Ergonomics in Manufacturing: Enhancing Safety and Efficiency
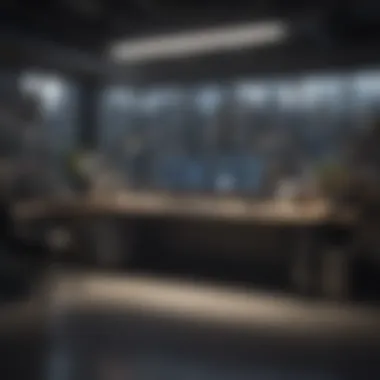
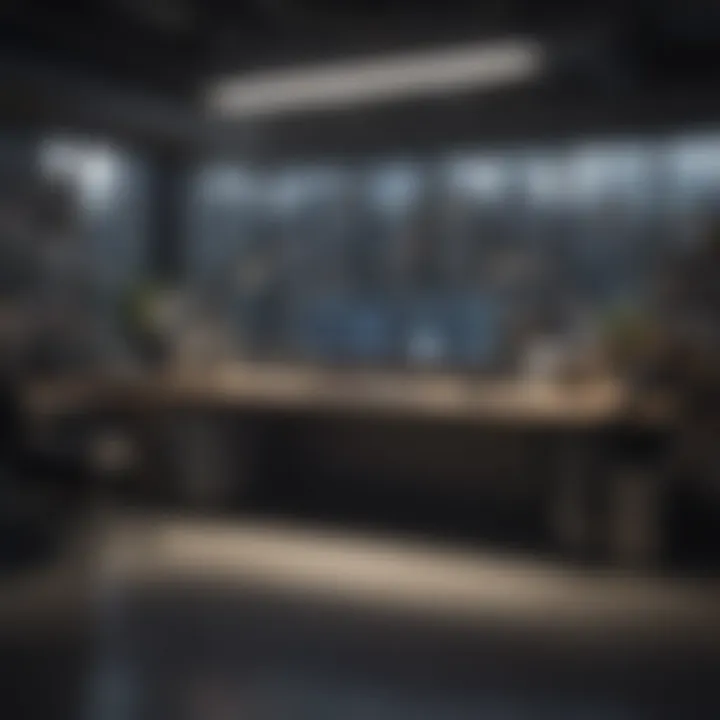
Intro
In the bustling world of manufacturing, where the clang of machinery blends with the hum of human effort, ergonomic principles stand as a cornerstone for cultivating a more efficient and safer working environment. This focus on ergonomics isn’t merely a fleeting trend; rather, it’s an essential strategy that resonates through every aspect of workplace design and operation. When we talk about ergonomics, we refer to the intricate balance between human capability and the demands of their tasks, all aimed at enhancing both performance and satisfaction.
By acknowledging the physical, cognitive, and organizational factors at play, businesses can carve out a space where workers not only thrive but also feel valued.
Key Concepts and Terminology
Definition of Key Terms
Before diving deeper, it's essential to grasp the foundational terminology that shapes our understanding of ergonomic concepts. Here are some key terms that frequently come up:
- Ergonomics: The science concerned with the design of equipment and processes that optimize human well-being and overall system performance.
- Posture: The position in which someone holds their body when standing or sitting.
- Repetitive Strain Injury (RSI): Injuries caused by repetitive tasks and awkward postures, commonly encountered in manufacturing settings.
- Workplace Design: The arrangement of workspace elements, including equipment, furniture, and tools, to suit its users' needs.
Concepts Explored in the Article
This guide will engage with several core concepts integral to understanding how ergonomic principles shape manufacturing:
- Worker Safety: Investigating how ergonomics contribute to a safer working landscape.
- Productivity Enhancement: Understanding the positive correlation between ergonomic practices and productivity.
- Job Satisfaction: Exploring how well-designed work environments boost morale and reduce turnover rates.
- Balance Between Efficiency and Well-Being: Delving into the strategic equilibrium between operational productivity and employee health, emphasizing the long-term benefits of investing in ergonomic solutions.
"Prioritizing ergonomics in manufacturing is not just beneficial; it's essential for sustainable growth and worker retention."
Findings and Discussion
Main Findings
Research indicates a clear link between effective ergonomic strategies and improved job performance. Some notable findings include:
- Reduced Injury Rates: Implementing ergonomic assessments in factories leads to a marked decline in workplace injuries, directly saving costs associated with worker compensation and lost productivity.
- Enhanced Efficiency: Workers in ergonomically tailored settings have been shown to complete tasks faster and with fewer errors, driving overall productivity upwards.
