Corrosion Effects on Metals: Mechanisms and Protection
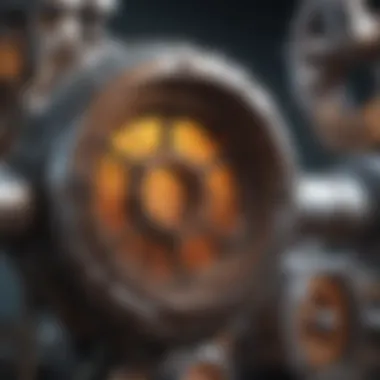
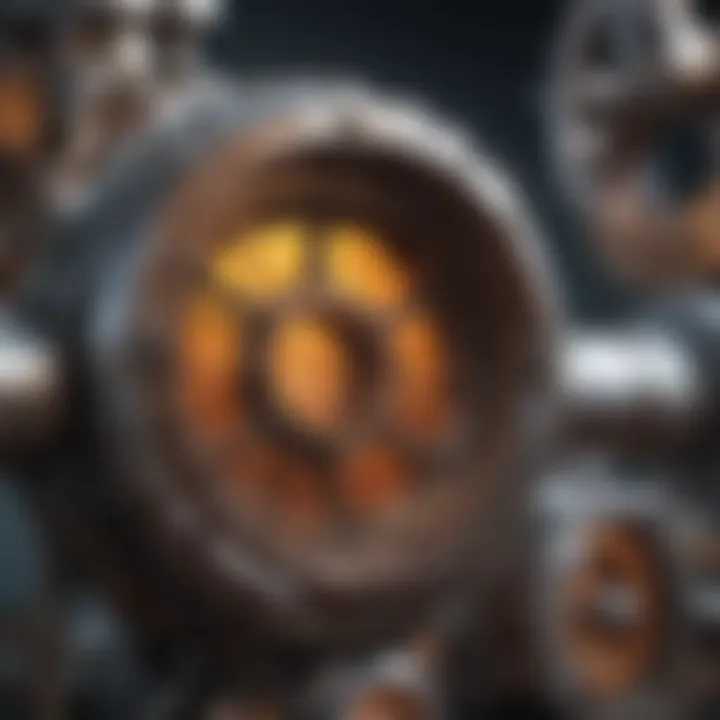
Intro
Corrosion is a process that not only deteriorates metals but also poses severe ramifications for structural integrity and safety. It is an omnipresent issue across various industries, impacting everything from bridges and pipelines to spacecraft and chemical processing plants. As metals react with the environment, the consequences can range from minor maintenance concerns to catastrophic failures.
In essence, understanding the corrosive effects on metals requires delving into a multitude of factors—chemical interactions, environmental conditions, and the intrinsic properties of the metals themselves. This exploration is critical, as it arms professionals in engineering, materials science, and maintenance management with the knowledge to protect and preserve valuable infrastructures. Such an endeavor moves beyond surface-level comprehension, demanding a more profound grasp of the mechanisms at play.
This article aims to dissect these elements methodically, enabling a clearer understanding of corrosion and its protective strategies. In doing so, we will encompass definitions, key terms, findings, and future research areas, enriching the reader’s knowledge base significantly. Let's embark on a journey into the realm of metal corrosion.
Prelude to Corrosion
Corrosion stands as a fundamental challenge in materials science, especially when it comes to the integrity of metals. It refers to the gradual destruction or deterioration of materials, particularly metals, due to their interactions with various environments. This process is not just an academic concern; its implications resonate throughout industries and infrastructure. From bridges to pipelines, understanding how and why corrosion occurs is crucial for maintaining safety and longevity.
Corrosion can be seen as a multifaceted issue crisscrossing chemistry, engineering, and environmental science. The endeavor to grasp the essence of corrosion leads to significant benefits, such as the development of better protective measures, cost-saving strategies, and enhanced safety in construction. Consider it as a vigilant watchtower, keeping us aware of the silent, often damaging forces at play in everyday materials.
"Corrosion is an uninvited guest that silently creeps in, deteriorating what seems to stand strong at first glance."
In exploring corrosion in this article, we will cover its definition, historical context, and why studying it matters.
Definition of Corrosion
Corrosion can be boiled down to a simple idea: it is the process through which metals convert to their more stable forms, often oxides, hydroxides, or sulfides, through their reaction with environmental agents like water, oxygen, and acids. Chemically, most corrosion phenomena can be depicted through electrochemical reactions, where metal atoms lose electrons and, in turn, become ions. This shedding of electrons compromises the metallic structure, leading to physical degradation.
