Understanding the Cement Production Process Thoroughly
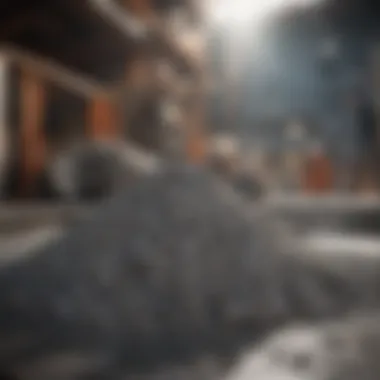
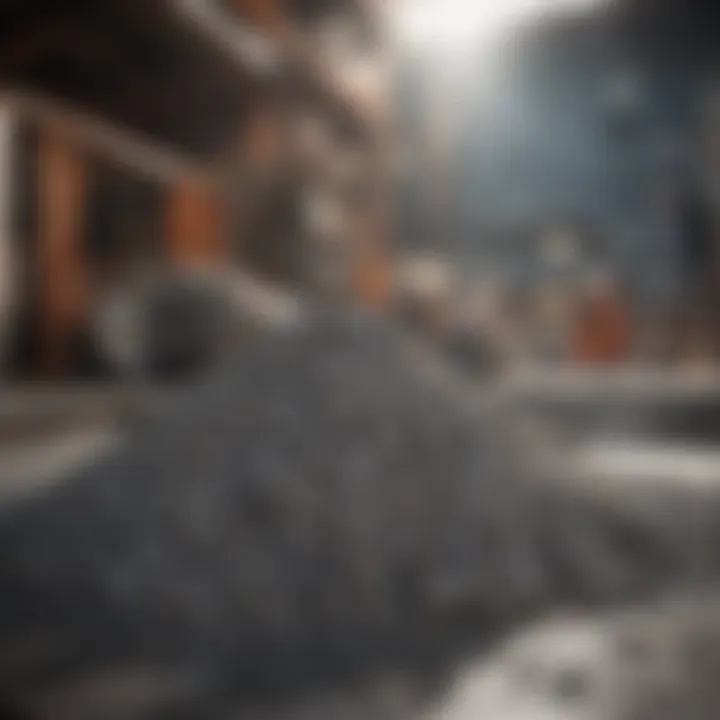
Intro
Cement stands as one of the cornerstones of modern construction, providing the essential material that shapes everything from skyscrapers to bridges. Its impact is immense and often underestimated. As we step into the intricate realm of cement production, it’s crucial to recognize how various elements come together in a symphony of science and engineering. This journey encapsulates the careful balancing of natural resources, human ingenuity, and technological advancements.
To truly grasp the significance of cement, one must delve into its production process, made up of several interlinked stages. It’s not just about mixing a few ingredients; it’s about managing every step—from raw material extraction to creating that final strong product which ensures durability in construction.
In this article, we will breakdown this multifaceted process, highlighting its relevance not just in construction, but also in environmental considerations and technological enhancements. By the end, you'll have a thorough understanding of how cement production operates and its broader implications.
Key Concepts and Terminology
Definition of Key Terms
Before plunging into the nitty-gritty of the cement production process, it's important to familiarize yourself with some of the terminology that will pop up:
- Clinker: This refers to the solid material produced in the kiln during the cement manufacturing process, crucial for the formation of cement.
- Aggregate: These are the materials—like sand, gravel, or crushed stone—that are mixed with cement to create concrete.
- Hydration: A chemical process where water reacts with cement to harden and strengthen.
Concepts Explored in the Article
We will cover a range of topics:
- Extraction and preparation of raw materials
- Specific stages in production: grinding, blending, heating, and cooling
- Quality control measures throughout the production process
- Environmental considerations that come into play
- Innovations shaping the future of cement technology
Findings and Discussion
Main Findings
The exploration of the cement production process reveals several critical insights:
- Raw Material Dependence: The quality of cement hinges on the raw materials used, demanding careful selection and extraction techniques for optimal results.
- Energy Consumption: Cement production is energy-intensive; thus, advances in technology are focused on decreasing energy use while maintaining production quality.
- Environmental Impact: The emissions from cement manufacturing contribute significantly to global CO2 output, underscoring the need for more sustainable practices in the industry.
Potential Areas for Future Research
Looking ahead, there are several opportunities for research and improvement in the cement production process:
- Exploring alternative raw materials that reduce environmental impact.
- Investigating new energy-efficient processing methods that cut emissions.
- Developing stronger yet lighter forms of cement that could reshape the construction landscape.
"The production of cement is not just a matter of chemistry; it’s an interplay of technology, sustainability, and practicality that influences the very foundations we build upon."
Prologue to Cement Production
Cement stands as a cornerstone in the world of construction, a silent partner that underpins just about every building we see around us. The significance of cement production cannot be overstated. It serves as a binding agent in various construction materials, largely responsible for the integrity and durability of structures. This article delves deep into the cement production process, unraveling the multifaceted levels of craftsmanship that lie behind one of the most pivotal components in modern architecture and engineering.
Understanding cement production is crucial for several reasons. First, it provides insight into the various materials and techniques involved in creating cement. Familiarity with the raw ingredients alongside the production sequence gives one an appreciation of the complexities that engineers and technicians manage daily.
Moreover, with the ongoing focus on sustainability and environmental practices, comprehending the intricacies of cement production equips stakeholders with knowledge to innovate and implement eco-friendlier methods. There’s also the economic aspect – cement production is a billion-dollar industry with market dynamics that can affect prices and availability of key materials.
This foundational knowledge serves students, researchers, and industry professionals alike. It’s about fostering a comprehensive understanding that touches upon not just the step-by-step process of cement manufacturing but also the quality measures involved as well as the technological advancements shaping the industry’s future. Ultimately, the goal is to create a narrative that elevates the understanding of cement production beyond mere statistics and figures, exploring its historical roots and modern relevance.
Historical Significance of Cement
To appreciate cement's role in today's construction scene, one must first take a step back in history. The use of cement as a building material dates back thousands of years. The ancient Romans pioneered its usage, laying down durable roads and constructing stunning structures like the Pantheon, which still stands today. Their blend of volcanic ash, lime, and seawater created a substance we would recognize as cement in various forms.
As times progressed, cement saw various iterations and improvements. The invention of Portland cement in the 19th century was a game-changer. Named after the Isle of Portland, famous for its stone, this form became the bedrock of modern construction. It enabled the construction of not just buildings but bridges and roads that could withstand significant weight and stress. This marked the beginning of significant urbanization and architectural innovation that has carried on into modern times.
