Understanding Chemical Manufacturing: An In-Depth Overview
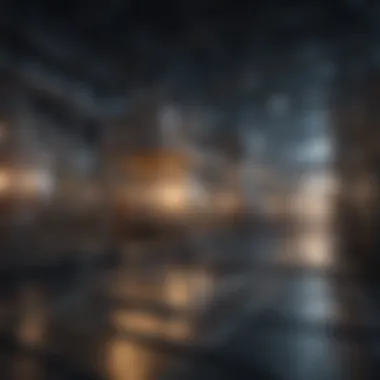
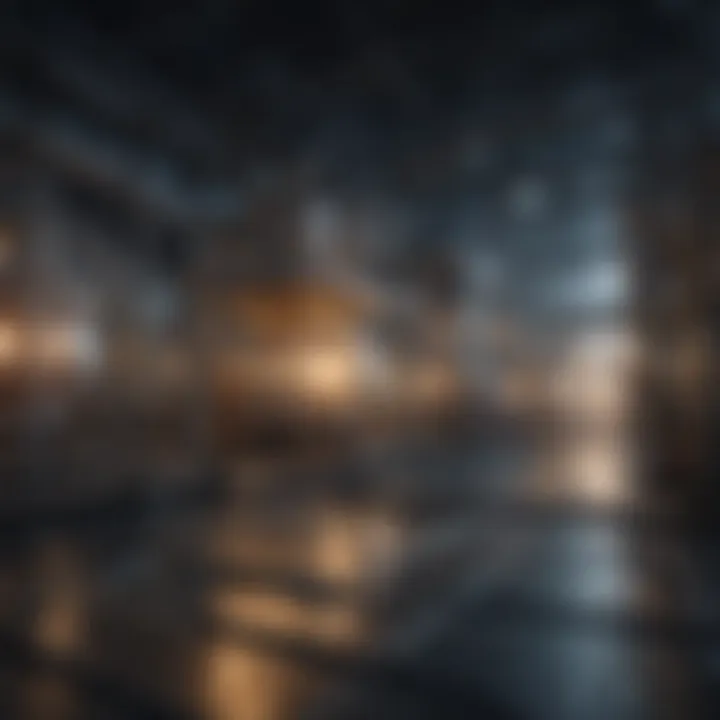
Intro
Chemical manufacturing stands as a cornerstone of modern industry. The transformation of raw materials into usable products sparks vital discussions about economic, environmental, and social dynamics. In this article, we will examine the intricate processes, evolving technologies, and challenges that define this field.
Understanding the underlying concepts and terminology is essential for grasping the complexities involved. Beyond basic definitions, we will uncover the significance of chemical manufacturing in various sectors, emphasize regulatory frameworks, and highlight future trends. By engaging with this topic, we aim to formulate a well-rounded perspective, beneficial for students, researchers, and industry professionals alike.
Key Concepts and Terminology
Definition of Key Terms
Chemical manufacturing refers to the large-scale production of chemicals that are used in a variety of applications, from industrial processes to consumer products. Key terms include:
- Chemical Process: A series of steps that transform raw materials into products.
- Batch Production: A method of manufacturing in which products are made in groups or quantities.
- Continuous Production: A production method that runs continuously to produce a constant output.
These terms will serve as a foundation as we explore the broader context of the industry.
Concepts Explored in the Article
This article will address essential concepts such as:
- The role of chemical manufacturing in global markets.
- The importance of sustainability and environmental impact.
- Technological advancements and their implications.
By shedding light on these concepts, readers can appreciate the depth of this field.
Findings and Discussion
Main Findings
Through our exploration, the following main findings emerge:
- Economic Relevance: Chemical manufacturing contributes significantly to the economy, providing jobs and driving innovation.
- Environmental Challenges: The industry faces scrutiny regarding its environmental footprint, prompting a push toward greener practices.
- Technological Innovations: Innovations such as automation and data analytics change the way chemicals are produced, making processes more efficient.
These components interlink, showcasing the multifaceted nature of the industry.
Potential Areas for Future Research
Identifying areas for further inquiry can yield valuable insights. Potential research pathways include:
- The integration of renewable resources in chemical production.
- The impact of global regulatory changes on manufacturing processes.
- Advances in safety protocols within manufacturing facilities.
By focusing on these topics, future research may address pressing issues and contribute to industry advancement.
