In-Depth Exploration of Hammer Mill Screens
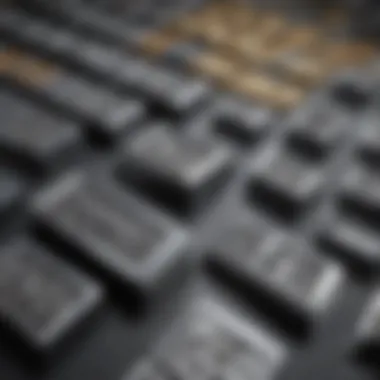
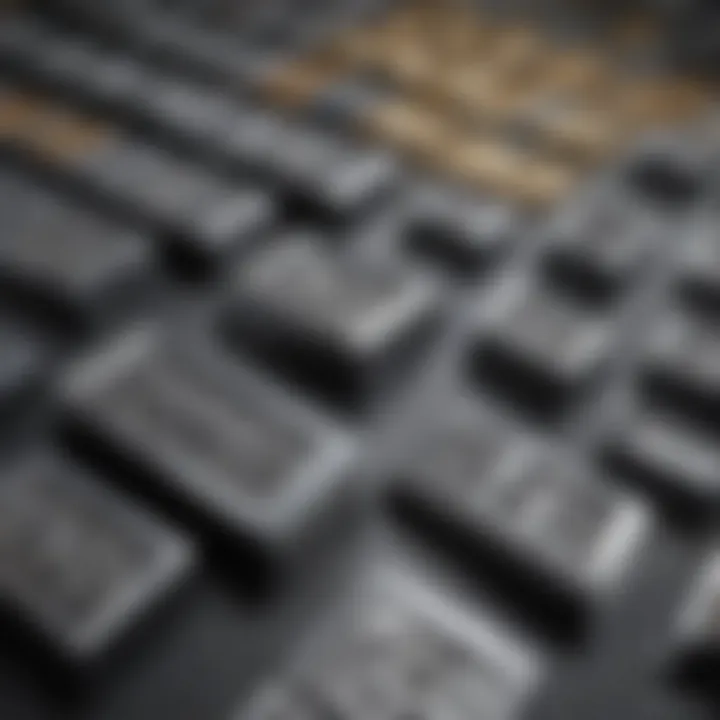
Intro
In the world of agriculture and industry, hammer mills stand as pivotal machinery for material processing. These machines, rather than showcasing just their mechanical prowess, rely heavily on a component often overlooked: the hammer mill screens. The screens dictate the quality, efficiency, and fineness of the processed material. Without them, the entire operation of the hammer mill would be akin to a ship without a sail, drifting aimlessly.
This article aims to bring a spotlight to the importance of hammer mill screens. By dissecting their function, identifying various types, and discussing optimization techniques, we hope to equip students, researchers, and industry professionals with the tools they need for a more profound understanding of this critical aspect of hammer mills.
Through an exploration of key terminology, a thorough analysis of findings, and potential areas for future research, we will connect the dots between theory and practical application, making this a comprehensive resource for anyone looking to enhance their knowledge or operational capacity regarding hammer mill screens.
Key Concepts and Terminology
Definition of Key Terms
- Hammer Mill: A type of mill used to pulverize materials, where hammers strike the material to break it down into smaller particles.
- Screens: Mesh-like structures that control the size of the output particles, determining the final material's quality and texture.
- Optimization: The process of making a system as effective as possible.
Concepts Explored in the Article
This piece will delve into varied themes surrounding hammer mill screens, covering:
- The working principle of hammer mill screens and their role in the milling process.
- Types of screens available in the market, discussing their respective advantages and applications.
- Factors influencing screen selection, including material properties and desired particle size.
- Maintenance practices for screens to enhance longevity and performance.
- Different optimization techniques that can be employed to improve efficiency.
"The right hammer mill screen not only improves the quality of the product but also impacts operational efficiency—making it a vital choice for any milling process."
Findings and Discussion
Main Findings
Through our investigations, we discovered that hammer mill screens significantly impact the particle size of processed materials. For instance, screens with smaller openings yield finer particles, which can be crucial for specific applications such as animal feed production or pharmaceuticals. Additionally, various materials used for screens, such as stainless steel or perforated sheets, contribute various benefits such as corrosion resistance and durability.
Another striking finding involves the maintenance of the screens. Regular cleaning and inspection can prevent potential downtimes and enhance overall efficiency. The cost of neglecting screen maintenance could lead to larger operational disruptions—something operators cannot afford.
Potential Areas for Future Research
As trends in agriculture and industrial practices evolve, there is plenty of room for further investigation. For instance, exploring new materials for screens that enhance their performance or studying the environmental impacts of utilizing different screen configurations can be insightful. Additionally, developing smart technologies to monitor screen wear in real time could revolutionize how we approach maintenance in milling processes.
Foreword to Hammer Mill Screens
In the realm of manufacturing and processing industries, hammer mill screens hold an indispensable role. Understanding their functionality and significance can enhance operational efficiency remarkably. They function as the gatekeepers of particle size reduction and product quality, directly influencing the end results in agricultural and industrial settings. Without these screens, processes could falter, leading not only to subpar products but also increased waste and operational costs. Thus, delving into the intricacies of hammer mill screens offers insights into optimizing production and maintaining quality standards vital for businesses.
Definition and Purpose
Hammer mill screens are crucial components that determine how materials are processed within a hammer mill. Essentially, these screens are perforated barriers that allow particles to pass through while retaining larger, unprocessed materials. Their primary purpose is to control the size and consistency of the final product, ensuring it meets specific requirements for various applications, from animal feed to biofuel.
The ultimate goal of a hammer mill screen is not merely to allow material to pass but to produce a product that has the desired characteristics, ensuring efficiency throughout the grinding process. The size of the holes in these screens can significantly affect throughput, energy consumption, and ultimately the quality of the end product. Therefore, selecting the appropriate screen for a given operation is paramount.
Historical Development
The evolution of hammer mill screens is closely tied to advancements in milling technology. Originally, early milling methods were rudimentary at best, relying on basic mechanical grinding. As agriculture and industry began to burgeon, there was a pressing need for more efficient milling solutions. The transition to the use of hammer mills in the early 20th century marked a significant turning point.