In more visual terms, think of a shiny new car left out in the rain. Over time, rust begins to sneak in, slowly erasing that once-perfect surface.
Historical Perspectives on Corrosion
Historically, corrosion has been observed since ancient civilizations. For example, the Greeks and Romans dealt with rust as they built their renowned structures, often employing innovative practices to slow down the deterioration of their metals. They coated iron with lead to protect it from rust. Fast forward to the Industrial Revolution, the challenge appeared even more significant, as factories and machinery became essential. The rapid development of steel and iron structures brought corrosion to the forefront of engineering challenges.
Today, so much of our infrastructure and technology hinges on materials that confront corrosive environments. One might think of the Panama Canal, whose construction sparked extensive studies on corrosion prevention because of the maritime conditions that threatened its integrity.
Significance of Corrosion Studies
Understanding corrosion is vital for several reasons. First, it allows for better risk assessments related to safety and service life of structures and objects. Imagine a bridge slowly corroding over time; knowing its degradation path allows engineers to intervene before catastrophe strikes. Secondly, the economic impact of corrosion is staggering. It’s often estimated that corrosion costs industries billions annually, making it essential for organizations to invest in corrosion research and prevention.
Moreover, as environmental regulations tighten, developing corrosion-resistant materials that are eco-friendly and sustainable becomes imperative. This sets the stage for future innovations that balance technology and the environment.
In essence, studying corrosion isn’t merely about understanding a material’s decline; it fosters resilience across industries, innovating ways to preserve our infrastructure and investments. As we delve further into this article, we will explore the types of corrosive substances, mechanisms at play, and strategies for combating corrosion challenges.
Types of Corrosive Substances
Understanding the types of corrosive substances is crucial for comprehending how they affect metals. Each type has its unique interactions with different alloys, which can lead to varying degradation paths. Recognizing these substances helps industries in selecting the right materials for their applications and in establishing effective protective measures against corrosion.
Different corrosive agents can cause diverse damage to metal structures, and it varies with environmental conditions. This awareness can save a lot of time and money by preventing premature failure of metal components in vehicles, infrastructure, and machinery.
Acids and Bases
Acids and bases play a significant role in the corrosion of metals. Acids, like sulfuric and hydrochloric, are particularly notorious for their ability to react with metals, leading to degradation. This occurs due to the release of hydrogen ions, which can strip away metal, frequently resulting in pits and grooves.
On the flip side, bases can also cause corrosive effects, although they are often less discussed. For example, sodium hydroxide can be as damaging as strong acids, especially to aluminum and its alloys. Different metals react uniquely to various acid concentrations, which is why understanding these reactions is paramount in industries such as aerospace and automotive.
Some key points regarding acids and bases include:
- Temperature Sensitivity: Elevated temperatures can intensify the corrosive effects of acids and bases, accelerating metal deterioration.
- Concentration Matters: Higher concentrations result in more aggressive corrosion, making it pivotal to monitor and control substance levels.
- Environmental Factors: Humidity and temperature influence how acids and bases act on metals, which means real-world applications should always consider surroundings.
Salts and Chlorides
Salts, particularly chlorides, are infamous corrosion accelerators. Sea salt, for instance, can induce significant corrosion on metallic surfaces exposed to marine environments. When metal comes in contact with saline solutions, a process called electrochemical corrosion is triggered, where ions migrate and lead to metal loss.
Chlorides can break down protective oxide layers on metals like stainless steel, making them vulnerable to pitting corrosion. This phenomenon is more pronounced in environments with high humidity and temperature.
Key aspects related to salts and chlorides:
- Widespread Presence: Salts are found in many environments, from coastal areas to underground mines. Any metal used in these settings must be resistant to chloride-induced corrosion.
- Increased Conductivity: Saline solutions enhance electric conductivity, facilitating corrosive processes.
- Regular Maintenance: Regular cleaning and application of protective coatings can help mitigate the risks posed by salts.
Oxidizing Agents
Oxidizing agents are another critical category of corrosive substances. These compounds can take electrons from metals, resulting in their oxidation, which hinders the integrity of metals. Common oxidizers include oxygen, chlorine, and nitric acid.