Understanding the landscape of chemical manufacturing is crucial not just for industry professionals but for society as a whole. By studying this field, we can better grasp our interconnected global systems.
Prologue to Chemical Manufacturing
The domain of chemical manufacturing is essential to the modern economy and touches numerous sectors, including pharmaceuticals, agriculture, and industrial applications. Understanding this field involves grasping its processes, technologies, and inherent challenges. This article provides a deep dive into the mechanics and implications of chemical manufacturing, giving readers a thorough understanding of its significance.
Definition and Scope
Chemical manufacturing refers to the process of producing chemicals, including synthetic and natural substances, on a large scale. This industry is responsible for converting raw materials into usable products, which serve various purposes in everyday life. The scope of chemical manufacturing encompasses a diverse range of activities, from the synthesis of new chemicals to their purification and distribution. It is pivotal for creating materials that are foundational to health, agriculture, and various manufacturing processes.
Key activities in this realm involve:
- Design and execution of chemical processes
- Quality control to ensure product safety and efficacy
- Compliance with environmental and safety standards
The definition of this field is broad yet critically important, as it integrates science, engineering, and economics. Professionals involved in chemical manufacturing work on both the theoretical aspects and the practical application of chemical processes.
History and Evolution
The history of chemical manufacturing is rich and reflects significant advancements in technology and understanding of chemistry. It can be traced back to ancient civilizations that utilized basic chemical processes for agriculture and medicine. The evolution accelerated during the Industrial Revolution when globalization permitted widespread production.
In the early 19th century, major developments occurred with the creation of new methods to synthesize chemicals, such as the production of sulfuric acid and ammonia. These innovations laid the groundwork for the modern chemical industry, which expanded rapidly in the 20th century due to breakthroughs in organic and inorganic chemistry.
As industries developed, the need for more sophisticated and efficient methods led to the introduction of automation and newer technologies. Today, the chemical manufacturing sector continues to evolve with advancements in green chemistry and sustainable practices, aiming to minimize environmental impact while meeting market demands.
This ongoing evolution reflects the dynamic nature of the industry, which is continuously adapting to challenges and opportunities presented by technological advances and global shifts.
Fundamental Processes in Chemical Manufacturing
The fundamental processes in chemical manufacturing serve as the backbone of the industry. Understanding these processes is crucial. They dictate the efficiency and effectiveness of production, which in turn influences product quality, cost, and market competitiveness. Each process plays its own role, shaping how chemicals are synthesized, separated, and purified. By analyzing these fundamentals, one can gain valuable insights into the operational dynamics of chemical manufacturing, allowing for improved practices and innovative strategies.
Synthesis Techniques
Synthesis techniques are central to chemical manufacturing, as they transform raw materials into desired products. These methods encompass a range of approaches, such as batch synthesis, continuous synthesis, and microwave-assisted synthesis. Each technique has its advantages and specific applications.
- Batch Synthesis: In this traditional method, reagents are combined in single batches. This allows for flexibility in production but can be inefficient for larger-scale operations due to clean-up time and potential contamination risk.
- Continuous Synthesis: This method continuously feeds raw materials into the system, leading to higher production rates and efficiency, particularly beneficial for the production of bulk chemicals.
- Microwave-Assisted Synthesis: An emerging technique that utilizes microwave radiation to enhance chemical reactions. This method can improve reaction rates and yields significantly, making it attractive for research and small-scale production.
These techniques are closely monitored and optimized, ensuring that they meet the specific needs of the production environment, ultimately affecting the speed and efficiency of chemical output.
Separation Processes
Separation processes play an essential role in isolating products from undesired by-products or impurities after synthesis. This stage is critical for achieving the purity standards required in many applications. Common separation methods include distillation, filtration, and chromatography.
