Understanding Etching Primers for Anodized Aluminum
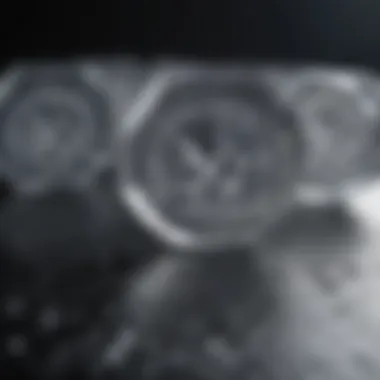
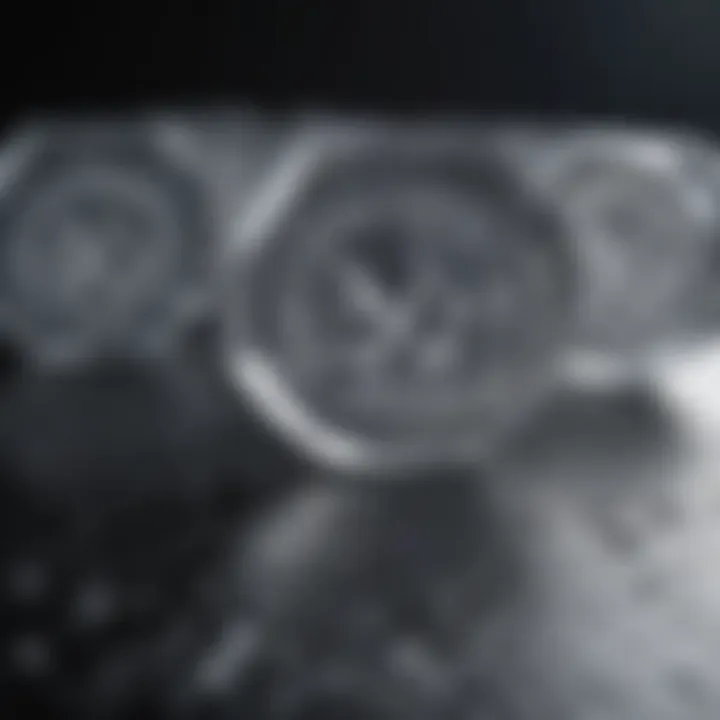
Intro
The use of etching primers has become increasingly significant in the context of anodized aluminum surfaces. Anodizing enhances the natural oxide layer on aluminum, providing corrosion resistance and improved aesthetic appeal. However, the inherent smoothness of anodized surfaces poses challenges for effective coating adhesion. Thus, etching primers are formulated to prepare these surfaces, allowing subsequent coatings to bond securely.
In this analysis, we will delve into the fundamental properties, benefits, and application techniques of etching primers tailored for anodized aluminum. With a focus on practical applications, the article is directed at students, researchers, and professionals in materials science and engineering. By understanding the key concepts and terminologies involved, the readers will gain insights necessary for making informed decisions surrounding etching primers.
Key Concepts and Terminology
Definition of Key Terms
To fully grasp the nuances of this topic, it is crucial to define a few key terms:
- Etching Primer: A specialized coating designed to enhance adhesion on smooth surfaces, especially metals like anodized aluminum.
- Anodized Aluminum: Aluminum that has undergone an electrochemical process to increase its oxide layer for enhanced durability and resistance.
- Surface Preparation: The method of cleaning and treating a surface to facilitate proper adhesion of coatings.
Concepts Explored in the Article
This article will explore several important concepts, including:
- The chemical composition of etching primers and how it contributes to their efficacy.
- Techniques for applying etching primers to anodized surfaces, including surface preparation practices.
- The environmental impact and regulatory considerations associated with using these products.
Findings and Discussion
Main Findings
Research indicates that etching primers are particularly effective in promoting the adhesion of paints and adhesives to anodized aluminum. The primers function by creating micro-roughness on the smooth anodized surface, enhancing mechanical bonding. Additionally, they often contain acids or other chemicals that can etch the oxide layer further, improving bonding potential.
Potential Areas for Future Research
Future investigations could focus on several areas:
- Development of eco-friendly etching primers with reduced hazardous compounds.