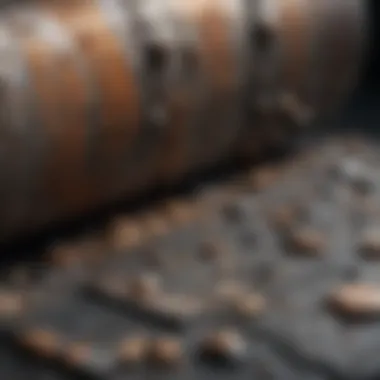
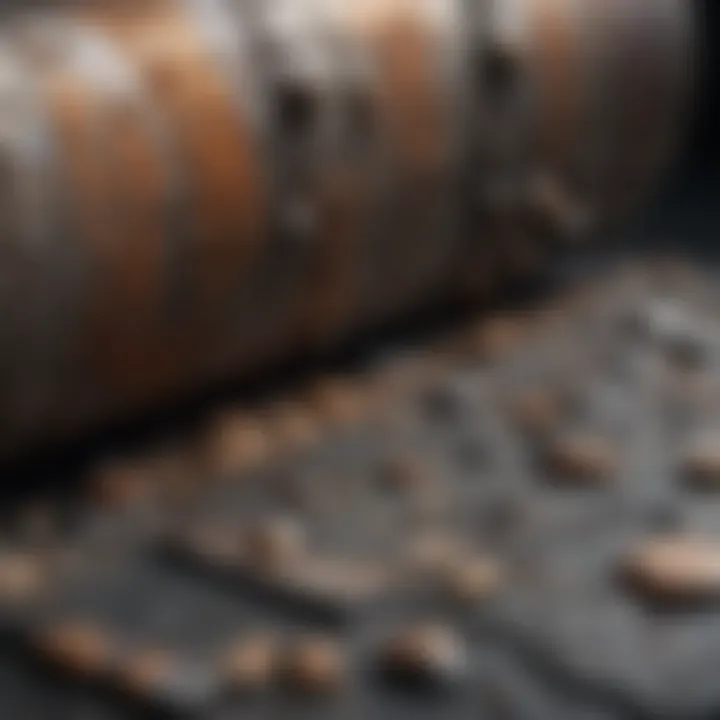
The process can be rapid, especially in materials such as iron and steel, leading to rust formation. Interestingly, although many metals can act as oxidizers, some, like gold or platinum, resist this damaging effect.
Important considerations for oxidizing agents include:
- Environmental Impact: Ambient oxygen can accelerate corrosion in open environments, particularly where humidity levels are high.
- Metal Type Matters: The effectiveness of oxidizing agents varies with metal type, making it essential to choose the right material for specific applications.
- Protective Measures: Coatings and inhibitors can provide a protective barrier against oxidizers, helping to preserve metal integrity over time.
In summary, knowing the types of corrosive substances and their specific effects on metals is fundamental to preventing damage. Proper understanding leads to sound decisions in material selection and protective strategies, ultimately saving costs and increasing safety in various applications.
Mechanisms of Metal Corrosion
Understanding the mechanisms behind metal corrosion is crucial to grasping its broader implications for industry, safety, and environmental management. These mechanisms help shed light on how metals deteriorate over time via chemical reactions that are often invisible until significant damage has occurred. Delving into these mechanisms allows us to recognize not only the vulnerabilities of specific metals but also the strategies we can adopt to prolong their lifespan and protect infrastructure.
Electrochemical Reactions
At the heart of metal corrosion lies the electrochemical reaction process. This involves the transfer of electrons between materials, commonly between the metal and its environment. Essentially, when a metal surfaces is exposed to moisture and oxygen, an electrochemical reaction can start.
These reactions typically result in the oxidation of metals, forming metal ions and electrons, which then lead to metal loss. The importance of understanding such reactions cannot be understated as it allows professionals to foresee potential corrosion issues before they escalate. By recognizing early signs of corrosion, informed decisions can be made regarding maintenance and preventive interventions.
Environmental Factors Influencing Corrosion
The environment plays a pivotal role in corrosion processes. Several factors significantly influence corrosion rates and their mechanisms, including humidity, temperature variations, and the presence of contaminants. These elements contribute to the dynamics of corrosion, effectively accelerating or decelerating the rates at which it occurs.
Humidity and Moisture
Moisture is a major player in the corrosion game. When humidity levels rise, water can settle on metal surfaces, creating the perfect breeding ground for corrosion. The presence of water essentially facilitates the movement of ions, making electrochemical reactions more likely. One notable aspect of humidity is that it not only promotes corrosion but can actually trigger it, acting as a catalyst. Moist air can be particularly damaging as the continuous cycle of drying and wetting puts stress on metal surfaces, leading to pitting and localized corrosion.