- Higher Employee Retention: Job satisfaction stemming from ergonomic design can contribute to enhanced employee loyalty. Companies prioritizing ergonomics often witness lower turnover rates.
Potential Areas for Future Research
Despite the clear advantages, there are areas where further exploration could yield significant insights:
- Long-term Well-being Effects: More studies could focus on how ergonomic improvements impact the long-term health of workers, examining not just immediate benefits, but also chronic conditions that may develop over time.
- Cost-Benefit Analyses: Detailed economic analyses could help businesses weigh the initial investment in ergonomic interventions against the long-term benefits gained.
- Innovation in Technology: The role of emerging technologies in supporting ergonomic practices, such as artificial intelligence in predicting and mitigating workplace hazards, presents a ripe area for investigation.
As the manufacturing landscape continues to evolve, the commitment to ergonomic principles remains vital for creating not only a safer but also a more productive work environment.
Prelims to Ergonomics in Manufacturing
Ergonomics in manufacturing is not just a buzzword; it’s foundational for optimizing the workspace and enhancing worker experience. In environments where precision and efficiency are paramount, understanding ergonomic principles can be the difference between thriving and merely surviving. As manufacturers face pressures from productivity demands and safety regulations, the importance of ergonomic adjustments cannot be overstated. It’s all about making the workplace fit the worker, not the other way around.
Defining Ergonomics
At its core, ergonomics refers to the study of how people interact with their environment, particularly in the workplace. It involves designing tools, workspaces, and tasks to ensure that they are tailored to the physical capabilities and limitations of workers. Think of it as creating a symbiotic relationship between people and their equipment.
When defining ergonomics, one can break it down into several key components:
- Physical Ergonomics: Focuses on human anatomical, anthropometrical, physiological, and biomechanical characteristics. This area emphasizes how work tasks can be designed around the body's capabilities.
- Cognitive Ergonomics: Deals with mental processes, such as perception, memory, and decision-making, regarding interactions between humans and systems.
- Organizational Ergonomics: Involves the optimization of sociotechnical systems, which includes the organizational structure, policies, and processes.
By understanding these aspects, manufacturers can create a holistic approach that not only meets safety standards but also enhances comfort and productivity on the production floor.
The Role of Ergonomics in Manufacturing
Ergonomics plays a crucial role in manufacturing by addressing common challenges that arise in repetitive and physically demanding jobs. The integration of ergonomic principles can lead to significant benefits in various ways:
- Reduction of Work-Related Injuries: When workstations are designed with workers' physical needs in mind, injuries related to repetitive strain, awkward postures, or excessive force can be significantly reduced. This leads to fewer sick days and better overall health for employees.
- Increase in Productivity: By minimizing discomfort, workers can maintain focus longer and perform tasks more efficiently. When employees are comfortable, they are more likely to produce quality work at a higher volume.
- Employee Satisfaction: A workplace that prioritizes ergonomics fosters a culture of care and respect. This can enhance job satisfaction and retention rates, as employees feel valued and tended to.
- Economic Benefits: From a financial perspective, the implementation of ergonomic solutions can lead to a reduction in workers' compensation claims, less training on repetitive injury prevention, and can even enhance production times.
"Investing in ergonomics isn’t just about compliance; it's about creating a better future for both the business and its workers."
In summary, the role of ergonomics in manufacturing transcends simple comfort; it encompasses improving safety, facilitating efficiency, and cultivating a sustainable work culture. Understanding and applying ergonomic concepts is vital for any manufacturer looking to modernize their practices and ensure the well-being of their workforce.
