In-Depth Exploration of 7075 Aluminum Alloy Properties
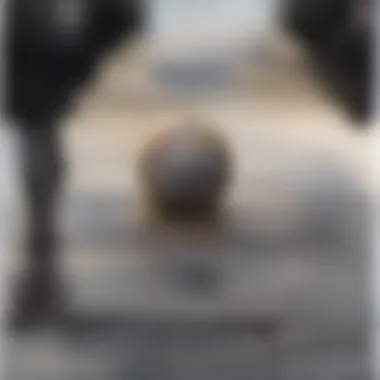
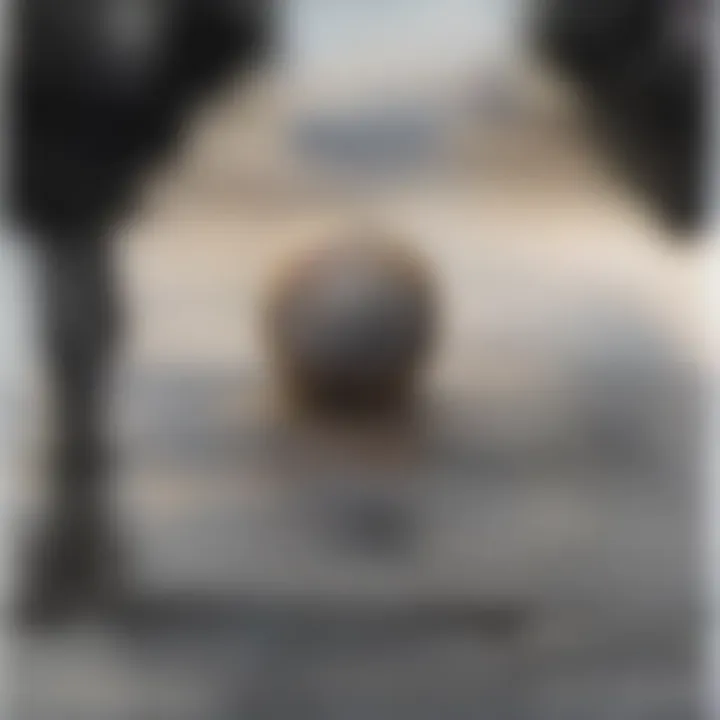
Intro
7075 aluminum alloy is recognized for its exceptional strength and is primarily utilized in industries demanding high performance, such as aerospace and military applications. Understanding its properties is crucial to optimizing its use in various engineered products. This section will convey a broad overview of the key concepts and terms that will be extensively discussed, such as its composition, mechanical properties, and corrosion resistance. The aim is to lay a foundation upon which more detailed discussions can be built.
When we talk about 7075 aluminum alloy, we often refer to the specific composition of aluminum mixed with zinc and other elements. This alloy’s unique attributes make it a favorable choice for many industrial applications. Below, we define the critical terminology and concepts that will be explored in this analysis.
Key Concepts and Terminology
Definition of Key Terms
- Alloy: A mixture of metals or a mixture of a metal and another element. In this case, 7075 is an alloy of aluminum.
- Tensile Strength: The resistance of a material to breaking under tension. 7075 aluminum alloy has high tensile strength, making it ideal for heavy-duty applications.
- Corrosion Resistance: The ability of a material to withstand damage caused by oxidization or other chemical reactions. The aluminum alloy is treated for better corrosion resistance.
- Heat Treatment: A process used to alter the physical and sometimes chemical properties of a material. For 7075, heat treatment enhances its mechanical properties.
Concepts Explored in the Article
The article will delve into several pertinent concepts:
- Composition Analysis: The specific elements that create the alloy and how they contribute to its properties.
- Mechanical Properties: Assessment of strength, ductility, and toughness of the alloy.
- Thermal Characteristics: Examination of thermal conductivity and heat treatment processes that enhance the alloy.
- Corrosion Activities: Evaluation of its resistance in various environments and the methods to enhance it.
- Applications: Discussing where 7075 aluminum alloy is applied in the real world, including aerospace, transportation, and sporting equipment.