The unique feature of humidity as a corrosion accelerant is also tied to how it can influence temperature. Higher humidity levels can cause thermal variations on surfaces, impacting their integrity directly. So, while humidity may seem harmless, it’s a sneaky contributor to corrosion that can have serious implications on metal longevity.
Temperature Variations
Temperature variations present another layer of complexity in corrosion mechanisms. Fluctuating temperatures can cause expansion and contraction in metals, creating stress that can lead to cracking or micro-defects. Not only that, but temperatures can also influence the solubility of corrosive substances in water, meaning more aggressive solutions can form at higher temps.
The interplay of temperature with corrosion is indeed interesting; warmer conditions lead to increased kinetic energy, which can speed up electrochemical reactions, escalating corrosion rates significantly. Thus, managing temperature conditions in processes involving metals is vital for minimizing corrosion-related failures.
Presence of Contaminants
Contaminants introduce an entirely different dimension of risk regarding corrosion. These can range from salts and acids to particulates and pollutants. Each type of contaminant can have a unique effect on how and when corrosion occurs. For example, chlorides found in saltwater are notorious for increasing corrosion rates immensely.
The key characteristic of contaminants is that they often lead to localized corrosion, creating weaknesses in metals that can lead to catastrophic failures if not managed appropriately. By understanding the specific contaminants that may affect different metals, industries can take tailored steps toward monitoring and controlling corrosion risks more effectively.
Types of Corrosion Phenomena
Corrosion isn’t a one-size-fits-all issue; rather, it presents itself in several distinct forms based on the underlying mechanisms and environmental conditions. Understanding these phenomena is essential for recognizing how to categorize and subsequently manage corrosion-related risks.
Uniform Corrosion
Uniform corrosion is often the easiest type to recognize due to its even distribution across a surface. This type occurs fairly uniformly on exposed surfaces when electrochemical reactions happen over the whole area. It’s essential to understand how uniform corrosion can lead to gradual thinning of metal, as it may not be consistently apparent until it becomes severe. While detecting uniform corrosion can be simpler, it still requires proactive monitoring to mitigate its long-term effects on structures and components.
Localized Corrosion
In contrast to uniform corrosion, localized corrosion tends to target specific areas, leading to phenomena like pitting and crevice corrosion. This kind of corrosion can be considerably more damaging as it may cause rapid material degradation over time in targeted areas, potentially resulting in catastrophic failures. The tough part with localized corrosion is its often-hidden nature, making it imperative for ongoing monitoring through advanced techniques to detect early signs.
Galvanic Corrosion
Galvanic corrosion occurs when two dissimilar metals come into contact in a corrosive environment, forming a galvanic cell. In this case, one metal (the anode) corrodeds faster than the other (the cathode), often leading to significant degradation. Understanding galvanic corrosion is vital, particularly in construction and engineering contexts where different metals are frequently combined. Recognizing when galvanic interactions are likely to occur can lead to informed decisions about materials selection and design strategies, helping to mitigate the risks associated with this phenomenon.
"Corrosion management begins with understanding the intricate dance of electrochemical processes and environmental factors. Recognizing these mechanisms is the key to developing effective strategies for protection and mitigation."
By appreciating these mechanisms and their various implications, stakeholders can create robust strategies designed to counteract corrosion, ensuring not just the longevity of materials, but also the safety and reliability of structures.
Impact of Corrosion on Metals
Corrosion is not just a technical issue; it transcends into a major concern that influences economic stability, safety protocols, and environmental health. Understanding the impact of corrosion on metals is vital, as its consequences ripple through various sectors, from manufacturing to infrastructure. The challenge lies in identifying how corrosive processes degrade metal structures, leading to potential hazards and unforeseen expenditures. In this section, we will dive into the degradation mechanisms that characterize corrosion and explore the economic and safety implications that arise from ignoring this critical issue.
