Understanding Wafer Particle Counters in Manufacturing

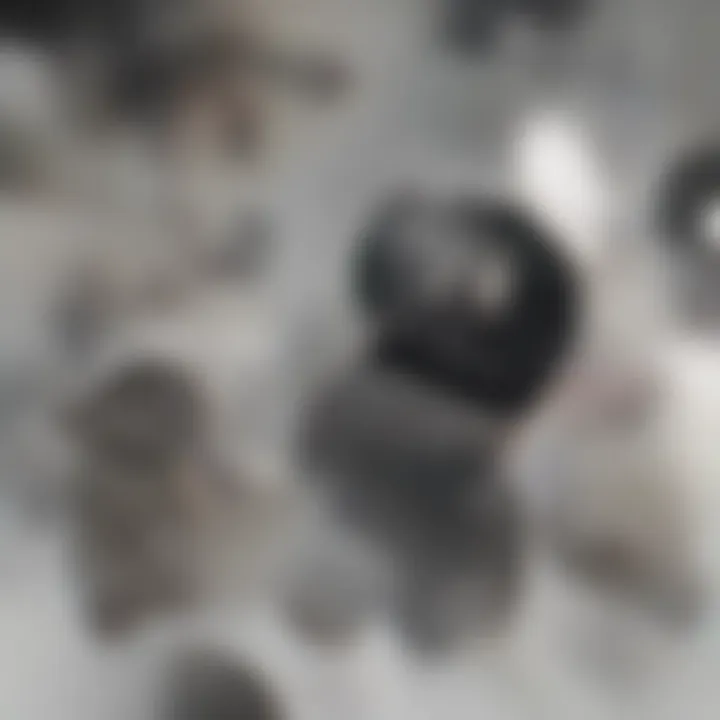
Intro
In semiconductor manufacturing, precision is paramount. To achieve this, monitoring and controlling particle contamination is crucial. Wafer particle counters serve as essential tools in this quest for perfection. They detect and quantify particles on silicon wafers, where even minuscule contaminants can significantly affect the performance of finished products.
This article explores the technology behind wafer particle counters, their components, and their applications. A comprehensive understanding of this technology and its impact is vital for professionals in the semiconductor industry.
Key Concepts and Terminology
Definition of Key Terms
- Wafer: A thin slice of semiconductor material, typically silicon, used in the fabrication of integrated circuits.
- Particle Counter: An instrument that detects and counts airborne particulate matter or surface contaminants on wafers.
- Contamination: The presence of unwanted particles or substances that can impair the quality and functionality of semiconductor devices.
Concepts Explored in the Article
In this article, the following concepts will be examined:
- The operational principles of wafer particle counters.
- The key components that make up these devices.
- The applications of particle counters in various industries.
- Trends in measuring particle contamination, focusing on future technology developments.
- The correlation between particle contamination and the quality of semiconductor products.
Findings and Discussion
Main Findings
The examination reveals that wafer particle counters utilize advanced techniques for detection and measurement. Their importance cannot be understated in semiconductor manufacturing, where maintaining a clean environment is critical. A few noteworthy findings include:
- Particle counters can measure particles as small as 0.1 microns, significantly enhancing contamination tracking capabilities.
- They often employ laser-based detection systems, ensuring high precision and efficiency in operation.
- Applications go beyond semiconductor manufacturing, influencing industries such as pharmaceuticals and aerospace, where cleanliness is equally vital.
Potential Areas for Future Research
Research in this field remains dynamic. Some potential areas for future inquiry include:
- Developing more sensitive detection methods to identify even smaller particles.
- Integrating artificial intelligence in data analysis for real-time monitoring of particle levels.
- Exploring the environmental impact of particle contamination across different manufacturing sectors.
"Maintaining cleanliness in semiconductor fabrication is a continuous challenge that requires sophisticated tools like wafer particle counters."
As the semiconductor industry evolves, understanding the significance of these tools will play a critical role in ensuring the reliability and efficiency of next-generation technologies.
Prelude to Wafer Particle Counters
Wafer particle counters play a critical role in the semiconductor industry. These instruments are essential for maintaining the integrity and quality of semiconductor manufacturing processes. By measuring the number and size of particles present on wafers, they ensure that the production environment meets stringent cleanliness standards. The accuracy and reliability of these measurements directly influence product performance, yield rates, and overall operational efficiency.