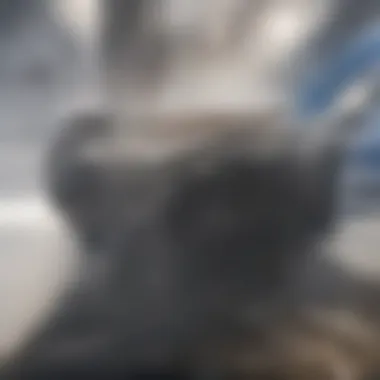
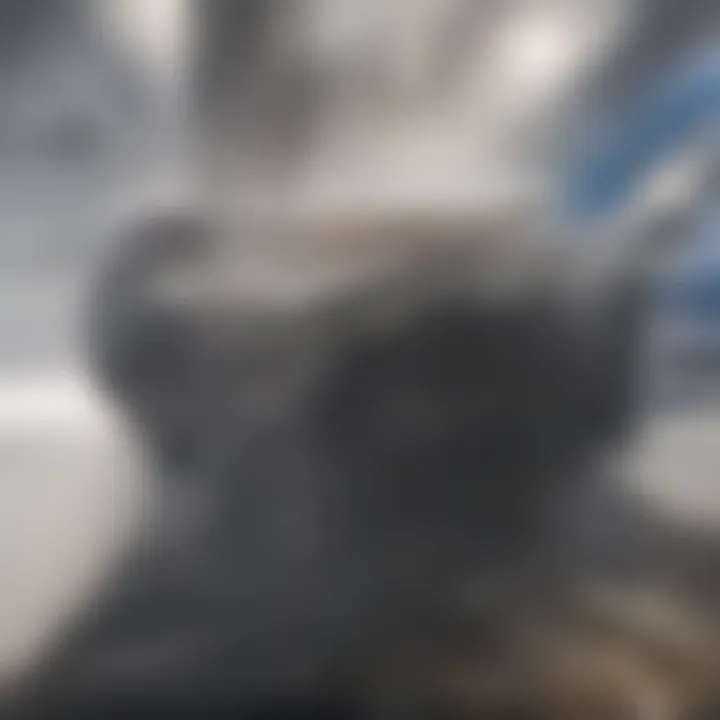
- Distillation: This classic method separates components based on different boiling points. It is widely used in the petrochemical industry and for producing beverages, indicating its versatile application.
- Filtration: A mechanical method that involves passing a mixture through a filter to separate solid particles from liquids or gases. It can be simple or complex, depending on the level of purification required.
- Chromatography: This sophisticated technique separates components based on their affinity to a stationary phase. It is crucial for analyzing and purifying complex mixtures, especially in pharmaceuticals.
By implementing appropriate separation processes, manufacturers can ensure high-quality end products that meet regulatory and consumer standards.
Purification Methods
Purification methods are vital to ensure that the final products are free from contaminants. These contaminants can affect both the safety and performance of chemical products. Several techniques are used for purification, including recrystallization, extraction, and ion exchange.
- Recrystallization: This method involves dissolving a solid in a hot solvent and then cooling it to form pure crystals. It is particularly useful for purifying organic compounds.
- Extraction: This process separates chemicals based on their solubility in different solvents. It is commonly used in both organic and inorganic processes to isolate desired components.
- Ion Exchange: This method removes unwanted ions from a solution, replacing them with other ions. Applications include water treatment and pharmaceutical manufacturing.
Effective purification methods are essential for facilitating compliance with industry standards, ensuring that all products are safe, effective, and suitable for their intended use.
"Understanding synthesis, separation, and purification processes is crucial for optimizing production and ensuring product safety in the chemical manufacturing sector."
Chemical Manufacturing Technologies
Chemical manufacturing technologies play a critical role in the efficiency and effectiveness of production processes. These technologies encompass various methods and innovations that facilitate the transformation of raw materials into finished products. In this section, we shall discuss key technologies that are transforming todayβs chemical manufacturing landscape.
Batch vs. Continuous Production
Batch production refers to the process where chemicals are produced in groups, or batches, rather than in a continuous flow. This method allows for flexibility and the ability to produce a wide range of products.
- Advantages:
- Flexibility in product formulation.
- Lower initial capital investment.
- Easier to switch between products.
Continuous production, on the other hand, involves a constant flow of materials through the production process. This method can be highly efficient.
- Advantages:
- Higher production rates.
- Typically lower production costs.
- Consistent quality of products over time.
Choosing between batch and continuous production depends largely on the specific requirements of the manufacturing setup, including product types and volumes.
Automation and Control Systems
Automation in chemical manufacturing involves the use of technology to control production processes without human intervention. This has significant implications for the industry. Improved automation means better precision in process control, enhanced safety, and reduced human error.
Control systems manage operations across several fields.
- Key benefits:
- Enhanced efficiency and optimization of processes.
- Ability to monitor systems in real time.
- Reduction in operational costs.
With advancements in technology, these systems become increasingly complex and can integrate data analytics to predict maintenance needs or optimize production settings.