In the late 1930s and 1940s, the introduction of organized farming practices led to a greater demand for feed processing, which, in turn, propelled the refinement of hammer mill designs. Screens became more standardized with specific dimensions becoming common as industry practices matured. Materials used in screen manufacturing also advanced, with the transition from wood to metal enhancing durability and effectiveness. Rapid innovation continued throughout the latter half of the 20th century, leading to a multitude of screen types designed to meet evolving industry needs.
A solid understanding of hammer mill screens can trace their significance back decades, illustrating how modern practices build upon historical advancements to enhance productivity and efficiency in various sectors.
Mechanics of Hammer Mills
Understanding the mechanics of hammer mills is like getting a peek under the hood of a finely tuned machine. The way these machines operate is critical not just for functionality but also for the efficiency of their performance. Hammer mills are often the backbone of various processing industries, handling materials ranging from grains in agriculture to plastics in recycling. When we dissect the mechanics, we see how they contribute to the effectiveness of hammer mill screens, which are pivotal in determining the output quality and overall production rate.
The basic operation revolves around transforming large feed material into smaller particles. Recognizing how these processes work can help operators refine their practices and improve overall outcomes.
Basic Working Principles
In a nutshell, hammer mills utilize high-speed rotating blades to shred material into smaller pieces. The principle is straightforward yet efficient. When raw material enters the chamber, it encounters rapidly spinning hammers which deliver rigorous force. This force reduces the size of the material as it hits surfaces and screens strategically placed inside the machine.
The key stages in this process include:
- Feeding: Material is fed into the mill, often through a gravity-fed hopper.
- Size Reduction: Rounded hammers strike the material, breaking it down. The type of hammer mill screen determines the size of the output particles.
- Separation: Once the material reaches the desired fineness, it exits through the screen while larger pieces are retained for further milling.
"The design and layout of the hammer mill directly influences the efficiency of the operation, leading to higher quality output."
Components Overview
A hammer mill is more complex than it appears at first glance. Understanding its components can clarify why certain setups yield better results. Here are the critical components that come into play:
- Hammers: The moving parts that strike the material, they can vary in shape and size depending on the specific milling needs.
- Screens: Made up of various materials and hole sizes, screens are essential for controlling the resultant particle size.
- Chamber: This is where the magic happens. The design affects airflow and particle movement, which influences the milling efficiency.
- Motor: Drives the hammers and can vary in size depending on the expected load.
- Feed Hopper: Regulates the amount of material entering the mill, ensuring a steady flow that supports consistent operation.
To sum it up, knowing how hammer mills work and their components lays the foundation for understanding their role in larger industrial processes. This also connects to the importance of selecting the right hammer mill screen, as it plays a vital role in the milling process and overall efficiency.
Functionality of Hammer Mill Screens
Hammer mill screens play a crucial role in various industrial and agricultural processes. Their primary purpose is to facilitate the size reduction of materials, ensuring that the end products meet specific particle size requirements. An understanding of the functionality of these screens can illuminate how they affect overall milling performance, energy efficiency, and product quality. The effectiveness of a hammer mill is largely dependent on the design and condition of its screens, making it vital for users to appreciate their contribution to the operations.
Size Reduction Mechanism
The size reduction mechanism in a hammer mill relies significantly on the interaction between the hammers and the screens. When material enters the mill, it is impacted by high-speed rotating hammers, which exert shear and impact forces. This process generates particulate sizes by breaking down larger pieces into smaller ones. The screens act as a filter; they ensure that only materials of the desired size pass through.
- Different screen hole sizes allow for varied particle distributions. If the screens have larger holes, larger particles can escape, while smaller holes restrict exit and create finer particles.
- The configuration of the hammer mill itself can also impact the effectiveness of the size reduction. For instance, when screens become clogged, it can hinder the flow of material, leading to inefficient milling and energy wastage.
Moreover, the arrangement of the screens relative to the hammers is pivotal. When properly positioned, they allow for a more efficient reduction process, where materials continually circulate through the mill until reaching the desired size before exiting.
"The efficiency of size reduction can dramatically shift based on hammer mill screen configuration and maintenance. Ignoring this aspect can lead to operational inefficiencies."
Role in Product Quality
Another element that underscores the functionality of hammer mill screens is their impact on product quality. The final characteristics of the milled product are closely tied to the choices made concerning screen type and maintenance practices. Here are a few noteworthy points on how screens influence quality:
- Homogeneity of Particle Size: Efficient milling leads to a more uniform particle size, which is often essential for applications in feed manufacturing and pharmaceuticals. Uneven particle sizes can cause issues in subsequent processes, like mixing or conditioning.
- Nutritional Value Retention: In agricultural settings, the size of particles can affect the digestibility of feeds. Proper screen selection ensures that essential nutrients are retained while undesirable components are reduced.
- Final Product Appearance: For products designed for market sale, having the right particle size and shape can impact consumer perception. A well-milled product is often considered higher quality, leading to better market performance.
- Reduced Dust: A well-functioning Hammer Mill with appropriate screens can minimize excessive dust creation, which is not only a quality issue but can also pose safety and health risks in a production environment.
In summary, the screens in a hammer mill are instrumental not only for size reduction but to maintain and enhance the quality of the final product. Understanding how different screens work and their maintenance lays the foundation for optimizing performance.
Types of Hammer Mill Screens
Understanding the various types of hammer mill screens is crucial for anyone involved in the agricultural and industrial processes. Each screen type serves a distinct purpose, influencing particle size, processing efficiency, and product quality. Selecting the right screen can significantly impact the performance of a hammer mill and ultimately determine the success of production operations. By familiarizing oneself with these options, users can make informed decisions to optimize their applications.
Perforated Screens
Perforated screens are one of the most common types of hammer mill screens. These screens feature a series of holes of uniform size, typically crafted from durable materials like metal. The principal advantage of perforated screens lies in their versatility; they can be designed with various hole diameters to correspond with specific processing needs. This adaptability ensures that businesses have greater control over the particle size distribution of their final product.
When setting up a production line, it's essential to consider the material being processed. For instance, processing grain or similar materials may necessitate larger holes to allow for efficient flow and reduce the risk of clogging. Conversely, for fine powders, smaller holes will yield better results. As a general practice, users must evaluate not only the size but also the arrangement of these holes to maximize throughput while maintaining quality.