Importance of Ergonomics in Workplace Design
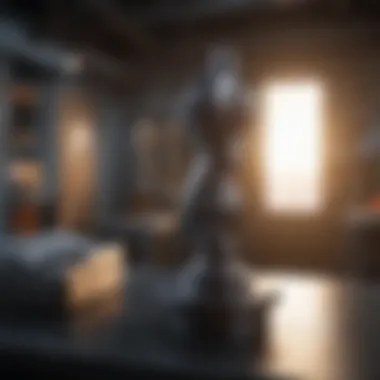
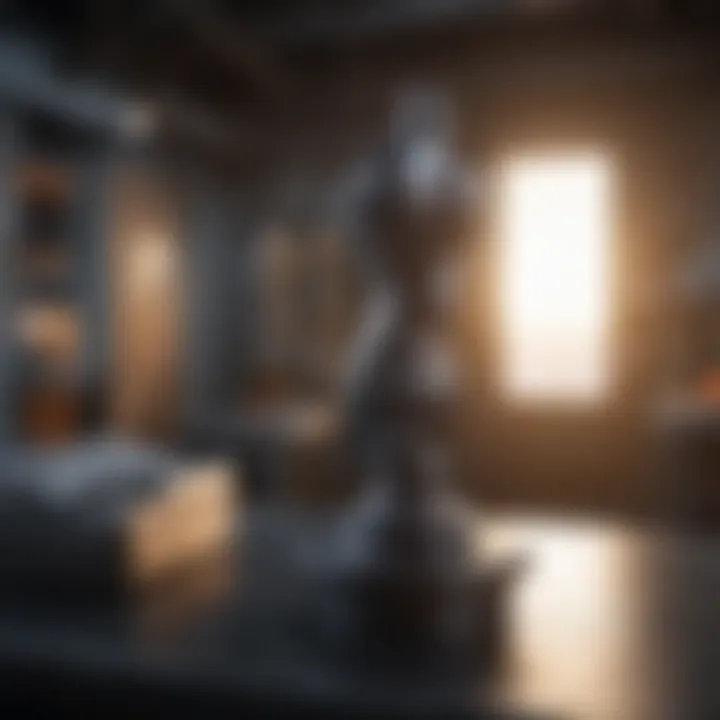
In today's manufacturing landscape, where efficiency and worker welfare are paramount, the importance of ergonomics in workplace design cannot be overstated. Properly integrating ergonomic principles results in an environment that not only promotes health and safety but also enhances productivity. This holistic approach to workplace design acknowledges that optimizing the physical workspace leads to better outcomes for both employees and the organization.
Ergonomics focuses on adapting the workplace to fit the workers rather than forcing the workers to fit the workplace. This customization can alleviate several workplace issues, such as musculoskeletal disorders caused by repetitive tasks. By prioritizing ergonomic design, manufacturers can significantly reduce injury rates and healthcare costs, ensuring a healthier workforce.
Impact on Health and Safety
When ergonomics is integrated thoughtfully into workplace design, the impact on health and safety stands out prominently. For starters, proper ergonomics reduces the risk of injuries. For example, adjustable workstations allow employees to modify their setups to suit their height or task requirements, minimizing strain. This not only cuts down on the time lost to injuries but also saves costs associated with worker compensation claims.
Employees who work in ergonomically sound environments report lower levels of discomfort and fatigue. Moreover, studies show that organizations implementing such designs often see a drop in absenteeism. Healthy workers are productive workers. When fatigue and pain are kept at bay, employees can focus on their tasks, ultimately leading to a more efficient workflow.
Additionally, an emphasis on ergonomics aids in compliance with health and safety regulations. Companies that adhere to ergonomic standards not only safeguard their employees but also avoid potential fines or legal issues. This proactive approach fosters a culture where worker well-being is prioritized, contributing to a positive organizational image.
Enhancing Productivity
Alongside health benefits, the implementation of ergonomic principles in workplace design yields substantial productivity gains. When employees work within a well-structured environment tailored to their needs, their output increases significantly. For instance, intuitive tool placements and equipment designed for ease of use enhance workflow efficiency. Workers do not waste time reaching for items or adjusting their postures awkwardly, which can disrupt their focus.
Also, consider the importance of proper lighting and noise control, which are crucial elements of ergonomic design. Well-lit areas and quiet surroundings can significantly boost concentration levels. Factories that have adopted natural light sources and sound-dampening materials have noted an uptick in employee performance and satisfaction.
Moreover, fostering a culture of ergonomics encourages a feedback loop where employees engage in discussions about best practices and areas needing improvement. This involvement can ignite a sense of ownership and commitment to the workplace, translating into higher productivity.
Bottom Line: Emphasizing ergonomics in workplace design not only supports the health and safety of workers but also acts as a catalyst for increased productivity.
In summary, integrating ergonomic principles into workplace design is more than just a trend; it’s a necessity for modern manufacturing. As organizations perceive the tangible benefits of improved health and enhanced productivity, they pave the way for a sustainable, efficient future.
Key Ergonomic Principles for Manufacturing
In today’s fast-paced manufacturing environments, understanding and applying ergonomic principles is vital. These principles are not just guidelines; they form the backbone of a safer, more efficient workplace that takes into account the capabilities and limitations of human operators. By prioritizing ergonomics, manufacturers can witness a notable enhancement in employee satisfaction and operational productivity.