Cement's Role in Modern Construction
Fast forward to the present day, and cement remains integral to architectural design and engineering. It serves not just as a bind but contributes significantly to thermal mass, durability, and resistance to environmental elements. With advancements in technology, different types of cement have emerged, catering to specific structural needs. For instance, high-strength cement is favored for skyscrapers and prolonged durability, while white cement is often chosen for aesthetic finishes in decorative applications.
In terms of infrastructure, cement has a central role in building foundations, roadways, tunnels, and bridges. More than mere gray powder, it’s the backbone of modern civilization. As cities expand and populations grow, the demand for innovative structures will only continue to rise, making understanding the cement production process more relevant than ever.
"Cement is the primary material that supports the infrastructures of our societies, shaping the world we live in both practically and aesthetically."
Thus, grasping not just the production techniques but their historical context and modern applications completes the picture of why cement production deserves our focused analysis in this article. Knowing where cement comes from and how it has evolved enhances our appreciation for both the material and the mastery behind crafting robust, lasting structures.
Raw Materials for Cement Manufacturing
The foundation of cement production lies firmly in the selection and processing of raw materials. To produce high-quality cement that meets diverse construction needs, an array of raw materials is utilized. These include limestone, clay, iron ore, and gypsum, each contributing unique properties and essential characteristics that influence the final product.
Understanding these materials is crucial not only for production but also for ensuring durability and strength in construction applications. The benefits of using quality raw materials are manifold—enhanced performance, sustainability, and cost-effectiveness being at the forefront. However, considerations surrounding availability, quality control, and environmental impacts are equally vital in the discussion of raw materials for cement manufacturing.
Primary Components of Cement
Limestone
Limestone is the star player when it comes to the primary components of cement. It forms the bulk of the clinker produced in the kiln, contributing significantly to the strength and durability of the final product. This sedimentary rock, primarily composed of calcium carbonate, plays a crucial role in the chemical reactions during heating. The key characteristic of limestone is its availability in large deposits with variable purity, which makes it a cost-effective choice in many regions.
A unique feature of limestone is its ability to contribute not just to the chemistry but also to the physical properties of the cement. When heated, it produces a quicklime that reacts with silicates and aluminates present, forming compounds responsible for strength. One downside is that depending on its source, limestone can vary in impurities, which might affect the final product if not carefully managed.
Clay
Clay serves as a complementary material in cement production, providing silica, alumina, and iron oxide. Its fine-grained texture is essential for achieving a homogenized blend with limestone, enhancing material reactivity during processing. The key characteristic of clay is its plasticity when wet, which allows it to be easily shaped and mixed.
One notable advantage of clay is its abundance and renewability; it's often found near limestone sources, making transportation more efficient. However, controlling moisture content and impurities are essential, as excessive organic materials in clay can lead to inconsistent quality in the final cement product.
Iron Ore
Iron ore is another fundamental material that contributes to the overall composition of cement. This raw material primarily provides iron oxide, which plays a pivotal role in the formation of specific compounds during the heating phase. The key characteristic of iron ore is its ability to enhance the strength and performance of cement under various environmental conditions.
Iron ore is often viewed as a beneficial additive because its presence can improve the strength of concrete in infrastructure projects. However, sourcing high-quality iron ore can sometimes be challenging. If the ore contains excessive impurities, it could lead to issues with the final product's performance, which is why ongoing quality assessments are necessary.
Gypsum
Gypsum, often seen as the finishing touch in cement production, is critical for controlling the setting time of cement. Added at the end of the clinker production process, it helps regulate how quickly the cement hydrates, making it easier to manage during construction. The key characteristic of gypsum is its solubility and ability to interact positively with water.
Its unique feature lies in its role in preventing flash set, which can occur when water is mixed with cement too quickly. This characteristic ensures that the cement remains workable for a defined period, allowing construction processes to proceed smoothly. Gypsum's downside is that high concentrations can sometimes lead to delayed setting times if not monitored carefully.
Supplementary Cementitious Materials
In addition to primary substances, supplementary cementitious materials like fly ash and slag also play a significant role in the cement production process, enhancing properties and promoting sustainability.
Fly Ash
Fly ash is a byproduct of coal combustion, and it's become a popular choice in modern cement production due to its versatility. This pozzolanic material contributes to increased strength and reduced permeability in concrete. The key characteristic of fly ash is its fine powder form, which allows for better integration into cement mixes.
Its unique feature lies in its ecological benefits; using fly ash can substantially reduce the carbon footprint of cement production by recycling waste material. However, one must always be cautious, as the variability in quality among different sources can lead to inconsistencies in cement performance.
Slag
Slag, which is produced during the metal smelting process, is another valuable resource. It enhances the long-term strength of cement and improves resistance to various environmental factors, such as sulfate attack. The key characteristic of slag is its ability to impact the setting time favorably, helping prevent rapid hardening.
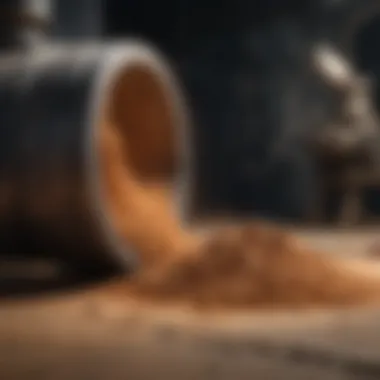
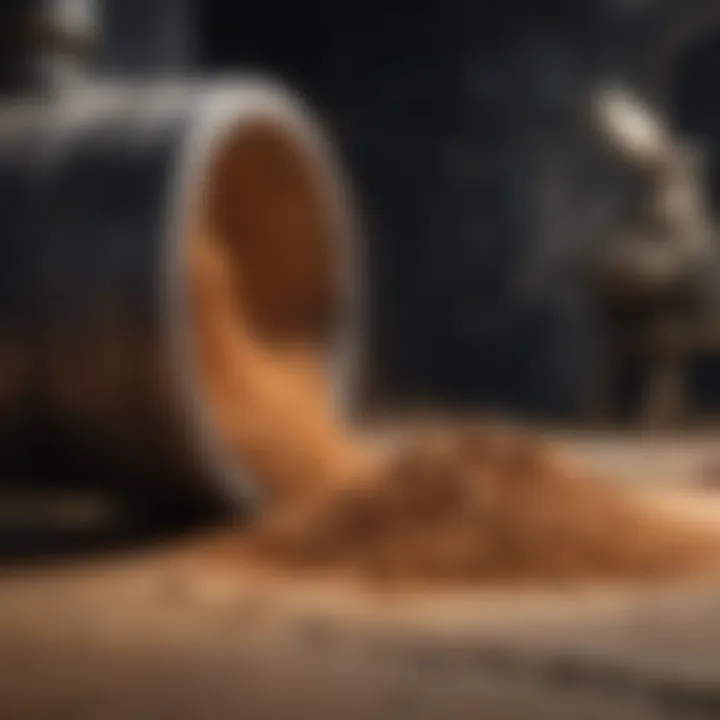
The unique feature of slag is its latent hydraulic properties, which means it can react with lime in the presence of moisture. This property makes it particularly advantageous for infrastructure projects that require durability. A potential disadvantage arises from the requirement for proper grinding to achieve fineness similar to that of Portland cement, which can sometimes add to production costs.
