Understanding Upset Forging: Techniques and Applications
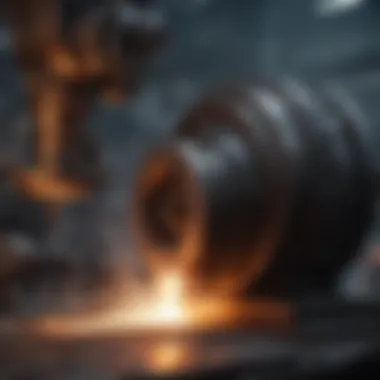
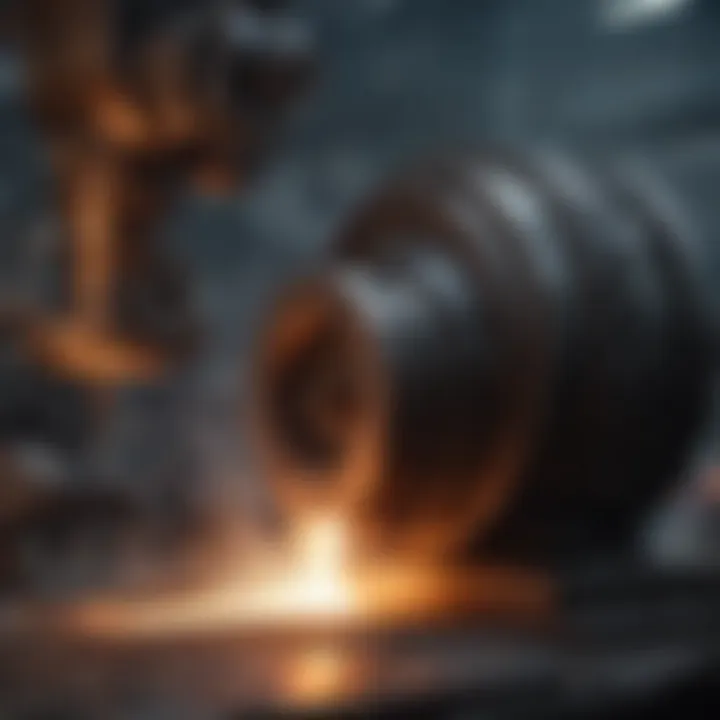
Intro
Upset forging is an essential methodology within the realm of metalworking. It plays a crucial role in enhancing material properties through controlled deformation. Understanding this technique is imperative not only for professionals in manufacturing but also for students and researchers who seek to grasp the intersections of material science and engineering practices. This comprehensive guide will take a closer look at upset forging by examining its key concepts, techniques, and various applications within different industries, ensuring a thorough examination of its importance in today's industrial landscape.
Key Concepts and Terminology
Definition of Key Terms
To foster a deeper comprehension, it is vital to define various terms associated with upset forging:
- Upset Forging: A forging process that involves the localized deformation of metal, usually through axial or lateral pressure. This enhances material strength and modifies geometry.
- Deformation: The alteration of shape or size in a material due to applied forces.
- Localized Deformation: The specific alteration that occurs in selected areas of a material, contributing to the overall mechanical benefits without affecting the entire structure.
Concepts Explored in the Article
This article will explore several concepts fundamental to upset forging, including:
- The mechanical principles underlying upset forging techniques.
- Different types of upset forging, such as cold and hot upset forging.
- Applications that showcase the versatility of this technique across various sectors, from automotive to aerospace industries.
Findings and Discussion
Main Findings
Research and analysis reveal that upset forging significantly improves material properties. The process leads to enhanced grain structure, promoting increased strength and durability. Key findings include:
- Enhanced mechanical integrity due to refined grain flow.
- Costs savings in material usage through effective deformation minimizing wastage.
- Flexibility in design, offering options for producing complex shapes efficiently.
Potential Areas for Future Research
There are multiple avenues for future exploration in upset forging that could yield valuable insights and innovations. Notable areas include:
- Development of new alloys optimized for upset forging processes.
- Improvement of forging tools and techniques to further enhance efficiency.
- Exploration of automation in upset forging procedures to meet increasing industrial demands.
The significance of upset forging extends beyond individual processes; it is foundational to advancements in material science and engineering design.