Definition and Importance
A wafer particle counter is an analytical device used to detect and quantify particulate contamination on semiconductor wafers. The detection capabilities of these devices enable manufacturers to monitor particle levels continuously. The importance of wafer particle counters lies in their ability to detect minute particles that could potentially compromise the performance of semiconductor devices. Such contamination can lead to device failures, inefficient electrical characteristics, and reduced product lifespan.
In semiconductor fabrication, the presence of even a single particle can disrupt a delicate process. Therefore, wafer particle counters are invaluable to maintaining the high precision required in chip production. They provide essential data that assist in adhering to quality control regulations and ensure the overall reliability of the final products.
Historical Context
The development of wafer particle counters can be traced back to the evolution of semiconductor manufacturing itself. In the early days, the focus was primarily on the functionality of devices and less on the impurities present during the production. As technology advanced, manufacturers began to realize the significance of a clean production environment.
The first particle counters were rudimentary in design and primarily relied on basic optical principles. Over time, technological advancements led to the integration of more sophisticated detection techniques, allowing for improved sensitivity and specificity. By the late 1970s and early 1980s, particle counters had become a standard tool in semiconductor cleanrooms.
The growth in complexity of semiconductor devices, particularly with the emergence of integrated circuits, highlighted the critical need for accurate particle measurement technologies. This historical context has shaped the current landscape of wafer particle counting and has made it a cornerstone of modern semiconductor manufacturing.
Principles of Operation
The principles of operation for wafer particle counters are crucial for understanding how these devices function and their significance in ensuring quality control in semiconductor manufacturing. These principles outline the mechanisms that these counters use to detect, quantify, and analyze particles on the wafer's surface. This knowledge is imperative, as the efficiency and accuracy of a wafer particle counter greatly influence the overall yield and reliability of semiconductor products.
Basic Working Mechanism
Wafer particle counters generally operate by employing various physical detection methods. At the core of these mechanisms is the ability to analyze the light interaction with particles when illuminated. The counters shine a laser onto the surface of a wafer and measure the light scattered by particulate contamination. This process involves several stages:
- Light Emission: A light source, usually a laser, emits a beam that focuses onto the wafer surface.
- Scattering Detection: As the light interacts with particles, it gets scattered in various directions. The counter has sensors that detect this scattered light.
- Data Processing: The detected signals are analyzed to determine particle size and count.
This mechanism allows for real-time monitoring and assessment, which is essential for maintaining the integrity of the manufacturing process.
Types of Detectors Used
Several types of detectors are common in wafer particle counters, each with unique attributes suited for different applications. Here are some of the key types:
- Photoresistors: These detectors change resistance based on light exposure and are useful for low-cost applications.
- Photomultiplier Tubes: Known for high sensitivity, these are used in environments with very low light levels to accurately measure scattered light.
- Charge-Coupled Devices (CCDs): CCDs capture images of particle scatter patterns, allowing for detailed analysis of particle characteristics.
Choosing the right detector is essential as it affects the counter's sensitivity, range, and operational speed, demonstrating how detector choice impacts measurement accuracy.
Calibration Techniques
Calibration is vital to ensure that wafer particle counters provide precise and reliable measurements. Without proper calibration, the data collected might lead to erroneous conclusions about particle contamination. There are several accepted calibration techniques used:
- Standard Particle Suspension: A known concentration of particles in liquid is used to calibrate the system. This method helps in establishing a baseline for size and count.
- Internal Calibration: Some systems have built-in calibration functions, which check readings against known reference points internally.
- Regular Maintenance Checks: Periodic calibration against standards is advised to accommodate any drift in the measuring system over time.
