Testing
The time of flight diffraction (TOFD) testing is an advanced ultrasonic technique. It relies on measuring the time it takes for sound waves to travel from the transducer to the weld and back. This method is particularly valuable for inspecting the depth and size of defects.
Key Benefits:
- Accuracy in Defect Sizing: TOFD can accurately provide dimensions of detected flaws, which is crucial for assessing weld performance and reliability.
- Rapid Testing Process: The technique allows for fast and efficient testing, contributing to overall project timelines.
Considerations:
- Expert Knowledge Required: This method requires a greater level of expertise, both in operation and interpretation, making operator training essential.
Understanding these ultrasonic testing techniques is vital for engineers and technicians aiming to achieve high standards in weld quality assessment. Each method has its own merits and specific use cases that are pivotal across various industries.
Factors Affecting Ultrasonic Testing Results
Ultrasonic testing (UT) is a powerful non-destructive evaluation method that offers insight into the integrity of welded joints. However, its efficacy is influenced by several factors. Understanding these factors helps in obtaining accurate assessment of weld quality and reliability.
Weld Geometry
Weld geometry significantly impacts the results of ultrasonic testing. The shape and configuration of a weld can dictate how sound waves propagate through the material. For instance, complex geometries, such as those found in multi-pass welds, can create variations in sound wave reflection and refraction. These variations may lead to difficulty in detecting or sizing defects. Moreover, the angle of the weld joint can affect the ability of ultrasonic waves to reach potential flaws.
Considerations include:
- Joint Design: The design of the weld joint, whether it is a butt, lap, or T-joint, influences wave travel.
- Weld Size: Thicker welds may require higher energy input and appropriate frequency adjustments to ensure penetration.
- Access Points: Limited access to the weld can require specialized transducer arrangements to achieve effective results.
Material Properties
Material properties play a crucial role as well. Variations in density, elasticity, and acoustic impedance influence how sound waves behave when they encounter different materials. The type of material being welded, such as steel, aluminum, or composites, can affect both the velocity and attenuation of the ultrasonic signals.
Key aspects to consider include:
- Density: Higher density materials tend to exhibit more scattering, which can mask small defects.
- Weld Material vs Base Material: Different materials might yield mismatched acoustic properties, complicating interpretation.
- Grain Structure: The microstructure of the weld can affect overall performance and may lead to anisotropic behavior in ultrasonic propagation.
Surface Condition
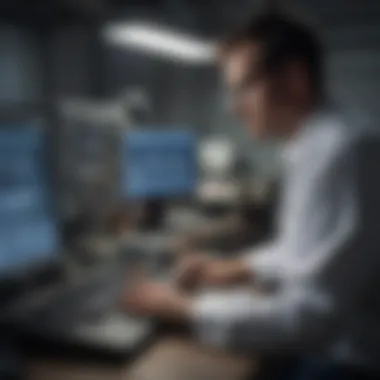
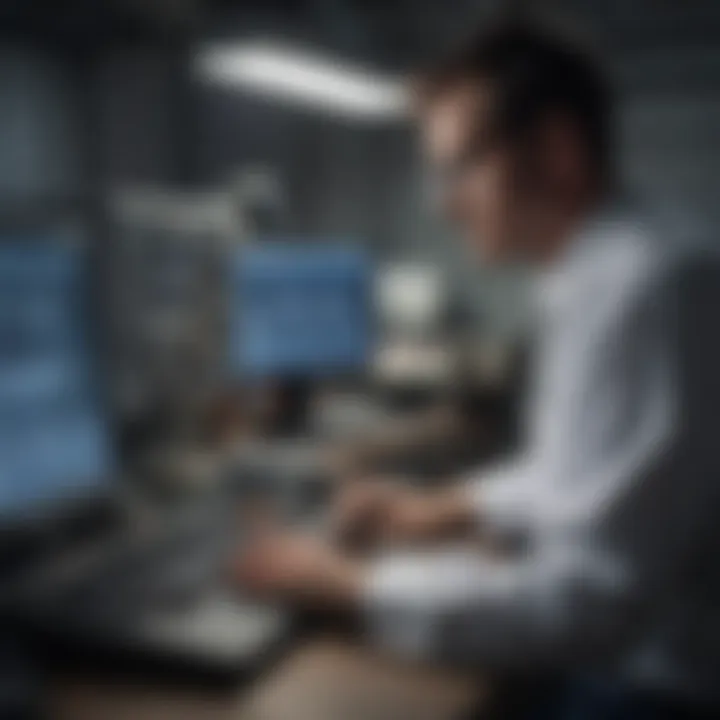
The surface condition of the weld joint is paramount in ultrasonic testing. Surface roughness or contaminants—such as oil, rust, or paint—can hinder the transmission of ultrasonic waves. A clean, smooth surface allows for better coupling between the transducer and the weld, ensuring that sound waves travel efficiently.