Prologue to Upset Forging
Upset forging holds a significant place in the realm of metalworking. This technique not only enhances the mechanical properties of metals, but also optimizes material usage across various industries. Understanding its principles is critical for students, researchers, and professionals who are interested in manufacturing processes. By focusing on the characteristics and advantages of upset forging, one gains insight into how this method impacts production and product quality.
Upset forging involves the deformation of metal through the application of compressive forces, effectively thickening specific regions of the workpiece. The enhanced strength and integrity of the final product are key selling points, particularly in sectors like automotive and aerospace. Furthermore, this technique aligns with principles of sustainability in manufacturing, as it results in less waste when compared to traditional methods.
Defining Upset Forging
Upset forging is defined as a form of forging where the metal is locally shortened and thickened. The process involves applying compressive force to a workpiece, causing it to expand radially. This technique is particularly useful for producing components like bolts and other fasteners, where strength and reliability are paramount. The main advantage lies in its ability to create a product with superior mechanical properties due to the grain structure alignment that occurs during deformation.
The importance of upset forging cannot be overstated. It allows for high production rates and can be integrated with automated systems to enhance efficiency. Additionally, the technique can be adapted to work with a variety of metals, including steel and aluminum, making it versatile and widely applicable in different manufacturing sectors.
Historical Context and Development
The origins of upset forging can be traced back to the early days of metallurgy. Historically, blacksmiths used rudimentary tools to create forged parts, gradually evolving into more sophisticated techniques by the 20th century. As industrial needs grew, so did the technology surrounding upset forging.
In the mid-1900s, technological advancements allowed for the automation of upset forging processes. This development not only increased production capabilities but also introduced precision that was previously unattainable. As industries expanded globally, the demand for sturdy, reliable components led to the widespread adoption of upset forging practices.
Today, upset forging is recognized for its efficiency and capability to produce reliably strong components. Research continues to enhance the techniques involved, exploring new materials and methods that further refine this essential manufacturing process.
Fundamental Principles of Upset Forging
Upset forging, a specialized process in metalworking, is driven fundamentally by a few core principles that dictate its efficiency and efficacy. Understanding these principles is key for students, researchers, and professionals who aim to enhance their knowledge in manufacturing processes. This section appreciates the pivotal role these elements hold not only in shaping the final product but also in optimizing the forging process itself.
The Basics of Metal Deformation
Metal deformation occurs when a material is subjected to mechanical forces resulting in permanent shape change. This principle is critical in upset forging, where localized compression is applied to a heated workpiece. The core idea is to alter the shape by applying sufficient pressure to cause flow without fracture.
Factors influencing metal deformation include:
- Temperature: Generally, metals become ductile when heated, making them easier to work with.
- Strain Rate: The speed of deformation can affect mechanical properties; faster rates can lead to more hardened structures.
- Material Properties: Each metal has unique characteristics affecting how it deforms, such as yield strength and ductility.
By applying these factors effectively, manufacturers can produce components with superior mechanical attributes.
Material Properties Affected by Forging
The forging process significantly impacts the mechanical properties of metals. Through upset forging, several changes can be observed:
- Improved Strength and Toughness: The crystalline structure becomes refined, enhancing strength.
- Grain Flow Alignment: This impacts how the material behaves under stress, as aligned grains contribute to higher strength in the direction of forging.
- Reduction of Porosity: During the upset forging process, any pre-existing imperfections in the metal are often eliminated.