Advanced Manufacturing Techniques
Advanced manufacturing techniques encompass multiple innovative approaches to improving production efficiency and product quality. Two key approaches in this area are microscale manufacturing and process intensification.
Microscale Manufacturing
Microscale manufacturing focuses on producing small quantities of chemical materials using advanced tools and precision techniques. This method is gaining traction due to its specific advantages.
- Key characteristics:
- Ability to precisely control reactions on a small scale.
- Reduced waste and resource consumption.
The unique feature of microscale manufacturing is its suitability for high-value products where efficiency and sustainability are crucial. However, the initial investment in technology can be high, which may deter some manufacturers.
Process Intensification
Process intensification involves strategies aimed at making chemical processes more efficient, by increasing their productivity while using less energy and resources. This includes improved reactor designs, hybrid processes, and reduced equipment footprints.
- Key characteristics:
- Integration of multiple processes into one system.
- Significant reductions in chemical usage and waste.
A unique feature of process intensification is its ability to achieve higher yields while minimizing capital and operational costs. However, implementation can be complex and requires careful consideration of potential challenges, including the need for specialized training.
Conclusion: Advances in chemical manufacturing technologies hold great promise for the future, with significant potential benefits for efficiency, safety, and sustainability in the industry. Embracing these technologies is essential for chemical manufacturers aiming to stay competitive in a rapidly evolving market.
Applications of Chemical Manufacturing
Chemical manufacturing plays a crucial role in various sectors, impacting everyday life and driving economies. The processes involved in manufacturing chemicals are vital for producing a wide range of products that contribute significantly to public health, agriculture, and industrial output. Understanding these applications provides insights into not only the complexities of the industry but also its relevance and significance in modern society.
Pharmaceuticals
The pharmaceutical industry is one of the most prominent sectors relying on chemical manufacturing. It encompasses the design, development, and production of drugs that enhance health and well-being. Chemical manufacturing enables the synthesis of active pharmaceutical ingredients (APIs), which are the core components in medications. Advances in synthesis techniques have led to greater efficiency and lower costs in drug production.
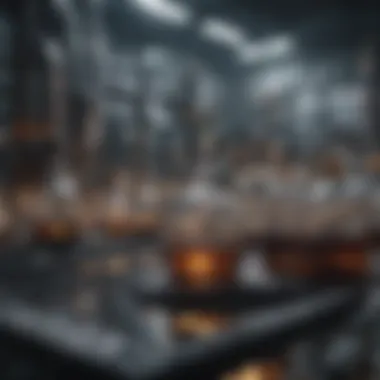
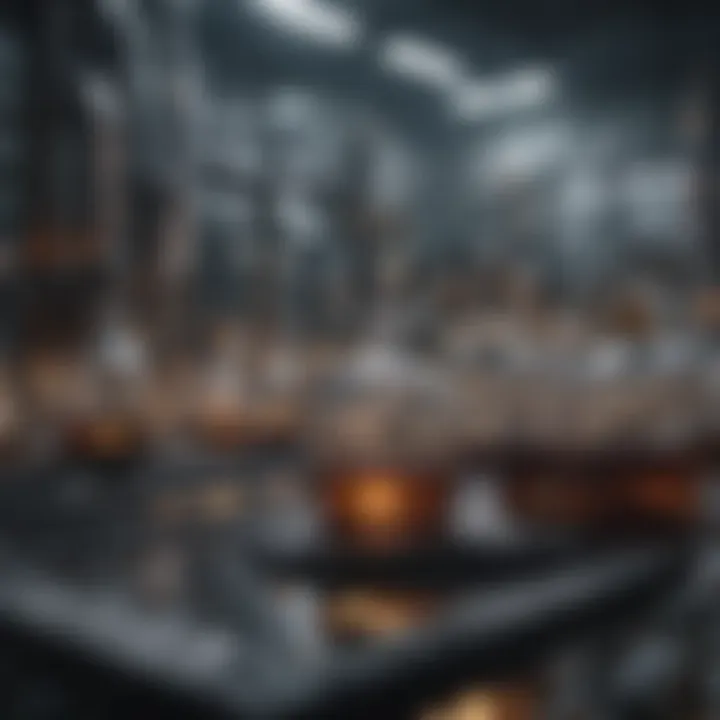
Moreover, chemical manufacturing processes facilitate the formulation of different dosage forms such as tablets, injectables, and creams. This versatility is essential, as it ensures that medications can be tailored to meet diverse patient needs. Continuous innovation in this field is needed to address challenges such as drug resistance and the demand for personalized medicine.