Designing for Human Capability
The cornerstone of ergonomic design is the understanding of human capability. Every workforce consists of individuals with varying heights, strengths, and cognitive skills. Designing machinery, tools, and workspaces based on a one-size-fits-all approach can lead to inefficiencies. It simply doesn’t jive with reality.
For instance, adjustable workstations are a practical application of this principle. These workstations facilitate workers with different body types by allowing customization to fit individual needs. Such an approach significantly reduces strain and discomfort, leading to fewer errors and injuries.
Moreover, ergonomic tools should not only enhance functionality but also ensure that they align with the natural motions of the body. For example, a hand tool designed to fit the grip of an average-sized hand can reduce fatigue and promote better control during tasks.
Reducing Repetitive Strain
Repetitive strain injuries, known in acronym-laden terms as RSI, are a silent saboteur in manufacturing. They arise from performing the same motions over and over again. Take a moment to consider assembly line workers who perform the same tasks for hours on end. Their bodies, over time, begin to keep a tally of the repetitive stresses.
To combat this, manufacturers should implement job rotation and encourage micro-breaks. Job rotation keeps tasks fresh and gives muscle groups a chance to recover. In addition, certain ergonomic tools, like specialized grips or torque wrenches, can help mitigate the impact of repetitive motions.
“Investing in ergonomic strategies today means investing in a healthier, more resilient workforce tomorrow.”
Implementing Proper Posture
Proper posture is often overlooked, yet it plays a critical role in manufacturing ergonomics. Misaligned postures can lead not only to discomfort but also to long-term structural issues. Workers hunched over their tasks can put significant strain on their backs, necks, and shoulders.
Training employees in proper ergonomic practices can dramatically influence posture habits. Implementing floor markings to guide proper heights for workspaces, or providing chairs that are supportive and adjustable, can aid in maintaining the correct posture. Furthermore, regularly scheduled ergonomic assessments of workstations can aid employers in fine-tuning their setups to match ergonomic best practices.
Ultimately, the cumulative effect of focusing on human capability, reducing repetitive strain, and ensuring proper posture leads to a powerful synergy that enhances overall workplace efficiency and safety. The implications of these ergonomic principles extend far beyond the individual; they contribute to the overall health of the organization and the well-being of its employees.
Ergonomic Tools and Technology
In the modern manufacturing landscape, the role of ergonomic tools and technology cannot be overstated. These tools are more than just gadgets; they are essential elements that foster a healthier workplace. When companies integrate ergonomic tools, they pave the way for a safer work environment, leading ultimately to enhanced productivity and employee satisfaction. The technology that supports ergonomics is designed not only to alleviate physical strain but also to improve efficiency in workflows. A well-thought-out ergonomic approach helps in creating synergies between workers and technology. This leads to optimizing both human capability and machine efficiency.
Adjustable Workstations
Adjustable workstations represent a significant leap in the ergonomic design of workspaces. The flexibility they offer allows workers to customize their environments according to their specific needs. This adaptability is crucial because not everyone has the same physical stature or working style. By adjusting desk height or monitor position, employees can maintain a neutral posture that minimizes stress on the body.
- Benefits of Adjustable Workstations:
- Reduces the risk of musculoskeletal disorders.
- Increases comfort levels of workers.
- Enhances focus and efficiency as ergonomics align with physical comfort.
By investing in height-adjustable desks, manufacturers can witness a noticeable drop in reported fatigue and discomfort levels among workers. So, not only does this foster a healthier workforce, but it also reflects positively on the company’s bottom line in terms of reduced absenteeism and a more motivated team.