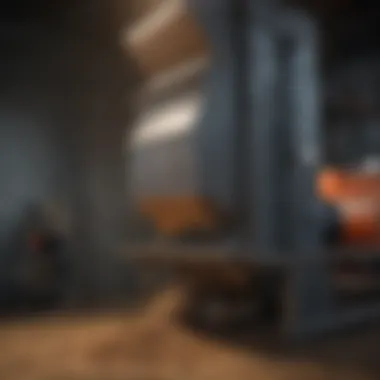
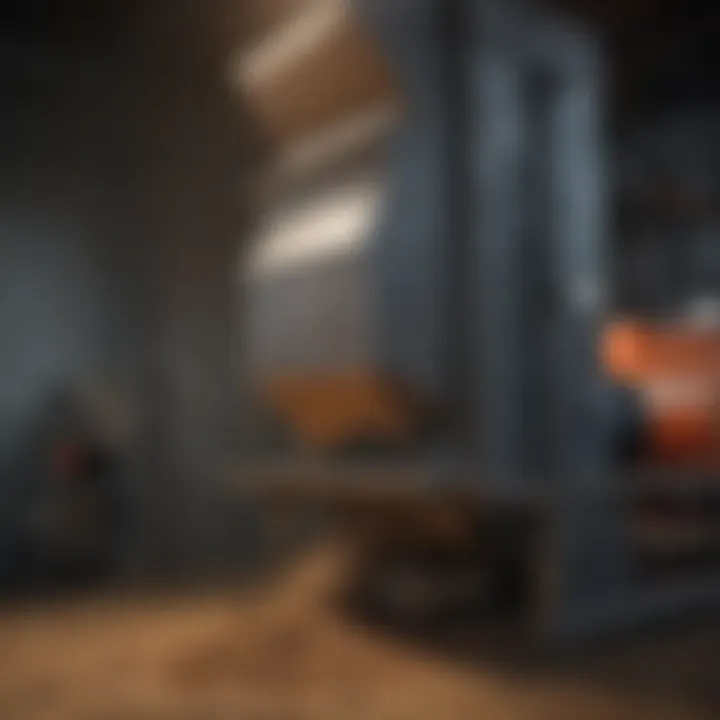
"Properly selected perforated screens can mean the difference between smooth operation and frequent downtime."
Wire Mesh Screens
Another important type is the wire mesh screen. Unlike perforated versions, wire mesh screens consist of intertwined wires forming a mesh of variable openness. These screens are particularly effective for finer materials, allowing them to retain smaller particle sizes while ensuring that larger particles are efficiently cycled back into the grinding process.
In many applications, wire mesh screens can be advantageous due to their lightweight nature and ease of cleaning. However, they might wear out quicker than their perforated counterparts, so maintaining an inventory of replacements or monitoring their use can be practical steps to adopt. As they often possess a more intricate design, some operators may find that a careful balance between mesh size and material flow rate is crucial for optimal functioning.
Bar Screens
Bar screens stand apart from the other two types mainly due to their construction and intended use. Composed of parallel bars spaced at fixed distances, these screens are beneficial for applications requiring significant material retention, such as in the processing of fibrous materials or those that tend to compact easily. The gaps between bars can be adjusted depending on the specific requirements of the process.
Though they have a more specialized application, bar screens can be instrumental in preventing over-grinding and ensuring that only the desired particle sizes reach the final product stage. Operators must remain vigilant to avoid clogs, especially with materials that have a tendency to wrap around the bars. This type of screen is often less accessible than others, which may pose challenges during routine inspections or cleanings.
In summary, the diversity of hammer mill screens—from perforated to wire mesh and bar screens—provides myriad options to match the distinct processing requirements of various materials. Each type presents unique benefits and considerations, making it essential for operators to thoroughly assess their needs before selecting the appropriate screen.
Factors Influencing Hammer Mill Screen Selection
Choosing the right hammer mill screen is no small feat; it’s akin to picking the best tool for a job. If you’ve ever tried to bake without the proper measuring cups, you know how essential the right choices are. Hammer mill screens play a vital role in determining the efficiency of milling processes across various industries. A proper understanding of the key factors influencing this selection can lead to improved product quality, optimized operation, and enhanced overall performance.
Material Characteristics
The very first thing one must consider when selecting a hammer mill screen is the characteristics of the material to be processed. Not all materials are created equal; some are tough as nails, while others are as soft as butter.
- Hardness: Harder materials often require stronger screens to withstand wear and tear. For instance, grinding grains is different from processing minerals.
- Moisture Content: High moisture content can lead to clogging, which paradoxically calls for finer screens or perhaps a redesign in the mill setup itself.
- Bulk Density: Material density influences how screens should be designed. A dense material may require a screen with a larger surface area to facilitate better throughput.
Understanding these characteristics is key to not only selecting the right screens but also maximizing operational effectiveness. For many in agriculture or feed manufacturing, tailoring the hammer mill screens to the specific materials being processed can mean the difference between success and operational hiccups.
Desired Particle Size Distribution
Next on the list is the desired particle size distribution. Imagine digging for gold but only collecting pebbles instead; it's frustrating, right? Similarly, achieving the right particle size is crucial for meeting product specifications.
- Coarse versus Fine Grinding: If your end goal is to achieve a coarse product, selecting a screen with larger holes is appropriate. Conversely, for fine particle sizes, perforated screens with smaller holes should be employed.
- Uniform Distribution: In industries where consistent particle size is required, such as pharmaceuticals or specialized food products, meticulous selection is non-negotiable. This might also involve post-processing steps to refine the particle size further.
- Testing and Adjustments: Regular testing of particle size can help dial in the optimal holes on screens. Adjustments based on empirical data are often the most reliable approach.
Production Capacity Needs
Finally, keeping a keen eye on production capacity needs adds another layer of complexity to screen selection. This essence isn’t just about choosing a quick-fix solution; it’s about planning for efficiency in the long haul.
- Throughput Requirements: How much output do you expect from your hammer mill setup? Screens that can handle higher loads without excessive wear lead to reduced downtime.
- Operational Costs: Screens also play a role in energy consumption. Poor choices can mean everything from increased electricity costs to more frequent replacements.
- Scalability: As businesses grow, their requirements change. Selecting a screen that can adapt to scaling needs makes the ongoing operation smoother and less costly.
In summary, the right selection of hammer mill screens hinges on understanding material characteristics, desired particle size distributions, and production capacity. A comprehensive examination of these elements leads to not only improved efficiency but also product consistency—both of which are essential in today's fast-paced industrial world.