Important factors include:
- Roughness: Increased roughness can scatter waves and lead to inaccurate readings.
- Contaminants: Substances on the weld surface must be removed to prevent distortion of the transmitted signal.
- Preparation Method: Finishing processes like grinding or polishing can enhance surface quality, optimizing ultrasonic testing results.
"Attention to the factors affecting ultrasonic testing results helps ensure accurate evaluation and promotes the integrity of welded structures."
Applications of Ultrasonic Testing
Ultrasonic testing (UT) plays a significant role across various industries, ensuring the integrity and long-term reliability of welds. Its importance cannot be overstated, given that welding is often a critical process in manufacturing, construction, and aerospace applications. The key elements that make ultrasonic testing beneficial include its precision, efficiency, and its capability for non-destructive evaluation. Additionally, it helps industries maintain safety and compliance with standards, minimizing the risk of weld failures that could lead to catastrophic incidents.
Manufacturing and Fabrication
In the manufacturing and fabrication sector, the application of ultrasonic testing is indispensable. It is utilized to assess the quality of welds in products ranging from simple metal structures to complex machinery. With the increasing emphasis on efficiency, manufacturers rely on UT to quickly detect any flaws in welds such as cracks, porosity, and inclusions before they progress in the production line.
Benefits of using ultrasonic testing in manufacturing include:
- High Sensitivity: The technique can easily identify small defects that other methods might miss.
- Versatile Applications: It can be applied to various metals and welding processes, making it suitable for diverse manufacturing needs.
- Reduction of Downtime: UT is a fast inspection method, allowing for quick evaluations without significant production delays.
Moreover, ultrasonic testing supports compliance with relevant standards, ensuring the finished products meet safety and operational requirements. This is crucial in maintaining not only customer trust but also regulatory compliance.
Construction and Civil Engineering
In construction and civil engineering, ultrasonic testing is vital in assessing welds in critical infrastructure such as bridges, buildings, and pipelines. These structures require robust integrity to withstand various stresses and environmental conditions.
Key aspects of ultrasonic testing in construction include:
- Structural Safety: UT helps identify weak points in welds that may lead to structural failures.
- Cost-Effectiveness: Although initial inspection costs may seem high, early defect detection saves significantly on repair costs later in the project.
- Long-Term Monitoring: Ultrasonic testing can be used during various phases of construction and even as part of ongoing maintenance strategies.
By implementing ultrasonic testing, engineers can ensure long-lasting and reliable structures, ultimately enhancing public safety.
Aerospace Industry
The aerospace industry demands strict adherence to quality because even minor defects can have severe consequences. Ultrasonic testing is extensively used in this sector to evaluate welds in aircraft components and assemblies.
The significance of UT in aerospace includes:
- Critical Safety Standards: Aerospace components must meet high safety standards, and ultrasonic testing is one of the essential methods to verify weld integrity.
- Weight Efficiency: Because aircraft must be lightweight, UT helps in ensuring strong welds without the need for additional materials.
- Advanced Techniques: The aerospace sector benefits from advanced UT techniques like phased array testing, which can produce highly detailed and accurate images of weld integrity.
Standards and Guidelines in Ultrasonic Testing
The significance of standards and guidelines in ultrasonic testing cannot be overstated. They provide a framework that ensures uniformity and reliability across different examination processes. Adhering to these standards assures stakeholders that the ultrasonic examination meets essential safety and performance criteria, which is critical in sectors such as manufacturing, aerospace, and civil engineering. Moreover, established guidelines help in minimizing human error by providing a clear protocol for technicians to follow.