Agricultural Chemicals
Agriculture relies heavily on chemical manufacturing to produce fertilizers, pesticides, and herbicides that enhance crop yields and protect against pests. These products are vital for sustaining the global food supply, which is increasingly challenged by population growth and climate change. Chemical manufacturers are tasked with the vital role of developing effective and environmentally sound agricultural chemicals.
Sustainable practices in chemical manufacturing can reduce agricultural runoff, which often leads to larger environmental issues. Innovations such as precision agriculture enable farmers to utilize chemicals more effectively, minimizing waste and reducing exposure to harmful substances. Understanding these applications in agriculture is essential for meeting future food demands while mitigating environmental impact.
Industrial Chemicals
The industrial chemicals sector encompasses a wide range of products used across various industries, including construction, textiles, and plastics. Chemicals such as solvents, acids, and bases are integral for manufacturing processes and materials. Without chemical manufacturing, many of the conveniences of modern life would not exist.
Chemical manufacturing provides the building blocks for industrial applications. For instance, methanol is crucial for producing formaldehyde, a key component in many plastics. A focus on improving efficiency and safety standards within this field is non-negotiable. This ensures that industrial chemicals can be produced responsibly and sustainably, addressing regulatory and consumer demands for safer products.
"Innovative applications of chemical manufacturing are essential for supporting modern technologies while minimizing environmental consequences."
In summary, the applications of chemical manufacturing are vast and deeply embedded in various sectors, showcasing its importance. By examining pharmaceuticals, agricultural chemicals, and industrial chemicals, one can appreciate the breadth of influence this industry has on daily life and the global economy.
Environmental and Safety Considerations
Environmental and safety considerations play a crucial role in the field of chemical manufacturing. The industry is associated with various hazards that could potentially harm human health and the environment. Addressing these concerns is essential for sustainable practices and industry growth. The ethical responsibility of manufacturers includes ensuring safe production processes while minimizing negative impacts on ecosystems. Compliance with regulations not only protects workers but also enhances a company's reputation and sustainability profile.
Pollution Control
Pollution control in chemical manufacturing refers to strategies and technologies that aim to reduce harmful emissions and waste. This is vital for both environmental health and operational sustainability. Various methods are accessible for effective pollution control, such as:
- Emission Control Systems: Technologies like scrubbers and filters help capture pollutants before they are released into the atmosphere.
- Waste Minimization Techniques: By revising processes, companies can reduce waste generation, thus lessening the burden on waste management systems.
- Recycling and Reuse: Implementing systems for recycling by-products can significantly decrease waste and enhance resource efficiency.
Efforts in pollution control lead to various benefits:
- Improved air and water quality.
- Compliance with environmental regulations, which reduces legal risks.
- Enhanced corporate reputation among environmentally-conscious consumers.
"Effective pollution control is not just a regulatory requirement but a critical aspect of corporate social responsibility."
Health and Safety Regulations
Health and safety regulations are essential for maintaining a safe working environment in chemical manufacturing. Organizations like OSHA in the United States impose standards that protect workers from potential hazards. Key elements of these regulations include:
- Worker Training Programs: Educating employees on safe handling of chemicals and emergency response procedures.
- Regular Safety Audits: Conducting frequent assessments can help identify risks and enforce compliance with safety norms.
- Personal Protective Equipment (PPE): Providing suitable PPE ensures worker safety against chemical exposure.
The implications of adhering to health and safety regulations are profound:
- They help prevent workplace accidents, leading to fewer injuries and fatalities.
- Ensure operational continuity by minimizing downtime caused by incidents.
- Promote a safety culture that boosts employee morale and productivity.
The integration of effective pollution control measures and adherence to health and safety regulations encapsulates a strategic approach for chemical manufacturers. This ensures both the safety of workers and the preservation of the environment.
Regulatory Frameworks in Chemical Manufacturing
Regulatory frameworks are essential to ensure safety, environmental protection, and compliance in chemical manufacturing. These frameworks govern how chemicals are produced, handled, and disposed of. Understanding regulatory frameworks is crucial for students, researchers, and industry professionals, as they shape practices and standards in the chemical industry. Non-compliance can lead to severe consequences, including legal penalties, environmental disasters, and economic losses.
