Understanding Color Masterbatch: Applications and Impact
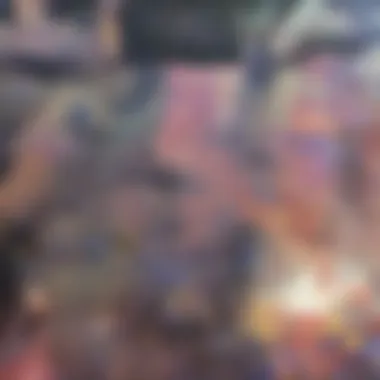
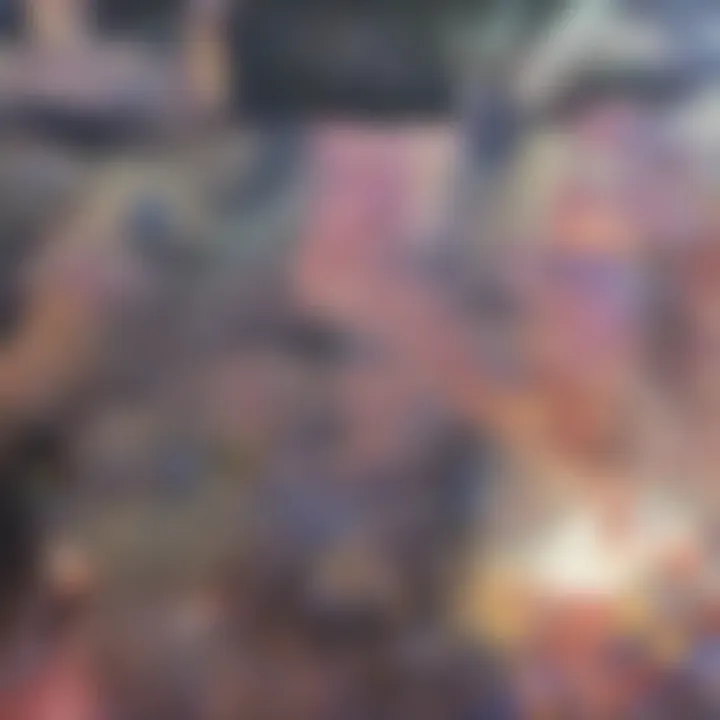
Intro
Color masterbatches are essential in many industries, offering a unique solution for adding color to various materials. As manufacturing processes evolve, understanding the compositional aspects, applications, and the impact of these masterbatches becomes critical. This article aims to break down the complexities surrounding color masterbatches, exploring their definitions, production processes, and broader industry implications. The goal is to provide a meticulous overview tailored for students, researchers, educators, and professionals seeking to enhance their knowledge in this field.
Key Concepts and Terminology
Definition of Key Terms
To comprehend color masterbatches fully, it is vital to first clarify some key terms:
- Color Masterbatch: A concentrated mixture of pigments and additives, encapsulated in a carrier resin. They are used in the manufacture of plastics to achieve desired colors.
- Carrier Resin: A base polymer that serves as a medium for pigments and additives in masterbatches. Various types of resins can be utilized depending on the application.
- Pigments: These are substances that provide color to materials. They can be organic or inorganic, depending on the desired properties.
- Additives: Additional substances mixed into the masterbatch to improve performance, such as UV stabilizers, anti-oxidants, or processing aids.
Concepts Explored in the Article
The article examines multiple concepts surrounding color masterbatches, including:
- The compositional aspects of color masterbatches, detailing how pigments and additives work together.
- Diverse applications across various industries, highlighting where and how color masterbatches are utilized.
- The production processes used to create masterbatches and how these influence their quality and functionality.
- The advantages and challenges in the adoption of color masterbatches in manufacturing.
Findings and Discussion
Main Findings
Throughout this analysis, several critical findings emerge:
- Color masterbatches significantly improve efficiency in the coloring process of plastics. Using masterbatches simplifies the blending and results in a more uniform color.
- There is a growing trend toward the adoption of sustainable and eco-friendly pigments. Companies are exploring bio-based alternatives to reduce environmental impact.