Standards also facilitate communication between inspectors and clients by defining the criteria for quality and acceptance testing. This is particularly important because the interpretation of ultrasonic signals can vary significantly from one inspector to another. With standardized practices, discrepancies in evaluation and reporting can be reduced, leading to more trustworthy outcomes.
In addition, compliance with well-defined standards can enhance the credibility of testing results when inspections are conducted. This fosters trust among stakeholders and can have positive implications for the business, such as improving project timelines and reducing material costs.
ASTM E2140
ASTM E2140 is a vital standard that outlines the practice for ultrasonic examination of welds. It focuses on ensuring that ultrasonic testing is performed consistently and effectively. This standard specifies the techniques to be used to detect defects in welds in metallic materials, providing guidelines on equipment calibration and the necessary response to various indications.
One primary benefit of adhering to ASTM E2140 is its detailed guidance on establishing testing parameters such as sound frequency, probe selection, and scanning techniques. This level of detail helps reduce variability and increases the repeatability of tests, which is essential when comparing results across numerous inspections. Furthermore, it sets the stage for the qualifications needed for individuals performing the tests, thereby ensuring that only competent personnel are responsible for critical assessments.
ASME Section
ASME Section V is another essential standard that governs non-destructive testing, including ultrasonic methods. This standard provides specific requirements related to the qualification of personnel, equipment, and procedures used for ultrasonic testing in various applications.
The ASME guidelines emphasize the importance of thorough training for personnel involved in ultrasonic examination. It requires that individuals demonstrate their ability to apply techniques correctly and interpret results accurately. This helps maintain a high level of quality assurance within the industry, ensuring that the tests performed are reliable and their resultant reports are accurate.
Moreover, ASME Section V also covers the criteria for acceptance and rejection of welds based on ultrasonic testing results. This aspect is critical, as it directly impacts the decision-making process related to the integrity and safety of structures or components.
ISO
ISO 17640 provides internationally recognized guidelines for the ultrasonic testing of welded joints. This standard is instrumental in standardizing practices across countries, helping to eliminate discrepancies that may arise from local regulations or practices. It sets criteria for the design of examinations, the positioning of transducers, and the interpretation of signals.
One significant aspect of ISO 17640 is its attention to detail in defining the acceptance levels for various types of welds and their configurations. By specifying limits for acceptable defects based on the geometry involved, this standard supports more effective and accurate evaluations.
Not only does ISO 17640 assist in ensuring consistent testing results, but it also promotes the harmonization of quality control practices globally. By aligning with international standards, organizations can foster better cooperation and understanding between parties engaged in inspections across different nations.
The three discussed standards—ASTM E2140, ASME Section V, and ISO 17640—are fundamental to achieving high-quality ultrasonic testing outcomes and ensuring the safety and reliability of welded structures.
Challenges in Ultrasonic Weld Examination
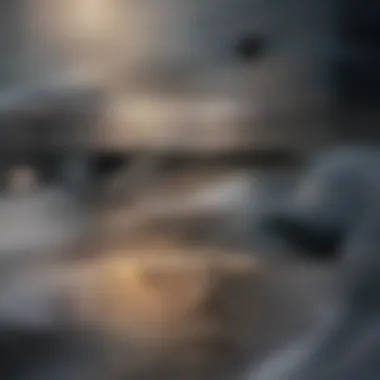
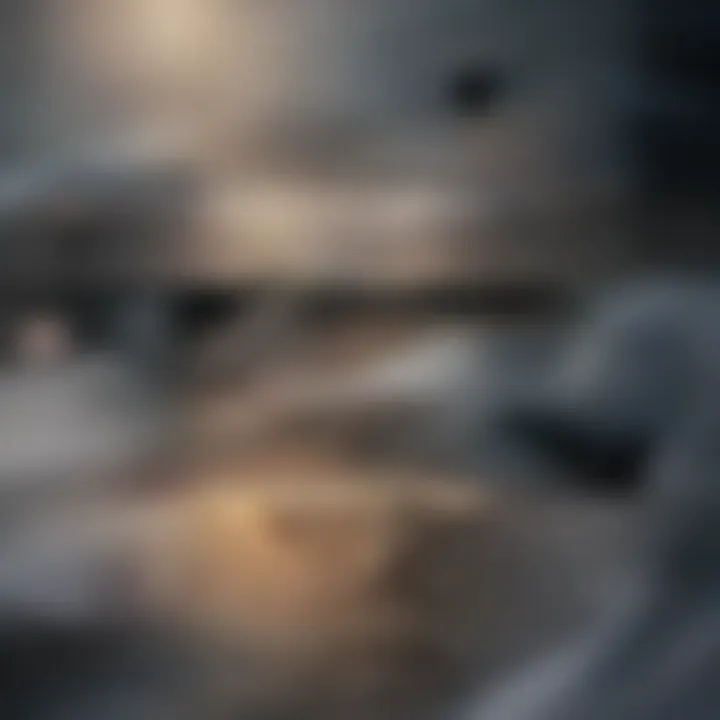