Performance Metrics of Hammer Mill Screens
Understanding the performance metrics of hammer mill screens is vital for evaluating the efficiency of milling processes in both agricultural and industrial settings. Performance metrics provide operators and manufacturers alike with a framework for assessing how well screens are functioning. The effectiveness of these screens not only impacts productivity but also influences the quality of the final output. As such, adequate attention must be given to specific elements that contribute to performance such as throughput efficiency and energy consumption.
Throughput Efficiency
Throughput efficiency is a measure of how much material a hammer mill can process in a given amount of time. It essentially indicates the effectiveness of the mill’s design and screening choices in achieving the desired size reduction. A higher throughput efficiency signifies that the mill is capable of handling more raw materials, which can lead to reduced operational costs and increased profitability.
Several factors influence throughput efficiency:
- Screen hole design: Larger or differently shaped holes can either facilitate or hinder the material’s passage.
- Hammer speed: Increased speed generally leads to better reduction and higher throughput, but it can also elevate wear rates.
- Material characteristics: Dense or abrasive materials can slow down the milling process, affecting overall efficiency.
Maximizing throughput efficiency often involves fine-tuning such variables. Operators should also regularly monitor performance metrics, which can provide insights into overall machine effectiveness and help pinpoint necessary adjustments.
Energy Consumption Analysis
Energy consumption analysis is another critical aspect of assessing hammer mill screens. With energy costs rising, scrutinizing how much energy the milling process consumes has become increasingly important for businesses striving for sustainability and profitability.
Energy consumption can be impacted by:
- Design of screens: Different screen materials or configurations can result in varying energy requirements.
- Operational settings: Running mills at inefficient speeds or not maintaining equipment can lead to excessive energy usage.
- Material characteristics: The type and moisture content of the raw materials can dictate how much energy is consumed during processing.
To ensure optimal energy utilization, it is essential to balance the milling efficiency and energy consumption. A mill that uses lower energy without sacrificing throughput will not only save on operational costs but also reduce environmental impact. Therefore, it's beneficial to employ energy monitoring systems that provide data to guide operational adjustments.
"Optimizing these performance metrics gives a roadmap to achieving not just economic benefits but also environmental sustainability."
Maintenance Practices for Hammer Mill Screens
Maintaining hammer mill screens is essential for their optimal functionality. Just as a car needs regular tune-ups to run smoothly, hammer mill screens require consistent care to perform at their best. Proper maintenance ensures not just longevity but also enhances performance and efficiency. Here, we’ll delve into the critical aspects of maintenance practices, focusing particularly on regular inspections, effective cleaning methods, and guidelines for replacements.
Regular Inspection Protocols
Inspections play a pivotal role in the maintenance routine of hammer mill screens. Regular checks can help spot potential issues before they escalate into costly repairs or inefficiencies. So, what should these inspection protocols look like?
- Frequency: Setting a clear inspection schedule is the first step. A good rule of thumb is to inspect screens every 200 hours of operation and after any significant screen change or adjustment.
- Visual Checks: Inspect for physical damage, such as cracks or signs of wear, especially at edges and mounting points. The need of the hour is to catch these issues early on.
- Alignment and Fit: Ensure that screens are aligned properly and fit snugly within the mill. Misalignment can lead to ineffective grinding and excess strain on other components.
- Documentation: Keep a log of inspections as this helps track wear over time and identifies patterns that may point to underlying problems.
Following these protocols not only helps ensure the screens are functioning well but can also minimize downtime, a crucial factor in any production environment.
Cleaning Methods
Keeping hammer mill screens clean is as important as inspecting them. Dust, residues, and buildup from the processed material can severely hinder performance. Here are some effective cleaning methods:
- Blow-off Air: Use compressed air to blow off loose particles, which is often the quickest method. Just ensure safety precautions are taken to avoid inhaling dust.
- Agitated Scrubbing: For tougher residues, agitated scrubbing with a soft brush can be beneficial. This method should be done carefully to avoid damaging the screen surface.
- Chemical Cleaners: Sometimes, chemical solutions may be needed to dissolve stubborn buildups, especially if processing oily or sticky materials. Make certain that these cleaners are compatible with the screen materials to avoid deterioration.
Ultimately, a regular and thorough cleaning regimen can lead to increased efficiency and product quality, not to mention prolonging the life of the screens.
Replacement Guidance
Even with diligent maintenance, screens will eventually wear out. Recognizing the right time to replace them is critical.
- Signs of Wear: Keep an eye out for uneven wear patterns, increased particle size distribution, or noticeable cracks. These are clear indicators that replacement is around the corner.
- Life Span: Depending on usage and material processed, screens may need replacement every 6 months to a year. It’s often best to stick to manufacturer recommendations.
- Choosing New Screens: When choosing replacement screens, consider matching the specifications of the original to maintain process standards. Materials and hole size should closely align with what has been effective previously.
By adopting these maintenance practices, one can ensure the hammer mill screens not only last longer but also contribute to smoother operations and improved product quality. Focusing on maintenance might seem like a chore, but it’s truly an investment in operational efficiency that pays dividends over time.
"Sloppy maintenance today can lead to big headaches tomorrow."
Optimization Techniques for Hammer Mill Screens
Optimization techniques for hammer mill screens are not just a trivial pursuit; they encompass a vital set of practices that can significantly enhance operational efficiency and product quality. The right optimization methods can dictate the efficiency of size reduction and ensure consistency in the output. It’s essential to grasp the various techniques available and how they directly impact the performance of hammer mill screens.
Adjusting Screen Hole Sizes
The size of the holes in hammer mill screens determines the particle size of the final product. Adjusting these hole sizes is one of the most straightforward yet effective optimization techniques available. For instance, expanding the diameter of the holes could quicken the throughput, allowing larger particles to escape and reducing the workload on the mill. This might be beneficial when processing coarse materials. However, while larger holes may enhance throughput, they could also compromise the uniformity of particle size.
Conversely, smaller holes result in finer outputs, catering to sectors that demand high precision, such as the pharmaceutical industry. Here are some key considerations:
- Material Characteristics: Different materials require different hole sizes for effective processing. Hard materials may need finer holes to minimize wear and tear on the screens.
- Desired Particle Size Distribution: Choose hole sizes according to the targeted output. Sometimes, achieving a specific size class is more important than mere speed.
- Screen Durability: Frequent adjustments to hole sizes might result in increased wear and eventual failure of the screen. Therefore, understanding the material flow and wear rates is crucial.