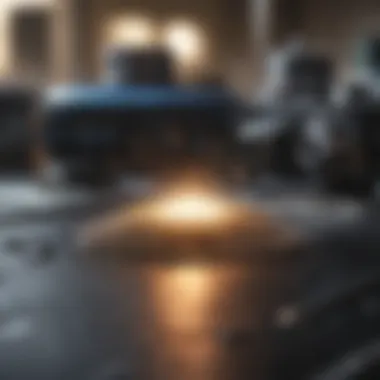
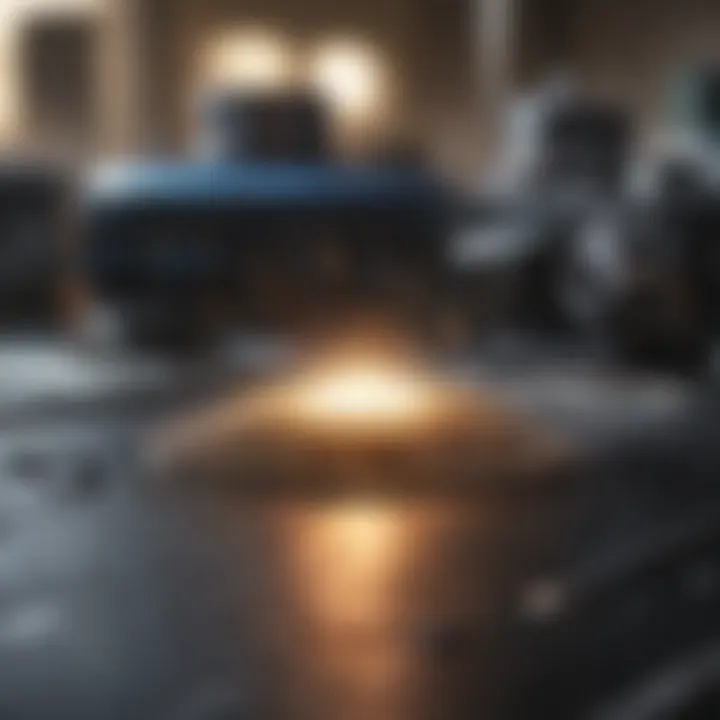
Careful calibration ensures the effectiveness of wafer particle counts, thereby reducing the risks related to contamination in semiconductor manufacturing.
"Understanding the principles of operation illuminates the path to mastering wafer particle counters, leading to enhanced product quality in semiconductor manufacturing."
Key Components of Wafer Particle Counters
Wafer particle counters are essential for maintaining high standards in semiconductor manufacturing. Their effectiveness heavily relies on several key components that enable accurate measurement of particles on wafers. Understanding these components is crucial for anyone involved in this field. This section will elaborate on the optical systems, fluidics systems, and data processing units which are the backbone of wafer particle counters.
Optical Systems
Optical systems in wafer particle counters utilize light to detect and analyze particles. These systems often employ laser and photodetector technologies. The primary role of optical systems is to illuminate the wafer surface and measure the scatter of light caused by particles.
This scattering is proportional to the size and concentration of particles, allowing for precise quantification. A well-designed optical system can enhance sensitivity and improve the detection limits. Furthermore, the choice of wavelengths in the optical setup is critical; different materials absorb and scatter light differently.
The advantages of optical systems include high throughput and real-time monitoring. They can rapidly assess the cleanliness of wafers, facilitating timely production decisions. However, technological considerations such as alignment, stability under temperature fluctuations, and maintenance of the optical components are necessary to ensure optimal performance.
Fluidics Systems
Fluidics systems play a significant role in the sampling process of wafer particle counters. These systems manage the movement of air or liquid that interacts with the wafer surfaces. They ensure that the wafers are exposed to the sampling medium, which carries away particles for measurement.
The fluidic design must prevent contamination during sampling. This requires high-quality materials and careful engineering to avoid trapping particles or creating unwanted turbulence. The system typically consists of pumps, filters, and valves that work in a synchronized manner.
An efficient fluidics system enhances the accuracy and reliability of particle counting. It also impacts the overall throughput of the measurement process. Therefore, designers must consider various configurations to achieve optimal performance while managing costs and ease of maintenance.
Data Processing Units
Data processing units are central to translating the measurements taken by the optical and fluidics systems into actionable information. These units are responsible for data acquisition, analysis, and reporting. They utilize complex algorithms to interpret scattering data, providing real-time feedback on particle levels.
Strong processing capabilities are essential for handling vast amounts of data generated. This section not only processes the measurements but also stores historical data, enabling trend analysis. The integration of data processing units with advanced software can improve monitoring efficiency and facilitate compliance with industry standards.
Moreover, the ability to connect with other systems is increasingly important in the context of smart manufacturing. Data processing units often incorporate machine learning techniques, allowing for predictive analysis and enhancing overall process reliability.
"Data processing is where the magic happens. It turns raw measurements into insights that can drive quality improvements."
In summary, each component within wafer particle counters plays an integral role in ensuring effective particle measurement. By focusing on these systems—optical, fluidics, and data processing—professionals can achieve better precision and reliability in semiconductor manufacturing.
Applications of Wafer Particle Counters
Wafer particle counters serve critical roles across several industries, predominantly in semiconductor manufacturing, research and development, and quality assurance in electronics. Understanding these applications provides insights into how particle counting technologies contribute to efficiency and product integrity.