- The quality of the masterbatch plays a crucial role in its performance. Variability in production processes can affect consistency, requiring stringent quality controls.
"Color masterbatches not only add aesthetic value but also enhance the mechanical properties of the final products."
Potential Areas for Future Research
Looking ahead, several areas require further exploration:
- Research into new sustainable materials that can be used as carrier resins or additives may contribute to greener manufacturing practices.
- Investigating the long-term durability and stability of various pigments under different environmental conditions is also essential.
- There could be advancements in technology for more precise application in color processing, potentially leading to improvements in efficiency and product quality.
Through this exploration of color masterbatches, the importance of technical understanding in modern manufacturing becomes evident. As industries continue to evolve, the role of color masterbatches will likely remain central to innovation and productivity.
Preamble to Color Masterbatch
Color masterbatch plays a crucial role in the world of materials science and manufacturing. It refers to a concentrate of pigments and additives that are uniformly mixed with a host polymer to produce colored products. This blend enhances the aesthetic appeal of plastics while maintaining their performance characteristics. Understanding color masterbatch is vital for industries that rely on colored plastic components, as it affects both the quality and functionality of the final product.
The significance of color masterbatch extends beyond mere color. It influences factors such as processing efficiency, cost-effectiveness, and product safety. As businesses strive to create more visually appealing and efficient products, color masterbatch becomes a key element in the production process.
In addition to aesthetics, color masterbatch incorporates technical benefits. It facilitates consistency in shades and reduces the likelihood of defects. Masterbatch is not just about visual appeal; itβs about achieving high standards in product quality. In this sense, color masterbatch is integral to the modern manufacturing landscape.
Definition and Importance
Color masterbatch is essentially a mixture of colorants and additives within a polymer carrier. This combination allows for the easy dispersion of pigments during the manufacturing process. The importance of color masterbatch lies in its ability to produce a vast range of colors with precision and consistency.
Moreover, utilizing color masterbatch contributes to sustainability in manufacturing. Many suppliers now focus on creating eco-friendly masterbatches that comply with environmental regulations, thus minimizing potential adverse impacts.
Historical Context
The use of masterbatch dates back several decades when the need for consistent coloration in plastic products became apparent. Initially, the industry relied on raw pigments that were difficult to process. As technology advanced, the concept of color masterbatch emerged, enabling manufacturers to simplify their production processes. This historical shift allowed companies to not only enhance the visual appearance of products but also to optimize production efficiency.
The development of color masterbatch technology has been shaped by innovative processes and the evolving demands of various industries. Over the years, manufacturers have continued to refine formulation practices, leading to the introduction of specialized products tailored for specific applications. This evolution highlights the enduring significance of color masterbatch in modern production, driving both aesthetic and functional improvements across multiple sectors.
Composition of Color Masterbatch
The composition of color masterbatch plays a vital role in determining its effectiveness and application across various industries. A deep understanding of the components involved is essential for professionals who ultimately want to formulate high-performance products. Each element contributes not only to the aesthetic aspects but also to the functional properties that can influence product durability, processability, and end-use applications.
Polymer Base Materials
Polymer base materials are the foundational element of color masterbatches. Typically, these are polymers such as polyethylene, polypropylene, and polystyrene. The choice of base material affects the melting temperature, viscosity, and compatibility with the end products. For instance, polyethylene is known for its flexibility, making it suitable for applications requiring a degree of stretch, whereas polypropylene offers higher rigidity and heat resistance.
Each polymer has specific characteristics that can enhance the performance of the color masterbatch. For example, when using polypropylene, the resulting products can exhibit improved impact resistance and mechanical strength. Thus, selecting the right polymer base is a critical first step in developing effective color masterbatches.