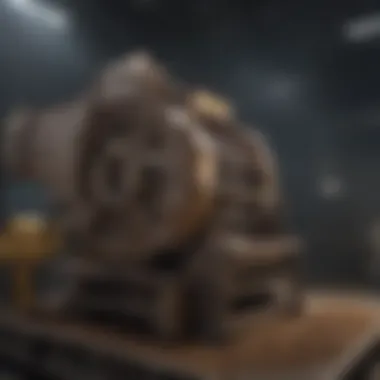
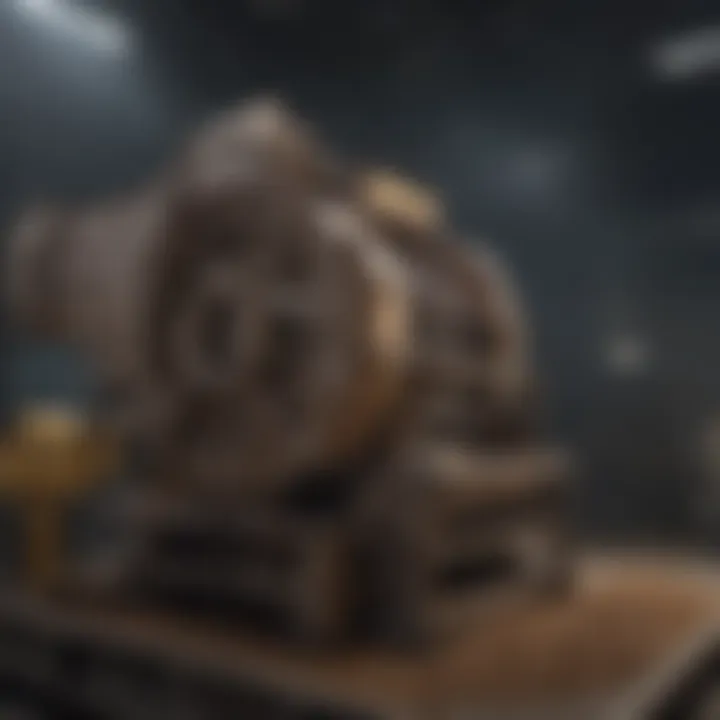
Ultimately, it’s a balancing act: fine-tuning screen holes is a tailored solution to meet specific processing demands without causing unwanted inefficiencies in the operation.
Utilizing Variable Speed Technology
In today’s fast-paced industrial environments, the adoption of variable speed technology is becoming increasingly prominent. This optimization technique allows for real-time adjustments to the hammer mill’s operational speed, providing users with the flexibility to adapt to varying material types and production needs.
Adopting variable speed technology can have multiple benefits:
- Enhanced Control: Operators can adjust the speed based on the material fed into the mill, optimizing the size reduction process. For example, when dealing with wet materials, reducing the speed may prevent clogging, while dry materials may handle higher speed more effectively.
- Energy Efficiency: By tailoring the speed to actual requirements, it reduces energy consumption, which can have a significant impact on operational costs over time.
- Improved Product Quality: Variable speeds can also lead to a more consistent particle size due to reduced variability in the size reduction process.
"Efficiency isn’t just about speed; it's also about precision and adaptability in processing."
To gain the full benefits of this technology, it’s prudent to also invest in suitable control systems that allow easy adjustments and real-time monitoring. This ensures that operators can readily respond to changes in material characteristics without unnecessary downtime or loss of quality.
In summary, both optimizing screen hole sizes and harnessing variable speed technology can lead to significant advancements in the performance of hammer mill screens. These optimization techniques are not mere options; they are necessities for anyone looking to derive maximum benefit from their milling operations.
Applications of Hammer Mill Screens
In the ever-evolving landscape of agriculture and industrial processing, the application of hammer mill screens emerges as a linchpin for efficiency and productivity. These screens are not merely functional components; they dictate how materials are processed, influencing not only the final product's quality but also the operational efficacy of the machinery itself. Understanding their applications is vital for anyone involved in these sectors, as it allows for enhanced performance and optimization in various processes.
Agricultural Sector
The role of hammer mill screens in the agricultural sector is paramount. These screens are integral in the milling of grains, as they help to achieve the desired particle size for animal feed or flour. In essence, they serve as the first line of quality control, allowing only particles of suitable size to pass through while retaining larger and undesired sizes.
- Quality Assurance: The ability to control particle size directly impacts the nutritional value of feed and the efficiency of grain processing. Finer particles tend to enhance digestibility, thus benefiting livestock productivity.
- Versatility: Hammer mill screens are adaptable. Various hole diameters can be employed for different applications—yielding products ranging from coarse grits for poultry to fine powders for specialized feeds.
- Cost-Effectiveness: By optimizing particle sizes, producers can reduce waste and improve feed conversion ratios, ultimately leading to better economic outcomes.
Feed Manufacturing
In feed manufacturing, the efficiency of hammer mills is often dictated by the design and condition of the screens used. These screens not only affect the throughput but also directly influence the operational costs. Efficient screens maximize throughput while minimizing power consumption, leading to significant savings.
- Screen Durability: Selecting robust screens can fend off wear and tear, which is crucial in a high-demand environment like feed production. The materials used in the screens can affect their lifespan greatly.
- Production Flexibility: Manufacturers can produce a wide range of feed products with different formulations. By adjusting screen types and sizes, they can tailor feed mixtures to meet specific animal dietary needs.
- Continuous Processing: The screens allow for consistent material flow, facilitating streamlined operations. This results in less downtime and more efficient processing.
Industrial Processing
In the industrial sector, hammer mill screens facilitate the milling of various materials, from wood to plastics. The application here is broader, catering to diverse industries such as recycling, construction, and food processing.
- Material Specificity: Different materials require tailored screens. For instance, processing wood may require screens that can handle fibrous consistency while metal processes need more durable, robust designs to withstand abrasive wear.
- Reduced Energy Consumption: By optimizing the type and size of the screen, companies can reduce energy consumption in their operations. This is crucial in a time when energy efficiency is paramount.
- Environmental Compliance: Effective size reduction not only ensures quality but also helps industries comply with environmental regulations by minimizing emissions associated with particulate matter.
“The right hammer mill screen can transform not only the end product but also the overall efficiency of your processing line.”