Ultrasonic weld examination is a highly effective non-destructive testing method, yet it is not without its challenges. Addressing these challenges is vital to formulating a successful approach to weld assessments. Understanding these issues helps practitioners strategize effective solutions, ultimately improving the reliability of the evaluation process. In this section, we will explore the specific obstacles encountered in ultrasonic weld examination, specifically focusing on the detection of small defects, the skill level of operators, and the importance of equipment calibration.
Detection of Small Defects
One of the most significant difficulties in ultrasonic weld examination is the detection of small defects. These defects may include micro-cracks, inclusions, and porosity, which can be challenging to identify using standard techniques. Their small size can result in weak signals that are easily overshadowed by noise or other artifacts in the reading. In fact, small defects might not produce sufficient echoes to be detected clearly.
Properly identifying defects requires an understanding of the material properties and appropriate settings on the ultrasonic equipment. Advanced techniques like Phased Array Ultrasonic Testing may offer benefits in these circumstances. They allow the detection of small defects at greater sensitivity. However, even these advancements face limitations based on the specific conditions of the weld.
Operator Skill Level
The skill level of the operator significantly influences the outcomes of ultrasonic weld examination. An experienced technician possesses the ability to interpret signals correctly and discern relevant information from an ultrasonic readout. In contrast, an untrained operator may struggle with identifying relevant echo patterns and differentiating them from artifacts or noise.
Regular training and skill assessments are essential to maintain high inspection standards. The complexities of ultrasonic techniques necessitate a robust understanding of both the equipment and the underlying physics. A skilled operator also needs to be able to adapt to the variables presented by different weld types and materials. Hence, continuous professional development is crucial in achieving accurate results.
Equipment Calibration
Proper equipment calibration is one of the foundational elements of a successful ultrasonic weld examination. Calibration ensures that the ultrasonic devices are providing accurate measurements, which is essential for reliable results. Without proper calibration, the risk of false readings or undetected flaws escalates.
Several factors play into the calibration process, including:
- Frequency of the ultrasonic waves: Different materials require varying frequencies to achieve optimal wave propagation.
- Temperature influences: Variations in temperature can affect the speed of sound in a material, leading to inaccurate readings.
- Material properties: Variations in density, elasticity, and grain structure also necessitate adjustments in calibration.
Regular calibration checks should be part of standard operating procedures. This practice prevents unnecessary errors and ensures the instruments are functioning properly.
Proper calibration is not just a routine task; it is a critical component that can determine the success of the inspection itself.
In summary, addressing the challenges in ultrasonic weld examination requires attention to detail in detecting small defects, thorough training for operators, and strict adherence to equipment calibration. Each of these factors contributes to the overall effectiveness of ultrasonic testing, helping ensure the integrity and quality of welded structures.
Recent Advancements in Ultrasonic Technology
Recent advancements in ultrasonic technology bring significant improvements to the conventional methods of weld examination. The integration of innovative techniques not only enhances the accuracy of defect detection but also optimizes the efficiency of the entire testing process. The focus of this section is on notable developments, such as phased array ultrasonic testing, digital signal processing, and the incorporation of robotics and automation.