Degradation Mechanisms
Corrosion degrades metals through several mechanisms, each uniquely damaging and often interrelated. Here are some key processes:
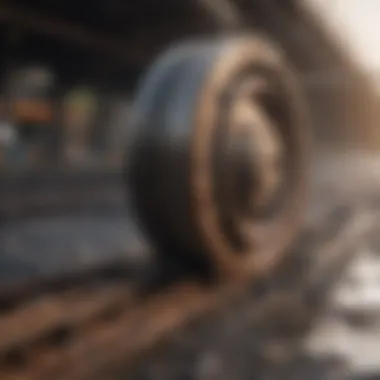
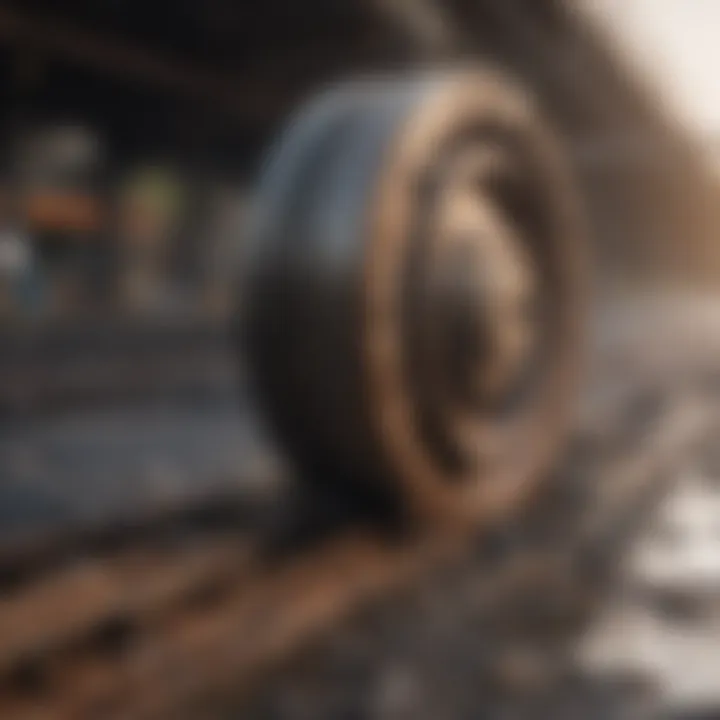
- Uniform corrosion occurs evenly across the surface, leading to a gradual loss of material. This type is often predictable, making it easier to manage with scheduled maintenance.
- Localized corrosion, on the other hand, presents a more insidious problem. It focuses in specific areas, creating deep pits that can compromise the integrity of the entire structure without obvious signs of distress on the surface. This is often seen in marine environments where saltwater facilitates such attacks.
- Galvanic corrosion arises when dissimilar metals come into contact in an electrolyte, leading to accelerated deterioration of one metal (the anode) at the expense of the other (the cathode). This requires careful materials selection to avoid unintentional pairings that can trigger this type of corrosion.
Each of these mechanisms can vary significantly in progression depending on environmental conditions and the nature of the materials involved. Recognizing these patterns allows industries to better strategize and apply protective measures.
Economic and Safety Implications
The economic footprint of corrosion is staggering, spanning billions of dollars globally. It is estimated that corrosion costs the United States alone over $300 billion annually, factoring in repairs, maintenance, and lost productivity. Investing in corrosion control is not just a protective measure; it is a strategic financial decision.
Moreover, the safety implications are equally grave. Corroded structures can fail catastrophically, leading to accidents that jeopardize lives and potentially result in legal ramifications for businesses. For instance, a corroded bridge can collapse during peak traffic, causing not only injuries but also halting economic activity in the area. To mitigate such risks, regular inspections and proactive treatments are essential procedures for any infrastructure management plan.
"Corrosion doesn't just wear away metal; it threatens the very fabric of our industrial society."
In summary, recognizing the impact of corrosion on metals is a quintessential aspect of maintaining both economic viability and public safety. The degradation mechanisms that underlie corrosion warrant serious attention, particularly as industries navigate complex and sometimes perilous material environments. By fortifying our understanding of corrosion’s repercussions, we can foster a culture of diligence and foresight that respects the intricate balance between progress and preservation.
Protection Strategies Against Corrosion
Corrosion is an inevitable process that can significantly undermine the longevity and integrity of metal structures. Therefore, understanding protection strategies against corrosion is essential for maintaining the operational effectiveness of metal components across various industries. The implications of ineffective corrosion management can be staggering, often leading to costly repairs, safety hazards, and a shorter lifespan of equipment.
To ensure that metals withstand corrosive environments, there are several key elements at play:
- Prevention through proper choice of materials
- Application of protective coatings
- Implementation of cathodic protection techniques
By assessing these strategies in detail, we can explore their benefits, considerations, and how they can effectively combat corrosion in everyday applications.
Material Selection
Material selection is foundational when discussing protection strategies against corrosion. Different metals exhibit varying levels of resistance to corrosive agents. For instance, stainless steel is often favored in environments where moisture and corrosive substances are prevalent, due to its inherent properties but many applications call for more specific requirements.