The Cement Production Process Overview
The cement production process is both intricate and critical to the construction industry. Understanding the various stages involved not only enhances one’s appreciation for this vital material but also sheds light on how each phase impacts the quality and attributes of the final product. This overview sets the stage for a deeper dive into the operations behind cement manufacture, emphasizing the interconnectedness of the tasks at hand.
Stages of Cement Production
Extraction
The extraction of raw materials is the first crucial step in the production chain. It typically begins with the quarrying of limestone, which is the primary ingredient in cement. The limestone's availability in various geographic locations makes it a widely favored choice for this process. One of the key characteristics of extraction lies in its dependency on careful planning and execution; it demands monitoring of environmental factors, ensuring that activities do not adversely affect the surrounding ecosystem.
A unique feature of extraction is its reliance on heavy machinery. This not only accelerates the process but also enhances efficiency, which leads to a lower cost of production. However, this approach also poses challenges, such as potential damage to the landscape and the necessity for strict regulations regarding land use.
Processing
Once materials are extracted, they undergo processing, which comprises two phases: crushing and grinding. The processing phase transforms the massive, rough chunks of rock into fine powders, facilitating uniform blending. This is crucial because the quality of the final cement product is heavily influenced by the thoroughness of the processing. The reliability of this phase is substantial; it aligns with the goal of achieving consistent particle sizes, which subsequently aids in the efficiency of the heating process.
Among the processing tasks, one special characteristic is the use of technology, such as automated systems, to enhance precision and speed. While the advantages are clear—higher efficiency and risk reduction—processing also presents some drawbacks. Notably, the equipment involved can be costly and requires ongoing maintenance to avoid disruptions in production.
Heating
The heating phase is where the transformation truly takes place, as raw materials are calcined in a kiln at extreme temperatures ranging from 1400°C to 1600°C. This process results in the formation of clinker, a semi-finished product. One of the benefits of the heating stage is its ability to initiate the chemical reactions that change the raw material’s properties, ultimately defining the nature of the cement being produced.
A significant feature of this phase is the type of kiln employed—rotary kilns are common due to their efficiency and effectiveness in maintaining consistent heat flow. Though this method is efficient and widely accepted, the environmental implications, such as greenhouse gas emissions, cannot be overlooked. The cement industry is increasingly under pressure to incorporate cleaner technologies, making the heating phase a point of ongoing development and innovation.
Overall Workflow in Cement Manufacturing
The overall workflow in cement manufacturing is a culmination of many interdependent steps, each playing a pivotal role in creating quality cement. From the initial extraction of raw materials through processing and finally to the heating stage—each phase is structured to ensure that potential inefficiencies are minimized.
Crucially, communication and coordination among different teams—is vital at each point in the workflow to maintain progress and ensure adherence to regulatory standards. Each stage not only feeds into the next but also requires ongoing assessments and adaptations to meet quality control benchmarks, thereby ensuring a high-quality final product.
"The true art in cement production lies in the harmony between raw materials and advanced technology to produce reliable construction solutions."
In this article, the intent is to unravel the complexities of these processes, highlighting how they all contribute to producing the cement vital for modern infrastructure. Understanding this comprehensive structure is fundamental for students, researchers, and industry professionals alike as it provides insights into both the challenges and innovations facing the cement industry today.
Extraction of Raw Materials
The extraction of raw materials stands as a cornerstone in the process of cement production. This phase focuses on obtaining fundamental components that will form the backbone of cement manufacturing. Understanding the intricacies of this process underscores its relevance not only for quality assurance but also for environmental sustainability. The materials extracted typically include limestone, clay, iron ore, and gypsum, each possessing unique properties that contribute to the final product.
Quarrying Techniques
When it comes to quarrying, the methods employed greatly impact the efficiency of raw material extraction. Traditional techniques often involve drilling and blasting, by which explosives are utilized to break apart rock formations. For instance, limestone, being a primary ingredient in cement, is usually extracted from open-pit quarries. Here, companies may employ the use of heavy machinery like excavators and loaders for the excavation. Every so often, this method raises concerns about environmental degradation, hence alternative techniques like controlled blasting or hydraulic methods are starting to see more action. These methods strive to minimize vibration and control dust emissions — crucial in maintaining the surrounding ecosystem.
- Drilling and Blasting: Commonly used for limestone, involves explosives to fracture the rock.
- Hydraulic Methods: Use of high-pressure water to excavate, reducing noise and vibration.
- Controlled Blasting: Focused on minimizing environmental disruption while efficiently removing materials.
Effective quarrying not only ensures the procurement of quality raw materials but also sets a precedent for operational efficiency and safety.
Transportation of Raw Materials
Once the raw materials are extracted, the next step involves their transportation to processing facilities. This part of the process requires careful planning and execution to maintain quality and reduce costs. Selecting the right transportation method can depend on the geographical features of the site and the types of materials being moved.
Common practices for transporting raw materials include:
- Conveyor Belts: Efficient for transporting materials over varying distances, minimizing manual handling.
- Trucks: Offer flexibility, especially for short distances; can navigate rough terrains where infrastructure may be lacking.
- Rail Systems: Ideal for bulk transport over longer distances; these can be more economical and environmentally friendly compared to road transport.
"The logistics of raw material transportation are often just as critical as the extraction itself in determining the overall sustainability and cost-effectiveness of cement production."
Adopting an optimized transportation plan can minimize material loss, ensure timely delivery to processing plants, and adhere to quality standards. It is essential to integrate these practices within a comprehensive production strategy as they lay the groundwork for subsequent stages of cement manufacturing.
Processing of Raw Materials
Processing of raw materials is a critical phase in cement production, serving as the backbone of the entire manufacturing process. This step dictates not only the efficiency of production but also significantly affects the quality of the final product. A well-executed processing phase ensures that all components are finely prepared, setting a strong foundation for the subsequent stages.