Effective regulatory frameworks often improve product safety, enhance environmental performance, and foster trust among stakeholders.
Global Standards and Compliance
Global standards such as ISO 9001 and ISO 14001 play a vital role in chemical manufacturing. Compliance with these standards helps organizations manage quality and environmental impacts effectively. Many countries adopt these standards to harmonize regulations internationally. This uniformity aids companies operating globally and simplifies the process of entering new markets.
Additionally, organizations may follow specific regulations tailored to their industry. The European Union's REACH regulation, for instance, focuses on the registration, evaluation, and authorization of chemical substances, enhancing safety measures across member states. This regulation not only aims to protect human health and the environment but also promotes innovation in sustainable chemical processes.
"Regulatory compliance is not just a legal obligation; it's a strategic advantage that can improve competitiveness and build consumer trust."
Local Regulations and Impact
Local regulations can significantly influence chemical manufacturing practices. Each region may impose unique requirements based on specific environmental concerns, public health needs, and economic conditions. Staying abreast of local regulations is crucial for companies to avoid legal issues and to support sustainable development within their communities.
For example, in the United States, the Environmental Protection Agency (EPA) enforces regulations that govern air and water quality. This ensures that manufacturers implement pollution control measures, thereby safeguarding public health. Compliance with local regulations often requires ongoing monitoring and reporting, which can increase operational costs but ultimately leads to better practices and community relationships.
Technological Innovations in Chemical Manufacturing
In the ever-evolving landscape of chemical manufacturing, technological innovations play a pivotal role. These advancements not only enhance productivity but also improve product quality and reduce environmental impact. Keeping pace with technology is essential for industries aiming to remain competitive in a global market. This section will explore both emerging technologies and the concept of smart manufacturing and how they shape the future of chemical production.
Emerging Technologies
Nanotechnology
Nanotechnology involves manipulation of matter on an atomic or molecular scale. This field of study is vital for its ability to improve both the efficiency and effectiveness of chemical processes. One key characteristic of nanotechnology is its capacity to increase surface area while decreasing the amount of material needed. This feature makes it an attractive option in chemical manufacturing.
The unique aspect of nanotechnology in this context is its application in catalyst development. Catalysts at the nanoscale can accelerate chemical reactions while using fewer resources. The advantages of this approach include reduced energy consumption and increased reaction rates. However, challenges exist, notably the potential toxicity of nanoparticles and their impact on human health and the environment.
Biotechnology
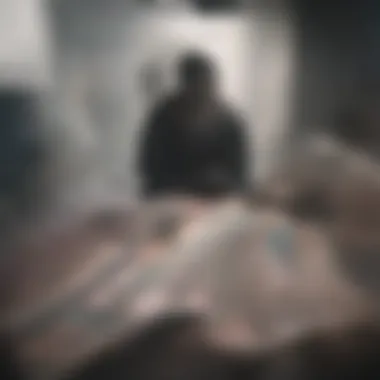
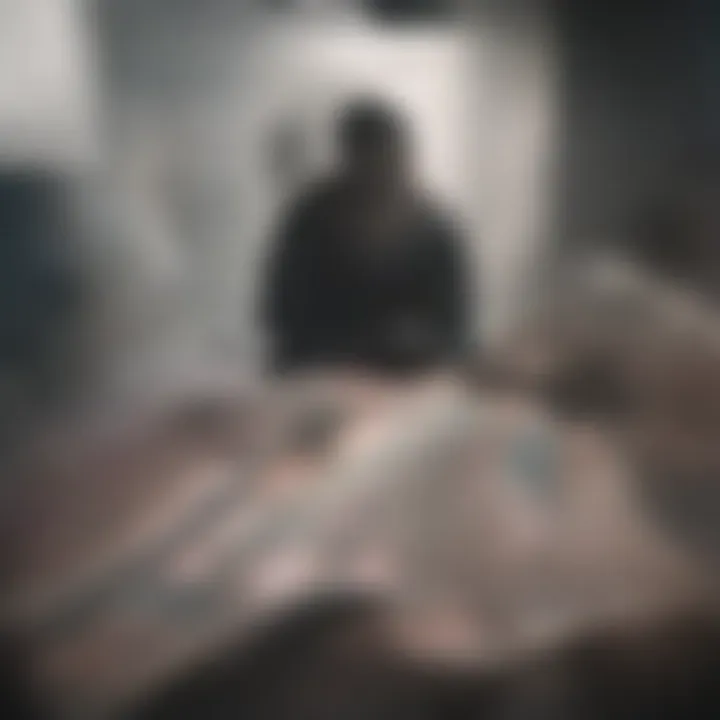
Biotechnology brings the biological processes into the realm of chemical manufacturing. Its contributions are significant, particularly in the production of bio-based chemicals. A critical characteristic of biotechnology is its reliance on living organisms or biological systems to develop products. This process often leads to more sustainable practices compared to traditional methods, as it utilizes renewable resources.