- Comparative studies of various etching primer formulations to determine optimal combinations for specific applications.
- Long-term performance evaluations of coatings applied over different etching primers under diverse environmental conditions.
Understanding these aspects of etching primers is vital for advancing knowledge in materials science and engineering, especially as it relates to anodized aluminum.
"Understanding the application and effectiveness of etching primers enhances coating longevity and performance in various environments."
Through this comprehensive examination, we aim to provide a valuable resource that combines both theoretical insights and practical guidance.
Preface to Anodized Aluminum
Anodized aluminum is a subject of significant interest in materials science and engineering. It involves a crucial surface treatment process designed to enhance the properties of aluminum. This introduction will set the stage for understanding how anodization affects aluminum and why it is an important consideration when using etching primers.
Definition and Process of Anodization
Anodization is an electrochemical process that converts the surface of aluminum into a durable, corrosion-resistant, anodic oxide finish. This process involves immersing aluminum in an electrolyte bath, often composed of sulfuric acid, while passing an electric current through it. The aluminum itself acts as an anode. As a result, the oxygen in the electrolyte combines with the aluminum to form aluminum oxide, a very hard and dense layer that protects the base metal from degradation.
The anodization process typically includes several key steps:
- Cleaning: Initial cleaning of the aluminum surface is essential. This often involves using alkaline cleaners or solvents to remove grease, dust, and other impurities.
- Anodizing: The cleaned aluminum is immersed in the electrolyte solution and subjected to direct current. The thickness of the anodic layer can be controlled through time and current.
- Sealing: After anodization, the aluminum oxide layer can be sealed to enhance its durability. This sealing process often involves immersing the aluminum in boiling water or using specific sealing agents.
Through anodization, the aluminum develops a number of enhanced properties. These include improved corrosion resistance, increased surface hardness, and better adhesion for paints and coatings process. Understanding the precise nature of these enhancements is crucial when considering products like etching primers.
Properties of Anodized Aluminum
Anodized aluminum boasts several distinctive properties that make it favorable for various applications. Its most notable characteristics include:
- Corrosion Resistance: Anodized aluminum forms a protective oxide layer that prevents further oxidation. This makes it particularly suited for applications in harsh environments.
- Surface Hardness: The anodic coating provides a high degree of hardness, making anodized aluminum resistant to scratches and wear.
- Adhesion Qualities: The porous nature of anodized aluminum allows for better adhesion of paints, seals, and other coatings. This characteristic relates directly to the effectiveness of etching primers used on anodized surfaces.
- Aesthetic Appeal: Anodizing can also add color to aluminum without compromising its surface. This makes anodized aluminum popular in design and architecture.
In summary, the importance of anodized aluminum and its properties cannot be overstated. They form the foundation for subsequent discussions about etching primers, helping to elucidate how these primers interact with the anodized surfaces. Proper grasp of anodization not only aids in application technique but also reveals the multifaceted nature of aluminum as a material.
Understanding Etching Primers
Understanding etching primers is essential for anyone involved with anodized aluminum, from manufacturers to end-users. The role of etching primers extends beyond mere surface preparation; they enhance adhesion, resist corrosion, and contribute to aesthetic quality. Knowing the intricacies of etching primers can vastly improve the performance and longevity of coatings applied to anodized aluminum surfaces.
This section elucidates the definition and purpose of etching primers, followed by a breakdown of their key components. By grasping these fundamentals, readers gain a deeper appreciation of how etching primers influence the coating processes and the resultant material performance.
Definition and Purpose
Etching primers are specialized coatings designed for enhancing the adhesion of subsequent layers, particularly when applied to anodized aluminum. These primers contain a blend of resins, solvents, and abrasive components that effectively roughen the surface of the substrate. This roughening process maximizes the physical and chemical interlocking necessary for effective adhesion.
The purpose of etching primers goes beyond creating a textured surface. They also provide a chemical bonding mechanism that improves the longevity of the coating. Most notably, they form a barrier to environmental factors that are detrimental to the material. Without adequate primer, coatings applied directly on anodized aluminum may fail prematurely due to poor adhesion or corrosion.