Semiconductor Manufacturing
In semiconductor manufacturing, particle contamination can have dire consequences. Wafer particle counters are essential tools that help detect and quantify particulate matter in cleanroom environments. They ensure that the wafer surfaces are free from contaminants that could affect the electrical characteristics of the chips produced. When particle levels exceed certain thresholds, manufacturers can halt production to mitigate risks, thereby preserving product quality. The application of these counters leads to better yield rates and lower defect densities.
The technology used in wafer particle counters allows for real-time monitoring, thus enabling quick responses to contamination events. The data generated can be crucial for process optimization, allowing engineers to adjust parameters and enhance cleanroom operations. This proactive approach helps maintain longer equipment life and reduces operational costs associated with rework and scrapped wafers.
Research and Development
In research and development sectors, wafer particle counters support innovation and technological advancements. As new materials and processes emerge, understanding the influence of particulate contamination becomes imperative. Researchers utilize these instruments to experiment with different manufacturing conditions and to analyze how various contaminants interact with new semiconductor materials.
Moreover, the use of advanced particle counters aids in the validation of new concepts. For example, the development of next-generation semiconductor devices demands stringent control over contamination. Findings from particle counting can inform the design of more effective cleanroom environments and processes, ultimately fostering progress in electronic technologies. Collaboration between academia and industry often leans on these data insights to transition new research into commercial applications.
Quality Assurance in Electronics
For quality assurance in electronics, wafer particle counters play a pivotal role in ensuring compliance with industry standards. Devices manufactured for consumer electronics, automotive applications, and medical devices require rigorous testing for contamination. By employing wafer particle counters, manufacturers can demonstrate adherence to specifications set forth by regulatory organizations.
In the context of quality assurance, these devices are instrumental in verifying production consistency. Frequent particle measurements help spot deviations from acceptable levels, allowing for immediate corrective actions. As a result, manufacturers reduce the risks associated with faulty products reaching the market, thus safeguarding brand reputation.
“The implementation of wafer particle counters is not merely a regulatory requirement but a foundational practice for maintaining electronics quality.”
Impact of Particle Contamination
Particle contamination is a significant concern in semiconductor manufacturing. It can compromise the integrity and performance of products, leading to defects that affect overall yield. Understanding its impact is essential for professionals in the industry, as well as researchers who are exploring new methodologies for quality assurance.
Effects on Product Quality
Particles, however small, can have negative impacts on product quality. Even minute contaminants, like dust or airborne particles, can lead to issues such as surface defects in wafers. This can subsequently affect the electrical characteristics of semiconductor devices.
When chips are manufactured, they must adhere to strict specifications to function correctly. Any deviation from these specifications can lead to failures. Studies show that a single particle can result in significant defects that render a chip unusable.
Additionally, particle contamination can also lead to yield loss, which is particularly critical in an industry where margins are already tight. Quality control measures must be stringent, requiring reliable particle counting methods to identify and mitigate contamination risks.
"The threshold for acceptable particle size in semiconductor manufacturing is continually decreasing, making stringent monitoring essential."
Cost Implications
The consequences of particle contamination extend beyond product quality to include considerable cost implications. When defects occur, manufacturers face increased expenses in many areas. For instance, rework costs for defective products can escalate quickly. This includes labor and material costs associated with repairing or discarding flawed wafers.
Moreover, when a batch is found unacceptable, it may lead to production delays. Delays can disrupt supply chains and affect the market availability of products. As a result, companies may experience decreased customer satisfaction and loyalty.