- Manufacturing Advancements: The latest technology and processes in the alloy’s production.
By unpacking these key terms and concepts, we can better understand the relevance and implications of 7075 aluminum alloy in modern engineering and manufacturing practices.
"7075 aluminum alloy exemplifies a remarkable balance between strength and weight, crucial for high-performance applications."
Findings and Discussion
Main Findings
The findings highlight the alloy's superior mechanical properties, reinforced further by various heat treatments available. 7075 aluminum alloy offers a combination of lightweight and high tensile strength, which is crucial for efficient design in aerospace components, improving fuel efficiency and performance. Additionally, advancements in surface treatment processes can enhance corrosion resistance, ensuring longevity in various applications.
Potential Areas for Future Research
Future research should focus on exploring the capabilities of 7075 aluminum alloy in extreme environments, examining its fatigue resistance over time. Another aspect could be developing new alloys that blend the characteristics of 7075 with other materials for enhanced performance.
Foreword to Aluminum Alloy
7075 aluminum alloy stands as a prominent material in various industries due to its superior strength and versatility. Recognized mainly for its use in aerospace applications, it offers a balance of light weight and high performance, making it an ideal choice for aircraft structures and components. This section explores the unique characteristics that make 7075 alloy a preferred option in demanding environments.
One of the main reasons for the widespread use of 7075 aluminum is its composition, which includes zinc as the primary alloying element. This specific formulation results in exceptional mechanical properties, setting it apart from other aluminum alloys. Engineers and researchers often turn to 7075 due to its high tensile strength, which can exceed 570 MPa in certain heat-treated conditions. This strength enables engineers to design products that can withstand extreme stress without deforming.
When considering the benefits of using 7075 aluminum, lightweight is another critical factor. In aviation, every gram contributes to fuel efficiency. Thus, using 7075 allows manufacturers to engineer more fuel-efficient designs while maintaining structural integrity.
However, it is not just the advantages that merit attention. There are also considerations when selecting 7075 aluminum alloy for a specific application. Its susceptibility to stress corrosion cracking necessitates careful treatment and processing methods to enhance its durability in hostile environments. Consequently, this topic warrants a deeper exploration of properties, manufacturing processes, and operational considerations in the subsequent sections.
To summarize, the introduction of 7075 aluminum alloy provides a backdrop for understanding why this material is significant. Emerging trends in material science ensure that its role in industry will continue to evolve, aligning with technological advancements and new demands in various sectors. This understanding renders the subsequent examination of its properties and applications critical for anyone engaged in materials engineering.
Composition of Aluminum Alloy
The composition of 7075 aluminum alloy is critical to understanding its performance and applications. It plays a significant role in determining the alloy's mechanical and physical properties. Knowledge of the specific elements within 7075 allows engineers and material scientists to optimize its use in various industries, especially those that demand high strength and durability, like aerospace and automotive. Furthermore, understanding the composition helps in making informed decisions regarding manufacturing processes and treatment methods to achieve desired performance levels.
Primary Alloying Elements
7075 aluminum alloy is primarily known for its high strength, which is largely attributed to its main alloying elements: zinc, magnesium, and copper. These elements combine to enhance the mechanical characteristics of the alloy.
- Zinc is the principal alloying element in 7075, contributing significantly to its strength. It enhances the hardness and tensile strength, making this alloy one of the strongest aluminum alloys available.
- Magnesium promotes improved corrosion resistance and contributes to the alloy's workability. It helps maintain the alloy’s toughness, especially after heat treatment processes.
- Copper boosts strength and is crucial for the aging process, allowing the alloy to achieve high strength levels and excellent fatigue performance. However, it may slightly reduce the corrosion resistance.
This blend of elements creates an alloy that is not only strong but also effectively balances weight and reliability, making it suitable for demanding applications.