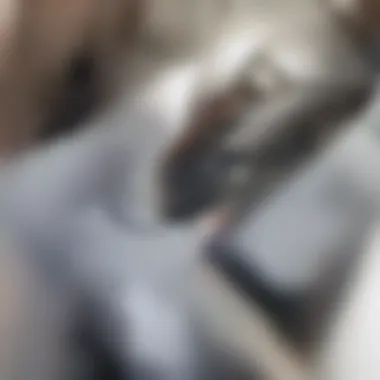
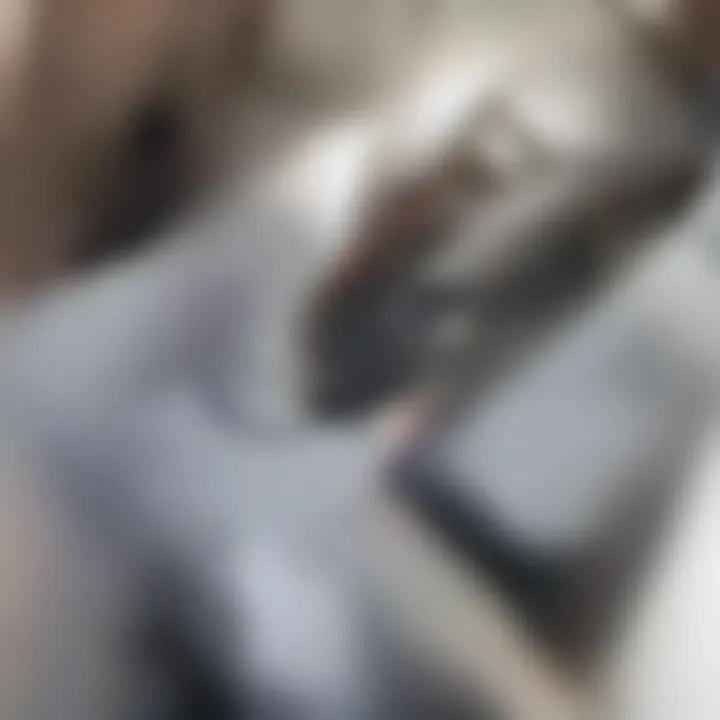
Key Components of Etching Primers
Etching primers consist of several key components that contribute to their effectiveness:
- Resins: Resins are the backbone of the primer, providing the essential adhesive properties. Common types include epoxy and urethane resins, known for their durability and resistance to chemicals.
- Solvents: Solvents play a pivotal role in controlling the viscosity of the primer and facilitating the application process. They evaporate quickly upon application, allowing the resin to solidify and adhere effectively.
- Abrasive Fillers: These materials create a texture on the anodized aluminum surface, which maximizes contact area and improves adhesion. Common fillers include silica and aluminum oxide.
- Additives: Various additives might be included to improve specific properties such as drying time, flow characteristics, or UV resistance.
By developing a comprehensive understanding of these components, professionals can select the right etching primer for their specific application needs.
"The effectiveness of an etching primer can often be the difference between a successful and a failed coating application."
In summary, etching primers are more than just preparatory applications; they are vital in ensuring that subsequent coatings perform well on anodized aluminum. Knowing their definition, purpose, and components provides critical insight for anyone involved in material preparation and finishing processes.
The Chemistry of Etching Primers
The chemistry of etching primers is fundamental to their function and effectiveness when applied on anodized aluminum. Understanding the interactions among various chemical compounds is crucial. This knowledge allows for the optimization of adhesive bonds between the primer and the substrate. Moreover, it reveals how these interactions can enhance the overall performance of coatings applied over the primer.
Chemical Properties and Interactions
Chemical properties of etching primers primarily include their composition and the specific interactions they have with metal surfaces. This type of primer usually contains acids or alkaline agents, which play a significant role in the etching process. The etching operation helps to remove contaminants and creates a rough surface that improves adhesion.
For example, phosphoric acid is commonly used not only for its effectiveness in cleaning the surface but also for its ability to chemically bond to aluminum oxide. This bonding enhances the primer's ability to adhere firmly to the anodized surface. Understanding how the chemical properties influence these interactions is essential for formulators.