Some critical factors to consider in material selection:
- Environment: The type of environment where the metal will be located has a large impact on its longevity. A marine environment, for instance, poses unique challenges due to salt exposure, thus materials specifically designed for marine applications should be used.
- Mechanical properties: The strength and flexibility of the material impact its resistance to external forces and corrosive wear.
- Cost effectiveness: While choosing the most corrosion-resistant material may seem ideal, budget constraints often necessitate compromise. Thus, striking a balance between performance and cost is crucial.
Protective Coatings
The use of protective coatings serves as a barrier between metals and corrosive substances, making this strategy paramount in corrosion management. Various types of coatings are available, each suited to different applications.
Common types of protective coatings include:
- Paints
- Plastics
- Galvanization (zinc coating)
- Polymer coatings
These coatings not only act as physical barriers but can also chemically impede the corrosion process by neutralizing corrosive agents. However, one must be diligent in applying and maintaining these coatings, as any flaw could become a corrosion initiation point. Regular inspection is thus a necessity to uphold the integrity of the protective layer.
Cathodic Protection Techniques
Cathodic protection is crucial in environments where the risk of galvanic corrosion is high. This technique involves applying a protective current to metal surfaces, essentially converting the metal surface into a cathode in a galvanic cell.
Two primary types of cathodic protection include:
- Sacrificial Anode Protection: In this method, a more reactive metal, such as magnesium or zinc, is used as an anode. It corrodes preferentially, protecting the steel structure.
- Impressed Current Cathodic Protection (ICCP): This involves using an external power source to provide a current to the metal surface, bolstering its resistance against corrosion.
Implementing these techniques requires careful planning and monitoring to ensure effectiveness.
"The best protection is often a multi-layered approach, combining various strategies for maximum effectiveness against corrosion."
Corrosion Monitoring Techniques
Corrosion monitoring is a critical aspect in managing the health of metal structures. It serves as the backbone for preventative measures, enabling timely intervention before extensive damage manifests. By employing effective monitoring techniques, industries can maintain safety, optimize resources, and ensure longevity of materials. Corrosion can be sneaky, often progressing without visible damage, making regular monitoring crucial. This section delves into two primary methods for detecting and assessing corrosion: visual inspection alongside non-destructive testing, and electrochemical methods.
Visual Inspection and Non-Destructive Testing
Visual inspection is often the first line of defense against corrosion. Skilled personnel can identify early signs of corrosion, assessing visible changes in the surface condition of materials through direct observation. Regular visual checks can often catch peeling paint, rust spots, or changes in texture, which are indicators that corrosion may be lurking underneath.
Non-destructive testing (NDT) complements visual checks by allowing more in-depth analysis without compromising the integrity of the material. Techniques such as ultrasonic testing or magnetic particle inspection can detect subsurface faults, which visual methods might overlook. For instance:
- Ultrasonic Testing: Utilizes high-frequency sound waves to gauge the thickness of materials, thereby identifying any corrosion-induced loss of structure.
- Magnetic Particle Inspection: This method is particularly effective for detecting surface and near-surface defects in ferrous materials, revealing areas of potential weakness.
"An ounce of prevention is worth a pound of cure." An adage that fits well here, as catching corrosion early saves both time and resources.