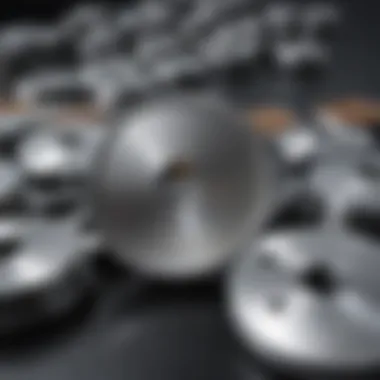
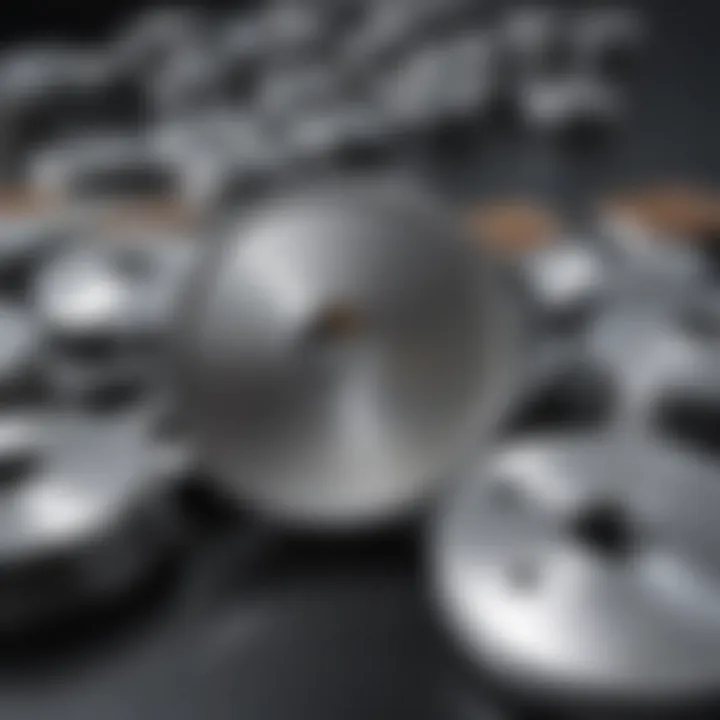
Trace Elements and Their Influence
Trace elements in 7075 aluminum alloy, although present in smaller quantities, also have considerable effects on the alloy's characteristics. These elements include manganese, silicon, and chromium, among others. Each contributes uniquely to the properties of the alloy.
- Manganese helps improve the resistance to corrosion and enhances the strength of the alloy, particularly in the welded condition.
- Silicon can improve fluidity and helps in casting applications, although it is typically present in lower amounts in 7075.
- Chromium can enhance strength and corrosion resistance, ensuring the material performs reliably in challenging environments.
While these trace elements might seem minor, they play a crucial role in the alloy's overall performance, ensuring that it meets stringent requirements for industries where safety and efficiency are paramount.
"Understanding the composition of 7075 aluminum alloy opens opportunities for innovation in engineering applications and processing techniques."
Overall, the intricate balance of elements in 7075 aluminum alloy emphasizes the importance of material selection in engineering and design, particularly for applications requiring high-performance materials.
Mechanical Properties
Mechanical properties play a pivotal role in defining the utility of 7075 aluminum alloy across various demanding sectors. Understanding these properties is crucial not only for engineers and designers but also for researchers focused on material science. The mechanical properties ascertain how the material will perform under tensile stress, fatigue, and extreme environmental conditions, thereby making it a fundamental consideration during the design and manufacturing processes.
The key aspects of mechanical properties include tensile strength, yield strength, fatigue resistance, hardness, and ductility. Each of these elements provides significant insights into the alloy's behavior and adaptability in practical applications. For industries like aerospace and automotive, where the integrity of materials can directly affect safety and performance, knowing these details becomes imperative. Furthermore, improvements in alloy formulations and processing techniques continually enhance these properties, keeping pace with the evolving demands of modern engineering.
"The mechanical properties of a material are crucial in determining its potential applications and performance under stress."
Tensile Strength and Yield Strength
Tensile strength refers to the maximum stress a material can withstand when being stretched or pulled before failing. In the case of 7075 aluminum alloy, it exhibits a tensile strength in the range of 570 to 700 MPa, depending on the temper. This high tensile strength is one of the major reasons it is favored in high-performance applications.