Challenges in Hammer Mill Screen Usage
In the ever-evolving landscape of agricultural and industrial processes, understanding the obstacles that accompany hammer mill screens is crucial. These challenges not only affect operational efficiency but also have implications on product quality and cost. When one concurs with the notion that knowledge is power, it's clear that being equipped with insights into these challenges can bolster productivity and decision-making.
Screen Wear and Tear
One of the most pressing issues with hammer mill screens is screen wear and tear. This phenomenon is an inevitable outcome of the constant interaction with materials during grinding. Over time, the holes in perforated or mesh screens can expand or become deformed, which leads to less efficient particle size reduction and can compromise product uniformity.
The factors that exacerbate wear and tear include:
- Material Composition: Harder materials will often lead to faster screen degradation.
- Moisture Content: Wet materials can lead to increased friction and, consequently, more wear.
- Operating Conditions: High-speed operations can increase stress on screens, accelerating their wear.
Regular monitoring and maintenance can mitigate some of these issues. For instance, using screens made from durable materials can extend lifespan and performance. Employing predictive maintenance strategies, where data is utilized to forecast when replacements are necessary, can also save costs in the long run, ensuring screens don’t fail unexpectedly.
"A stitch in time saves nine"—addressing screen wear proactively is much less costly than facing operational downtime.
Clogging Issues
Another significant concern is clogging. This issue arises from the accumulation of material within the screen openings, which can drastically hinder throughput. When screens become clogged, not only is the grinding process interrupted, but it also poses a risk to the hammer mill's overall operation, leading to potential damage.
Clogging can be attributed to various factors, including:
- Type of Material: Finer or sticky materials are more prone to clogging.
- Screen Configuration: Screens with smaller openings or improper orientation can trap material.
- Operating Speed: Too slow of a speed may not effectively push material through, causing backups.
To deal with clogging, operators often implement certain strategies:
- Regular Check-Ups: Frequently inspecting screens can help catch early signs of clogging.
- Vibration Mechanisms: Integrating vibratory movements can dislodge trapped particles.
- Selecting the Right Screen Type: Choosing the appropriate type of screen for the material being processed is critical.
In closing, the challenges associated with hammer mill screens underscore the importance of strategic management and understanding the operating environment. Monitoring screen wear and tackling clogging not only support operational efficiency but enhance product quality and reduce costs. As the saying goes, knowledge is indeed half the battle.
Future Trends in Hammer Mill Screen Technology
The technology surrounding hammer mill screens is on the brink of dynamic transformation, driven by continuous innovations and evolving industry demands. As agricultural and industrial sectors strive for higher efficiency and reduced operational costs, these trends become vital. Adopting cutting-edge techniques helps in boosting performance, increasing product quality, and ensuring sustainable practices. Understanding future trends is essential for stakeholders across various fields as they navigate a rapidly changing landscape.
Innovations in Material Science
The advancements in material science are playing a pivotal role in the evolution of hammer mill screens. Manufacturers are increasingly experimenting with composite materials, which possess a combination of properties that are not achievable with traditional metal screens. By integrating materials such as reinforced polymers or advanced alloys, these new screens offer improved durability, reduced weight, and enhanced resistance to wear and tear.
Some key takeaways regarding materials include:
- Increased Lifespan: Screens made from advanced compounds can significantly extend the operational life, reducing downtime for replacements.
- Customization: The flexibility in material composition allows for customization of screens tailored to specific applications, leading to optimized performance.
- Cost-Effectiveness: While initial investment may be higher, the long-term savings on maintenance and replacement can markedly offset the upfront costs.
As we delve deeper into the science behind these innovations, it's evident that the future of hammer mill screens lies in materials that not only minimize environmental impact but also maximize efficiency in processing.
Advancements in Automation
Automation technology is reshaping the way hammer mills operate, enhancing both productivity and consistency in processing outputs. With the integration of smart technologies, such as sensors and data analytics, operators can now monitor and adjust hammer mill settings in real-time. This leads to precision processing and helps in achieving the desired particle sizes with minimal human intervention.
Some noteworthy advancements include:
- Real-Time Monitoring: Systems equipped with sensors can provide continuous feedback, enabling operators to make necessary adjustments instantly.
- Predictive Maintenance: Leveraging data analytics can forecast when maintenance is needed, helping to avoid unexpected breakdowns and ensuring smooth operations.
- Energy Efficiency: Automated systems can optimize energy usage during operations by adjusting the feed rate and air flow, effectively reducing operational costs.
"The integration of material science and automation in hammer mill technology is gearing up to unlock unprecedented levels of productivity and sustainability across industries."
Case Studies on Hammer Mill Screen Application
Examining real-world applications of hammer mill screens can shine a light on their impact and versatility across different industries. These case studies not only illustrate the practical usage of screens but also highlight challenges, benefits, and the resulting efficiencies that can be achieved. In the realm of agricultural and industrial processing, understanding these applications can inform best practices and enhance operational strategies for professionals in the field.
Performance Analysis in the Feed Industry
The feed industry presents a compelling case study for analyzing hammer mill screens. Companies often encounter a range of ingredients with varying textures and moisture content. A notable example involved a major animal feed manufacturer aiming to improve the consistency in particle size for better animal nutrition and feed efficiency.
They initially utilized perforated screens with a specified hole size aimed at a coarse grind. However, it became apparent that this resulted in uneven mixtures and reduced digestibility for the livestock they were feeding.
After conducting an analysis of their operations, they decided to switch to a finer mesh screen. This change allowed for a more uniform particle size that promoted better feed conversion rates. The outcomes were significant:
- Reduced Waste: There was less feed lost due to dust and larger particles that animals could not consume effectively.
- Improved Growth Rates: Livestock exhibited healthier growth patterns, attributed directly to the improved digestibility of the feed.
- Cost Savings: With increased feed efficiency, the overall cost for feed production saw a notable decrease.
Through this analysis, it’s clear that the correct choice of hammer mill screens can dramatically transform product quality in the feed industry, leading to better animal health and operational efficiency.