When we talk about the importance of processing raw materials, there are a few core elements that come into play:
- Consistency in Composition: Variation in raw materials can impact the chemical balance essential for clinker formation, which we can imagine as baking a cake; if you change the recipe too much, the cake might not rise the same way. This consistency is achieved through precise measuring, crushing, and blending methods.
- Reduction of Particle Size: Crushing and grinding are primary focuses here. By reducing the particle size, we increase the surface area of the materials, which leads to better chemical interaction during the heating phase. Think of it like breaking up sugar to dissolve it faster in water.
- Homogenization: This ensures uniformity across the raw materials. If you’ve ever made a smoothie, you understand the need to blend everything thoroughly; inconsistency can lead to a less than delightful drink. The same principle applies to cement production, where blending helps eliminate variations in material properties.
Crushing and Grinding
The crushing and grinding of raw materials represent the first hands-on effort in processing. These are fundamental operations that can significantly enhance the efficiency of the cement production process. During crushing, larger aggregates are broken down into smaller pieces. This often involves primary crushers that handle the bulk materials, followed by secondary crushers to further reduce the size.
Once crushed, the materials undergo grinding, where they are pulverized into a fine powder. This is generally done using ball mills or vertical roller mills—each method offering different benefits. The finer the particles, the more reactive they are during the kiln phase.
Key Points to Consider:
- The choice of crushers and mills influences energy consumption. Efficient machinery cuts costs in the long run.
- Proper maintenance of equipment is vital to minimize downtime and ensure a consistently high-quality end product.
Blending and Homogenization
Following crushing and grinding, blending and homogenization become crucial. This phase brings together the various powdered raw materials to ensure a uniform mix. Achieving this uniformity is paramount, as it determines the overall quality of the clinker produced later in the process.
In this context, blending might involve both physical mixing techniques and chemical adjustments. Advanced technologies like automatic blending systems can help monitor and adjust the material composition in real-time, ensuring that deviations are corrected swiftly, similar to adjusting spices while cooking to achieve the desired flavor.
Important Note: The homogeneity of the raw materials directly influences the properties of the final product. A well-homogenized mix enhances the predictability of the cement’s performance, which is vital for construction projects.
This stage might also include the use of supplementary cementitious materials like fly ash or slag, which can not only reduce the energy requirements associated with the heating process but also improve the performance characteristics of cement without compromising quality.
The Clinker Production Phase
The clinker production phase is a pivotal step in the overall cement manufacturing process. It marks the transition from raw materials to a material that has the potential to create sturdy concrete. During this phase, raw materials undergo significant transformations under high temperatures, leading to the formation of clinker—a key ingredient in cement. This section delves into the critical aspects of this phase, highlighting the kilns used, the thermal treatment involved, and the reactions that occur during the process. Understanding the clinker production phase is essential as it significantly influences the properties of the final cement product.
Kiln Types and Designs
Rotary Kiln
The rotary kiln is the most prevalent design utilized in cement production. This long, cylindrical furnace rotates slowly and is inclined slightly so that materials can move from one end to the other by gravity. The main contribution of the rotary kiln to the clinker production phase lies in its ability to maintain a consistent temperature throughout the material passage, which is crucial for the chemical reactions necessary for clinker formation.
One of the key characteristics of the rotary kiln is its high efficiency in energy usage. By continuously moving materials and evenly distributing heat, it ensures that the raw mix is adequately sintered. This method is beneficial because it leads to a more homogeneous clinker that exhibits improved properties in the final cement product.
However, there are some drawbacks. Rotary kilns require significant investment in terms of capital and maintenance. They also occupy a large footprint in production facilities. Despite these challenges, the advantages, such as scalability and process efficiency, make rotary kilns the choice for many cement manufacturers.
Vertical Kiln
On the other hand, the vertical kiln is known for its simplicity and lower cost. Unlike its rotary counterpart, this kiln operates in an updraft or downdraft mode, where materials move vertically through the kiln. This design allows it to produce clinker with less energy consumption, which is a significant advantage in areas where resources are limited.
A notable characteristic of vertical kilns is their ability to handle a more varied composition of raw materials without compromising the quality of clinker produced. This flexibility makes them advantageous for smaller operations where specific material availability can fluctuate.
Despite its benefits, vertical kilns come with limitations. They often produce a less homogeneous clinker than rotary kilns, which can lead to variability in the final product. Moreover, the production capacity is typically lower, making them less suitable for large-scale operations. Nonetheless, for specific applications and regions, vertical kilns can be an efficient solution in the cement production phase.
Thermal Treatment and Reactions
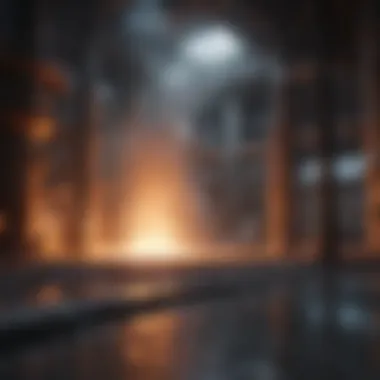
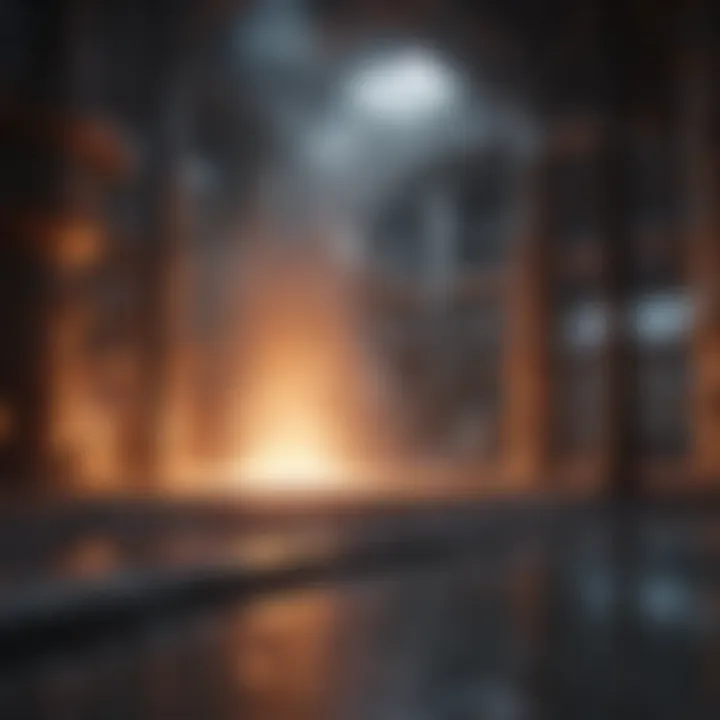
Thermal treatment in the clinker production phase is critical, as it involves applying intense heat to convert raw materials into clinker through a series of complex reactions. The temperatures in the kiln can soar above 1400°C, facilitating the transformations necessary for creating the final product.