Yield strength is another essential measure, indicating the point at which a material deforms plastically. The yield strength of 7075 aluminum generally ranges from 450 to 505 MPa. This property ensures that the alloy can maintain its shape under significant loads without permanent deformation, essential for components exposed to fluctuating stress levels.
Fatigue Resistance
Fatigue resistance is the ability of a material to withstand repeated loading and unloading cycles without failing. 7075 aluminum alloy has commendable fatigue resistance, which is critical in applications where components experience cyclic stresses, such as in aircraft wings and automotive chassis. This property ensures longevity and reliability, which are essential for safety-critical applications.
Recent research has shown that innovations in alloy formulations can further enhance fatigue performance by optimizing the microstructure, leading to better load distribution during cycles of stress.
Hardness and Ductility
Hardness is a measure of a material's resistance to localized plastic deformation, which helps in assessing wear resistance and surface durability. 7075 aluminum impacts hardness significantly, often described with a Vickers hardness rating ranging from 150 to 180 HV.
Contrastingly, ductility refers to the material's ability to deform under tensile stress, often represented as elongation. While 7075 has decent ductility, it is essential in applications where some amount of deformation is desirable before failure occurs. This characteristic is vital during machining operations, where materials undergo significant shaping and forming processes.
Thermal Properties of Alloy
Understanding the thermal properties of 7075 aluminum alloy is crucial for its application in various industries. These properties dictate how the material behaves under temperature changes, influencing its performance in practical scenarios. Engineers and manufacturers must consider these attributes to ensure optimal application and performance of the alloy in demanding environments. This section will highlight key thermal properties, including thermal conductivity and thermal expansion coefficient, and discuss their implications.
Thermal Conductivity
Thermal conductivity refers to a material's ability to conduct heat. For 7075 aluminum alloy, this property is particularly significant. A high thermal conductivity means that the material can dissipate heat efficiently, which is essential in applications where temperature management is crucial. This quality enhances the longevity of components subjected to high temperatures, as rapid heat dissipation can prevent overheating.
Typically, the thermal conductivity of 7075 aluminum alloy is around 130 W/m·K. Compared to other aluminum alloys, 7075 offers reasonable thermal conductivity. However, it may not be the best choice in situations where superior thermal management is a priority. For example, in aerospace applications, effective heat management can impact the performance and safety of aircraft structures.
Factors Influencing Thermal Conductivity:
- Composition: The presence of alloying elements like zinc and copper can affect how well heat is conducted.
- Microstructure: The way the alloy is processed influences its thermal properties. Heat treatment processes can either enhance or degrade thermal conductivity.
- Temperature: As heat increases, the conductivity of aluminum alloys generally increases but at varying rates depending on the specific alloy formulation.
Thermal Expansion Coefficient
The thermal expansion coefficient (TEC) measures how much a material expands when heated. For 7075 aluminum alloy, the TEC typically ranges between 22.5 to 24.0 µm/(m·K). This value indicates a moderate expansion rate compared to other metals. Understanding the TEC is essential in applications where precise tolerances are critical.
Thermal expansion in 7075 alloy must be managed carefully, especially in assemblies of different materials. Mismatched expansion rates can lead to stresses in joints, which may cause failure over time.