"The correct chemical interactions in etching primers are vital for creating a resilient and long-lasting adhesive bond with anodized aluminum surfaces."
Some key chemical interactions to note include:
- Dissolution: Soluble components in etching primers dissolve contaminants.
- Activation: Chemical activity can alter the oxidation state of aluminum, enhancing bonding.
- Hydrophilicity: This property can improve the wetting of primer on the surface, leading to better adhesion.
Impact on Surface Enhancement
The impact of etching primers on surface enhancement cannot be overstated. When properly applied, these primers serve not only as a bonding agent but also can significantly improve the surface characteristics of anodized aluminum. This leads to notable benefits in the performance of final coatings.
One of the primary impacts is the enhancement of adhesive strength. By creating a micro-pattern on the surface, etching primers provide more surface area for mechanical grip, which is essential for coatings that require high durability. Moreover, the primers contribute to improving overall corrosion resistance. The chemical makeup often includes additives that help seal the surface, protecting it from moisture and chemical attack.
In summary, understanding the chemistry of etching primers—especially their chemical properties, interactions, and impacts—is vital. This knowledge aids in choosing the right products and procedures, ultimately fostering better application outcomes. Effective use of etching primers informed by chemistry can lead to superior surface performance in anodized aluminum applications.
Benefits of Using Etching Primers
The use of etching primers in the field of anodized aluminum processing is essential for enhancing performance characteristics in various applications. The etching primer serves to prepare the surface effectively, allowing for superior adhesion of subsequent coatings. It is important to understand the benefits involved in using these products, as they significantly impact overall project outcomes in terms of durability, aesthetics, and long-term maintenance.
Adhesion Improvement
Adhesion is a critical element in ensuring the longevity of any coating applied to anodized aluminum. Traditional primers often fail to provide the necessary bond required for demanding applications. Etching primers, however, chemically and mechanically bond with the aluminum surface. The etching process creates a rough texture that enhances the surface area available for adhesion. This improved contact translates into stronger bonds, greatly reducing the risk of delamination, especially in environments where resistance to wear is necessary.
Corrosion Resistance
Corrosion poses a significant threat to aluminum surfaces, particularly when exposed to moisture and environmental contaminants. Etching primers contribute to corrosion resistance by providing a protective barrier that can withstand various external factors. These primers contain corrosion inhibitors that actively repel rust and other related processes. By utilizing these primers, the lifespan of anodized aluminum components can be significantly extended, lowering maintenance costs and enhancing reliability. It is crucial to consider these properties during selection as they reflect on long-term performance in real-world conditions.
Aesthetic Quality
The visual appeal of anodized aluminum surfaces is often a priority for manufacturers and end-users alike. Etching primers can help maintain high aesthetics through even coating application. They provide a uniform base for subsequent paints or finishes, enhancing the overall look of the product. When correctly applied, these primers help to prevent common issues such as orange peel or gloss variation, ensuring the final appearance meets aesthetic standards required in industries ranging from automotive to architecture. This quality adds value to the product, making etching primers an indispensable element in the finishing process.
"The effective use of etching primers not only improves functionality but also ensures that aesthetic aspects are not overlooked in anodized aluminum components."
Application Techniques
The section on application techniques serves an essential role in understanding how to effectively utilize etching primers on anodized aluminum surfaces. The right application technique not only maximizes the performance of the primer but also ensures that the final coating adheres properly and lasts longer. Key elements include surface preparation, application methods, and the equipment used. Each of these aspects influences the overall quality of the finished product.
Surface Preparation Methods
Before any etching primer is applied, surface preparation is critical. This phase ensures that no contaminants—such as oils, dust, or oxidation—are present. Failure to prepare the surface correctly can lead to poor adhesion and reduced durability of coatings. Common methods for surface preparation include:
- Cleaning with Solvents: Using solvents like acetone or isopropyl alcohol can remove oils and dirt.
- Mechanical Abrasion: Sanding or blasting the surface can provide a rough texture, enhancing adhesion.
- Chemical Etching: This involves using a chemical solution to strip away the anodized layer slightly and create a better bond.