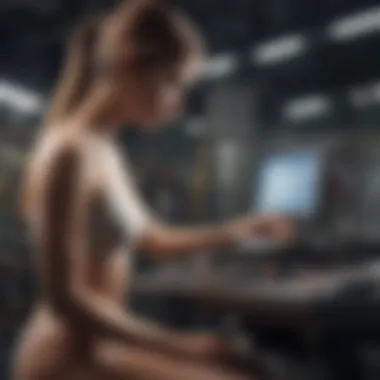
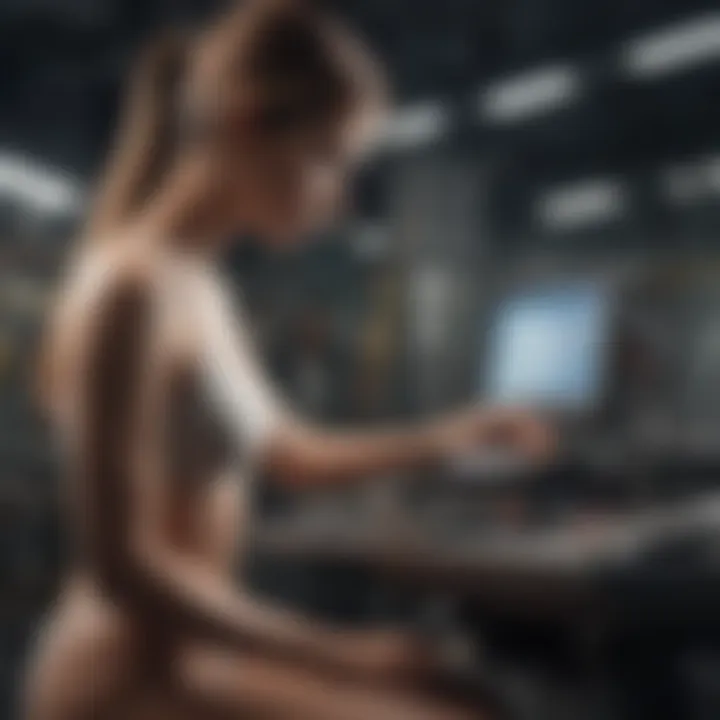
Ergonomic Tools and Equipment
The right tools can make a world of difference in how employees perform their tasks. Ergonomic tools are crafted specifically to fit human use, providing proper support and preventing injury.
- Key Tools to Consider:
- Ergonomic hand tools: Designed to minimize strain and increase control.
- Anti-fatigue mats: Often implemented in standing workstations to reduce leg and back fatigue.
- Task lighting: Improves visibility, allowing workers to maintain proper posture without straining their necks or eyes.
Incorporating these types of equipment can significantly affect employees’ operational abilities. When folks have access to tools that fit their needs, not only do they feel more appreciated, they also execute their jobs better.
Wearable Ergonomics
Wearable technology is the wild card in the ergonomic toolkit. The rise of wearables such as smartwatches or specialized exoskeletons brings a new dimension to workplace ergonomics. These devices monitor body positions or collect data about movements, signaling when a worker might be at risk of injury.
- Advantages of Wearable Technology:
- Real-time feedback helps workers adjust their posture and movements instantly.
- Encouragement of active lifestyles, as wearables can promote movement and breaks.
- Data collection enables management to identify patterns that might indicate areas for improvement in ergonomic practices.
Implementing wearable ergonomics can feel like adding a layer of protection that not only shields workers from injuries but also promotes a culture of health awareness within the organization.
Investing in ergonomic tools and technology is not merely a matter of regulatory compliance; it is an essential practice in enhancing the overall health and productivity of the workforce.
Through the combination of adjustable workstations, ergonomically designed tools, and innovative wearables, manufacturers can create an environment that values the well-being of its workers. And when workers feel valued, they are likely to contribute positively, leading to heightened productivity across the board.
Employee Training and Awareness
Employee training in ergonomic practices is a pivotal aspect of enhancing workplace safety and productivity in manufacturing. Understanding the right techniques and principles can transform the way employees engage with their work environment, making it not only safer but also more efficient. There’s a profound truth in the saying, "An ounce of prevention is worth a pound of cure.” Proper training programs equip workers with the knowledge necessary to avoid injuries, reduce strain, and improve their overall well-being on the job.
Importance of Training Programs
Effective training programs foster an awareness of ergonomic principles among all employees, from leadership down to the ground workers. This lends itself to a three-fold benefit: increased safety, improved productivity, and heightened job satisfaction. When employees can identify potential hazards in their workspace and understand how to maintain good posture and use proper lifting techniques, they mitigate the chances of workplace injuries significantly.
- Preventing Injuries: Statistically, workplaces that prioritize ergonomic training report fewer injuries. Regular training sessions can keep the topic fresh in employees' minds, ensuring that they remain aware of best practices and preventative measures.
- Enhancing Productivity: Workers who know how to operate efficiently in their environment are less likely to suffer fatigue. This can translate into quicker, more effective work processes. Moreover, training often incorporates ways to streamline tasks, meaning employees work smarter, not harder.
- Boosting Morale: Employees appreciate when their well-being is prioritized. Training fosters a supportive environment, showing workers that their health matters, which in turn inspires dedication and loyalty.
Training programs should be regular and adaptable, addressing various roles and changing technologies. Using hands-on demonstrations, engaging materials, and real-life scenarios creates an interactive learning environment that resonates with everyone involved. To ensure effectiveness, feedback should be welcomed, allowing improvements to be made based on participant experiences.