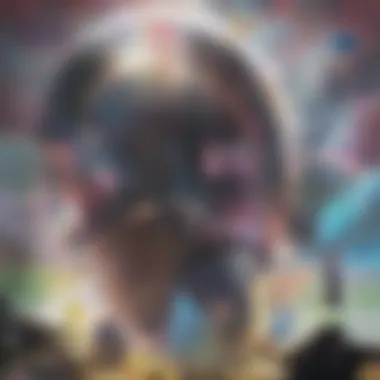
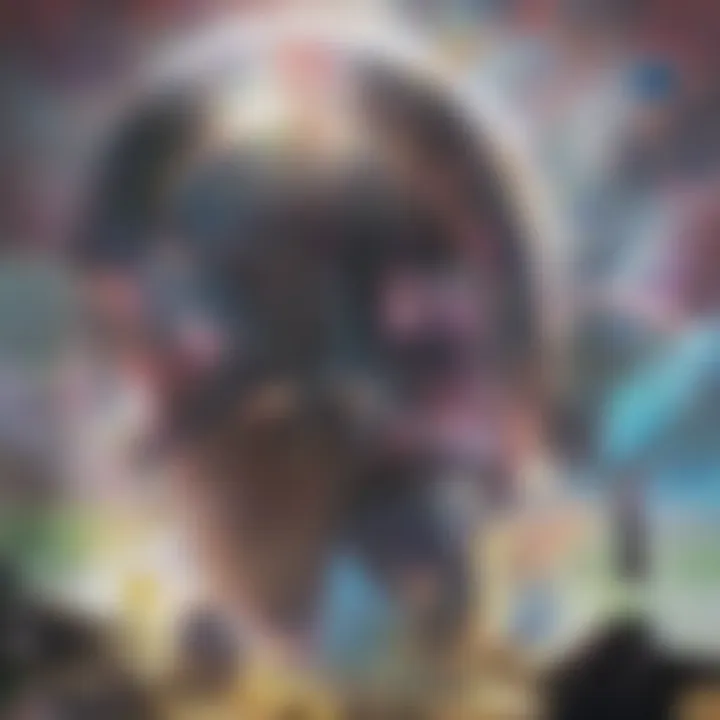
In the long run, frequent contamination issues can tarnish a company's reputation, leading to loss of business. Investing in high-quality wafer particle counters is crucial. Such counters help in early detection of contaminations, ultimately saving costs by preventing extensive rework and maintaining product quality.
In summary, the impact of particle contamination in semiconductor manufacturing is profound, affecting product quality and carrying significant cost implications. Professionals in the field must prioritize systems and practices that ensure strong monitoring to minimize these risks.
Future Trends in Particle Measurement Technologies
The landscape of particle measurement is continually evolving, driven by the need for improved accuracy, efficiency, and integration within industrial processes. As industries, particularly semiconductor manufacturing, advance, the importance of staying ahead of trends in particle measurement technologies becomes critical. These trends can significantly influence product quality, operational costs, and overall business success. In this section, we will explore two pivotal aspects: advancements in sensor technology and integration with smart manufacturing.
Advancements in Sensor Technology
Recent innovations in sensor technology are reshaping how wafer particle counters detect and analyze particulate contamination. Modern sensors are not only more sensitive and accurate, but they also offer a wider range of detection capabilities. For instance, advancements in optical sensors have led to higher resolution imaging, enabling the detection of even the smallest particles with ease. This capability is crucial in semiconductor environments, where even minuscule contaminants can lead to significant production failures.
Moreover, sensors now increasingly incorporate machine learning algorithms. This integration allows for real-time analysis of data, optimizing performance by adapting to varying environmental conditions. Enhanced data processing capabilities also minimize response times, which can substantially affect the manufacturing process.
In addition, the miniaturization of sensors contributes to more compact designs for wafer particle counters. This portability allows for easier integration into different stages of the production process, which facilitates continuous monitoring without interrupting workflow.
- Key Benefits of Sensor Advancements:
- Increased sensitivity and accuracy
- Real-time data analysis through machine learning
- Enhanced portability and compact designs
These technological advancements position wafer particle counters to be more effective than ever, ensuring higher standards in semiconductor manufacturing.
Integration with Smart Manufacturing
The transition to smart manufacturing represents a paradigm shift in various industrial sectors. This concept emphasizes interconnected systems and automation based on data and analytics. When it comes to wafer particle counters, their integration into smart manufacturing frameworks significantly enhances operational efficiency.
Particle counters that interface seamlessly with other manufacturing systems can provide crucial data for process optimization. For instance, they can help identify contamination patterns, enabling preemptive actions before defects could impact production. This proactive approach can potentially reduce waste and improve yield rates, ultimately enhancing profitability.
Furthermore, integrating wafer particle counters with cloud-based platforms allows for comprehensive data aggregation. Manufacturers can access this data remotely, facilitating better decision-making based on real-time analytics.
- Considerations for Integration:
- Compatibility with existing systems
- Data security and management
- Scalability for future advancements
As industries increasingly adopt smart manufacturing principles, the role of wafer particle counters in maintaining product quality and operational efficiency will grow, making it necessary for manufacturers to keep pace with these changes.
"Advancements in technology are not just trends; they are essential shifts that define the future of industries and manufacturing processes."