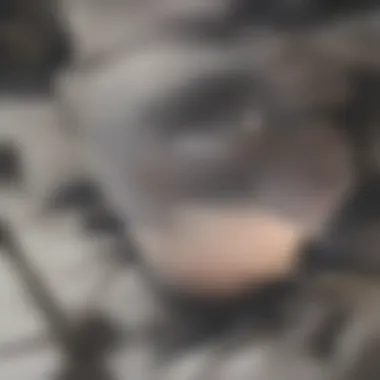
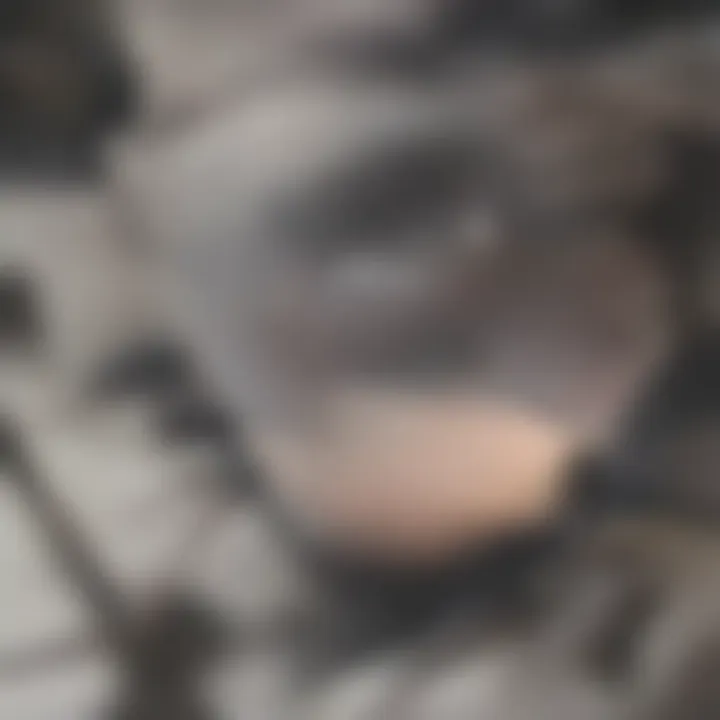
Key Points About Thermal Expansion:
- Design Considerations: When designing components that include 7075 aluminum alloy, engineers must consider the expansion characteristics to avoid structural integrity issues.
- Application Scenarios: Different applications can be affected uniquely by TEC. In aerospace constructions, for example, parts need to maintain tight tolerances despite temperature fluctuations.
- Influence of Heat Treatment: The production process can alter TEC values, emphasizing the need for rigorous testing after fabrication.
In summary, the thermal properties of 7075 aluminum alloy are integral to its usage in various applications. Understanding thermal conductivity and expansion behaviours helps engineers make informed decisions, ensuring the durability and safety of their designs. Effective management of these properties can lead to improved performance and reduced maintenance costs for end-users.
Corrosion Resistance
Corrosion resistance is a key property of 7075 aluminum alloy that impacts its performance in various environments. Understanding this aspect is essential, particularly for industries where material integrity is critical. Corrosion can lead to structural failures and safety hazards, especially in fields like aerospace and automotive manufacturing. Thus, examining the alloy’s response to environmental factors and protective measures is crucial.
Effects of Environmental Factors
Several environmental factors can significantly affect the corrosion resistance of 7075 aluminum alloy. Moisture, salt presence, and temperature fluctuations are prime examples.
- Moisture: High humidity or contact with water can initiate corrosion, especially if the alloy is not protected.
- Salinity: Exposure to saline environments accelerates the corrosion process, particularly for alloys not specifically formulated for such conditions.
- Temperature Changes: Extreme temperatures can also impact corrosion resistance, with high temperatures often accelerating the chemical reactions that lead to corrosion.
Research illustrates how surface conditions, including the formation of a natural oxide layer, can influence the corrosion rates. The pH level of the surrounding environment can also play a role. In alkaline or acidic conditions, the alloy may experience different corrosion behaviors.
Protective Coatings and Treatments
Implementing protective coatings and treatments is vital in enhancing the corrosion resistance of 7075 aluminum alloy. Various methods exist, each offering distinct advantages.
Common protective strategies include:
- Anodizing: This process creates a thick oxide layer which enhances corrosion resistance and can also improve wear characteristics.
- Alclad Layering: A thin layer of pure aluminum is bonded to the surface, providing a barrier against corrosion.
- Paint and Sealants: These not only provide aesthetic benefits but also serve as a protective barrier against environmental exposure.
It is important to note that the effectiveness of these treatments can depend on the specific application. Choosing the appropriate coating or treatment can significantly prolong the life of components made from 7075 aluminum, reducing maintenance costs and improving reliability.
In summary, understanding corrosion resistance is critical in the practical application of 7075 aluminum alloy, making proper selection of protective measures a necessity for various industries.