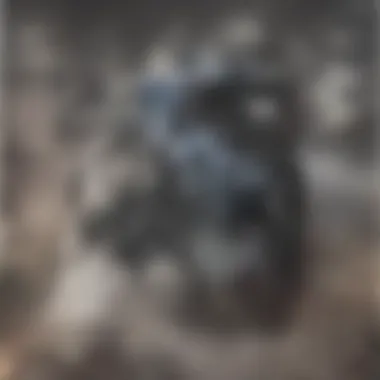
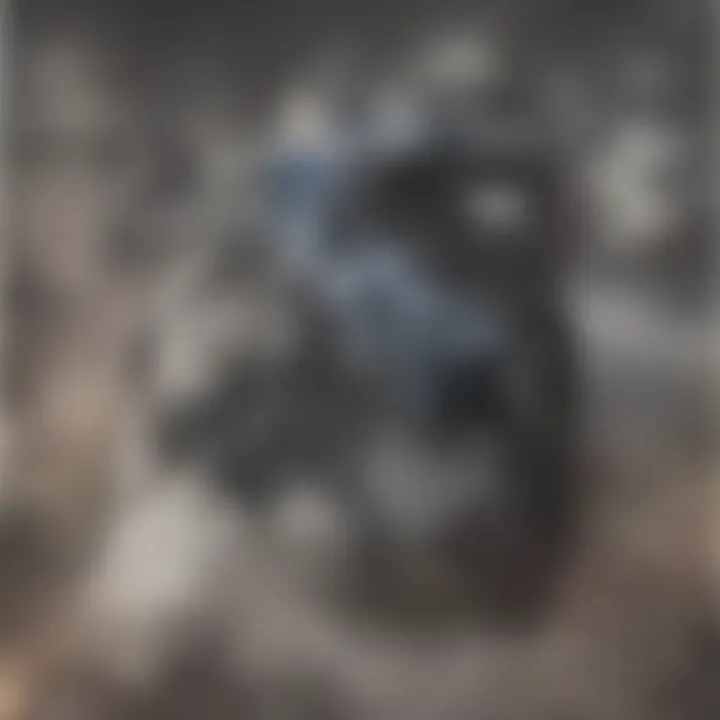
These alterations underscore the relevance of upset forging in industries requiring materials to endure high stress and strain, making it a go-to option for applications in automotive parts, aerospace components, and pressure vessels.
"Understanding the properties that upset forging can influence is essential for predicting how a finished component will respond in its intended environment."
Technical Process of Upset Forging
The technical process of upset forging is fundamental to understanding how this method transforms metal into desired shapes and properties. This section outlines the essential elements and practices in upset forging that contribute to its efficiency and effectiveness. By delving into the stages of preparation, heating, and equipment, we can highlight the intricacies that define this process and its importance in industrial applications.
Preparation of the Workpiece
The preparation of the workpiece is a crucial initial step in upset forging. It involves selecting the right raw material and configuring it to suit the specific requirements of the forging process. Before forging, the material must be cut to the appropriate dimensions and inspected for any imperfections. Key considerations include:
- Material Selection: The choice of metal influences the foating outcome. Common materials include steel, aluminum and titanium, each bringing unique properties to the final product.
- Cleaning: The workpiece should be free from contaminants. Any dirt, rust, or oil can affect material flow and the overall quality of the forged part.
- Shaping: Preforming the workpiece may be necessary for enhanced geometrical accuracy. This might involve preliminary machining or cutting operations to better accommodate the die design.
Efforts in this stage minimize waste and enhance the forging's quality, ultimately affecting the mechanical properties of the finished parts.
Heating Methods and Temperature Control
Heating methods are critical for achieving the desired malleability in the metal, allowing it to be deformed without cracking. The temperature at which the metal is heated influences its viscosity and workability. Common heating techniques include:
- Induction Heating: This method quickly raises the temperature of the workpiece through electromagnetic induction. It offers precise temperature control.
- Furnace Heating: Traditional furnaces provide uniform heating for larger batches. However, they may take longer and lack the specificity of induction.
Temperature control is paramount. Each metal has a specific forging temperature range that must be adhered to in order to optimize deformation and maintain material integrity. Low temperatures may make the metal brittle, while excessively high temperatures can lead to excessive grain growth, resulting in inferior mechanical properties.
"Heating significantly influences the outcome of upset forging. Neglecting temperature control could lead to catastrophic failures during metal deformation."
Forging Equipment and Machinery
The success of upset forging heavily relies on the precision and efficiency of the equipment used. Different types of machinery serve this purpose:
- Forging Presses: Hydraulic or mechanical presses are commonly used for upset forging, providing the necessary force to deform the workpiece.
- Die Sets: These are specially designed components that shape the workpiece. They should be carefully engineered to achieve consistent results and minimized material waste.
- Automation Systems: Modern manufacturing often incorporates robotic systems to enhance productivity and consistency. Automation in upset forging can significantly reduce cycle times and improve safety by minimizing human intervention.