Cultivating an Ergonomic Culture
The significance of a robust ergonomic culture cannot be overstated. Cultivating such an environment involves more than just training—it incorporates a holistic approach that merges policy changes, employee involvement, and continual reassessment of practices.
Developing an ergonomic culture starts with leadership setting strong examples and committing to the principles of ergonomics. When management prioritizes ergonomics, it signals to all levels of the organization the importance of safe work practices. Here’s how to foster this culture:
- Open Lines of Communication: Facilitate discussions about ergonomics and encourage employees to voice concerns. This not only empowers them but also provides valuable insights into potential improvements.
- Team-Driven Initiatives: Involve workers in ergonomic assessments and solution implementations. Bringing employees into the process ensures that the solutions are practical and tailored to their unique challenges.
- Ongoing Education: Make training a continuous effort rather than a one-off session. Regular updates on ergonomic practices can keep the awareness alive and ensure that workers stay informed about new tools or methods.
"Creating an ergonomic culture is about fostering an environment where safety is woven into the fabric of daily operations."
- Recognizing and Rewarding Best Practices: Highlighting employees who demonstrate excellent ergonomic practices can inspire others. Acknowledgment may come in the form of small rewards, shout-outs during meetings, or features in internal publications.
Ultimately, a commitment to nurturing an ergonomic culture leads to a workplace that champions health, safety, and productivity. Workers feel valued and engaged, which is a recipe for success in the long run.
Challenges in Implementing Ergonomic Solutions
Implementing ergonomic solutions can often feel like trying to swim against the tide. While the benefits are clear, a number of challenges can complicate the adoption of ergonomic practices in manufacturing. It is critical to understand these obstacles, as they not only affect worker health but also influence productivity and morale. As we navigate through this section, we will delve into the most common hurdles faced when trying to integrate ergonomic solutions into manufacturing processes and explore strategies for overcoming them.
Financial Constraints
When discussing ergonomic improvements, the elephant in the room frequently is cost. Investing in ergonomic tools or redesigning workspaces often comes with a hefty price tag. You might find that the initial financial outlay for adjustable workstations, ergonomic tools, or specialized chairs can scare away potential buyers even before they take their first step towards improvement.
However, it’s important to remember that these costs should be viewed through a long-term lens. Think of it as planting a seed that eventually grows into a fruitful tree. While the upfront investment might pinch the budget now, the returns can be significant. Studies show that companies can see a reduction in workplace injuries, which translates to lower workers' compensation claims and fewer sick leaves. This means savings down the line that may well outweigh those initial costs.
In addition to direct costs, there are indirect expenses related to the training of employees and implementation of new systems. Decisions made within the financial context can often lead to inadequate implementation of ergonomics. Without proper funding, ergonomic solutions may become half-baked. Companies should also consider that financial limitations often lead them to prioritize short-term savings over long-term investment in employee health.
Resistance to Change
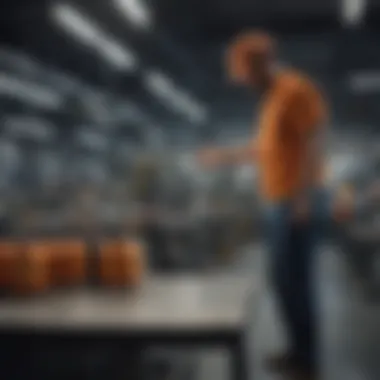
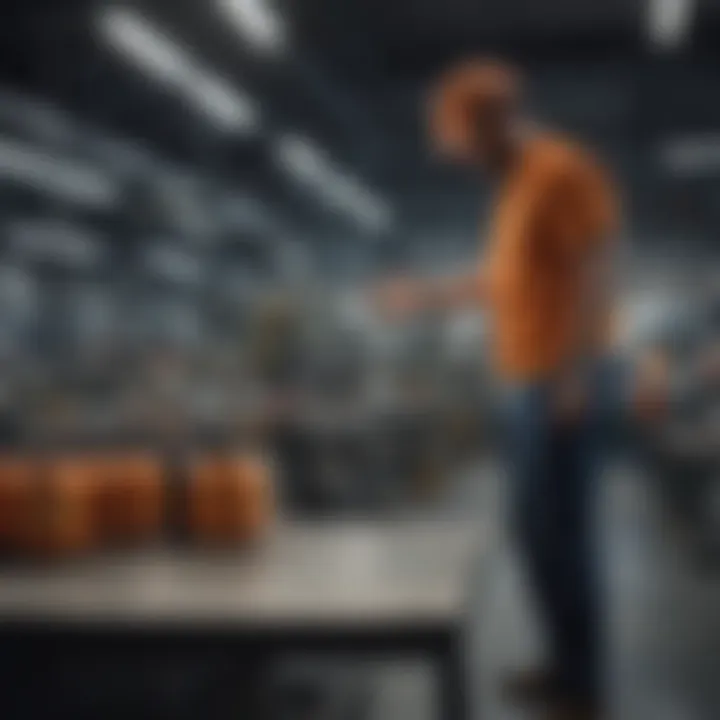
Just as finances can be a stumbling block, so too can the reluctance to change ingrained habits. Humans are creatures of habit, and in many cases, the resistance stems from a simple discomfort with altering established routines. Implementing new ergonomic practices can feel like asking employees to step into uncharted waters, raising discomfort or skepticism about efficacy. Employees might think, "Why change something that has worked for years?"