The chosen method depends on the specific application and desired finish. Proper preparation establishes a solid foundation for the primer, ensuring optimal bonding with the anodized surface.
Application Methods and Equipment
Once surface preparation is complete, the next step is the actual application of the etching primer. Different methods have varied efficiency and effectiveness. Some common application techniques include:
- Spray Application: This method offers uniform coverage and is particularly effective for larger surfaces. It also allows for good control over thickness.
- Brushing: Suitable for small areas or touch-ups, brushing permits precise application but may result in uneven coating if not done correctly.
- Roller Application: This method can be useful for larger flat surfaces but may require multiple coats for adequate coverage.
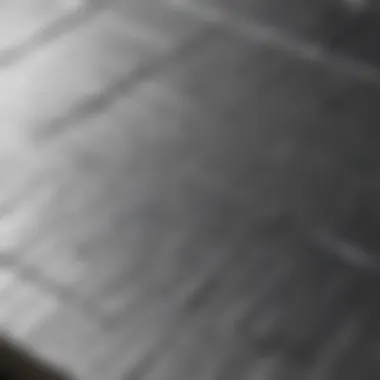
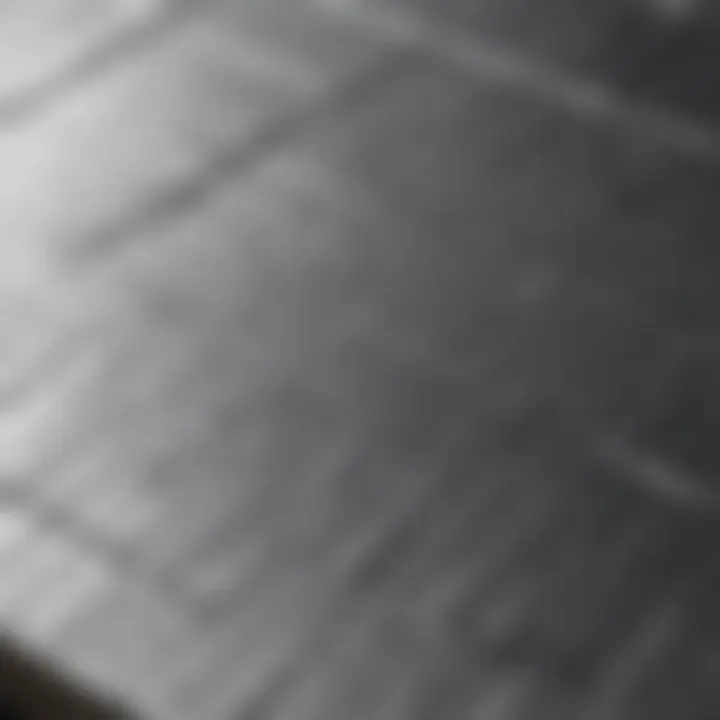
The equipment used is just as important as the method. Conventional spray guns, airless sprayers, and roller brushes each have unique benefits and limitations. The choice of equipment directly affects the ease and quality of application.
Important Note: Proper maintenance of application equipment is vital to prevent contamination, which can compromise the primer's performance.
In summary, mastering application techniques enhances the effectiveness of etching primers for anodized aluminum. Understanding the intricacies of surface preparation and application methods—along with appropriate equipment—contributes significantly to achieving high-quality finishes that meet performance expectations.
Compatibility with Coatings
The compatibility of etching primers with various coatings is critical in the context of anodized aluminum applications. Adherence to the primer ensures a strong bond between layers, which is paramount for the performance and longevity of the final product. When etching primers are compatible with the topcoats, they significantly enhance the overall durability and effectiveness of the surface finish.
Several factors influence the compatibility of etching primers and coatings. These include the chemical composition of both the primer and the coating, the surface texture resulting from etching, and the environmental conditions during application. Ensuring compatibility helps to avoid issues such as peeling, bubbling, or discoloration, which can compromise the aesthetic and protective qualities of the coatings.
Benefits of ensuring compatibility can be summarized as follows:
- Enhanced adhesion: A compatible primer and coating create a stronger chemical bond, leading to better adhesion.