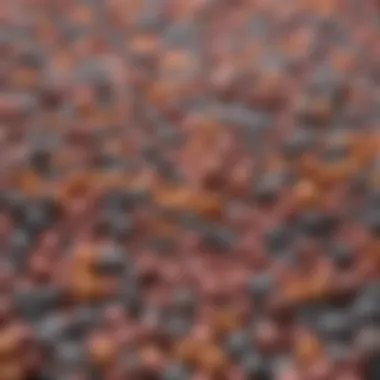
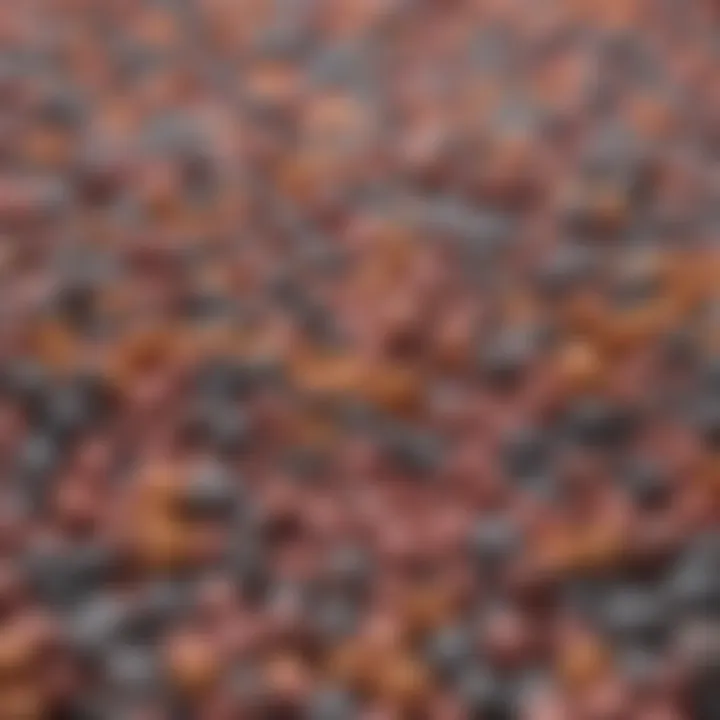
Colorants Used
Colorants, which can be either organic or inorganic, are crucial for providing the desired color. Organic colorants are often vibrant and suitable for a range of applications; however, they may have lower stability when exposed to UV light or heat. In contrast, inorganic colorants tend to be more stable, offering durability and lightfastness.
Key factors to consider when selecting colorants include:
- Light Fastness: The ability to maintain color under sunlight exposure.
- Heat Stability: Resistance to changes in color at high processing temperatures.
- Toxicity: Ensuring compliance with safety regulations in various industries.
In many instances, the choice of colorants directly affects the appeal of the final product. Colors can influence buyer perceptions and market competitiveness, making this selection process crucial for companies.
Additives and Processing Aids
The third component in the composition of color masterbatches is the additives and processing aids. These substances serve various purposes, such as enhancing processability, improving mechanical properties, and modifying surface characteristics. For example:
- Slip Additives reduce friction during processing, which improves the flow of materials.
- Anti-Block Agents prevent sheets from sticking together, facilitating easier handling and processing.
- UV Stabilizers protect against degradation caused by UV radiation, enhancing the longevity of the end product.
Additives can also impart specific qualities like improved gloss or matte finishes, which can be particularly important in consumer goods packaging. The balance between the primary components and these additional substances can lead to innovations that fulfill specific market needs.
Production Processes for Color Masterbatches
The production processes for color masterbatches are critical to their functionality and efficiency in a variety of applications. These processes determine not only the quality of the masterbatch but also its suitability for specific end-product requirements. Each method of production introduces unique characteristics to the final product, influencing factors such as color precision, consistency, and ease of integration into manufacturing systems. Understanding these processes allows manufacturers to select the most appropriate techniques tailored to their needs while maintaining high standards of quality control.
Extrusion Techniques
Extrusion is a predominant technique used for manufacturing color masterbatches. It involves forcing a mixture of additives, polymer, and pigments through a die to form the desired shape. The benefits of this method include:
- Uniform Mixing: Extrusion ensures that colorants are evenly distributed within the polymer matrix, leading to consistent color quality.
- Scalability: This method can be adapted for large scale production, making it suitable for industrial use.
- Versatility: Various polymers and colorants can be used, offering flexibility in product design.