Each piece of equipment must be regularly maintained for optimal performance, as any failure can severely disrupt production and compromise quality.
In summary, the technical process of upset forging is a meticulous operation. Each stage, from preparation and heating to machinery selection, comes together to form an integral part of the forging workflow. Understanding these processes equips professionals and researchers with knowledge that aids in maximizing efficiency, quality, and ultimately, the success of upset forging in various industries.
Types of Upset Forging Techniques
Upset forging techniques are vital for achieving specific shapes and properties in metal materials. Different methods cater to various needs in manufacturing, impacting efficiency, quality, and costs. Each technique offers distinct advantages and considerations when it comes to forging processes.
Closed Die Forging
Closed die forging, also known as impression die forging, is a process where metal is deformed within a fixed die shape. This method is productive for mass production because it allows for tight tolerances and complex shapes that can be repeated. Here, the pre-heated metal becomes more malleable. Once placed in the die, a powerful ram strikes to compress the metal into the die's shape. This makes it one of the most popular methods in industries that require precision pieces like automotive and aerospace.
Key benefits of closed die forging include:
- High dimensional accuracy.
- Enhanced mechanical properties due to work hardening.
- Minimal material waste since less scrap is generated compared to some other methods.
However, the initial costs of creating dies can be high. Thus, it's best used when producing large quantities to spread these costs over many items.
Open Die Forging
Open die forging permits more flexibility as the metal is shaped by a series of blows from a hammer or press without containment between two closed dies. This technique is applied when larger pieces are forged, such as shafts, blocks, and rings. It allows for a variety of shapes and is especially useful for items that do not require compact geometries.
Advantages of open die forging encompass:
- Versatility in shaping large components.
- Better suited for low-volume production runs.
- Less costly initial setup compared to closed die forging.
On the downside, open die forging can lead to lower precision and might generate more waste compared to enclosed methods. Therefore, the choice of this technique depends on the product specifics and production goals.
Cold and Hot Upset Forging
Cold and hot upset forging addresses the temperature conditions of the process, influencing flexibility and strength of the materials involved. In cold upset forging, the metal is deformed below its recrystallization temperature, which results in work-hardening of the metal. This provides high strength and surface finish but can be limited to smaller shapes and less complex designs.
Hot upset forging, on the other hand, takes place above the recrystallization temperature, allowing the use of materials that would otherwise be difficult to shape. This method leads to less work hardening and can produce larger, more intricate pieces due to the increased plasticity of the heated metal.
Here are notable aspects:
- Cold upset forging yields superior surface quality and dimensional precision.
- Hot upset forging offers benefits in larger, more complex shapes and is less labor-intensive.
Effective choice of forging techniques can enhance product performance and reduce overall manufacturing costs.
For further insights, interested parties may want to explore resources such as Britannica to understand the historical and industrial context of these forging techniques.
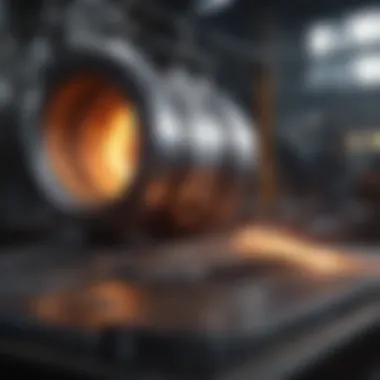
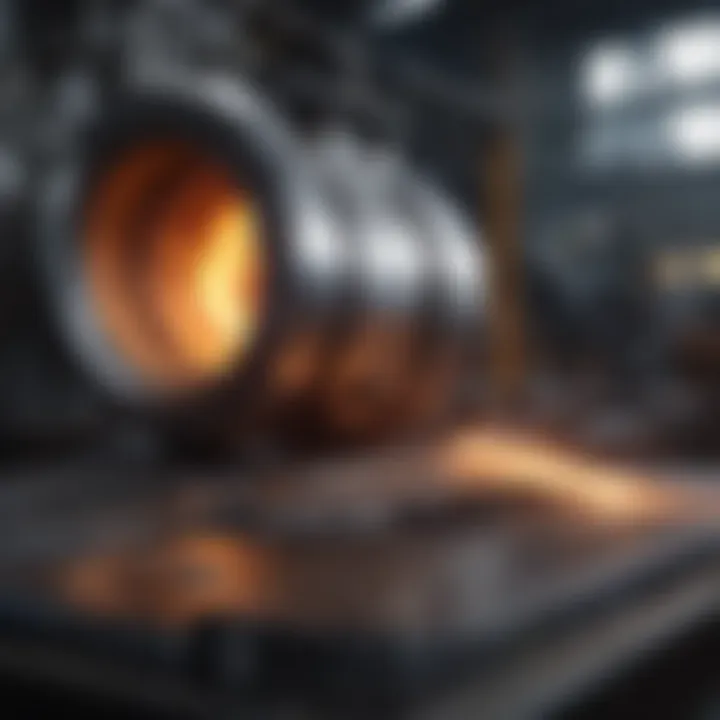
Applications of Upset Forging