In summary, future trends in particle measurement technologies, particularly advancements in sensor technology and integration with smart systems, are vital in shaping the future of semiconductor manufacturing. As these trends unfold, they will play a crucial role in ensuring the integrity and quality of high-tech components.
Comparative Analysis with Other Particle Measurement Methods
Wafer particle counters play a significant role in ensuring the quality and precision in semiconductor manufacturing. To truly appreciate their capabilities, it is essential to compare them with other particle measurement techniques. Understanding the strengths and weaknesses of these methods can help professionals choose the right technology for specific application needs. This comparative analysis highlights the differences, advantages, and limitations inherent in various particle measurement techniques.
Static vs. Dynamic Measurement Techniques
Static measurement techniques assess particle contamination by analyzing samples when they are at rest. This approach may include techniques like microscopy or sedimentation analysis. While these methods can provide detailed insights into particle morphology, they may fail to accurately represent the real-time particle situation during manufacturing processes. In semiconductor environments where contamination can change rapidly, static analyses may lead to misleading conclusions.
Conversely, dynamic measurement techniques, such as those employed by wafer particle counters, offer real-time analysis of particle concentrations and sizes. These methods typically rely on moving fluid and continuous sampling, facilitating immediate detection of any contamination that may occur during production. The advantages of dynamic methods include:
- Real-time monitoring: This helps in immediate corrective actions to prevent defective products.
- Higher sensitivity: Dynamic techniques can detect smaller particles that static methods may overlook.
- Continuous data stream: Provides ongoing information, aiding in the analysis of trends over time.
Yet, dynamic methods are not without their downsides:
- Complexity: The technology and infrastructure required can be costly and challenging to implement.
- Sensitivity to environmental changes: Fluctuations in temperature or pressure might affect measurement accuracy.
Advantages and Limitations
Comparing wafer particle counters with other particle measurement methods reveals distinct advantages and limitations.
Advantages of Wafer Particle Counters:
- Precision: Ability to measure the smallest particles critical in semiconductor applications.
- Versatility: They can be utilized in various settings, from manufacturing to research environments.
- Data Integration: Wafer particle counters often integrate with other quality assurance systems, providing a comprehensive view of contamination sources.
Limitations of Wafer Particle Counters:
- Cost: Initial investments in wafer particle counters can be higher than some static methods.
- Technical Expertise Required: Operators must be trained to interpret data correctly and manage the equipment.
It is important to consider these factors when selecting a particle measurement solution. Evaluating not only the technology but the specific requirements of the facility or production line is crucial for optimal results.
Regulatory Standards and Compliance
In the realm of wafer particle counting, regulatory standards and compliance play a pivotal role. These frameworks ensure that particle counters operate within specific guidelines that maintain accuracy and reliability in semiconductor manufacturing processes. The significance of adhering to these standards cannot be overstated, as they directly influence product quality, operational efficiency, and safety protocols.
Compliance with established regulations helps manufacturers minimize defects in their products and enhances overall yield. This is particularly relevant given the ultra-clean conditions required in semiconductor fabrication environments, where even minute particles can lead to substantial issues in production. Thus, understanding the landscape of regulations is essential for industries relying on wafer particle counters to uphold their quality assurance processes.
Regulatory compliance is not merely about meeting legal requirements; it is a commitment to quality and reliability in manufacturing.