Despite its advantages, the extrusion process requires precise control of temperatures and pressures. Inaccurate settings can lead to color degradation or inconsistent product quality. Therefore, professionals need to be vigilant and knowledgeable about the materials being processed.
Batch Processes
Batch processes are another common method for producing color masterbatches. In this approach, a specified amount of materials is combined and processed, often in smaller quantities compared to extrusion. This method offers several advantages:
- Controlled Environment: Production can be closely monitored, which helps in maintaining high quality and reducing variability in color.
- Customization: Batch processing allows for small adjustments in formulation, making it easier to meet unique customer specifications.
- Shorter Production Runs: This setup is ideal for manufacturers who require less frequent production but need to maintain a variety of colors.
However, the batch process can result in longer processing times and may not offer the same level of efficiency as continuous extrusion. Manufacturers must weigh these factors based on demand and production needs.
Quality Control Measures
Quality control is a crucial aspect throughout the production of color masterbatches. Implementing strict quality assurance protocols ensures that the end product meets both performance and aesthetic expectations. Some important quality control measures include:
- Testing Viscosity: Monitoring viscosity helps in assessing the flow characteristics, ensuring the masterbatch is suitable for the intended processing method.
- Color Evaluation: Regular assessment against color standards helps in maintaining consistency and adherence to customer requirements.
- Material Testing: Testing raw materials before they enter production can prevent inconsistencies and unwanted surprises later in the process.
"Quality control in color masterbatch production is not just about the end product; it starts from raw material selection and continues through every stage of processing."
Overall, effective quality control not only safeguards the productβs integrity but also protects the manufacturer's reputation.
Applications of Color Masterbatch
The applications of color masterbatch are diverse and critical in various industries. Understanding these applications enhances the appreciation of their role in modern manufacturing while also highlighting the benefits they offer. This section explores how color masterbatches are integrated into different products and processes. Their usage not only impacts the visual appeal but also the functionality and durability of the final products.
Packaging Materials
Color masterbatches are widely used in the packaging sector. They provide consistency in color across large production runs, which is essential for branding and customer recognition. Packaging is often the first point of contact for consumers with a product, making its color choice pivotal. Using color masterbatch can improve UV stability, thus prolonging the life of packaging materials against fading. Moreover, the addition of colorants can modify the mechanical properties of the polymer, enhancing its barrier functions against moisture or gases.
Consumer Goods
In the world of consumer goods, color masterbatches play a significant role in product differentiation. Many products rely on color to attract consumers and convey brand identity. For example, household items like containers or appliances often utilize vibrant colors that are achievable through masterbatches. The ability to achieve uniform color helps ensure that the product not only looks appealing but also meets quality standards. Additionally, these colorants can often offer additional properties, for instance, anti-bacterial effects, which are becoming increasingly desirable in todayβs market.
Automotive Industry
The automotive industry also heavily relies on color masterbatch. In this context, color is more than aesthetic; it can enhance the performance and durability of vehicle components. For instance, using black masterbatch in the production of bumpers can provide UV protection, reducing degradation over time. Additionally, interior parts benefit from carefully selected colors and surface textures that can improve comfort and appeal. Efficient use of color masterbatch in automotive applications leads to reduced waste and streamlined processes, reinforcing its significance in this competitive sector.