At this stage, the raw materials, mainly limestone and clay, experience calcination, which involves the decomposition of calcium carbonate into calcium oxide and carbon dioxide. This reaction not only contributes to the formation of clinker but also highlights the importance of controlling emissions, as a significant amount of carbon dioxide is released during this process.
The reaction sequence during thermal treatment is intricate. The calcium oxide combines with silica, alumina, and iron oxide at high temperatures to form various compounds, crucial components of clinker, such as tricalcium silicate and dicalcium silicate. These compounds are essential for the cement's strength and setting characteristics.
"The interplay of temperatures and raw materials during this phase is what ultimately dictates the quality and functionality of the cement produced."
Understanding the thermal treatment and the resulting reactions sheds light on why specific practices, such as preheating and precalcining, are integrated into modern cement production. These methods improve efficiency by reducing the energy requirements and enhancing the quality of the clinker produced.
In summary, the clinker production phase is central to the cement manufacturing process. The choice between rotary and vertical kilns significantly influences energy consumption and product quality, while the thermal treatment and reactions determine the characteristics of the final product. This phase highlights the intricate balance between technological efficiency and production quality, ultimately affecting the performance of cement in real-world applications.
Cooling and Grinding of Clinker
Cooling and grinding of clinker represent critical steps in the cement production process. These operations not only influence the energy efficiency of the manufacturing procedure but also significantly affect the final characteristics of the cement produced. Properly managing these stages ensures that the cement meets stringent quality standards while optimizing operational costs.
The cooling phase is vital as it aids in stabilizing the clinker structure and minimizes the formation of unwanted compounds. In addition, this process allows the cement to achieve the appropriate crystalline form, which is essential for ensuring its durability and strength. Furthermore, quickly cooling the clinker can enhance the grindability of the material.
Methods of Cooling
Clinker cooling can be done in several effective ways, each with distinct advantages:
- Air Cooling: In this method, ambient air is blown over the clinker. This is a cost-effective process but may not provide uniform cooling. The heat absorbed by the surrounding air can be a concern, affecting energy recovery systems.
- Water Cooling: This approach involves spraying water onto the clinker. It provides rapid cooling improving the quality of the clinker by reducing the risk of overburning or premature hydration. However, it requires careful management to avoid excessive thermal expansion and cracking.
- Cooling Grates: A more advanced technique where clinker is spread over a grate to allow air to flow through. This process not only cools the clinker efficiently but also helps in reclaiming heat energy to optimize the overall operational efficiency.
Each method has its own set of considerations regarding energy savings and efficiency, thus requiring a comprehensive analysis to determine the most suitable option for a given plant.
Final Grinding Process
Once the clinker has cooled, it enters the final grinding stage, which transforms the chunky material into the fine powder recognized as cement. This phase is equally significant, as insufficient grinding can lead to variability in the performance of the final product.
The grinding stage typically involves:
- Ball Mill Grinding: The most commonly used method where clinker, along with a small percentage of gypsum, is fed into rotating cylindrical drums with steel balls. The sheer motion causes the materials to crush and grind effectively, resulting in a fine powder.
- Vertical Roller Mills: These are becoming increasingly popular due to their energy efficiency. They use large rollers to crush the material against a rotary table, producing a consistently fine product while consuming less energy.
- Other Alternate Technologies: New technologies, such as high-pressure grinding rolls (HPGR), are also gaining traction. They operate by crushing the clinker using high-pressure rollers, providing significant energy savings compared to traditional methods.
"Efficient grinding is crucial not just for product quality but also impacts the energy consumption of the entire process. Optimization can lead to tangible savings and lower emissions, making it a focal point in modern cement production."
Quality Control in Cement Production
Quality control in cement production plays a pivotal role in ensuring that the final product meets the required specifications and standards for various construction applications. Cement acts as the backbone of the construction industry, and subpar quality not only jeopardizes structural integrity but can also incur significant financial losses and safety risks. Given the varying compositions of raw materials and the complex interactions during the production process, maintaining rigorous quality control measures is crucial.
One of the primary benefits of quality control is minimizing variability in the finished product. When raw materials like limestone, clay, and gypsum are sourced, they can differ in terms of chemical composition, moisture content, and particle size. By establishing thorough testing protocols, manufacturers can identify and eliminate inconsistencies that may affect cement properties such as strength, workability, and durability.
Moreover, quality control ensures compliance with environmental regulations, an increasingly critical aspect of cement production. The industry faces mounting pressure to minimize environmental impact. Hence, monitoring emissions during production processes not only satisfies regulatory requirements but also fosters a culture of sustainability. For instance, detailed checks on particulate emissions and greenhouse gases help manufacturers align with legal standards while reaffirming their commitment to responsible practices.
Testing Methods for Raw Materials
Testing methods for raw materials are essential in determining their suitability for cement manufacturing. Various techniques are employed to assess the chemical and physical properties of raw materials:
- Chemical Analysis: This involves analyzing the elemental composition of materials to ensure they align with specified requirements. Methods such as X-ray fluorescence (XRF) spectroscopy or inductively coupled plasma (ICP) can provide accurate assessments.
- Physical Characterization: Techniques like sieve analysis help determine particle size distribution, which significantly impacts grinding and required energy consumption.
- Moisture Content Analysis: Knowing the moisture content is vital for determining the appropriate drying process and for calculating the correct batch proportions for mixing.
Regular sampling and testing throughout the procurement and production stages can help preemptively discover any anomalies. Consistency in the quality of raw materials directly correlates to the final properties of the cement produced.
Quality Assurance of Finished Product
Quality assurance of the finished product focuses on verifying that cement meets the specified standards and customer requirements. Various methods and practices can be put into place:
- Strength Testing: Standard tests such as compressive strength assessment at specific curing times provide insight into the cement’s performance.
- Setting Time Evaluation: Determining the initial and final setting times ensures that the cement will perform effectively in different environmental conditions.
- Durability Testing: Assessments for resistance to sulfate attack, water absorption, and freeze-thaw cycles help establish the longevity of the cement in actual applications.