Global Regulations
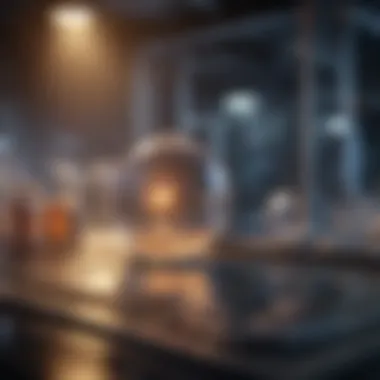
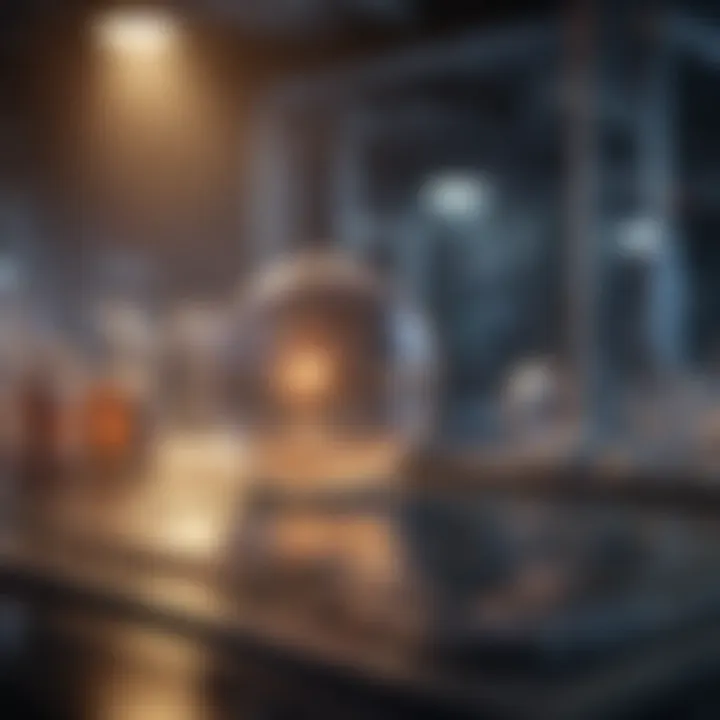
Global regulations surrounding wafer particle counters vary across regions and industries. Entities such as the International Organization for Standardization (ISO) and the Semiconductor Equipment and Materials International (SEMI) institute numerous protocols that dictate operational performance, calibration, and testing procedures. For instance, ISO 14644 focuses on cleanroom standards, establishing limits for airborne particles that can affect product integrity.
Understanding these global regulations helps ensure that manufacturers maintain compliance while also promoting a culture of quality. Additionally, numerous government agencies, such as the FDA in the United States, set forth requirements related to semiconductor devices, influencing how particle counters are utilized in those settings. Compliance with these regulations not only avoids potential penalties but also fosters trust among stakeholders and customers.
Industry Best Practices
Adopting industry best practices for regulatory compliance is crucial for effective wafer particle counting. Best practices often include regular calibration and maintenance of particle counters, comprehensive training programs for personnel, and stringent record-keeping systems. Proper calibration ensures that the counters function accurately, thus producing reliable data for analysis.
Furthermore, implementing a framework of continuous improvement — such as Lean or Six Sigma methodologies — can enhance the overall quality of the manufacturing process.
- Develop regular training schedules to educate staff on compliance and operational standards.
- Establish a routine for equipment inspection and calibration to maintain functionality.
- Maintain detailed documentation of processes and compliance checks to demonstrate adherence to regulations.
By emphasizing these best practices, manufacturers can not only achieve compliance but cultivate an environment conducive to innovation and operational excellence.
Challenges in Wafer Particle Counting
The accuracy of wafer particle counting plays a crucial role in semiconductor manufacturing. However, this process is not without its challenges. Understanding these challenges provides a more rounded perspective on the intricacies involved.
Technical Barriers
Technical barriers are among the foremost hurdles in wafer particle counting. These barriers can stem from the sophisticated measurement techniques required to ensure precision. Different particle sizes, materials, and shapes can all influence measurement accuracy. The detectors used must have the capability to differentiate between various particles while minimizing interference from external factors. Each components’ compatibility with the rest of the system also commands attention.
Calibration procedures represent another technical challenge. Regular calibration ensures that the equipment maintains its precision over time. Due to environmental factors and wear, recalibration might be needed oftern. This process can be resource-intensive and may lead to downtime in manufacturing.
The complexity of modern semiconductor designs also presents challenges. Advanced packaging techniques lead to narrower tolerances, demanding even higher sensitivity in particle count measurements. Limited access to critical areas of wafers can hinder comprehensive inspections, further complicating the counting process.
Economic Factors
Economic factors significantly impact the operation of wafer particle counters. The initial investment required for advanced particle counting systems can be substantial. This investment does not solely include the cost of the equipment but also encompasses installation, maintenance, and training of personnel. The funding necessary to implement cutting-edge technologies can strain budgets, especially for smaller manufacturers with limited resources.
Moreover, the costs associated with potential contamination events can escalate quickly. Even minor contamination issues can lead to significant production losses, requiring costly recalls or repairs. On the other hand, manual labor costs for monitoring and maintaining standard counting practices must also be factored into overall operational expenses.
In times of economic uncertainty, companies may be forced to prioritize immediate cost savings over long-term investments in advanced particle counting technologies. This can hinder their ability to adapt to evolving standards that require stricter contamination controls.
In summary,
"The overall health of the semiconductor industry is highly dependent on the ability to address these challenges in wafer particle counting."