The applications of upset forging are crucial for understanding its practical significance in various industries. This technique enhances material properties and meets specific engineering requirements. Industries integrate upset forging due to its ability to produce high-strength components with excellent fatigue resistance. Therefore, examining these applications provides insight into how upset forging contributes to advancements in technology and production efficiency.
Automotive Industry
In the automotive sector, upset forging is widely used to manufacture components that require high strength and durability. Parts such as crankshafts, gears, and connecting rods undergo forging to enhance their mechanical properties.
- Strength-to-weight ratio: Upset forging creates components that are lighter yet stronger than cast or machined alternatives.
- Customization: Manufacturers often tailor parts to meet specific design criteria, improving performance and safety.
- Cost Savings: Forged parts typically require less finishing work, resulting in lower manufacturing costs.
This technique plays a significant role in producing parts like steering knuckles and suspension components that can withstand high loads and stresses during vehicle operation.
Aerospace Engineering
Aerospace engineering demands materials and components that can endure extreme conditions. Upset forging has important applications here, contributing to manufacturability and performance of critical components.
- High-strength materials: Materials like titanium and steel, which are often used in aircraft, benefit greatly from upset forging.
- Reduction in material usage: This process allows for the efficient use of metals, minimizing waste and ensuring greater sustainability in production.
- Improved fatigue resistance: Components forged are less likely to fail under cyclic loading, which is crucial in aerospace applications.
Forged components can be found in turbine engines and landing gear, highlighting how upset forging aligns with safety and reliability standards in the aerospace industry.
Oil and Gas Sector
In the oil and gas sector, upset forging is integral for creating parts that withstand harsh environments and operational stresses. This includes making tools and fasteners that must perform reliably under extreme conditions.
- Durability: Components like valves, flanges, and drill bits made through upset forging showcase extended service life.
- Enhanced performance: The forging process improves mechanical properties, which is essential in high-pressure applications.
- Cost-effective solutions: The technique reduces scrap and lowers manufacturing costs, an essential factor in this competitive industry.
Parts produced for extraction and transportation activities highlight the significant role that upset forging plays in upholding efficiency and reliability in the oil and gas sector.
Advantages of Upset Forging
Upset forging offers several advantages that make it a preferred choice in various metalworking applications. Understanding these benefits helps in recognizing why many industries have adopted this technique. The significance of upset forging lies not only in its effectiveness in transforming metal but also in its capacity to enhance the overall production process.
Enhanced Mechanical Properties
One of the primary benefits of upset forging is the substantial improvement in the mechanical properties of the produced components. The process involves localized deformation of the material, which leads to a refined grain structure. This refinement enhances toughness and strength. The impact of such changes cannot be understated, as it directly influences the durability and performance of the final product.
Specifically, upset forging increases yield strength and fatigue resistance, making components suitable for high-stress conditions. As research indicates, components produced through this method exhibit superior resilience and reliability.
Material Efficiency
Upset forging also stands out for its material efficiency. The process often results in less waste compared to traditional methods. This advantage stems from the fact that the technique optimally utilizes the raw material by manipulating its shape without excessive cutting or machining.