Implementing a quality management system based on international standards like ISO 9001 can fortify these assurance practices. This involves not just product checks, but also maintaining effective records, regular audits, and continuous improvements over time.
"Quality is not an act, it is a habit." - Aristotle
An unwavering commitment to quality can yield long-term benefits and promote trust in the cement industry among all stakeholders.
For more information on quality control practices, visit Wikipedia or Britannica.
Environmental Considerations in Cement Production
In today's world, awareness of environmental concerns has taken center stage in nearly every industry. Cement production, as a major contributor to global carbon emissions, faces significant scrutiny. This section delves into the importance of addressing these factors, focusing on emission control measures and sustainable practices in cement manufacturing. The implications of these environmental considerations extend beyond the industry itself, affecting climate change, air quality, and community health.
Emission Control Measures
Cement production is responsible for approximately 8% of global carbon dioxide emissions. This staggering figure underscores the need for effective emission control measures. Thankfully, many advancements are bridging the gap between manufacturing and environmental responsibility.
Implementing efficient technology is one of the crucial steps for reducing emissions. Here are a few methods currently in play:
- Carbon Capture and Storage (CCS): This involves capturing CO2 emissions before they enter the atmosphere and storing them effectively underground. This technology shows promise in reducing overall emissions.
- Alternative Fuels: By replacing traditional fossil fuels with alternative fuels, such as waste-derived fuels, the carbon footprint of cement production can be significantly lessened. These alternatives provide energy while simultaneously diverting waste from landfills.
- Energy Efficiency Improvements: Optimizing processes to use less energy naturally leads to a reduction in CO2 emissions. Using waste heat recovery systems represents a practical approach to enhancing overall efficiency without compromising production capacity.
"Integrating emission control measures is not just beneficial for the environment; it often leads to cost savings in the long run, highlighting that sustainability and efficiency can go hand in hand."
Sustainable Practices in Cement Manufacturing
Incorporating sustainable practices within the cement industry is not merely a nice-to-have; it has become an urgent necessity. The focus here shifts to methods of production that minimize environmental impacts while ensuring economic feasibility.
- Use of Supplementary Cementitious Materials (SCMs): Materials like fly ash and slag can replace portions of traditional clinker, leading to lower CO2 emissions. These by-products can enhance the performance of cement products while decreasing the raw material needed for production.
- Water Management: Effective water management strategies can drastically reduce water usage in cement production. Recycling wastewater for certain processes is one innovative approach that not only saves water but also lessens the burden on local water bodies.
- Community Engagement: Building relationships with local communities about production activities and their environmental impacts is pivotal. Transparent communication fosters trust and can lead to joint efforts for sustainability initiatives.
Adopting these sustainable practices not only helps in managing the ecological footprint but also aligns with the increasing pressure from regulatory bodies and concerned stakeholders.
At the end of the day, environmental considerations in cement production are non-negotiable. As the sector grapples with evolving technologies and regulatory frameworks, the urgency for integration into day-to-day practices remains high, shaping the future of construction.
Innovations in Cement Technology
In the ever-evolving field of construction materials, innovations in cement technology stand as a cornerstone that transforms not only how cement is produced, but also how it performs in various applications. These advancements are significant for multiple reasons. Firstly, they enhance the efficiency of the production process. For instance, new methods aim to reduce the energy consumption associated with cement manufacturing, thus lowering operational costs. Secondly, innovative techniques are geared toward improving the durability and sustainability of cement, which aligns with the increasing global focus on eco-friendly practices.
Advancements in Production Techniques
Recent strides in production techniques reflect a commitment to both efficiency and sustainability. For example, techniques such as dry process manufacturing have emerged as more energy-efficient compared to traditional wet methods. This shift not only conserves water but also minimizes the waste generated during production.
Moreover, the incorporation of alternative fuels, like biomass, has changed the landscape of cement kilns. By replacing traditional fossil fuels, these alternatives cut down on carbon dioxide emissions, enhancing the eco-friendliness of the cement industry. Utilizing waste materials from other industries as raw materials further contributes to the circular economy.
- Higher efficiency: Advanced kiln designs, like the use of pre-calciner technology, allow for more efficient thermal exchange, optimizing energy usage.
- Use of pozzolans: Integrating materials such as natural pozzolans into the production process not only boosts the strength of the cement but also reduces the total clinker production, leading to lower emissions.
Smart Technologies in Cement Plants
The rise of smart technologies in cement plants has revolutionized how the industry operates. The utilization of artificial intelligence, real-time monitoring systems, and automation are reshaping operations.
With these smart technologies, data analytics play a pivotal role. Cement plants can predict maintenance needs, assess production efficiency, and optimize resource consumption. This predictive capability ensures not only cost reduction but also increases the longevity of machinery and equipment, which is essential in maintaining uninterrupted production cycles.
"The integration of smart technology in cement production is not just a trend; it’s a fundamental shift towards a more sustainable and efficient future."
The following highlights show how smart technology is applied within cement production:
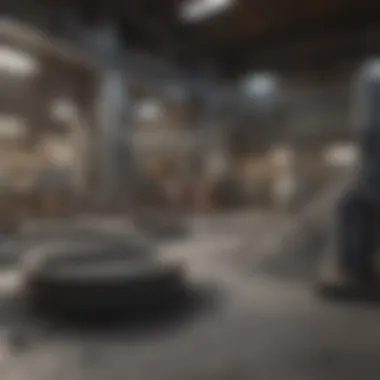
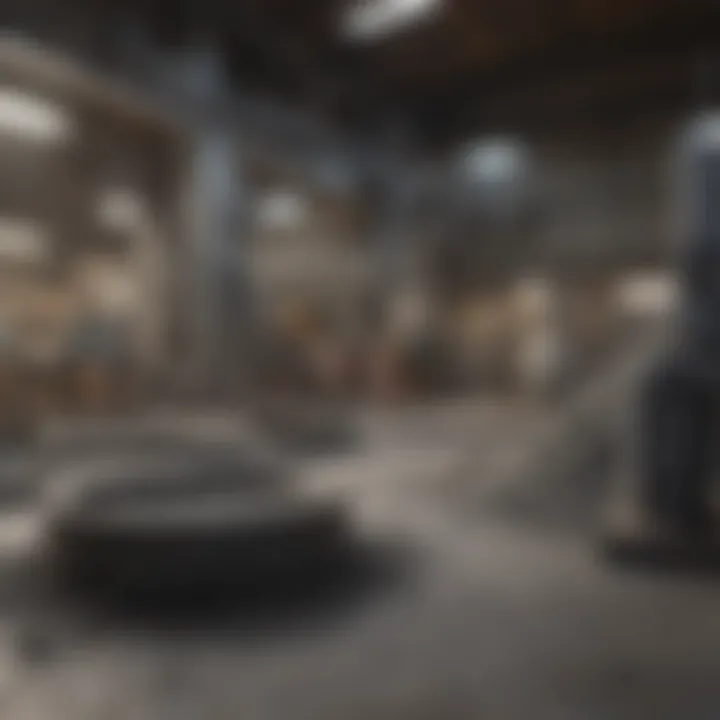
- IoT Sensors: These devices gather real-time data on energy usage, temperature, and emissions, helping managers make informed decisions.