- Increased durability: Properly matched components can withstand environmental stressors, maintaining integrity over time.
- Improved visual appeal: Compatibility promotes a smooth and uniform finish, which enhances the aesthetic quality of the coated surface.
Types of Coatings Used Over Etching Primers
The selection of coatings that can be applied over etching primers is vast, each offering specific benefits tailored to different applications. Common types of coatings used over etching primers on anodized aluminum surfaces include:
- Polyurethane Coatings: Known for their toughness and flexibility, polyurethane coatings provide excellent chemical resistance and durability. They are particularly useful in exterior applications.
- Epoxy Coatings: These offer superior adhesion and corrosion resistance, making them ideal for industrial environments where high performance is required.
- Acrylic Coatings: Acrylics are valued for their UV resistance and clarity. They are often used in decorative applications where appearance is essential.
- Alkyd Coatings: Alkyds provide good adherence and are often used for metal surfaces requiring maintenance and repair.
It is crucial to choose the right coating based on the specific requirements of the application, considering factors such as environmental exposure and desired aesthetics.
Testing for Adhesion and Durability
Testing the adhesion and durability of coatings applied over etching primers is essential for ensuring the performance of the final product. Various methods are available to assess these characteristics, and selecting the appropriate test is dependent on the specific application and requirements.
Common adhesion tests include:
- Pull-off Test: This involves applying controlled force to detach the coating from the substrate. It provides direct measurement of adhesion strength.
- Cross-hatch Test: A grid pattern is cut into the coating, and adhesive tape is applied. The amount of coating removed indicates the adhesive properties.
For durability, tests should evaluate the coating's resistance to:
- Corrosion: Salt spray tests can simulate harsh conditions, providing insights into how the coating holds up over time.
- Impact: Evaluating the coating's performance under mechanical stress helps predict how it will perform in real-world applications.
Ensuring that coatings exhibit strong adhesion and durability is vital in achieving longevity, reducing maintenance costs, and preserving the aesthetics of anodized aluminum products.
Environmental Considerations
The use of etching primers for anodized aluminum is not only significant from a performance standpoint but also crucial from an environmental perspective. As industrial practices evolve, a growing emphasis on sustainable products has emerged. This section addresses the essential environmental considerations related to etching primers, focusing on regulations, compliance, and eco-friendly alternatives.
Regulations and Compliance
Regulatory frameworks play an essential role in guiding the manufacturing and application of etching primers. These regulations typically aim to monitor and control the environmental impact of industrial substances. Manufacturers must adhere to guidelines established by organizations such as the Environmental Protection Agency (EPA) in the United States or similar bodies in other countries.
Specific restrictions may include limits on volatile organic compounds (VOCs), which are common in many etching primers. VOCs can contribute to air pollution and may have adverse health effects. The compliance process often requires manufacturers to provide data on emissions and to demonstrate that their products meet safety and environmental standards.
Businesses using etching primers should stay informed about regional legislation. Non-compliance can result in not only penalties but also risk reputational damage. This landscape requires companies to be proactive in their approach to regulatory compliance, as environmental conditions can change rapidly.
Eco-Friendly Alternatives
As concerns regarding environmental sustainability rise, the development of eco-friendly alternatives to traditional etching primers has gained traction. Such alternatives aim to reduce the environmental footprint while still providing the necessary performance for anodized aluminum applications.
One notable approach is the formulation of water-based etching primers. These products generally contain lower levels of VOCs compared to solvent-based options. Water-based etching primers also present lower health risks during application.
Other advancements include bio-based etching agents derived from renewable resources. These innovative formulations utilize natural compounds that can effectively etch surfaces without the negative environmental impacts associated with synthetic chemicals.
„Sustainability is not just a trend. It is the future of manufacturing.“
When considering eco-friendly alternatives, users must still evaluate the performance aspects. Comprehensive testing ensures that the substitutes offer comparable adhesion, corrosion resistance, and durability. Choosing environmentally responsible products fosters a culture of sustainability within the industry and aligns business practices with contemporary expectations.
In summary, environmental considerations are crucial when using etching primers for anodized aluminum. Compliance with regulations safeguards public health and ecological balance, while the exploration of eco-friendly alternatives supports a more sustainable future.