Construction Materials
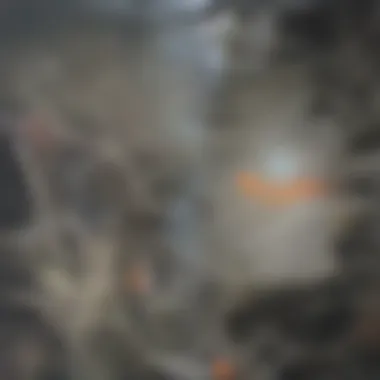
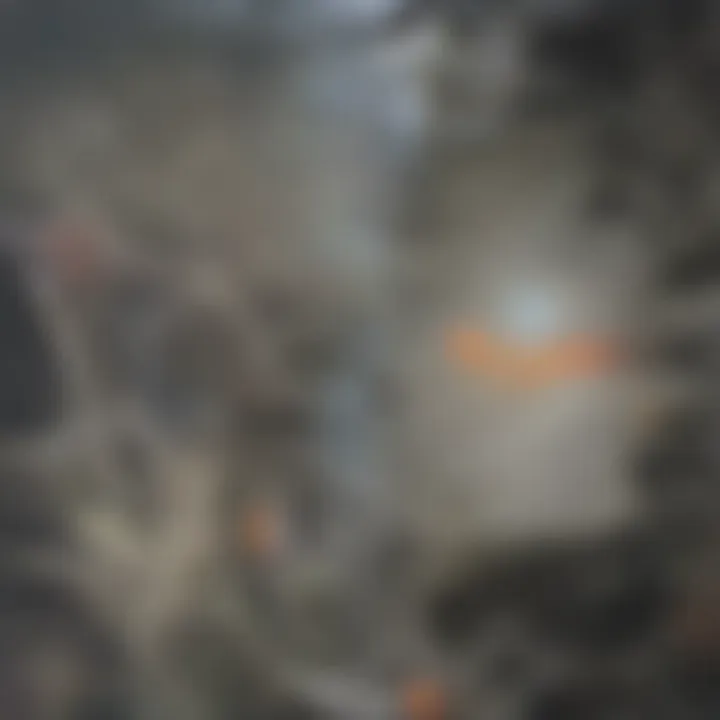
In construction, color masterbatch is important for aesthetic and functional reasons. Building materials such as concrete and tiles can incorporate color masterbatch to offer a wide range of appealing options. This can elevate the visual aspect of buildings and structures significantly. Moreover, colored masterbatches can contribute to heat reflection, helping to improve energy efficiency in buildings. Differences in surface coatings can also lead to increased durability and maintenance properties, which are critical in both residential and commercial construction.
"The application of color masterbatch is integral in shaping products not just for aesthetics but also for their functional capabilities."
Advantages of Using Color Masterbatch
Color masterbatch presents a variety of benefits that are crucial for manufacturers across several industries. Understanding these advantages sheds light on why color masterbatch has become a preferred solution in modern production environments. The benefits include consistent color quality, improved processing efficiency, and enhanced environmental sustainability. These factors not only elevate product quality but also contribute to operational effectiveness and ecological responsibility.
Consistent Color Quality
One of the prominent advantages of color masterbatch is its ability to provide consistent color quality across batches. This consistency is vital, especially in industries like packaging and consumer goods, where color variations can lead to significant issues in branding and product perception. With color masterbatch, manufacturers can ensure that each production run maintains the same hue and shade. This reliability stems from the precise formulation of colorants and additives provided in masterbatch. As a result, companies can avoid costly reworks and maintain a strong brand identity in the marketplace.
Improved Processing Efficiency
The use of color masterbatch can significantly improve processing efficiency. By integrating colorants with polymer bases through controlled processes, manufacturers can minimize the need for downstream mixing and blending. The masterbatch is designed for easy incorporation into the production process, which reduces equipment wear and tear and lowers energy consumption. Additionally, the pre-measured formulation ensures that manufacturers do not have to spend additional time on color adjustments. This streamlined operation can lead to higher throughput and reduced cycle times, ultimately enhancing profitability in production environments.
Enhanced Environmental Sustainability
Sustainability is an increasing concern in manufacturing, and color masterbatch plays a role in this regard. Using color masterbatch can lead to reduced waste, as it enables more accurate dosing compared to traditional coloring methods. This precision minimizes the amount of excess material that often ends up discarded. Furthermore, many manufacturers are now producing eco-friendly formulations of color masterbatch, utilizing recycled materials and non-toxic colorants.
This shift towards sustainability is not just a response to regulatory demands; it has become a competitive advantage in attracting environmentally conscious consumers.
Challenges and Limitations
The topic of challenges and limitations in color masterbatch production is crucial. Addressing these issues helps stakeholders understand the complexities and potential obstacles they may encounter. Awareness brings transparency and allows for better preparation in both manufacturing and marketing.