- Automated quality control: Systems that analyze the chemical composition of cement during production ensure that the final product meets stringent quality standards without constant manual testing.
Applications of Cement in Construction
Cement serves as the backbone of modern construction, acting as a fundamental ingredient in various structural and non-structural applications. Understanding its applications is crucial for professionals in the field, as it heavily influences material choice, project cost, and overall durability. Cement is not merely a binding agent but also a pivotal element shaping the integrity and longevity of construction projects.
From towering skyscrapers to the humblest of homes, cement's versatility is unmatched. It contributes to different construction techniques, ranging from the traditional to contemporary methods, ensuring resilience and stability. A key consideration in its application is recognizing the appropriate type of cement for the specific environments and structural needs.
Different Types of Cement and Their Uses
Portland Cement
Portland cement is the most widely used type of cement in construction, forming the standard against which other cements are measured. Its recognition stems from its robust strength and durability, making it a go-to choice for a diverse range of construction projects. Characteristically, Portland cement hardens as a result of hydration, entering a series of chemical reactions that yield a solid, rock-like structure.
One of the unique features of Portland cement is its adaptability. It can be mixed with various aggregates (like sand and gravel) to achieve the desired strength and workability. However, the specific aspect of Portland cement that amplifies its popularity is its capacity to perform well under different environmental conditions, lending itself effectively to both indoor and outdoor applications.
While the strengths of Portland cement are clear, it does come with its share of disadvantages. For instance, it can be prone to cracking due to shrinkage and is also significantly affected by moisture levels during curing.
Blended Cement
Blended cement combines Portland cement with supplementary materials, such as fly ash or slag, thereby enhancing its properties and functionalities. This mixture not only helps improve the durability and strength of concrete but also enhances its resistance to various environmental factors. One of the key characteristics of blended cement is its redeeming feature of sustainability. Using industrial byproducts as part of its composition reduces waste and promotes eco-friendliness in construction.
In terms of unique features, blended cement offers improved workability and can be advantageous in complex applications, such as mass concrete pours. It also exhibits lower heat of hydration, making it suitable for use in large structures. However, it's worth noting that blended cement may require more meticulous quality control during mixing and application to ensure consistency in performance.
Role of Cement in Infrastructure Development
Cement plays an indispensable role in infrastructure development, forming the backbone of public and private works alike. From highways to bridges, cement is a vital component in creating durable and reliable infrastructures. Its structural capacity allows for complex designs and supports the ever-growing demands of urbanization.
Moreover, the properties of cement make it an ideal material for road construction. Its adaptability allows roads to withstand heavy traffic and adverse weather conditions, thus serving the community more effectively. Similarly, in the production of precast elements, such as walls and beams, cement’s robustness ensures that these structures maintain their integrity under various stresses.
"Cement isn't just a material; it's an essential part of the fabric of construction that shapes our cities and infrastructure."
Economic Considerations of Cement Production
The economic aspects of cement production hold significant weight within the broader context of the construction industry. They dictate not only the pricing of cement but also influence the operational strategies of manufacturing plants. Understanding these economic considerations is crucial, as they shape business decisions that can drastically impact profitability, market competitiveness, and sustainable practices.
Cost Factors in Cement Manufacturing
The production of cement involves several layered cost factors that, when understood, can lead to more efficient business strategies. These costs often break down into the following categories:
- Raw Material Costs: The first input in the production process comprises the geological materials needed, primarily limestone, clay, iron ore, and gypsum. The volatility of these materials in the market can lead to fluctuating production costs, impacting profitability.
- Energy Expenditures: Cement manufacturing is energy-intensive. The kiln operations, which consume a vast amount of energy, largely determine the overall production cost. Pricing trends in fossil fuels and electricity can directly affect the bottom line for producers.
- Labor and Employment Costs: Skilled labor is needed for various production facets, from handling raw materials to quality control. In some regions, a labor shortage drives wages upward, cutting into profit margins.
- Transportation and Logistics: Moving heavy materials from quarries to plants and distributing finished products to construction sites involves considerable logistics costs. Fluctuations in fuel prices can lead to unpredictable expenditure in this area.
Managing these cost factors effectively can lead to better pricing strategies, ensuring cement remains competitive in a crowded market.
Market Trends Affecting the Cement Industry
The cement industry does not operate in a vacuum; it is deeply influenced by broader market trends that can reshuffle priorities and approaches at a moment's notice. Here are some trends worth noting:
- Sustainable Construction Demands: As environmental awareness grows, many construction projects now favor sustainable practices. Cement producers are increasingly offering eco-friendly alternatives, such as blended cements that incorporate supplementary cementitious materials. This trend not only addresses environmental concerns but also creates new market opportunities.
- Construction Growth Rates: Economic cycles greatly impact the construction sector. For instance, an upturn in housing starts or infrastructure projects can lead to an increase in cement demand. Conversely, economic downturns often stall projects and reduce the need for cement.
- Technological Advancements: Innovations in production techniques, such as the increased use of automation and data analytics, can lead to cost reductions and efficiency improvements, allowing firms to respond better to market demands while maintaining healthy margins.
- Global Supply Chain Fluctuations: The global nature of cement production means events overseas—be it political unrest, trade policies, or natural disasters—can ripple through supply chains. For cement manufacturers, being agile can help mitigate these risks.
Challenges in Cement Production
The cement industry, despite being a cornerstone of modern construction, faces a myriad of challenges that influence its production processes and overall sustainability. Understanding these challenges is crucial, as they highlight both the complexities of manufacturing and the pressing need for innovation. Through examining these challenges, readers will gain insights into the operational hurdles and compliance pressures that shape the cement sector's future.
Operational Challenges
Operational challenges are an everyday reality for cement manufacturers. To start, one prominent issue is the fluctuation of raw material costs. Since limestone, clay, and other ingredients can be subjected to market volatility, companies often find their budgeting thrown off course. Additionally, maintaining a steady and reliable supply chain for those materials is also critical. A disruption in the supply of limestone can have a domino effect, delaying production and inflating costs down the line.