Phased Array Ultrasonic Testing
Phased array ultrasonic testing (PAUT) stands out as a major leap forward in ultrasonic methods. This technique employs multiple ultrasonic elements that can be electronically focused and steered in various directions. By controlling the phase of each element, PAUT creates various beam angles and focal depths, allowing for a detailed assessment of complex geometries and thick welds.
Key benefits of PAUT include:
- Enhanced Coverage: With its ability to manipulate beams, inspectors can cover areas that traditional methods might miss.
- Defect Visualization: PAUT systems produce clear and detailed imaging of defects, aiding better interpretation of data.
- Efficiency in Time: The comprehensive scanning capability leads to faster examinations, thus reducing downtime in manufacturing and construction operations.
Digital Signal Processing
Digital signal processing (DSP) has become crucial in refining ultrasound signals for more accurate analyses. This technology uses algorithms to analyze and enhance received signals from ultrasonic tests. The processed data reveals subtle features in the welds that may be ignored in conventional evaluations.
Important aspects of DSP include:
- Noise Reduction: DSP can eliminate extraneous noise, leading to cleaner signal outputs and clearer results.
- Improved Resolution: It enhances the resolution of images generated from the ultrasonic tests, allowing for the detection of smaller flaws.
- Real-Time Analysis: This processing can potentially deliver instant feedback, enabling swift decisions and actions in the field.
Robotics and Automation in Testing
The introduction of robotics and automation marks a significant evolution in ultrasonic testing. These systems can perform weld examinations autonomously, minimizing human error and enhancing consistency in testing results. Robotic platforms equipped with ultrasonic testing tools can navigate complex structures and provide comprehensive data without extensive manual intervention.
Considerations regarding robotics in testing include:
- Increased Precision: Robots can execute tests with repeatable accuracy, ensuring reliable results each time.
- Access to Difficult Areas: Robotics can reach challenging locations that may pose risks to human inspectors.
- Cost-Effectiveness: Over time, deploying robotic systems can lead to reduced labor costs and shortened testing cycles.
Overall, the advancements in phased array ultrasonic testing, digital signal processing, and robotics not only push the boundaries of what is measurable but also improve the quality of weld inspections significantly. These developments are redefining industry standards and raising expectations for nondestructive testing methodologies.
The impact of these technologies is profound and continues to evolve, offering exciting possibilities for future applications in various fields.
The End and Future Perspectives
In the realm of non-destructive testing, ultrasonic examination of welds stands as a significant pillar ensuring integrity and reliability in various industries. This concluding section encapsulates essential insights and forecasts key trends that will shape the future landscape of ultrasonic welding examination. The comprehensive review of techniques, applications, standards, and challenges presented in this article serves to highlight the invaluable role ultrasonic testing plays in maintaining quality and safety in weld construction.
Summary of Key Insights
Throughout the article, we have explored a variety of topics associated with ultrasonic examination of welds. Here are some critical insights:
- Ultrasonic testing provides high-resolution evaluation of welds without damaging the material being tested. This non-invasive characteristic is crucial for maintaining structural integrity.
- Different techniques, such as pulse-echo and phased array, offer unique benefits tailored to specific industry needs.
- Factors influencing test results include weld geometry, material properties, and surface conditions. Understanding these elements is vital for accurate assessments.
The application of ultrasonic testing spans numerous industries, including manufacturing, construction, and aerospace. Adhering to standards like ASTM E2140 and ASME Section V ensures consistency and reliability in test outcomes.
Future Trends in Ultrasonic Welding Examination
Looking ahead, several trends are likely to impact the field of ultrasonic welding examination:
- Integration of Advanced Technologies: The adoption of digital signal processing and phased array technology will enhance the precision and efficiency of weld evaluations.
- Increased Use of Automation: As industries strive for greater efficiency, the implementation of robotics in ultrasonic testing processes will likely increase. This will streamline operations and potentially reduce the scope for human error.
- Focus on Training and Skill Development: With evolving technology, continuous education for operators will become crucial. Emphasizing skill development will ensure that the workforce remains competent in using advanced ultrasonic testing equipment.
The pursuit of continuous improvement and adaptability in ultrasonic testing practices is essential to meet the growing demands of various sectors.