This mindset can be particularly pronounced in senior employees who have honed their methods over time. They often view new approaches as a challenge to their expertise, leading to passive or active resistance. In some instances, they may not see how these changes benefit them or their work efficacy directly.
To navigate this resistance, it's crucial to focus on communication and education. Making it clear how changes improve both individual comfort and overall productivity can help ease the transition. Providing demonstrations or pilot programs can also assuage fears by showcasing the tangible benefits of ergonomics firsthand. Involving employees in the planning stages can turn skeptics into advocates, creating a sense of ownership over their work environment.
By addressing these challenges head-on—acknowledging the financial investment required and mitigating resistance through education—manufacturers can pave the way for an environment that prioritizes ergonomic solutions.
"Adopting ergonomic principles is less about forced change and more about fostering a culture that values health and productivity."
Case Studies of Ergonomic Success
Exploring successful applications of ergonomic concepts provides profound insights into the tangible benefits these practices can yield in the manufacturing sector. These case studies act as a beacon for both employers and employees, illuminating how effective ergonomic design can substantially enhance workplace safety, efficiency, and overall satisfaction. Let’s delve into some exemplars.
Sector-Specific Applications
Different sectors face unique challenges and conditions that shape their ergonomic strategies. For instance:
- Automotive Industry: In an automotive assembly plant, the introduction of adjustable height workstations led to a dramatic reduction in musculoskeletal disorders. Workers could customize their workstations to suit their heights and tasks, allowing more natural postures during assembly. This simple adjustment not only improved their comfort but also reduced the time lost to injuries.
- Electronics Manufacturing: Here, a global company implemented anti-static mats and ergonomically designed tools for workers handling sensitive components. By fine-tuning the work environment, they not only minimized potential defects due to mishandling but also engaged workers’ physical well-being. After these changes, employee feedback showed a 40% improvement in job satisfaction.
- Food Processing: In this sector, ergonomic intervention included redesigning packaging lines to eliminate excessive reaching and twisting. Results reported a steep drop in worker fatigue and an observed increase in output. The workers mentioned feeling less exhausted, which led to fewer mistakes and higher morale on the floor.
These examples illustrate that when companies tailor ergonomic solutions to their environment and workforce, they unlock doors to improved health and productivity.
Quantitative Benefits Observed
Measuring success quantitatively reinforces the benefits of ergonomics in manufacturing. Various studies have collated data demonstrating the financial and operational impact of ergonomic interventions. A few notable observations are highlighted below:
- Increased Productivity: A clothing manufacturer documented a 25% increase in output after implementing ergonomic tools and redesigning workflows. They acknowledged that not only did injury rates decrease, but workers were also able to operate more efficiently with less fatigue.
- Reduction in Injury-Related Costs: A case study from a shipping company found that investing in ergonomic training and equipment led to a 50% decrease in workers’ compensation claims related to strains and sprains over five years. The cost savings were substantial, with funds redirected back into workforce development and new technologies.
- Enhanced Employee Retention: By improving workplace ergonomics, a metal fabrication company saw a notable increase in employee retention rates—up to 30% over several cycles. The ability to maintain a healthier workforce resulted in fewer recruitment and training expenses, showcasing a compelling long-term financial advantage.
These quantitative benefits underscore how ergonomic practices, often viewed as ancillary, become central investments in a company's operational efficiency.