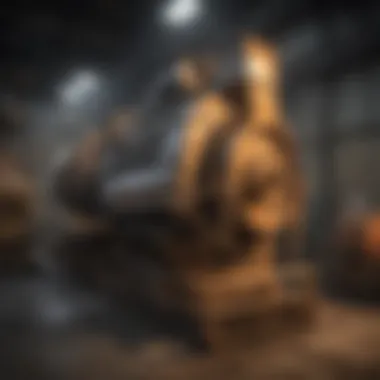
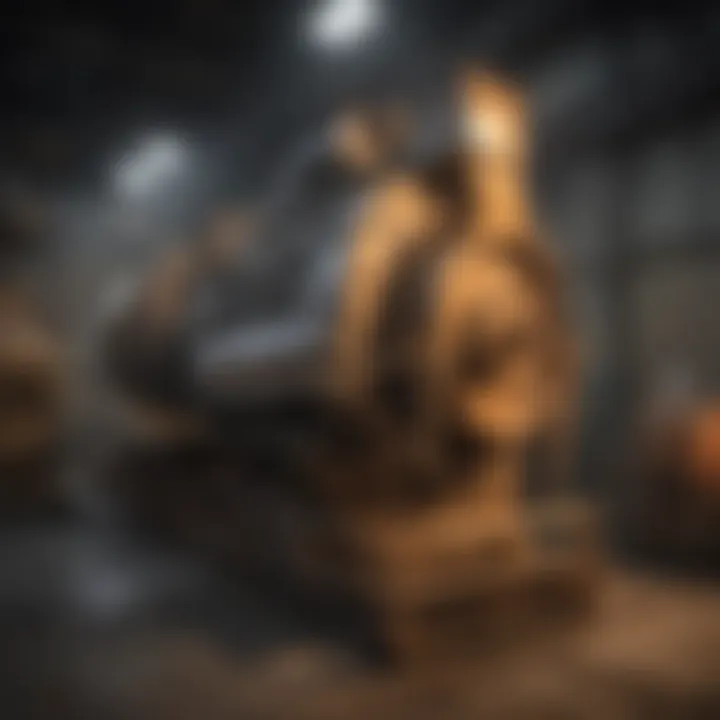
Research Trials in Agricultural Processing
Another fascinating case study emerges from agricultural processing, specifically in grain milling. In a research trial conducted at an agricultural university, the purpose was to assess the effectiveness of different screen types in enhancing the extraction rates of flour from various grains, including wheat and corn.
The researchers implemented a series of trials to compare:
- Bar Screens
- Wire Mesh Screens
- Perforated Screens
The outcomes overwhelmingly favored a combination of bar screens for pre-treatment, followed by perforated screens during the final milling stage. The findings were as follows:
- Higher Extraction Rates: Using bar screens first facilitated improved removal of larger husk particles, thus allowing for a higher yield of flour during subsequent milling stages.
- Quality Enhancement: Perforated screens produced a finer flour with a more consistent texture, which is crucial for baking applications.
- Operational Efficiency: The study illustrated a reduction in processing times, thanks to the optimal sequencing of screen types.
"The right hammer mill screens not only serve to reduce operational costs but also contribute significantly to product quality and marketability."
These trials showcase how targeted application of hammer mill technology can elevate production levels and enhance product quality.
By dissecting these instances, it becomes evident that the thoughtful selection and application of hammer mill screens can lead to not just operational adjustments but substantial competitive advantages in the feed and agricultural processing industries.
Regulatory Standards for Hammer Mill Screens
Understanding the regulatory standards surrounding hammer mill screens is crucial for ensuring both safety and efficiency in operations. These standards establish guidelines that help protect workers while also ensuring the product meets quality expectations. Regulatory frameworks can differ from one region to another, but certain universal principles often guide the establishment of safety and quality measures.
One of the primary benefits of adhering to these regulations is compliance with safety requirements that reduce the risk of accidents or machinery failure. Regulatory standards typically specify design, construction, and operational factors that safeguard both the user and the environment. For businesses, aligning with these standards not only promotes worker safety but also enhances their reputation in the market.
Safety Guidelines
Regulatory safety guidelines are foundational elements that dictate how hammer mill screens should be designed and maintained. They often encompass several critical aspects, including:
- Material Specifications: Screens must be made from materials that do not degrade under operational conditions, like high-stress manufacturing environments.
- Design Standards: The screen designs should prioritize operators' safety, ensuring that they cannot easily come into contact with moving parts during operation.
- Emergency Protocols: Organizations must provide clear emergency procedures and training for all workers, depending on the hammer mill screen's specific use case.
Ensuring that operators are equipped with personal protective equipment (PPE) is also an aspect covered under safety guidelines. This mitigates risks associated with dust inhalation and accidental injuries from equipment.
Quality Control Measures
In conjunction with safety standards, quality control measures are equally pivotal. These measures aim to ensure the screens perform optimally and consistently produce the desired product quality. Key quality control measures may include:
- Regular Testing: Hammer mill screens must undergo regular performance assessments to ensure they meet required dimensional tolerances and material integrity.
- Production Consistency Checks: Continuous checks during the manufacturing process can help identify variations that could affect product quality.
- Documentation and Reporting: Maintaining detailed records of testing and inspections creates accountability and aids in tracking improvements or failures over time.
By aligning operations with quality control measures, businesses can not only fulfill regulatory requirements but also boost their overall production efficacy.
"Adhering to regulatory standards isn't just about compliance; it's about fostering a culture of safety and quality that can lead to improved operational success."
In summary, establishing a strong understanding of the regulatory framework for hammer mill screens can significantly impact safety, product quality, and operational efficiency. Companies that prioritize these standards are better positioned to navigate the complexities of modern regulatory environments.
Comparative Analysis of Hammer Mill Screen Materials
When exploring the realm of hammer mill screens, an essential aspect that often comes under the microscope is the materials they are made from. The right choice of material can make all the difference in performance, longevity, and overall efficiency of the hammer mill. The comparative analysis between metal and composite materials gives insights into both the benefits and considerations for selection.
Metal Versus Composite Materials
When we talk about metal screens, we're usually referring to options like stainless steel and carbon steel. These materials are known for their durability and robustness. They can withstand higher wear and tear, which is particularly relevant in industries that deal with tougher materials such as wood, grains, and even minerals. Additionally, metal screens offer smoother surfaces, which can aid in reducing friction, hence potentially increasing the speed of production. But here's the catch: metal screens can represent a higher upfront cost. In certain applications, the risk of rust and corrosion, especially under humid or wet conditions, is another concern that needs careful consideration.
On the flip side, composite materials present an interesting alternative. They are often lighter, which can positively impact the overall machine operation. Composite screens can be less expensive compared to their metal counterparts, and they sometimes offer improved flexibility. This distinct property can be beneficial in applications where tight tolerances are necessary. However, it’s worth noting that while composite materials can fend off corrosion quite well, they might not hold up in conditions where extreme abrasion is a concern.