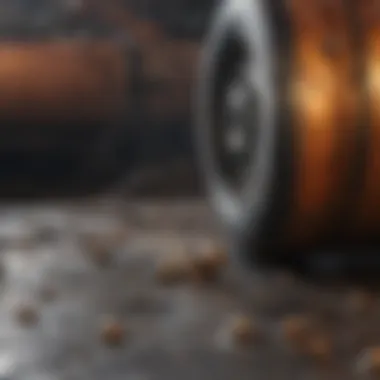
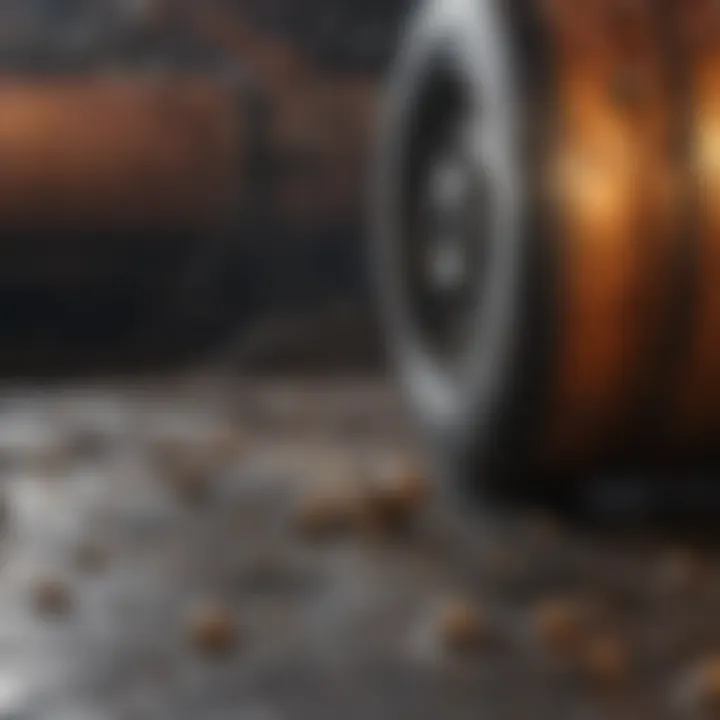
While these techniques are valuable, it's important to recognize their limitations. Visual inspection can miss subsurface corrosion, and non-destructive techniques often require trained specialists to interpret the results accurately. Both methods should be integrated into a comprehensive maintenance strategy, ensuring no stone is left unturned in the quest to mitigate corrosion risks.
Electrochemical Methods
Electrochemical methods offer a more sophisticated approach to monitoring corrosion. These techniques measure the electrochemical response of metals in their operating environment, giving insight into the corrosion process in real time. Such methods are vital for environments where predictive modeling is critical, such as oil rigs or bridges where stakes are high.
Common electrochemical monitoring techniques include:
- Potentiodynamic Polarization: This method assesses the corrosion rate by evaluating the metal's response to an applied voltage, determining both the susceptibility to corrosion and the polarization resistance.
- Electrochemical Impedance Spectroscopy (EIS): A more advanced technique, EIS analyzes the impedance of an electrochemical system, offering detailed insights into the corrosion mechanisms at play.
- LPR (Linear Polarization Resistance): LPR is a simple and effective approach to monitoring corrosion rates, providing real-time data on the metal's condition based on voltage changes.
These methods are valuable for their precision and the information they provide, enabling targeted maintenance actions that can prolong the lifespan of metal components. However, they may require specialized equipment and trained personnel, thus incurring higher initial costs.
Case Studies in Corrosion Management
The field of corrosion management can gain significant insights from analyzing specific case studies. By examining real-world instances where corrosion has had a tangible impact, professionals can not only understand the consequences but also explore effective strategies for mitigation. This analysis serves as a substantial resource for students, researchers, and industry professionals alike.
Industrial Applications
Industries worldwide face the relentless challenge posed by corrosive elements. For instance, the oil and gas sector often grapples with corrosion in pipelines that transport crude oil and natural gas. These systems are frequently exposed to aggressive environments, including high pressure and sea water, which significantly accelerates degradation. In a notable case, a major oil company found that implementing improved corrosion-resistant materials reduced pipeline failure rates by nearly 30%. This transition not only safeguarded the infrastructure but also considerably cut down maintenance costs and production downtime.
Moreover, the aerospace industry provides a compelling example. Aircraft structures are subjected to varied climatic conditions, leading to different corrosion mechanisms. A comprehensive study revealed that replacing aluminum components with specialized alloys resulted in a marked increase in lifespan. This proactive step reflected not only financial prudence but enhanced safety. Such examples underscore the necessity to prioritize corrosion management in sectors heavily reliant on metal integrity, ranging from manufacturing to construction.
Infrastructure Failures and Lessons Learned
Infrastructure failures can be catastrophic, both in terms of human safety and economic implications. Take, for instance, the collapse of a bridge in a major city due to severe corrosion in steel girders. Investigation later revealed that inadequate protective measures and lack of regular monitoring were pivotal in allowing corrosion to thrive. This incident served as a critical lesson for urban planners and civil engineers.
The key takeaways from such failures include:
- Regular Inspections: Anticipating corrosion can help manage its risks before significant damage occurs.
- Material Development: Utilizing higher-grade materials and coatings that resist corrosion are essential to prolong the lifespan of structures.
- Public Policy and Regulations: Reassessing guidelines around construction and maintenance can lead to better standards for corrosion management.
In a broader sense, addressing these lessons can drive new policies, enforce stricter guidelines, and elevate training standards across the industries frequently encountering corrosion issues. The alignment of research, field experience, and regulatory frameworks enhances protective measures, ensuring a safer and more durable infrastructure overall.