In industries where material costs constitute a significant portion of production expenditures, optimizing material usage is crucial. By reducing scrap and using only what is necessary, companies can lower their overall costs and increase sustainability. This efficiency aligns with current trends towards greener manufacturing practices.
Cost-effectiveness in Production
The cost-effectiveness of upset forging further enhances its appeal to manufacturers. Initial setup and tooling costs can be higher than some traditional methods. However, the rapid production rates and reduced labor requirements yield significant long-term savings.
Moreover, the enhanced mechanical properties that result from upset forging can lead to fewer failures in service. This reliability reduces warranty claims and maintenance costs over the product's lifecycle. Thus, companies can see a return on investment relatively quickly when using this forging technique.
Overall, the advantages of upset forging underscore its value in the manufacturing landscape.
Disadvantages and Limitations
Understanding the disadvantages and limitations of upset forging is crucial for a well-rounded discussion about this methodology. While it offers several advantages, such as enhanced mechanical properties and material efficiency, there are also significant challenges that practitioners must consider.
Material Waste Concerns
One of the primary drawbacks of upset forging relates to the potential for material waste. During the forging process, excess material may be generated as the metal is displaced outward. This occurs especially in operations involving closed die forging, where the shape of the finished product needs to fit strictly within the die's confines. Any surplus material that does not form part of the final component leads to wastage that can inflate production costs.
Additionally, the need for excess stock to accommodate deformation can increase the environmental footprint of manufacturing practices. Addressing these concerns often requires optimizing the design of dies and careful calculation of the required material to minimize scraps.
Effective waste management strategies are essential to enhance the sustainability of upset forging processes.
Equipment and Operational Costs
The financial implications of upset forging can be considerable. The initial investment in specialized machinery and equipment used for this type of forging is often substantial. Equipment like hydraulic presses, forging hammers, and heat treatment systems require not only a high capital outlay but also ongoing maintenance and operational costs.
Moreover, the precision required in upset forging demands skilled operators. Training personnel on this technology can add to the operational budget. Overall, companies engaging in upset forging must weigh these costs against the long-term benefits of this manufacturing technique, ensuring that they achieve adequate returns on their investment.
In summary, while upset forging holds immense potential for producing superior components, the associated material waste and financial burdens are important factors for manufacturers to consider.
Innovations in Upset Forging
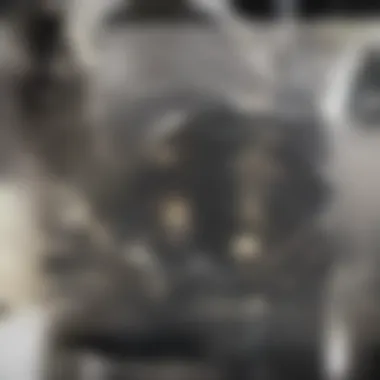
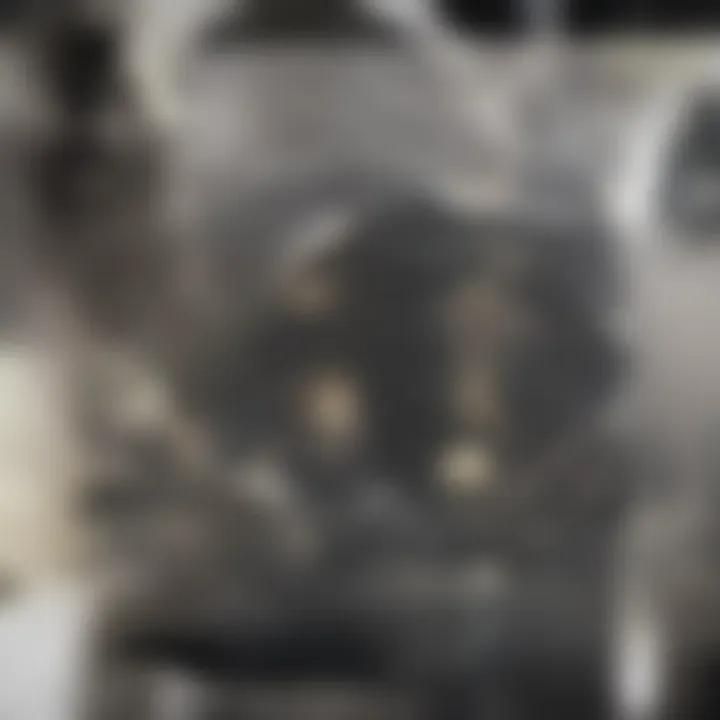
Innovations in upset forging represent a pivotal shift in how the manufacturing industry approaches metalworking. The integration of new technologies and materials enhances the capability and efficiency of traditional forging techniques, paving the way for improved productivity and product quality.