Another layer of complexity arises from the intricacies of the production technology itself. Cement plants utilize vast amounts of energy to power their operations, which presents both economic and environmental concerns. Efficient energy management becomes a balancing act; while companies aim to reduce operational costs, they must also adhere to quality standards which can demand higher energy consumption.
Moreover, there’s the delicate matter of workforce management. Skilled labor is essential to navigate the technical challenges of cement production. However, many plants struggle to attract and retain qualified workers. High turnover rates can lead to inconsistent work quality and, ultimately, product integrity.
Compliance with Environmental Regulations
Compliance with environmental regulations poses yet another formidable challenge for cement producers. In recent years, the global focus on sustainability has intensified scrutiny on industries known for significant carbon emissions. Cement production generates a substantial amount of carbon dioxide, primarily through the calcination of limestone and the combustion of fossil fuels in kilns.
Regulatory frameworks vary widely across regions but tend to grow stricter over time, requiring plants to implement emission control technologies. While this can be costly, many companies view it as an opportunity to innovate and enhance production efficiency.
Furthermore, the increasing expectation for sustainability has led to a rising interest in alternative fuels and raw materials. However, transitioning to greener alternatives can be a double-edged sword. On one hand, it reduces reliance on traditional fossil fuels; on the other hand, it necessitates adjustments in the existing production process, which may require upfront investments and employee training.
"With the pressure to conform to stringent environmental standards, the cement sector must adapt or face serious repercussions in both regulatory compliance and public perception."
In summary, challenges in cement production encompass a spectrum of operational and regulatory hurdles. Tackling these obstacles will be essential for the industry's progress. By putting in place strategies to manage costs, enhance workforce stability, and comply with environmental mandates, cement manufacturers can not only ensure their survival but potentially lead the way in sustainability within the construction sector.
Future Trends in Cement Production
The cement production industry is on the cusp of a major transformation, driven by innovation and a growing commitment to sustainability. As society shifts towards more eco-friendly building practices, understanding future trends in cement production becomes increasingly vital for stakeholders at all levels, from manufacturers to consumers.
Among the most critical aspects to consider is how these trends can help reduce environmental impact while also enhancing production efficiency. This section delves into the emerging technologies and practices that may redefine cement production, ultimately benefiting quality control and addressing regulatory challenges.
Emerging Technologies and Their Impact
Cement production is experiencing a wave of technological advancements that promise to change how the industry operates. Here are key innovations making waves:
- 3D Printing: This technology is gradually making its presence felt in construction, allowing for the development of complex structures using less material. It significantly cuts down on waste, and this efficiency could lead to lower production emissions.
- Alternative Fuels: Many plants are starting to use alternative fuels, such as biomass or waste-derived fuels, instead of fossil fuels. This shift not only reduces CO2 emissions but also presents a cost-effective way of operating.
- Carbon Capture Utilization and Storage (CCUS): As emissions regulations tighten, finding efficient ways to capture and either reuse or store CO2 is gaining traction. The development of effective CCUS technologies could help cement manufacturers meet legislative requirements while continuing to operate profitably.
By integrating these technologies, cement production could not only better align with environmental regulations but also enhance operational efficiency.
Predictions for the Cement Industry
Looking ahead, several predictions can be outlined for the cement sector. These insights provide a framework for what could shape the future:
- Greater Focus on Sustainability: The push for carbon neutrality is unlikely to fade. We can expect an increase in demand for high-performance, eco-friendly cement types, which might incorporate more supplementary materials like fly ash or slag.
- Digitalization and Automation: Smart factories are already on the horizon. The integration of IoT devices and AI in production processes will streamline operations, improve quality control, and reduce downtimes.
- Global Market Changes: Economic fluctuations can heavily impact the availability and cost of raw materials. The industry might see zones or regions specializing in specific cement types based on local resources, which will ultimately affect global market dynamics.
- Increased Research and Development: With innovative solutions consistently emerging, companies will likely ramp up R&D efforts to stay competitive. Expect collaboration between academia and industry to foster groundbreaking discoveries in cement chemistry and application.
"The future of cement production lies not just in technological advancements but in how well these innovations align with the world's urgent need for sustainability."
In summation, the shifting landscape of cement production suggests that the industry must adapt to a variety of factors. From technology to sustainability, these trends encapsulate the challenges and opportunities ahead. The future promises a steady evolution, emphasizing the industry's role in a rapidly changing world.
Closure and Final Thoughts
In wrapping up our exploration of the cement production process, it becomes clear that understanding this intricate procedure is not merely an academic exercise; it holds significant practical implications for a range of stakeholders in the construction industry. From the sourcing of raw materials to the final stages of production, each element contributes to the quality and performance of the end product. This connection underscores the need for rigorous quality control measures, sustainable practices, and continuous innovation to enhance efficiency and reduce environmental impact.
Recap of the Cement Production Process
Cement production is a multifaceted journey involving several key stages:
- Extraction of Raw Materials: This stage includes quarrying of limestone, clay, and other components essential for cement making.
- Processing of Raw Materials: Involves crushing, grinding, and blending raw materials to achieve the desired uniformity and composition.
- Clinker Production: Heating the blended materials in kilns where chemical reactions occur, yielding clinker as a primary output.
- Cooling and Grinding of Clinker: Techniques are employed to cool and grind the clinker, transforming it into the fine powder we recognize as cement.
- Quality Control: Throughout the process, strict testing and assurance protocols are in place to guarantee that the produced cement meets industry standards.
The recap not only highlights the steps involved but also clarifies how each phase impacts the overall quality of the cement produced.
The Importance of Understanding Cement Production
Grasping the nuances of cement production transcends basic knowledge; it enables professionals in the field—architects, engineers, and construction managers—to make informed decisions that can directly affect project outcomes. For instance:
- Material Selection: Knowledge of various cement types allows for proper selection based on project requirements. Using Portland cement for durability in foundations, or blended cement for projects seeking sustainability, is vital.
- Cost Management: Recognizing how different production methods and material choices impact costs can lead to more budget-friendly project execution.
- Innovation: Staying informed about advancements in cement technology fosters a culture of innovation, encouraging the use of more efficient materials and practices that can drastically alter construction timelines and environmental footprints.
Understanding cement production is thus not just relevant for the production side, but crucial for all factors involved in construction projects—from initial planning through execution and maintenance. With such insights, stakeholders can optimize their practices, aligning their operations with contemporary expectations for sustainability and quality.