Variability in Color Production
Color consistency is a significant factor in the usage of color masterbatches. Variability can arise from several sources. The quality of raw materials used can change based on the supplier or batch. Even slight variations in the mixing process can lead to differences in the final color. This inconsistency can affect product quality, and ultimately, brand reputation.
Maintaining standardized processes is necessary to mitigate this variability. Quality assurance measures, such as routine testing and monitoring, must be implemented. Manufacturers should document production parameters to recognize patterns in variability.
"The quest for color consistency in masterbatch production is ongoing and necessitates stringent quality control measures."
Cost Considerations
Cost is an essential element in the decision to use color masterbatches. Initial expenses can be higher than using traditional coloring methods. This includes costs of higher-grade colorants and additives. However, the long-term benefits need to be evaluated.
These include:
- Improved processing efficiency, leading to reduced labor costs.
- Higher quality end-products, which can command better prices in the market.
- Reduced waste, which can cut down materials cost in the long term.
The long view in investments often pays off when evaluating cost versus quality. However, manufacturers must carefully analyze their production needs to justify the initial expenses.
Handling and Storage Issues
The handling and storage of color masterbatches come with specific challenges. These materials can be sensitive to external conditions such as temperature and humidity. Improper storage can lead to clumping or degradation of the colorants, affecting performance in later stages.
It is important to establish best practices for storage, including:
- Maintaining a controlled environment to prevent the exposure of masterbatches to moisture.
- Using appropriate containers to prevent contamination during storage.
- Implementing a first-in, first-out (FIFO) policy to manage inventory effectively.
Attention to these factors can lead to better preservation of quality and consistency in production. Understanding these limitations enables successful navigation and enhances the application of color masterbatches in different industries.
Recent Trends in Color Masterbatch Technology
The evolution of color masterbatch technology is crucial in addressing the demands of modern industries. As markets become more competitive, companies seek innovative solutions that not only meet functional requirements but also resonate with consumer preferences. Recent advancements in this field showcase how technology can enhance not just performance but also environmental considerations.
Innovations in Colorant Technology
Advancements in colorant technology are redefining the capabilities of color masterbatches. New formulations now offer improved resistance to fading, which allows products to maintain their aesthetic appeal over longer periods. Companies are developing more vibrant colorants that enhance product visibility in the marketplace. Additionally, the introduction of specialty additives has enabled manufacturers to create color masterbatches that are compatible with a variety of polymer types. This flexibility promotes wider application across different manufacturing processes, ranging from extrusion to injection molding.
The use of high-performance pigments is a noteworthy trend. These pigments not only offer superior vibrancy but also contribute to better performance in applications exposed to harsh environmental conditions. Alongside these enhancements, the shift towards non-toxic and eco-friendly colorants is prominent. Manufacturers are increasingly opting for organic pigments that minimize health hazards while still achieving the desired color quality. As the demand for sustainable practices grows, incorporating safe colorants becomes not just a preference but a necessity.