Automation and Robotics
Automation and robotics play a crucial role in modernizing upset forging. These advancements streamline processes, reduce manual labor, and increase accuracy in operations. Robotic arms can handle the intricate tasks of arranging and manipulating metals with precision, thus mitigating the risk of human error. The speed of automated systems also means lower production times and a more consistent output.
One notable example is the implementation of programmable logic controllers (PLCs) that monitor and control various parameters during forging. This technology allows for real-time adjustments to temperature and pressure, ensuring that the workpiece receives optimal treatment. Furthermore, automated systems can work continuously, leading to substantial increases in overall output.
Moreover, automation facilitates the integration of data analytics. This capability allows manufacturers to track performance metrics, predict maintenance needs, and optimize processes based on real-time data. As a result, companies can reduce operational costs while increasing the longevity of their machinery.
Advanced Material Use
The use of advanced materials marks another significant innovation in upset forging. Developments in metallurgy have introduced higher-strength alloys and composites that can withstand extreme conditions. These materials not only enhance product durability but also expand the possibilities for applications across various industries.
For instance, aerospace engineering is seeing the incorporation of titanium alloys in upset forging. These materials provide the necessary strength-to-weight ratio, crucial for flight applications. Likewise, the automotive sector benefits from advanced high-strength steels that improve vehicle performance while ensuring safety.
The ability to manipulate these materials through upset forging leads to better mechanical properties, such as improved fatigue resistance and tensile strength. Manufacturers increasingly focus on material specifications to tailor the forged products for specific use cases, allowing them to meet strict regulatory standards.
Case Studies in Upset Forging
The exploration of case studies in upset forging plays a significant role in understanding the practical applications and effectiveness of this technique. By analyzing real-world examples, one gains insights into not just the successes but also the setbacks that occur during the implementation of upset forging processes. These case studies highlight the advantages gained by utilizing upset forging, revealing how industries can improve their production capabilities and ultimately their product quality.
Moreover, case studies serve as a valuable learning tool. They showcase specific elements such as methodologies adopted, the technology utilized, and adjustments made to overcome particular challenges. This allows professionals and researchers in the field to derive lessons applicable to their own projects, ensuring that the knowledge is both practical and relevant.
Successful Implementations
Upset forging has seen numerous successful implementations across various industries. For instance, in the automotive sector, companies like Ford have utilized this technique for production of high-strength components. The process aids in creating complex shapes and stronger materials, essential for modern vehicle design and safety. Through the implementation of upset forging, Ford achieved reduced weight in components while retaining durability, a critical balance for fuel efficiency and performance.
In aerospace, companies like Boeing have adopted upset forging for critical parts of aircraft. The process not only enhances the mechanical properties of metals used but also contributes to weight reduction and structural integrity. This is particularly important given the stringent safety requirements in the aerospace industry.
These successful implementations reflect the practicality and effectiveness of upset forging, reinforcing its place in modern manufacturing practices.
Lessons Learned from Failures
Examining failures in upset forging provides valuable insights that contribute to future successes. One notable case involved a hydraulic press malfunction that resulted in numerous defective parts. The failure revealed the importance of regular maintenance and calibration of equipment, highlighting that even slight discrepancies in pressure can lead to substantial quality issues.
Another failure occurred during a production run at a metal fabrication plant, where the temperature control during heating was inadequate. This led to improper deformation and resulted in scrapped materials. The lesson learned here was the paramount necessity of precise temperature monitoring throughout the forging process to ensure optimal results.
These lessons illustrate that despite its advantages, upset forging is not without challenges. However, they collectively emphasize the importance of careful planning, strict quality control, and continual learning from past experiences to enhance production techniques. Through understanding both the successful applications and the lessons from failures in upset forging, industries can significantly improve their operations.