The uniqueness of biotechnology lies in its use of enzymes and microorganisms to catalyze chemical reactions. This not only minimizes waste but also allows for the production of high-value chemicals. While biotechnology has many benefits, there are also disadvantages. The development cycles can be longer, and regulatory hurdles are often more complex due to concerns about genetic modifications and environmental safety.
Smart Manufacturing
Smart manufacturing integrates advanced technologies like IoT (Internet of Things) and artificial intelligence into chemical processes. This incorporation allows for better monitoring, control, and optimization of manufacturing operations. The importance of smart manufacturing within the chemical industry cannot be overstated as it leads to increased efficiency, minimized downtime, and enhanced decision-making capabilities.
The advantages of smart manufacturing include real-time data collection and analysis. This ability to analyze data on-the-fly helps manufacturers to quickly respond to issues and improve their processes. However, the dependency on technology raises concerns about cybersecurity and the need for upskilling the workforce to manage sophisticated systems effectively.
"Technological advancements are not just about efficiency; they represent a pivotal shift towards sustainability and safety in chemical manufacturing."
Challenges in Chemical Manufacturing
Chemical manufacturing is an essential sector that faces numerous challenges affecting its efficiency, sustainability, and profitability. Recognizing these challenges is crucial for stakeholders across the industry, including policymakers, companies, and researchers. This section delves into significant obstacles that hinder growth and innovation while providing insights that can guide strategic approaches.
Supply Chain Disruptions
Supply chain disruptions are a persistent challenge in chemical manufacturing. These disruptions can arise from various factors such as natural disasters, geopolitical tensions, or shifts in market demand. Each of these can severely impact the flow of raw materials and finished products.
- Natural Disasters: Events like hurricanes or earthquakes can halt production. They damage facilities and disrupt transportation routes.
- Geopolitical Tensions: Tariffs or trade sanctions can lead to supply shortages, creating bottlenecks in production. This can hinder access to critical materials needed for chemical processes.
- Market Demand Shifts: Sudden changes in consumer preferences can lead to excess inventory in some areas while creating shortages in others.
These supply chain issues not only affect production times but also increase costs. Managing these disruptions requires robust risk management strategies and flexible operations to adapt to these unforeseen challenges. Companies are increasingly investing in advanced analytics and supply chain management software to enhance visibility and resilience.
Cost Management
Cost management is another critical challenge in the chemical manufacturing industry. Rising operational costs can emerge from various sources, impacting profit margins. These costs often include labor, raw material expenses, compliance with regulations, and maintenance of equipment.
A few specific aspects include:
- Raw Material Prices: Fluctuations in global markets can drive up costs. For instance, crude oil prices directly influence the price of petrochemicals.
- Labor Costs: Skilled labor shortages are common in this industry, leading to higher wages and training costs.
- Regulatory Compliance: Adhering to environmental and safety regulations adds additional costs. Companies may face severe penalties if they fail to meet compliance standards.
To combat these rising costs, companies are focusing on process optimization. By implementing lean manufacturing principles, firms can reduce waste and improve overall efficiency. Automation also plays a critical role, helping to minimize labor costs while enhancing output quality and consistency.
"The effective management of costs and disruptions is vital for maintaining competitiveness in the global chemical market."
The landscape of chemical manufacturing requires constant adaptation and innovation. Awareness of these challenges is the first step toward developing comprehensive strategies that can mitigate risks and enhance operational efficiency.
Future Trends in Chemical Manufacturing
Future trends in chemical manufacturing play a crucial role in shaping the industry's landscape. As emerging technologies and societal demands evolve, the sectors linked to chemical production are forced to adapt. This section examines sustainability initiatives and digital transformation, two pivotal elements that will influence the future direction of this field.