Processing and Fabrication Techniques
The processing and fabrication techniques of 7075 aluminum alloy play a crucial role in determining its performance in various applications. Understanding these methods is essential for engineers and manufacturers looking to optimize the alloy's strengths. This section delves into the key processes involved in shaping 7075 aluminum, highlighting specific techniques and considerations that influence material characteristics.
Casting and Forging Methods
Casting and forging are two primary techniques used in the fabrication of 7075 aluminum alloy. Casting involves pouring molten metal into a mold where it solidifies into the desired shape. This method is advantageous for producing complex shapes efficiently. However, careful control of the melt temperature and cooling rates is necessary to avoid defects like porosity.
Forging, on the other hand, involves shaping the aluminum by applying compressive forces. This method enhances the alloy's microstructure, resulting in improved mechanical properties like strength and toughness. The forging process can also refine grain structure, making it particularly suitable for high-stress components.
"The selection between casting and forging influences not just shape but the overall integrity of the final product."
Key Points on Casting and Forging:
- Complexity: Casting allows for intricate designs that would be difficult to achieve with other methods.
- Strength: Forging improves material strength through work hardening.
- Cost Efficiency: Both methods can be optimized for cost, depending on production volume and design requirements.
Welding and Machining Considerations
Welding and machining are additional vital processes in the fabrication of 7075 aluminum alloy. Welding requires special attention because of the alloy's propensity to crack when exposed to high heat. Preheating the workpieces and using appropriate filler materials can mitigate these risks. Selecting the right welding technique, such as gas tungsten arc welding (GTAW), is also essential to ensure strong joints without compromising performance.
Machining of 7075 aluminum can be complex due to its hardness. The use of the correct cutting tools and techniques is important to prevent excessive wear on the equipment. Coolant can be implemented during machining to enhance tool life and ensure a smooth finish. Proper clamping methods are critical to avoid distortion during machining.
Important Considerations:
- Welding Techniques: GTAW is preferred for its precision and control over the heat input.
- Tool Selection: Carbide tools are effective for machining due to their durability.
- Cooling: Adequate cooling prevents overheating and maintains integrity during processing.


Applications of Aluminum Alloy
The 7075 aluminum alloy is renowned for its exceptional strength and lightweight properties. These characteristics make it an ideal choice for a variety of applications across different industries. Understanding the applications of 7075 aluminum is essential for industry professionals and designers aiming to leverage its benefits effectively. The alloy's notable attributes also influence design considerations, fabrication processes, and performance outcomes.
Aerospace Industry Use Cases
7075 aluminum is widely utilized in the aerospace sector due to its high strength-to-weight ratio. It is often found in aircraft structures such as wings, fuselage components, and landing gear. These components require materials that maintain structural integrity while minimizing weight. 7075 aluminum excels in these scenarios, continuing to meet the rigorous demands of air travel.
Furthermore, aerospace designs often involve exposure to various environmental conditions. The alloy’s significant fatigue resistance and corrosion resistance contribute to its use in critical applications. Engineers often select 7075 aluminum not only for its strength but also to ensure component longevity under harsh conditions.
Automotive Engineering Applications
In automotive manufacturing, 7075 aluminum alloy is becoming more common as manufacturers strive to produce lighter and more fuel-efficient vehicles. It is used in parts like chassis components, wheel rims, and high-stress load areas where durability is vital. The lower weight of 7075 aluminum leads to improved handling and fuel efficiency, addressing modern automotive performance standards.
Another consideration in automotive applications is safety. Components made from 7075 aluminum can withstand high-impact forces, providing enhanced safety features in vehicles. Its machineability also allows for precision manufacturing processes, ensuring that components fit seamlessly within intricate assemblies vital for vehicle performance.
Sports Equipment Manufacturing
In the sporting goods industry, 7075 aluminum is valued for its application in high-performance equipment. Items such as bicycles, skis, and camping gear often utilize this alloy. The lightweight nature of 7075 aluminum allows for ease of use and transport, which is a significant advantage for athletes and outdoor enthusiasts.