Future of Upset Forging
The future of upset forging holds significant potential, both in terms of advancing metalworking techniques and enhancing industrial applications. As the global demand for high-performance materials grows, upset forging is becoming increasingly relevant. Industries are seeking methods that not only improve material properties but also optimize manufacturing processes. Innovations in upset forging could lead to more efficient production lines and better overall product quality, which is crucial in competitive manufacturing environments.
Another essential aspect to consider is the shift towards sustainability in manufacturing. As companies aim to reduce waste and energy consumption, upset forging techniques present a viable solution by minimizing material waste. Utilizing these processes can lead to a greener approach to manufacturing, aligning with global sustainability goals. With advancements in technology, the ability to recycle materials within upset forging practices will likely enhance its appeal for manufacturers.
"The integration of modern technologies in upset forging can redefine operational efficiencies and environmental impact."
Trends in Industry Practices
Several trends are emerging within the realm of upset forging that reflect the evolving landscape of manufacturing. One notable trend is the growing adoption of automation. Companies are increasingly implementing robotics and automated systems to enhance precision and productivity. Automation reduces the risk of human error and allows for better control over the forging process, leading to improved quality and consistency in products.
Another trend observed is the shift towards hybrid forging techniques. These methods combine traditional upset forging with newer technologies, such as additive manufacturing. This hybrid approach not only broadens the range of materials that can be used in the forging process but also enables the creation of intricate geometries that would be difficult to achieve with conventional methods. Industries are exploring these innovations, particularly in sectors like aerospace and automotive, where material efficiency and mechanical properties are paramount.
Key industry practices include:
- Integration of automation in forging processes
- Exploration of hybrid techniques with additive manufacturing
- Focus on sustainable practices and material efficiency
Predictions for Technological Advancements
As we look ahead, several predictions regarding technological advancements in upset forging can be made. The continuous evolution of materials science will play a crucial role in shaping the future of upset forging. As lighter and stronger materials are developed, forging techniques will need to adapt to accommodate these new substances, ensuring that they are properly processed to maintain desired mechanical properties.
Moreover, advancements in data analytics and machine learning can revolutionize the monitoring and optimization of forging processes. By utilizing real-time data, manufacturers can fine-tune operational parameters, anticipate potential issues, and minimize downtime. This predictive approach enhances overall efficiency and can lead to significant cost savings.
In summary, the potential for upset forging lies in its adaptability to changing industry needs. With ongoing advancements and a focus on sustainability, upset forging is poised to remain a key player in the future of manufacturing, contributing to improved products and processes across various sectors.
End
The conclusion of this article holds significant value as it synthesizes the critical elements discussed throughout various sections regarding upset forging. Understanding upset forging is crucial for several reasons, especially for those engaged in manufacturing and engineering. It encapsulates the essence of the techniques, processes, and applications that define this metalworking method.
Summarizing Key Points
In summary, upset forging stands out due to its specific methods and applications in different sectors. Here are the key takeaways:
- Definition and Historical Development: Upset forging is a technique that has evolved over time, shaping metalworking methodologies.
- Principles and Processes: The process harnesses basic principles of metal deformation and considers various material properties that are essential for quality outcomes.
- Types of Techniques: Different methods such as closed die forging, open die forging, and temperature variations affect the final product significantly.
- Applications Across Industries: The automotive, aerospace, and oil sectors utilize this technique for enhanced performance and reliability of components.
- Advantages and Limitations: The technique offers benefits like improved mechanical properties but also faces challenges, including material waste and costs.
- Future Trends: Innovations such as automation and advanced materials play a vital role in shaping the future of upset forging.
Final Thoughts on Upset Forging
In concluding this discourse, it is evident that upset forging is integral to modern manufacturing. Its implications stretch beyond mere techniques, reaching into broader horizons like material science advancements and industrial efficiency. As research progresses, the refinement of upset forging practices can enhance productivity and reduce waste. For anyone involved in metallurgy or manufacturing technologies, a solid grasp of upset forging's nuances is essential for driving innovation and improving production standards.
Understanding this technique not only benefits individuals in their careers but also fosters the evolution of the entire industry to meet future challenges.