In a nutshell, the choice between metal and composite materials hinges on:
- Nature of the Process: Whether the hammer mill is dealing with abrasive or soft materials will greatly influence material selection.
- Cost Consideration: Initial costs versus potential longevity and performance.
- Environmental Factors: Humidity, temperature, and abrasiveness all play roles in determining suitability.
When it comes to hammer mill screens, one size neither fits all nor can one material cover all use cases. Thoughtful selection based on application requirements is paramount.
Cost-Efficiency Evaluations
Evaluating the cost-efficiency of hammer mill screen materials is not merely a matter of price tags. It involves a multifaceted approach that balances initial expenditure against life cycle costs, performance, and operational efficiencies.
- Initial Investment: Metal materials might demand a heftier upfront investment due to their durability. However, if these screens last significantly longer than composite ones in specific applications, the longer-term savings can be substantial.
- Maintenance and Repairs: Composite materials may require less maintenance due to reduced likelihood of oxidation. Therefore, from a practical standpoint, one must account for the potential costs associated with repairs or replacements in both scenarios.
- Efficiency Gains: In terms of throughput and speed, metal screens may allow for faster processing times due to their rigidity. An efficient screen can lead to less downtime.
- Waste Management: Depending on the service environment, metal screens might generate materials that can be recycled, which can provide some return on investment. Composite screens, while offering flexibility, might lead to higher waste if damaged.
User Experiences and Recommendations
When evaluating the effectiveness of hammer mill screens, the voices of those who use them daily can provide invaluable insights. User experiences, grounded in real-life applications, shed light on common challenges and triumphs that may not be documented in technical manuals. It's paramount to delve into the research or feedback from end-users to understand how hammer mill screens, in practice, influence efficiency, product quality, and maintenance. Without a doubt, integrating user experiences offers a richer perspective when discussing functionality, types, and optimization.
Customer Feedback Insights
Many users express that the choice of hammer mill screen significantly impacts their production levels and overall quality of output. Feedback often reveals a few central themes around performance and reliability. For instance, operators in the feed industry frequently stress quality over quantity, reporting that the right sized holes led to a more uniform particle distribution, enhancing the palatability of feed. Moreover, some have noted that screen wear and tear can be a substantial concern, leading to unforeseen downtimes. This reinforces the need for regular inspection and using durable materials.
A customer recently mentioned, "Swapping out our standard screens for ones made from composite materials has completely changed the game for us. They last longer and resist clogging better, especially with our high-moisture materials."
This feedback correlates closely with others who note that investing in higher-quality screens early on often pays off in operational efficiencies and reduced replacement frequencies. Users are often keen to share these experiences in forums such as Reddit and on vendor websites, where they exchange tips and insights.
Best Practices from Industry Experts
Insights from seasoned professionals in the field offer a treasure trove of best practices when it comes to hammer mill screens. These individuals, with their wealth of experience, underline the necessity of pre-screening materials prior to processing. Expert recommendations often include:
- Conducting a thorough material evaluation to identify characteristics that may affect the screen selection. This is pivotal for enhancing both the life of the screens and the quality of output.
- Adopting a preventative maintenance schedule. Experts advise checking for signs of wear and tear regularly, not just during scheduled maintenance. Simple steps like ensuring that screens are clean can mitigate clogging issues.
- Variety in screen types. Experts suggest having a mix of screens available to adapt to changing material requirements. This flexibility can prove crucial during peak production times.
In addition, they highlight the merit in developing partnerships with screen suppliers. Working closely with manufacturers like Schutte-Buffalo or Prater can yield deeper insights into evolving product lines and innovations that potentially suit specific needs.
Finale: The Importance of Hammer Mill Screens
In summary, the significance of hammer mill screens cannot be overstated. They are at the heart of size reduction processes across various industries. Their function extends beyond merely breaking down materials, influencing product quality, efficiency, and operational costs. When one understands the role that these screens play, it becomes abundantly clear why careful selection and maintenance are critical.
Key Benefits of Hammer Mill Screens:
- Enhanced Particle Size Control: The right screens enable precise control over the size of processed materials, ensuring uniformity and meeting product specifications.
- Improved Processing Efficiency: Well-maintained hammer mill screens contribute to higher throughput, reducing downtime and boosting overall productivity.
- Cost-Effectiveness: Properly selected screens can decrease energy consumption, enhancing cost-efficiency in the long run.
- Quality Assurance: Screens help maintain the integrity of the product by preventing contamination or the presence of oversized particles.
The considerations surrounding hammer mill screens involve a deep understanding of various aspects such as the material properties, desired outcomes, and the specific needs of the operation. Addressing these elements leads to better decision-making and ultimately, improved processes.
Summary of Key Points
To succinctly recap, this article has covered:
- The key functionalities of hammer mill screens, detailing how they aid in the size reduction process and impact product quality.
- Different types of screens available, such as perforated, wire mesh, and bar screens, each tailored for specific industrial needs.
- Factors influencing screen selection, including material characteristics and production capacity.
- Performance metrics and maintenance practices that ensure screens operate at optimal levels.
- Technological advancements expected in hammer mill screens, which push the boundaries of efficiency.
Understanding these elements forms a robust foundation for anyone involved in the fields using hammer mill screens, whether in agriculture, manufacturing, or research.
Future Directions for Research
Looking ahead, there is a multitude of avenues for further exploration involving hammer mill screens.
- Innovative Materials: There's ongoing research into new materials that could improve screen longevity and reduce wear. Materials with enhanced resistance properties may lead to increased productivity.
- Smart Technology Integration: As industries embrace automation, hammer mill screens may benefit from integration with smart technology. Sensors that monitor performance in real-time can provide valuable data and enable proactive maintenance.
- Nanotechnology Applications: Future studies might focus on how nanotechnology can transform how materials are processed by providing finer control over particle size and characteristics.
- Sustainability Practices: Research into environmentally friendly practices in the manufacture of hammer mill screens could address growing concerns about sustainability across industries.
By pursuing these directions, the field stands to gain insights into optimizing processes, enhancing efficiency, and ultimately leading to better outcomes in various applications.
"An investment in hammer mill screens is an investment in efficiency, quality, and ultimately, success across industrial processes."
In closing, the journey into understanding hammer mill screens is more than a technical endeavor; it is a critical component of advancing industry practices, ensuring that both productivity and quality meet the standards expected in today's competitive landscape.