"An investment in ergonomics is an investment in the well-being of your workforce, and ultimately, in your company’s future." - Anonymous
Future Trends in Ergonomics for Manufacturing
As we look ahead, the landscape of manufacturing is shifting dramatically, largely influenced by advancements in technology and changing workplace dynamics. Embracing ergonomic principles will become even more crucial as companies strive to remain competitive. The integration of futuristic technologies can alleviate the common physical stresses faced by workers, greatly improving job satisfaction and efficiency. Moreover, a focus on sustainability ensures that these innovations do not come at the expense of our environment. Understanding these trends offers insights that can lead to practical applications in everyday work environments.
Integration of AI and Robotics
Artificial Intelligence and robotics are making waves in manufacturing, not just in terms of production but also with respect to employee ergonomics. The fusion of these technologies can lead to significant ergonomic enhancements. For instance, robots can take over the most physically demanding tasks, reducing the risk of worker injury. Beyond that, AI can be employed to analyze workplace ergonomics data, identifying patterns that may not be apparent to human observers.
For instance, wearable technologies equipped with AI can track workers’ movements. This information can pinpoint repetitive stress actions or poor posturing throughout the day. When data is collected, it can be used to design interventions that enhance work practices and ergonomics, fostering a safer working environment. With so much real-time data, companies can adapt workflows dynamically, ensuring that ergonomic practices evolve alongside manufacturing processes.
Sustainable Ergonomic Solutions
The conversation around sustainability extends into ergonomics. There are increasing efforts to develop ergonomic solutions that align with environmentally friendly practices. Such solutions include designing tools and equipment that are both ergonomic and made from sustainable materials. For example, companies are exploring recycled plastics and sustainable wood sources for hand tools, which not only support the ecosystem but can also significantly reduce the weight of tools—resulting in less strain on workers.
Furthermore, applying sustainable strategies in workspace design is essential. This includes considering the lifespan of materials, energy-efficient lighting, and a layout that promotes natural movement, which helps to minimize physical strain.
In addition, embracing renewable energy sources in manufacturing operations can have positive effects on worker morale. A production facility powered by solar or wind energy becomes a point of pride for employees, leading to increased job satisfaction and, ultimately, better productivity.
"Ergonomics is not just about comfort; it’s about creating a system that benefits both the employee and the employer, especially when innovation meets sustainability."
Finale
In wrapping up our exploration of ergonomics in manufacturing, it's clear that this topic is not just a footnote in worker safety discussions but a pivotal element that can elevate a company's overall performance. Emphasizing ergonomics means valuing the workers who contribute to the daily operations. When organizations focus on creating ergonomically sound practices, they see tangible improvements—not just in the safety of their employees but also in the efficiency of operations.
Summary of Benefits
The benefits of implementing ergonomic principles in manufacturing are manifold and cannot be overstated:
- Health Enhancements: Reducing musculoskeletal injuries by optimizing the workplace layout and minimizing repetitive tasks fosters better health for employees.
- Increased Productivity: Workers are more engaged and effective when they have a comfortable work environment. Studies demonstrate that even slight adjustments to workstations can lead to significant gains in output.
- Job Satisfaction: A workplace that takes ergonomics seriously can improve morale. When employees feel cared for, they're likely to be more committed to their roles.
- Financial Savings: Lower rates of injury lead to decreased medical expenses and reduced operational downtime—keeping both workers and management happy.
In essence, the conversation around ergonomic practices in a manufacturing setting highlights a crucial intersection of human welfare and business acumen. As companies invest in ergonomics, they gain a competitive edge that is hard to ignore.
Call to Action for Manufacturers
Manufacturers are encouraged to take a proactive stance toward ergonomic integration in their environments. Here are several strategies to consider:
- Conduct Ergonomic Assessments: Take a close look at your current setup. What aspects can be improved? Evaluate how your workstations align with ergonomic principles.
- Invest in Training: Regular training sessions for staff on the importance of ergonomics can cultivate an ergonomically aware culture. This helps workers to think critically about their own setups and movements throughout their shifts.
- Engage Workers in Solutions: Don’t dictate changes from the top down. Engage employees when developing ergonomic enhancements. Their experiences can provide invaluable insights that lead to practical and effective solutions.
- Regularly Review and Update Practices: Ergonomics is not a one-and-done deal. Regular reviews ensure that practices remain aligned with both technological advances and changing employee needs.
In summary, adopting ergonomic concepts isn’t merely a trend—it’s a smart, sustainable initiative that pays dividends in many forms. For manufacturers, the time to act is now. It’s about building a framework where safety, productivity, and worker well-being come together for a brighter future.