Sustainability Initiatives
Sustainability is becoming increasingly vital in chemical manufacturing. The industry faces growing pressure to reduce environmental impact while maintaining productivity. This has led to several important sustainability initiatives, which include:
- Resource Optimization: Manufacturers are focusing on using fewer raw materials and minimizing waste. This entails efficiency not just in production but also in sourcing.
- Green Chemistry Practices: By utilizing non-toxic chemicals and environmentally friendly processes, manufacturers can create safer products. This approach minimizes hazardous byproducts and seeks sustainable resources.
- Recycling and Circular Economy: A trend towards recycling materials and promoting a circular economy is gaining traction. Instead of following a linear model of production and disposal, companies are designing processes that allow materials to be reused.
These initiatives are not only environmentally responsible but can also yield cost savings, making them appealing for companies aiming for long-term viability.
Sustainability initiatives are essential for the chemical manufacturing industry's future, aligning economic success with environmental stewardship.
Digital Transformation
Digital transformation represents another significant trend shaping the future of chemical manufacturing. This encompasses a variety of technological advancements that streamline operations and enhance decision-making. Key aspects include:
- Data Analytics: The integration of data analytics enables manufacturers to harness big data for insight generation, thus facilitating informed decisions. Predictive analytics can foresee problems and enhance efficiency.
- Automation and Smart Technologies: Automation reduces human error and increases production speed. Smart technologies, such as the Internet of Things (IoT), connect equipment for better process control.
- Supply Chain Transparency: Technology fosters clearer visibility across the supply chain. Better tracking reduces delays and optimizes inventory management, ultimately affecting the bottom line positively.
Through digital transformation, chemical manufacturers can not only improve operational efficiencies but also adapt more swiftly to market demands.
The future of chemical manufacturing hinges on these trends. By adopting sustainability initiatives and embracing digital transformation, the industry can address current challenges while preparing for future opportunities.
Culmination
The conclusion serves as a pivotal element in this article, synthesizing the key points discussed throughout the various sections. It encapsulates the essence of chemical manufacturing, emphasizing its multifaceted nature and its crucial role across different industries. Understanding the complexities involved ensures that students, researchers, and professionals appreciate the scope and impact of this sector.
A thorough review of the main topics covered in the article reflects the need for accountability and innovation in chemical manufacturing. Each point raised β from fundamental processes to technological advancements β contributes to a holistic comprehension of the subject. This encourages readers to consider how these factors interrelate in practice.
Moreover, the conclusion prompts reflection on current trends and future directions within the industry. As professionals engage with the information presented, they can better navigate the challenges and opportunities that lie ahead. The various threads woven throughout the article underline how imperative it is to approach chemical manufacturing with informed strategies that align with sustainability initiatives and regulatory frameworks.
"The future of chemical manufacturing rests on balancing innovation with responsibility."
Summary of Key Points
In summation, the key points of this article include:
- The definition and scope of chemical manufacturing and its evolutionary history.
- Fundamental processes: synthesis techniques, separation processes, and purification methods.
- The distinction between batch and continuous production, along with the role of automation.
- Various applications in sectors like pharmaceuticals, agriculture, and industrial chemical production.
- Environmental considerations, including pollution control and adherence to health regulations.
- Regulatory frameworks governing practices on both global and local levels.
- Innovations emerging from nanotechnology and biotechnology, alongside the impact of smart manufacturing.
- Challenges like supply chain disruptions and managing costs in an evolving economic landscape.
- Future trends emphasizing sustainability and digital transformation in chemical manufacturing.
By summarizing these points, we highlight the interconnectedness of the manufacturing processes and the need for ongoing dialogue and education in the field.
Implications for Future Research
Future research in chemical manufacturing should focus on several critical areas:
- Enhanced sustainability practices, examining ways to integrate eco-friendly methods into production.
- The development of alternative raw materials that reduce dependence on traditional sources, thereby mitigating ecological impact.
- Further exploration of digital transformation and its potential to optimize efficiency and reduce waste across the manufacturing chain.
- Investigation into health and safety advancements, ensuring that manufacturing processes continue to safeguard worker wellbeing.
Research initiatives that address these themes will contribute significantly to the evolution of chemical manufacturing. They can help create a more resilient, sustainable industry that caters to the demands of the present while preparing for future transformations.