"Corrosion is often called the silent destroyer because it can be difficult to detect. Well-planned case studies expose vulnerabilities and promote smarter strategies."
Future Directions in Corrosion Research
Research into the corrosive effects on metals is an ongoing journey, with new chapters continually being drafted. The importance of focusing on future directions in this field cannot be overstated. With ever-increasing demands from industries to maintain structural integrity and ensure safety, studying corrosion from fresh angles is crucial. Embracing innovative approaches provides not only enhancements in materials but also improved modeling capabilities. This fusion of innovation and empirical investigation equips researchers and industry practitioners with the tools to address corrosion more effectively.
Innovative Materials and Solutions
The development of innovative materials plays a pivotal role in the fight against corrosion. One promising direction is the utilization of advanced alloys which blend traditional metals with elements such as titanium and chromium. These materials exhibit better resistance to corrosive environments. Another area gaining attention is biopolymers which are derived from natural sources. These have shown potential in fabricating protective coatings that can reduce corrosion rates significantly. One fascinating material is graphene, known for its remarkable strength and durability—its application might enable coatings to protect metals while being environmentally friendly.
Further, self-healing materials are a cutting-edge concept worth mentioning. When damaged, they possess the capability to repair themselves, thereby preventing corrosion from progressing. This concept isn’t strictly theoretical anymore; real-world applications are emerging in many sectors, including aerospace and automotive where metal fatigue due to corrosion can have dire consequences.
Advancements in Corrosion Modeling
Advancements in corrosion modeling represent another promising frontier. Traditionally, predicting corrosion behavior relied heavily on empirical data which, while useful, can be limited and time-consuming. However, recent shifts are underway as computational methods provide robust alternatives. Machine learning techniques are now employed to analyze corrosion mechanisms through data-driven predictions. This provides more accurate assessments of a material's long-term performance in varying environments.
Furthermore, multi-physics modeling integrates various factors such as electrochemistry, fluid dynamics, and temperature fluctuations for comprehensive analysis. This enables researchers to predict how metals will react under a multitude of conditions. By being able to simulate different scenarios, industry professionals can preemptively develop strategies to mitigate corrosion, ultimately prolonging the life of metal structures and components.
"An ounce of prevention is worth a pound of cure." This adage rings especially true in corrosion research, where proactive measures can save significant costs and resources down the line.
To sum up, the future of corrosion research is bright, with numerous pathways to explore. From innovative materials to sophisticated modeling techniques, the field is ripe with potential. Ongoing collaboration among researchers, industry leaders, and educational institutions will undoubtedly yield breakthroughs that will shape the way we approach corrosion in the years to come.
Culmination
Understanding corrosion is not merely an academic pursuit but a fundamental necessity in various industries. The conclusion of this article encapsulates the vital role corrosion awareness plays, especially in the life cycle of metal materials. There are numerous key elements and implications that arise from the study of corrosion, each worthy of consideration.
Summary of Key Points
The exploration of corrosion presented several nuanced aspects:
- Mechanisms of Corrosion: It is crucial to understand that corrosion isn't just a singular event but rather a spectrum of mechanisms, including electrochemical reactions driven by environmental influences like humidity and temperature.
- Economic Impact: The cost tied to corrosion can be staggering, impacting industries and infrastructure alike, leading to significant maintenance expenses and safety hazards.
- Protection Strategies: Various methods such as material selection, protective coatings, and cathodic protection are available to mitigate corrosion risks effectively. Each method has its advantages depending on the context.
In rolling these points together, it’s clear that the knowledge of corrosion effects not only increases the efficiency of metal components but also safeguards investments and enhances safety measures.
Final Thoughts and Recommendations
As we draw this discussion to a close, it's prudent to highlight that awareness and proactive measures can transform corrosion from a foe into a manageable aspect of material science. One recommendation is continuous monitoring and analysis—keeping a close eye on the condition of metal assets can often save considerable future costs. Embracing innovative materials that resist corrosion or developing advanced corrosion modeling methods will also provide significant benefits moving forward.
Furthermore, educating relevant stakeholders, including students, researchers, and professionals, on the complexities of corrosion can foster better protective strategies and enhancements in industrial practices. Collaboration across disciplines such as chemistry, engineering, and economics is necessary.
"It is not the strongest of the species that survives, nor the most intelligent, but the one most responsive to change." — Charles Darwin