Market Overview
The market for etching primers tailored for anodized aluminum is essential for various industries, including aerospace, automotive, and construction. Anodized aluminum surfaces require special treatment to achieve optimum adhesion of coatings. Using etching primers is a critical step in this process, making understanding the market dynamics imperative. The relevance of this overview lies in the recognition of leading brands, manufacturers, and prevailing trends. This knowledge equips professionals and researchers with insights needed to make informed decisions.
Leading Brands and Manufacturers
Several brands dominate the market for etching primers specially designed for anodized aluminum. Notably, Bonderite and PPG Industries have established strong reputations due to their extensive research and innovative formulations.
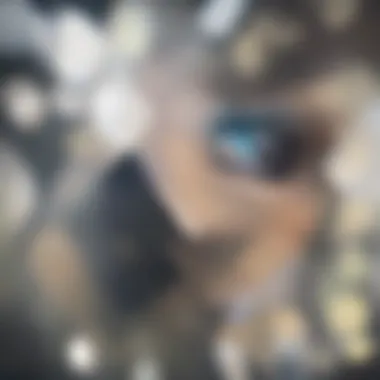

- Bonderite: Bonderite's etching primers are recognized for their enhanced adhesion properties and corrosion resistance. They are used in various sectors, reinforcing the importance of their performance.
- PPG Industries: PPG offers a wide array of primers that cater to specific needs in different applications. Their products are considered reliable, often preferred for critical aerospace components.
Other manufacturers like Dupon and Sherwin-Williams also contribute significantly, pushing the envelope on technology and formulations. These companies focus on continuous improvement and compliance with regulatory standards, which further solidifies their market presence.
Trends in the Industry
The industry for etching primers reflects a few notable trends that shape its future.
- Eco-Friendly Formulations: There is a significant push towards developing environmentally friendly products. Many companies aim to reduce volatile organic compounds (VOCs) in their formulations.
- Technological Advancements: Innovations in chemistry are leading to improved adhesion properties and reduced drying times. Notably, new formulations are being developed to cater to the increasing needs of specialized sectors.
- Regulatory Compliance: As regulations regarding environmental safety become more stringent, manufacturers are adapting to ensure that their products comply. This trend assures customers that products will maintain performance while being safe for the environment.
"Staying ahead in market trends is crucial for manufacturers and users alike to ensure optimal performance and compliance with evolving standards."
These dynamics highlight the necessity for continuous adaptation and understanding of manufacturing processes, which ultimately affects the choice of etching primers users make in diverse applications.
Case Studies
Through case studies, researchers and professionals can see not only the effectiveness of etching primers but also how they can be misapplied or misformulated, resulting in failures. This analysis leads to informed decision-making and enhances future applications in different contexts.
Successful Applications of Etching Primers
In this subsection, various successful applications of etching primers on anodized aluminum will be explored. For instance, in the aerospace industry, etching primers are commonly used to prepare aluminum components for high-performance coatings. The process has been shown to significantly increase adhesion, which is critical in applications exposed to extreme conditions.
Additionally, automotive manufacturers have adopted etching primers to enhance durability and visual appeal. These primers support improved adhesion of topcoats, leading to longer-lasting finishes. Companies like Boeing, and Ford report reducing maintenance costs by using etching primers efficiently.
Benefits of conducting thorough case studies in successful applications include:
- Documentation of best practices: Clear guidance can be established based on previous successes.
- Benchmarking for quality: Companies can measure their outcomes against successful case studies to refine their processes.
- Innovation stimulation: Analysis of successful applications encourages new formulations and techniques to be developed.
Successful application of etching primers can lead to significant improvements in product performance and aesthetics.
Failures and Lessons Learned
Mistakes in the application of etching primers can lead to severe repercussions. Examining failures is as vital as studying successes, as both provide insightful lessons. For example, in a notable case in the construction industry, an etching primer was applied incorrectly, leading to significant delamination of the coatings. The root cause determined was improper surface preparation, highlighting the critical importance of following established protocols.