Advancements in Sustainability Practices
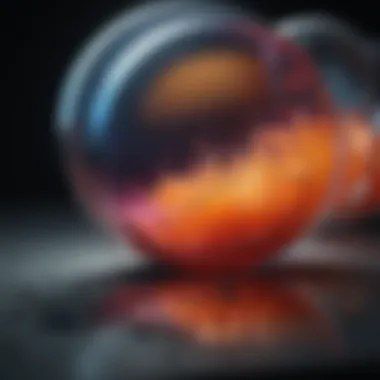
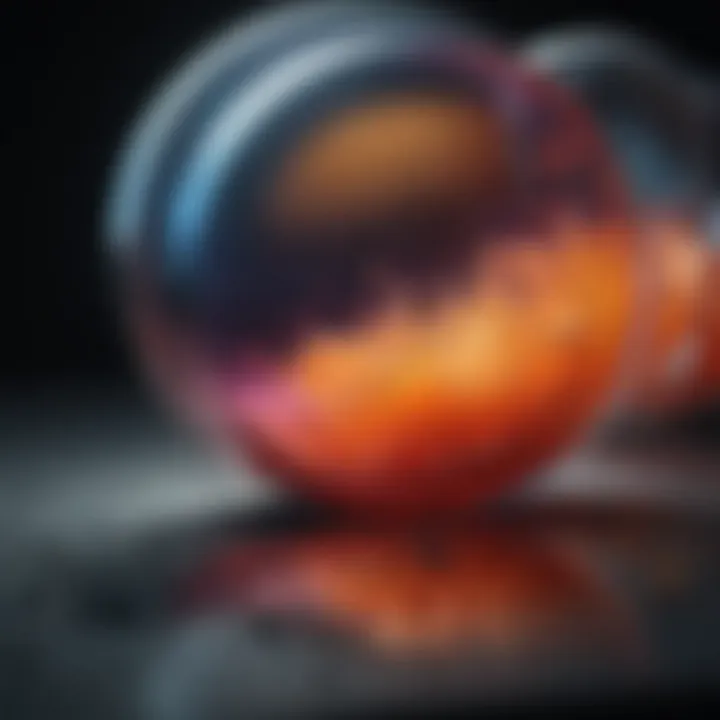
Sustainability is central to recent developments in color masterbatch technology. With heightened awareness of environmental issues, the industry is making substantial strides toward reducing its carbon footprint. Many companies are adopting renewable resources for both the base polymer and colorants to minimize reliance on fossil fuels. The result is a greener product offering that appeals to environmentally conscious consumers.
Furthermore, practices such as recycling and reusing materials are becoming standard. The establishment of closed-loop systems allows manufacturers to reclaim waste streams from production processes, transforming them back into valuable color masterbatch. This not only reduces waste but also cuts material costs, showcasing the financial benefits of sustainable practices.
Efforts in waste reduction extend to packaging as well. Companies are re-evaluating their packaging options and transitioning to biodegradable materials that align with the sustainability goals. Some manufacturers even explore innovative packaging design that reduces overall material usage while maintaining protection and aesthetic integrity.
"The trend toward sustainable color masterbatch not only benefits the environment but also enhances brand reputation and consumer loyalty."
In summary, innovations in colorant technology and advancements in sustainability practices are reshaping the future of color masterbatches. The impact of these trends goes beyond just functionality; they drive the market toward more responsible and conscious practices.
Case Studies on Color Masterbatch Applications
Case studies serve as a critical examination tool within the color masterbatch domain. They provide tangible evidence of how theoretical principles translate into practical outcomes. Analyzing these real-world applications helps industry stakeholders understand the efficacy, benefits, and challenges associated with color masterbatches in various contexts. This section explores notable examples and highlights important lessons learned from their implementation.
Successful Implementation in Industry
One significant case study involved the use of color masterbatches in packaging materials. A leading manufacturer in the food packaging sector decided to enhance its product line by employing color masterbatches. The company aimed to achieve consistent color quality while maintaining compliance with safety regulations. The implementation was successful due to several factors:
- Color Consistency: Utilizing specialized color masterbatches ensured uniformity across all production runs, reducing the risk of color variation.
- Material Compatibility: The chosen masterbatches were perfectly compatible with the polypropylene used in packaging, enhancing the mechanical properties of the final products.
- Cost Efficiency: The manufacturer noted a decrease in production waste due to the precise dosing of colorants in the masterbatches.
This case underlined the versatility of color masterbatches in achieving both aesthetic and functional requirements. It also demonstrated the importance of strategic supplier partnerships to secure high-quality materials and technical support.
Comparative Analysis of Products
To further enrich the understanding of color masterbatch applications, a comparative analysis was conducted involving different brands of color masterbatches used in automotive components. Two competing companies, BASF and Clariant, focused on color solutions for their automotive interior parts. Key findings from this analysis included:
- Performance Metrics: Each product was evaluated based on durability, heat resistance, and fade resistance under exposure to sunlight.
- Color Range: The available color options differed significantly; BASF offered a broader range that catered to unique customer preferences.
- Sustainability: Clariant's masterbatches had a more substantial emphasis on sustainability practices, aligning with industry trends towards environmentally-friendly solutions.
"The comparative analysis reveals that while performance is paramount, aspects such as range and sustainability are increasingly influential in decision-making."