Addressing both technical and economic barriers is vital for advancing measurement technologies in this field. Companies need to carefully evaluate their capabilities and resource allocations to remain competitive in an ever-changing market.
Case Studies in Wafer Particle Counting
Case studies in wafer particle counting provide invaluable real-world insights into the practical application of these technologies. They illustrate how industries leverage wafer particle counters to enhance quality control, improve production efficiency, and mitigate contamination risks. Often, theoretical concepts require empirical validation, and these case studies serve as clear examples of successful implementations and offer lessons learned.
Successful Implementations
Numerous companies have successfully integrated wafer particle counters within their production lines. One notable instance involves Intel Corporation, which incorporated advanced particle measurement technology in their microprocessor manufacturing. By adopting the latest innovation in optical systems, Intel reported a significant reduction in defects related to particle contamination. This case emphasizes how effective monitoring of wafer cleanliness aids in achieving higher yields of functional chips, ultimately enhancing operational profitability.
In another example, Samsung Electronics implemented real-time monitoring systems in their semiconductor fabrication plants. They utilized a hybrid approach, combining both light scattering and laser-based detection methods. This dual strategy not only improved detection sensitivity but also allowed for instantaneous feedback on environmental conditions. As a result, adjustments could be made promptly, optimizing functionality and reducing downtime in the production process.
Lessons Learned
From these implementations, several key lessons have emerged that can guide future projects involving wafer particle counters. First, the integration of measurement technology should prioritize flexibility and scalability. As production volumes fluctuate, having adaptable systems can accommodate varying requirements without extensive redesign.
Second, investing in training and education is crucial. Technical personnel must be fully versed in the operation and maintenance of these sophisticated devices. This ensures reliability and maximizes the benefit derived from the technology.
Lastly, ongoing collaboration between equipment manufacturers and end-users contributes significantly to system optimization. Tailoring solutions to specific production needs often reveals unique challenges and potential solutions that have not been anticipated.
"Understanding practical applications and learning from past experiences significantly enhance the adoption of innovative technologies in manufacturing environments."
In summary, case studies highlight the real-world impact of wafer particle counters in the semiconductor industry. By examining successful implementations and recognizing lessons learned, organizations can better navigate the complexities of particle counting technology.
Ending and Insights
In the realm of semiconductor manufacturing, the integration of wafer particle counters cannot be understated. They play a critical role in ensuring that the purity of wafers is maintained throughout the production process. As this article has explored, the significance of these devices extends beyond mere contamination measurement; they are essential for maintaining high yield rates and product quality. The insights gathered from this exploration highlight several key elements.
First, the accuracy of wafer particle counters directly influences the quality of semiconductor devices. This is particularly crucial in industries where even the smallest contaminants can lead to significant operational failures. Hence, investing in advanced wafer particle counters means investing in the long-term reliability of products.
Second, the technological advancements discussed earlier suggest that future devices are likely to be more sensitive and capable of detecting smaller particles. These efficiencies can lead to better quality assurance practices, ultimately saving costs associated with defects and recalls.
Additionally, the regulatory landscape mandates strict compliance with cleanliness standards, which makes wafer particle counters not just beneficial but necessary. Organizations that prioritize the implementation of these devices will likely see enhanced credibility and trust in their products.
Summary of Findings
The investigation into wafer particle counters has yielded numerous valuable conclusions:
- Significance: They are pivotal in detecting contaminants that can compromise the quality of semiconductor wafers.
- Technological Innovations: Continuous advancements are improving their accuracy and efficiency.
- Regulations: There are increasing demands for adherence to strict cleanliness standards globally.
- Cost Implications: Efficient monitoring can significantly reduce costs related to product defects and improve overall yield rates.
These findings underscore the importance of understanding how wafer particle counters operat and why they should be a priority in semiconductor manufacturing environments.
Future Research Directions
Future research in wafer particle counting technologies should focus on several impactful areas:
- Sensor Technology: Continued research into nanotechnology can enhance sensor capabilities, making them sensitive to even finer particulate matter.
- Data Integration: Developing methods to integrate data from particle counters with existing manufacturing systems could lead to more informed decision-making processes.
- AI in Measurements: Implementing artificial intelligence for real-time analysis could provide adaptive capabilities, optimizing operational processes.
- Sustainability Practices: Exploring the environmental impact of contamination on semiconductor production can stimulate innovation in sustainable manufacturing practices.
Overall, the field of wafer particle counting holds considerable potential for advancements, and targeted research can further enhance their effectiveness in semiconductor manufacturing.