Another example occurred in the consumer electronics sector, where an etching primer's formulation was not compatible with the subsequent coatings. This resulted in peeling and a poor finish, impacting product functionality and customer satisfaction.
Some critical lessons from these failures include:
- Importance of Surface Prep: Consistent surface preparation practices must be adhered to prevent failures.
- Testing Compatibility: Ethching primer formulations should be tested with specific coatings before large-scale application to ensure compatibility.
- Adapting to Environment: It is essential to consider environmental factors that might affect primer performance.
In summary, case studies analyzing both successful applications and failures of etching primers provide valuable insights. They reveal the importance of proper application techniques and highlight the myriad of factors that influence success. These case studies serve as beneficial tools for educators, researchers, and professionals seeking to deepen their understanding of etching primers.
Future Directions
The future of etching primers for anodized aluminum presents numerous opportunities for innovation and refinement. As industries continue to demand high-performance materials, the importance of advancing etching primer technology can not be overstated. One specific element of focus is the development of primers that not only enhance adhesion but also exhibit multimodal properties suitable for various environmental conditions.
The benefits of pursuing research in this area include improved durability and sustainability of coatings. Enhanced formulations can contribute to greater resistance against corrosion, wear, and environmental degradation. Considering that anodized aluminum is widely used in construction, transportation, and consumer goods, any improvement in etching primers directly benefits these sectors.
Research Opportunities
In the realm of etching primers for anodized aluminum, researchers have several areas ripe for exploration. One promising avenue is the study of bio-based components in primer formulations. These materials could replace traditional solvents, offering a more eco-friendly option. Additionally, exploring nanotechnology could lead to the creation of advanced primer systems that improve bonding strength and enhance surface characteristics at a molecular level.
Another area for investigation is the optimization of application methods. Research into spray techniques or electrostatic application could lead to more uniform coverage and efficiency. Studies focusing on various substrate pretreatments could also yield insights into maximizing primer effectiveness.
Innovative Formulations
The landscape of etching primers is evolving, with a clear shift towards innovative formulations. Manufacturers are now more inclined toward creating multi-functional primers that address not only adhesion but also additional performance characteristics such as hydrophobicity and UV resistance.
Incorporating smart materials into etching primers represents a groundbreaking direction. These materials can respond to environmental stimuli, enhancing their functionality in real-time. For instance, primers that release inhibitors in corrosive environments can significantly extend the lifespan of anodized aluminum surfaces.
Exploring alternative curing methods, such as ultraviolet or LED curing, can also be beneficial. These technologies can reduce drying times and improve adhesive properties significantly.
Epilogue
The conclusion of this article provides a vital recap of the key elements regarding etching primers for anodized aluminum. With the growing emphasis on material efficiency and surface performance in various industries, the role of etching primers cannot be overstated. They enhance adhesion, provide corrosion resistance, and contribute to the aesthetic qualities of finished products. Understanding these elements is crucial for students, researchers, and professionals who aim to optimize the application and performance of anodized aluminum.
Summary of Key Points
In summary, this article has explored several pivotal aspects of etching primers:
- Definition and Purpose: Etching primers serve as an intermediary layer that improves the adhesion of coatings to anodized aluminum surfaces.
- Chemical Properties: The unique chemistry of etching primers facilitates interaction with the aluminum surface, thereby enhancing performance.
- Application Techniques: Proper surface preparation and application methods are essential for achieving optimal results.
- Environmental Considerations: Awareness of regulations and the availability of eco-friendly alternatives is increasingly relevant.
- Market Overview: Knowledge of leading manufacturers and industry trends can guide informed purchasing decisions.
- Future Directions: Emerging research opportunities and innovative formulations highlight ongoing advancements in this field.
Final Thoughts on Etching Primers
Etching primers hold significant relevance in numerous industries that utilize anodized aluminum. The understanding of their properties, applications, and the environmental implications allows professionals to make informed choices in their use. As the standards for material performance continue to evolve, the importance of etching primers in ensuring durability, aesthetic appeal, and environmental compliance will only increase. Their role in contemporary materials science is thus both critical and multifaceted.
"The choice of the right etching primer is as important as the choice of the anodized aluminum itself."