Additionally, the strength of 7075 aluminum enhances the durability of sports equipment. For example, manufacturers of bicycle frames leverage its properties to create products that withstand tough conditions without adding unnecessary weight. The alloy’s performance under mechanical stress plays an important role in competitive sports, where durability is required without compromising speed or mobility.
"The use of 7075 aluminum alloy in sports gear optimizes performance by providing lightweight yet durable materials essential for athletes."
In summary, the applications of 7075 aluminum alloy span numerous fields, including aerospace, automotive, and sports. Each one takes advantage of the alloy’s unique properties, ensuring that the material remains relevant and essential in modern engineering and manufacturing pursuits.
Recent Advancements in Aluminum Technology
The field of aluminum alloys is always evolving. Recent advancements in 7075 aluminum technology are crucial for maintaining its position in competitive industries. These developments focus on refining alloy formulations and enhancing processing techniques. They aim to improve the properties and applications of this versatile material further.
Innovations in Alloy Formulations
The ongoing research into 7075 aluminum has led to innovative alloy formulations. These new combinations seek to increase strength while maintaining or improving other critical properties such as ductility and corrosion resistance. For example, incorporating elements like lithium can optimize the balance between weight and durability. This specific innovation is significant in sectors such as aerospace, where reducing weight is essential for improving fuel efficiency.
Moreover, additive manufacturing techniques are being explored. This approach allows for tailored properties and unique geometries that traditional processing cannot achieve. By leveraging these innovations, manufacturers can produce components that meet the precise requirements of specific applications while minimizing material waste.
"Developments in alloy formulations play a pivotal role in enhancing the functionality and application range of 7075 aluminum, catering effectively to the evolving needs of various industries."
Enhancements in Processing Techniques
Advancements in processing techniques for 7075 aluminum have also been noteworthy. These include improved heat treatment and machining processes that enhance mechanical properties and surface finish. More efficient heat treatment processes can lead to a finer microstructure, which benefits tensile strength and fatigue resistance.
Furthermore, advanced machining strategies, such as high-speed machining and machine learning applications, are being integrated into production. These methods increase precision and reduce processing time, leading to considerable cost savings.
The combination of new alloy formulations and enhanced processing techniques not only elevates the performance of 7075 aluminum but also paves the way for its application in cutting-edge technological solutions. Continuous improvement in these areas will be important for companies looking to push the boundaries of what 7075 aluminum can achieve.
Closure and Future Directions
The conclusion of this study provides a synthesis of the information regarding 7075 aluminum alloy. This alloy is notable for its combination of strength, light weight, and favorable mechanical properties. In wrapping up, we should highlight three key findings: the importance of its composition, the significance of its mechanical properties, and the role of innovative processing methods.
Summary of Key Findings
The primary findings of this article include:
- High Strength: 7075 aluminum alloy exhibits superior tensile and yield strength, making it a prime choice in high-stress applications such as aerospace and automotive industries.
- Corrosion Resistance: While naturally susceptible to corrosion, the application of appropriate protective coatings can enhance its durability in hostile environments.
- Versatility in Applications: Its various forms, including sheets, plates, and extrusions, offer engineers flexibility in design and implementation across different sectors.
These points illustrate the essential qualities that make 7075 a material of choice for demanding applications. Understanding these elements is crucial for engineers and designers seeking to maximize performance while minimizing weight.
Emerging Trends in Material Science
With developments continuously emerging in material science, 7075 aluminum alloy is also benefiting from innovative research and technology. Some trends shaping its future include:
- Advanced Alloys: New formulations for 7075 are being introduced that enhance its fatigue resistance and further reduce its weight without compromising strength.
- Sustainability: There is a growing emphasis on sustainable manufacturing processes. Integrated recycling programs for aluminum alloys are increasingly important in maintaining an eco-friendly manufacturing environment.
- Smart Materials: The incorporation of smart technology into materials is on the rise. Researchers are exploring mechanisms that allow 7075 to respond to environmental changes, further enhancing its utility.
In summary, the future of 7075 aluminum alloy looks promising. As new technologies and methods emerge, this alloy will continue to evolve, finding new applications and remaining a key material in advanced engineering fields.