This analysis provided insights not only into product performance but also into market positioning and emerging trends. Understanding these differences equips companies with the knowledge to make informed decisions on selecting the right color masterbatch for their needs.
Future Outlook of Color Masterbatch Industry
The future of the color masterbatch industry is integral to the broader landscape of manufacturing and production processes across a wide array of sectors. As industries continue to seek greater efficiency and sustainability, color masterbatch technology is expected to play an even more pivotal role. Understanding the future direction of this field can uncover opportunities for innovation and growth.
Predicted Market Trends
Several trends are shaping the future of the color masterbatch market. There are increasing demands for environmentally friendly solutions. Manufacturers are turning to bio-based colorants and recyclable materials. These shifts align with the global call for sustainability, pushing companies to reduce their environmental footprint.
Another notable trend is the rise of automation in production processes. Automation enhances processing speed and ensures consistent quality. This is especially important in high-volume applications where consistency is crucial. Advanced digital technologies like big data and machine learning are also being incorporated, facilitating more precise quality control and supply chain management.
Conditions within various industries also affect the color masterbatch market. For example, the packaging sector is expected to continue expanding due to growth in e-commerce. More colorful and creative packaging solutions can elevate brand presence and consumer engagement. Thus, a surge in demand within packaging can drive innovation in color masterbatches to meet specific market needs.
The Role of Regulatory Changes
Regulatory changes are a significant aspect of the color masterbatch industry. As consumer awareness about environmental issues rises, regulations governing the use of colorants and additives become more stringent. Compliance with these regulations is essential for any manufacturer looking to remain competitive.
Innovations in colorant technology often arise from these regulatory pressures. Manufacturers are encouraged to develop safer, non-toxic alternatives that meet compliance standards. The shift toward natural colorants and additives not only benefits product safety but also enhances brand reputation.
Additionally, the labeling of products is taking on new importance. Stricter regulations concerning transparency in ingredient disclosure are leading companies to rethink their formulations. By embracing this trend, manufacturers can build trust with consumers, ensuring their loyalty.
"In a rapidly evolving market, staying ahead of regulatory changes can provide strategic advantages to manufacturers."
In summary, the future outlook for the color masterbatch industry is marked by a complex interplay of market trends and regulatory changes. Embracing sustainability, innovation, and compliance will be essential for participants in this field to thrive. By understanding these dynamics, stakeholders can position themselves effectively for the challenges and opportunities that lie ahead.
End
Understanding the conclusion of this article on color masterbatch is key to grasping its significance in modern manufacturing. Throughout the sections, we have highlighted the complex composition, diverse applications, and the broader industry implications of color masterbatch technology. The conclusion serves as a synthesis of the primary topics addressed, reinforcing the importance of color masterbatches in various sectors.
Color masterbatches offer several benefits, such as enhanced processing efficiency, consistent color quality, and improved environmental sustainability. The strategic incorporation of colorants into the production process not only meets aesthetic demands but also fulfills functional requirements across industries, including packaging, automotive, and consumer goods. By focusing on the relevant trends and challenges, this article provides valuable insights that can guide professionals in making informed decisions regarding color masterbatch use.
Recap of Key Takeaways
- Definition and Importance: Color masterbatches are vital for achieving desired aesthetics in plastic products.
- Composition Insights: These masterbatches consist of polymer base materials, colorants, and additives.
- Applications: They find utility in packaging materials, consumer goods, automotive industry, and more.
- Advantages: Benefits include consistent quality, processing efficiency, and sustainability.
- Challenges: Variability in production, costs, and handling issues must be navigated.
- Future Trends: There are ongoing innovations in technology and sustainability efforts that impact the industry.
Final Thoughts on Color Masterbatch
"The evolution of color masterbatch technology reflects broader industry trends and societal demands for sustainability and aesthetics."
As we move forward, the knowledge gained from exploring color masterbatches will be crucial for researchers, educators, and professionals alike in optimizing manufacturing processes and adopting new strategies. Their impact reaches beyond mere appearance, influencing efficiency, cost, and environmental outcomes.